
книги / Неформованные огнеупоры. Свойства и применение неформованных огнеупоров Сост. И. Д. Кащеев [ др.]; Под ред. И. Д. Кащеева
.pdfРис. 8.3. Крепежная арматура для |
7 |
футерования печи набивной мас сой: 1 — продольный прут; 2 — поперечный прут; 3 — арматура для крепления цепей; 4 — попе речное сечение
Нгн1 Цп)
Рис. 8.4. Блочная футеровка горячего обреза вращающейся печи диаметром 5 длиной 185 м: 1 — торцевые плиты; 2 — бетонный блок; 3 — упорная плита; 4 — крепежный болт; 5 — огнеупорный бетон; 6 — кирпичная кладка
На рис. 8.3 показано крепление футеровки из набивной массы в цепном участке печи. Кольцевая крепежная арматура состоит из закрепленных на кожухе крюков, вер тикальных и горизонтальных прутьев, на которые методом пневмотрамбования укла дывают набивную массу.
Для футеровки горячего обреза печи из бетонных блоков разработана конструкция, представляющая собой кольцо, состоящее из блоков, крепящихся к корпусу печи с помощью специального узла (рис. 8.4).
8.2. Футеровка циклонных теплообменников и декарбонизаторов
В печах сухого способа производства зоны подсушки, подогрева и дегидратации вынесены в неподвижные вертикальные или горизонтальные стационарные теплооб менные устройства (запечные теплообменники). Сырьевая мука поступает в запечной теплообменник, в котором нагревается до 700-750 °С. При этом происходят процессы подогрева, дегидратации и частично декарбонизации. Применяют запечные теплооб менники нескольких конструкций: циклонные, шахтные и комбинированные (шахт но-циклонные).
Наиболее совершенный способ передачи тепла обжигаемому материалу осуществ ляется в печных агрегатах, включающих, кроме циклонных теплообменников, реак- тор-декарбонизатор, в котором при температуре около 1000 °С происходит декарбо низация предварительно нагретой до 750 °С в теплообменнике сырьевой муки путем интенсивного нагрева во взвешенном состоянии. Применение реактора-декарбониза- тора позволяет довести степень декарбонизации основного компонента сырьевой смеси
— известняка до 80-90 %; при этом создаются условия для уменьшения диаметра печи и повышения стойкости футеровки короткой вращающейся печи. Кроме того, появляется возможность применения для футеровки неподвижных циклонных тепло обменников и декарбонизаторов ультралегковесных и стекловолокнистых теплоизо ляционных материалов, обладающих высокими теплоизоляционными свойствами, но имеющих низкую механическую прочность, ограничивающую их применение во вра щающихся печах.
В состав циклонных теплообменников входят циклоны (четырехступенчатые, в пос
ледние годы — пяти- и шестиступенчатые), газоходы, пересыпные устройства и пат рубки. Наиболее тяжелые условия службы футеровки циклонных теплообменников наблюдаются на участках циклонов и узлов примыкания к ним газоходов; в местах установки компенсаторов, ремонтных и смотровых люков, врезки пересыпных уст ройств в газоходы; пересыпных устройств циклонов теплообменника; патрубка, ло бового листа и шахты загрузочной головки.
Футеровку шахты циклонного теплообменника и ответственных участков газохо дов рекомендуется выполнять из специального подвесного шамотного кирпича. Меж ду металлическим кожухом и шамотным кирпичом выполняют теплоизоляционный слой из листового асбеста или стекловолокнистых материалов. В местах установки ремонтных и смотровых люков, врезок пересыпных устройств рекомендуется исполь зование специальных шамотных блоков и блоков из жароупорных бетонов.
Для футеровки циклонов и газоходов теплообменника применяют жаростойкий тор крет-бетон, наносимый на теплоизоляционный слой и закрепляемый анкерами. Со став жаростойкого торкрет-бетона, кг, приведен ниже:
Циклон I ступени и газоходы |
|
Высокогпиноземистый цемент.................................................... |
400 |
Высокогпиноземистый заполнитель (А120 3 > 62 %): |
|
мелкий...................................................................................... |
950 |
крупный................................................................................... |
800 |
Циклоны II и III ступеней и газоходы |
|
Высокогпиноземистый цемент.................................................... |
450-500 |
Шамотный порошок..................................................................... |
1400-1450 |
Огнеупорная глина........................................................................ |
10-15 |
Ниже рассмотрена конструкция футеровки технологических узлов этажерки четы рехступенчатого циклонного теплообменника вращающейся печи диаметром 4,5 и длиной 80 м.
Исходя из теплофизических характеристик применяемых огнеупорных материалов футеровку циклонов выполняют в три слоя. Общая толщина футеровки вертикальной стенки циклона I ступени и наклонной поверхности конуса равна 330 мм. Первый слой футеровки цилиндра циклона толщиной 40 мм кладут из минераловатных прошивных матов марки 100, второй слой толщиной 60 мм — из муллитокремнеземистых плит МКРП-340, третий слой — из стандартного и клинового шамотного кирпича.
Трехслойную футеровку стенок конуса выполняют из шамотного кирпича и двух слоев муллитокремнеземистых плит общей толщиной 100 мм. Кладку шамотного кир-
выполняют на цементном молоке из портландцемента марок 400 и 500 вперевязку. Крышку циклона выполняют из фасонного шамотного подвесного кирпича ША унифицированной формы (применяется для футеровки всех циклонов и колосникового холодильника). Пространство между подвесным кирпичоми стальной крышкойциклона высотой 100 мм закладывают муллитокремнеземистым рулонным материалом. Общая толщина футеровки крышки составляет 335 мм.
Футеровку крышек циклонов II и III ступеней выполняют аналогично футеровке циклона I ступени. Футеровка цилиндрической части циклонаПступени состоит из трех слоев: первый слой— из двух минераловатных прошивных матов общей толщиной 80 мм, второй— из муллитокремнеземистой плитытолщиной 40 мм, третий, внутренний слой футеровки — из шамотного прямого кирпича и торцового клина.
Общая толщина футеровки циклона 292 мм. Футеровка конуса циклона состоит из шамотного кирпича и трех слоев муллитокремнеземистых плит. Общая толщина футе ровки конуса циклона также равна 292 мм. Толщина футеровки циклона Ш ступени меньше, чем у циклона II ступени, за счет отсутствия минераловатных прошивных матов'. Футеровку выкладывают из прямого и клинового кирпича и муллитокремнеземистых плитмарки МКРП-340 толщиной 70 мм. Общая толщинафутеровки циклонасоставляет 242 мм. Футеровку нижней части циклонов I, II и III ступеней до первого опорного кольца крепления, а также в местах установки трубок для термопар выполняют из жароупорного бетона следующего состава, %: шамотный заполнитель 70, огнеупорная глина 5, высокоглиноземистый цемент 25. IV ступень, состоящую из двух циклонов, футеруют армированным стальными проволочными спиралями жароупорным шамотным бетоном на портландцементе.
Футеровку вертикальных газоходов между всеми циклонами изготовляют из шамот ного прямого и клинового кирпича с двумя слоями теплоизоляции (первый— прошив ные минераловатные маты, второй— плиты МКРП-340).
Пересыпные устройства, соединяющие циклоны всех ступеней, футеруют жароупор ным бетоном, армированным стальной проволокой, следующего состава, % (рис. 8.5):
муллитовыйзаполнитель 75, высокогпиноземистыицемент25, вода(сверх 100%) 10-11.
Реактор-декарбонизатор включает вихревую
камеру, собственно декарбонизагор, смесительную камеру, переходной лоток и газовое оборудование (рис. 8.6). В вихревую камеру подается мазут или природный газ через горелки, по тангенциальным патрубкам подводится нагретый воздух от охлади теля клинкера. Вихревая горелка, расположенная на вихревой камере, выполняет роль запального уст ройства. Горячая пылегазовая смесь с температу рой около 1000 °С из вихревой камеры по наклон-
Рис. 8.5. Футеровка пересыпного устройства циклонного теплообменника: 1— стальная крышка; 2 — соединитель ный фланец; 3 — стальная спиральная проволока диамет ром 4 мм; 4 — огнеупорный бетон
ному газоходу поступает в смесительную камеру, в которой смешивается с газами, выходящими из вращающейся печи. Образовавшаяся смесь с температурой 800-900 °С подается по газоходу в циклон. Горячие дымовые газы из печи поступают в смеси тельную камеру через загрузочную головку. Сырьевая мука, уловленная в циклоне, по пересыпному устройству ссыпается в загрузочную головку и затем по загрузочному лотку поступает во вращающуюся печь. Газы из циклона удаляются через патрубок. Температура внутренней стенки футеровки около 1400 °С, в реакторе-декарбонизато- ре 1000-1100 °С, в смесительной камере около 920 °С. Температура факела горящего газа в вихревой камере 1400-1500 °С.
Для футеровки реактора-декарбонизатора применяют огнеупорный бетон, огнеупор ные изделия или сочетание бетона и изделий. Футеровка вихревой камеры состоит из двух слоев: теплоизоляционного из муллито-кремнеземистых плит МКРП-340 тол щиной 80 мм и рабочего из корундового бетона следующего состава, %: корундовый заполнитель ЗК-90 (ГОСТ 23037-78) 83-85, высокоглиноземистый цемент 15-17. Соб ственно декарбонизатор футеруют также в два слоя общей толщиной 270 мм. Тепло изоляционный слой состоит из плит МКРП-340, рабочий— из хромитопериклазового прямого и клинового кирпича. Кладку производят насухо с перевязкой кирпича.
Наиболее ответственную часть футеровки — верхнюю крышку (рис. 8.7) выклады вают периклазохромитовым кирпичом. Кирпич имеет отверстия для подвески. Крыш ка декарбонизатора имеет кольцевые кронштейны, к которым крепят подвески с про пущенным через них стержнем. На стержень подвешивают периклазохромитовые кирпичи, между которыми закладывают стальные пластины. Пространство между крышкой и футеровкой заполняют муллитокремнеземистым рулонным материалом МКРР. Толщина футеровки крышки 380 мм.
Переходной лоток между декарбонизатором и смесительной камерой выполнен в виде патрубка и футеруется аналогично камере. Смесительная камера имеет трехслой-
1 2
Рис. 8.7. Деталь футеровки крышки декарбони- |
Рис. 8.8. Футеровка узла примыкания переходно |
затора: 1 — стальная крышка; 2 — кольцевой |
го лотка к смесительной камере: 1 — стальная |
кронштейн; 3 — подвеска из металла; 4— стер |
стенка смесительной камеры; 2 — прошивные |
жень диаметром 16 мм; 5 — подвесной перик- |
минераловатныеплиты; 3— муллитокремнеземи |
лазохромитовый кирпич; б — муллитокремне |
стые плиты; 4 — кронштейн; 5, 6 — фасонный |
земистый рулонный материал |
подвесной шамотный кирпич |
ную футеровку. Теплоизоляционный слой толщиной 50 мм состоит из прошивных минераловатных плит, второй слой — из муллитокремнеземистых плит МКРП-340 такой же толщины, третий, рабочий слой — из фасонного подвесного шамотного кир пича. Кирпич крепится к стенке камеры специальным кронштейном, который уста навливается через 5 рядов кладки. Шамотный кирпич кладут насухо, без раствора. Футеровка узла примыкания переходного лотка к смесительной камере показана на рис. 8.8.
Глава 9.
ПРИМЕНЕНИЕ НЕФОРМОВАННЫХ ОГНЕУПОРОВ В ПЕЧАХ ОГНЕУПОРНОЙ ПРОМЫШЛЕННОСТИ
Наибольшее распространение в огнеупорной промышленности получили шахтные, туннельные и вращающиеся печи.
9.1. Шахтные печи
Шахтные печи применяют для обжига кусковых огнеупорных материалов: глины, магнезита, доломита, извести и т.д.
На рис. 9.1 показана огнеупорная кладка шахтной печи для обжига магнезита. Раз меры печи: высота 14,7 м, диаметр рабочей зоны 2,75 м, объем рабочего пространства
— 127,8 м3. В шахте выделяют зоны подогрева (6,7 м), обжига (1,4 м) и охлаждения (6,6 м).
Зоны подогрева и охлаждения футеруют периклазохромитовыми изделиями (ПХ), в зоне обжига — наружный слой выложен хромитопериклазовыми изделиями (ХП), а внутренний — периклазовыми изделиями из плавленого периклаза (ПП), горелочные туннели — периклазовыми изделиями из плавленого периклазохромита.
9.2. Туннельные печи
Туннельная печь является наиболее совершенным агрегатом для обжига всех видов формованных изделий, которые перемещаются по печи на футерованной вагонетке. В огнеупорной промышленности эксплуатируюттуннельные печи длиной от 5-6 м (для обжига специальных изделий) до 243 м (для обжига динасовых изделий).
В футеровке туннельных печей для обжига огнеупоров применяют следующие ог неупорные изделия: шамотные (Ш), муллитовые и муллитокремнеземистые (МЛ), хромитопериклазовые, периклазохромитовые, периклазохромитовые из плавленого периклаза, периклазохромитовые из плавленого периклазохромита, легковесные теп лоизоляционные (ШЛ, КЛ).
Типовая схема футеровки туннельной печи для обжига основных огнеупоров пока зана на рис. 9.2.
В процессе эксплуатации туннельных печей наибольшему износу подвергается фу теровка вагонеток. Она должна сохранять достаточную механическую прочность при температурах обжига, обеспечивать минимальные потери тепла и иметь максималь ный срок службы. Схема футеровки вагонетки туннельной печи показана на рис. 9.3. Общая толщина огнеупорной футеровки составляет 582 мм и состоит из слоя шамот ного порошка и слоя шамотных изделий ША, составляющего 132 мм. На поверхность шамотных изделий укладывают слой муллитовых изделий МЛС-62 (А120 3 > 62 %) толщиной 300-350 мм. Верхний слой толщиной 150 мм выкладывают периклазохро митовыми или хромитопериклазовыми изделиями. Кладку внутреннего массива про изводят насухо без раствора, торкретирование бортов вагонетки ведут с использова нием бетона, состоящего из 75-80 % шамотного порошка фракции мельче 5 мм и 2025 % глиноземистого цемента. Зерновой состав шихты для приготовления торкрет-
массы, %: фракции 5-3 мм 3-6,3-0,063 мм 67-74, мельче 0,063 мм 20-30. К тщатель
но перемешиваемому порошку добавляют воду в количестве 15-20 % (сверх 100 %). Существуют и другие схемы футеровки вагонеток.
03760
ППЛУ
(№4,11)
Рис. 9.1. Вертикальный (а) и горизонтальные (6) разрезы шахтной печи для обжига магнезита
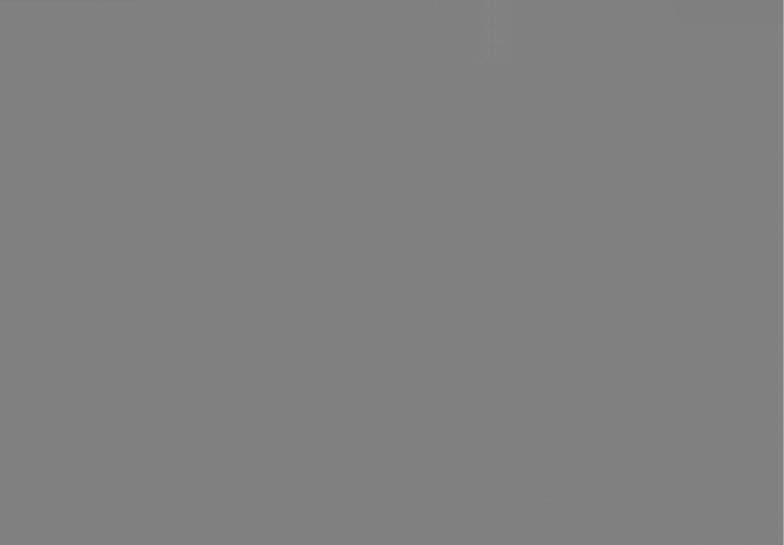
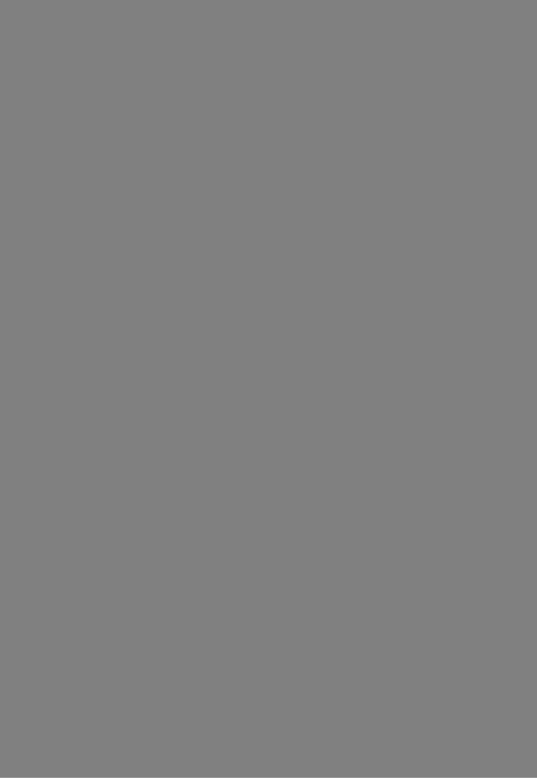
9.3. Вращающиеся печи
Вращающиеся печи, применяемые в огнеупорной промышленности, по общей кон струкции аналогичны вращающимся печам для обжига цементного клинкера (см. гл. 8), однако футеровка печей определяется их технологическим назначением, температур ным уровнем и условиями эксплуатации.
В табл. 9.1 приведены технические характеристики четырех размеров вращающих ся печей для обжига магнезита и печи для обжига глины. В футеровке этих печей применяют шамотные изделия различных видов, периклазохромитовые и хромитопериклазовые изделия. Кладку выполняют насухо со стальными пластинами или с при-
Т а б л и ц а 9.2
Огнеупорные материалы для футеровки вращающихся печей для обжига магнезита
Расстояние от |
Толщина |
Стойкость, |
Марка |
Способ кладки |
горячей |
футеровки, |
|||
головки,м |
мм |
сут |
изделия |
|
|
|
|
||
|
|
|
ПечьI |
|
0-0,1 |
220 |
400-500 |
ШЦУ, ША |
На шамотно-цементном растворе |
1,0-3,0 |
220 |
400-500 |
ША (ШБ) |
Насухо со стальными пластинами |
3,0-25,0 |
230 |
400-500 |
ША в сочетании Тоже |
|
|
|
|
сПХЦ |
|
25,0-38,0 |
230 |
400-500 |
ШЦУ |
На шамотно-цементном растворе |
38,0-49,2 |
150-160 250-300 |
ШКК, ШЦУ |
Тоже |
|
49,2-50 |
150 |
200-250 |
ША (ШБ) |
» |
|
|
|
Печь II |
|
0-1,0 |
230 |
370-470 |
ШЦУ |
На шамотно-цементном мертельном |
|
230 |
|
ША |
растворе |
1,0-3,0 |
370-470 |
На шамотно-цементном мертельном |
||
|
230 |
|
ША (ШБ) в |
растворе и стальных пластинах |
3,0-58,0 |
400-700 |
Насухо со стальными пластинами |
||
|
|
|
сочетании с |
|
58,0-74,2 |
150-160 |
|
ПХЦ |
|
400-700 |
ШКК или ШЦУ На шамотно-цементном мертельном |
|||
74,2-75,0 |
300-230 |
250-400 |
ША (ШБ) |
растворе |
Тоже |
||||
|
|
|
Печь III |
|
0-1,3 |
260 |
340-390 |
ШЦУ |
На шамотно-мертельном растворе |
1,3-48,3 |
230 |
350-400 |
ША, ХП или |
Насухо со стальными пластинами |
|
|
|
ПХЦ |
|
48,3-60,0 |
200 |
300-700 |
ШЦУ |
На шамотно-цементном мертельном |
60,0-90,0 |
160 |
300-700 |
ШЦУ, ШКК |
растворе |
Тоже |
||||
|
|
|
Печь IV |
|
0-4,0 (конус) |
230-340 |
150-250 |
ШЦУ |
На шамотно-цементном мертельном |
|
|
|
|
растворе |
4,0-23,0 |
230 |
150-250 |
ПХЦ, ХП, ШЦУ Насухо со стальными пластинами |
|
23,0-75,0 |
230 |
350-400 |
ПХЦ, ХП или |
Насухо со стальными пластинами |
|
|
|
ПХЦ.ХПв |
|
75,0-114,0 |
200 |
350-600 |
сочетании с ША |
|
ШЦУ |
На шамотно-цементном мертельном |
|||
114,0-167,0 |
200 |
600-700 |
ШКК |
растворе |
То же |