
книги / Изучение функциональных свойств многослойных пленок на основе двух- и трехкомпонентных нитридов тугоплавких металлов и их соединений с легкоплавкими металлами и неметаллами
..pdf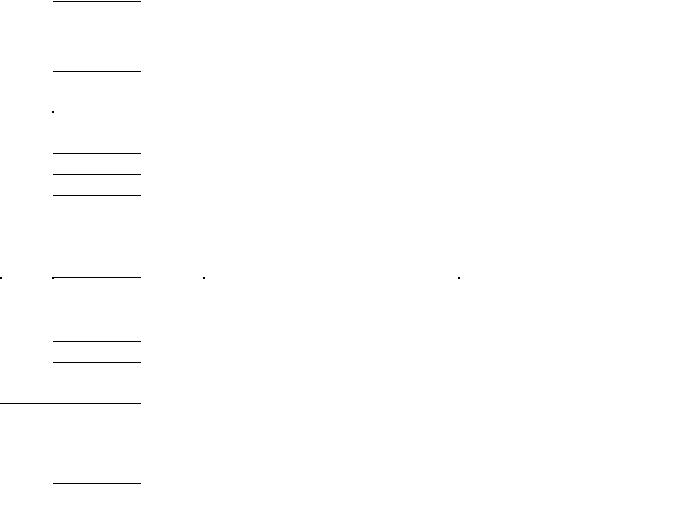
91
Таблица 3 . 1 7 Трибологические свойства многослойных пленок на основе Ti1–хAlхN слоев, сформированных МР, ЭДИ и ЭДИ+МР
|
|
|
|
|
|
|
|
|
|
|
ТемП |
|
|
m |
,·10 |
–5 |
V |
,·10 |
–4 |
|
|
V |
,·10 |
–8 |
|
|
|
|
|
||||||
|
|
|
|
|
|
|
|
|
|
|
|
|
|
|
|
|
|
|
|
||||||||||||||||
|
|
|
|
|
|
|
|
|
|
|
|
|
Iп |
|
Iп |
|
|
I |
|
|
|
|
|
|
|
|
|||||||||
|
|
|
|
|
|
|
|
|
|
|
|
–3 |
|
|
|
к |
|
dп, |
Vк, ·10 |
–3 |
|
Мтр, |
|||||||||||||
|
|
|
|
|
|
|
|
|
|
|
|
|
|
|
|
|
|
|
|||||||||||||||||
|
|
|
ТехП |
|
|
|
|
|
|
|
Vнагр.с, |
m, ·10 |
|
мг |
|
|
|
|
3 |
|
|
|
|
|
|
3 |
|
|
|
f |
|||||
|
|
|
|
|
|
|
|
|
|
|
|
|
|
|
|
|
|
|
|
|
|
|
|
|
|
|
|||||||||
|
|
|
|
|
|
|
|
|
|
|
Тс, К |
|
К/мин |
мг |
|
|
мм |
|
|
|
мм |
|
мм |
мм/с |
|
|
Н·м |
||||||||
|
|
|
|
|
|
|
|
|
|
|
|
|
|
|
|
|
|
|
|
|
|
|
|
|
|
|
|
|
|||||||
|
|
|
|
|
|
|
|
|
|
|
Н·м |
|
Н·м |
|
|
|
Н·м |
|
|
|
|||||||||||||||
|
|
|
|
|
|
|
|
|
|
|
2 |
|
|
|
|
|
|
|
|
|
|
|
|
||||||||||||
|
|
|
|
|
|
|
|
|
|
|
|
|
|
|
|
|
|
|
|
|
|
|
|
|
|
|
|
|
|
|
|
|
|
|
|
|
|
|
1 |
|
|
|
|
|
|
|
3 |
4 |
|
5 |
|
|
|
|
6 |
|
|
|
|
|
|
7 |
|
|
8 |
9 |
|
10 |
11 |
||
|
|
|
|
|
|
|
|
|
|
|
|
|
|
|
|
|
|
|
|
|
|
|
|
|
|||||||||||
|
Магнетронное распыление: общие ТехП: Uвыс = 600 В; tи.о = 5 мин; Vнагр.подл = 70 К/мин; N = 2,0 кВт; Р = 1,0 Па; Uсм = 80 В; |
||||||||||||||||||||||||||||||||||
|
|
|
|
|
|
|
|
|
|
|
605…620 |
|
N2 = 35 %, LAl = 270 мм и LTi = 100 мм (* – tи.о = 20 мин) |
|
|
|
|
|
|||||||||||||||||
|
Р, Па |
0,8 |
|
|
0,3 |
6,5 |
7,80 |
|
3,50 |
|
|
|
3,77 |
|
0,81 |
1,09 |
|
0,13 |
0,15 |
||||||||||||||||
|
|
|
|
|
|
605…625 |
|
|
|
|
|
|
|
|
|
|
|
|
|
|
|
|
|||||||||||||
1,0 |
|
|
0,4 |
5,4 |
6,08 |
|
2,76 |
|
|
|
2,15 |
|
0,62 |
0,84 |
|
0,12 |
0,14 |
||||||||||||||||||
|
|
|
|
|
|
|
|
|
|
|
605…630 |
|
|
|
|
|
|
|
|
|
|
|
|
|
|
|
|
||||||||
|
|
|
|
|
|
1,2 |
|
|
0,6 |
2,9 |
3,54 |
|
0,92 |
|
|
|
0,68 |
|
0,53 |
0,72 |
|
0,09 |
0,11 |
||||||||||||
|
|
|
|
|
|
|
|
|
|
|
605…610 |
|
|
|
|
|
|
|
|
|
|
|
|
|
|
|
|||||||||
|
|
|
|
|
|
40 |
|
|
|
0,1 |
12,7 |
14,78 |
|
8,58 |
|
|
|
10,24 |
4,12 |
5,57 |
|
0,25 |
0,30 |
||||||||||||
|
Uсм, В |
|
|
|
|
|
605…615 |
|
|
|
|
|
|
|
|
|
|
|
|
|
|
|
|
||||||||||||
60 |
|
|
|
0,2 |
10,5 |
12,25 |
|
7,53 |
|
|
|
9,56 |
|
3,05 |
4,12 |
|
0,17 |
0,19 |
|||||||||||||||||
|
|
|
|
|
|
|
|
|
|
|
690…710 |
|
|
|
|
|
|
|
|
|
|
|
|
|
|
|
|
||||||||
|
|
|
|
|
|
80* |
|
0,4 |
1,2 |
0,12 |
|
0,38 |
|
|
|
0,18 |
|
0,38 |
0,51 |
|
0,08 |
0,10 |
|||||||||||||
|
|
|
|
|
|
|
|
|
|
|
|
|
|
|
|
|
|
|
|
||||||||||||||||
|
Электродуговое |
|
|
испарение: общие ТехП: Uвыс = 1000 В; tи.о = 20 мин; Vнагр.подл = 25 К/мин; Uсм = 200 В; N2 = 100 %; Iд =75 А; |
|||||||||||||||||||||||||||||||
|
|
|
|
|
|
|
|
|
|
|
670…725 |
|
|
Р = 1,0 Па; LAl = 310 мм и LTi = 310 мм |
|
|
|
|
|
|
|
|
|
|
|
||||||||||
|
|
|
|
|
|
0,5 |
|
|
1,9 |
7,6 |
9,24 |
|
6,96 |
|
|
|
7,26 |
|
1,59 |
2,15 |
|
0,15 |
0,17 |
||||||||||||
|
|
|
|
|
|
|
|
|
|
|
670…735 |
|
|
|
|
|
|
|
|
|
|
|
|
|
|
|
|||||||||
|
Р, Па |
0,6 |
|
|
2,2 |
10,2 |
11,75 |
|
6,59 |
|
|
|
10,15 |
2,13 |
2,88 |
|
0,16 |
0,18 |
|||||||||||||||||
|
|
|
|
|
|
|
|
|
|
|
|
|
|
|
|
|
|
|
|
|
|
|
|
|
|
|
|
|
|
|
|||||
0,8 |
|
670…775 |
|
3,5 |
6,8 |
8,10 |
|
4,15 |
|
|
|
5,77 |
|
1,36 |
1,84 |
|
0,14 |
0,15 |
|||||||||||||||||
|
|
|
|
|
|
|
|
|
|
|
|
|
|
||||||||||||||||||||||
|
|
|
|
|
|
|
|
|
|
|
670…790 |
|
|
|
|
|
|
|
|
|
|
|
|
|
|
|
|
||||||||
|
|
|
|
|
|
1,0 |
|
|
4,0 |
0,20 |
1,06 |
|
0,26 |
|
|
|
0,78 |
|
0,54 |
0,73 |
|
0,11 |
0,13 |
||||||||||||
|
|
|
|
|
|
|
|
|
|
640…760 |
|
|
|
|
|
|
|
|
|
|
|
|
|
|
|
|
|||||||||
|
|
|
|
|
|
45 |
|
|
|
4,0 |
7,2 |
8,69 |
|
5,23 |
|
|
|
6,15 |
|
1,45 |
1,96 |
|
0,14 |
0,15 |
|||||||||||
|
|
|
|
|
|
|
|
10 |
|
|
|
|
|
|
|
|
|
|
|
|
|
|
|
|
|
|
|
|
|
|
|
|
|
|
|
|
|
|
|
|
|
251 |
|
670…790 |
|
|
|
|
|
|
|
|
|
|
|
|
|
|
|
|
|||||||||||
|
|
|
|
К/мин |
|
|
|
4,0 |
0,08 |
0,03 |
|
0,05 |
|
|
|
0,43 |
|
0,10 |
0,14 |
|
0,09 |
0,10 |
|||||||||||||
|
Vнагр.подл |
, |
|
|
|
|
|
|
|
|
|
|
|
|
|
|
|
|
|
|
|
|
|
|
|
|
|
|
|
|
|
|
|||
20 |
|
|
|
|
|
|
|
|
|
|
|
|
|
|
|
|
|
|
|
|
|
|
|
|
|
|
|
||||||||
|
tи.о |
|
мин |
|
15 |
|
|
670…850 |
|
6,0 |
0,13 |
0,08 |
|
0,10 |
|
|
|
0,62 |
|
0,37 |
0,50 |
|
0,11 |
0,12 |
|||||||||||
|
|
|
40 |
|
|
|
|
|
|
|
|
|
|
|
|
|
|
|
|
|
|
|
|
|
|
|
|
|
|
|
|||||
|
|
|
|
|
|
|
|
|
770…890 |
|
|
|
|
|
|
|
|
|
|
|
|
|
|
|
|
||||||||||
|
|
|
|
|
|
10 |
|
|
|
4,0 |
0,10 |
0,05 |
|
0,07 |
|
|
|
0,57 |
|
0,23 |
0,31 |
|
0,10 |
0,11 |
|||||||||||
|
|
|
|
|
|
|
60 |
|
|
|
|
|
|
|
|
|
|
|
|
|
|
|
|
|
|
|
|
|
|
|
|
|
|
|
|
|
|
|
|
|
|
|
|
|
|
|
|
|
|
|
|
|
|
|
|
|
|
|
|
|
|
|
|
|
|
|
|
|
|
|
|

92
Окончание табл. 3 . 1 7
1 |
2 |
3 |
4 |
5 |
6 |
7 |
8 |
9 |
10 |
11 |
|
|
|
|
|
|
|
|
|
|
|
Комбинированный метод – МР+ЭДИ: общие ТехП: Uвыс = 600 В; N = 2,0 кВт; Uсм = 90 В; N2 = 50 %; Iд = 75 А; Р = 1,0 Па;
LAl = 270 мм (катод) и LTi = 100 мм (мишень)
|
|
|
|
|
702 |
|
605…685 |
2,6 |
4,9 |
5,58 |
2,83 |
5,34 |
0,92 |
1,24 |
0,13 |
0,15 |
|
|
|
|
К/мин |
|
600 |
|
|
|
|
|
|
|
|
|
|
|
|
Vнагр.подл |
|
|
602 |
|
615…700 |
|
|
|
|
|
|
|
|
|
|||
, |
|
2,9 |
3,8 |
1,34 |
1,97 |
0,81 |
0,87 |
1,18 |
0,12 |
0,14 |
|||||||
|
tи.о |
мин |
|
700 |
|
|
|
|
|
|
|
|
|
|
|||
|
|
|
|
|
|
|
|
|
|
|
|
||||||
|
|
|
|
203 |
|
690…815 |
4,2 |
3,1 |
1,45 |
0,87 |
1,06 |
0,32 |
0,43 |
0,09 |
0,10 |
||
|
|
|
|
|
|
||||||||||||
|
|
|
|
|
|
600 |
|
|
|
|
|
|
|
|
|
|
|
|
|
|
|
|
|
|
|
|
|
|
|
|
|
|
|
|
|
1TiN-Ti1–хAlхN – технологический процесс осаждения слоев пленки проводится при напряжении смещения Uсм = 280 В, остальные процессы при Uсм = 200 В.
2TiМР-Ti1–хAlхNМР+ЭДИ. 3TiЭДИ-•TiNМР-Ti1–хAlхNМР+ЭДИ•-Ti1–хAlхNМР+ЭДИ.
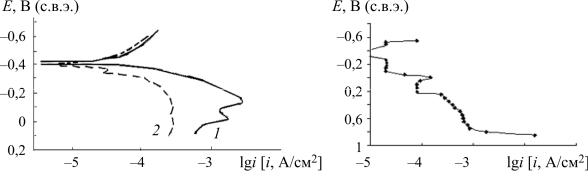
плотности тока 3 мА/см2, затем падает (см. рис. 3.27, а, кривая 1). Рост анодного тока в щелочных растворах связан с селективным растворением зерен WC. Кривая 2 (см. рис. 3.27) представляет поляризационную кривую образца ВК8 c осажденным Ti1–хAlхN слоем. Установлено, что сформированный Ti1–хAlхN слой не влияет на потенциал свободной коррозии Екор, который как и на образце без упрочнения близок к –0,4 В; а также не влияет на кинетику восстановления кислорода (катодные участки кривых 1 и 2 практически совпадают). Анодный ток достигает предельного значения при потенциале –60 мВ, выше которого начинается переход в пассивное состояние. Сравнение токов при одинаковом потенциале –0,2 В кривых 1 и 2 на рис. 3.27, а показывает, что Ti1–хAlхN слой существенно тормозит процесс анодного растворения. Скорость растворения при потенциале –0,2 В уменьшается примерно в 18 раз.
На рис. 3.27, б представлена поляризационная кривая неупрочненных образцов. Анодная кривая характеризуется тремя участками пассивного состояния.
а |
б |
Рис. 3.27. Поляризационные кривые образца из ВК8: 1 – без Ti1–хAlхN слоя;
2 – с Ti1–хAlхN слоем (а) и из Р6М5 (б)
Первый участок кривой с –300 до –70 мВ имеет самую малую плотность тока в пассивном состоянии 15 мкА·см–2. Второй участок пассивности наступает при потенциалах выше 0 В и простирается до 0,4 В. Ток в пассивном состоянии составляет 79 мкА·см–2, т.е. в 5,3 раза выше, чем на первом участке пассивности. Третий участок торможения растворения на-
чинается с потенциала 0,4 В и простирается до 0,75 В. На этом участке ток медленно растет с 22 до 83 мА·см–2.
Полученные результаты позволили заключить, что наличие пассивности с низкими токами растворения делает проблематичным определение тормозящего влияния Ti1–хAlхN слоя на скорость растворения, так как если
93
бы она препятствовала растворению, то токи получались бы меньше и выходили за рамки чувствительности милливольтметра.
Установлено, что Ti1–хAlхN слой с максимальным содержанием h-Ti3Al2N2 и Al уменьшает скорости растворения при коррозии сплава ВК8 в 18 раз, а стали Р6М5 – в 13 раз.
3.4. УПРАВЛЕНИЕ ФИЗИКО-МЕХАНИЧЕСКИМИ, ТРИБОЛОГИЧЕСКИМИ, КОРРОЗИОННЫМИ И АДГЕЗИОННЫМИ СВОЙСТВАМИ МНОГОСЛОЙНЫХ ПЛЕНОК НА ОСНОВЕ ДВУХКОМПОНЕНТНЫХ TIN (ZrN)
И ТРЕХКОМПОНЕНТНЫХ TIХZr1–ХN И TI1–ХAlХN СЛОЕВ С ГРАДИЕНТОМ СТРУКТУРЫ, ФАЗОВОГО И ЭЛЕМЕНТНОГО СОСТАВА
С ИСПОЛЬЗОВАНИЕМ РАЗЛИЧНЫХ ИСТОЧНИКОВ ПЛАЗМЫ
На основании комплексных механических, трибологических и коррозионных испытаний TiхZr1–хN и Ti1–хAlхN слоев были установлены способы управления ФМС, ИАС и коррозионными свойствами разработанных МП.
Оптимальным комплексом ФМС, ИАС, минимальной хрупкостью, высокой трещиностойкостью и адгезионной прочностью обладают многослойные многокомпонентные пленки на основе двух- и трехкомпонентных слоев:
1. Многослойная Ti,Zr-ИБ-•TiхZr1–хN-Ti,Zr-ИБ•-TiхZr1–хN пленка на основе наноструктурированных слоев с максимальными объемными доля-
ми с-TiZrN2 (24,4 %) и Zr3N4 (66,9 %) фаз, максимальным содержанием Zr (35,02 ат. %), минимальной дефектностью поверхности, максимальной инертностью к обрабатываемому материалу и высокими ФМС: Н = 36 ГПа;
Е = 213 ГПa; We = 78 %; H/E = 0,18; H3/E2 = 1,1 ГПa, трибологическими: Iпm = 0,86·10–5 мг·Н–1·м–1, IпV = 0,08·10–4 мм3·Н–1·м–1, IкV = 0,12·10–8 мм3·Н–1·м–1, f = 0,07 и адгезионными свойствами: HF-1, Sотп = 0,44·105 мкм2, коэффициентом трещиностойкости Ктр = 0,03, коэффициентом отслоения Ко = 0,08, хрупкостью Sотп = 28,11 мкм2 и динамической микротвердостью Н115 = 0,9 ГПа получена при проведении ИБ промежуточных металлических Ti,Zr слоев перед осаждением TiхZr1–хN слоев МП.
2. Многослойная TiЭДИ-•TiNМР-TiхZr1–хNМР+ЭДИ•-TiхZr1–хNМР+ЭДИ плен-
ка с объемными долями с-TiZrN2 (71,5 %) и Zr3N4 (13,4 %) фаз, содержанием Zr (36,11 ат. %), с градиентом структуры и состава слоев, минимальной дефектностью поверхности, максимальной инертностью к обрабатываемому материалу и высокими ФМС: Н = 37 ГПа; Е = 411 ГПa; We = 69 %; H/E = 0,15; H3/E2 = 0,8 ГПa, заданными трибологическими: Iпm = 0,97·10–5 мг·Н–1·м–1,
IпV = 0,35·10–4 мм3·Н–1·м–1, IкV = 0,85·10–8 мм3·Н–1·м–1, f = 0,08 и адгезионны-
94
ми свойствами: HF-1, Sотп = 0,68·105 мкм2, Ктр = 0,16, Ко = 0,12, хрупкостью
Sотп = 24,24 мкм2 и Н115 = 0,9 ГПа получена за счет увеличения степени ионизации плазменного потока при одновременном использовании электро-
дугового испарителя и магнетронного распылителя.
3. Многослойная TiМР-•TiNМР-ZrNЭДИ•-TiхZr1–хNМР+ЭДИ пленка с поликристаллическими и наноструктурированными слоями с объемными доля-
ми с-TiZrN2 (19,2 %) и Zr3N4 (74,8 %) фаз, содержанием Zr (32,11 ат. %),
с градиентом структуры и состава слоев, минимальной дефектностью поверхности, максимальной инертностью к обрабатываемому материалу и высокими ФМС: Н = 36 ГПа; Е = 312 ГПa; We = 70 %; H/E = 0,12;
H3/E2 = 0,82 ГПa, заданными трибологическими: Iпm = 1,07·10–5 мг·Н–1·м–1,
IпV = 0,27·10–4 мм3·Н–1·м–1, IкV = 0,72·10–8 мм3·Н–1·м–1, f = 0,08 и адгезионны-
ми свойствами: HF-1, Sотп = 0,14·105 мкм2, Ктр = 0,15, Ко = 0,10, хрупкостью
Sотп = 19,50 мкм2 и Н115 = 1,1 ГПа получена за счет увеличения степени ионизации плазменного потока при попеременном и одновременном исполь-
зовании электродугового испарителя и магнетронного распылителя.
4. Многослойная Ti-TiN-•Zr-ZrN•-Zr-•TiхZr1–хN-Zr•-TiхZr1–хN пленка с поликристаллическими и наноструктурированными слоями с объемными долями с-TiZrN2 (31,6 %), Zr2N (47,9 %) и Zr3N4 (20,5 %) фаз, содержанием
Zr (35,02 ат. %), с Zr слоями с высокой энергоемкостью, теплопроводностью, сопротивлением истиранию и TiхZr1–хN слоями с высокой термической устойчивостью к твердофазным и жидкофазным диффузионным реакциям и окислению при повышенных температурах, минимальной дефектностью поверхности и заданными ФМС: Н = 45 ГПа; Е = 436 ГПa; We = 63 %;
H/E = 0,10; H3/E2 = 0,75 ГПa, трибологическими: Iпm = 1,16·10–5 мг·Н–1·м–1, IпV = 0,54·10–4 мм3·Н–1·м–1, IкV = 1,07·10–8 мм3·Н–1·м–1, f = 0,1 и адгезионны-
ми свойствами: HF-1, Sотп = 0,68·105 мкм2, Ктр = 0,10, Ко = 0,07, хрупкостью
Sотп = 40,48 мкм2 и Н115 = 0,7 ГПа получена за счет разделения функций между Zr слоями с максимальной теплопроводностью и ZrN, TiN, TiхZr1–хN
слоями с высокой термической устойчивостью.
5. Многослойная TiЭДИ-•TiNМР-Ti1–хAlхNМР+ЭДИ•-Ti1–хAlхNМР+ЭДИ плен-
ка поликристаллическими и наноструктурированными слоями с объемной долей h-Ti3Al2N2 (100 %) фазы, содержанием Al (28,7 ат. %), заданным элементным составом и ФМС: Н = 36 ГПа; Е = 356 ГПa; We = 76 %;
H/E = 0,1; H3/E2 = 1,31 ГПa, износостойкими: |
Iпm |
= 1,45·10–5 мг·Н–1·м–1, |
IпV = 0,05·10–4 мм3·Н–1·м–1 и антифрикционными: |
IкV |
= 0,43·10–8 мм3·Н–1·м–1, |
f = 0,09 и высокой адгезионной прочностью: Sотп = 0,56·105 мкм2 и HF-1,
Sотп = 0,09·105 мкм2, Ктр = 0,15, Ко = 0,10, хрупкостью Sотп = 30,48 мкм2
95
иН115 = 0,9 ГПа получена за счет увеличения степени ионизации плазменного потока при одновременном использовании электродугового испари-
теля и магнетронного распылителя в процессе осаждения Ti1–хAlхN слоев многослойной пленки и образования во время резки оксидного слоя Al2O3, увеличивающего термостойкость МП и сохраняющего ее свойства.
6.Многослойная TiNп.с-•TiNн.с-Ti1–хAlхNн.с•-Ti1–хAlхNн.с пленка с заданным фазовым составом: в TiNп.с слое – TiN (97,5…99,6 %), TiN0,3 (0,4…2,0 %)
иTi2N (0…1,5 %), в TiNн.с слое – TiN (99,2 %), TiN0,3 (0,8 %) и в Ti1–хAlхNн.с
слое – h-Ti3Al2N2 (100 %). TiNн.с слой многослойной пленки с ФМС –
Н = 36 ГПа; Е = 387 ГПa; We = 64 %; H/E = 0,09; H3/E2 = 0,31 ГПa, Sотп =
= |
0,94·105 мкм2, износостойкими: Iпm |
= 3,54·10–5 мг·Н–1·м–1, |
IпV |
= |
||
= |
0,08·10–4 мм3·Н–1·м–1 |
и |
антифрикционными свойствами: |
IкV |
= |
|
= |
0,18·10–8 мм3·Н–1·м–1, |
f = |
0,08. TiNп.с |
подслой многослойной пленки |
с ФМС– Н = 36 ГПа; Е = 387 ГПa; We = 64 %; H/E = 0,09; H3/E2 = 0,31 ГПa, Sотп = 0,94·105 мкм2, износостойкими: Iпm = 4,16…8,63·10–5 мг·Н–1·м–1, IпV
= 1,05…1,90·10–4 мм3·Н–1·м–1 и антифрикционными свойствами: IкV =
= 0,25…2,97·10–8 мм3·Н–1·м–1, f = 0,08…0,16. Ti1–хAlхNн.с слой МП с высокими ФМС: Н = 36 ГПа; Е = 358 ГПa; We = 76 %; H/E = 0,10; H3/E2 = 1,31 ГПa,
высокой адгезионной прочностью: Sотп = 0,09·105 мкм2 и HF-1, износостойкими: Iпm = 0,03·10–5 мг·Н–1·м–1, IпV = 0,05·10–4 мм3·Н–1·м–1 и антифрикцион-
ными свойствами: IкV = 0,43·10–8 мм3·Н–1·м–1, f = 0,09. По разработанному
способу может быть получена многослойная многокомпонентная
TiNп.с-•TiNн.с-TiхZr1–хNн.с•-TiхZr1–хNн.с пленка..
3.5. ЭКСПЛУАТАЦИОННЫЕ СВОЙСТВА МНОГОСЛОЙНЫХ ПЛЕНОК НА ОСНОВЕ ДВУХКОМПОНЕНТНЫХ TIN (ZrN) И ТРЕХКОМПОНЕНТНЫХ
TIХZr1–ХN И TI1–ХAlХN СЛОЕВ С ГРАДИЕНТОМ СТРУКТУРЫ, ФАЗОВОГО И ЭЛЕМЕНТНОГО СОСТАВА ПРИ ОБРАБОТКЕ СИЛЬВИНИТОВОЙ РУДЫ,
АУСТЕНИТНЫХ, ЗАКАЛЕННЫХ ВЫСОКОЛЕГИРОВАННЫХ, УГЛЕРОДИСТЫХ,
КОРРОЗИОННО-СТОЙКИХ И ЖАРОПРОЧНЫХ СТАЛЕЙ
Стойкость многослойных пленок на основе двухкомпонентных
TiN (ZrN) и трехкомпонентных TiхZr1–хN, Ti1–хAlхN и Ti-B-Si-N слоев при обработке сильвинитовой руды и аустенитных сталей. Термиче-
ская стабильность МП на основе двухкомпонентных TiN (ZrN) и трехкомпонентных TiхZr1–хN, Ti1–хAlхN и Ti-B-Si-N слоев, сформированных ЭДИ,
96
МР ЭДИ+МР, была установлена в результате лабораторных стойкостных испытаний упрочненных сверл при обработке аустенитной стали. Результаты лабораторных испытаний приведены в табл. 3.18.
При изучении внутренней поверхности отверстия, полученного неупрочненным и упрочненным сверлами, установлено, что при обработке сверлом с МП на основе Ti1–хAlхN слоев отверстие ровное, чистое, без видимых следов смятия (рис. 3.28, а), а отверстие, полученное при сверлении неупрочненным сверлом, имеет грубую шероховатость и следы смятия материала на выходе, что говорит о затуплении главных режущих кромок сверла (рис. 3.28, б).
В процессе резания сверлом из Р6М5 произошло выкрашивание ленточки и нагрев сверла (рис. 3.29, а). После сверления 13 отверстий наблюдается смятие материала на выходе, режущие кромки затупляются. На 17-м отверстии резко возрастает величина осевого усилия на инструмент, что свидетельствует о затуплении перемычки сверла. Характер процесса резания неравномерный, присутствуют рывки и скрип. Стружка сливная, неравномерная по толщине и ширине. Первые 7 отверстий имеют низкую шероховатость, после чего наблюдается постепенное понижение качества поверхности. Резкое ухудшение чистоты поверхности происходит на 17-м отверстии, что говорит о затуплении режущей кромки ленточки.
Наблюдается незначительный износ задней (ЗП) и передней (ПП) поверхности режущей кромки поверхности сверла, упрочненного МП на основе Ti1–хAlхN слоев (рис. 3.29, б). Присутствует заметный износ угла, образованного ПП режущей кромки и ленточкой сверла. МП разрушена на перемычке и ленточке. Целостность МП на ЗП и ПП практически не изменяется. Характер процесса резания – непрерывный с незначительными рывками. Стружка непрерывная сливная с постоянным сечением и размером. Смятие материала на выходе практически отсутствует, чистота обработки получаемой поверхности ухудшается с 16-го отверстия.
При резании сверлом с TiN поверхностным слоем наблюдается незначительный износ ЗП и ПП режущей кромки (рис. 3.29, в). Присутствует заметный износ угла, образованного ПП и ленточкой сверла. Присутствует выкрашивание первой ленточки. Вторая ленточка, включая вспомогательную поверхность, сколота. TiN слой МП разрушен, как на перемычке, так и на ленточке, на ЗП и ПП – изношен до быстрорежущей матрицы. Характер процесса резания – непрерывный с незначительными рывками. Стружка прерывистая сливная с непостоянным сечением и размером. Смятие материала на выходе присутствует с 7-го отверстия, чистота обработки получаемой поверхности ухудшается с 7-го отверстия.
97

98
Таблица 3 . 1 8
Продолжительность обработки аустенитной стали сверлами с МП на основе TiN, ZrN, TiхZr1–хN и Ti1–хAlхN слоев, полученных ЭДИ и МР
Номер |
Материал слоя |
|
|
|
|
|
|
|
|
Номеротверстия |
|
|
|
|
|
|
|
|
Тобщ, |
|||
сверла |
пленки |
1 |
2 |
3 |
4 |
5 |
6 |
7 |
8 |
9 |
10 |
11 |
12 |
13 |
14 |
15 |
16 |
17 |
18 |
19 |
20 |
с |
|
|
|
|
|
|
|
|
|
|
|
|
|
|
|
|
|
|
|
|
|
|
|
1 |
– |
62 |
67 |
63 |
71 |
63 |
64 |
72 |
84 |
98 |
106 |
112 |
108 |
115 |
87 |
78 |
104 |
85 |
87 |
100 |
113 |
1739 |
|
|
|
|
|
|
|
|
|
|
|
|
|
|
|
|
|
|
|
|
|
|
|
2 |
TiN МР |
68 |
118 |
80 |
98 |
102 |
88 |
105 |
78 |
470 |
74 |
88 |
82 |
75 |
72 |
75 |
56 |
70 |
88 |
58 |
63 |
2008 |
|
|
|
|
|
|
|
|
|
|
|
|
|
|
|
|
|
|
|
|
|
|
|
3 |
ZrN МР |
72 |
126 |
85 |
103 |
107 |
92 |
111 |
91 |
77 |
76 |
96 |
98 |
80 |
89 |
84 |
62 |
83 |
95 |
75 |
88 |
1790 |
|
|
|
|
|
|
|
|
|
|
|
|
|
|
|
|
|
|
|
|
|
|
|
4 |
AlN МР |
78 |
134 |
93 |
117 |
124 |
101 |
139 |
106 |
97 |
93 |
106 |
105 |
94 |
90 |
101 |
82 |
104 |
104 |
92 |
92 |
|
|
|
|
|
|
|
|
|
|
|
|
|
|
|
|
|
|
|
|
|
|
|
|
5 |
TiхZr1–хN МР |
73 |
117 |
89 |
97 |
98 |
94 |
118 |
74 |
78 |
64 |
78 |
100 |
77 |
73 |
74 |
88 |
115 |
96 |
57 |
74 |
1734 |
6 |
Ti1–хAlхN МР |
62 |
114 |
81 |
94 |
85 |
85 |
100 |
65 |
64 |
56 |
70 |
88 |
60 |
71 |
66 |
54 |
72 |
82 |
47 |
56 |
1472 |
7 |
TiN ЭДИ |
65 |
118 |
80 |
98 |
102 |
88 |
105 |
78 |
470 |
74 |
88 |
82 |
75 |
72 |
75 |
56 |
70 |
88 |
58 |
63 |
2005 |
|
|
|
|
|
|
|
|
|
|
|
|
|
|
|
|
|
|
|
|
|
|
|
8 |
ZrN ЭДИ |
68 |
126 |
85 |
103 |
107 |
92 |
111 |
91 |
77 |
76 |
96 |
98 |
80 |
89 |
84 |
62 |
83 |
95 |
75 |
88 |
1786 |
|
|
|
|
|
|
|
|
|
|
|
|
|
|
|
|
|
|
|
|
|
|
|
9 |
TiхZr1–хN ЭДИ |
39 |
41 |
60 |
54 |
55 |
62 |
45 |
51 |
67 |
42 |
66 |
48 |
50 |
69 |
74 |
42 |
43 |
44 |
46 |
53 |
1051 |
10 |
Ti1–хAlхN ЭДИ |
46 |
37 |
33 |
57 |
71 |
61 |
59 |
66 |
87 |
63 |
96 |
65 |
74 |
60 |
81 |
62 |
34 |
90 |
72 |
62 |
1276 |
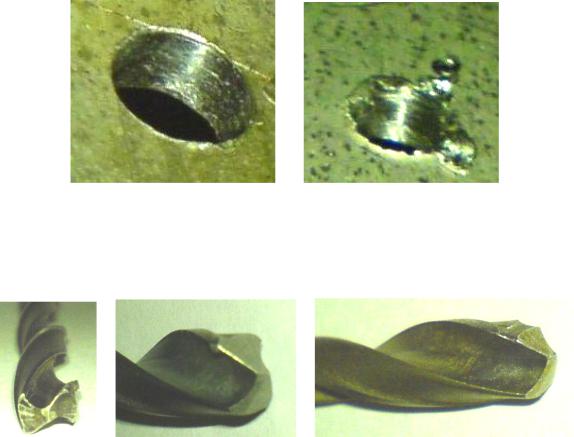
а |
б |
Рис. 3.28. Внешний вид внутренней поверхности отверстия, полученного: а) сверлом с МП на основе Ti1–хAlхN слоев; б) неупрочненным сверлом
а |
б |
в |
Рис. 3.29. Внешний вид сверла из Р6М5 после завершения процесса резания без поверхностного слоя (а) и с поверхностным слоем Ti1–хAlхN (б), TiN (в)
Максимальной термической устойчивостью и коррозионной стойкостью при обработке сильвинитовой руды в условиях сухого трения и воздействия агрессивной среды является МП на основе Ti1–хAlхN слоя, максимально снижающей температуру в зоне резания. При обработке сверлом с МП на основе Ti1–хAlхN ЭДИ слоев возрастает стойкость сверл за счет образования высокоадгезионной плотной оксидной пленки Al2O3, предотвращающей усталостные деформации режущей кромки сверла и сохраняющей более длительное время неизменной микротвердость поверхности Ti1–хAlхN слоя и сверла. TiхZr1–хN слой МП, сформированный ЭДИ, незначительно уступает Ti1–хAlхN слою по термической устойчивости и стойкости.
Стойкость многослойных пленок на основе двухкомпонентных
TiN (ZrN) и трехкомпонентных TiхZr1–хN, Ti1–хAlхN и Ti-B-Si-N слоев при обработке закаленных высоколегированных, углеродистых, корро- зионно-стойких и жаропрочных сталей. Стойкостные испытания сверл с МП на основе ZrN слоев, осажденных при оптимальном сочетании ТехП,
99
проводили на ремонтном предприятии при экстремальных режимах обработки нержавеющей стали 12Х18Н10Т. Результаты испытаний приведены в табл. 3.19.
Таблица 3 . 1 9
Стойкостные испытания сверл с МП на основе ZrN слоев
инструментаТип |
ммДиаметр, |
Материал инструмента |
V |
V |
Обрабатываемый материал |
обрабатыТолщинаммдеталиваемой, |
пленкислояМатериал |
обработкиВремя,мин |
чистотыКласс поверхности |
отверстийКоличество |
обработкиСкорость, минотв/ |
состояние |
|
|
|
об,мин/ |
об/мин |
|
|
|
|
|
|
|
|
|
|
|
шпинделя |
подачи |
|
|
|
|
|
|
|
Стружка/ |
|
|
|
|
|
|
|
|
|
|
обработанной |
||
|
|
|
|
, |
|
|
|
|
|
|
|
|
|
|
|
|
|
|
|
|
|
|
|
|
поверхности |
|
|
|
|
|
|
|
|
|
|
|
|
|
|
|
|
|
|
12Х18Н10Т |
|
Нет |
|
|
|
|
Элементная, |
|
8 |
Р6М5 |
500 |
100* |
20 |
10 |
4 |
max 60 |
6 |
|||
|
|
|
|
|
|
|
|
|
|
|
|
рваныекрая/ |
Сверло |
|
|
|
|
|
|
|
|
|
|
|
поверхность |
|
|
|
|
|
|
|
|
|
|
|
цами, налипание |
|
|
|
|
|
|
|
|
|
|
|
|
|
деталисзаусен- |
|
|
|
|
|
|
|
|
|
|
|
|
стружки |
|
|
|
|
|
|
|
Zr-ZrN |
30 |
6 |
300 |
10 |
Сливная/чистая |
*Вертикально-фрезерный станок модели 6Р13.
Установлена взаимосвязь: условия работы инструмента – состав пленки – метод осаждения – технологические параметры – обрабатываемый материал. Стойкость сверл увеличена в 5 раз, скорость обработки – в 1,7 раза. Улучшено качество обработанной поверхности.
Опорные детали топливорегулирующей аппаратуры упрочняют с целью повышения их долговечности и работоспособности (рис. 3.30).
Для повышения работоспособности мелкоразмерного инструмента (Ø 1,5…2,0 мм) подбирают режим нагрева перед упрочнением. Мелкоразмерный инструмент более чувствителен к высоким температурам и быстро охлаждается при удалении от источника нагрева. Такие сверла устанавливают в бронзовые оснастки и обеспечивают минимальный зазор между ними и оснасткой, незащищенными остаются только 8…10 мм режущей части сверла. Эффективность данного приспособления при упрочнении мелкоразмерных сверл высока.
На рис. 3.31 представлены зависимости температуры сверла от времени. Режим нагрева подбирают соответственно диаметру сверла. Тепловой режим контролируют прибором следящего действия КВП 1.
100