
книги / Неформованные огнеупоры. Т. 1 Общие вопросы технологии
.pdfДополнительно через дефис ставится цифра, обозначающая содержание в массе карбида кремния (например, ВГМВ-23).
Во многих случаях (прежде всего — зарубежные фирмы-производители) в марки ровку включаются первые буквы наименования фирмы, а далее — последующая ин формация (способ применения или укладки, содержание основного компонента и т.д.). Рассмотрим примеры маркировки неформованных огнеупоров, производимых меж дународной фирмой “РНЬпсо” [2.22]. Для плотных вибролитых традиционных бето нов на ВГЦ принята маркировка “РНсазГ, для плотных вибролитых низкоцементных (“ЬС”) бетонов принята маркировка “РНсаз* ЬС”, для плотных вибролитых сверхниз коцементных (“1Л.С”) бетонов — “РНсаз! 1ЛЛ Для саморастекающихся (литых — Яо^) бетонов принято аналогичное обозначение — “Р1Шо>у” . Д ля пластичных масс приняты обозначения: “РНЬпсо 51апс1агсГ (А120 3 = 27-30 %), “РНЬпсо Зирег” (А120 3 = 40-50 %), “РНЬпсо 60АВ - РНЬпсо 90АВ” (А120 3 = 60-90 %).
Для набивных (гашшеп) масс принята маркировка “РПгаш”, легочных масс— “Р1йар”, виброуплотняемых сухих смесей — “Р1мЬе”, инжекционных нагнетаемых масс для ремонта — “Р1уес1” и т.д.
2.5. Тенденции развития и применения неформованных огнеупоров
Развитие производства неформованных огнеупоров связано прежде всего с нарас тающим объемом их применения в производстве стали. По ориентировочным дан ным, около 75 % всех производимых в Японии неформованных огнеупоров использу ется в черной металлургии.
Как отмечено в работе [2.38], понижение показателя удельного расхода огнеупоров по мере постепенного увеличения доли применяемых неформованных огнеупоров свя зано с лучшей их пригодностью клональномуремонту по сравнению с формованными огнеупорами. Даже в том случае, когда стойкость неформованных огнеупоров уступа ет таковой для формованных, то и тогда удельный расход удается понизить за счет периодического выполнения локального ремонта, что невозможно при обычной (кир пичной) футеровке. В связи с изложенным, именно по этой причине в области нефор мованных огнеупоров значительно увеличивается производство бетонов и торкрет-
50 1
Рис. 2.2. Динамика изменения относительной доли про |
|
изводства огнеупорных бетонов (7), торкрет-масс (2) и |
_____ I_____ |_____ |_____ |_____ |
набивных масс (3) в общем выпуске неформованных ог- |
1975 1980 1985 1990 1995 2000 |
неупоров в Японии за 1975-2000 гг. |
Годы |
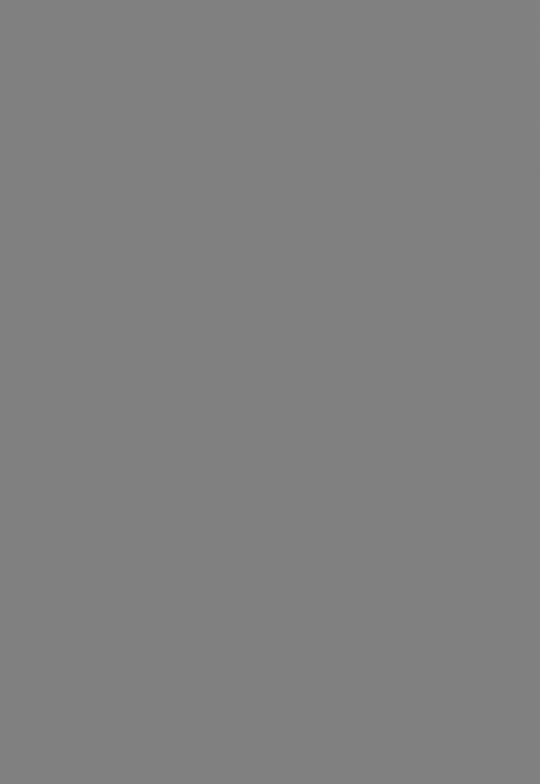
торкретирования наносится рабочий торкрет-слой (4). Если арматурная футеровка (тол щина 120-150 мм) характеризуется высокой плотностью, механической прочностью
ивысокой стойкостью (до нескольких сотен плавок), то рабочий слой (40-50 мм) от личается достаточно высокой пористостью (40-50 %), низкой теплопроводностью, механической прочностью и стойкостью не выше 10-12 плавок. Теплозащитная крышка промковша (5) футерована высокопористым (теплоизоляционным) бетоном алюмо силикатного состава и выполняется или методом литья (при достаточно высоком со держании ВГЦ и воды) или набивной. С целью повышения стойкости рабочего и ар матурного слоя футеровки в месте падения струи расплава устанавливают бойную плиту (б), которая должна характеризоваться максимальной плотностью, прочностью
иизносоустойчивостью. Для обеспечения требуемого гидродинамического режима и улучшения режима работы в промковше устанавливают перегородочные плиты (по роги) преимущественно высокоглиноземистого состава (7). Как бойные плиты, так и перегородочные плиты устанавливают в виде предварительно отформованных и тер мообработанных бетонных изделий. Как показала практика промышленных испыта ний на НТМК, для этой цели оптимальными являются высокоглиноземистые керамобетонные блоки (плиты), полученные на ВКВС боксите с применением корундового заполнителя. Важной составной частью футеровки промковша является и гнездовой блок (8). Последние могут устанавливаться как в виде предварительно изготовленных изделий, например, из керамобетона [2.34], так и изготавливаться “по месту” методом набивки по шаблону.
2.6. Преимущества и проблемы применения
неформованных огнеупоров
Увеличение относительной доли производства и потребления неформованных ог неупоров обусловлено рядом неоспоримых их преимуществ. Последние могут рас сматриваться с точки зрения как производителя, так и потребителя. Обобщающие дан-
|
|
Т а б л и ц а 2.9 |
|
Условия производства и применения формованных (кирпичи) |
|||
и неформованных огнеупоров (сравнение характерных данных) |
|||
Условия |
Огнеупорные |
Неформованные |
|
кирпичи |
огнеупоры |
||
|
|||
Производство огнеупоров: |
30-50 |
10-15 |
|
площадь цеха, м2/(т-ч) |
|||
производительность, т/чел .-мес. |
5-20 |
40-100 |
|
топливо (мазут), л/т |
200-655 |
20-30 |
|
электроэнергия, кВт- ч/т |
150-300 |
30-50 |
|
возможности для автоматизации |
Трудные |
Легкие |
|
Использование огнеупоров: |
Лимитированы |
Легкие |
|
мероприятия по транспортировке |
|||
механизация футеровочных работ |
Трудная |
Легкая |
|
производительность футерования, т/чел .-суг |
0,5-2,0 |
5,0-20,0* |
* Высокая благодаря эффективным способам футерования и футеровочному оборудованию.
ные по их эффективности представлены в табл. 2.9, явившейся итогом анализа произ водства и применения неформованных огнеупоров в Японии в период до 1980 г. [2.19].
Согласно данным [2.19], преимущества неформованных огнеупоров, с точки зрения производителя, состоят в следующем:
1.Повышение производительности (сокращение затрат труда). Согласно данным [2.9], в Японии производство огнеупорных штучных изделий составляет 5-20 т на человека в месяц. Производство же неформованных повышается до 40-100 т. Боль шую роль здесь играет возможность автоматизация технологических процессов и их непрерывность, что гораздо труднее реализовать при производстве штучных изделий.
2.Сокращение расхода энергии. В зависимости от вида огнеупоров на производство неформованных огнеупоров удельные энергозатраты в 5-6 раз, а затраты технологи ческого топлива в 10-20 раз ниже, чем в случае штучных.
3.Снижение издержек производства. Последнее, кроме отмеченных факторов (п. 1, 2), обусловлено упрощенной технологией (отсутствием дорогостоящих прессов, про цесса обжига), большим выходом годного продукта (в производстве штучных огне упоров брак может быть существенным), благоприятными условиями создания по точных процессов.
4.Уменьшение складских запасов и сроков хранения. При производстве обычных
(штучных) огнеупоров каждым предприятием производится широкая номенклатура изделий различных форм. При этом многие виды изготовляются в относительно не большом количестве, а процесс их производства длителен. И в то же время необходи мы складские запасы изделий, так как заказы потребителей необходимо выполнять без задержек. Неформованные традиционные огнеупоры можно изготавливать в зна чительных количествах, так как они имеют большую область применения (могут при меняться для футеровок различных агрегатов и габаритов). Учитывая, что продолжи тельность технологического процесса для неформованных огнеупоров невелика, от падает необходимость в создании запасов. Благодаря изложенному, удельные произ водственные площади в технологии неформованных огнеупоров в 3 раза ниже.
5.Экологические преимущества. Несмотря на то, что при производстве неформо ванных огнеупоров используются сыпучие материалы (порошки и заполнители) все технологические операции можно осуществлять в закрытой системе. При получении же керамобетонов применяют мокрые (беспыльные) процессы. Отсутствие высоко температурных процессов (выделение газов типа С 02) также улучшает экологические условия.
Преимущества неформованных огнеупоров, с точки зрения потребителей, состоят
вследующем:
1.Большая свобода проектирования. Можно выполнить монолитную футеровку или изготовить крупные фасонные блоки любой формы.
2.Бесшовность футеровки. Применение огнеупорных бетонов позволяет решить проблему так называемой “шовности” обычной огнеупорной кладки. Разрушение пос ледней, как правило, начинается по швам, так как материал шва (мертель) характери зуется существенно большей пористостью, чем огнеупор. В монолитной же футеров ке швы полностью отсутствуют.
3.Упрощение ремонтных работ, экономия материалов. При помощи неформован ных материалов представляется возможным осуществлять ремонт (в том числе “горя-
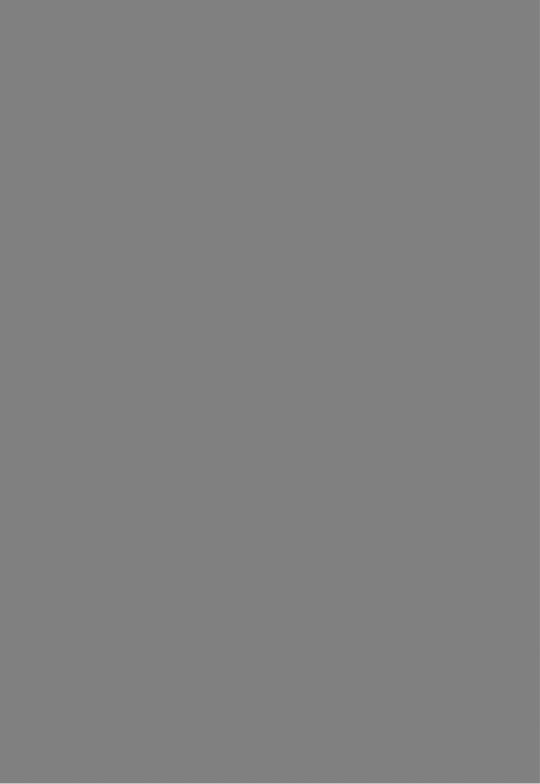
нию доли неформованных огнеупоров (до 60 % в последние годы). Таким образом, переход на неформованные огнеупоры способствует снижению общего энергопотреб ления в производстве, хотя некоторые процессы в их производстве отличаются боль шей энергоемкостью по сравнению с формованными. Во-первых, применение нефор мованных огнеупоров обычно предусматривает их увлажнение и перемешивание при изготовлении футеровки, а обезвоживание и горячая сушка (разогрев перед службой) требуют затрат энергии. Во-вторых, в сравнении с формованными изделиями, в про изводстве неформованных огнеупоров применяют большую долю энергоемкого сы рья, например, карбида кремния, корунда, периклаза.
Таким образом, неформованные огнеупоры по сравнению с формованными отлича ются наличием энергоемких процессов вне основного производства. Однако, темпе ратура сушки неформованных огнеупоров невысока, и при использовании малоэнер гоемкого сырья они по сравнению с формованными огнеупорами являются энерго сберегающими [2.38].
В рассмотренном аспекте весьма эффективно применение отходов огнеупоров в производстве неформованных огнеупоров [2.39]. В частности, успешно опробована добавка в бетонную смесь для футеровки сталеразливочных ковшей отходов торкре тирования промежуточных ковшей (материал “отскока”, который не сцепляется с ос новной футеровкой при торкретировании).
Посредством применения различных типов неформованных огнеупоров (прежде всего — бетонов) решается проблема так называемой “шовности” обычной огнеупор ной кладки. В процессе службы (например, сталеразливочных ковшей) разрушение кладки, как правило, начинается по швам. Обусловлено это тем, что безобжиговый материал шва характеризуется существенно меньшей плотностью и прочностью, чем материал соответствующего огнеупорного кирпича. В качестве примера на рис. 2.6 по данным [2.6] приведены данные по изменению прочностных свойств (а иэг) материа лов мертеля после различных температур их термообработки.
С учетом того, что первичный разогрев огнеупорной футеровки осуществляют до 900-1000 °С, можно предположить, что минимальной прочностью швы футеровки ха рактеризуются на первой стадии их эксплуатации. Но даже после термообработки при
|
|
|
|
Рис. 2.6. Влияние температуры предварительной тер |
|
|
|
|
мообработки на показатели предела прочности при |
|
|
|
|
изгибе воздушнотвердеющих огнеупорных растворов: |
|
|
|
|
1— высокоппиноземистый; 2,3 — шамотные различ |
0 |
500 |
1000 |
1500 |
ных составов; 4 — динасовый; 5 — изоляционный; б |
|
Температура термообработки, °С |
— термотвердеющий шамотный мертель |
Рис. 2.7. Сопоставительный пример кирпичной (У) и монолитной (блочной) футеровки (2)
высоких температурах их прочность существенно ниже, чем таковая для обжиговых огнеупоров различных классов.
Простой и наглядный пример эффективности применения огнеупорных бетонов взамен кладки из огнеупорного кирпича приведен на рис. 2.7.
В случае кирпичной футеровки для выполнения последней с площадью 1 м2 требу ется 63 стандартных кирпича, что соответствует наличию в кладке 252 швов. В случае же предварительно отформованного блока с той же рабочей площадью при установке количество швов уменьшается до 4.
Несмотря на многие преимущества, существуют проблемы, связанные с применени ем неформованных огнеупоров [2.3, 2.18].
По сравнению с формованными (обжиговыми) огнеупорами, многие традиционные неформованные (в том числе бетоны) имеют пониженные характеристики, например, по показателям огнеупорности и химической стойкости. Обусловлено это, как прави ло, соответствующими свойствами вяжущей системы бетонов.
Некоторые проблемы связаны с технологией. Монолитная футеровка, образно го воря, представляет собой большое фасонное изделие, изготавливаемое непосредствен но (например, в сталелитейном цехе). Поэтому весьма актуальны вопросы правильно го применения огнеупорных бетонов, их однородность, технологичность (удобоукла- дываемостъ). И если для обжиговых огнеупоров на всех технологических стадиях производителем осуществляется надежный контроль и, как следствие, воспроизводи мы результаты службы, то в случае применения бетонов может наблюдаться двух- и трехкратный разброс по их стойкости. Обусловлено это тем, что часть технологичес ких процессов в последнем случае выполняется у потребителя. А между тем даже незначительные нарушения, например, в дозировке воды, условий смешения и уклад ки обуславливают понижение ресурса службы футеровки. В качестве примера на рис. 2.8 показано влияние влажности исходных формовочных систем на показатели пористости и предела прочности при сжатии а сжкак бетонов, так и торкрет-масс.
Немаловажное значение при применении неформованных огнеупоров имеет также температура воды, помещения и футеруемого агрегата (например, арматурной футе ровки сталеразливочного ковша).
Важнейшим технологическим параметром бетонов является продолжительность их твердения, определяющая, например, время извлечения шаблона при изготовлении
Рис. 2.8. Влияние технологической влажности смеси IVна открытую пористость Птки предел проч ности при сжатии стсж бетонов: У, 2— низкоцементный бетон в системе А120 3 (40,6 %) - 8Ю2 (54,1 %) - СаО (1 %) после сушки (У) и термообработки при 1000 °С (2); 3,4 — бетон в той же системе с обыч ным содержанием цемента (4,3 % СаО) после сушки (3) и термообработки при 1000 °С (4); 5 — вибролитой улучшенный материал на основе 2г8Ю4; б— он же при нанесении торкретированием; 7
— обычный бетон из 2г8Ю4 для торкретирования
монолитных футеровок. Кинетика твердения в значительной степени зависит от тем пературы. Например, при бетонировании желоба доменной печи при повышении тем пературы оставшейся футеровки с 20 до 50 °С время извлечения шаблона уменьшает ся с 4 до 2 ч, а при 80 °С — до 1ч [2.3].
Характерной особенностью низкоцементных огнеупорных бетонов (например, по сравнению с обычными на ВГЦ или с набивными массами) является пониженная их пористость и более тонкокапиллярная структура (рис. 2.9).
Эти факторы, в свою очередь, определяют ее проницаемость, что оказывает суще ственное влияние на условия сушки и начального этапа термообработки этих бето нов. Особые сложности отмечаются при сушке толстостенных крупногабаритных футеровок.
Важными технологическими параметрами рассматриваемых бетонов с точки зре ния режимов сушки являются содержание в них цемента и условия (температура, про-
Рис. 2.9. Интегральные кривые пористости низкоце ментного литого огнеупорного бетона (У) и набивной массы аналогичного состава (2); 4п— диаметр пор
Рис. 2.10. Кривые распределения температуры ( и внутреннего давления р в блоке низкоцементного огнеупорного бетона на глубине 30 (7) и 90 мм (2) в процессе сушки по режиму (3)
должительность) предварительной выдержки. Указанные факторы определяют, в час тности, содержание химически связанной жидкости, усложняющей процесс бездефек тной сушки. Массовые потери при прокаливании для низкоцементных и обычных на ВГЦ огнеупорных бетонов составляют 1,15 и 4,5 % соответственно.
При неоптимальном режиме сушки и термообработки в бетонах образуются сколы, трещины и происходит явление так называемого “взрывного растрескивания”, сопро вождающееся сильным шумом [2.32]. Причиной взрывного растрескивания считает ся превышение критического давления пара внутри бетона в процессе сушки. Экспе риментальные исследования по изучению условий сушки и оптимизации процесса проведены в ряде работ, обобщенных в [2.3]. В них решались проблемы, связанные с измерением давления пара внутри бетона при сушке, изменением характеристик бе тонов, перемещением (миграцией) влаги, установлением оптимального режима и тем пературы окончания процесса.
В качестве примера подобных исследований на рис. 2.10 показана кинетика прогре ва и внутреннего давления в блоке низкоцементного бетона с пористостью 14,1 % и с изг = 7 Н/мм2 (в высушенном состоянии) на различной его глубине.
Видно, что максимальные внутренние напряжения, которые наиболее опасны с точ ки зрения эффекта взрывного растрескивания, для различных глубин в бетоне соот ветствуют различным участкам режима сушки.
К недостаткам всех типов низкоцементных бетонов относится экологический фак тор, связанный с применением у потребителя сухих порошков. В этом отношении у керамобетонных масс, поставляемых в увлажненном состоянии, есть несомненные преимущества.
2.7. Огнеупорные бетоны
В соответствии с определением, принятым в отечественной литературе [2.40-2.41],
огнеупорными бетонами называют безобжиговые композиционные материалы с ог неупорностью от 1580 °С и выше, состоящие из огнеупорного заполнителя, вяжуще го материала, добавок и пор, затвердевающие при нормальной или повышенной тем пературе и обладающие ограниченной усадкой при температуре применения.
В определении “огнеупорный бетон” (РеиегЬе(оп), принятом в Германии, под после дним подразумевают материал, полученный по бетонной технологии на основе тепло- и жаростойких заполнителей.... и предназначенный для службы в области температур 350-2000 °С [2.5, с. 19], т.е. это определение охватывает и класс жароупорных вето- нов. Согласно определению [2.42, с. 4], жароупорным бетоном называют специаль ный вид бетона, способный сохранять в заданных пределах основные физико-механи ческие свойства при длительном воздействии на него высоких температур. Согласно [7, с. 119], огнеупорные бетоны определяются как огнеупоры с огнеупорностью выше 1500 °С.
Созданию современных огнеупорных бетонов предшествовал 100-летний эволюци онный путь их развития. Согласно данным [2.5, с. 22], первый патент Германии, каса ющийся создания жароупорного бетона, выдан 23.10.1901 г. Фредерику Валеру за № 134820 (“СетепФеЮп ипб УегГаЬгеп гиг Аизк1е1с1ип§ уоп Ееиегип§8ап1а8еп”). Этот бетон состоял из цемента и природных жаростойких заполнителей.
ВРоссии (в Санкт-Петербурге) в 1903 г. строителем Житкевичем была опубликова на статья “Бетон как огнеупорный строительный материал” (цитируется по [2.5]).
Начало развития огнеупорных бетонов в США (фирма “РНЬпсо”) относится к двад цатым-тридцатым годам. При этом в качестве вяжущего использовали как цемент, так
ижидкое стекло [2.19].
В1925 г. в США и в 1926 г. в Западной Европе были запатентованы гидравлически твердеющие огнеупорные бетоны, из которых сначала изготовляли блоки для футе ровки туннеля горелки [2.19]. Развитие и расширение применения огнеупорных бето нов в Японии в конце 40-х годов было связано с тем, что на военных базах США паровые котлы футеровали только огнеупорными бетонами и пластичными массами. Кроме того, футеровку всех паровых котлов тепловых электростанций также осуще ствляли огнеупорными бетонами.
Систематическое исследование жароупорных бетонов в СССР было начато в 1942 г. [2.42].
Прогресс в области гидравлически твердеющих огнеупорных (или жаростойких) бетонов в значительной мере был определен соответствующими достижениями в об ласти создания новых цементов и повышения их свойств. Важнейшим этапом при этом явилась разработка и применение высокоглиноземистых цементов (фирма “ЬаГаг^е”, Франция).
Однако традиционные огнеупорные бетоны гидратационного твердения, которые содержат значительное количество ВГЦ, характеризуются значительными недостат ками. Как показывает анализ составов, структуры и свойств традиционных огнеупор ных бетонов, носителем огнеупорных свойств в них является заполнитель. Роль вяжу щего сводится к обеспечению необходимой транспортной монтажной прочности бе тонов после твердения и сушки. При последующем нагреве до температур, предше ствующих спеканию, в вяжущем, как правило, протекают необратимые деструктив ные процессы. С учетом того, что в структуре бетона вяжущее совместно с тонкомо лотыми добавками является матричной (непрерывной) фазой, отмечается существен ное понижение термомеханических характеристик материала. Поэтому основным на правлением в совершенствовании известных и создании новых огнеупорных бетонов является предельно возможное снижение содержания в них традиционных (напри