
книги / Усталость крупных деталей машин
..pdfРис. 54. Модели трехсекционного сборного ротора:
а — со стыками на бочке (модели № 9 и № 11); б — со стыками по кольцевым выточ
(модель № 10):
/ — концевик; 2 — бочка; 3 — стяжка
кие стяжки и различные параметры резьбы. Основные характе ристики, определяющие несущую способность модели ротора (амплитуда изгибающего момента и долговечность при цикличе ском нагружении до усталостного повреждения) у модели № 9 выше, чем у каждой из предшествующих моделей. Наивысшее значение амплитуды изгибающего момента, при котором испыты вали модель № 9, составило МнзГ = 170 кН-м. При этой величине изгибающего момента экспериментально определенные напряже ния на поверхности модели на полюсе посередине между стыками
в |
зоне максимального нагружения при изгибе |
составили |
= |
= |
45 МПа. Общая долговечность при ступенчатом |
нагружении мо- |
дели(при напряженияхах= 15,сг2=20, о3=30, |
сг4= 4 0 и<х5=45МПа) |
до усталостного повреждения составила |
А7= 4 ,7 -1 07 циклов. |
Т а б л и ц а 56
Результаты испытаний на усталость крупных пропорциональных моделей сборного ротора четырехполюсного генератора
Тип и диаметр
Модель ротора стяжки, вид резьбы
Пятисекционная без шпонок на сты ках, № 1
Пятисекционная со шпонками на сты ках, № 2, № 3
Трехсекционная с радиальными штиф-
тами иа стылах, № 4
Гладкая
0 90 мм,
Уя 90Х 5 X 4 5 °
Гладкая
0 90 мм,
Уп 9 0 Х 5 Х 4 5 °
Гладкая
0 90 мм,
У/г9 0 Х 5 Х 4 5 °
Гладкая 0 ПО мм,
УпООХ 5 Х 45°
|
стыка,окМПа |
Амплитудаизгиба моментающего Мн, м-кН |
а (МПа) на |
||
|
эксперимен- 1 тальные |
расчетные1 |
|||
|
|
|
полюсе по |
||
|
|
|
середине ме |
||
|
|
|
жду стыками |
||
0рас |
|
|
|
|
|
стяжки, |
|
|
|
|
|
МПа |
|
|
|
|
|
220 |
|
35,1 |
7 |
7 |
|
|
17 |
12 |
|||
|
81,9 |
||||
|
|
||||
|
1 |
|
|
|
|
256 |
269 |
35.1 |
11 |
10 |
|
|
|
52,6 |
|||
|
|
6 3 .2 |
13 |
11 |
|
300 |
236 |
58,5 |
17 |
16 |
|
|
|
||||
400 |
270 |
43,8 |
12 |
10 |
|
16 |
14 |
||||
|
|
58,5 |
|||
|
|
87,7 |
24 |
21 |
|
|
|
117 |
32 |
27 |
|
|
|
38 |
34, |
||
|
|
140,4 |
арасч» МПа
стыка |
коль |
вы |
|
в зоне |
в зоне |
цевой |
точки |
Число |
|
|
|
циклов |
Характер поврежден |
||
нагруже |
|||
ния N |
|
|
|
3 , 8 - 10е |
Без повреждений |
||
6 , 2 - 10е |
Смещение |
секций |
|
|
в окружном и |
радиаль |
|
|
ном направлениях |
||
1 .7 - |
Б ез повреждений |
||
107 |
|
|
|
1 .8 - 107 |
Разруш ение |
шпоноч |
|
1 , Ы 0 7 |
|||
|
ных соединений |
||
1 ,5 - 107 |
Разрушение |
шпоноч |
|
|
ного |
соединения |
|
2* 10е |
Без |
повреждений |
|
107 |
|
|
|
107 |
|
|
|
107 |
Разруш ение |
по резьбе |
|
3 - 10е |
стяжки |
|
Трехсекционная с радиальными штиф
тами на сты ках, № 5
Ко 6
Ко. 8
Ко 9
|
Гладкая |
300 |
417 |
15 |
|
1 |
|
|
|
||||
0 |
130 мм, |
|
|
25 |
|
|
У п 130Х 5 X 4 5 ° |
|
|
33 |
|
|
|
|
|
|
|
38 |
|
|
|
|
|
|
25 |
|
|
|
|
|
|
30 |
|
|
|
Гладкая |
|
|
38 |
|
|
|
|
|
|
|
|
|
0 |
110 мм, |
|
|
|
|
|
Уп\ 1 0 X 5 X 4 5 ° |
|
|
25 |
|
|
|
|
|
|
|
|
|
|
|
|
|
|
40 |
|
|
Ступенчатая |
— 370 |
— 230 58,5 |
15 |
17 |
27 |
|
0 |
135/90 мм, |
(на диа |
77,2 |
20 |
23 |
36 |
У л 1 3 0 Х 5 Х 4 5 ° |
метре |
117 |
30 |
34 |
55 |
|
|
|
90) |
158 |
40 |
46 |
74 |
|
|
|
170 |
45 |
50 |
80 |
Ко |
10 |
|
Гладкая |
300 |
287 |
129 |
30 |
32 |
183 |
60 |
|
|
0 |
110 мм, |
|
|
171 |
40 |
42 |
240 |
80 |
|
|
Уп\ 1 0 X 5 X 4 5 ° |
|
|
184 |
45 |
46 |
260 |
86 |
|
Ко. |
И |
Ступенчатая |
— 400 |
— 227 |
192 |
42,5 |
47,5 |
205 |
89 |
|
|
|
0 |
135/90 мм, |
(на диа |
|
210 |
46 |
52 |
224 |
98 |
|
|
У л 130Х 5 Х 45° |
метре |
|
|
|
|
|
|
|
|
|
|
|
90) |
|
|
|
|
|
|
Ю7 • 107
2* 107
3 .1 0 е
ю 7 107 2-10®
5-10®
9-10®
ю7
ю7
ю7
ю7
7 .1 0 е
107 ю 7
38-10®
ю7
1,6-10®
Б ез повреждений
Разрушение по резьбе стяжки
Без повреждений
Разруш ение по резьбе стяжки
Без повреждений
Разруш ение по резьбе стяжки
Б ез повреждений
Разруш ение по шейке
Без повреждений
Разруш ение по резьбе стяжки
Без повреждений
Разруш ение по резьбе стяжки
П р и м е ч а н и я : |
1. |
Секции и стяжки моделей роторов К» I и 2 изготовлены из стали 34XH3M, для остальных моделей — из стали |
|||
25ХНЗМФА. |
|
|
и |
2 полюсы роторов при испытании в машине располагали под углом 45° относительно плоскости максимального |
|
2. |
В моделях № 1 |
||||
изгиба, |
в остальных |
моделях пару полюсов располагали в плоскости максимального изгиба. |
|||
3. |
Модель |
7 |
отсутствует в связи с тем, что этот номер был присвоен модели в сварно-сборном исполнении. |
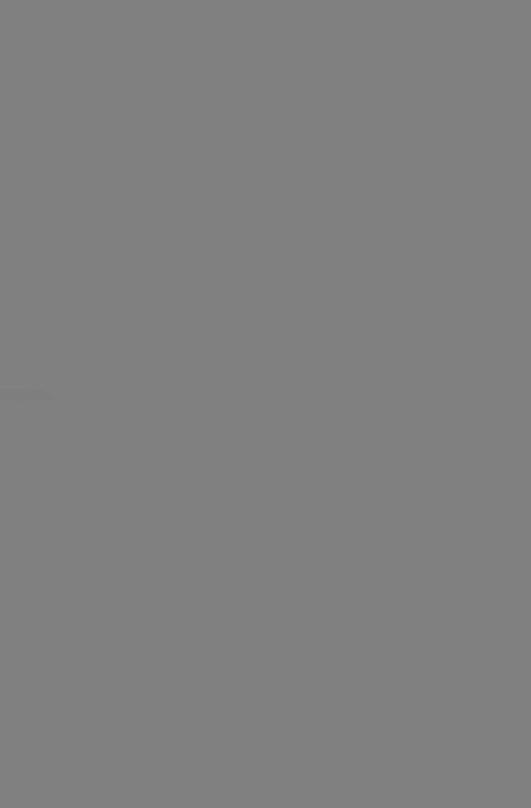
Рис. 56. Распределение напряжений на поверхности среднего зубца модели № 2 пяти-
секционного ротора при статическом нагружении Л!изг:
1 - 11, 7; |
2 — 23,4; 3 — 35, 1; 4 — 46,8; |
5 — 58,5; 6 - 70,2; 7 - 81,9 кН-м ( / - / / / - |
|||
стыки) |
|
|
|
|
|
Аналогичная зависимость имеется и для коэффициента кон |
|||||
центрации |
напряжений а х |
в |
круговых |
галтелях ступенчатых |
|
валов |
при |
кручении [21 ]. |
Эти формулы |
(для определения а„ |
и а т) сохраняют необходимую точность во всем диапазоне соотно шений геометрических размеров ступенчатых валов, с которыми приходится встречаться в машиностроении. Значения теорети ческого коэффициента концентрации напряжений для круговой галтели модели ротора составили а„ « 3,1 при расчете по этой формуле [21 ] и а„ — 2,92 по графикам коэффициентов а„ для изгибаемого ступенчатого кругового стержня с кольцевой гал телью [27].
Модель № 10 (со стыками по кольцевым выточкам) и модель № 11 (аналогичная модели № 9) при напряжении на бочке, соот ветствующем последней ступени нагружения модели № 9 (сг = = 45 МПа), воспринимали амплитуды изгибающих моментов Мизг = 184 и Л4иЯГ = 210 кН-м (большие по величине, чем у мо дели № 9).
В обоих случаях на последней ступени нагружения отмечали нарушение плотности стыка на моделях № 10 и № 11 и поврежде ние резьбы стяжек. В моделях № 10 и № 11 отношение изгиба ющих напряжений в стыке при циклическом нагружении к кон тактным напряжениям в стыке ост/<гк было высоким и составило
соответственно 90,6 и 98,4%. В модели № И были |
высокими |
и средние растягивающие напряжения в стяжке (сгр = |
400 МПа), |
которые накладываются на амплитудные изгибающие напря жения.
Для обеспечения большей долговечности при циклическом нагружении следует обеспечивать при сборке моделей ротора опти мальный уровень ар в стяжке, и отношение аст/ак, видимо, не должно превышать 0,7—0,8. В моделях № 10 и № 11 расчетные напряжения в зоне кольцевой выточки были выше, чем в модели № 9. Однако усталостные повреждения этих моделей произошли
не от |
галтельного |
сопряжения. |
|
= |
В |
модели № 10 |
растягивающие напряжения в стяжке сгр = |
300 МПа были ниже напряжений в стяжках моделей № 9 (сгр = |
|||
= |
370 МПа) и № 11 (Ор = 400 МПа), но имели место высокие по |
||
уровню изгибающие напряжения в стыке (аст = 260 МПа). |
|||
|
Указанные факторы привели к нарушению плотности стыка |
||
и |
повреждению резьбовых стяжек. |
||
|
Следует признать перспективной конструкцию трехсекцион |
ной модели ротора с размещением стыков вне бочки ротора, по кольцевой выточке (шейке). В этом случае предусмотрели более длинную стяжку I = 1600 вместо I = 970 мм на предыдущих моделях. Стяжка становится более податливой, а резьбовые головки располагаются в концевых секциях. Надо иметь в виду, что зона галтельного сопряжения с высокой концентрацией на пряжений (аа « 3 ,1 ) в модели № 10 располагается в поле сжима ющих напряжений, наводимых стяжкой при сборке ротора.
С целью дальнейшего повышения несущей способности сборной конструкции ротора при циклическом нагружении следует реко мендовать упрочнение поверхности наклепом (впадин резьбы
стяжки и |
зоны галтельного сопряжения кольцевой выточки) |
|
[18, |
301. |
|
В |
табл. |
57 приведены значения эффективных коэффициентов |
концентрации напряжений и оценена эффективность поверхно стного упрочнения пластическим деформированием стали 25ХНЗМФА на образцах диаметром 18 мм с различной степенью концентрации напряжений. Образцы изготовляли из поковки диаметром 625 мм, длиной 3 м и массой 7• 103 кг из стали 25ХНЗМФА, выполненной из слитков вакуумно-дугового пере плава. Образцы, закрепленные одним концом, испытывали при изгибе с вращением на машине У-20 конструкции ЦНИИТМАШа при частоте нагружения 3000 цикл/мин на базе 107 циклов.
После обкатки роликом дна надреза сопротивление усталости образцов значительно возросло: для образцов с круглой выточкой на 97%, для образцов с V-образной выточкой на 136%. Поверхно стный наклеп существенно снизил чувствительность стали 25ХНЗМФА к концентрации напряжений, что подтверждает высо кую эффективность поверхностного упрочнения для повышения сопротивления усталости.
Экспериментальный и промышленный опыт ЦНИИТМАШа по казывает, что эффективность поверхностного пластического де формирования зон концентрации напряжений в повышении со противления усталости с ростом размеров деталей сохраняется
Т а б л и ц а 57
Пределы выносливости образцов диаметром 18 мм из стали 25ХНЗМФА
сг_ |К, МПа
Вид надреза
Исходное i.адре. состояние обкатьы роликом
R1 |
1 ,6 - 1 ,8 |
180 |
|
355 |
0 ,8 — 0,9 |
115 |
2 , 6 - 2 ,7 |
295 |
1 .0 - 1 ,1 |
П р и м е ч а н и е . Для гладких образцов ст_, = 295-г315 МПа.
[17]. Применение поверхностного наклепа может в значительной мере или полностью нейтрализовать неблагоприятное действие концентрации напряжений (надрез, защемление, сварной шов).
Напряженное состояние ответственных зон сборного ротора изучали на моделях № 2 и № 3.
Деформации при статических нагружениях определяли как на зубцах, так и на полюсах моделей сборного ротора в различных зонах: на стыках, вблизи стыков и на различных удалениях от стыков. Измеряли также деформации на кольцевой выточке кон цевой секции и на галтельном сопряжении выточки с торцовой поверхностью бочки. Для измерения деформаций использовали малобазные фольговые тензорезисторы ФКПА-0,8 (база 0,8 мм, сопротивление 70 Ом), так как вблизи стыков и на самих стыках имеются значительные градиенты напряжений.
В основном тензорезисторы наклеивали на среднем зубце и на полюсе на растянутой стороне моделей сборного ротора, рас положенных в плоскости максимального изгибающего момента. Дополнительно наклеивали тензорезисторы и на сжатую сторону ротора.
Был выполнен значительный объем исследований — на две модели ротора было установлено 580 тензорезисторов 1. Выбран ное расположение тензорезисторов позволило составить предста вление о характере распределения напряжений в сборной кон струкции ротора на поверхности среднего зубца модели ротора № 2 при различных ступенях нагружения (см. рис. 56).
1 Тензометрические |
измерения проводили с участием канд. техн . наук |
М. И. Этингоф и инж. |
С. Д . Щ ербатых. |
Проведенный широкий комплекс экспериментальных исследований напряженного состояния и сопротивления усталости круп ных моделей сборных роторов показал принципиальную возмож ность создания четырехполюсных роторов мощных турбогенера торов в сборном исполнении.
Результаты испытаний на усталость крупных моделей (Ml 5) позволили провести оптимизацию сборной конструкции и рекомен довать мероприятия по повышению ее сопротивления усталости, что дало возможность перейти к непосредственному промышлен ному освоению генераторов мощностью 50 и 500 мВт с четырех полюсными роторами.
Конструктивно-технологические принципы, использованные при сборке роторов, применяют при проектировании самых круп ных составных опорных валков прокатного стана «5000».
Результаты испытаний на усталость моделей диаметром 260 мм показали принципиальную возможность использования для газовых турбин сборной штифтовой композитной конструкции ротора.
Глава VII
УСТАЛОСТЬ СВАРНЫХ РОТОРОВ ТУРБИН И ГЕНЕРАТОРОВ
При создании из нескольких поковок металлоемких конструкций роторов турбин и генераторов применение сварки дает наиболее рациональное решение проблемы. Однако обеспечение должного запаса прочности в зонах сварных соединений приобретает для этих случаев особенно важное значение.
Применение сварки в крупных конструкциях роторов из леги рованных сталей может привести к недостаточно высокому уровню прочности при циклическом нагружении из-за неблагоприятного сочетания сварочных остаточных напряжений, резкой концентра ции напряжений и сварочных дефектов в опасной корневой зоне. Поэтому основное внимание следует обратить на обеспечение долж ного уровня сопротивления усталости сварных соединений.
Применение сварки является весьма перспективным техноло гическим решением при создании композитных роторов газовых турбин из разнородных материалов.
1. СВАРНЫЕ КОМПОЗИТНЫЕ РОТОРЫ ГАЗОВЫХ ТУРБИН
В ЦНИИТМАШе разработана технология сварки и термообра ботки композитного ротора газовой турбины.
Испытания на усталость проводили на крупных сварных мо делях, отражающих различные конструктивно-технологические решения — формы разделок кромок под сварку, конструкции кор невой части шва, композиции электродов и термообработки [17]. Модели композитного ротора представляли собой крупные ци линдрические полые образцы диаметром 250 мм, выполненные из двух дисков никелевого сплава ХН70ВМЮТ (ЭИ765) и двух
концевиков из аустенитной |
стали Х16Н25М6 |
(ЭИ395) (рис. 57) |
|
и |
имеющие, таким образом, сварные стыки |
из однородных |
|
и |
разнородных материалов. |
|
|
|
Стыки ротора собирали |
на прихватках с установкой на спе |
циальном манипуляторе с роликовыми опорами. Корневые слои выполняли в двух вариантах: на расплавляемой вставке из проюлоки Х15Н65М15 (аргонодуговая сварка вольфрамовым элек тродом) и на непроплавляемом подкладном кольце из стали
±
Трещина усталости
Рис. 57. Схемы моделей сварных композитных роторов для испытания на усталость:
а — модель с жесткими концевиками, сварной стык с подкорневой полостью; б — модель с уменьшенной жесткостью концевиков, сварной стык без наличия подкорневой полости; в — сварной стык с оставшимся подкладным кольцом; г — сварной стык с присадочной плавящейся вставкой; 1 , 4 — сталь Х16Н25М6 (ЭИ395); 2, 3 — сплав ХН70ВМЮТ (ЭИ765)
12Х18Н9, наплавленном электродами ЦТ-28. Заполнение разделок выполняли электродами ЦТ-28 (наплавленный металл Х15Н60М15В4). Было исследовано несколько вариантов термо обработки сварного ротора. Наилучшим оказался следующий. Перед сваркой поковки из сплава ХН70ВМЮТ подвергали за калке при температуре 1150°С (3 ч) в масле, поковки из стали Х16Н25М6 — закалке 1180 °С (3 ч) в воде. Термообработка ротора после сварки: нагрев до температуры 550 °С со скоростью 100— 150 °С, выдержка при этой температуре 1 ч, нагрев до 950 °С со скоростью 100 °С, выдержка 2 ч, охлаждение с печью до 800 °С, выдержка 20 ч, охлаждение с печью до 400 °С, а затем на воздухе. Испытания проводили на машине У-200 [44 ] по той же методике, что и для сборных композитных роторов (см. гл. VI).
Было испытано на усталость восемь моделей сварного ротора. Результаты испытания пяти крупных моделей ротора, имевших резкие концентраторы напряжений в подкорневой полости шва и выполненных с меньшей податливостью (/х = 20 мм) сопряга емых элементов (рис. 57, а), показали, что они имеют низкие раз рушающие напряжения, равные 34—51 МПа при долговечности, равной 1,8- 10е—2 - 107 циклов. В изломах этих моделей были обна-