
книги / Неформованные огнеупоры. Свойства и применение неформованных огнеупоров Сост. И. Д. Кащеев [ др.]; Под ред. И. Д. Кащеева
.pdfТ а б л и ц а 5.1 Порошки периклазовые и периклазоизвестковые спеченные
для сталеплавильного производства по ГОСТ 24862-31
Нормадля марки
Наименование
показателя
Массовая доля, %: М^О, не менее СаО, не более СаО, в пределах
ЗЮг, не более Потери массы при прокаливании, %, не более Зерновой состав, %:
остаток на сетке № 10, не более
остаток на сетке № 8, не более
остаток на сетке № 6, не более
ППЭ-88 |
ППП-86 |
ППО-86 |
оо |
ППЭ-87 |
ППК-85 |
ППМ-85 |
ППП-85 |
ППО-85 |
ППИК-78 |
ППИМ-78 |
ПМС1 |
ПМС2 |
С |
||||||||||||
|
|
|
00 |
|
|
|
|
|
|
|
|
|
88 |
86 |
86 |
88 |
87 |
85 |
85 |
85 |
85 |
78 |
78 |
88 |
85 |
4 |
7 |
7 |
4 |
6 |
6 |
6 |
8 |
8 |
6- |
6- |
|
|
— |
— |
— |
— |
— |
— |
— |
— |
— |
— |
— |
||
|
|
|
|
|
|
|
|
|
12 |
12 |
|
|
4,0 |
4,0 |
4,0 |
4,0 |
4,0 |
4,5 |
— |
4,5 |
5,0 |
4,5 |
4,5 |
4,0 |
5,0 |
0,6 |
1,0 |
1,0 |
0,6 |
0,8 |
0,6 |
0,6 |
1,0 |
1,5 |
1,0 |
1,0 |
|
|
— |
— |
— |
Не |
— |
Не |
Не |
— |
— |
Не |
Не |
— |
— |
|
|
|
ДОП. |
|
ДОП. ДОП. |
|
|
доп. ДОП. |
|
|
||
— |
— |
— |
10 |
— |
10 |
10 |
— |
— |
10 |
10 |
— |
— |
— |
3 |
3 |
— |
— |
— |
— |
3 3 — |
— |
— |
— |
пмсз |
ПМС4 |
ПМС5 |
80 75 70
—— —
6,0 6,0 8,0
—— —
—— —
— —
остаток на сетке |
5 |
|
|
|
5 |
|
|
|
|
|
|
|
|
|
|
|
№ 4, не более |
|
10- |
5- |
|
|
|
|
10- |
5 |
|
|
|
|
|
|
|
остаток на сетке |
— |
|
|
|
|
|
|
|
|
|
|
|
||||
№3 |
|
30 |
20 |
75- |
|
75- |
45- |
30 |
20 |
75- |
45- |
|
|
|
|
|
остаток на сетке |
— |
— |
— |
— |
— |
— |
— |
— |
— |
— |
— |
|||||
№1 |
|
|
|
90 |
|
95 |
75 |
|
|
90 |
75 |
|
|
|
|
|
проход через |
50- |
— |
— |
10- 50- 10- 25- — |
— |
10- |
25- |
— |
— |
— |
— |
— |
||||
сетку № 1 |
85 |
|
45- |
25 |
85 |
25 |
55 |
|
45- |
25 |
55 |
|
|
|
|
|
проход через |
|
|
|
|
|
|
|
|
|
|
|
|
|
|
||
сетку № 05 |
|
|
65 |
|
|
|
|
|
65 |
|
|
|
|
|
|
|
проход через |
— |
15- |
20- |
— |
— |
— |
— |
15- |
20- |
— |
— |
— |
— |
— |
— |
— |
сетку № 01 |
|
25 |
30 |
|
|
|
|
25 |
30 |
|
|
|
|
|
|
|
Для ремонта подины стен и откосов (заправки) допускается использование хромитопериклазовых порошков, изготовленных из бывшего в употреблении кирпича (2030 % общего расхода).
Набивной из массы хромитопериклазового состава может выполняться также футе ровка крышка завалочных окон.
5.2. Сталеплавильные конвертеры
Конвертерный способ производства стали заключается в продувке жидкого чугуна кислородом. В настоящее время разработаны и освоены методы продувки конверте-
Рис. 5.2. Конвертер типа 1Л) (с верхним дутьем) Рис. 5.3. Конвертер типа ОВМ (с нижним дутьем)
Рис. 5.4. Конвертер с комбинированным дутьем |
Рис. 5.5. Конвертер с отъемным днищем: 1 |
и фурмами в днище |
— безобжиговый огнеупор на смоляной связ |
|
ке; 2 — периклазовый огнеупор; 3— шамот |
|
ный огнеупор; 4 — набивка |
ров, определяющие в основном их эффективность и условия службы огнеупоров. Раз личают конвертеры с верхним дутьем (П )) (рис. 5.2), с нижним (ОВМ) (рис. 5.3) и с комбинированным (ТВМ, ЬВЕ и др.) (рис. 5.4).
В СНГ наибольшее распространение получили конвертеры с верхним дутьем. Конвертер представляет собой большую стальную реторту, футерованную огнеупор
ными изделиями. Форма корпуса обычно грушевидная, симметричная. Корпус кисло родного конвертера состоит из днища, нижнего усеченного конуса, цилиндрической части и конической горловины. У основания верхней конической части кожуха кон вертера расположено сталевыпускное отверстие.
Днища кислородных конвертеров на большинстве предприятий отъемные (рис. 5.5), что облегчает и ускоряет ремонт футеровки, однако создает угрозу проникновения металла во время плавки. Имеются также вставные (рис. 5.6) и неотъемные днища (рис. 5.7).
Футеровку конвертеров выполняют из двух, трех и (реже) четырех слоев. Первый слой от брони — арматурный, или постоянный, защищает кожух от перегрева и мест ных прогаров. При трехслойной футеровке между внутренним (рабочим) и арматур ным слоем выкладывают промежуточный слой из смолоизвестковопериклазовой мас-
2
8
00
3
Рис. 5.6. Конвертер со вставным днищем: 1— пе- |
Рис. 5.7. Конвертер с неотъемнымднищем; обо- |
риклазошпинелидный огнеупор; 2 — безобжиго- |
значения такие же, как на рис. 5.6 |
вый огнеупор на смоляной связке; 3 — набивка |
|
сы или штучных огнеупоров для более эффективного использования рабочего слоя и удлинения кампании конвертера.
Рабочий слой днища футеруют смолоизвестковопериклазовыми огнеупорами. Стык между рабочим слоем днища и цилиндрической частью, а также выравнивание футе ровки на стыке производят набивной смолоизвестковопериклазовой массой.
В конвертере с отъемным днищем футеровку днища выполняют насухо с засыпкой швов порошком или использованием массы для заполнения неплотностей кладки. При кладке шамотным огнеупором неплотности заполняют шамотным порошком или мас сой на его основе, при кладке периклазошпинелидным огнеупором — периклазовым или периклазохромитовым порошком или соответствующими массами, при кладке
Т а б л и ц а 5.2 Порошки молотые шамота и огнеупорной глины по ТУ 1522-009-00190495-99
|
Порошки шамота |
|
|
|
|
|
|
|
|
Нормадля марки |
|
|
|
Наименованиепоказателя |
ПШКМ; |
ПШАМ; |
ПШБМ; |
ПШВМ; |
ПШПБМ; |
ПШПВМ; |
|
шнкт |
ПШАТ |
ПШБТ |
пшвт |
ПШПБТ |
пшпвт |
Массовая доля АЬОз, %, не менее |
39 |
35 |
30 |
28 |
23 |
18 |
Огнеупорность, °С, не ниже |
1750 |
1730 |
1670 |
1580 |
1670 |
1580 |
Массовая доля влаги при отгрузке, |
4 |
4 |
4 |
4 |
4 |
4 |
%, не более |
|
|
|
|
|
|
Зерновой состав порошков шамота |
|
|
||||
|
|
Нормадля марки, в процентах |
|
|||
Наименованиепоказателя |
ПШКМ; ПШАМ; ПШБМ; ПШВМ; ПШКТ; ПШАТ; ПШБТ; ПШВТ; |
|||||
|
ПШПБМ; ПШПВМ |
ПШПБТ; ПШПВТ |
||||
Проход через сетку, %, не менее: |
|
|
|
|
|
|
№3,2 |
|
100 |
|
|
|
|
№2 |
|
90 |
|
|
— |
|
№1 |
|
— |
|
|
100 |
|
№05 |
|
40 |
|
|
90 |
|
|
Порошки глин |
|
|
|
|
|
Наименование показателя |
ПГА |
ПГБ |
Нормадля марки |
|
ПГПВ |
|
|
ПГВ |
ПГПБ |
||||
Массовая доля А120з на |
|
|||||
35 |
30 |
|
28 |
23 |
18 |
|
прокаленное вещество, %, не менее |
|
|
|
|
|
|
Огнеупорность, °С, не ниже |
1730 |
1670 |
|
1580 |
1670 |
1580 |
Массовая доля влаги при опрузке, |
12 |
12 |
|
12 |
12 |
12 |
%, не более |
|
|
|
|
|
|
Зерновой состав: |
|
|
|
|
|
|
проход через сетку, %, не менее: |
|
|
|
|
|
|
№3,2 |
100 |
100 |
|
100 |
100 |
100 |
№2 |
98 |
98 |
|
98 |
98 |
98 |
№05 |
40 |
40 |
|
40 |
40 |
40 |
Примечание. Допускается по согласованию изготовителя и потребителя порошки марок ПГА, ПГБ, ПГВ поставлять с массовой долей влаги не более 18 %.
смолосвязанными огнеупорами — массой, приготовленной на смоле из магнезитово го или доломитового порошка.
Характеристики шамотных порошков по ТУ 1522-009-00190495-99 приведены в
табл. 5.2, а периклазовых по ГОСТ 24862-81 |
_ |
в табл. 5.1. |
П Т ---------- |
Одновременно с футеровкой корпуса кон- |
2 |
вертера производится кладка сталевыпускно |
|
го отверстия. Отверстие выполняют из набив |
|
ной периклазовой массы с добавкой серно |
|
кислого магния или выкладывают специаль |
|
ными блоками из высококачественного огне |
|
упора. |
|
Ремонт и восстановление изношенных уча |
|
стков футеровки конвертера производят по |
|
лусухим и факельным торкретированием, |
|
подваркой боем изделий или специальными |
|
порошками, высокотемпературной керами |
|
ческой сваркой, разбрызгиванием шлака, под |
|
варкой загущенным шлаком. Горячее торкре |
|
тирование осуществляют полусухим спосо |
|
бом с помощью магнезитовых и доломитовых |
|
масс или способом факельного торкретиро- |
|
Рис. 5.8. Схема вертикального торкретирования кон |
|
вертеров: 1— кислородная фурма; 2 — подвод торк |
|
рет-массы; 3 — подвод кислорода; 4 —подвод воды; |
|
5 — отвод воды; б — механизм вращения торкрет- |
|
фурмы; 7— направляющая для фурмы; 8—торкрет- |
|
фурма; 9 — конвертер; 10 — торкрет-покрытие; 11 |
|
Рис. 5.9. Схема напольного факельного торкретирования конвертеров: 1 — торкрет-машина; 2 — фурма; 3 — подвод торкрет-массы, кислорода, подвод и отвод воды; 4 — факел; 5 — торкрет-покры тие; 6 — конвертер
вания. Факельное торкретирование, широко применяемое во всех конвертерных це хах СНГ, осуществляют с помощью вертикальных установок (Россия, рис. 5.8) или напольных машин (Украина, рис. 5.9). Расход массы на одну операцию 2,5-5,0 т, дли тельность операции не более 15 мин. Примерный удельный расход огнеупоров на тор кретирование 350-т конвертера 2,34-2,95 кг/т стали. Для факельного торкретирования зон цапф и загрузки на некоторых отечественных предприятиях используют импорт ные массы.
Для нанесения огнеупорных шлакообразующих покрытий способом факельного тор кретирования используется ОШП-процесс, особенностью которого является приме нение торкрет-масс на основе извести, что позволяет торкретировать конвертеры с предельной интенсивностью, практически приостанавливая износ футеровки. В каче стве материала для ОШП-процесса, кроме технологической извести, можно приме нять отходы известковообжигательного производства.
Ремонт изношенных участков цилиндрической части конвертера со стороны слива металла и шлака производят подваркой боем нового или бывшего в употреблении огнеупора, который в последнее время заменяют более эффективными порошкооб разными материалами, образующими более стойкое покрытие. Используют доломитодунитовую смесь, быстроспекаюшиеся заправочные материалы и др.
Перспективным направлением восстановления и ремонта футеровки конвертеров яв ляется высокотемпературная керамическая сварка (ВКС). Сущность способа ВКС со стоит в нанесении на поврежденное место в горячей печи порошка, состоящего из кера мического материала в смеси с металлическими порошками и добавками для стабили зации процесса в среде окислителя (кислорода). Разработаны порошки, специально пред назначенные для ремонта основной футеровки сталеплавильных конвертеров.
Для горячего ремонта вместо торкрет-масс широко применяют более стойкие периклазоуглеродистые массы (бетоны) на основе плавленого и спеченного периклаза. Массы содержат от 5,5 до 15 % остаточного углерода и изготовляют на органической (смола, пек) связке. Более высокая износостойкость этих масс по сравнению с торк рет-смесями обусловлена наличием матрицы из углеродистой связки и использовани ем для изготовления масс более чистого периклаза, что обеспечивает их лучшую ус тойчивость к термическим нагрузкам и химическому воздействию. Наряду с этим высокая прочность масс при повышенных температурах и, следовательно, высокая устойчивость к абразивному износу делают их пригодными для применения в зонах падения металлического лома и соединения днища с корпусом. В зоне падения метал лического лома защитный слой из периклазоуглеродистых масс служит 10-20 плавок, в зоне соединения днища со стенами — до 40 плавок. Удельный расход этих масс составляет 0,1-0,4 кг/т стали.
5.3. Дуговые сталеплавильные печи
Дуговые сталеплавильные печи (ДСП) различаются по вместимости, удельной мощ ности, способам загрузки шихты и выпуска металла. Вместимость дуговых печей по стоянно возрастает. В СНГ максимальная вместимость ДСП 150 и 200 т.
По удельной мощности (отношению мощности трансформатора к вместимости) печи подразделяются на печи обычной, высокой и сверхвысокой мощности; по способу
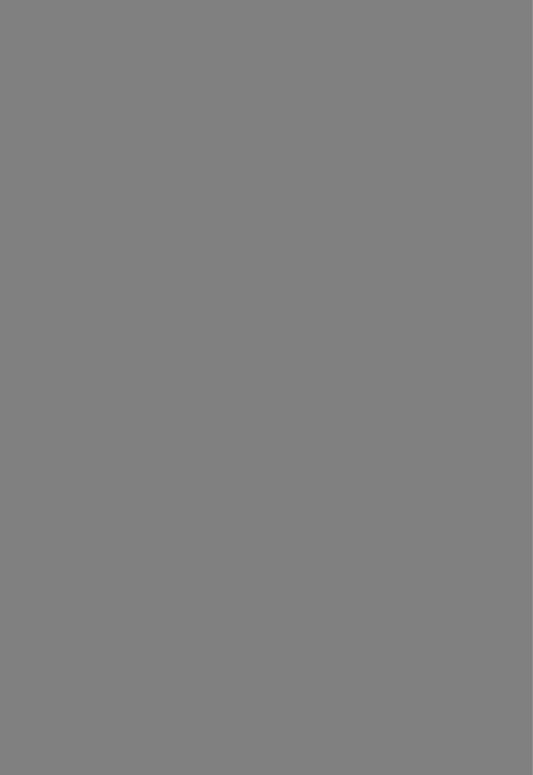
ют в зависимости от типа печи и температуры в различных слоях кладки. Швы долж ны перекрываться последующим рядом кладки. Между откосами и кожухом оставля ют вертикальный зазор, заполняемый периклазовым порошком.
Набивку рабочего слоя подины и откосов производят сухими прогретыми периклазовыми порошками с помощью пневматических трамбовок, вибраторов или виброштыревых устройств. При выполнении набивки увлажненным порошком в качестве связок применяют водный раствор жидкого стекла плотностью 1,15-1,17 г/см3 в коли
честве 5-8 %, каменноугольную смолу, пек и др.
Зерновой состав периклазового порошка должен включать 15-20 % фракции мельче
0,1 мм и 10-30 % 3-6 мм.
Сочленение кладки откосов и подины является наиболее вероятным местом ухода металла из-за смещения нижней части откосов при термическом расширении кладки подины и раскрытия швов в районе стыка, чему способствуют компенсационные швы,
закладываемые около кожуха печи.
Рациональная конструкция кладки в районе сочленения подины с откосами, а также конструкция швов и составы порошков для их заполнения (перемещение шва между кожухом и подиной в район сочленения кладки подины, откосов и набивной футеров ки, уменьшение толщины кладки откосов и образование металлонепроницаемого слоя из порошка соответствующего зернового состава и др.) способствуют уменьшению разрушения кладки откосов и увеличивают стойкость подины и откосов. Увеличение толщины набивного слоя подин (до 500 мм) за счет кирпичной кладки, практикуемое в последние годы, позволяет отказаться от теплоизоляционного слоя и повысить на дежность и стойкость подин. Повышение механической прочности утолщенного на бивного слоя за счет армирования подины из мелкозернистых порошков крупнозер-
Т а б л и ц а 5.3
Мертели алюмосиликатные по ГОСТ 6137-97
Предназначены для связывания алюмосиликатных изделий в огнеупорной кладке и подразделяются на марки, указанные ниже. По согласованию мертели МШ36 и МШЗ1 изготовляют с проходом через сетку № 2 — не менее 100 %, № 05 — 60-94 %.
Все мергели, за исключением МП16и ММК85, изготовляют пластифицированными. Мертель ММК85 пластифицируют у потребителя. Мертели МП18, МШЗ 1, МШ28 и ММЛ62 по согласованию изготов ляют непластифицированными. Все мертели термотвердеющие, мертели МШ36 и МШ39 могут из готовляться воздушнотвердеющими при введении у потребителя жидкого стекла.
|
|
Физико-химические показатели |
|
|
|
||||
Марка |
МП18 МШ39 МШ36 МШ31 МШ28 ММЛ62 |
ММК85 ММК77 ММК72 |
|||||||
Массовая доля, %: |
|
|
|
|
|
|
|
|
|
А120з, не менее |
18 |
39 |
36 |
31 |
28 |
62 |
85 |
77 |
72 |
Ре20з, не более |
— |
1,8 |
1,6 |
— |
— |
1,5 |
0,9 |
1,6 |
1,5 |
Ка2С0 3 |
1,12- |
0,12- |
0,12- 0,12- |
0,12- |
0,12- |
— |
0,12- |
0,12- |
|
лет |
0,18 |
ОДв |
ОДв |
0,18 |
0,18 |
0,18 |
|
0,18 |
0,18 |
0,07- |
0,07- 0,07- 0,07- |
0,07- |
0,07- |
— |
0,07- |
0,07- |
|||
Изменение массы при |
0,13 |
0,13 |
0,13 |
0,13 |
0,13 |
0,13 |
1,2- 1,9 |
0,13 |
0,13 |
1,3-3 |
1,3-2 |
1,3-3 |
1,8-3,2 |
1,3-3 |
1,5-3 |
1,2-1,9 |
1,6-3 |
||
прокаливании, % |
1610 |
1730 |
1730 |
1690 |
1650 |
1790 |
|
|
|
Огнеупорность, °С, не |
_ |
|
|
||||||
|
|
|
|
|
|
|
|
|
|
ниже |
|
|
|
|
|
|
|
|
|
Влажность, %, не более |
6 |
5 |
5 |
5 |
5 |
5 |
2 |
3 |
5 |
Масса муллитокорундовая набивная марки ММК-88 для футеровки сталеразливочных ковшей по ТУ У 322-7-00190503-123-97
Наименование показателя |
Норма |
Массовая доля на прокаленное вещество %: |
|
АЬОз, не менее |
88 |
РегОз, не более |
1,0 |
Р2О5, в пределах |
2,5-3,0 |
Изменение массы при прокаливании, %, в пределах |
1,2- 2,2 |
Массовая доля влаги, %, в пределах |
4,5-6,0 |
Зерновой состав, %: |
|
проход через сетку: |
|
№ 3,2, не менее |
97 |
№ 1, не менее |
45 |
№ 05, не менее |
40 |
№ 009, в пределах |
36-46 |
нистыми материалами того же состава существенно снижает степень износа подины при ударах шихты во время загрузки.
Футеровку стен выполняют из трех слоев: изоляционного, арматурного и рабочего. Для изоляции используют листовой асбест и шамотный порошок. Арматурный слой выкладывают хромитопериклазовыми, а рабочий слой — периклазохромитовыми из делиями. Кладку ведут насухо с пересыпкой швов между кирпичами сухим периклазовым порошком.
Рис. 5.11. Сталевыпускной желобДСП: 7— сте- |
Рис. 5.12. Сифонный сталевыпускной узел: 1 — |
на; 2— футеровка; 3— откос; 4— кладка поди- |
стена; 2 — откос; 3 — кладка подины; 4 — набив- |
ны; 5 — набивная подина |
ная подина; 5 — сифонный канал |
Рис. 5.13. Донный сталевыпускной узел, |
Рис. 5.14. Узел донного выпуска стали: 1 — кладка |
расположенный в выступе ванны (эркере): |
подины из периклазовых изделий ПУ; 2 — набивная |
1— кладка подины; 2 — набивная подина; |
подина из периклазового порошка марки ППЭ-88; 3 |
3 — выпускной узел; 4 — торцовая стена |
— периклазоуглеродистые трубки марки ПУПЭ; 4 — |
эркера; а — уровень шлака; б — уровень |
гнездовой блок марки ПГРБС; 5 — периклазоуглеро- |
металла |
дистая втулка марки ПУПЭ; б — затвор; 7— засыпка |
|
из обожженного дунитового порошка |
Наиболее изнашиваемой частью свода является его центральная часть в районе рас пада электродов. В последних моделях ДСП используют водоохлаждаемые своды, состоящие из центральной части, футерованной огнеупорными изделиями, и охлаж даемой периферийной части. Для футеровки центральной части применяют муллито корундовые и периклазохромитовые изделия. Кладку ведут на муллитокорундовом мертеле ММК-85 или периклазовом порошке, а зазоры между кольцами электродных отверстий и остальной кладкой набивают муллитокорундовой массой ММК-88. Ха рактеристики муллитокорундовых мертелей по ГОСТ 6137-97 приведены в табл. 5.3, а муллитокорундовой массы по ТУ У 322-7-00190503-123-97 — в табл. 5.4.
Сталь из ДСП выпускают через желоб — отверстие в стене выше уровня металла (рис. 5.11), через отверстие в стене с футерованным каналом, начало которого распо ложено ниже уровня жидкого металла, — сифонный выпуск (рис. 5.12) или через от верстие в подине, расположенное в специальном выступе-эркере, — эркерный, или донный асимметричный, выпуск (рис. 5.13). Узел донного выпуска показан на рис. 5.14.
Кладку сталевыпускного отверстия или желоба, расположенных выше уровня жид кой стали, а также столбиков и откоса под выпускным отверстием выполняют из пе риклазовых изделий насухо с засыпкой швов периклазовым порошком.
Кладку сталевыпускного отверстия с сифонным выпуском металла производят из пе риклазовых колец или блоков. Перед началом завалки сталевыпускной канал заполняют периклазовым порошком ППЭ-88, ППЭК-87. Кладку откосов в районе отверстия и же лоба ведут уступами из периклазовых изделий. Поверхность кладки откоса под футе ровку отверстия выравнивают массой из периклазового порошка ППЭ-88 на водном растворе жидкого стекла плотностью 1,20-1,25 г/см3 и утрамбовывают. Зазоры между футеровкой канала и кладкой откосов заполняют и уплотняют этой же массой.