
книги / Теория признаков распознавания образов на основе стохастической геометрии и функционального анализа
..pdf9.1. Задача автоматизации дефектоскопии |
191 |
Радиографический контроль качества сварных соединений — это метод контроля, при котором радиационное изображение просвечива емого объекта регистрируется на радиографическую пленку, ксерорадиографическую пластину или фотобумагу.
Радиографический контроль проводится для выявления внутренних дефектов в наплавленном металле сварного шва и переходной зоне к основному металлу, для определения геометрических размеров этих дефектов, а так же для выявления поверхностных дефектов, недоступ ных для обнаружения внешним осмотром.
Применяют рентгенографию в цеховых, реже в полевых условиях, когда к контролю качества сварных соединений предъявляют наивыс шие требования по чувствительности. Проведение радиографического контроля предполагает подготовку оборудования с соблюдением усло вий, обеспечивающих возможность выявления минимального дефекта контролируемого объекта. Для этого в соответствии с нормативными документами и особенностями контролируемого объекта выбирают ис точник излучения, радиографическую пленку, определяют схему про свечивания, фокусное расстояние и время экспозиции [49].
Регистрация рентгеновских и гамма-лучей, прошедших через шов, на фотопленку является основным видом контроля сварных соеди нений. Дефекты швов в виде трещин, пор, непроваров пропускают больше лучей, чем соседние бездефектные участки шва. Поэтому после проявления пленка под дефектами швов больше чернеет и тем самым выявляет их. Качество снимка характеризуется контрастностью и чет костью изображения дефектов. По рентгеновскому снимку (рентгено грамме) сварного шва можно определить наличие в шве макроскопи ческих дефектов в виде трещин, непроваров, газовых пор и шлаковых включений размерами в среднем от 1 % от толщины контролируемого шва.
В предшествующей главе были даны примеры дефектов сварных соединений на рис. 8.3: а) пора; б) шлак; в) непровар; г) трещина. Это изображения, полученные с рентгеновских снимков, инверсия которых осуществлена с помощью компьютера.
В настоящее время существуют телевизионные камеры, работаю щие в рентгеновском диапазоне и позволяющие вводить изображения в компьютер и хранить там в цифровом виде. Наряду с удобством применения, достоинством этого способа ввода данных является ис ключение промежуточного носителя — рентгеновской плёнки и вместе с ней исключение целого класса шумов, связанного с зернистостью рентгеновской плёнки: спекл шума. Однако, применение этих техниче ских средств требует изменения ГОСТов. В настоящее время, согласно существующим государственным нормативным документам, требует ся применять при радиографическом контроле рентгеновскую плёнку. Более того, рентгеновские снимки сварного шва являются главным документом, подтверждающим качество выполнения сварочных работ, гарантирующим возможность безаварийной эксплуатации.
192 |
Гл. 9. Распознавание дефектов сварных соединений |
9.2. Построение распознающей системы
Типы дефектов, которые должны быть выявлены в ходе радиогра фического контроля сварных соединений, определяет ГОСТ 23055-78 (Классификация сварных соединений по результатам радиографиче ского контроля) и ОСТ-102-51-85 (Контроль неразрушающий. Сварные соединения трубопроводов. Радиографический метод).
Классы распознавания. На основании требований вышеприведён ной нормативной документации и анализа рентгеновских изображений сварных соединений нами был предложен алфавит классов или обра зов, подлежащих распознаванию:
класс 1 — изображения сварных швов, не содержащие дефектов; класс 2 — изображения, содержащие дефект в виде сферической
поры; класс 3 — изображения, содержащие дефект в виде удлиненной
поры; класс 4 — изображения, содержащие дефект в виде включения;
класс 5 — изображения, содержащие дефект в виде непровара (в сложных случаях изображения относят к совокупности классов: непро вар или включение);
класс 6 — изображения с дефектами, расположенными на одной прямой;
класс 7 — изображения сварных швов с дефектом в виде цепочки пор (цепочки включений);
класс 8 — изображения с дефектом в виде скопления пор (цепочки включений);
класс 9 — изображения с несколькими произвольно расположенны ми дефектами.
Рассмотрим некоторые физические аспекты образования дефектов, поскольку они оказывают влияние на форму, расположение и гео метрические параметры дефектов и могут быть полезными при их автоматическом распознавании.
Газовые поры (см. рис. 8.3, а) образуются в шве при сварке плавлением вследствие перенасыщения ванны расплавленного металла газами. Размеры внутренних пор колеблются от микроскопических до 2-3 мм в диаметре.
Распределение пор в металле шва может быть равномерным по длине шва; поры могут располагаться группами на отдельных участках плотного металла и в линию, в виде цепочки по продольной оси шва. Поры нарушают плотность и прочность швов.
Шлаковые включения (см. рис. 8.3,6) можно разделить на макро- и микроскопические. Макроскопические включения имеют сфериче скую и продолговатую форму в виде вытянутых «хвостов». Эти вклю чения появляются в шве из-за плохой очистки свариваемых кромок от окалины и других загрязнений и чаще всего от внутренних подрезов и плохой зачистки шлака в первых слоях многослойных швов перед заваркой последующих слоев.
9.2. Построение распознающей системы |
193 |
Шлаковые включения ослабляют сечение шва и снижают проч ность сварных соединений. Шлаковые макроскопические включения, особенно продолговатой формы, вызывают местную концентрацию на пряжений по подрезам и между слоями в многослойных швах и могут снизить прочность сварных соединений. Микроскопические снижают пластичность швов.
Непровары (см. рис. 8.3, в) — это несплавление основного металла с наплавленным и незаполнение металлом расчетного сечения шва.
Наличие непроваров по кромкам создает концентрацию напряжений в шве и приводит к разрушению сварной конструкции. Непровары — незаполнение сечения — менее опасны, но также являются концен траторами напряжений и снижают прочность швов под действием динамических нагрузок.
Трещины (см. рис. 8.3, г) — наиболее опасный дефект сварных швов. По размерам трещины подразделяются на макро- и микроскопи ческие, а в зависимости от происхождения — на холодные и горячие.
Трещины любых размеров могут образовываться в швах в процессе сварки; вскоре после сварки; через некоторое время после сварки; вследствие возникновения напряжений, превышающих предел прочно сти металла, а также в процессе эксплуатации сварной конструкции от перегрузок.
По месту расположения в сварных соединениях трещины делятся на поперечные и продольные трещины в металле шва или в основном металле в околошовной зоне.
Трещины любого происхождения (горячие и холодные) часто трудно выявить при помощи методов контроля без разрушения. Исключение составляют трещины, возникающие в процессе эксплуатации сварной конструкции. Они являются следствием невыявленных (скрытых) горя чих трещин, пор, шлаковых включений, непроваров и других дефектов сварных швов. Эти трещины прямолинейны, часто выходят на поверх ность и, как правило, легко обнаруживаются.
Выше на рис. 8.3, а-8.3, г были даны изображения отдельных де фектов, полученные с рентгеновских снимков после компьютерной инверсии. На рис. 9.1 (см. цветную вклейку) приведены исходные рентгеновские снимки сварных швов, отмечены наиболее значимые дефекты: а) скопление пор, расположение поперёк шва; б) непровар в толще шва; в) цепочка пор, расположенных на линии вдоль оси шва; г) группа дефектов: сферическая пора и шлаковые включения.
Для задач дефектоскопии сварных соединений характерна зна чительная вариабильность формы дефектов и уровня их яркости, наличие фоновых шумов, обусловленных разбросом качества рент геновской пленки. В этих условиях придать большую устойчивость и надежность автоматической дефектоскопии позволяет опора на боль шое количество информативных признаков распознавания.
13 Федотов Н. Г.
194 |
Гл. 9. Распознавание дефектов сварных соединений |
Структурные методы непригодны для решения задачи распознава ния дефектов сварных соединений, так как не обладают инвариант ностью по отношению к группе движений и линейным деформациям изображений. Результат распознавания такими методами зависит от поворотов, перемещений и масштабных преобразований изображений дефектов. Придание инвариантности описаниям распознаваемых объ ектов, полученным с помощью структурных методов распознавания, требует больших вычислительных затрат.
Существуют некоторые интегральные методы, обладающие инвари антностью по отношению к группе движений и линейным деформациям изображений объектов. Однако эти методы узко специализированны и используют незначительную часть информации об объектах. Напри мер, метод моментов использует только функцию яркостной интенсив ности точек, не включает в распознающие инварианты информацию об окрестностях точек. Метод дескрипторов Фурье пригоден только для распознавания контурных изображений.
Подход к распознаванию. Предложенный нами в работах [49,
50, 85] подход на основе стохастической геометрии и функциональ ного анализа оказался, как показала практика, более эффективным при решении подобных задач. Это объясняется многими причинами. В частности, в признаках распознавания, основанных на совместном применении математического аппарата стохастической геометрии и функционального анализа, — триплетных признаках — полнее отра жаются свойства окрестности каждой точки пересечения изображе ния дефекта сканирующими линиями. Преимущества данного подхода связаны с гибкостью трёхзвенной структуры триплетных признаков. Как показано в предшествующей главе, варьируя свойства функцио налов, можно получать признаки, эффективно распознающие весьма вариабильную форму дефектов; их число и взаимное расположение; их геометрические параметры. При этом вычисление таких разнооб разных характеристик осуществляется в одной и той же технике. Это свидетельствует о достижении высокой степени унификации алгоритма распознавания в целом.
Подведём итоги. Итак, количество классов распознавания (обра зов) в рассматриваемой задаче невелико — равно девяти. Далее, как показано в главе 8, на основании трейс-преобразования и двойствен ного трейс-преобразования можно не только формировать триплетные признаки, но и осуществлять нелинейную фильтрацию изображений с целью уменьшения зашумлённости, сглаживания, полигональной аппроксимации (что понижает вариабильность дефектов). На основа нии вышесказанного можно прийти к выводу, что наиболее целесо образный путь решения задачи распознавания дефектов сварных соединений основан на экстракции триплетных признаков распо знавания (см. предшествующую главу).
9.2. Построение распознающей системы |
195 |
Для успешного распознавания дефектов сварных соединений необ ходимо построить распознающую систему как обучающуюся с учите лем. Архитектура обучающейся распознающей системы, основанной на генерации триплетных признаков, приведена на рис. 11.2. Экстракция триплетных признаков приводит к упрощению архитектуры за счёт ис ключения процедур генерации признаков и минимизации размерности признакового пространства.
Таким образом, в процессе обучения распознающей системы про исходит предварительная обработка изображений с помощью трейспреобразования и двойственного трейс-преобразования; формирование триплетных признаков распознавания путём экстракции их из изобра жения дефектов обучающей совокупности рентгенограмм; выбор реша ющего правила.
На этапе распознавания дефектов, после предварительной обра ботки изображений и вычисления триплетных признаков на тестовой совокупности — изображения дефектов относятся к одному из классов с помощью ранее выбранного решающего правила.
Обучение распознающей системы. После составления алфавита классов исследуемых изображений производится представление их в цифровом виде. Это обеспечивает возможность предварительной обра ботки и анализа изображений.
Все изображения были получены с рентгеновских снимков свар ных соединений стерилизаторов и парогенераторов, изготовленных на ФГУП «Автомедтехника» в течение пяти месяцев работы. Общее число изображений составило 1511 шт. При изготовлении изделий произво дится ручная сварка, толщина свариваемого металла — от 4 до 8 мм. Оборудование, применяемое для контроля, — рентгеновский аппарат РУП 150; тип плёнки — РТК.
Согласно требованиям дефектоскопии реализовано два режима рас познавания изображений: «детальный» и «годен/брак».
Первый режим предназначен для детального анализа каждого из обнаруженных дефектов. После завершения анализа изображения со общается число обнаруженных дефектов, их суммарная длина и пло щадь; в случае обнаружения единичного дефекта определяются коор динаты его центра, а также вид и геометрические размеры.
Реализация первого режима осуществляется в несколько этапов.
Этап 1. Формирование алфавита классов.
Этап 2. Формирование обучающей и тестовой совокупности изоб ражений.
Этап 3. Предварительная обработка изображений.
Этап 4. Экстракция признаков исследуемых изображений. Этап 5. Выбор решающего правила.
Все изображение разделены на две группы: обучающую и тесто вую совокупности, так чтобы в каждой из них были представлены изображения всех классов распознавания (образов). Распределение
13*
196 |
|
Гл. 9. Распознавание дефектов сварных соединений |
|||
|
|
|
|
Т а б л и ц а 9.1 |
|
К ласс |
|
О б у ч аю щ ая |
Т есто в ая |
В сего и зо б р а |
|
|
со во к у п н о сть, шт. |
с о во к у п н о сть, ш т. |
ж ен и й , ш т. |
||
|
|
||||
К л асс |
1 |
100 |
195 |
29 5 |
|
|
|
И з о б р аж е н и е с о д ер ж и т ед и н и ч н ы й д е ф е к т |
|
||
К л асс |
2 |
100 |
183 |
28 3 |
|
К л асс |
3 |
60 |
154 |
2 1 4 |
|
К л асс |
4 |
4 0 |
79 |
119 |
|
К л асс |
5 |
2 0 |
73 |
93 |
|
К л асс |
6 |
4 0 |
87 |
127 |
|
К л асс |
7 |
30 |
65 |
95 |
|
К л асс |
8 |
60 |
133 |
193 |
|
К л асс |
9 |
30 |
62 |
92 |
|
В сего |
|
4 8 0 |
1031 |
1511 |
|
и зо б р аж е н и й |
|||||
|
|
|
|||
изображений |
в каждой из групп по классам распознавания отражено |
||||
в табл. 9.1. |
|
|
|
Предварительная обработка изображений. Этот вид обработки, как отмечалось, осуществляется и в режиме обучения, и в контрольном режиме работы системы.
Трейс-преобразование осуществляется при сканировании изобра жений решёткой параллельных прямых 1(р,в) с шагом Ар. Далее сканирование осуществляется для нового значения угла, получившего приращение Ав, той же решёткой с шагом Ар. Через ац обозначим элемент трейс-матрицы i = i,n (связано с количеством линий в решёт ке), j = I, к (связано с количеством дискретных углов поворота 6j).
Реальные сварные швы, несмотря на механическую зачистку, содер жат по своим краям заусенцы, выступы, резкие перепады уровня, ко торые фиксируются на рентгеновском изображении. Эти детали краёв при сканировании изображений, независимо от вида Т-функционала, искажают трейс-трансформанту. Для избежания возможных в таких случаях искажений информации об обнаруженных дефектах произ водится предварительная обработка изображений сварных соединений с целью устранения «краевых эффектов» при вычислении признаков.
Указанное преобразование изображений иллюстрирует рис. |
9.2. |
На рис. 9.2, а представлено исходное изображение сварного шва, |
на |
рис. 9.2,6 — преобразованное изображение, на котором выделен де фект сварного соединения (непровар). Рис. 9.2,6 для удобства воспри ятия приведён в инверсную форму.
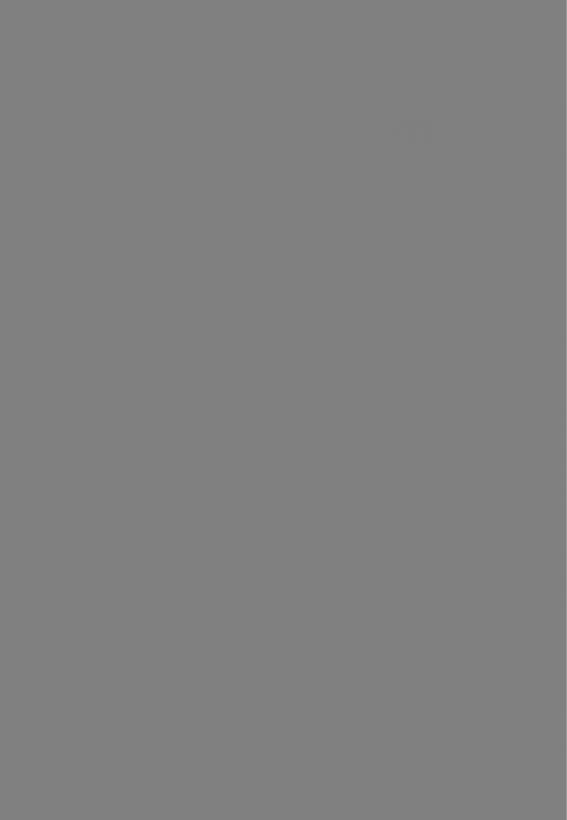
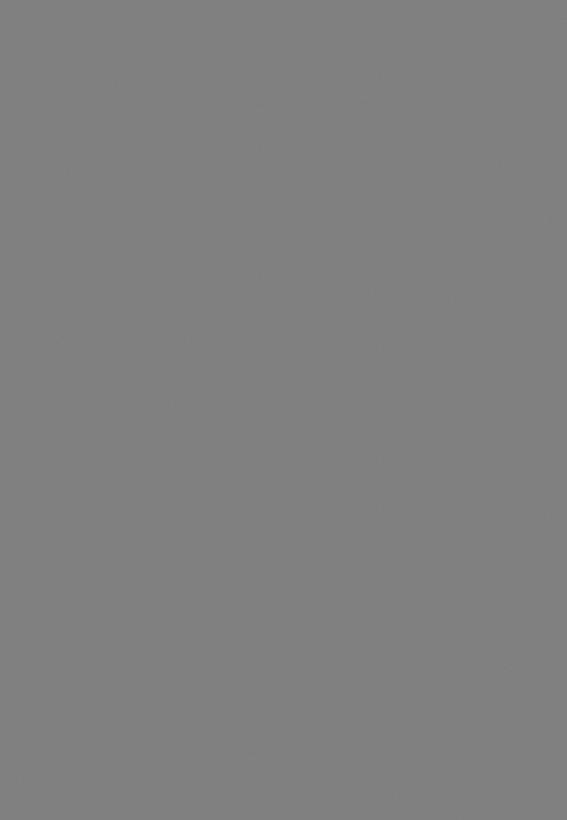
9.2. Построение распознающей системы |
199 |
Для сферических и удлиненных пор характерным является нали чие контура без резких «изломов». Форма сферических пор близка к окружности, форма удлиненных пор — к эллипсу. Включения имеют произволвную форму, «изрезанный» контур.
Непроварв1 отличает вв1тянутоств в направлении, параллельном сварному шву, форма схожая с прямоугольной. Однако в силу дискрет ности изображений некоторые дефекты этого класса имеют неровный край.
Для распознавания единичных дефектов сварных соединений сле дует создать признаки, позволяющие выявить особенности формы де фекта, а также определить его геометрические параметры и располо жение.
Определению геометрических характеристик дефектов и анализу их взаимного расположения много внимания уделено в предшествующей главе § 8.2. Рассмотрим для завершения темы пример, детально иллю стрирующий технику вычисления подобного признака.
Пример. Вычисление признака «расстояние между двумя близле жащими краями изображений двух дефектов».
Функционал Т — подсчёт числа пересечений изображения со ска нирующей прямой.
Функционал Р — если число групп ненулевых элементов в столбце матрицы (9.3) равно двум, подсчитываем число нулевых элементов,
расположенных между ненулевыми: |
|
|
|
||
если |
(aij = |
ф 0), то f\ = i — запоминаем |
номер первого |
||
нулевого элемента в j -ом столбце трейс-матрицы; |
|
|
|
||
если |
(а^ ф 0)&(сц_1^ = 0), то /2 = г — запоминаем |
номер послед |
|||
него нулевого элемента в j -ом столбце трейс-матрицы; |
|
|
|||
Pj = /2 —/ 1, где |
— элементы трейс-матрицы, |
i = 2,n, |
j = 1,к, |
||
п — число строк, к — число столбцов трейс-матрицы, /1 |
и /2 |
первона |
|||
чально принимают равными нулю. |
|
|
|
||
Для |
остальных |
случаев результат вычисления |
диаметрального |
функционала равен 0.
Функционал 0 — найти произведение наибольшего из полученных чисел max {p \,...,P k} и расстояния между сканирующими линия ми Ар.
Для создания признаков, чувствительных к особенностям формы распознаваемых дефектов, Т-функционал определим путём вычисления длины отрезка, высекаемого изображением на сканирующей прямой. Значения, соответствующие каждой сканирующей линии, будут отра жать особенности формы дефекта. Например, уменьшение длины 2-го отрезка по сравнению с длинами 1-го и 3-го (рис. 9.3, а) свидетельству ет об изломе контура дефекта. Чтобы оценить глубину такого излома, длину 2-го отрезка сравним с максимальным для данного направления сканирования: чем глубже излом, тем больше разность между ними.
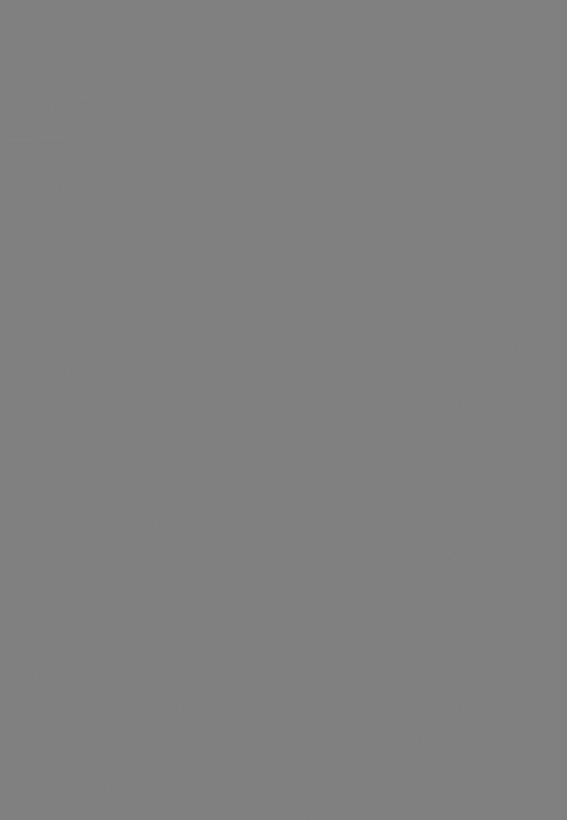