
книги / Неформованные огнеупоры. Свойства и применение неформованных огнеупоров Сост. И. Д. Кащеев [ др.]; Под ред. И. Д. Кащеева
.pdfРис. 6.15. Наварная лещадь отражательной печи: 1 — кварцевая набивка; 2 — огнеупор ный кирпич; 3 — строительный кирпич; 4 — фундамент; 5 — железобетонная обвязка фун дамента
1
Ряс. 6.16. Общий вид огнеупорной кладки в области расплава промышленной печи КФП: 1— футеровка подины; 2 — стальной кожух; 3 — футеровка стен; 4
— стальные конструкции (каркас) печей; 5— закладные медные элементы (кес соны); б — уровень ванны расплава
Рис. 6.17. Футеровка фурменного пояса конвертера: 1 — фур менные изделия с канавкой; 2 — набивка; 3 — футеровка надфурменной зоны
арки толщиной 460 мм или из комбинации двух слоев: нижнего слоя из динасовых изделий с засыпкой из сухого тонкомолотого кварцита и верхнего слоя из огнеупора ПХС с засыпкой из периклазового порошка. На верхнем слое делают кварцитовую набивку толщиной 30-50 мм.
Для защиты футеровки стен отражательной печи ее покрывают защитной обмазкой. При интенсификации работы отражательной печи условия службы футеровки су щественно ужесточаются и нормальная работа печей становится невозможной без применения кессонированных элементов ограждения. В частности, предлагается ус
тановка кессонов в боковой стене отражательной печи.
Конструкция кессонов, состоящих из цельнотянутых труб и набивной хромитопериклазовой массы прошла опытно-промышленную эксплуатацию на отражательной печи на одном из медеплавильных предприятий.
В руднотермических печах для плавки на штейн арочный свод выполняют из клино вого шамотного кирпича или огнеупорного бетона (температура подсводового про странства 400-600 °С). Толщина свода 230-350 мм.
Впечи взвешенной плавки зону перехода от шахты к нижней части печи (см. рис. 6.7) выполняют нанесением хромомагнезитовой торкрет-массы на систему медных охла дительных труб.
Впечи кислородно-факельной плавки подину изготавливают из огнеупорного бето на и трех слоев огнеупорного кирпича, выложенных в виде обратной арки (рис. 6.16). Верхние рабочие слои выкладывают из хромитопериклазового огнеупора, нижний — из шамотного. Зазоры между слоями заполняют периклазовым порошком.
Вустановке КИВЦЭТ основной элемент циклона — циклонная горелка — пред ставляет собой водоохлаждаемый или с испарительным охлаждением металлический корпус, футерованный хромитопериклазовой или периклазохромитовой набивной массой, нанесенной на ошипованную поверхность.
Впечи Ванюкова для плавки в жидкой ванне шахта печи полностью кессонирована. Со шлаковой стороны кессоны защищают обмазкой толщиной до 80 мм из хромито периклазового порошка на жидком стекле с добавкой кремнефтористого натрия.
Вгоризонтальных конвертерах периодического действия между кожухом конверте ра и кладкой делают забутовку толщиной до 40 мм из сухого хромитопериклазового или периклазового порошка для цилиндрической части футеровки (рис. 6.17) и из асбозуритового порошка толщиной 50 мм для футеровки торцов. Футеровку всей под фурменной и первых рядов надфурменной зон ведут на растворе из смеси хромитопериклазового порошка с жидким стеклом.
Вагрегате непрерывного конвертирования штейнов между кожухом и кладкой де лают набивку сухой периклазохромитовой массой.
6.2. Печи для производства никеля
Для восстановительно-сульфидной плавки окисленных никелевых руд на штейн применяют шахтные печи. Шахтная печь для плавки никелевых руд показана на рис. 6.18.
Печь состоит из внутреннего горна, шахты, колошника, шатра и внешнего отстойника. Шахта печи полностью кессонирована, может быть кессонирован также колошник печи.
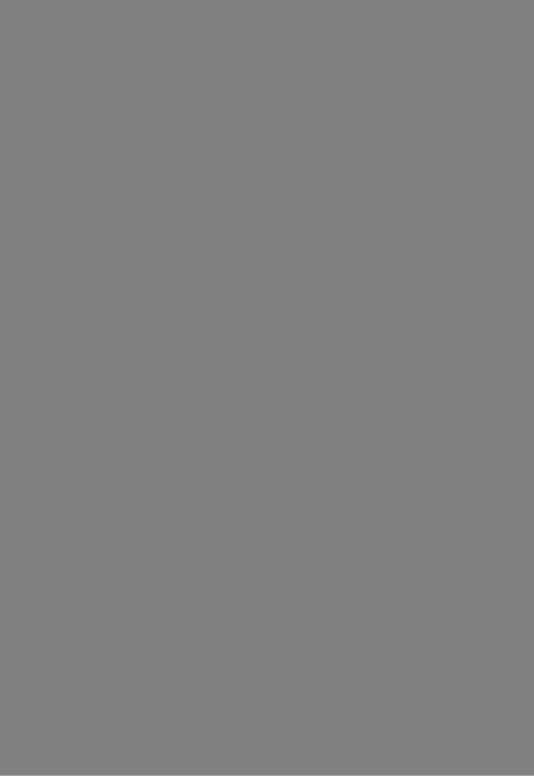
Рис. 6.19. Руднотермическая печь: 1— стены; 2 — шлаковая летка; 3 — ковш; 4 — заливочная ложка; 5 — газоход; 6 — электрод; 7— электрододержатель; 8 — уплотнение; 9 — газоотсасывающее устройство; 10 — штейновый желоб; 11 — шлаковоз
|'9
; |
1 |
1 |
1 --1 |
|
|
_____ _ |
|
А - А |
Рис. 6.20. Печи кипящего слоя для обжи |
|
|
га файнштейна: а — с наличием угла в |
|
|
сопряжении стены загрузочной камеры с |
|
|
шахтой печи (7 — дутьевая камера, 2 — |
|
Рис. 6.21. Дуговая печь: 7 — электрод; 2 — свод печи; 3 — сте |
загрузочная камера, 3 — газоходное от |
|
ны; 4 — подина |
верстие, 4 — форсунка для разогрева печи, 5 — разгрузочные отверстия, 6 — газоходы); б — с плавным сопряжением стены камеры с шахтой (7 — дутьевая камера, 2— разгрузочное отверстие, 3 — форсунка для разогрева печи, 4— газо ходное отверстие, 5 — экранирующий кожух, 6 — предохранительный клапан, 7
— загрузочное отверстие)
Ниже показано применение неформованных огнеупоров в печах для производства никеля.
В горизонтальных конвертерах для плавки никелевых и медно-никелевых штейнов кладку ведут на засыпке толщиной 25-30 мм из хромитопериклазовой крошки фрак ции 3-4 мм. Применяют также смолопериклазовую “подушку” толщиной 35-40 мм из 90-92 % периклазового порошка и 8-10 % каменноугольного пека. Иногда для кладки
фурменного пояса медно-никелевых конвертеров применяют забутовку из хромитопериклазового порошка с жидким стеклом для предотвращения выдувания сухого порошка из засыпки при повреждении фурменных трубок.
В печи кипящего слоя для окислительного обжига файниггейна подина представляет собой стальную плиту толщиной 16-20 мм с дутьевыми соплами, пространство между которыми заполнено огнеупорным бетоном с шамотным заполнителем на жидком стек ле или портландцементе. Для упрочнения свода используют стальную арматуру.
В дуговых печах для восстановительной плавки оксида никеля кладка хромитопериклазовых изделий производится насухо с пересыпкой швов хромитопериклазовым порошком. На футеровку свода наносят защитный слой набивной корундовой массы. Применяют также кессонированные водоохлаждаемые своды с футеровкой из высокопганоземистого бетона на высокоглиноземистом цементе.
В дуговых печах для получения чернового анодного никеля на подину печи сверху на бивают слой, состоящий из смеси плавленого магнезита с бурой или борной кислотой.
Для горячего ремонта футеровки дуговых печей используют технологию факельно го торкретирования, предусматривающую разогрев района износа футеровки до тем пературы, обеспечивающей максимальный эффект налипания торкрет-массы, нане сение покрытия в пиропластическом состоянии и его термообработку.
6.3. Печи и установки для производства цинка
Для окислительного обжига цинковых концентратов применяют цилиндрические печи кипящего слоя.
Цилиндрическая печь кипящего слоя показана на рис. 6.22. Печи имеют диаметр 5 - 7 м, высоту 7-12 м, площадь подины 20-40 м2. Температура в кипящем слое 940980 °С, отходящих газов 800-850 °С.
Для переплавки катодного цинка применяют индукционные канальные и отража тельные печи.
Индукционная канальная печь для переплавки катодного цинка показана на рис. 6.23. Футерованная ванна печи разделена перегородкой на плавильное и зумпфовое отде ление. Температура металла в ванне печи 500-520 °С. Отражательная печь для пере плавки катодного цинка показана на рис. 6.24.
Восстановление и дистилляцию цинка проводят в горизонтальных и вертикальных ретортах, а также в шахтных и руднотермических печах. Для восстановления и дис тилляции цинка в горизонтальных ретортах применяют цинкодистилляционные печи (рис. 6.25).
Реторты располагают по обеим сторонам средней капитальной стены. Под сводом печи имеются каналы для горячего газа и воздуха. Регенераторы для подогрева газа и
Рис. 6.22. Цилиндрическая печь кипящего слоя: 1— подина; 2 — |
Рис. 6.23. Индукционная канальная печь для переплавки катодного |
форсунка для розжига печи; 3 — форкамера; 4 — корпус печи; 5 |
цинка: 1 — загрузочная коробка; 2 — свод; 3 — каналы, соединяю |
— отвод газа; б — сливной порог; 7 — воздушная коробка; 8 — |
щие индукторы с ванной печи; 4— перегородка, отделяющая зумпф |
пневмопривод; 9 — футеровка; 10 — свод |
от плавильной части печи; 5— индукторы; б— набивная футеровка |
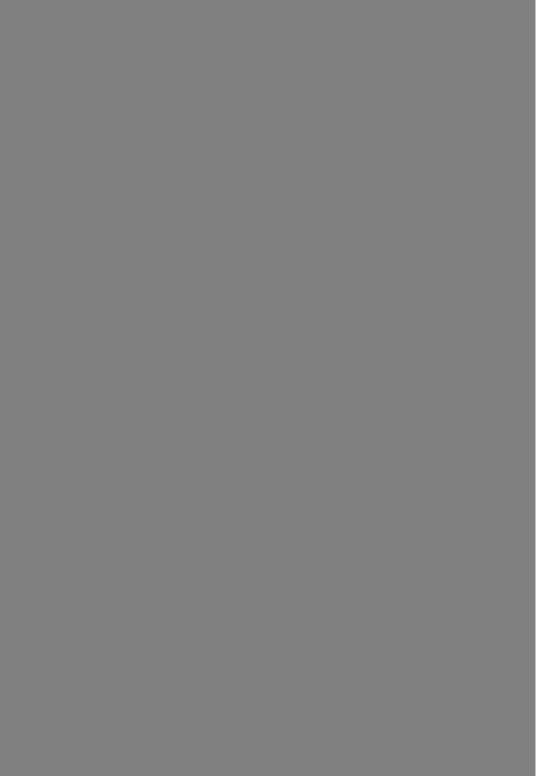
Отходящий газ в
коксовальную
печь
Рис. 6.26. Вертикальная реторта
Рис. 6.27. Схема установки для ректификации цинка (а — свинцовая колонна, б — кадмиевая): 1 — испарители; 2 — камеры сгорания газа; 3— конденсатор для паров цинка и кадмия; 4 — конденсатор Для паров, обогащенных кадмием; Ч— черновой цинк; О— остаток от ректификации; Р — рафини рованный цинк
Ликвационная печь представляет собой небольшую пламенную отражательную печь, состоящую из трех отделений: плавильного, отстойного и перегревательного. Темпе ратура в ванне печи 450 °С, газов 600-700 °С.
Ректификационная колонна показана на рис. 6.27. Колонна собрана из карбидкремниевых тарелок, нижняя ее часть— испарительная— расположена в топках и обогре вается, а верхняя часть — конденсационная, без обогрева. Температура в обогревае мой части свинцовой колонны 1000-1200 °С, а кадмиевой 900-1000 °С.
Ниже показано применение неформованных огнеупоров в печах для производства цинка.
В печи кипящего слоя для обжига цинковых концентратов наиболее ответственной частью печи является воздухораспределительная подина с воздушной коробкой. По дину выполняют из жароупорного бетона, состоящего из шамотного заполнителя и жидкого стекла с добавкой 4-5 % кремнефтористого натрия для ускорения затверде вания бетона. Зерновой состав шамотного заполнителя: 40-41 % фракции 5-18 мм,
20-23 % 1-5 мм, 33-35 % мельче 1 мм.
В индукционных канальных печах для переплавки катодного цинка рабочий слой футеровки ванны ниже уровня металла футеруют набивными огнеупорными массами влажностью 5-6 % или шамотными изделиями ША или ШБ. Состав массы, %: огне упорный шамот 70, огнеупорная глина 20, каолин 10. В условиях плавки цинка эта масса обладает достаточной химической стойкостью, удовлетворительной термостой костью и низкой стоимостью. К недостаткам массы следует отнести высокую откры тую пористость и относительно легкую размываемость металлом.
Футеровку индукционных единиц выполняют также из шамотной набивной массы на глинистой связке. Однако при применении индукционных единиц большой мощ ности и перегреве металла в канале стойкость шамотной массы становится недоста точной. Для повышения стойкости футеровки индукционных единиц применяют хи мически стойкую массу с низкой теплопроводностью на основе каолиновой ваты, обо жженной при 900 °С. Состав массы: 50 % высокоглиноземистого цемента марки СЕМВОК-73 по ТУ 14-194-215-97 (или глиноземистого, высокоглиноземистого це мента по ГОСТ 969-91) и 50 % рулонного материала МКРР-130 по ГОСТ 23619-79, 40-42 % (сверх 100 %) воды. Массу набивают пневмотрамбовками слоями толщиной
60-70 мм. Для уплотнения места стыковки индукционной единицы с ванной печи при меняют базальтовый картон.
Горизонтальные реторты цинкодистиляционных печей представляют собой муфели длиной до 2000 мм с поперечным сечением 170x280 мм и толщиной стенок 25-30 мм. Реторты изготавливают из пластичной огнеупорной шины (с минимальным содержани ем Ре20 3), шамота и кокса в соотношении 60:30:10 (шамотные реторты) или из шамота и шины с добавлением тонкомолотого кварца или кварцита (полукислые реторты).
Кокс добавляют в массу для увеличения огнеупорности, теплопроводности и шлакоустойчивости. Реторты изготовляют методом пластического формования на гидрав лических прессах и обжигают при 900-1000 °С. Перед обжигом для уменьшения газо проницаемости реторты покрываютлегкоплавкой глазурью, состоящей из шины (60 %), кварцита (30 %) и соды (10 %). Реторты оборудуют конденсаторами для цинка и алонжами, изготовленными из листовой стали, для улавливания не успевших сконденси-