
книги / Фосфогипс и его использование
..pdfсом 4 под давлением через форсунку 6 впрыскивают во вращающуюся печь 8, работающую в режиме противотока. В печи происходят сушка, затем дегидра тация фосфогипса, диссоциация карбоната кальция и спекание материала при 850—880 °С, который из печи поступает в приемный бункер 14. Отходящие газы очищают в циклоне 3 и электрофильтре 5, а уловленную пыль вновь возвра щают в печь 8.
Обожженный материал подвергают грубому помолу (дроблению) в мо лотковой дробилке 13, а затем через расходный бункер направляют в шаровую мельницу 12. Воздух из бункера и от аспирации мельницы очищается в си
стеме 7. Измельченный готовый |
продукт |
пневмонасосом 11 |
перекачивается |
|||
в силос 9, снабженный системой обеспыливания 7. |
|
|||||
Параметры процесса приведены ниже: |
|
|
|
|||
Отношение Ж :Т |
в фосфогипсе, |
подаваемом |
на обжиг |
1,5 |
||
Температура, °С: |
газа |
|
|
|
850—900 |
|
обжигового |
|
|
|
|||
материала послехолодильника |
|
|
150—200 |
|||
Крупность |
частиц последробления, мм, не |
более |
25 |
|||
Удельная |
поверхность готового |
продукта |
(по воздухопрони |
|
||
цаемости), |
тыс. см2/г |
|
|
|
3,5 —4,0 |
Основные проектные технико-экономические показатели
производства обоих видов |
ангидритовых вяжущих приведены |
|||
ниже: |
|
|
|
|
Годовая мощность, |
тыс. т |
4 |
||
Капитальные |
вложения в объекты |
основного производственно |
||
го назначения, руб/т |
|
34,8 |
||
Удельные затраты: |
|
|
|
|
топлива, т |
у. т. |
|
|
0,16* |
электроэнергии, |
кВт-ч/т |
160 |
||
Себестоимость вяжущего, |
руб/т |
18,2/18,8** |
||
Численность |
работающих, |
чел. |
216 |
* По нашим данным затраты топлива выше (см. рис. 3-3).
** В числителе — для вяжущего с добавкой фтористых солей, в знаменателе — алунитовой породы.
3.5. ПРОИЗВОДСТВО ГИПСОВЫХ ВЯЖУЩИХ ИЗ ФОСФОПОЛУГИДРАТА
Фосфополугидрат сульфата кальция по содержанию основного вещества (a-форма), водопотребности, плотности и ряду дру гих показателей соответствует автоклавным (высокопрочным) гипсовым вяжущим марок Г-10—Г-19 по ГОСТ 125—79. Одна ко вследствие особенностей условий получения (концентрация раствора фосфорной кислоты и содержание примесей), в отли чие от автоклавных вяжущих из природного сырья и фосфогип са, в исходном виде фосфополугидрат практически не обладает вяжущими свойствами.
Установлено (рис. 3-30), что причиной недостаточных вяжущих свойств являются пониженная скорость растворения и растворимость фосфополугидрата {23Г|.
Низкая гпдратацнонная активность фосфополугндрата сульфата кальция объясняется [231] образованием на поверхности кристаллов пассивирующих пленок и изменением кристаллохнмическпх характеристик полугидрата в ре зультате внедрения примесей. При растворении в большом количестве дистил-
Рис. 3-30.
С Са504 ’ 2 / Л £ c a S 0 4 -0,5H 20>% Кинетика гидратации и изменения концентрации C aS04 при твердении различных видов полугидрата сульфа та кальция:
/ — полугидрат а-модификацни из природ
ного гипсового камня; 2, 3, |
4 — фосфополу- |
||||
гидрат производства |
ЭФК |
соответственно |
|||
Винницкого |
химического завода, Сумского |
||||
ПО |
«Химпром», Красноуральсксго |
меде |
|||
плавильного |
комбината; |
сплошные |
ли |
||
нии-изменение содержания CaSO4-0,5H.>O |
|||||
во |
времени |
(кинетика |
процесса); пунктир |
ные линии — изменение концентрации CaS04, растворенного в жидкой фазе сус пензии
лированной воды на месте кристаллов фосфополугидрата остается полупроз рачная нерастворившаяся часть, которая полностью сохраняет форму исходного кристалла, хотя составляет от 3,7 до 4,4% от массы исходного фосфополу гидрата. Эта часть является как бы каркасом (скелетом) исходного кристалла, внутри которого располагается полугидрат сульфата кальция. Химический состав нерастворившейся части фосфополугидрата различных предприятий: 7,42— 12,8% СаО; 2,41—6,25% S 0 3; 3,55—5,81% F; 14,49—21,18% Р20 5; 13,21— 15,78% РЗМ; 9,76— 16,07% Н20; 6,66— 17,70% остатка, нерастворимого в со ляной кислоте.
Сделан вывод о том, что не растворившаяся в воде часть фосфополугид рата не механическая примесь, а содержит в своем составе активные соединения, оказывающие существенное влияние на его гидратацию. Образование каркаса
объясняется замещением в кристаллической решетке полугидрата ионов |
Са2н |
|
и S 0 42- |
на близкие по размерам ионы примесей (Sr2+, La3+, Ge3+, Рг3", Р 0 43“, |
|
S i0 32“ |
и др.) [851. Наличие в фосфополугидрате внедренных примесей |
под |
тверждается другими исследователями [249, 251, 252].
Основные работы по использованию фосфополугидрата для получения гип совых вяжущих ведутся в трех направлениях:
гидратация до гипса и получение качественного сырья для производства автоклавных и обжиговых вяжущих;
активация с сушкой и получением гипсовых вяжущих или использование во влажном состоянии для изготовления изделий или гранул и брикетов для цементной промышленности;
обжиг до ангидрита с введением активаторов твердения и других добавок. Гидратацию фосфополугидрата (до гипса) можно проводить в виде сус пензии или при его естественной влажности. Гидратация в суспензии позволяет получить более «очищенное» сырье и соответственно вяжущее более высокого качества [2311. Недостатком данного способа является высокая влажность полученного сырья, что имеет большое значение при его переработке обжиго вым способом. При производстве из полученного гипса автоклавных вяжущих его влажность не имеет значения ;[173]. Для производства обжиговых вяжу щих более предпочтительна гидратация фосфополугидрата с естественной влажностью. Это обеспечивает сравнительно невысокую влажность сырья (при
мерно 5— 10%) и соответственно низкий расход топлива при обжиге.
На основе фосфополугидрата получены различные виды вяжущих, пока затели свойств которых не уступают показателям свойств вяжущих из природ ного гипсового камня I и II сортов (содержание гипса соответственно не ме нее 95 и 90%). Данные зарубежных фирм также подтверждают чистоту полу чаемого этим способом сырья и качество вяжущих на его основе [пат. 1950658 ФРГ, 1977; 164]. Такой вариант утилизации фосфополугидрата, на наш взгляд, является практически единственным перспективным вариантом, по
скольку он в наибольшей степени обеспечивает стабильность и высокое каче ство готового продукта. Однако наиболее «привлекательным» с экономической точки зрения является второе направление, т. е. непосредственное получение изделий из влажного фосфополугидрата или его сушка и получение порошко образного вяжущего. Именно этим можно объяснить наибольшее число работ в этом направлении [164, 231, 246—251].
На основе фосфополугидрата Винницкого химкомбината им. Я. М. Сверд лова разработана технология вяжущего, основанная на снижении пассиви рующего действия пленок механической обработкой и нейтрализацией кислых примесей [231]. Получено гипсовое вяжущее, соответствующее требованиям нормативных документов.
Работами УПИ им. С. М. Кирова показана возможность получения вяжу щего в процессе сушки фосфополугидрата с последующим введением актива торов твердения, в качестве которых рекомендуются различные фтористые со ли. Лучшие результаты получены при введении кремнефтористоводородной
кислоты, нейтрализованной |
аммиаком. |
Оптимальное |
значение |
pH находится |
в сравнительно небольшом |
интервале |
(от 0,3 до 1,51 |
единицы) |
и зависит от |
количества вводимой кислоты. При содержании кислоты 0,4% (в пересчете на фтор) интервал минимальный, а при более высоком— увеличивается [246]. Активирующее действие добавки разработчики объясняют образованием кол лоидного фторида кальция, который способствует гетерогенному зарождению кристаллов гипса. На наш взгляд, такое объяснение нельзя считать полным, так как из данных рис. 3-30 следует, что лимитирующей стадией при тверде нии фосфополугидрата является скорость его растворения.
По данным ЛИСИ, нейтрализация фосфополугидрата различными щелоч ными добавками в сочетании с механической обработкой в бегунах позволяет без сушки фосфополугидрата получить смеси, из которых методом прессова ния можно изготавливать различные виды изделий [24, 250]. Данный способ рекомендован для внедрения на Волховском алюминиевом заводе.
Гипрохиму фирмой «Ргауоп» (Бельгия) передана проба фосфополугидрата, полученного при производстве экстракционной фосфорной кислоты дигидрат- но-полугидратным способом, который обладает вяжущими свойствами. По результатам испытаний, выполненных во ВНИИстроме, этот материал имеет следующие показатели свойств:
Водопотребность (поГОСТ |
125—79), |
% |
32 |
||
Предел прочности при сжатии, МПа: |
|
|
|||
через |
2 ч |
|
|
1,9 |
|
через |
1 |
сут. |
|
|
22,5 |
через |
28 |
сут.хранения |
вкомнатных |
условиях |
49,4 |
Сроки схватывания, мин: |
|
|
|
||
начало |
|
|
|
15 |
|
конец |
|
|
|
|
24 |
Третье направление, т. е. обжиг фосфополугидрата до ангидрита, описано в предыдущем разделе.
Однако, несмотря на простоту большинства способов и неплохие (по ли тературным данным) показатели свойств, ни одно из предложений не реализо вано даже в постоянно действующих опытных установках. По мнению автора, в настоящее время отсутствует необходимая для внедрения стабильность и воспроизводимость технологических параметров и показателей свойств вяжу щих и изделий, так как они в решающей степени определяются свойствами фосфополугидрата, «заложенными» при его образовании.
Из ориентировочного технико-экономического анализа опи санных направлений использования фосфополугидрата в строи тельстве следует, что при условии положительного решения еще имеющихся вопросов, наиболее перспективным является его непосредственное (без обжига, гидратации, дегидратации и т. п.)
использование для изготовления строительных изделий и гра нул или брикетов для цементной промышленности на месте об разования, а также получение путем сушки и помола порошко образного вяжущего, использование которого возможно в дру гом месте. Причем успех может быть обеспечен только при ус ловии комплексного подхода к проблеме, заключающегося в том, что полугидратный процесс экстракции фосфорной кис лоты должен рассматриваться как процесс, предназначенный
втом числе для получения фосфополугидрата со свойствами, необходимыми для его успешного последующего использования
впроизводстве гипсовых вяжущих или строительных изделий.
Некомплексный подход к использованию сырья привел к тому, что усилия специалистов по производству ЭФК ранее были направлены на получение пас сивированного фосфополугидрата, «удобного» для транспортирования в отва лы, а специалистов по строительным материалам — на его активацию. Послед нее, по мнению автора, проще и целесообразнее осуществить в процессе кри сталлизации полугидрата, что возможно только при совместных исследованиях и заинтересованности в конечном результате (получение ЭФК и вяжущего или изделий) обеих сторон. При таком подходе не исключена целесообразность двухстадийного (дигидратно-полугидратного) процесса получения ЭФК (см. гл. 1).
3.6. НОМЕНКЛАТУРА, СВОЙСТВА И ПРИМЕНЕНИЕ ГИПСОВЫХ МАТЕРИАЛОВ И ИЗДЕЛИЙ
По виду и назначению гипсовые материалы подразделяют на сухие смеси заводского изготовления, перегородочные, листовые, стеновые и отделочные изделия.
Сухие смеси заводского изготовления. Такие смеси предназначены для вы полнения различных видов работ в строительстве. Обязательным условием их успешного применения является тщательное смешение в заводских условиях всех компонентов смеси с тем, чтобы на строительной площадке ввести в них
только воду до получения |
масс требуемой подвижности. |
Г и п с о в ы е ш т у к |
а т у р н ы е с м е с и предназначены для отделки |
(«мокрой» штукатурки) внутренних поверхностей стен, а также потолков и пе
регородок |
из |
мелкоштучных |
материалов (кирпича, различных камней |
и др.). |
||
Основные требования к штукатурным смесям приведены ниже: |
|
|||||
Подвижность |
(расплыв по |
прибору |
Суттарда), мм |
120 |
||
Сроки схватывания, мин: |
|
|
|
|||
начало, |
не |
ранее |
|
|
60 |
|
конец, |
не позднее |
|
не менее |
90 |
||
Водоудерживающая способность, %, |
98 |
|||||
Прочность |
сцепления с основанием, |
МПа, неменее |
0,3 |
|||
Предел прочности при сжатии в сухом состоянии, МПа, не менее: |
|
|||||
при |
рСр=800 — 1000 кг/м3 |
|
|
2 |
||
при |
рср< 8 0 0 кг/м3 |
|
|
1 |
Кроме того, при нанесении на оштукатуриваемую поверхность смеси долж ны обладать способностью заглаживаться металлическим инструментом и нс растрескиваться.
Для придания необходимых свойств в смеси необходимо вводить водо удерживающую добавку (высокомолекулярные полимеры: метилцеллюлозу, полиоксиэтилцеллюлозу и др.). В зависимости от вида вяжущего необходимо применение замедлителей (для гипсовых) или, наоборот, ускорителей (для ан
гидритовых) вяжущих. Смеси, с одной стороны, должны иметь замедленное начало твердения, а с другой — приобретать через 2—3 ч достаточную проч ность.
Г и п с о в ы е с м е с и д л я у с т р о й с т в а с а м о н и в е л и р у ю щ и х с я с т я ж е к и о с н о в а н и й п о л о в предназначены для выравнивания и прида ния требуемой тепло- и звукоизоляции конструкции перекрытия различных
зданий. Основные требования к смесям приведены ниже |
(ТУ 21-53-50—86): |
||||
Подвижность |
(расплыв по прибору Суттарда через 15 |
мин |
|||
после смешения с водой), мм, не менее |
250 |
||||
Сроки схватывания, мин: |
|
|
40 |
||
начало, |
не ранее |
|
|
||
конец, не |
позднее |
|
|
180 |
|
Минимальное |
водотвердое |
отношение |
смеси (Ж :Т ), |
%, не |
|
более |
|
|
|
|
50 |
Коэффициент |
размягчения, |
не менее |
. |
0,5 |
|
Предел прочности при сжатии, МПа, не менее: |
3,5 и 6 |
||||
через 1 |
сут. |
|
|
||
в сухом |
состоянии |
|
|
10 и 15 |
Дополнительным требованием является прочность верхнего поверхностного слоя и отсутствие «высолов», что является причиной недостаточной приклейки материалов к стяжке. Весь комплекс свойств и соответственно качество стяжки обеспечиваются несколькими условиями: применением вяжущих с высокой прочностью и соответственно низкой стандартной (ГОСТ 125—79) водопотребностью; наличием добавок-разжижителей, снижающих водопотребность и при дающих массе тиксотропные свойства, что предотвращает водоотделение и ослабление поверхностного слоя и быстроту высыхания стяжек. Смеси могут
содержать различные виды заполнителей |
(песок, шлак и др.). |
|
Г и п с о в ы е с м е с и д л я т а м п о н и р о в а н и я н е ф т я н ы х и г а |
||
з о в ы х с к в а ж и н |
(принятое в настоящее время название «Тампонажный |
|
цемент типа ЦТН» |
неточно). Свойства и условия применения изложены |
|
в разд. 3.3.3. |
|
с м е с и предназначены для заделки |
Г и п с о в ы е ш п а к л е в о ч н ы е |
швов, дефектов и неровностей поверхностей. В зависимости от конкретного назначения требуемые свойства меняются в широких пределах. Обязательным
является замедленное твердение, |
большая водоудерживающая |
способность |
и хорошая адгезия к основанию. |
|
|
Г и п с о в ы е с м е с и д л я |
р а з л и ч н ы х в и д о в р а б о т |
в угольных |
шахтах в зависимости от назначения должны удовлетворять следующим тре бованиям:
Сроки схватывания, мин: |
15— |
90 |
начало |
||
конец |
30— 120 |
|
Предел прочности при сжатии, МПа |
1— |
50 |
В каждом конкретном случае применения предъявляются дополнительные требования по водостойкости, быстроте твердения и другим показателям.
Технология производства сухих смесей сводится к хранению, подаче, дози рованию и перемешиванию исходных порошкообразных компонентов. Как пра вило, используют периодическое дозирование и смешение исходных компонен тов, что обеспечивает более точный состав и стабильность свойств смесей. При отсутствии добавок с необходимыми свойствами возможна их предварительная подготовка (сушка, помол и т. п.). Смеси отгружают в мешках или контей нерах.
Перегородочные изделия. Изделия предназначены для устройства ненесущих перегородок в зданиях различного назначения с сухим, нормальным, влажным и мокрым режимом помещений по СНиП-3—79.
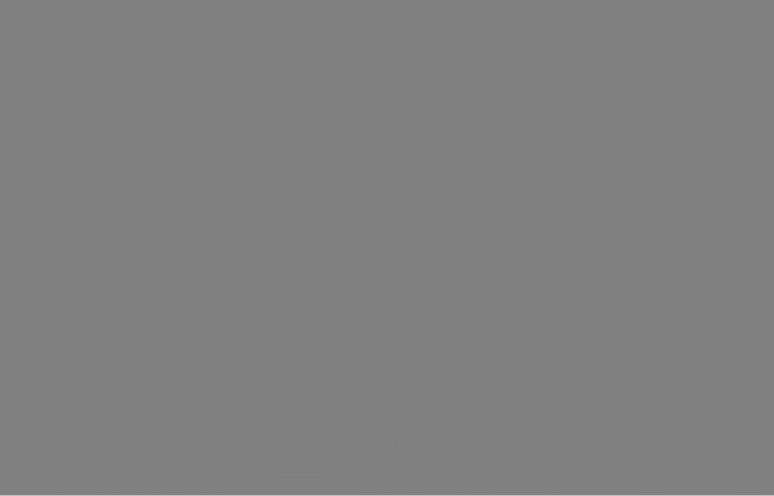
Рис. 3-31.
Технологическая схема изготовления гипсобетонных перегородочных панелей способом проката:
/ — передаточная тележка; 2 — вагонетка; 3 —тельфер; 4 — опрокидыватель; 5 — венти лятор; 5 — емкости; 7 — обгонный ленточный конвейер; 3 — сушилка; 9 — скребковый кон
вейер; 10 — бункер; |
// — ленточные питатели; 12 — гипсомешалка; 13 — прокатный стан |
с резиновой лентой; |
14 — винтовой конвейер; 15 — склад готовой продукции; /5 — ленточ |
ный конвейер для деревянных каркасов; 17 — кран; 18 — панелевоз
Рис. 3-32.
Технологическая схема производства гипсовых перегородочных плит на стен довой установке:
/ — силос; 2 — винтовой конвейер; 3 —дозатор воды; 4 — дозатор вяжущего; 5 — мешалка;
6 — съемник; 7 — формовочная машина; |
8 — вагонетки; 9 — передаточная тележка; 10 — |
погрузчик; // — склад плит; 12 — сушилка; /3 —кран; 14 — пакет плит; 15 — упаковочная |
|
машина |
|
П а н е л и г и п с о б е т о н н ы е |
д л я п е р е г о р о д о к (ГОСТ 9574—80) |
изготавливают преимущественно на прокатных станах |
(рис. 3-31). Они долж |
|||||
ны отвечать следующим требованиям: |
|
|||||
Размер панелей, мм: |
|
|
|
|||
длина, не |
более |
|
|
6600 |
||
ширина, |
не более |
|
4000 |
|||
толщина |
|
бетона при |
. |
60; 80; 100 |
||
Предел |
прочности |
сжатии, МПа |
5; 7,5 |
|||
Средняя |
плотность, |
кг/м3 |
. . |
1100—-1500 |
||
Отгрузочная влажность панелей, %, не более: |
|
|||||
на |
гипсовом вяжущем . |
|
8 |
|||
на |
композиционном вяжущем |
|
10 |
Панели имеют деревянный каркас, их изготовляют из гипсобетона с ис пользованием только нормально и быстротвердеющих вяжущих (ГОСТ 125— 79), так как кантование панелей и их перенос на сушильные вагонетки произ водят уже через 7—20 мин после формования. Гипсобетон содержит мелкий заполнитель (песок, шлак, мелкую фракцию гипсового камня и др.) и компо нент для армирования (преимущественно опилки). Расход материалов на 1 м2 панели толщиной 80 мм в среднем составляет:
Гипсовое вяжущее, кг |
|
55—65 |
|
Заполнитель, |
кг |
|
40—55 |
Опилки, м3 |
|
. |
0,15—0,25 |
Пиломатериалы (для |
изготовления каркаса), м3 |
0,005—0,006 |
|
Сталь (для |
подъемных |
петель) |
0 ,5 —0,6 |
П л и т ы |
г и п с о в ы е д л я п е р е г о р о д о к |
(ГОСТ 6428—83) выпу |
скают двух типов — пазогребневые и пазовые. Плиты формуют на стендовых кассетных установках (рис. 3-32) или карусельных машинах. Наиболее прог рессивным типом являются формы с жесткими вертикальными стенками, изде лия из которых извлекают выталкиванием (выпрессованием) гидравлическими толкателями. Это обеспечивает необходимую точность геометрических разме ров плит.
Технические требования к плитам приведены ниже: |
|
|
|
Размеры, мм: |
|
600; |
667; 800; 900 |
длина |
|
||
ширина |
(высота) |
300; |
400; 500 |
толщина |
|
80; 100 |
Предел прочности, МПа, не менее: |
|
||
через |
2 |
ч: |
3,5 |
при |
сжатии |
||
при |
изгибе |
1,7 |
|
сухих образцов: |
|
||
при сжатии |
5,0 |
||
при |
изгибе |
2,4 |
|
Отпускная |
влажность, %, не более |
12 |
|
Масса |
1 |
м2, кг |
75— 120 |
Высокая точность геометрических размеров (отклонение размеров по тол щине не более ±0,5 мм) и наличие пазогребневого замка по периметру плиты позволяют производить сборку перегородок на тонком (до 1 мм) слое гипсо вого клея.
П а н е л и п о л о с о в ы е п е р е г о р о д о ч н ы е (временные ТУ) изготав ливают экструзионным или литьевым способом. Они должны отвечать следую щим требованиям:
Размер, мм: |
|
|
2700—4200 |
||
длина |
(высота) |
|
|||
ширина |
|
|
|
300; |
600 |
толщина |
|
|
60; |
80; 100 |
|
Пустотность, |
% |
. |
20—45 |
||
Отпускная |
влажность, % |
|
5— 12 |
||
Масса 1 |
м2, |
кг |
|
40—55 |
Листовые изделия. Эти изделия предназначены для отделки стен, потол ков, колонн, устройства полов, перегородок и других конструкций в зданиях различного назначения, а также для изготовления декоративных и звукопогло щающих изделий.
Г и п с о к а р т о н н ы е л и с т ы (ГКЛ) представляют собой конструкцию из гипсового сердечника и картона, которым облицованы все плоскости ГКЛ, за исключением торцевых. Благодаря прочному сцеплению картона и сердеч ника, при небольшой толщине ГКЛ имеют высокий предел прочности на изгиб и ряд других свойств, делающих их незаменимыми при выполнении различных работ в строительстве. ГКЛ выпускают на высокомеханизированных конвейер ных линиях с годовой мощностью до 15 млн. м2 (за рубежом — до 25 млн. м*). Скорость формования листов достигает 50—60 м/мин. Технологическая схема производства ГКЛ приведена на рис. 3-33.
Технические требования к ГКЛ (ГОСТ 6266—81) |
приведены ниже: |
|
||||||
Размеры, мм: |
|
|
|
|
2500—4800 |
|||
длина |
|
|
|
|
||||
ширина |
|
|
|
|
600— 1200 |
14; |
||
толщина |
|
|
|
|
8; |
10; |
12; |
|
|
|
|
|
|
16; |
18; |
20; |
25 |
Средняя плотность, кг/м3, |
не |
более |
. . . |
. |
850 |
и 950 |
||
Предел прочности при изгибе ГКЛ толщиной 10 мм, МПа, |
|
|
|
|||||
не менее |
. |
|
|
|
|
10,5 |
|
|
Отпускная влажность, |
%, |
не |
более |
|
|
1 |
|
Гипсовый сердечник изготавляют из пеногипсового раствора и армируют для повышения ударной прочности рубленым стекловолокном или распущен ной бумажной макулатурой. Расход нормально и быстротвердеющего гипсо вого вяжущего на 1 м2 листа толщиной 10 мм — около 7 кг, стекловолокна
или макулатуры — до 70 г. |
|
|
Г и п с о в о л о к н и с т ы е |
л и с т ы |
(Г В Л) изготовляют формованием под |
небольшим (менее 0,3 МПа) |
давлением смеси гипсового вяжущего (80—85%) |
|
и распушенной бумажной макулатуры |
(15—20%). По сравнению с ГКЛ ГВЛ |
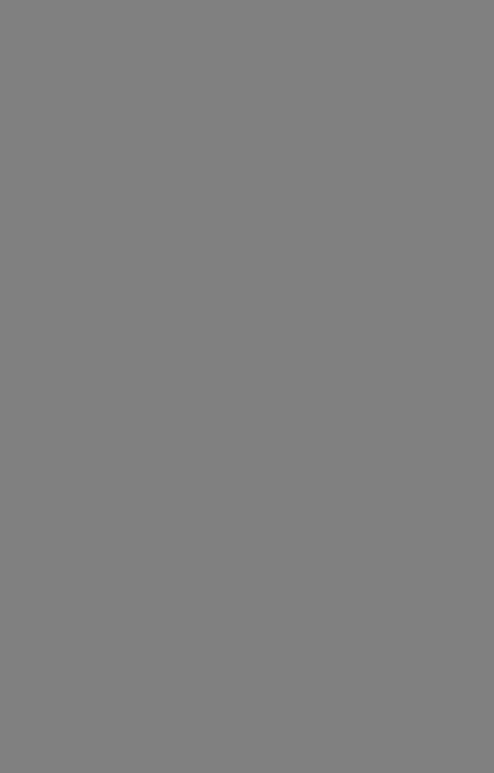
и оттаивания. Долговечность обеспечивается применением водо- и морозостойких композиционных вяжущих и (или) наружной защитой конструкций стен другими материалами или изделиями (декоративно-защитная отделка водо- и морозостойкими составами, защита асбестоцементными, полимерными и дру гими листовыми изделиями и т. п.). Для всех видов стеновых изделий морозо стойкость (сохранение прочности и массы при периодических циклах замо раживания и оттаивания во влажном состоянии) в зависимости от вида зданий и конструкции стены должно быть не менее 15, 25 и 35 циклов. Соответственно, для изготовления этих изделий наиболее целесообразно применение компози ционных гипсовых вяжущих.
К а м н и б е т о н н ы е с т е н о в ы е на г и п с о в о м в я ж у щ е м изго товляют преимущественно по литьевой технологии на карусельных машинах мощностью около 20 млн. штук условного кирпича в год (условный кирпич имеет размеры 250X 120X 65 мм). Для их изготовления применяют местные заполнители (шлак, песок, опилки, золы и др.) или только чистое вяжущее.
В соответствии с ГОСТ 6133—83 и другой нормативно-технической доку ментацией камни должны удовлетворять следующим требованиям:
Основные размеры, мм: |
390 |
||
длина |
|
||
ширина |
|
190 |
|
высота |
|
188 |
|
Масса, |
кг |
|
16,7—23,0 |
Предел прочности при сжатии, МПа, не менее: |
|||
рядовых |
камней |
25—200 |
|
лицевых |
камней |
75—200 |
|
Морозостойкость, циклы, не менее: |
|
||
рядовых |
камней |
15 |
|
лицевых |
камней |
25 |
|
Средняя плотность камней, кг/м3: |
|
||
эффективных, менее |
1400 |
||
условно-эффективных |
1401— 1650 |
||
тяжелых, |
более |
1650 |
|
Б л о к и |
и п а н е л и с т е н о в ы е |
г и п с о б е т о н н ы е изготовляют |
сплошными с легкими заполнителем (керамзит) или пустотелыми с последую щим заполнением пустот местными легкими материалами. При изготовлении керамзитобетонных блоков и панелей можно использовать типовые бетонные узлы для аналогичных изделий на основе цемента. Однако в отличие от послед них для гипсобетонных изделий отпадает необходимость длительной тепловой обработки паром, так как требуемая распалубочная прочность приобретается
вестественных условиях за 0,5—3,0 ч.
Всоответствии с нормативными документами блоки и панели должны отвечать следующим требованиям:
Размеры, мм: |
|
6000 |
|
длина, |
до |
|
|
высота |
|
|
1200—3200 |
толщина |
|
300—500 |
|
Средняя |
плотность, кг/м3 |
900— 1200 |
|
Коэффициент размягчениябетона, более |
0,7 |
||
Морозостойкость, |
циклы, более |
35 |
|
Расход композиционного вяжущего повышенной водостойкости в зависи |
|||
мости от марки бетона составляет от 300 до 450 кг/м3. |
|
||
Г и п с о б е т о н н ы е |
б л о к - к о м н а т ы изготовляют |
с использованием |
специальных формовочных машин. Они представляют собой монолитный «кол пак», включающий наружные стены, перегородки и перекрытие (покрытие). После формования их полностью отделывают и оснащают необходимыми эле ментами (санитарно-техническое оборудование, оконные блоки, электропровод ка и т. п.) в заводских условиях.