
книги / Усталость крупных деталей машин
..pdfРис. 13. Сборный образец (конструкции В. М. Андрейко) для испытания крупных валов на усталость при изгибе
Испытанию на усталость при изгибе по симметричному циклу
подвергали образцы 0 |
180 мм (изгиб в одной плоскости) и 0 18 мм |
|
(изгиб образца, закрепленного одним концом |
при вращении). |
|
Во всех случаях N = |
107. Кольцевые канавки |
на образцах вы |
полняли профильным резцом при малой радиальной подаче для уменьшения наклепа поверхности. Для обоих типов образцов
«о = 4.
Заготовки из сталей СтЗ и 45 использовали в состоянии по ставки. Заготовки из стали 40ХН2МА подвергали закалке в масло с отпуском при 550 °С.
Для испытания крупных валов на усталость при изгибе при менили новую конструкцию образца (рис. 13), состоящего из двух концевых частей (головок), которые можно использовать много кратно, и подлежащей испытанию сменной (полой или сплошной) рабочей части. Головки образца соединяют с рабочей частью стяж ками с резьбой М 100 X 3. Напряжения сжатия, возникающие в области стыкового соединения, не распространяются на испыты ваемую рабочую часть образца.
Части образца, соосность установки которых достигается при менением центрирующего выступа, соединяли методом растяже ния стяжки с помощью гидравлического домкрата с использова нием насоса высокого давления типа НСВД-250. Такой метод сборки образца обеспечивает достаточно высокую точность кон троля силы предварительной затяжки Q резьбового соединения. Для обеспечения необходимой жесткости стыкового соединения образца площадь поверхности контакта определяли из условия создания контактного напряжения в стыке <тк > 1,5сги_0б. гДе <ти. об — напряжение изгиба в рабочей части образца. Ширина h кольца контакта стыкового соединения была равна 15 мм, а отно шение ширины кольца к наружному диаметру h : D „= 0,068. При <УК= 200 МПа номинальное среднее напряжение в резьбе стяжки crm = 270 МПа с (0,5-ьО,6) 0Т, при котором обеспечивается
Т а б л и ц а |
4 |
|
|
|
|
Результаты испытаний на усталость валов с кольцевыми надрезами |
|
||||
Сталь |
о _ 1 (Ю)» МПа |
МПа |
° - М 1 8 0 )’ МПа |
ео (180) |
|
|
|
|
|
|
|
СтЗ |
|
175 |
95 |
75 |
2,3 |
45 |
|
248 |
145 |
55 |
4,5 |
40Х Н 2М А |
423 |
185 |
65 |
6,5 |
|
П р и м е ч а н и е . |
Во всех случаях для V-образных канапок с углом раскрытия 60° |
||||
для образцов |
0 18 мм |
t = 1,0 мм, |
R = 0,2 мм; |
0 180 мм t = 2 мм, R |
= 0,4 мм. |
достаточная плотность стыка и сопротивление усталости резьбо вого и стыкового соединений при асимметричном цикле нагру жения.
Расчетные диаметры образцов по дну надреза составляли 18 и 176 мм. Крупный образец был выполнен полым с внутренним диаметром 90 мм.
На усталость крупные сборные образцы испытывали на ма шине УП-200 при изгибе в одной плоскости по симметричному циклу. Частота нагружения образца 1000— 1200 цик/мин. Малые образцы, закрепленные одним концом, испытывали на машине типа У-20 по симметричному циклу при вращении. Малые образцы ( 0 18 мм) изготовляли из поверхностных слоев проката 0 220 мм в состоянии, соответствующем сталям крупных образцов. Ре зультаты испытаний на усталость представлены в табл. 4. Значе ния пределов выносливости для гладких образцов диаметром 10 мм получены расчетом из соотношения or_j (10) = 0,46сгв. Дан
ные табл. 4 показывают, |
что совместное проявление масштаба |
и концентрации (Ка ео) в |
сильной степени (почти в 3 раза) уве |
личивается при переходе от мягкой углеродистой стали к легиро ванной улучшенной стали. Преимущества высокопрочной легиро ванной стали, обнаруживаемые по показаниям прочности (стати ческой или циклической) на малых образцах, полностью утрачи ваются при переходе к крупным образцам. Крупные валы из стали СтЗ обладают даже несколько более высоким пределом выносливости, чем аналогичные валы из сталей 45 и 40ХН2МА.
Изложенные выше |
результаты опытов |
находятся в пол |
ном соответствии |
с закономерностями, |
установленными |
в ЦНИИТМАШ на основе испытаний крупных валов с другими видами концентраторов напряжений (резьбовые нарезки, гал-
тельные |
переходы ступенчатых валов, прессовые посадки, см. |
п. 2 этой |
главы). |
4.УСТАЛОСТЬ ЭЛЕКТРОШЛАКОВОГО ЛИТЬЯ
ИКОВАНОЙ СТАЛИ
Разработанный Институтом электросварки им. Е. О. Патона метод электрошлакового литья (ЭШЛ) значительно уменьшает трудо затраты и расход металла по сравнению с обычным методом полу чения кованых заготовок [26].
Ниже приведены опытные данные, полученные в ЦНИИТМАШ по сопоставлению сопротивления усталости крупных валов, изго товленных методом ЭШЛ и свободной ковкой х.
Испытаниям на усталость подвергали ступенчатые валы 0 133/200 мм с разными радиусами сопряжений (рис. 14). Часть валов из каждого вида стали упрочняли ППД. Образцы обтачи вали в галтели на возможно малый радиус (R < 0,5 мм), затем галтель обрабатывали на токарном станке вибрирующим роликом с профильным радиусом г = 3 мм до полного формирования гал тели того же радиуса. При этом углубление ролика в вал (считая по радиусу сечения цилиндрической части вала) составляло h = = 0,2г или h « 0,6 мм.
Испытания образцов на изгиб по симметричному циклу в од ной плоскости выполняли на машинах ЦНИИТМАШ типа УП-200. База испытаний была принята в 5 млн. циклов.
Заготовки как из кованой, так и из литой стали были подверг нуты нормализации и имели механические свойства, указанные
1 Опыты выполнены И . В . Кудрявцевым с участием инженеров А. А . Н а заровой и Р . Е . Грудской.1*
Рис. 14. Ступенчатый образец для ис питаний на усталость при изгибе
Рис. 15. Последовательность испытаний ступенчатых образцов, изготовленных из кованой (а) и литой ((У) стали:
1 — радиус |
галтели |
R = 3 |
мм; 2 — |
R = 9 мм; |
3 - R = |
0,2 + 3 |
мм (полу |
чен ППД). Точками обозначены несломавшиеся образцы, крестиками — сло мавшиеся
2 Кудрявцев И. В. и др.
Т а б л и ц а |
5 |
|
|
|
|
|
|
|
Состав и механические свойства исследованных сталей |
|
|
|
|||||
|
|
Химический |
состав, % |
|
Механический |
состав |
||
Сталь |
Мп |
Si |
S |
р |
V |
б. % |
4>. % |
|
|
С |
|||||||
|
|
|
|
|
|
МПа |
|
|
Кованая |
0,44 |
0,88 |
0,18 |
0,021 |
0,024 |
711 |
20,4 |
39,4 |
Литая (ЭШ Л) |
0,41 |
0,62 |
0,22 |
0,013 |
0,011 |
518 |
25,7 |
33,5 |
в табл. 5. Составы обоих видов стали были практически одинако выми.
Для определения среднего статистического значения предела выносливости каждой серии валов и его среднего квадратического
отклонения использовали |
метод «вверх-вниз» |
[35]. Число валов |
||||
в каждой серии составляло от 10 до 20 шт. |
|
|
||||
и |
Результаты |
испытаний |
и подсчеты представлены на рис. 15 |
|||
16 и в табл. 6. Сравниваемые стали обладают |
практически |
|||||
одинаковыми |
значениями |
предела |
выносливости |
на образцах |
||
с |
концентрацией напряжений а а = |
2,2 -=-3,4. |
Упрочнение гал |
телей наклепом привело к значительному повышению пределов выносливости как для кованой, так и для литой стали (соответ ственно в 2, 3 и 1,6 раза). Меньшая эффективность наклепа для ЭШЛ должна быть объяснена тем, что сопротивление усталости при этой обработке лимитируется прочностными свойствами под коркового слоя, которые у ЭШЛ были значительно ниже, чем у кованого металла. Все изломы образцов при испытаниях на усталось происходили по зоне галтельных переходов. Однако можно считать, что полученные для упрочненных образцов значения пределов выносливости близки к соответствующим значениям их
6,МПа |
для |
гладких |
образцов того |
же |
|||
диаметра. Основанием для такого |
|||||||
|
предположения являются резуль |
||||||
|
таты описанных в главе V иссле |
||||||
|
дований по |
определению эффек |
|||||
|
тивности |
наклепа |
ступенчатых |
||||
|
валов с галтелями малых радиу |
||||||
|
сов. |
Указанное |
допущение |
дает |
|||
|
возможность определить величины |
||||||
|
эффективных коэффициентов |
кон |
|||||
|
центрации напряжений /Со, а так |
||||||
|
же |
коэффициенты |
чувствитель |
||||
|
ности к концентрации для сталей |
||||||
|
испытанных валов. |
|
|
||||
Рис. 16. Долговечность образцов из |
Данные |
табл. |
6 |
показывают, |
|||
кованой (а) и литой (<!Г) стали (обозна |
что |
литая |
сталь |
менее чувстви- |
|||
чения серий те же, что на рис. 15) |
Т а б л и ц а |
б |
|
|
|
|
Результаты испытаний ступенчатых образцов 0 |
135/220 мм |
||||
на усталость |
при изгибе |
|
|
|
|
Сталь |
R (г), |
Способ |
а о |
0 - ь |
s a_i. |
мм |
образования |
||||
|
|
галтели |
|
МПа |
МПа |
|
3 |
Резцом |
3,4 |
87 |
6,05 |
|
9 |
2,2 |
106 |
16 |
|
Кованая |
|
||||
|
|
|
|
|
|
|
3 |
Роликом |
3,4 |
200 |
26,9 |
|
3 |
Резцом |
3,4 |
84 |
6,5 |
|
9 |
2,2 |
106 |
12 |
|
|
|
||||
Литая (ЭШЛ) |
|
|
|
|
|
|
3 |
Роликом |
3,4 |
136 |
19 |
Т а б л и ц а |
7 |
|
|
|
|
Сопоставление кованой и литой стали |
|
|
|
||
по их чувствительности к абсолютным размерам |
|
||||
|
|
Предел выносливости, МПа |
|
||
Сталь |
° - 1 (10) |
а - 1 (135) |
|||
|
|
||||
Кованая |
|
327 |
|
200 |
|
Литая (ЭШЛ) |
239 |
|
136 |
|
Хо
2,3
1,9
1,0
1,6
1,3
1,0
а
II -о |
Ь . |
1 |
J3 |
1 |
|
|
в |
|
0,54
0,75
0
0,25
0,25
0
_ а - 1 (135)
1 (10)
0,61
0,57
тельна |
к концентрации напряжений (в 2—3 раза) по сравнению |
с кованой. Этим обстоятельством и следует объяснить практиче |
|
ское совпадение значений пределов выносливости кованой и литой |
|
стали на образцах с концентраторами напряжений. По получен |
|
ным значениям предела выносливости для крупных валов можно |
|
определить и коэффициенты чувствительности рассматриваемых |
|
сталей к абсолютным размерам. Воспользуемся для этого доста |
|
точно |
надежной зависимостью между значениями временного |
сопротивления разрыву а в и предела |
выносливости а_кю) [41] |
при изгибе малых образцов a_j (10) = |
0,46авРезультаты подсче |
тов (табл. 7) показывают, что коэффициенты влияния абсолютных размеров для рассматриваемых сталей практически одинаковы.
5. УСТАЛОСТЬ КОЛЕНЧАТЫХ ВАЛОВ МОЩНЫХ СУДОВЫХ ДИЗЕЛЕЙ
Высокая надежность работы судового дизеля в тяжелых условиях морского плавания обеспечивается главным образом прочностью и долговечностью коленчатого вала — наиболее ответственной высоконапряженной и дорогостоящей детали дизеля. В резуль тате воздействия циклически изменяющихся нагрузок материал
Рис. 17. Натурный отсек коленчатого вала:
1 — литой кривошип; 2 — кованые шейки; 3 — тензорезистор
вала работает на усталость. Экспериментальные данные о вели чине напряжений и характер разрушений крупных коленчатых валов свидетельствуют о том, что прочность их лимитируется в основном нормальными напряжениями от изгиба.
Определенный уровень сопротивления усталости коленчатых судовых Балов реализуется металлургической технологией их изготовления.
Крупные коленчатые валы малооборотных судовых дизелей мощностью 3,7— 15,5 МВт изготовляют в основном сбор ными с литыми кривошипами или щеками. Кованые шейки за прессовывают по горячей посадке в кривошипы и щеки. К отлив кам коленчатых валов дизелей предъявляют высокие требования по механическим свойствам, на отсутствие различного рода метал лургических дефектов, которые при литье в земляную форму трудно обеспечить. В связи с этим широко распространенный способ получения крупнотоннажных отливок кривошипов (литье в зе млю) заменяют другими более прогрессивными, например спосо бом электрошлакового литья (ЭШЛ), обеспечивающим высокое качество отливок [5].
Заготовки кривошипа коленчатого вала получают способом электрошлакового переплава (ЭШП) электрода в охлаждаемом кристаллизаторе.
Увеличение мощности форсированных судовых дизелей, вне дрение новых способов изготовления крупных коленчатых валов вызывает необходимость сравнительной оценки сопротивления усталости этих валов.
В ЦНИИТМАШе проведены испытания на усталость натурных отсеков коленчатых валов полусоставной конструкции с литыми кривошипами, изготовленными двумя способами — литьем в пес чано-глинистую форму и ЭШЛ с приплавлением кривошипов1
1 Испытания проводили под руководством И. В . Кудрявцева и И. Т . Гонча рова (ЦНИИТМ АШ ) с участием А. П . Куликова (Брянский машиностроитель ный завод).
Т а б л и ц а 8
Химический состав металла кривошипов, °о
Номер |
кривошипа |
с |
Мп |
Si |
р |
S |
Сг |
Ni |
Л1 |
1 |
|
0,22 |
0,63 |
0,30 |
0,025 |
0,018 |
0,08 |
0,05 |
0,04 |
2 |
|
0,25 |
0,78 |
0,32 |
0,035 |
0,010 |
0,08 |
0,11 |
0,05 |
1 |
(ЭШ Л) |
0,28 |
0,64 |
0,28 |
0,035 |
0,006 |
0,17 |
0,11 |
0,01 |
2 |
(ЭШ Л) |
0,32 |
0,66 |
0,33 |
0,032 |
0,004 |
0,14 |
0,11 |
0,02 |
Т а б л и ц а Э
Механические свойства металла кривошипов
Номер кривошипа |
Oq , МПа |
ат> МПа |
6, % |
% |
°Ц. кДж/м* |
|
1 |
|
470 |
235 |
33,0 |
59,0 |
1070 |
2 |
|
545 |
250 |
28,5 |
56,5 |
1010 |
1 |
(ЭШ Л) |
510 |
265 |
28,0 |
53,0 |
970 |
2 |
(ЭШЛ) |
550 |
260 |
27,5 |
48,0 |
750 |
В результате испытаний была проведена сравнительная оценка выносливости коленчатых валов двух металлургических техно логий. Для испытаний были изготовлены четыре натурных отсека вала (по два каждой технологии). Отсек коленчатого вала (рис. 17) имел диаметр шеек 320 мм, радиусы галтелей шатунной шейки 20 мм, коренной — 11 мм. Масса отсека 2500 кг. Материал литых
кривошипов — сталь |
20Г Химический состав и механические |
свойства стали приведены в табл. 8 и 9. |
|
Натурные отсеки |
испытывали на резонансной усталостной |
машине УП-300 (см. главу I), специально модернизированной для проведения этих.испытаний. На рис. 18 показан разрушенный вал после испытаний.
Отсек вала нагружали в процессе испытаний изгибающим мо ментом по симметричному циклу, действующим в плоскости колена кривошипа. Частота изменения напряжений равнялась 11 Гц. База испытаний 10 млн. циклов. Номинальное напряжение опре деляли в середине внутренней образующей шатунной шейки (см. рис. 17). Режим работы установки контролировали индика торными виброметрами конструкции ЦНИИТМАШ, обеспечив шими высокую точность измерения уровня напряжений. В ка честве дублирующей контрольной аппаратуры использовали
также осциллограф, подсоединенный |
к тензорезистору |
(см. |
рис, 17), Номинальное напряжение для |
кривошипа № 1 |
(литье |
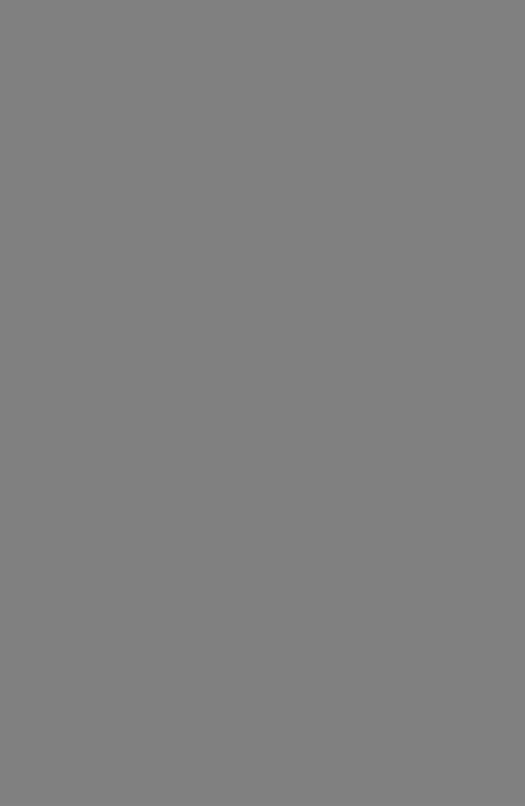
щеки совершенно одинаково, и лишь окончательно ломался криво шип по галтели, расположенной рядом с приводной траверсой испытательной машины.
На поверхности изломов всех кривошипов визуально металлур гических дефектов не обнаружено. В зоне долома наблюдалось крупнозернистое строение отливки, что свойственно отливкам большой массы и размеров.
Изломы кривошипов, изготовленных литьем в землю и методом ЭШЛ, аналогичны.
Сопротивление усталости металла кривошипов определяли также на образцах 0 18 мм, которые вырезали около поверх ности шатунной шейки вдоль ее образующих. Предел выносли вости от изгиба при вращении для металла, литого в землю, со ставил 162 МПа, а для ЭШЛ — 198 МПа.
В пересчете для стандартного лабораторного образца 0 7,5 мм (с учетом масштабного фактора) предел выносливости металла двух металлургических технологий можно принять соответственно 185 и 225 МПа.
В практике проектирования коленчатых валов мощных судо вых дизелей проверочные расчеты запаса прочности при перемен ных напряжениях весьма приближенны, так как эксперименталь ные данные, использующиеся в них, относятся к коленчатым ва лам малых размеров и иной конфигурации.
Проведенные испытания позволяют найти важный для расчетов на прочность коленчатых валов мощных двигателей коэффи циент /Сал, характеризующий снижение сопротивления усталости
коленчатого вала как детали по сравнению с лабораторным об разцом:
|
IS __ |
g -l |
|
|
|
A<ID |
a_i(D) * |
|
|
где a_! и |
(D) — предел выносливости металла кривошипа и ко |
|||
ленчатого вала (50 МПа). |
|
|
|
|
Для коленчатого вала, литого в землю, KoD = |
3,7, для вала, |
|||
изготовленного методом ЭШЛ, Ko{D) = |
4,5. |
быть исполь |
||
Найденные значения коэффициента |
Коп могут |
зованы при определении запаса прочности валов мощных мало оборотных судовых дизелей по нормальным напряжениям
_ а _ !
Установленные значения коэффициента K oDотносятся к литой
стали 20Г, которую в судовом дизелестроении в СССР и за рубе жом широко применяют для изготовления коленчатых валов. Для сталей других марок величина этого коэффициента, воз можно, потребует уточнения.
Основные геометрические размеры коленчатых валов, влия ющие на сопротивление усталости, регламентируются практически одинаковыми требованиями классификационных обществ, контро лирующих постройку судов, и, следовательно, подобны испытан ным отсекам коленчатого вала.
6. УСТАЛОСТЬ КРУПНЫХ ДЕТАЛЕЙ ПРИ АСИММЕТРИЧНЫХ ЦИКЛАХ
Во многих случаях детали машин работают в условиях перемен ных нагрузок, меняющихся по асимметричному циклу. К таким деталям относятся, в частности, ригели, стойки, арки и другие детали крупных гидравлических прессов, прокатных станов, установок для гидростатического прессования и др.
Ниже изложены основные закономерности, касающиеся уста лостных свойств машиностроительных материалов при перемен ном нагружении со средним напряжением, отличным от нуля.
Всякий асимметричный цикл изменения напряжений можно рассматривать как слагающийся из двух составляющих: постоян ного или среднего напряжения цикла
^ |
__ |
^тах + min |
Vm — |
2 |
и переменного симметрично меняющегося напряжения с ампли тудой
__ °тях ®min
° а “ |
2 |
’ |
гДе ашах и ^min — напряжение цикла максимальное и минимальное. Отношение стт1п сгтах = г характеризует степень асимметрии цикла и носит название коэффициента асимметрии. Обычно зави симость между средним напряжением цикла и соответствующими значениями предельных переменных напряжений (или амплиту дой цикла) выражают в виде полных диаграмм пределов вы носливости, экспериментальное построение которых весьма за труднено даже для лабораторных образцов небольших размеров. Поэтому естественны попытки построения указанных зависимостей
теоретически.
Многими авторами предложены различные зависимости между предельной амплитудой и средним напряжением цикла.
Так, если обозначить через £ относительную величину пре дельной амплитуды (£ = а с/ал), а через т — относительную вели чину среднего напряжения цикла (пг = сTm/a_j), то предложения различных авторов могут быть выражены следующим образом:
условие |
Гудмана £ = 1 — |
условие Гербера £ = |
1 — ( та- |
У ; |
условие |
Зодерберга £ = 1 — |
т^ ~ х ; условие |
Биргера |
£ = |
== У 1 — условие Одинга £ = - f - + " [ / " + 1•