
книги / Машины и оборудование нефтяных и газовых промыслов. Силовые приводы машин и оборудования нефтяных и газовых промыслов
.pdf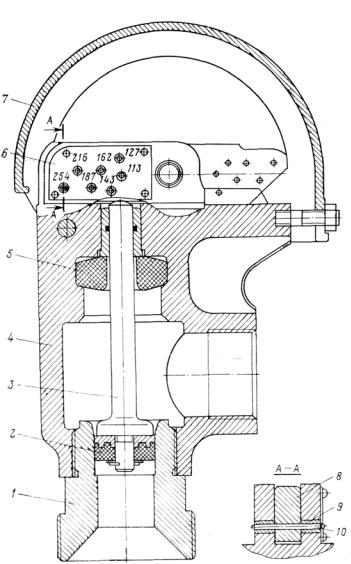
Рис. 5.20. Предохранительный клапан КП-250
При пульсациях давления в линии диафрагма перемещается и сжатый газ над ней то сжимается, то расширяется. Тем самым поддерживается более равномерное давление в линии. Это колебание давления считается приемлемым для буровых насосов, если коэффициент пульсации давления
δ = (pmax – pmin) / pср = 0,05…0,15, |
(5.27) |
где рmax и pmin – максимальное и минимальное значения давления газа в компенсаторе, соответствующие минимальному Vmin и максимальному Vmax значениям объема газа в полости; рср – среднее давление,
pср = (pmax + pmin) / 2. |
(5.28) |
Объем жидкости при пульсации
∆V = Vmax– Vmin. |
(5.29) |
Объем компенсатора Vк должен быть больше ∆V.
121

Рис. 5.21. Пневмокомпенсаторы буровых насосов:
а – всасывающий ПК-20/4; б – нагнетательный ПК-40/250; 1 – седло; 2 – корпус; 3 – диафрагма; 4 – вентиль; 5 – манометр; 6 – пробойник; 7 – крышка; 8 – стабилизатор
Приведенные на рис. 5.21 пневматические компенсаторы по конструктивному устройству мало отличаются. Напорный компенсатор имеет более прочный стальной литой корпус и более солидную диафрагму, снабженную стабилизатором 8. Когда в линии нет давления, диафрагма принимает форму внутренней полости компенсатора. Эти компенсаторы довольно хорошо выравнивают давление в линиях и достаточно надежны. Диафрагма при износе заменяется. Объем компенсатора заполняется газом через вентиль 4 от баллона до требуемого давления [6].
5.8. Центробежные насосы
Центробежные насосы широко применяются в нефтяной промышленности для добычи и перекачки нефтепродуктов и жидкостей различных вязкости и свойств. Они особенно эффективны при перекачке больших объемов при низких и средних значениях давления (до 10 МПа), но используются для перекачки и при более высоких значениях давления. В буровом оборудовании эти насосы применяют ограниченно, так как они не обладают свойством поднимать давление при малых подачах, необходимых при восстановлении циркуляции в скважине после остановок или при осложнениях в процессе бурения.
122
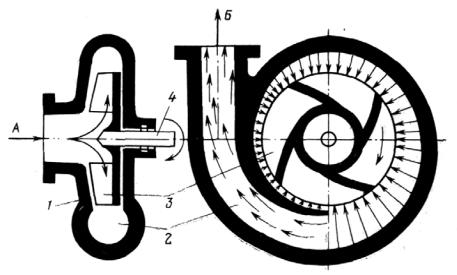
Их используют при вспомогательных работах, таких как нагнетание раствора в буровые поршневые насосы для улучшения их наполнения, перекачка растворов и воды при очистке или приготовлении буровых растворов.
Устройство и принцип действия
Центробежные насосы (рис. 5.22) относятся к динамическим насосам, в которых перекачиваемая жидкость получает напор, создаваемый лопатками быстровращающегося рабочего колеса.
Рис. 5.22. Схема действия центробежного лопастного насоса
Буровой раствор засасывается из резервуара через приемный фильтр-сетку, предохраняющий насос от попадания в него посторонних предметов. Вал насоса 4 соединен с валом электродвигателя, приводящим его во вращение. Через всасывающий патрубок А жидкость поступает вдоль оси корпуса 1 насоса и попадает на лопатки 3 рабочего колеса, насаженного на вал 4. Находясь в межлопастных каналах вращающегося колеса, жидкость разгоняется, движется к его периферии и выходит в спиральный канал 2 корпуса. В этом канале скорость жидкости снижается, так как она преодолевает давление, т.е. кинетическая энергия, приобретенная в роторе, преобразуется в энергию давления. Затем жидкость выходит из насоса через патрубок Б [6].
6. ОБОРУДОВАНИЕ ДЛЯ ПРИГОТОВЛЕНИЯ, ЦИРКУЛЯЦИИ И ОЧИСТКИ БУРОВЫХ И ЦЕМЕНТНЫХ РАСТВОРОВ
6.1. Назначение и основные требования к циркуляционной системе буровой установки
Буровой раствор циркулирует по замкнутой системе, т.е. раствор, закачиваемый в скважину, выходит из нее и снова должен закачиваться в скважину. Параметры выходящего из скважины раствора отличаются от параметров при его закачке.
Врастворе содержится выбуренная порода в виде отдельных частиц, а также часть породы, например глина, может растворяться в растворе. Кроме того, в него могут попасть минерализованные подземные воды и газ. При воздействии повышенных значений температуры и давления физические свойства раствора могут изменяться.
Вряде случаев часть раствора поглощается пластами и приходится периодически добавлять свежий раствор.
Таким образом, циркуляционная система буровой установки должна быть оборудована устройствами для очистки выходящего раствора от газа, выбуренной породы, песка и ила, а также для восстановления его параметров (вязкости, плотности,
123
водоотдачи и др.). В ряде случаев в зависимости от проходимых пород необходимо изменять свойства раствора или заменять его другим [6].
Циркуляционная система буровых установок включает в себя наземные устройства
исооружения, обеспечивающие промывку скважин путем многократной принудительной циркуляции бурового раствора по замкнутому кругу: насос – забой скважины – насос. Многократная замкнутая циркуляция дает значительную экономическую выгоду благодаря сокращению расхода химических компонентов и других ценных материалов, входящих в состав буровых растворов. Важно также отметить, что замкнутая циркуляция предотвращает загрязнение окружающей среды стоками бурового раствора, содержащего химически агрессивные и токсичные компоненты.
Циркуляционные системы буровых установок состоят из взаимосвязанных устройств и сооружений, предназначенных для выполнения следующих основных функций: приготовления буровых растворов, очистки бурового раствора от выбуренной породы и других вредных примесей, прокачивания и оперативного регулирования физико-механических свойств бурового раствора. В состав циркуляционной системы входят также всасывающие и напорные линии насосов, емкости для хранения раствора
инеобходимых для его приготовления материалов, желоба, отстойники, контрольноизмерительные приборы и др. Циркуляционные системы монтируются из отдельных блоков, входящих в комплект поставки буровых установок. Блочный принцип изготовления обеспечивает компактность циркуляционной системы и упрощает ее монтаж и техническое обслуживание.
Важнейшие требования, предъявляемые к циркуляционным системам буровых установок: качественное приготовление, контроль и поддержание необходимых для данных геолого-технических условий состава и физико-механических свойств бурового раствора. При выполнении этих требований достигаются высокие скорости бурения и в значительной мере предотвращаются многие аварии и осложнения в скважине.
Производительность установок для приготовления бурового раствора определяется из условий, обеспечивающих своевременное пополнение запасов бурового раствора:
Q = V + Vп, |
(6.1) |
где Q – производительность установок для приготовления бурового раствора, м3/ч; V –
объем выбуренной породы за 1 ч, м3; Vп – потери бурового раствора за 1 ч в результате
поглощений в скважине и утечек при очистке бурового раствора от выбуренной породы, м3.
Примерный объем Vp бурового раствора, необходимый для проводки скважины,
без учета поглощений и потерь за счет фильтрации |
|
Vp = Vскв+ Vп', |
(6.2) |
где Vскв – наибольший объем скважины, м3; Vп' – потери бурового раствора при проводке скважины, м3. Потери Vп' возрастают с увеличением объема выбуренной породы и утечек бурового раствора при его очистке.
В забое и в открытом стволе скважины буровой раствор загрязняется обломками выбуренной породы, глинистыми и твердыми частицами. Чрезмерное содержание в нем твердых и грубых глинистых частиц приводит к снижению скоростей бурения. Установлено, что при увеличении содержания твердой фазы в растворе на 1 % показатели работы долот снижаются на 7–10 %. Вследствие абразивного действия твердых частиц ускоряется износ и, соответственно, возрастает расход узлов и деталей насосов, вертлюгов и забойных двигателей. В результате этого увеличиваются трудовые и материальные затраты на ремонтные работы, что отрицательно влияет на техникоэкономические показатели бурения. Исходя из этого очистные устройства должны обеспечить тщательное удаление выбуренной породы и других загрязнений,
124
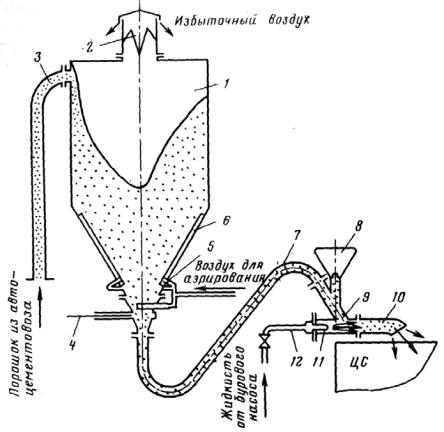
содержащихся в буровом растворе. Опыт показывает, что для поддержания оптимального состава бурового раствора в нем не должны содержаться частицы выбуренной породы, песка и ила размером 5 мкм и более. Пропускная способность очистных устройств должна быть не менее наибольшей подачи насосов.
В числе требований, предъявляемых к циркуляционным системам, важное значение имеют механизация и автоматизация процессов приготовления и очистки буровых растворов [1, 5, 11].
6.2. Устройства для приготовления и утяжеления буровых растворов
Устройства для приготовления и утяжеления буровых растворов по принципу действия делятся на механические и гидравлические. В связи с возрастающим применением порошкообразных материалов в последние годы преимущественное распространение получили гидравлические устройства. По сравнению с механическими глиномешалками они обладают более высокой производительностью, обеспечивают необходимое качество буровых растворов и экономное расходование материалов для их приготовления. Положительно зарекомендовали себя гидроэжекторные смесители блоков приготовления бурового раствора (БПР).
Выносной гидроэжекторный смеситель 9 (рис. 6.1) представляет собой струйный аппарат, в котором для образования гидросмеси порошкообразных материалов используется кинетическая энергия жидкости. Буровые насосы под давлением не более 4 МПа нагнетают жидкость по трубе 12 в сопло 11 смесителя, снабженного сменными штуцерами диаметром 30 мм для работы с глинопорошками и диаметром 20 мм для работы с утяжелителями. Вследствие сужения струи скорость жидкости в сопле увеличивается, а давление падает. Из сопла жидкость с пониженным давлением поступает в камеру всасывания.
Рис. 6.1. Конструктивная схема блока приготовления буровых растворов
125
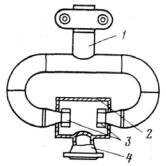
В результате создаваемого разряжения в камеру всасывания из силоса 1 по шлангу 7 засасывается порошкообразный материал, который увлекается жидкостью в камеру смешения и далее в конически расходящийся насадок (диффузор). При прохождении по диффузору скорость потока уменьшается, а давление возрастает,
иполученный раствор по патрубку 10 сливается в приемную емкость циркуляционной системы. За один цикл смешения плотность раствора возрастает на 0,3–0,35 г/см3. При недостаточной плотности полученного раствора проводится повторное смешение. Гидроэжекторный смеситель имеет относительно низкий КПД, однако обладает высокой надежностью благодаря отсутствию подвижных частей.
Блоки для приготовления бурового раствора рассчитаны для работы с бестарными
изатаренными глинопорошками. Основная масса глинопорошков доставляется автоцементовозами и под действием сжатого воздуха перегружается по трубе 3 в силос 1. Перед подачей в гидроэжекторный смеситель порошкообразные материалы разрыхляются воздухом, нагнетаемым в силос по аэродорожкам 6 системы аэрирования 5. Избыточный воздух выносится в атмосферу через фильтр 2, установленный на крышке силоса. Нижняя часть силоса имеет конусообразную форму и снабжена разгрузочным устройством 4, регулирующим подачу материала в гидроэжекторный смеситель. Материалы, используемые в небольших количествах, доставляются в затаренном виде и засыпаются в воронку 8, из которой поступают в камеру смешения гидроэжектора. Воронка снабжена разгрузочным клапаном для регулирования подачи материала.
Гидравлический диспергатор (рис. 6.2) используется для тонкого измельчения твердых и жидких фаз бурового раствора. Он состоит из камеры 2, входной дугообразной трубы 1 и сливного патрубка 4. На концах входной трубы с помощью накидных гаек установлены сменные насадки 3 из твердых сплавов либо металлокерамических материалов. Диаметр насадок выбирают в зависимости от подачи буровых насосов, используемых для нагнетания бурового раствора в диспергатор.
Встречные высокоскоростные потоки раствора, выходящие из насадок 3, приводят
кгидродинамической кавитации. Ультразвуковые колебания, создаваемые в кавитирующем растворе, усиливают диспергирование твердых и жидких фаз.
Вприемных емкостях циркуляционной системы устанавливают гидравлические и механические перемешиватели, обеспечивающие равномерное распределение компонентов бурового раствора и предотвращающие его расслоение.
Рис. 6.2. Гидравлический диспергатор
Гидравлические перемешиватели действуют подобно гидромонитору. Раствор посредством бурового либо центробежного насоса подается в приемный патрубок 1 (рис. 6.3) гидравлического перемешивателя. Оттуда раствор поступает в ствол 2, вращающийся на шарикоподшипниках замкового типа. Между приемным патрубком и стволом установлены уплотнения, предотвращающие утечку и попадание раствора в подшипники. На конце ствола при помощи накидной гайки 3 устанавливается
126
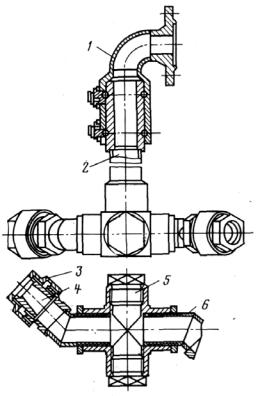
конически сходящаяся насадка 4 для повышения скорости, дальности действия и силы удара струи раствора, выбрасываемого из ствола.
На рис. 6.3 показана конструкция самовращающегося перемешивателя. Реактивная пара сил, возникающая при высокоскоростном истечении раствора из насадок 4, расположенных на противоположно направленных колонках 6, приводит во вращение крестовину 5. Благодаря этому перемешивание и размывание сгустков происходит по всему объему бурового раствора.
Рис. 6.3. Гидравлический перемешиватель
Механический перемешиватель (рис. 6.4), состоящий из мотор-редуктора 1, вала 4 и мешалки 5, устанавливается на раме 2, которая крепится болтами к верхней площадке емкости для бурового раствора. Вал составной конструкции вращается на конических подшипниках 3, установленных в стакане 7 и защищенных от попадания раствора кожухом 6. Мешалка располагается на небольшом расстоянии от дна емкости и при вращении создает потоки, перемешивающие буровой раствор и препятствующие осаждению утяжелителей. Турбинно-пропеллерные мешалки в перемешивателях создают перекрестные потоки, усиливающие перемешивание бурового раствора. Лопастные мешалки, применяемые в перемешивателях, обладают менее эффективным действием [1].
Конструкция оборудования для приготовления буровых растворов зависит от применяемых исходных материалов и химических реагентов. Для сухих порошкообразных материалов требуется лишь тщательное перемешивание и создание условий для полного смачивания твердых частиц. При приготовлении растворов из твердых материалов и перемешивании их с водой применяют механические или гидравлические мешалки. Наиболее прогрессивно и экономично оборудование для приготовления растворов из сухих порошкообразных материалов.
127
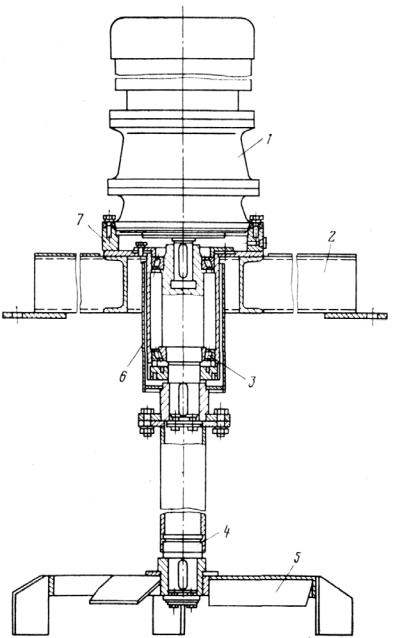
Рис. 6.4. Механический перемешиватель с турбинно-пропеллерной мешалкой
Блок приготовления бурового раствора из порошкообразных материалов состоит из двух резервуаров-силосов с фильтрами, укрепленных на основании. В нижней части силосы снабжены разгрузочным и аэрирующим устройствами. Для приготовления раствора открывается разгрузочное устройство, и порошок по шлангу поступает в гидромешалку.
Гидравлическая мешалка снабжена воронкой для загрузки химических реагентов и камерой смешения, в которую подаются порошок и под давлением 0,7–1,5 МПа жидкость от бурового насоса. В камеру смешения жидкость поступает через насадку, за счет чего образуется вакуум и засасывается порошок и химические реагенты. Порошок смешивается с жидкостью, образуя пульпу, поступающую в приемные резервуары буровых насосов.
Приемный блок циркуляционной системы – это резервуар, из которого раствор подается в буровые насосы. Он также служит для хранения резервного объема бурового раствора. В зависимости от глубины и конструкции скважины в циркуляционной
128
системе применяют от двух до пяти приемных блоков. Блок представляет собой прямоугольный металлический резервуар объемом около 40 м3, разделенный внутренней перегородкой на две равные части, что позволяет использовать одну половину резервуара для приготовления бурового раствора, не прекращая циркуляции его через скважину. Резервуар смонтирован на раме-салазках и оборудован двумя гидравлическими перемешивателями раствора.
Для хранения жидких химических реагентов и эмульсий для обработки растворов служит блок хранения химических реагентов, представляющий собой прямоугольный резервуар вместимостью 12 м3 или цилиндрический объемом 20 м3. Блоки соединяют между собой растворопроводами с шаровыми компенсаторами [5, 6].
6.3. Очистные устройства циркуляционной системы
Очистка буровых растворов осуществляется путем последовательного удаления крупных и мелких частиц выбуренной породы и других примесей, содержащихся в поступающем из скважины буровом растворе. Для полной очистки буровых растворов циркуляционные системы оборудуются комплексом очистных устройств. Первичная очистка проводится вибрационными ситами, посредством которых удаляются крупные частицы (размером более 75 мкм). Мелкие частицы вредных примесей удаляются посредством пескоотделителя (40 мкм), илоотделителя (25 мкм) и центрифуги (5 мкм), используемых на последующих ступенях очистки.
На вибрационных ситах частицы выбуренной породы просеиваются через сито под действием вибраций, которые создаются эксцентриковым (рис. 6.5, а) либо инерционным (рис. 6.5, б) вибратором. Привод вибратора состоит из электродвигателя и клиноременной передачи. В последние годы преимущественно распространены инерционные вибраторы, позволяющие сравнительно просто регулировать амплитуду колебаний путем изменения положения дебалансов (см. рис. 6.5, б). Частицы бурового раствора, превышающие размеры ячеек сетки вибросита, оседают на ней и по транспортному желобу сбрасываются в отвал (шламовый амбар). Очищенный раствор, пройдя через ячейки сетки, поступает в приемные емкости циркуляционной системы.
По числу вибрирующих рам различают одинарные, сдвоенные и строенные вибросита с одно-, двух- и трехъярусными горизонтально либо наклонно расположенными ситами (рис. 6.5, в). Вибрирующие рамы комплектуются индивидуальными вибраторами и выравнивателями для равномерного распределения раствора по ширине сита. В многоярусных виброситах буровой раствор из скважины поступает на верхнее сито с более крупными ячейками, а затем на нижние с меньшими ячейками. В результате возрастает производительность на единицу поверхности сита и одновременно уменьшается его износ.
Для буровых растворов высокой вязкости эффективность очистки возрастает с увеличением амплитуды вибраций и угла наклона сита. Многоярусные вибросита снабжаются устройством для независимой регулировки угла наклона сит. Для смягчения ударов и защиты от больших нагрузок виброрама подвешивается к опорной раме на спиральных пружинах либо резиновых амортизаторах. Колебание виброрамы происходит по замкнутой круговой либо эллиптической траектории. Предпочтительно встречное движение виброрамы и бурового раствора, способствующее самоочистке сита. Для восстановления пропускной способности вибросита застрявшие частицы удаляются путем периодической промывки сетки водой либо продувкой сжатым воздухом.
Пропускная способность и глубина очистки бурового раствора зависят от световой поверхности и размера ячеек сетки. Наибольшую световую поверхность имеют плетеные сетки из стальных проволок либо капроновых нитей. Долговечность сетки зависит от износостойкости и коррозионно-усталостной прочности используемых проволок и нитей, а также от равномерности натяжения сетки в вибрирующей раме.
129
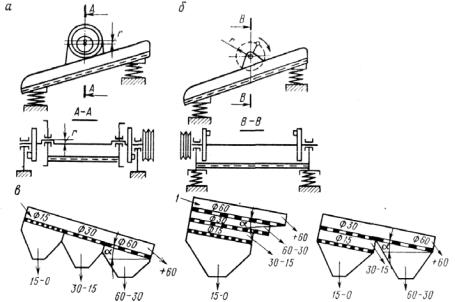
С увеличением толщины проволок возрастают их прочность и износостойкость. Однако при этом уменьшается световая поверхность сетки и, соответственно, пропускная способность вибросита.
Рис. 6.5. Конструктивные схемы вибросит
Ввиброситах применяются сетки, у которых размеры ячеек в свету составляют: 0,16×0,16; 0,2×0,2; 0,25×0,25; 0,4×0,4; 0,9×0,9 мм. В ряде стран сортамент сеток устанавливается по числу отверстий, приходящихся на единицу площади сетки. При выборе размера ячеек сетки учитывают необходимую степень очистки, пропускную способность вибросита и плотность бурового раствора.
Квибрирующей раме сетка крепится при помощи кассеты либо двух барабанов, расположенных по концам рамы. На один из барабанов сетка наматывается с запасом длины, используемым для перепуска поврежденных при эксплуатации участков рабочей поверхности сетки. Кассетное крепление обеспечивает равномерное натяжение сетки в продольном и поперечном направлениях. Волнистость рабочей поверхности сетки и неплотное его примыкание к вибрирующей раме приводят к преждевременным повреждениям. Вибросита лучших образцов позволяют полностью очистить буровые растворы от частиц размером более 0,125 мм и удалить при этом до 50 % выбуренной породы.
Последующая более тонкая очистка буровых растворов осуществляется гидромеханическим способом. Для этого в песко- и илоотделителях применяются конические гидроциклоны.
Вгидроциклон 1 (рис. 6.6) буровой раствор подается под давлением по питающей насадке 4. Благодаря тангенциальному расположению питающей насадки и высокоскоростному истечению буровой раствор интенсивно вращается относительно оси гидроциклона. Наиболее крупные и тяжелые частицы, содержащиеся в буровом растворе, отбрасываются центробежными силами во внешний поток раствора, образующийся в пристенной зоне конуса 2. Опускаясь по винтообразной траектории до вершины конуса, частицы удаляются через шламовую насадку 3 в находящийся под гидроциклоном шламосборник.
Мелкие частицы, обладающие недостаточной для преодоления сопротивления среды центробежной силой, оказываются во внутреннем восходящем потоке, создаваемом в результате образования вдоль оси гидроциклона воздушно-жидкостного
130