
книги / Усталость крупных деталей машин
..pdfПриварка вторых накладок на пластины с уже приваренными накладками, прошедшими нормализацию, является столь же неблагоприятной, как и приварка единичных накладок без после дующей термообработки. Резкое снижение пределов выносливости пластин в этом случае должно быть полностью отнесено за счет проявления неблагоприятных растягивающих остаточных на пряжений.
Исключительно резкое проявление остаточных напряжений связано с формой выбранных моделей, вызывающей высокую концентрацию этих напряжений в опасных зонах. Проявление остаточных напряжений в сопротивлении усталости сварных конструкций повышается с увеличением степени их концентра ции, связанной с формой.
Таким образом, можно заключить, что монтажные сварные швы в толстостенных конструкциях, не подвергаемых термообра ботке, могут вызывать значительное снижение сопротивления усталости даже в тех случаях, когда они расположены вне опасных зон, но способны вызвать неблагоприятные растягивающие сва рочные остаточные напряжения в опасных зонах конструкции, особенно в зонах с резкой концентрацией напряжений.
5. ВЛИЯНИЕ ДЕФЕКТОВ НА СОПРОТИВЛЕНИЕ УСТАЛОСТИ СВАРНЫХ СОЕДИНЕНИЙ
При проектировании сварных конструкций следует принимать во внимание возможность возникновения дефектов вследствие нарушения технологического процесса сборки и сварки. Дефекты следует рассматривать как концентраторы напряжений, могущие привести к понижению сопротивления усталости сварных соеди нений.
Основным методом оценки технологических отклонений при сварке является прямое испытание сварных соединений с дефек тами и накопление экспериментальных данных по их влиянию на прочность соединений при циклических нагрузках.
В настоящее время еще недостаточно экспериментальных дан ных для научно обоснованного подхода к оценке допустимости дефектов в сварных соединениях, особенно для металла большой толщины.
Известны два подхода к изучению и оценке влияния дефектов на сопротивление усталости сварных соединений.
Одни исследователи исходят из того, что сопротивление уста лости сварных соединений предопределяется в основном концен трацией напряжений, создаваемой формой соединения и техноло гическими дефектами. Степень концентрации напряжений свар ного соединения определяется размерами дефектов и их располо жением. В ряде работ удалось установить связь между величиной дефекта и сопротивлением усталости сварных соединений преиму щественно для металла небольшой толщины.
По мнению других исследователей [37 ], в усталостных явле ниях существенна роль концентрации не только рабочих, но и остаточных напряжений. Один и тот же дефект по-разному влияет на сопротивление усталости сварных соединений в зависи мости от того, где он расположен — в поле сжимающих или растя гивающих напряжений. Действие дефекта, находящегося в поле сжимающих остаточных напряжений, может быть сильно ослаблено проявлением этих напряжений. Но если тот же дефект расположен в поле высоких растягивающих остаточ ных напряжений, его влияние на сопротивление усталости воз растает.
Конструкторам и технологам необходимы обоснованные кри терии для оценки степени опасности или допустимости сварочных дефектов различного характера, формы, ориентировки и размеров в зависимости от условий нагружения конструкции, ее назначе ния, степени ответственности и других факторов.
Однако разработка таких критериев является весьма сложной задачей. Прежде всего, сварочные дефекты весьма многообразны: трещины, непровары, подрезы, поры, шлаковые включения и дру гие конструктивно-технологические отступления. Кроме того, внутренние дефекты выявляют неразрушающими методами кон троля (рентгеноили гаммографирования, УЗД), которые обла дают ограниченной разрешающей способностью и позволяют установить только наличие дефекта, его расположение по толщине и приблизительные размеры. Характер дефекта и степень его остроты чаще всего остаются невыясненными.
Ниже рассмотрены вопросы допустимости дефектов округлой формы (пор и шлаковых включений) и возможности эксперимен тальной оценки влияния их на сопротивление усталости сварных соединений. Кроме того, оценивается сопротивление усталости одностороннего кольцевого сварного соединения в связи с техно логическими отступлениями при сварке, исказившими конструк тивные особенности корневой зоны шва.
Для оценки влияния трещиноподобных дефектов (трещин, непроваров, подрезов) обычно используют критерии механики разрушения.
Действующие нормативы в отношении допустимого размера даже таких наиболее легко обнаруживаемых дефектов, как поры и шлаковые включения, не всегда согласуются между собой, например для сосудов и трубопроводов высокого давления, пред назначенных для аналогичных условий эксплуатации. Имеются существенные различия в ограничениях величины и распределе ния пор (минимально допустимых расстояний между порами) в различных стандартах и нормативах.
Данные рис. 68 и 69 свидетельствуют об отсутствии согласо ванности между основными технологическими нормативами в США на допустимые поры и шлаковые включения для изделий с тол щиной металла до 100 мм [36].
ММ
Рис. 68. Сравнение максимально до |
Рис. 69. Сравнение допустимых пре |
||||||
пустимой |
величины пористости по |
делов для шлаковых включений по |
|||||
основным |
общепринятым |
в |
США |
основным |
общепринятым |
в США |
|
стандартам контроля: |
|
|
стандартам |
контроля: |
|
||
1 — стандарт |
ASME; 2 — военно- |
/ — стандарт Американского нефтя |
|||||
морской стандарт 250 — 1500 для уг |
ного института API — 1104; 2 — нор |
||||||
леродистых сталей и медно-никеле |
мативы Американской ассоциации |
||||||
вых сплавов; |
3 — военно-морские |
стандартов |
на трубопроводы высо |
||||
стандарты |
250— 1500 — I |
и |
250 — |
кого давления; 3 — стандарт ASME; |
|||
692—2; 4 — стандарт Американско |
4 и 5 — военно-морской |
стандарт |
|||||
го нефтяного |
института |
АР 1-1104 |
2 5 0 -1 5 0 0 -1 и 2 5 0 - 6 9 2 - 2 |
Изучение влияния сварочных дефектов на сопротивление усталости весьма сложная задача. Прежде всего возникают значи тельные трудности с получением естественных дефектов заранее заданных размеров и форм, с расположением их в определенных сечениях изделия с необходимой повторяемостью на требуемом числе изучаемых объектов. Поэтому прибегают к искусственному созданию дефектов. Так, для имитации сварочных дефектов типа пор на поверхности образца высверливают отверстия заданного диаметра и глубины.
Искусственное создание дефектов обработкой лезвийным ин струментом приводит к созданию острого углубления от сверла, наклепу металла и наведению остаточных напряжений в зоне образуемого дефекта, что может исказить результаты испытаний на усталость.
В связи с указанными недостатками механического способа создания искусственных дефектов в ЦНИИТМАШе предложен новый способ, целью которого является усовершенствование ме тода определения влияния сварочных дефектов. Искусственный дефект создают на металле шва или основном металле высверлива нием (или другим способом механической обработки) цилиндри ческого отверстия заданного диаметра и глубины с последующим разогревом до оплавления металла в области донной части отверсгия с применением неплавящегося электрода. Создаваемый при. этом в зоне дна отверстия литой металл наиболее близок по состо янию к металлу в области естественного дефекта.
£
so
-м------- ►
Рис. 70. Образец для изучения на усталость влияния групповых наружных пор, имити руемых сверлением отверстий диаметром 5 и 3,5 мм, глубиной 4 мм
Предлагаемый способ оценки влияния искусственных дефектов на прочность изделий был реализован при испытании на усталость крупных образцов сечением 50 X 74 мм из стали 15Х2НМФА.
Для испытаний были приняты три серии образцов: 1) гладкие, 2) с групповыми порами (без оплавления) и 3) с групповыми порами, оплавленными электрической дугой.
Испытания на усталость образцов проводили на машине УП-50 при изгибе по симметричному циклу ца базе 10е циклов.
Были приняты два размера: крупные диаметром 5 мм и средние диаметром 3,5 мм. Общее число пор составляло десять, по пять штук диаметром 3,5 и 5 мм. Суммарная приведенная площадь средних и крупных пор на ширине образца, равной 74 мм, соста вляла FnpHB = 146 мм2.
Цепочка пор из пяти пор диаметром 3,5 мм имела равные расстояния 10,5 мм между краями пор. В двух цепочках пор диаметром 5 мм расстояния между порами были 10, 20 и 30 мм.
Уменьшение площади поперечного сечения образца из-за наличия пор составляло в сечениях I —I, I I —II, I I I —I I I (рис. 70)
Т а б л и ц а 68
Пределы выносливости образцов сечением 50X 74 мм стали 15Х2НМФА с групповыми наружными порами
Образцы
Предел выносливо сти при 10е циклов
II
|
МПа |
% |
|
Гладкие |
315 |
100 |
— . |
С групповыми порами в исходном со |
185 |
59 |
1.7 |
стоянии |
|
|
|
С групповыми порами, оплавленными |
115 |
36 |
2,7 |
электрической дугой |
|
|
|
П р и м е ч а н и е . а_, — предел выносливости гладких образцов; о выносливости образцов с групповыми порами.
соответственно |
1,6; |
1 и |
1,9%. Подобное |
|
|
6У |
|
|
|
|
|||||||||
расположение пор |
преследовало |
цель |
|
|
1 ' |
|
WJQI711 |
|
|||||||||||
сравнительно оценить влияние |
размера |
320 |
|
£ |
w & 6 3 — |
|
|||||||||||||
|
|
|
|||||||||||||||||
и расположения пор на сопротивление |
|
|
|
|
|
|
|
||||||||||||
усталости. |
|
Указанный |
характер |
рас |
280 |
|
|
|
|
— |
|||||||||
положения |
пор воспроизводили на всех |
|
|
|
|
||||||||||||||
|
|
|
|
|
|
||||||||||||||
образцах |
обеих |
серий. Донную |
часть |
|
|
|
|
|
|
|
|||||||||
отверстий |
|
оплавляли |
на |
автоматиче |
240 |
|
|
|
|
— |
|||||||||
ской установке для аргонодуговой свар |
|
2 |
|
|
--- |
|
|||||||||||||
ки неплавящимся электродом на свароч |
|
|
|
|
|
||||||||||||||
|
|
/ |
|
|
|
|
|||||||||||||
ном токе |
|
/ |
= |
230 -=-----265 |
А, |
и д = |
691" ' *■ —. |
|
|
|
|
||||||||
|
200 —О------- |
|
|
- |
.F o o 6 J |
|
|||||||||||||
= 9-г-Ю В. |
|
|
|
|
|
|
|
|
|
|
|
|
|
|
|||||
|
групповое |
расположение |
|
|
|
|
_ с л З Д » |
|
|||||||||||
Принятое |
160 |
< 5 |
721161п |
|
69 61 |
66 |
|||||||||||||
наружных |
|
пор, |
имитируемых |
сверле |
|
- о - |
|||||||||||||
|
|
а 1'Ч N » |
|
|
|
|
|||||||||||||
нием отверстий, |
привело к |
понижению |
-------- |
|
ч |
- |
72 611— |
|
|||||||||||
предела выносливости на 41% |
(рис. 71, |
120 |
|
|
|
|
|
|
|||||||||||
табл. 68). Из |
четырех |
испытанных об |
|
|
|
|
|
ЬЧ* |
|
||||||||||
разцов |
в |
трех |
случаях |
усталостное |
|
|
|
|
- |
|
|||||||||
80 |
|
|
|
|
64 r |
|
|||||||||||||
повреждение |
происходило от |
крупных |
|
|
|
|
|
|
|||||||||||
пор. Причем в двух случаях |
при мини |
|
|
|
|
|
| |
||||||||||||
|
|
|
|
|
|
|
|
|
|
|
|
|
|
|
|
|
|||
мальном |
расстоянии |
между |
порами, |
10 |
|
|
|
|
|
|
|||||||||
равном |
10 мм. |
|
|
|
|
|
|
|
Рис. |
71. |
Результаты испытания |
||||||||
Оплавление донной части отверстий |
|||||||||||||||||||
на усталость образцов сечением |
|||||||||||||||||||
дугой |
неплавящимся |
вольфрамовым |
50X74 мм из стали 15Х2НМФА: |
||||||||||||||||
/ — гладких; 2 — с групповы |
|||||||||||||||||||
электродом |
привело к |
более |
резкому |
||||||||||||||||
ми порами (исходными отвер |
|||||||||||||||||||
(на 64%) снижению предела выносли |
стиями); |
3 — с групповыми |
по |
||||||||||||||||
рами |
(отверстиями), оплавлен |
||||||||||||||||||
вости |
образцов |
с |
аналогичным |
груп |
ными электрической дугой (рим |
||||||||||||||
повым |
расположением |
пор |
по |
сравне |
скими цифрами |
обозначены |
но |
||||||||||||
мера |
образцов, |
испытанных |
на |
||||||||||||||||
нию с |
пределом выносливости |
гладких |
разных |
уровнях |
напряжений |
||||||||||||||
после прохождения ими без по |
|||||||||||||||||||
образцов. |
|
|
|
|
|
|
|
|
|
|
вреждения базы испытаний) |
|
|||||||
Помимо концентрации |
напряжений, |
|
|
|
|
|
|
|
|||||||||||
вызываемой |
|
отверстиями, |
в данном случае дополнительными не |
благоприятными факторами, приведшими к понижению сопротив ления усталости, явились наличие литого металла и зоны терми ческого влияния в основании отверстий (пор) и сварочных рас тягивающих напряжений вследствие температурного воздействия на металл сварочной дуги.
Изломы от усталости четырех образцов с оплавленными отвер стиями проходили по трем различным цепочкам пор (см. рис. 70) в сечениях / —/, I I —II и I I I —I I I (два случая).
В ЦНИИТМАШе оценено влияние единичных шлаковых вклю чений на сопротивление усталости сварных соёдинений стали 22К при симметричном изгибе при 107 циклов на крупных образцах сечением 200 X 200 мм.
При наличии внутренних, не выходящих на поверхность крупных шлаковых включений трещины усталости зарождались в глубине сечения образца при напряжениях ниже, чем на поверх ности. Включения округлой формы (длиной 7—10 мм) залегали
Пределы выносливости и эффективные коэффициенты концентрации напряжений различных конструкций односторонних сварных соединений стали 34ХМ
|
|
|
|
Предел |
|
|
|
Объект испытаний |
выносливости |
о * II |
“ |
||||
|
|
||||||
|
|
|
|
МПа |
% |
|
* |
|
|
|
|
1 |
|
||
|
|
|
|
|
|
|
|
Основной |
металл |
215 |
100 |
|
— |
||
Соединение |
с |
подкладной |
85 |
39,5 |
|
2,5 |
|
планкой |
|
|
|
|
|
|
|
Соединение |
со |
срезанной |
<100 |
<46,5 |
>2,1 |
||
подкладной |
планкой |
|
|
|
|
||
Основной |
металл |
205 |
100 |
|
— |
||
Соединение |
с |
нормальным |
95 |
46,4 |
|
2,2 |
|
стыком |
|
|
|
|
|
|
|
Соединение |
с |
корытообраз |
75 |
36,6 |
|
2,7 |
|
ной планкой |
|
|
|
|
|
|
|
Соединение |
с |
медной под |
55 |
26,8 |
|
3,7 |
|
кладной трубой |
|
|
|
|
|
||
Соединение с плоской планкой |
45 |
21,9 |
|
4,6 |
|||
Соединение |
замковое |
35 |
17,1 |
|
5,9 |
Вид
заготовки
Натурная
модель
ротора
Плита
по зоне сплавления электрошлакового шва на глубине 20—33 мм от поверхности образца. Установлено, что' максимальная протя женность включений до 10 мм обеспечивает предел выносливости, составляющий 85% предела выносливости соединения с без дефектными швами.
На сопротивление усталости односторонних кольцевых стыко вых соединений решающее влияние оказывает качество выполне ния корневой зоны шва. Концентрация напряжений в указанной зоне сварного соединения может быть весьма значительной при отсутствии проплавления корневой зоны шва, неблагоприятной формы корневого шва и наличии дефектов сборки и сварки.
Дефекты конструктивного оформления и технологического исполнения односторонних стыковых соединений могу г приводить к значительному снижению сопротивления усталости сварных соединений.
Рис. 72. Схема вырезки образцов для испытаний на усталость из сварного соединения хвое стовой части натурной модели ротора ЦНД паровой турбины П ВК-150
Опыты ЦНИИТМЛШа [17] при изгибе по симметричному циклу образцов сечением 50 X 75 мм, сварных соединений стали 34ХМ, вырезанных из натурной модели ротора и сварных плит, показали, что эффект ивHole коэффициенты концентрации напряжений свар ных соединений с различными вариантами корневых сечений шва при серьезных конструктивно-технологических нарушениях изме нялись в довольно широких пределах и достигали весьма высоких значений К а = 2,2-е—5,9 (табл. 69).
Из натурной модели ротора вырезали крупные образцыпогоны (рис. 72) с подкладным кольцом и со снятым механической обработкой подкладным кольцом. Сварные соединения плит имели в корневой части шва соответственно (рис. 73): разделку без подкладки — нормальный стык; корытообразную подкладную планку; медную подкладную трубу; плоскую подкладную планку и замковое соединение. Кованый металл подвергали закалке при температуре 860—870 °С в масло и отпуску при 535—600 °С. Сварку производили с предварительным и сопутствующим нагре вом до температуры 300—400 °С. После сварки моделей ротора и плит проводили отпуск при температуре 600 °С, 6 ч. Многослой ную сварку выполняли электродами ЦЛ-30. В натурной модели корневую часть шва выполняли электродами ЦУ-1 (с целью уменьшёния концентрации напряжений в корне шва), дающими мягкую основу (от = 380 МПа, о„ = 530 МПа).
При визуальном осмотре и электромагнитной дефектоскопии образцов перед испытаниями на усталость на образцах с замковым соединением, медной трубой и плоской подкладной планкой были обнаружены значительные технологические дефекты. В пла стинах с замковым соединением не был сохранен зазор 5 X 1,5 мм, который, по мнению конструкторов, должен был играть роль сборника шлака. Образцы с медной подкладной трубой и плоской подкладной планкой имели трещины. На образцах с медной
I t)
Рис. 73. Виды разделок для односторонней сварки плит:
а— нормальный стык; б — с корытообразной планкой; в — с медной подкладной трубой;
г— с плоской планкой; д — замковое соединение
подкладной трубой трещины проходили от корня шва в месте сопряжения с трубой, распространяясь по высоте шва.
На образцах с плоской подкладной планкой трещины распола гались в средней части шва. На каждом образце было по две-три трещины протяженностью 5—7 мм. Плоская подкладная планка оказалась приваренной непараллельно плоскостям образца. При чем планка упиралась боковыми стенками в вертикальный вырез разделки. Медная подкладная труба не сопрягалась по всей своей поверхности с закруглениями разделки, и, кроме того, при сварке она была сильно подплавлена.
Результаты этого исследования указывают на необходимость тщательного контроля при изготовлении односторонних соедине ний с тем, чтобы не допускать отступлений от конструктивнотехнологических решений корневых сечений стыкового шва.
Пониженные значения пределов выносливости рассмотренных сварных соединений не следует относить за счет плохой сварива емости стали 34ХМ. Опытами ЦНИИТМАШа (см. табл. 62) была показана равнопрочность при переменных нагрузках основного металла и сварных соединений стали 34ХМ, выполненных элекрошлаковым способом сварки при применении соответствующей термообработки.
При выполнении соединений встык прежде всего стремятся обеспечить полный провар и получить металл с необходимыми механическими свойствами, без сварочных дефектов. В ряде слу чаев внешней форме шва уделяют меньшее внимание. Вместе с тем сопротивление усталости стыковых соединений в значительной
степени определяется формой и внешними размерами шва. Осо бенно заметное понижение сопротивления усталости отмечается для соединений, имеющих резкий переход от усиления шва к основному металлу из-за значительной концентрации напря жений.
Так, |
при отнулевом |
цикле растяжения образцов сечением |
|||||
38 X 70 мм |
из |
сварного |
соединения |
малоуглеродистой |
стали |
||
BS15 (ов = |
442 |
МПа), |
выполненного |
электрошлаковой сваркой |
|||
с хорошим |
усилением |
шва, был получен предел выносливости |
|||||
а:) = 200 |
МПа. Предел |
выносливости |
сварного соединения |
с не |
благоприятным профилем усиления шва, полученным при сварке
в результате |
несовпадения медных |
ползунов, составил лишь |
|
110 МПа, т. е. понизился на 45%. |
|
||
6. |
УСТАЛОСТЬ |
КРУПНЫХ |
ЭЛЕМЕНТОВ |
КОНСТРУКЦИЙ |
ПОСЛЕ РЕМОНТНОЙ СВАРКИ |
При выявлении различного рода повреждений и дефектов при контроле изделия в процессе изготовления или эксплуатации возникает необходимость в ремонте. Обнаруженные при контроле дефекты полностью удаляют механической зачисткой. Характер ремонта определяется объемом выборки металла. В зависимости от рода и толщины металла, а также размеров конструкции и усло вий ее эксплуатации разрабатывается различная технология ремонтной сварки.
Выбор оптимального ремонтного решения должен базироваться на результатах экспериментальных исследований по сравнитель ной оценке прочности элементов с заваренными выборками или наплавками.
В ЦНИИТМАШе после сварочных ремонтных операций была проведена оценка сопротивления усталости крупных пластин, изготовленных из стали 16ГНМА толщиной 115 мм [2, 16]. На пластинах имитировали наплавку на поверхность отверстия диаметром 99 мм (рис. 74, а) и заварку местной поверхностной выборки (рис. 74, б) применительно к барабанам котлов высо кого давления.
Наплавку отверстий в пластинах выполняли электродами УОНИ-13/55 в соотве!ствии с основными положениями по техно логии ремонта, а также высоконикелевыми электродами ЦТ-36. Отверстия наплавляли в два слоя по спирали на всю толщину пластины. После наплавки отверстия растачивали до диаметра 90 мм, а наплавленный металл вокруг отверстия торцевали резцом заподлицо с поверхностью пластины.
Поверхностный наклеп наплавленного металла в отверстиях пластин выполняли с помощью устройства (рис. 75), основанного на базе пневматического молотка 1 типа МР-6. Устройство уста навливали в отверстие пластины ввинчиванием шпильки 5 в опор ный стакан 4, прикрепленный к пластине. Наклеп отверстия осуществляли тремя бойками 3. Перемещение бойков вдоль отвер-
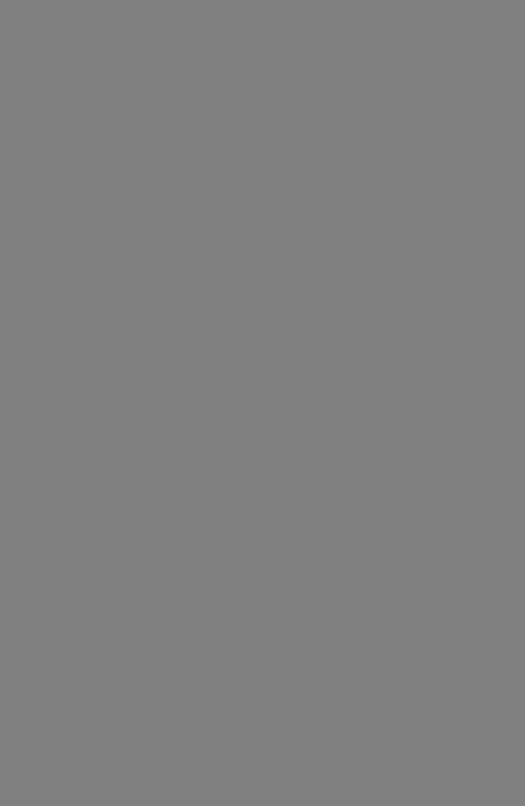