
книги / Усталость крупных деталей машин
..pdfРезультаты испытаний на усталость образцов (б = 200 и 50 мм) при изгибе по симметричному циклу
|
|
|
|
а_, |
(МПа) |
|
|
|
|
|
Сечение |
образцов |
|
|
|
|
Образцы |
|
|
|
|
||
|
образцов, |
|
с упроч |
|
с упроч |
||
|
|
|
мм |
неупроч- |
неупроч- |
||
|
|
|
|
ненных |
нением |
ненных |
нением |
|
|
|
|
|
обкаткой |
|
обкаткой |
Гладкие |
|
2 0 0 X 2 0 0 |
145 |
— |
— |
— |
|
С |
открытой |
канавкой |
2 0 0 X 3 0 0 |
95 |
140 |
1,53 |
1,00 |
R = |
25 (рис. |
36) |
|
|
|
|
|
С |
опорами |
на валики |
200Х 300 |
55 |
65 |
2,63 |
2,23 |
R = |
25 (рис. |
37) |
|
|
|
|
|
Гладкие |
|
5 0 X 7 5 |
165 |
— |
— |
— |
|
С |
открытой |
канавкой |
5 0 X 7 5 |
95 |
35 |
1,73 |
1,22 |
R = |
6,25 (рис. 36) |
|
|
|
|
|
|
С |
опорами |
на валики |
5 0 X 7 5 |
75 |
90 |
2,20 |
1,83 |
R = |
6,25 (рис. 37) |
|
|
|
|
|
Если ста и а т обозначают соответственно амплитуду и среднее напряжение асимметричного цикла, то приведенное напряжение (или напряжение, соответствующее амплитуде симметричного
цикла) будет аИ? = сга -f- ф0сгт , где ф<, — коэффициент влияния асимметрии цикла, равный отношению изменения предельной амплитуды цикла к соответствующей величине изменения среднего напряжения цикла. Величина коэффициента фа может быть при нята для нашего случая не более 0,1. Имея в виду малую вели чину этого коэффициента, а также малую величину среднего напряжения цикла, можно пренебречь их произведением, т. е.
величиной ф„сгт г» 0,015сгтах, и считать ст"? = <ха = 0,85<ттах* Э т о й формулой пользовались для подсчета приведенных напря жений при испытаниях на усталость пластин, зажатых между валиками. При этом момент сопротивления сечения больших
пластин определяли из расчета Л = 175 мм.
Принятый способ расчета дает результаты, существенно отли чающиеся от тех, которые получились бы при предположении, что высота сечения большой пластины нетто равна 150 мм и что валики не препятствуют деформированию выточек на пластинах, а следовательно, имеет место симметричный цикл изменения напряжений.
Действительно, |
|
о"? = 0,85 |
о'_хл; 0,62о'_г |
Аналогичный расчет применяли и для пластин сечением 50x75 мм, защемленных в валиках.
Ш
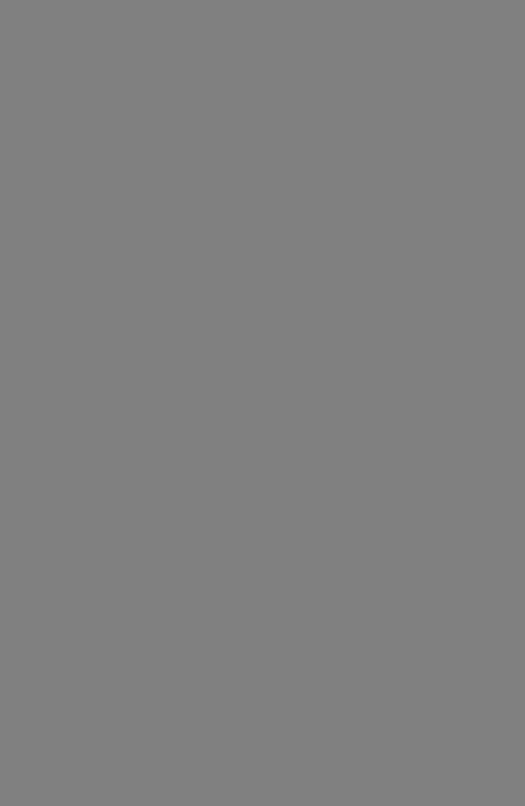
Следует указать, что аналогичная закономерность отмечалась авторами и при испытании пластин, зажатых по концам между плоскими опорными плитами (см. гл. IV).
В |
результате проведенных испытаний установлено: |
1. |
Предел выносливости пластин толщиной 200 мм, зажатых |
ме^кду валиками, снижается в 2,5 раза по сравнению с пределом выносливости гладких пластин. Аналогичное снижение (но в не сколько меньшей степени) установлено и при испытаниях пластин сечением 50x75 мм.
2. Увеличение толщины пластин с 50 до 200 мм сопровождается существенным снижением их предела выносливости в условиях
контакта |
с цилиндрическими валиками (с 75 до 55 МПа, т. е. |
на 36%). |
Значение коэффициента К а в зоне контакта пластины |
сваликами при увеличении размера пластины (с 50 до 200 мм) повышается с 2,20 до 2,63.
3.Канавка в виде выкружки радиусом 25 мм в пластине тол щиной 200 мм вызывает снижение предела выносливости пластины
с145 до 95 МПа. Аналогичная канавка в пластинах толщиной 50 мм (радиус канавки 6,25 мм) приводит к снижению предела выносливости пластин с 165 до 95 МПа.
4.Предел выносливости гладких образцов (в отличие от об разцов с концами, зажатыми между валиками) с увеличением их толщины с 50 до 200 мм изменяется незначительно (соответственно 165 и 145 МПа).
5.Упрочняющий наклеп шариками контактных поверхностей пластин с валиками повысил сопротивление усталости пластин
обоих размеров (50 и 200 мм) на величину около 20%. При этом установлено значительное увеличение долговечности пластин
врезультате наклепа зон контакта.
6.Упрочняющий наклеп шариками открытых канавок (без опор на валики) оказался эффективным средством повышения сопротивления усталости пластин в местах концентрации напря
жений (увеличение в результате обкатки канавок на 42% для образцов толщиной 50 мм и на 47% для образцов толщиной 200), т. е. эффективность наклепа в данном случае оказалось более значительной, чем при наклепе образцов, защемленных по концам.
7. Проведенные исследования позволяют рекомендовать при менение упрочняющего поверхностного наклепа контактных по верхностей узла сочленений ригелей и стоек для случаев, анало гичных рассмотренному.
5. ВЫБОР ПАРАМЕТРОВ ДЕФОРМАЦИОННОГО УПРОЧНЕНИЯ СТУПЕНЧАТЫХ ВАЛОВ
Сопротивление усталости при изгибе или кручении ступенчатых валов значительно понижается в зонах галтельного перехода од ного сечения к другому. Наиболее эффективным средством повы-
Рис. 42. Схема к выбору разме |
Рис. 43. Схема к определению |
ров ролика для упрочнения гал |
степени и глубины деформации |
телей ступенчатых валов |
при упрочнении галтелей сту |
|
пенчатых валов |
шения прочности валов в зонах галтелей является обработка этих зон ППД. Систематические исследования этого метода, прове денные в ЦНИИТМАШе, позволили рекомендовать систему основ ных параметров, определяющих рациональное проведение про цесса и его высокую эффективность [13].
Отличительной особенностью и большим достоинством метода является применимость его для галтельных переходов весьма малых радиусов (R d < 0,02). Важным в методе ЦНИИТМАШа является отсутствие строгих допусков на радиус галтельного перехода при изготовлении валов под упрочняющую обработку. При этом наименьшее его значение не ограничено.
Способ упрочнения малых галтелей применим для стальных и чугунных валов любых размеров, вплоть до диаметров в сотни
миллиметров. При этом эффективность способа |
не уменьшается |
с увеличением размеров валов. |
|
Большим преимуществом метода упрочнения |
малых галтелей |
является существенное сокращение поводок валов по сравнению с обычными поводками, возникающими при упрочнении валов с галтелями больших радиусов. Галтели упрочняют на металло режущих станках с помощью обкатывающих приспособлений.
Метод может быть применен в сочетании с химико-термической обработкой или индукционной закалкой, которые выполняют для повышения износостойкости шеек валов.
Поиски оптимальных режимов упрочнения галтелей произ водили в ЦНИИТМАШе на основе испытаний на усталость с ис пользованием большого парка испытательных машин, позволив ших определять сопротивление усталости образцов значитель ных размеров ( 0 до 400 мм).
Ниже приведены основные параметры, определяющие режим упрочняющего наклепа.
Максимальную глубину деформированного слоя а целесооб разно создавать на том участке галтельного перехода, где кон центрация наружных рабочих напряжений является наибольшей.
Максимальные напряжения при изгибе ступенчатого вала возни кают вблизи начальной части галтели и тем ближе к ее началу, чем меньше D d и больше г d (рис. 42). Центральные углы ф°, соответствующие наибольшим напряжениям по профилю гал тели, находятся в диапазоне от 8 до 24°
Нецелесообразно выбирать исходный профиль галтели радиу сом г большим, чем радиус R обкатывающего ролика (шарика). Предположим, что г > R, тогда вдавливание инструмента вызо вет изменение исходного контура галтели до положения, обозна ченного на рис. 42 штриховой линией, и максимальная глубина вдавливания h будет вне опасной зоны (точка А). При достаточно большой разнице между г и R опасная зона около точки А может оказаться совсем ненаклепанной или наклепанной в меньшей степени, чем другие зоны галтели.
Проведенный анализ показывает, что максимальная деформа ция в наиболее напряженной зоне галтельного перехода будет обеспечиваться только при г < R.
При выборе глубины вмятия h (рис. 43) целесообразно исхо дить из необходимости обеспечить должную степень пластической деформации е и должную глубину пластически деформирован ного а слоя в опасной зоне галтельного перехода. Глубина h должна быть также достаточной, чтобы формируемая галтель имела профиль правильной формы, соответствующей радиусу R вдавливаемого шарика (ролика).
При исследовании обработок ППД во многих случаях поль зуются в качестве характеристики степени деформации е отноше нием диаметра лунки к диаметру вдавливаемого шарика. Приме нительно к формированию галтельного перехода по аналогии
можно принять |
|
e = b :2 R . |
(1) |
Степень деформации е < 0,3 не обеспечивает еще максималь ного упрочнения стали. Увеличение е сверх 0,4—0,5 не вызывает повышения твердости и таким образом с этой точки зрения яв ляется бесполезным. Целесообразно принять
е ^ 0,4. (2)
Верхнее значение е не играет существенной роли. Из построения
следует |
(R — h)2 -)- (-^-) |
= |
R 2, |
откуда, |
если |
принять |
h = |
||||
= |
mR, |
получим |
b = |
2R V 2т — m2, |
т. |
е. |
е = b |
2R — |
|||
= |
V 2 т |
— т 2 и ет1п |
= |
0,4 |
= |
(/2 т |
— т 2, отсюда rnmln = 0,083» |
||||
» |
0,1, и минимальное значение глубины вмятия ftmln, определяе |
||||||||||
мое только из соображений достаточной |
степени |
наклепа, |
будет |
||||||||
|
|
|
|
|
|
— 0,1/?. |
|
|
|
(3) |
Глубина пластически деформированного слоя, согласно ана лизу [5],
а = 4,2 УМ. |
(4) |
Вместе с тем практика применения ППД подтвердила целесо образность назначения глубины пластически деформированного слоя в зависимости от диаметра d упрочняемого вала в пределах
О,Old < а < 0,05d. |
(5) |
Следует также учесть экспериментальные исследования и опыт упрочнения ППД резьбовых деталей, где достаточно высокая упрочняемость достигалась при деформации впадин резьбы на глубину
0,001 d < /г < 0 ,005d |
(б) |
Из сопоставлений условий (5) и (6) следует, что
а = ЮЛ. |
(7) |
Анализ данных [5] показывает также, что для обеспечения правильной формы галтели необходимо, чтобы
Л > 0,2R. |
(8) |
Этим требованием перекрывается условие (3), выведенное только из соображений обеспечения достаточной степени наклепа. Основные показатели упрочняющего деформирования галтельных переходов приобретают следующий вид. Глубина пластически
деформированного слоя а = 4,2 V Rh = 9,48Л « ЮЛ; а =
= 4,2 У Rh = 1,89/? л; 2R. Величина радиуса ролика должна укладываться, как правило, в диапазон 0,005d < R < 0,025d.
Следует отметить, что в некоторых случаяхглубину пласти ческогоподнутрения Л целесообразно значительноувеличить, доведя ее до Л = 0,6R и даже до Л = 0,8R. Это необходимо для сохранения эффекта деформационного упрочнения для валов, подвергающихся перешлифовыванию. При этом при увеличении деформационного поднутрения сверх к = 0,2R эффективность упрочнения не только не уменьшается, но даже увеличивается, что объясняется возрастанием глубины наклепа. В табл. 49 при ведены значения глубины наклепа а при выдавливании галтелей роликом с профильным радиусом R при различной глубине под нутрения [Л = (0,2-г-0,8) /?]. Диаметры упрочняемых валов удов-
1 |
5 \ |
(“Too" |
lo o* ) cl- |
При испытаниях на усталость при изгибе ступенчатых сталь ных или чугунных валов, упрочненных по рекомендуемым режи мам, обнаруживается, как правило, начало разрушения под упрочненным слоем, а в ряде случаев вне зоны галтельных пере ходов (на гладкой части вала).
Глубина наклепанного слоя при различных глубинах деформационного выдавливания роликов радиусом 1—4 мм
R, мм |
Л, мм |
а = |
4,2 V~Rh' |
Диаметр вала d (мм) при а, равном |
|
|||
|
|
|
|
|
||||
|
мм |
0,01</ |
0,02d |
0,03</ |
0,04 d |
O.Obd |
||
|
|
|
|
|||||
|
0,2 |
|
1,9 |
190 |
95 |
63 |
47 |
38 |
1 |
0,4 |
|
2,6 |
260 |
130 |
87 |
65 |
52 |
|
0,6 |
|
3,2 |
320 |
160 |
107 |
80 |
64 |
|
0,8 |
|
3,7 |
370 |
185 |
123 |
92 |
74 |
2 |
0,4 |
|
3,7 |
370 |
185 |
123 |
92 |
74 |
0,8 |
|
5,3 |
530 |
265 |
177 |
132 |
106 |
|
|
1,2 |
|
6,5 |
650 |
325 |
217 |
162 |
130 |
|
1,6 |
|
7,5 |
750 |
375 |
250 |
187 |
150 |
|
0,6 |
|
5,6 |
560 |
280 |
187 |
140 |
112 |
3 |
1,2 |
|
8,0 |
800 |
400 |
267 |
200 |
160 |
|
1,8 |
|
9,8 |
980 |
490 |
327 |
245 |
196 |
|
2,4 |
|
11,3 |
ИЗО |
565 |
377 |
282 |
226 |
|
0,8 |
|
7,5 |
750 |
375 |
250 |
187 |
150 |
4 |
1,6 |
|
10,6 |
1060 |
530 |
353 |
265 |
212 |
|
2,4 |
|
13,0 |
1300 |
650 |
433 |
325 |
260 |
|
5,2 |
|
14,8 |
1480 |
740 |
493 |
370 |
296 |
В ЦНИИТМАШе была произведена экспериментальная оценка сопротивления усталости крупных ступенчатых валов (диаме тром 135—220 мм) при испытаниях на изгиб по симметричному циклу до полного разрушения на базе 107 циклов. Применяли метод «вверх—вниз» при испытаниях 20 валов в каждой серии.
Сравнивали |
величины пределов |
выносливости валов |
в |
связи |
||||
с |
сортом |
стали, |
радиусом |
галтельного |
перехода |
г |
d = |
|
= |
(0,02-5-0,06) и |
способом |
формирования |
галтелей (обработка |
||||
резцом, пластическое выдавливание обкаткой роликом). |
|
|
||||||
|
Результаты испытаний (табл. |
50) показывают весьма высокую |
эффективность упрочнения малых галтелей методом ППД. При этсм особенно высокий эффект обнаруживается для легированной стали.
Результаты испытаний |
на усталость |
ступенчатых валов 0 1 3 5 /2 2 0 мм |
с различной обработкой |
галтельных |
переходов |
Сталь |
r(R), |
ао |
Ко |
O-t, |
М П а |
Способ формирования |
мм |
М П а |
галтели |
||||
|
|
|
|
|
V - i . |
|
|
3 |
3,4 |
3,3 |
88 |
6 |
Обработка резцом |
34Х Н 1М |
9 |
2,2 |
1,9 |
152 |
13 |
|
|
3 |
3,4 |
1,0 |
290 |
17 |
Выдавливание |
|
3 |
3,4 |
2,5 |
76 |
3 |
Обработка резцом |
45 |
9 |
2,2 |
1,7 |
ПО |
7 |
|
|
3 |
3,4 |
1,0 |
191 |
16 |
Выдавливание |
Разработанные рекомендации были успешно применены для упрочнения прямых и коленчатых валов (работающих на изгиб или кручение при переменных нагрузках).
6. РАСЧЕТНЫЕ УСИЛИЯ ДЛЯ ДЕФОРМАЦИОННОГО УПРОЧНЕНИЯ СТУПЕНЧАТЫХ ВАЛОВ
Ниже приведена методика определения величин усилий, необ ходимых для вдавливания ролика (шарика) радиусом R на глу бину h = 0,2R при формировании галтели обкаткой.
Воспользуемся известным условием
где Р — усилие |
на ролик; |
R — радиус вдавливаемого |
шарика; |
||||
h — остаточная |
глубина лунки. Если принять по условию h = |
||||||
= |
0,2/?, то Р = 1,2 H BR2. |
|
|
|
|
||
|
Экспериментальная проверка этой зависимости применительно |
||||||
к |
нанесению |
круговой канавки на |
гладкий вал |
обкаткой его |
|||
Т а б л и ц а 51 |
|
|
|
|
|
|
|
Усилие на ролик, |
необходимое для |
получения канавки глубиной h — 0,2 R |
|||||
|
R, мм |
|
л, |
Р ( к Н ) п р и Н В Н / м м 2 |
|
|
|
|
|
|
|
|
|
||
|
|
|
|
7 0 0 |
1 3 0 0 |
|
2 4 0 0 |
|
2 |
|
0,4 |
4 (3,36) |
7,4 (6,24) |
12,5 (13,7) |
|
|
3 |
|
0,6 |
7,5 (7,56) |
12,5 (14,04) |
- |
(25,92) |
роликом (без перемещения |
|
|
|
|
|
|
|
|||||||||
по образующей) дала впол |
|
|
|
|
|
|
|
|||||||||
не удовлетворительные ре |
|
|
|
|
|
|
|
|||||||||
зультаты для |
материалов |
|
|
|
|
|
|
|
||||||||
различной |
твердости |
(ва |
|
|
|
|
|
|
|
|||||||
лы 0 |
100—220 мм из алю |
|
|
|
|
|
|
|
||||||||
миния и стали). В табл. 51 |
|
|
|
|
|
|
|
|||||||||
указаны |
эксперименталь |
|
|
|
|
|
|
|
||||||||
ные и расчетные (в скоб |
|
|
|
|
|
|
|
|||||||||
ках) |
|
усилия |
на |
|
ролик. |
|
|
|
|
|
|
|
||||
Для |
определения |
уси |
|
|
|
|
|
|
|
|||||||
лия |
на |
ролик при выдав |
|
|
|
|
|
|
|
|||||||
ливании |
галтели |
на |
сту |
|
|
|
|
|
|
|
||||||
пенчатом |
валу |
следует |
|
|
|
|
|
|
|
|||||||
принять |
во внимание, что |
|
|
|
|
|
|
|
||||||||
это усилие (см. рис. 43), |
|
|
|
|
|
|
|
|||||||||
направленное |
под |
|
углом |
|
|
|
|
|
|
|
||||||
45° к оси вала, будет |
|
|
|
|
|
|
|
|
|
|||||||
Q - = P / 2 ”» |
1,4Р |
или |
|
|
|
|
|
|
|
|
||||||
|
|
|
|
\JHBR\ |
|
|
|
|
|
|
|
|
|
|
||
По |
последней |
зависи |
|
|
|
|
|
|
|
|||||||
мости |
построены графики |
|
|
|
|
|
|
|
||||||||
(рис. |
44). |
Ограниченные |
|
|
|
|
|
|
|
|||||||
штриховыми линиями |
об |
Рис. |
44. |
График зависимости |
усилия на ролик |
|||||||||||
ласти |
определены |
|
из |
ус |
||||||||||||
|
(с профильным радиусом R ), |
необходимого для |
||||||||||||||
ловия |
|
h min = |
0,15/? |
|
и |
вдавливания его в |
ступенчатый вал |
на |
глубину |
|||||||
|
|
h = |
0,2R от НВ |
|
|
|
|
|||||||||
^шах = |
0,25/?. |
|
|
|
|
|
|
|
|
|
|
|
|
|||
Данный |
расчет усилия |
|
|
|
|
|
|
|
||||||||
на |
ролик |
предполагает, |
что |
исходный |
радиус |
г |
упрочня |
|||||||||
емой |
галтели |
мал |
по |
сравнению |
с профильным |
радиусом R |
||||||||||
ролика |
(шарика). |
Если |
исходный |
радиус |
галтели |
будет |
при |
ближаться к радиусу ролика, то усилия, необходимые для надлежащего деформирования галтели, будут значительно возрастать. Как видно из графика, применение роликов радиу сом /? > 3 мм при обкатке валов из материалов средней твердости (НВ < 2500 Н/мм2) требует значительных усилий, близких к пре дельно допустимым даже для крупных токарных станков (при давлении на ролик суппортом). В связи с этим представляет ин терес применение для выдавливания галтелей динамического метода деформирования (вибрирующим роликом или чеканкой).
Для |
|
динамического |
выдавливания используют пневмати |
ческие |
или механические пружинные ударники. Потенциаль |
||
ную |
энергию бойка |
при этом определяют по следующей ме |
тодике.
Энергия удара Эу, необходимая для образования лунки диа метром d при вдавливании сферического бойка в плоскую поверх
Рис. 45. Энергия бойка (с профильным радиусом R ), необходимая для вдавливания его в ступенчатый вал на глубину h = 0,2R
ность металлического образца, |
может быть выражена форму |
||
лой |
[13] |
НВ |
d4 |
|
Эу |
||
|
12 |
R ’ |
|
где |
R — радиус бойка. |
|
|
Данная формула выведена применительно к упрочняющей чеканке конструкционных сталей средней твердости (НВ 1100— 2100 Н/мм2) соответствует экспериментальным данным для широ кого диапазона величины радиуса бойка.
Можно принять приближенно d = 2,8|/Rh (что вытекает из приравнивания площади сферического отпечатка к площади его проекции). Тогда Эу = 5,3 H BRh2. Рациональным соотношением между R и Н, как было показано выше, является h = 0,2R. При этом Эу = 0,2 H BR3.
|Для определения энергии удара при пластическом выдавлива нии галтели на ступенчатом валу следует принять во внимание, что направление удара будет составлять угол около 45° с образую щей вала, и, таким образом, энергия удара, выраженная послед ней формулой для нормального к поверхности направления удара, должна быть увеличена в случае обработки галтелей и составит
Этулл = Эу / 2 = 1,4ЭУ = 0,28HBR\
Проведенными опытами [13] было показано также, что по тенциальная энергия ударника Э„ только частично тратится на образование пластического отпечатка, а некоторая часть ее при ходится на упругий отскок бойка, прогиб обрабатываемого об разца и пр.