
книги / Усталость крупных деталей машин
..pdfвости в этом случае составило всего 7% по сравнению с гладким валом. Было также показано, что при передаче крутящего момента через ступенчатую втулку (при которой контактное давление на вал 100 МПа сохраняется только в части вала, находящегося в захватах машины, и постепенно уменьшается к торцу втулки) снижение предела выносливости составляет только около 30% предела выносливости гладкого вала. Таким образом, степень снижения сопротивления усталости валов в связи с напрессован ными втулками возрастает с увеличением жесткости втулки. Можно также отметить, что неблагоприятное проявление прессо вых посадок в усталости валов при переменном кручении проявля ется слабее, чем при переменном изгибе (см. главу II).
Из приведенного обзора опытных данных можно также сделать вывод, что влияние посадок на сопротивление усталости при кручении не во всех случаях увеличивается при переходе от простых углеродистых сталей к высокопрочным легированным (см. данные табл. 14 и 19). Это дает основание полагать, что надле жащий выбор состава и свойств легированных сталей может при вести к обеспечению достаточно высокого сопротивления усталости при кручении (по-видимому, и при изгибе) для деталей, несущих неподвижные посадки. Сделать определенные выводы о рациональ ном выборе состава легированных сталей для указанных целей в настоящее время не представляется возможным.
3. УСТАЛОСТЬ ПРИ КРУЧЕНИИ КОЛЕНЧАТЫХ ВАЛОВ
Сопротивление усталости коленчатых валов, как правило, опре деляют зоны галтельных переходов. Поэтому в большинстве слу чаев радиус галтелей у коленчатых валов принимают равным не менее 0,07 диаметра шеек. Наиболее эффективным и технически простым способом повышения сопротивления усталости коленча того вала является поверхностное пластическое деформирование (ППД), при применении которого нет надобности выполнять галтельные переходы коленчатых валов по столь большому ра диусу.
Рис. 26. Коленчатый вал для испытаний на кручение
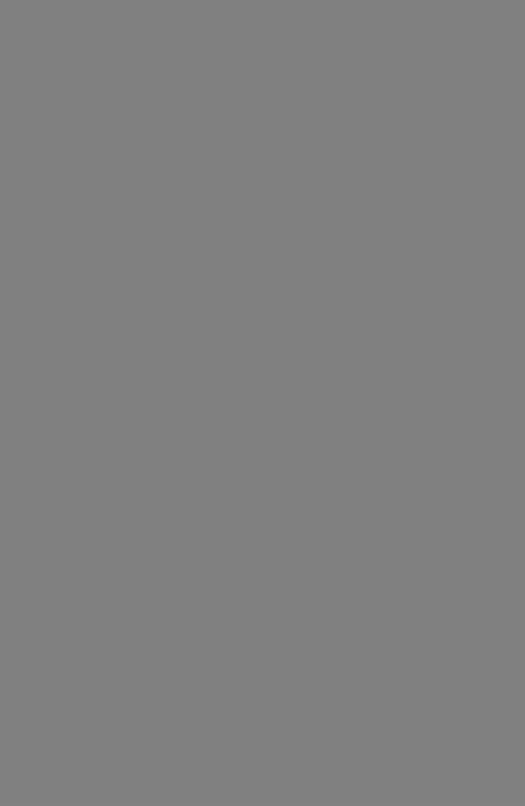
Г л а в а IV
УСТАЛОСТЬ КРУПНЫХ ДЕТАЛЕЙ МАШИН В ЗОНАХ КОНТАКТА
1.УСТАЛОСТЬ КРУПНЫХ ВАЛОВ
СНЕПОДВИЖНЫМИ ПОСАДКАМИ
Сопротивление усталости деталей машин и элементов сооружений резко понижается в зоне контакта сопрягаемых частей. Это необ ходимо учитывать при назначении безопасных напряжений во многих деталях (осях в местах соприкосновения с подшипниками и в зонах напрессованных на них ступиц, всевозможных валах в зонах охватывающих их деталей, рессорных листах, рамных конструкциях, в зонах взаимного контакта элементов и др.). Втулка, напрессованная на вал, может привести к снижению предела выносливости вала в 3—4 раза. Это неблагоприятное влияние контакта усиливается с ростом прочности материала деталей, подвергающихся переменным нагружениям.
Значительный экспериментальный материал накоплен по сопро тивлению усталости валов и осей с неподвижными посадками. Особое значение эта проблема приобрела в связи с оценкой запасов прочности осей подвижного состава железных дорог. По-видимому, первые работы по исследованию сопротивления усталости крупных образцов (натурных локомотивных осей) с неподвижными посад ками были выполнены в США фирмой Темкен еще в начале 40-х годов [12]. Для этих целей была построена специальная машина с вращающимся образцом-осью, закрепленным одним концом.
Испытаниям подвергали оси диаметром в подступичной части 292 мм. Ступица, обод и бандаж были нормальных размеров, таких же как и в эксплуатации. Химический состав и механические свойства осей приведены в табл. 21. Предел выносливости металла осей, определенный на образцах диаметром 6 мм, составлял 389 МПа. Состав (%) и механические свойства осей: 0,24 С, 3,1 Ni, 0,02 S, 0,03 Р, ав = 657, ат = 485 МПа, 6 = 30%, НВ 1920 Н/мм2.
Результаты испытаний на усталость при изгибе (табл. 21) показали, что даже при весьма малых значениях напряжений в подступичной части оси возникают трещины, которые медленно развиваются с увеличением числа циклов. При испытаниях оси не доводили до разрушения, но трещина одной из осей распростра нилась почти до ее центра.
В ЦНИИТМАШе были проведены испытания на усталость при изгибе крупных валов с неподвижно посаженными втулками. Испытывали валы, изготовленные из углеродистых и легированных
Результаты испытаний на усталость осей 0 |
292 мм |
|
||
с напрессованными ступицами |
|
|
||
Натяг |
Напряжен не |
Пробег |
Глубина |
|
|
||||
запрессовки, |
изгиба, |
МПа |
103, км |
трещины, мм |
мм |
|
10\ об |
|
|
0,43 |
134 |
5,7 |
33 |
116,0 |
0,41 |
98 |
19,8 |
112 |
10,3 |
0,41 |
84 |
28,7 |
163 |
52,0 |
0,41 |
74 |
83,8 |
467 |
1,6 |
П р и м е ч а н и е . Пробег в километрах получен пересчетом числа оборотов при диаметре колеса 1,83 м.
Т а б л и ц а 22
Результаты испытаний на усталость при изгибе валов с неподвижными посадками
Сталь |
Вид образцов |
Диаметр |
Предел вы |
|
Коэффи |
|
вала, мм |
носливости, |
|
циент к а |
|||
|
|
|
|
МПа |
|
|
40 |
Гладкие |
|
42 |
245 |
|
_ |
40 |
С неподвижной |
посадкой |
42 |
ПО * |
|
2,2 |
40 |
Гладкие |
|
180 |
200 |
|
_ |
40 |
С неподвижной |
посадкой |
180 |
70 * |
|
2,9 |
40Х |
Гладкие |
|
160 |
330 |
|
_ |
4 0 Х |
С неподвижной |
посадкой |
160 |
135 |
|
2,4 |
40Х Н |
Гладкие |
|
160 |
335 |
I |
_ |
40Х Н |
С неподвижной |
посадкой |
160 |
130 |
|
2,6 |
* Эти |
значения пределов выносливости получены |
началу |
|
образования |
трещин, в остальных случаях по полному разрушению.
сталей на базе 10 млн. циклов. Как видно из результатов испыта ний (табл. 22), неблагоприятное влияние посаженных втулок возрастает с увеличением диаметров испытывавшихся валов.
Накопленные опытные данные показывают, что величина кон тактного давления оказывает влияние как на предел выносливости по трещинообразованию, так и на предел выносливости по разру шению валов. При этом величина предела выносливости по трещи нообразованию снижается линейно с ростом величины контактного давления в пределах от 0 до 100 МПа. Предел выносливости по излому валов с прессовой посадкой также снижается с ростом
Т а б л и ц а |
23 |
|
|
|
|
|
Механические свойства сталей |
|
|
|
|
||
Сталь |
ов, МПа |
ог, МПа |
4'. |
6. % |
ан, кДж/м* |
НВ, Н/мм* |
34Х Н 1М |
887 |
746 |
52,8 |
16,1 |
710 |
2620 |
35 |
540 |
303 |
55,9 |
29,3 |
880 |
1560 |
Т а б л и ц а |
24 |
|
|
|
|
|
Результаты испытаний на усталость гладких валов |
|
|
||||
и валов с напрессованными втулками сталей 34ХН1М и 35 |
|
|||||
|
|
|
|
Предел выносливости валов, МПа |
||
Сталь |
Диаметр |
|
|
с напрессованными |
||
вала, мм |
|
гладких |
||||
|
|
|
|
|
втулками |
|
34Х Н 1М |
12 |
|
305 |
|
185 |
|
|
|
20 |
|
— |
|
145 |
|
|
160 |
|
— |
|
105 |
35 |
|
12 |
|
185 |
|
115 |
|
|
20 |
|
— |
|
115 |
|
|
160 |
|
— |
|
115 |
контактного давления, однако это снижение наблюдается только в пределах 60—80 МПа. Дальнейшее увеличение контактного давления ни приводит к снижению предела выносливости по излому.
В ЦНИИТМАШе при участии НКМЗ и Краматорского инду стриального института были проведены сравнительные испытания на усталость кованых валов из сталей 35 и 34ХН1М. Валы диа метром 12, 20 и 160 мм испытывали с прессовыми посадками втулок. Испытания вели на изгиб с вращением по симметричному циклу при N = 107 циклов. Число циклов до разрушения определяли по моменту излома образца. Объектами исследования являлись шесть натурных гребных валов из стали 34ХН1М диаметром 590 мм, длиной 13 м и массой около 20 -103 кг каждый и один вал из стали 35 диаметром 695 мм, длиной 12 м и массой 37 ПО3 кг. Заготовки подвергали закалке (через воду в масло) и последующему отпуску. Механические свойства исследованных сталей приведены в табл. 23.
Результаты |
испытаний |
всех групп |
валов представлены |
|
в табл. |
24. |
из табл. 24, |
преимущества |
легированной стали |
Как |
видно |
перед углеродистой по величине предела выносливости обнаружи ваются достаточно резко для гладких образцов 0 12 мм и для образцов 0 12 и 20 мм с напрессованными втулками. Однако для
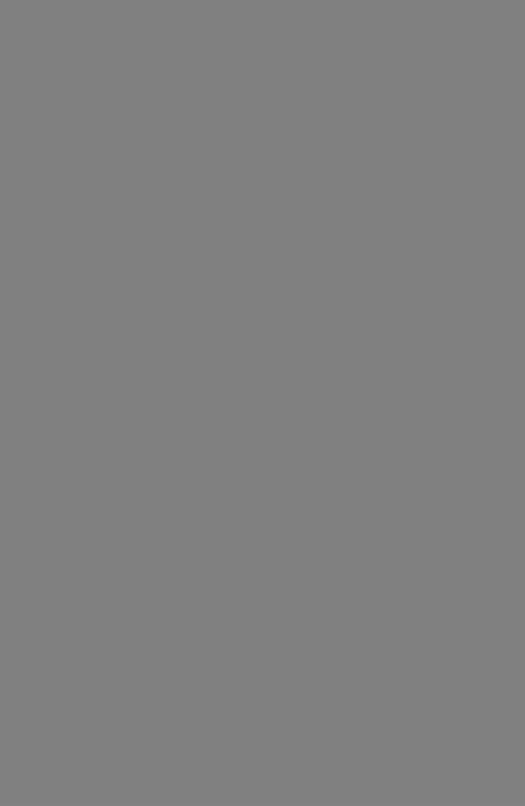
Т а б л и ц а 25
Влияние контакта на сопротивление усталости деталей в зоне контакта
|
|
|
|
Форма и |
размеры |
|
Вид |
Предел вы |
Ко |
|
|
Сталь |
|
|
носливости |
эффи |
|||||
|
|
|
образца |
|
нагру |
в зоне |
циент |
|||
|
|
|
|
|
|
|
|
жении |
контакта |
* 0 |
|
|
|
|
|
|
|
|
|
о_,. МПа |
|
|
|
|
|
|
|
|
|
|
|
|
М алоуглеродистая |
Цилиндрические |
|
Изгиб |
115 |
2,0 |
|||||
а в = |
450 |
МПа |
0 |
12 |
мм |
с напрессо |
с вра |
|
|
|
Хромомолибдено |
ванной |
втулкой |
|
щением |
155 * |
3,3 |
||||
вая о |
в= |
890 МПа |
|
|
|
|
|
|
|
|
|
|
|
Пластины |
толщиной |
Изгиб |
90 |
1,72 |
|||
М алоуглеродистая |
50 |
мм, |
защемленные |
по |
в одной |
|
|
|||
концам |
|
|
|
плоско |
|
|
||||
а и = |
460 |
МПа |
Пластины |
толщиной |
сти |
45 |
3,21 |
|||
|
|
|
|
|||||||
|
|
|
200 |
мм, защемленные |
по |
|
|
|
||
|
|
|
концам |
|
|
|
|
|
|
* По данным А. Тума.
ции напряжений (уменьшение контактного давления, нанесение разгружающих выточек, обеспечение плавных закруглений торцов охватывающих деталей и пр.). Однако это объяснение нельзя считать исчерпывающим. Известно, например, что резкое сниже ние сопротивления усталости охватываемой детали наблюдается даже при весьма малых контактных давлениях. Другой причиной неблагоприятного влияния контакта деталей является так назы ваемая фреттинг-коррозия, т. е. коррозия, возникающая на поверхностях сопрягаемых деталей в связи с их взаимным пере мещением, обусловленным переменным нагружением. Коррозия при указанных перемещениях идет особенно интенсивно, а в уста лостных изломах деталей можно наблюдать значительные местные коррозионные повреждения.
Одной из причин снижения предела выносливости деталей машин в результате контакта может быть и контактное трение, приводящее в условиях циклического нагружения к механиче скому износу соприкасающихся поверхностей.
В процессе износа могут образовываться отколы и поверх ностные надрывы, являющиеся очагами усталостного разрушения детали. Процесс износа поверхности контакта тесно связан с кор розионным процессом. Образующаяся между поверхностью кон такта прослойка окислов может приводить к местному повышению контактного давления или играть роль абразива.
В. С. Иванова и И. А. Одинг 17 ] в результате эксперименталь ных исследований пришли к заключению, что при циклическом нагружении деталей в условиях контактного трения, помимо про
цессов механического износа, имеют место еще и электроэрозионные разрушения, протекающие под действием термоэлектрического тока, возникающего при трении двух металлов [о чем указывалось и в более ранних (1952 г.) работах П. Л. Гордиенко и др. ]. В зави симости от направления термоэлектрического тока, разрушаться будет либо подвергающаяся циклическому нагружению деталь, либо соприкасающаяся с ней поверхность.
Причиной снижения предела выносливости стальных деталей в зонах контакта (заделки) является, по-видимому, совместное проявление концентрации напряжений, электроэрозионного раз рушения поверхности, механического истирания поверхности и фреттинг-коррозии. Степень влияния того или иного фактора может быть в разных условиях различной и определяется мате риалом соприкасающихся деталей и условиями нагружения.
Ниже приведены результаты опытов, проведенных И. В. Куд рявцевым в ЦНИИТМАШе с целью получения дополнительных данных, позволяющих судить о причинах понижения предела выносливости стальных деталей в зоне контакта поверхностей и выбора средств, препятствующих понижению сопротивления уста лости.
2. ВЛИЯНИЕ МАТЕРИАЛА И ТОЛЩИНЫ ПРОКЛАДОК В МЕСТАХ КОНТАКТА НА УСТАЛОСТЬ СТАЛЬНЫХ ПЛАСТИН
Из проката стали СтЗ (0,2% С, НВ 1300 Н/мм2) толщиной 80 мм были изготовлены образцы в виде пластин с постоянным сечением (50x75 мм) по всей длине образца.
Испытания пластинчатых образцов на изгиб в одной плоскости по симметричному циклу с частотой около 2000 в минуту прово дили на машинах УП-50 (см. главу I). Пластины испытывали на усталость в условиях защемления их по концам. Прокладки помещали между стальными плоскими захватами машины и образцом (выступали из захватов на 5—7 мм). Контактное давле ние при этом составляло: от затяжки захватов (постоянное) около 90 МПа и от изгибающего момента (переменное) около
± 3 МПа.
Постоянное контактное давление определяли измерением дефор маций упругих элементов захватов тензометрами конструкции Гугенбергера. Пульсирующее давление определяли расчетом, исходя из изгибающего момента, соответствующего напряжению от изгиба пластины 90* МПа.
При испытаниях предел выносливости пластин определяли по двум признакам: либо по изломам, либо по трещинообразованию. В первом случае образцы считали разрушенными, если в них усталостная трещина была видна невооруженным глазом. Во втором случае образцы считали разрушенными после появления в них усталостной трещины такой величины, которую можно
Результаты испытаний на усталость пластин из стали СтЗ, защемленных по концам [предел выносливости гладких пластин 165 МПа]
Прокладки |
|
|
|
(МПа) |
Коэффициент |
|
|
|
|
пластин |
|
Ко |
|
|
|
Толщи |
по |
по тре- |
ПО |
по тре- |
Материал |
HV |
щнно- |
щино- |
|||
на, мм |
из |
образо- |
из |
образо- |
||
|
|
|
лому |
ванию |
лому |
ванию |
|
|
|
|
|
||
Без прокладок |
— |
— |
78 |
72 |
2,1 |
2,3 |
Прессшпан |
— |
0,4 |
92 |
92 |
1,8 |
1,8 |
|
— |
0,8 |
125 |
115 |
1.3 |
1,4 |
|
— |
1,5 |
125 |
125 |
1.3 |
1,3 |
Цинк |
50 |
0,32 |
125 |
105 |
1.3 |
1,6 |
Коррозионно-стойкая сталь |
180 |
0,8 |
95 |
95 |
1.7 |
1,7 |
Углеродистая сталь |
— |
0,2 |
85 |
75 |
1.9 |
2,2 |
Алюминий |
30 |
1,0 |
85 |
75 |
1.9 |
2,2 |
Медь |
45 |
0,2 |
75 |
75 |
2 ,2 |
2,2 |
» |
45 |
1,0 |
115 |
— |
1.4 |
— |
обнаружить лишь с помощью магнитной дефектоскопии. Для этого образцы, прошедшие базу испытаний (10 млн. циклов), без заметных невооруженным глазом следов разрушения подвергали магнитной дефектоскопии. Результаты испытаний приведены в табл. 26. Было обнаружено, что увеличение толщины прессшпановых прокладок сопровождается увеличением их положительного эффекта.
Если принять во внимание, что прессшпановые прокладки даже самых малых толщин (0,4 мм) не разрушались при испытании образцов, то можно сделать вывод, что предохранение металличе ской поверхности образца от электроэрозионного разрушения достигается уже при малых толщинах прессшпановых прокладок. Таким образом, повышение эффективности прессшпановых про кладок с увеличением их толщины должно быть объяснено только причинами, не связанными с электроэрозионным разрушением (изменением величины концентрации напряжений, условий трения или коррозионных явлений).
Применение прокладок из цинка (6 = 0,32 мм) привело к повы шению предела выносливости пластин с 78 до 125 МПа, т. е, на 60% (по изломам), и с 72 до 105 МПа, т. е. на 46% (по трещине*- образованию).
По данным В. С. Ивановой и И. А. Одинга 17 J, положительное влияние цинковых прокладок можно объяснить тем, что между
цинком и пластиной (образцом) при контактном трении возникает термоэлектрический ток благоприятного направления. Прокладка цинка является анодом и поэтому разрушается, а испытуемый образец служит катодом и не разрушается.
Прокладки из коррозионно-стойкой стали (18% Сг и 12% Ni) по отношению к металлу пластин являются катодами и с точки зрения электроэрозионного разрушения пластин являются небла гоприятными. Этим и следует объяснить меньший эффект от этих прокладок по сравнению с эффектом от прессшпановых или цинко вых прокладок. Однако применение алюминия, меди и коррозион но-стойкой стали для прокладок (хотя и в меньшей степени, чем прессшпана) способствует повышению сопротивления усталости пластин в заделке. Их полезная роль должна, следовательно, складываться из какого-то благоприятного фактора и указанного неблагоприятного. По-видимому, благоприятным фактором при применении прокладок из меди, алюминия и коррозионно-стойкой стали является уменьшение коррозионных явлений на соприка сающихся с прокладкой поверхностях образца. Меньшая корро зионная повреждаемость образцов при применении таких прокла док хорошо обнаруживалась визуальными наблюдениями.
Повышение эффективности медных прокладок с увеличением их толщины следует объяснить (так же как и в случае с прессшпановыми прокладками) соответствующим уменьшением концентра ции напряжений в зоне контакта (уменьшением касательных на пряжений у поверхностей контакта).
Некоторое повышение предела выносливости защемленных
взахватах пластин с применением прокладок из углеродистой стали можно объяснить уменьшением истирания в зонах контакта
всвязи с малым относительным перемещением опорной части образца и контактирующейся с ним плоскости.
3. ВЛИЯНИЕ ЧАСТОТЫ НАГРУЖЕНИЯ НА СОПРОТИВЛЕНИЕ УСТАЛОСТИ ВАЛОВ
ВЗОНЕ НЕПОДВИЖНЫХ ПОСАДОК
Принято считать, что изменение частоты нагружения гладких валов от 100 до 6000 циклов в минуту не сказывается на их пределе выносливости при испытаниях в воздушной среде. С этим можно согласиться, если иметь в виду гладкие лабораторные образцы. При испытании крупных образцов повышение частоты до 1500— 2000 циклов в минуту может сопровождаться заметным нагревом образцов. В связи с этим не исключены изменения сопротивления усталости. Это особенно относится к деталям, несущим неподвиж ные посадки втулок. Так, по опытным данным Р. М. Погорецкого (табл. 27), изменение частоты изгибных нагружений от 500 до 3000 циклов в минуту приводило к снижению предела выносли вости при симметричном цикле от 9 до 17%. При этом наибольшее уменьшение отмечено для валов с большим диаметром.