
книги / Машины и оборудование нефтяных и газовых промыслов. Силовые приводы машин и оборудования нефтяных и газовых промыслов
.pdf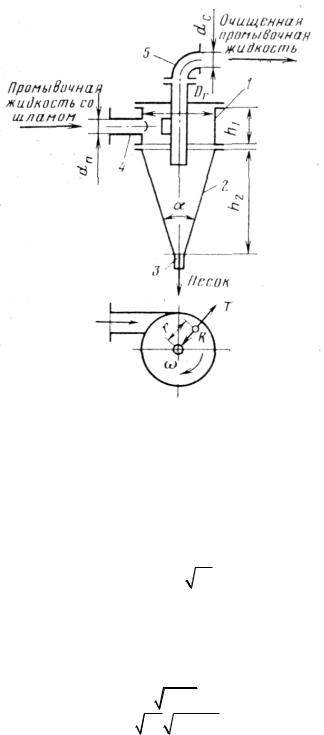
столба пониженного давления. Восходящий поток очищенного бурового раствора направляется к сливной насадке и по патрубку 5 поступает в приемную емкость циркуляционной системы.
Рис. 6.6. Конструктивная схема гидроциклона
Технологические и конструктивные параметры гидроциклонов рассчитываются по формулам, полученным различными авторами на основе определенных допущений. Отсутствие однозначных зависимостей обусловлено многообразием факторов, влияющих на показатели работы гидроциклонов. Для расчета пропускной способности гидроциклонов, используемых в песко- и илоотделителях, наиболее приемлема эмпирическая формула
Qг k1dпdсDг pв , |
(6.3) |
где Qг – пропускная способность гидроциклона, л/с; k1 – эмпирический коэффициент, k1 = 0,12; dп и dс – диаметры питающей и сливной насадок, см; Dг – диаметр гидроциклона, см; pв – давление на входе в гидроциклон, МПа.
Диаметр граничного зерна δ (в мкм) с достаточной для практических расчетов точностью определяется по формуле
δ k2 |
|
|
dс |
DгТп |
|
, |
(6.4) |
||
d |
|
4 p |
ρ |
|
ρ |
|
|||
|
ш |
т |
ж |
|
|||||
|
|
в |
|
|
|
где k2 – эмпирический коэффициент, k2 ≈ 0,5; dc, dш – диаметры сливной насадки гидроциклона и шламовой насадки, см; Тп – содержание песка в исходном продукте, %; рв – давление на входе в гидроциклон, МПа; ρт и ρж – плотность твердой и жидкой фаз раствора, г/см3.
Диаметр граничного зерна характеризует тонкость очистки, обеспечиваемой гидроциклоном. Сепарации поддаются частицы, диаметр которых больше диаметра граничного зерна. Частицы меньшего диаметра остаются в растворе и вместе с ним выносятся через сливной патрубок. Из формул (6.3) и (6.4) следует, что с увеличением диаметра гидроциклона возрастает его пропускная способность, а тонкость очистки
131
ухудшается вследствие увеличения диаметра граничного зерна. В связи с этим диаметр гидроциклона в илоотделителях меньше диаметра гидроциклона в пескоотделителях.
На качество очистки существенно влияют диаметры питающей, шламовой и сливной насадок, высота цилиндрической части и угол конуса гидроциклона. По опытным данным приняты следующие оптимальные соотношения:
–диаметр питающей насадки dп = (0,125…0,25)Dг;
–диаметр сливной насадки dс = (0,25…0,50)Dг;
–диаметр шламовой насадки dш = (0,15…0,45)dс;
–высота цилиндрической части гидроциклона h1 = (1,0…1,2)Dг;
–высота конической части гидроциклона h2 = Dг / (2 tg α/2).
Угол конуса выбирается в зависимости от диаметра гидроциклона и составляет 15°–20°. При чрезмерном увеличении или уменьшении угла конуса снижается степень
извлечения частиц твердой фазы и глины Е, характеризуемая отношением |
|
|||
Е = |
П П0 |
100 %, |
(6.5) |
|
П |
||||
|
|
|
где П и П0 – содержание твердой фазы и глины в буровом растворе соответственно до и после его очистки, г/л.
На эффективность очистки существенно влияет соотношение диаметров сливной и шламовой насадок, а также давление на входе в гидроциклон. Оптимальное соотношение диаметров сливной и шламовой насадок выбирается в зависимости от физико-механических свойств бурового раствора и удаляемых частиц. Давление на входе в гидроциклон зависит от подачи шламовых насосов, нагнетающих буровой раствор в песко- и илоотделитель, и диаметра питающей насадки. Давление на входе в гидроциклон должно быть в пределах 0,4–0,5 МПа. При этом обеспечиваются необходимая степень очистки и минимальные потери бурового раствора, возникающие в результате его утечки через шламовую насадку гидроциклона.
Требования, предъявляемые к тонкости очистки буровых растворов, ограничивают диаметр и, соответственно, пропускную способность гидроциклонов. Ввиду этого в песко- и илоотделителях устанавливают несколько параллельно действующих
гидроциклонов, число которых определяется по формуле |
|
nг ≥ Q / Qг, |
(6.6) |
где Q и Qг – пропускная способность песко- и илоотделителя и гидроциклонов, л/с. Пескоотделители (рис. 6.7) состоят из четырех гидроциклонов диаметром 150
мм, расположенных в один ряд.
В илоотделителях (рис. 6.8) используются шестнадцать гидроциклонов диаметром 75 мм, расположенных в два ряда. Гидроциклоны, используемые в пескоотделителях и илоотделителях, в основном различаются размерами одноименных деталей. Корпус гидроциклонов имеет разъемную конструкцию и состоит из силуминовых литых цилиндра, конуса и обоймы для шламовой насадки. Для предохранения от износа и коррозии внутренние поверхности корпуса, контактирующие с буровым раствором, покрывают резиновым чехлом. Насадки изготовляют из износостойких сталей и сплавов.
Гидроциклоны 2 (см. рис. 6.7 и 6.8) устанавливают на сварной раме 3. Буровой раствор поступает в гидроциклоны из общего коллектора 5. Очищенный раствор по отводам 6 поступает в сливной коллектор 1. Частицы выбуренной породы и других примесей поступают из гидроциклонов в общий шламосборник 4, в донной части которого установлена труба 7 для выгрузки шлама.
Центрифуги предназначены для извлечения тонкодисперсных частиц утяжелителя из буровых растворов. Основная рабочая часть центрифуги – барабан (ротор) с дырчатыми фильтрующими стенками, вращающийся в неподвижном кожухе. Разделение твердых частичек в центрифуге происходит под действием центробежных
132
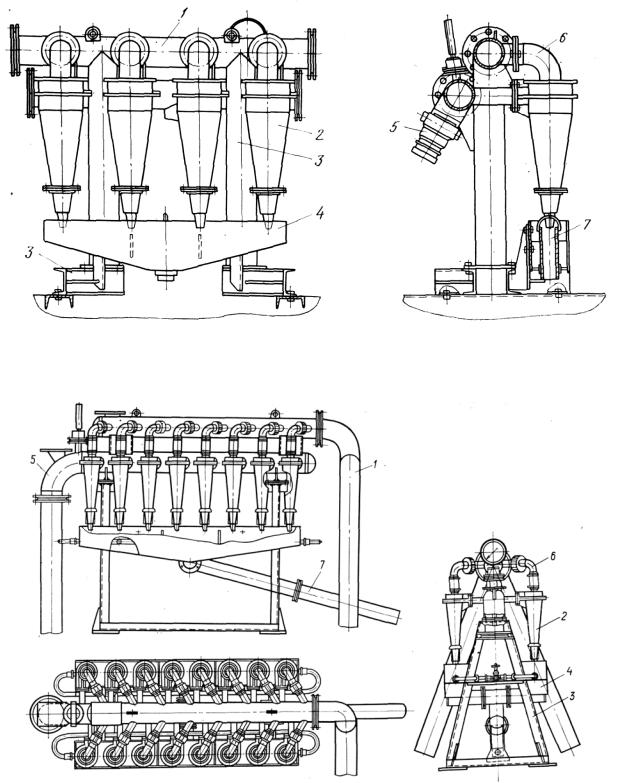
сил. Крупные частицы выбрасываются через отверстия в стенке барабана и накапливаются в кольцевом пространстве между кожухом и барабаном.
Рис. 6.7. Пескоотделитель
Рис. 6.8. Илоотделитель
Очищенный раствор поступает в сливную горловину, расположенную под барабаном центрифуги. Возможности разделения увеличиваются с повышением частоты вращения барабана центрифуги [1, 9, 11].
133
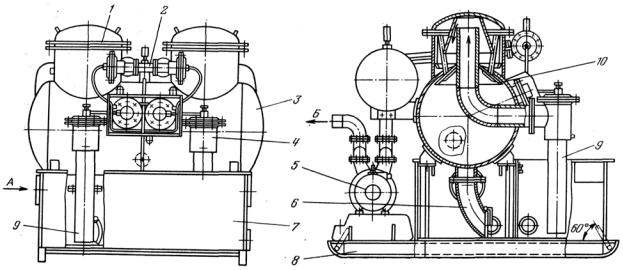
6.4. Дегазаторы
Дегазаторы бурового раствора применяют в циркуляционных системах в случае поступления в буровой раствор газа при проходке газосодержащих пород или в буровых установках для разведочного бурения при проводке скважин в неисследованных породах. При больших количествах поступающего газа применяют газоотделители и сепараторы или дегазаторы различных конструкций, которые устанавливают до вибросит для первичного удаления газа. Для вторичного удаления оставшегося газа из раствора предназначены вакуумные дегазаторы.
Вакуумный дегазатор (рис. 6.9) состоит из металлической рамы 8, на которой смонтирован резервуар 7. Раствор, содержащий газ, из циркуляционной системы поступает (стрелка А) в этот резервуар. Над резервуаром смонтирована цилиндрическая камера 3, разделенная в середине поперечной перегородкой. Над каждой частью резервуара расположены две дегазационные камеры 1, которые через клапанразрядник 2 соединены с всасывающей линией вакуумного насоса 5.
Рис. 6.9. Вакуумный дегазатор
Дегазатор является аппаратом двойного действия. Клапан-разрядник 2 поочередно соединяет дегазационные камеры 1 с вакуумной линией насоса, за счет чего в одной из них создается разряжение, под действием которого раствор с газом из резервуара 7 по всасывающему патрубку 9 с приемным клапаном 4 поочередно поступают в одну из камер 1, и там происходит отделение раствора от газа. Чистый раствор сливается по сепарационному конусу 10 в отсек цилиндрической камеры 3, а газ отсасывается вакуум-насосом (стрелка Б). После того как камера полностью заполнится раствором, происходит переключение клапана-разрядника, и вакуумный насос начинает откачивать газ из другой камеры, а из заполненной камеры очищенный от газа раствор сливается по выкидному патрубку 6 в приемный резервуар буровых насосов [6, 10].
6.5. Всасывающие линии и манифольд
Очищенный буровой раствор посредством подпорных насосов либо самовсасыванием подается из приемных резервуаров циркуляционной системы в буровые насосы. Всасывающим трубопроводом или линией всасывания называют участок трубопровода, по которому подводится раствор из опорожняемой емкости к насосу.
Всасывающие линии имеют важное значение в обеспечении заданных технических показателей буровых насосов. Эффективность действия их определяется полнотой
134
заполнения жидкой средой рабочих камер насоса. При неполном заполнении рабочих камер при всасывании уменьшается подача буровых насосов, а также снижаются прочность и долговечность всей насосной установки из-за гидравлических ударов, возникающих при обратном ходе поршней. Для полного заполнения рабочих камер насоса всасываемая жидкость должна безотрывно следовать за поршнем. Надо иметь в виду, что при отрыве всасываемой жидкости от поршня в рабочих камерах насоса образуется вакуум, в результате которого возникает кавитация, способная привести к полному срыву подачи. Таким образом, для обеспечения безотрывного перемещения всасывающей жидкости за поршнем и предотвращения кавитации давление на входе в насос должно быть выше давления насыщенных паров жидкой среды, pв > pп.
В зависимости от компоновки циркуляционной системы буровые насосы располагаются выше или ниже уровня бурового раствора в емкости. Предпочтительнее располагать насос ниже уровня бурового раствора в опорожняемой емкости. В этом случае насосы работают с подпором, определяемым разностью значений высоты бурового раствора в опорожняемой емкости и центра тяжести сечения входа в насос. Если буровой насос располагается выше уровня раствора в емкости, то высота установки его ограничивается допускаемой вакуумметрической высотой всасывания, при которой обеспечивается работа насоса без изменения основных технических показателей.
Высоту всасывания вычисляют на основании уравнения Бернулли для потока жидкости в сечениях za, совпадающих с уровнем раствора в опорожняемой емкости, и в сечении zв, совпадающем с входом в насос:
ρgz |
|
p |
ρ |
2 |
|
p |
ρ |
2 |
|
p |
p . |
(6.7) |
а |
а ρgz |
в |
в p |
|||||||||
|
а |
|
2 |
в |
|
2 |
н |
г |
к |
|
||
|
|
|
|
|
|
|
|
|
|
|
Скорость υa опорожнения емкости можно принять равной нулю, а давление ра над свободной поверхностью жидкости – равным давлению р0 окружающей среды. Учитывая, что высота всасывания z = zв – za, из уравнения (6.3) получим
|
p p ρ |
2 |
|
|
|
|
|
|
в p p p |
|
|
||||
z |
0 в |
2 |
и |
г |
к |
, |
(6.8) |
|
|
|
|
||||
|
|
ρg |
|
|
|||
|
|
|
|
|
|
|
где рв – давление на входе в насос, Па; υв – скорость бурового раствора на входе в насос, м/с; ρ – плотность бурового раствора, кг/м3; g – ускорение свободного падения, м/с2; ∆ри – потери давления на преодоление инерции бурового раствора (определяются массой и ускорением бурового раствора во всасывающей трубе), Па; ∆рг – потери давления на преодоление гидравлических сопротивлений всасывающей трубы и приемного коллектора насоса, Па; ∆рк – потери давления на преодоление сопротивления клапана насоса, Па.
Пользуясь уравнением (6.8), можно определить высоту всасывания, если приравнять давления рв и рп. Кроме того, при заданной геометрической высоте всасывания и допустимом перепаде давления р0 – рп можно рассчитать предельно допустимую подачу насоса и минимально необходимый диаметр всасывающей трубы, от которых зависят инерционные ∆ри и гидравлические ∆рг потери всасывающей линии. Для снижения инерционных потерь давления рекомендуется на всасывающей линии устанавливать воздушный компенсатор. При недостаточном давлении рв на входе в насос и работе с буровыми растворами высоких значений плотности и вязкости всасывающие линии снабжаются подпорными насосами.
135
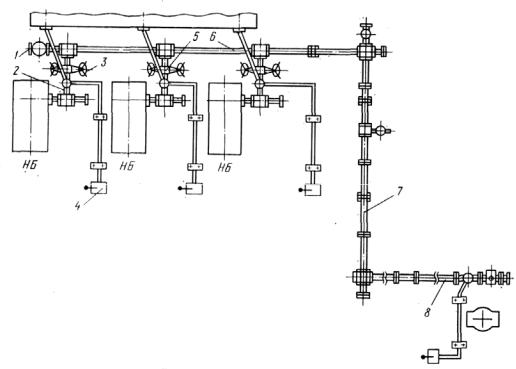
Длина всасывающей линии должна быть минимально возможной, а диаметр используемых труб – не менее диаметра приемного коллектора бурового насоса. На свободном конце всасывающей линии устанавливают сетчатый фильтр, световая площадь которого должна быть не менее площади сечения труб, используемых в линии всасывания. Всасывающий трубопровод крепят к насосу посредством фланцевого соединения, уплотняемого листовой прокладкой из резины. Неточность изготовления и монтажа всасывающих линий компенсируется подвижными соединительными муфтами (компенсаторами). Для защиты бурового раствора от промерзания всасывающие линии покрывают теплоизоляционным материалом. Запасные емкости циркуляционной системы с буровым раствором и химическими реагентами подключаются к всасывающей линии с помощью труб сравнительно небольшого диаметра, снабженных клиновыми задвижками или поворотными шиберами.
Манифольдом или линией нагнетания называется участок трубопровода между буровым насосом и вертлюгом, по которому буровой раствор подается в бурильную колонну. Буровые насосы, входящие в комплект циркуляционной системы, имеют индивидуальные всасывающие линии и общий манифольд. Реже при небольшом удалении от оси скважины буровые насосы снабжаются индивидуальными манифольдами.
Манифольд (рис. 6.10) состоит из трубной обвязки 6 буровых насосов, трубной обвязки 8 вышечного блока; трубопровода 7, соединяющего обвязки в насосном и вышечном блоках; вспомогательного трубопровода 1; пультов управления 4. Трубная обвязка насосов предназначена для подачи бурового раствора по отводам 2 насосов к распределителю с дроссельно-запорным устройством 3 и 5. Отводы состоят из набора трубных секций и переходных колен, необходимых для соединения нагнетательного патрубка насоса с распределителем. На отводах устанавливают задвижки для слива бурового раствора, а также манометры с предохранительным устройством. Задвижки 3 распределителя служат для подачи бурового раствора в скважину либо в перемешивающие и очистные устройства циркуляционной системы.
Рис. 6.10. Схема манифольда
136
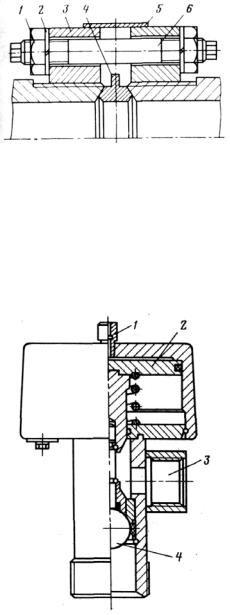
Трубная обвязка 8 вышечного блока состоит из стояка и распределительнозапорного устройства, позволяющего подавать буровой раствор в вертлюг либо превентор, а также откачивать его от цементировочного агрегата. Стояк представляет собой набор трубных секций, имеющих линзовые соединения (рис. 6.11). К стояку крепится изогнутое колено для присоединения бурового рукава, по которому раствор подается в вертлюг.
Рис. 6.11. Линзовые соединения:
1 – гайка; 2 – шайба; 3 – фланец; 4 – линза; 5 – кожух; 6 – шпилька
Для плавного перевода бурового насоса с холостого режима работы на рабочий применяют дроссельно-запорное устройство (рис. 6.12), которое приводится в действие сжатым воздухом, поступающим от компрессорной станции буровой установки. Управление этим устройством осуществляется четырехклапанным краном, установленным на пульте управления.
Рис. 6.12. Дроссельно-запорное устройство:
1 – штуцер для подвода сжатого воздуха; 2 – пневматический цилиндр с поршнем; 3 – выкид для раствора; 4 – шаровой клапан
Трубные секции манифольда соединяются при помощи быстроразъемных замковых соединений (рис. 6.13). Между отдельными блоками буровой установки трубы манифольда соединяются монтажными компенсаторами (рис. 6.14), обеспечивающими угловое смещение соединяемых труб на 10° и линейное их смещение до 200 мм.
137

Рис. 6.13. Быстроразъемное замковое соединение:
1 – полухомут; 2, 4 – патрубки; 3 – армированная манжета; 5 – шпилька; 6 – гайка
Рис. 6.14. Монтажный компенсатор:
1 – седло; 2 – уплотнение; 3 – шар; 4 – кольцо; 5 – коронка; 6 – цилиндр; 7 – втулка; 8 – манжета; 9 – накидной замок
Крепление манифольда к основанию буровой установки и вышке осуществляется при помощи хомутовых соединений. В технической характеристике манифольдов указаны значения рабочего и пробного давления, диаметр и толщина стенок труб, а также масса манифольда. Манифольды изготовляют с рабочим давлением 20, 25, 32 и 40 МПа в зависимости от класса буровой установки. Пробное давление составляет соответственно 30, 38, 48 и 60 МПа. Трубы, используемые в манифольдах, имеют диаметр проходного отверстия 80, 100 и 125 мм [1].
6.6. Состав и технологическая схема циркуляционной системы
Устройства для приготовления и очистки бурового раствора располагаются в виде отдельных блоков, взаимодействующих согласно технологической схеме (рис. 6.15).
Глинопорошки и порошкообразные утяжелители хранятся в силосах 1 блока приготовления промывочного раствора (БПР). Порошкообразные химические реагенты, затаренные в мешки, складируются на крытой площадке 2. В блок приготовления промывочного раствора входят также дозатор, гидроэжекторный смеситель 4, диспергатор 3 и механический смеситель 8. Загрузка порошкообразных материалов в силосы и подача их в гидроэжекторный смеситель осуществляются пневмотранспортом. Приготовленный для промывки скважины буровой раствор поступает в резервуар 9, снабженный гидравлическими 17 и механическими 18 перемешивателями. Подпорными
138
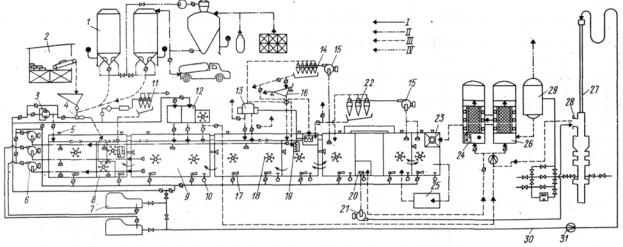
насосами 6 готовый раствор из резервуара 9 подается на прием буровых насосов 7, нагнетающих его по манифольду 30 в бурильную колонну 27.
Рис. 6.15. Технологическая схема циркуляционной системы
(линии: I — нагнетательная; II — всасывающая; III — сливная; IV — воздушная)
Из скважины буровой раствор по устьевому желобу 28 поступает в блок очистки, включающий два вибросита 26, отстойник 23, гидроциклонные пескоотделитель 22 и илоотделитель 14, центрифугу 13. Для подачи бурового раствора в пескоотделитель 22 и илоотделитель 14 используются центробежные шламовые насосы 15. Специальное вибросито 16 с мелкоячеечной сеткой служит для разделения частиц утяжелителя и глины. Кроме того, для удаления избытка глины при утяжелении бурового раствора предусмотрено эжекторно-гидроциклонное устройство 11. Для подачи раствора в центрифугу 13 служит винтовой насос 19. При наличии пластового газа буровой раствор направляется в блок очистки от газа, в состав которого входят газовый сепаратор 29 и дегазатор 25.
В циркуляционную систему также входят блок 12 обработки промывочного раствора, блок 6 подпорных насосов и резервуарный блок, состоящий из нескольких металлических емкостей, часть которых имеет отдельные отсеки с механическими и гидравлическими перемешивателями. Люки 5 служат для очистки резервуаров от скопившихся отходов бурового раствора. Мерный отсек 20 и центробежный насос 21 используются для долива скважины при подъеме бурильной колонны.
При спуске труб в скважину отсек 20 используется для контроля объема вытесняемого бурового раствора. Для контроля процесса промывки скважин применяются уровнемеры 10, установленные на всех резервуарах, расходомеры 31 и манометры, регистрирующие давление буровых и подпорных насосов, а также в камере эжекторного гидросмесителя и входных гидроциклонов. Газосодержание и плотность бурового раствора на приеме буровых насосов и при сливе из скважины контролируются приборами, расположенными на панели 24. Блок приготовления промывочного раствора снабжен гидравлическим измерителем массы порошкообразных материалов. Частота вращения центрифуги контролируется тахометром [1].
6.7. Цементировочные агрегаты
Спуск обсадных труб и цементирование скважин – заключительные сложные и наиболее ответственные операции при бурении скважин. От успешности цементирования зависят продолжительность и нормальная эксплуатация скважины, а
139
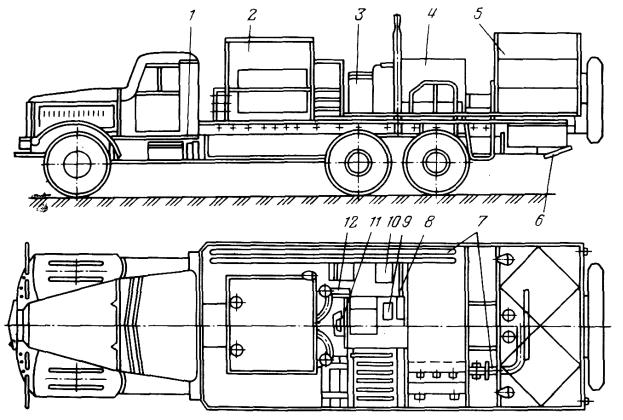
если скважина разведочная, то и правильность оценки пласта и перспективности изучаемого месторождения.
Сложность этих работ обусловливается большими массой и диаметрами спускаемых труб (колонны диаметром 279–305 мм имеют массу до 300 т), высокими значениями давления (более 25–30 МПа), возникающего при подъеме цементного раствора за колоннами, спущенными на глубину более 5000 м, а также трудностью определения точного количества жидкости, которое необходимо закачать в трубы для продавливания цементного раствора.
Особенной ответственности требуют эти работы при спуске труб в осложненных скважинах, где не исключается возможность их прихвата. Для восстановления циркуляции жидкости в таких скважинах, как правило, необходимо создавать большие значения давления, при освобождении прихваченных труб – большие натяжки.
Скважины цементируют с помощью агрегатов, смесительных машин и другого вспомогательного оборудования.
Цементировочный агрегат 3ЦА-400 (рис. 6.16) предназначен для цементирования глубоких скважин. На шасси 1 автомобиля установлен цементировочный трехпоршневой насос 4, расположенный между замерным баком 5 и двигателем 2. Насос приводится через редуктор 8, коробку передач 3 (КПП) валами 9 и 11. Он имеет разветвленную приемную (всасывающую) линию 7, соединяющую его с замерным баком через задвижку и позволяющую осуществлять двусторонний забор цементного раствора. Нагнетательная 50-миллиметровая линия 6 высокого давления при помощи быстродействующих соединений легко присоединяется к заливочной головке, установленной на устье скважины.
Рис. 6.16. Цементировочный агрегат 3ЦА-400
Цементировочный насос обычно снабжается сменными втулками нескольких диаметров для изменения подачи и давления. Мерники агрегата служат для измерения объема закачиваемой жидкости в скважину. Управление всеми механизмами агрегата
140