
книги / Изучение функциональных свойств многослойных пленок на основе двух- и трехкомпонентных нитридов тугоплавких металлов и их соединений с легкоплавкими металлами и неметаллами
..pdfства из трубчатых ТЭНов; снижения количества и размеров микрокапельной фазы (МКФ) – за счет совершенствования электродуговых испарителей и применения многокатодных устройств.
Получение пленок с заданной стехиометрией, структурой и свойствами при высокой однородности их по толщине и площади затруднено невозможностью раздельного регулирования энергии и потока ионов, бомбардирующих катод/мишень, отсутствием возможности управления потоком ионов, падающих на подложку, миграцией атомов и ионов по подложке, которые не позволяют управлять взаимосвязью между процессами распыления и осаждения пленок, а также различием значений коэффициентов распыления (Кр) материалов катодов/мишеней, параметров их кристаллической решетки (КР), температурой, фазовым и химическим составом материала катодов/мишеней и способа их изготовления и охлаждения.
Несмотря на многолетний опыт оптимизации и применения ионноплазменных технологий, снижение нестабильности эксплуатационных свойств ТИ и ПТ остается актуальной проблемой, в частности, в понимании общих закономерностей, управляющих формированием реальной структуры пленок.
Проблема улучшения износо- и трещиностойких свойств многочисленных многослойных пленок (МП) В.П. Табаковым решается варьированием элементного состава слоев за счет изменения количества и элементного состава катодов, содержания реакционного газа в газовой смеси с аргоном (Ar), управления температурой пленки путем изменения опорного напряжения. С.Н. Григорьев для изменения элементного состава слоев использует расходуемый материал из сплава элементов IV–VI групп Периодической системы, по меньшей мере, с одним элементом с более высоким коэффициентом ионного распыления и ступенчато с шагом, обеспечивающим заданную разницу между концентрацией Cr и/или Al в расходуемом материале и концентрацией упомянутых элементов в МП или ее отдельных слоях, изменяет отрицательный потенциал на подложке. А.С. Верещака для повышения износостойкости, термостабильности и коррозионной стойкости, уменьшения адгезии с обрабатываемым материалом для получения МП в интервале температур 430…550 К чередует двух- и многокомпонентные слои. N. Wangyang и M. Ronald Ti1–хAlxN пленки формируют в диапазоне 673…873 К для получения х = 0,53…0,58 молей и от 0 до 15 мас. % гексагональной фазы с текстурой (200) и (111). Учеными L. Ipaz, J.C. Caicedo, J. Esteve предложены МП с высокими механическими и трибологическими свойствами: критическая нагрузка 45 Н, коэффициент трения (f) 0,28, а также получены МП с различными механизмами формиро-
11
вания за счет уменьшения толщины слоев до 25 нм и увеличения их количества до 100.
Приоритетной задачей является выбор составов пленок и разработка конструкций МП с комплексом функциональных свойств; актуальной задачей – управление наиболее значимыми процессами, участвующими в формировании пленок, прогнозирование их структуры по технологическим (ТехП) и температурным (ТемП) параметрам осаждения; научно-прикладной задачей – изучение фазовых и структурных изменений в пленках под влиянием условий их формирования для сообщения им комплекса высоких функциональных свойств и установление взаимной зависимости ФМС и трибологических свойств пленок. Решение указанных задач может позволить получать МП с комплексом высоких функциональных свойств.
В последние годы технология получения наноструктурированных и поликристаллических пленок, в том числе многослойных, привлекает внимание многих исследователей. Практически отсутствует корреляционная связь между результатами исследований фазового и элементного состава, параметров структуры и эксплуатационными свойствами упрочненного ТИ и ПТ.
Вопрос о том, какими должны быть структурные и фазовые характеристики пленок с комплексом высоких ФМС, износостойких и антифрикционных свойств (ИАС), пока остается открытым, требует дополнительного изучения и представляет как научный, так и практический интерес.
Для разработки и получения многослойных поликристаллических пленок на основе наноструктурированных и поликристаллических слоев нитридов элементов III и IV групп Периодической системы с комплексом высоких ФМС, ИАС, адгезионных, коррозионных, трещино- и теплостойких свойств широкой области применения необходимо изучить зависимость указанных свойств пленок от их строения, внутренних напряжений, фазового и элементного состава.
12
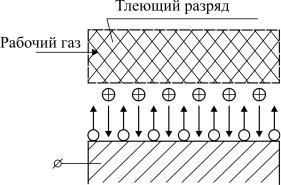
1. МЕТОДЫ И ОБОРУДОВАНИЕ ДЛЯ ФОРМИРОВАНИЯ МНОГОСЛОЙНЫХ ПЛЕНОК НА ОСНОВЕ ДВУХ- И ТРЕХКОМПОНЕНТНЫХ СЛОЕВ
1.1. МАГНЕТРОННОЕ РАСПЫЛЕНИЕ
Магнетронное распыление относится к ионно-плазменным методам,
вкоторых используется тлеющий разряд (рис. 1.1). При использовании
вкачестве рабочего газа смеси из Аr и химически активного газа (О2, N2 и т.п.) реализуется реактивный метод осаждения оксидов, нитридов и т.п.
Рис. 1.1. Использование тлеющего разряда при ионно-плазменном осаждении пленок
Различают магнетронное распыление на постоянном токе, высокочастотное магнетронное распыление, магнетронное распыление с ЭЦР, реактивное магнетронное распыление [1] и импульсное магнетронное распыление.
Метод импульсного магнетронного распыления основан на действии магнетронных распылительных систем. Магнетронные распылительные системы получили свое название от СВЧ приборов М-типа (магнетронных устройств), хотя кроме наличия скрещенных электрического и магнитного полей ничего общего с ними не имеют. Магнетронные системы относятся к системам распыления диодного типа, в которых распыление материала происходит за счет бомбардировки поверхности мишени ионами рабочего газа, образующимся в газе аномально тлеющего разряда. Высокая скорость распыления, характерная для этих систем, достигается увеличением плотности ионного тока за счет локализации плазмы у распыляемой поверхности мишени с помощью сильного поперечного магнитного поля [2, 3].
13
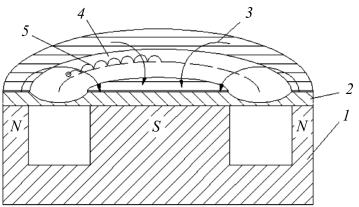
Принцип действия магнетронной распылительной системы показан на рис. 1.2. Основными элементами устройства являются катод-мишень, анод и магнитная система. Силовые линии магнитного поля замыкаются между полюсами магнитной системы. Поверхность мишени, расположенная между местами входа и выхода силовых линий магнитного поля, интенсивно распыляется и имеет вид замкнутой дорожки, геометрия которой определяется формой полюсов магнитной системы.
Рис. 1.2. Схема магнетронной распылительной системы с плоской мишенью: 1 – магнитная система; 2 – катод-мишень; 3 – силоваялиниямагнитногополя; 4 – зонанаибольшейэрозии поверхностикатода; 5 – траектория движения электрона
При подаче постоянного напряжения между мишенью (отрицательный потенциал) и анодом (положительный или отрицательный потенциал) возникает неоднородное электрическое поле и возбуждает аномальный тлеющий разряд. Наличие замкнутого магнитного поля у распыляемой поверхности мишени позволяет локализовать плазму разряда непосредственно у мишени. Эмитированные с катода под действием ионной бомбардировки электроны захватываются магнитным полем, им сообщается сложное циклоидальное движение по замкнутым траекториям у поверхности мишени. Электроны оказываются как бы в ловушке, создаваемой с одной стороны магнитным полем, возвращающим электроны на катод, а с другой стороны – поверхностью мишени, отталкивающей электроны. Электроны циклируют в этой ловушке до тех пор, пока не произойдет несколько ионизирующих столкновений с атомами рабочего газа, в результате которых электрон потеряет полученную от электрического поля энергию. Таким образом, большая часть энергии электрона, прежде чем он попадет на анод, используется на ионизацию и возбуждение, что значительно увеличивает эффективность процесса ионизации и приводит к возрастанию концентрации положительных ионов у поверхности катода. Это в свою оче-
14
редь обусловливает увеличение интенсивности ионной бомбардировки поверхности мишени и значительный рост скорости распыления, а следовательно, и скорости осаждения пленки.
1.2. ЭЛЕКТРОДУГОВОЕ ИСПАРЕНИЕ
Осаждение пленок дуговым разрядом в вакууме происходит за счет эрозии вещества в сильноточных дуговых разрядах (с холодным и горячим катодом), образования ионизированной паровой фазы (20–100 % ионов), переноса ее с большой скоростью (энергия частиц Е до 10 эВ) и конденсации на поверхности подложки.
Кдостоинствам метода осаждения тонких пленок дуговым разрядом
ввакууме относятся: практически неограниченная электрическая мощ-
ность; высокий коэффициент ионизации испаряемых частиц Ки; возможность получения пленок сплавов, окислов, нитритов, карбидов и т.п., причем как путем использования мишеней из этих материалов, так и реактивным методом; отсутствие необходимости в дополнительном газе для
ионизации; скорость осаждения V0 – максимально возможная (ограничивается допустимым потоком энергии на поверхность конденсации). Недостатками являются наличие в потоке осаждаемого вещества капельной фазы, нерегулируемая энергия частиц Е и относительная сложность конструкции дуговых источников.
1.3. ОБОРУДОВАНИЕДЛЯФОРМИРОВАНИЯМНОГОСЛОЙНЫХ ПЛЕНОК
НАОСНОВЕДВУХ- ИТРЕХКОМПОНЕНТНЫХ СЛОЕВ
Методы формирования многослойных пленок на основе двухкомпонентных (TiN, ZrN) и трехкомпонентных (Ti1–xAlxN, TiхZr1–xN) слоев – электродуговое испарение (ЭДИ), магнетронное распыление (МР): высокочастотное МР и МР на постоянном токе.
Оборудование для формирования МП – модернизированная и автоматизированная установка УРМЗ 3.279.048 и промышленная установка ННВ-6,6-И1 (табл. 1.1).
Способы охлаждения катода/мишени:
– без принудительного охлаждения (температура воды, охлаждающей
(Тохл.вод) катод/мишень на входе ≈299…300 К, на выходе ≈301…302 К);
– с принудительным охлаждением (Тохл.вод на входе ≈291…292 К, на выходе ≈293…294 К).
15

16
Таблица 1 . 1
Технические характеристики вакуумных установок электродугового испарения и магнетронного распыления
|
|
Вакуумная установка |
|
||
Техническая |
|
Двухкамерная установка |
Установка |
Установка УРМЗ 3.279.048 |
|
|
электродугового |
||||
характеристика |
ННВ-6,6-И1 |
магнетронного |
периодического |
||
и магнетронного |
|||||
|
|
распыления [4–9] |
действия [10] |
||
|
|
распыления [11–16] |
|||
|
|
|
|
||
|
|
|
|
|
|
1 |
2 |
3 |
4 |
5 |
|
Техническоесостояние |
Без модернизации |
Модернизирована |
Модернизирована |
Автоматизирована |
|
Основамодернизации |
– |
Установка производства |
Вакуумный универсаль- |
Модернизованная установка |
|
|
|
ОАО ЦНИТИ «Техномаш» |
ный пост производства |
УРМЗ3.279.048 производства |
|
|
|
|
МГТУ им. Н.Э. Баумана |
ГОУ ВПО ПГТУ |
|
|
|
|
|
|
|
Управление |
Ручное |
Ручное |
Ручное |
Автоматическое |
|
Потребляемая мощность, кВт |
50 |
1,5 |
20 |
55 |
|
Диаметр и высота вакуумной |
600; 600 |
600; 100 |
300; 300 |
500; 400; 600 |
|
камеры, мм |
|
|
|
(ширина, длина, высота) |
|
|
|
|
|
|
|
Откачные средства |
Н-250 |
Н-250 |
АВП250-630 УХЛ 4,2 |
Н-400 |
|
Предельный вакуум, Па |
0,93·10–3 |
1,33·10–4 |
10–3 |
0,60·10–3 |
|
Технологические особенно- |
Электродуговой |
Высокочастотная МРС |
МРС на постоянном |
Магнетрон на постоянном токе |
|
сти источника плазмы |
испаритель |
|
токе |
иэлектродуговой испаритель |
|
|
|
|
|
|
|
Тип/количество источников |
Электродуговой |
Цельнометаллический |
Планарный |
Дуговой испаритель / 1 |
|
|
испаритель / 3 |
планарный ненакаливае- |
магнетрон/ 1 |
|
|
|
|
мый магнетрон / 2 |
|
|
|
|
|
|
|
|
|
Диаметр/толщина мишени, |
– |
90/3 |
125/3…6 |
– |
|
мм |
|
|
|
|
|
|
|
|
|
|
|
Диаметр основания и высота |
79/48 |
– |
– |
55/44 |
|
катода, мм |
|
|
|
|
|
|
|
|
|
|

Продолжение табл. 1 . 1
1 |
2 |
|
|
|
3 |
|
|
4 |
|
|
|
5 |
|
|
|
|
|
|||||||||||
Материал пленки TiN, |
|
|
|
TiN |
; |
ZrN |
; |
|
Ti-B-Si-N |
|
|
|
Ti-B-Si-N |
|
|
|
|
|
TiN |
; ZrN |
; |
|||||||
|
|
|
|
|
|
|
|
|
|
|
|
|
|
|
|
|
|
|
|
|
||||||||
материал мишени/катода– |
|
|
|
|
|
|
экзотермическая |
экзотермическая |
|
|
|
|
|
|
||||||||||||||
|
|
ВТ-1-00 |
|
Э110 |
|
|
|
|
ВТ-1-00 |
|
Э110 |
|
|
|||||||||||||||
ВТ-1-00 |
|
|
|
Ti-Zr-N |
; |
смесь состава |
|
смесь состава |
|
|
|
|
|
Ti-Zr-N |
; |
|||||||||||||
|
|
|
|
|
|
76,0 % Ti |
|
|
55,2 % Ti |
|
|
|
|
|
|
|
||||||||||||
|
|
ВТ-1-00 и Э110 |
|
|
ВТ-1-00 и Э110 |
|||||||||||||||||||||||
|
|
|
|
Ti-Al-N |
|
|
+4,0 % B |
|
|
+24,8 % B |
|
|
|
|
|
Ti-Al-N |
|
|||||||||||
|
|
|
|
|
|
|
|
|
|
+20 % Si |
|
|
+20 % Si |
|
|
|
|
|
|
|
|
|
|
|
|
|||
|
|
|
|
ВТ-1-00 и A99 |
|
|
|
|
|
|
|
|
ВТ-1-00 и A99 |
|
||||||||||||||
|
|
|
|
|
|
|
|
|
|
|
|
|
|
|
|
|
|
|||||||||||
Способ изготовления като- |
|
|
|
Литье |
|
Высокотемпературный |
|
|
СВС |
|
|
|
|
|
|
|
Литье |
|
||||||||||
да/мишени |
|
|
|
|
|
|
|
|
синтез под давлением |
|
|
|
|
|
|
|
|
|
|
|
|
|
|
|
|
|
||
|
|
|
|
|
|
|
|
|
|
|
|
|
|
|
|
|
|
|
|
|||||||||
Степень ионизации, % |
80 |
|
|
|
10 |
|
10 |
|
80 |
20…100 |
10 |
|
80 |
|
|
|
|
|
~ 90 |
|||||||||
Количество подложкодержа- |
1 |
|
|
|
1 |
|
|
|
1 |
|
|
|
|
2 |
|
|
|
|
|
|||||||||
телей |
|
|
|
|
|
|
|
|
|
|
|
|
|
|
|
|
|
|
|
|
|
|
|
|
|
|
|
|
|
|
|
|
|
|
|
|
|
|
|
|
|
|
|
||||||||||||||
Косвенный нагрев подложки |
|
|
|
– |
|
|
|
Нагреватель подложки |
– |
|
– |
|
АИИ |
Резистивный нагреватель |
||||||||||||||
|
|
|
|
|
|
|
|
|
мощностью0,5 кВт |
|
|
|
|
|
|
мощностью3 кВт |
||||||||||||
|
|
|
|
|
|
|
|
|
|
|
|
|
|
|
|
|
|
|
||||||||||
Температура подложки, К |
|
|
|
673…1000 |
|
573 |
|
|
|
373…573 |
|
|
|
|
|
|
473…573 |
|
||||||||||
Расстояние мишень (катод) – |
310 |
|
|
|
|
40…100 |
|
|
50…250 |
|
|
|
|
|
100…300 |
|
||||||||||||
подложка, мм |
|
|
|
|
|
|
|
|
|
|
|
|
|
|
|
|
|
|
|
|
|
|
|
|
|
|
|
|
|
|
|
|
|
|
|
|
|||||||||||||||||||||
Финишная очистка и актива- |
|
|
Ионная очистка |
|
– |
Ионно-лучевая обработ- |
Нагрев резистивным нагревате- |
|||||||||||||||||||||
ция поверхности подложки |
|
|
|
|
|
|
|
|
|
|
|
ка с использованием |
лем, очисткав тлеющем и/или |
|||||||||||||||
|
|
|
|
|
|
|
|
|
|
|
|
|
|
АИИ |
|
|
магнетронном разряде, ионная |
|||||||||||
|
|
|
|
|
|
|
|
|
|
|
|
|
|
|
|
|
|
|
|
|
|
очистка |
|
|||||
|
|
|
|
|
|
|
|
|
|
|
|
|
|
|
|
|||||||||||||
Состояние подложки |
|
|
|
Подвижная |
|
Неподвижная |
|
Неподвижная |
|
|
|
|
|
Подвижная |
|
|||||||||||||
Способ измерения темпера- |
Пирометр «Смотрич» |
Оптический микропи- |
|
|
– |
|
|
Инфракрасныйбесконтактный |
||||||||||||||||||||
туры подложкии пленки |
|
|
|
|
|
|
|
|
рометр(ВИМП−043м) |
|
|
|
|
|
пирометр «Термикс» |
|||||||||||||
|
|
|
|
|
|
|
|
|
|
|
|
|
||||||||||||||||
Материал подложки |
|
|
|
ВК8, Р6М5, |
|
ВК8, Р6М5, |
|
ВК8, Р6М5, |
|
|
|
ВК8, Р6М5, Ст3, |
||||||||||||||||
|
|
|
|
12Х18Н10Т |
|
ситалл СТ−50, α-Al2O3, |
|
12Х18Н10Т |
|
|
|
|
|
12Х18Н10Т |
|
|||||||||||||
|
|
|
|
|
|
|
|
|
12Х18Н10Т |
|
|
|
|
|
|
|
|
|
|
|
|
|
|
|
|
|
||
|
|
|
|
|
|
|
|
|
|
|
|
|
|
|
|
|
|
|
|
|
|
|
|
|
|
|
|
|
17

18
Окончание табл. 1 . 1
1 |
2 |
3 |
4 |
|
5 |
|
Диапазон стабильных рабочих |
0,45…0,75 |
0,1…6 |
1,0…2,0 |
|
0,8…1,2 |
|
давленийгазовой смеси, Па |
|
|
|
|
|
|
|
|
|
|
|
|
|
Содержаниереакционного газа |
90…100 |
60 |
14 |
35…70 |
30…90 |
30…50 |
(N2) в газовой смеси, % |
|
|
|
|
|
|
|
|
|
|
|
|
|
Напряжениесмещения на под- |
–200…280 |
–50; +45 |
|
–40…80 |
–80…250 |
–80…90 |
ложке, В |
|
|
|
|
|
|
|
|
|
|
|
|
|
Напряжение на магнетроне, В |
– |
350 |
250…500 |
300…700 |
– |
400…500 |
Ток на магнетроне, А |
– |
0,5 |
0,9…2,5 |
3,0…6,0 |
– |
4,0…5,0 |
Ток дуги, А |
70…75 |
– |
– |
– |
80…100 |
80…90 |
Предельная мощность разряда, |
– |
0,2…3,0 |
0,6 |
4,0 |
|
|
кВт |
|
|
|
|
|
|
|
|
|
|
|
|
|
Способ измерения толщины |
На поперечном |
С использованием двух |
На поперечном |
На |
поперечном |
шлифе |
пленки в процессе ее осаждения |
шлифе |
кварцевых датчиков |
шлифе |
|
|
|
|
|
|
|
|
|
|
Скорость осаждения пленки, |
13…40 |
1…4 |
1,5 |
4 |
10 |
12 |
мкм/ч |
|
|
|
|
|
|
|
|
|
|
|
|
|
Методы формирования слоев МП: магнетронное распыление, электродуговое испарение, комбинирование данных методов.
Материал и размеры тестовых образцов:
–12×10×5, 3×3×2 мм – из быстрорежущей стали Р6М5;
–3×3×2 мм – из нержавеющей стали 12Х18Н10Т;
–10×12×3, 3×3×2 мм – из твердого сплава ВК8 (см. табл. 1.1).
Элементный состав, метод изготовления и закрепления многоком-
понентных композитных мишеней:
–76,0 % Ti+4,0 % B+20 % Si – высокотемпературный синтез под давлением (ВСД), прижатие к корпусу магнетрона вакуумной двухкамерной установки МР без непосредственного контакта с охлаждающей водой.
–55,2 % Ti+24,8 % B+20 % Si – самораспространяющийся высокотемпературный синтез (СВС), прижатие к корпусу магнетрона с непосредственным контактом с охлаждающей водой.
19
2. МЕТОДИКИ ИЗУЧЕНИЯ ФУНКЦИОНАЛЬНЫХ СВОЙСТВ МНОГОСЛОЙНЫХ ПЛЕНОК НА ОСНОВЕ ДВУХ-, ТРЕХ-
И МНОГОКОМПОНЕНТНЫХ СЛОЕВ И УПРОЧНЕННЫХ ИЗДЕЛИЙ
2.1. МЕТОДИКА ИЗУЧЕНИЯ АДГЕЗИОННОЙ ПРОЧНОСТИ
СФОРМИРОВАННЫХ МНОГОСЛОЙНЫХ ПЛЕНОК НА ОСНОВЕ
ДВУХ-, ТРЕХ- И МНОГОКОМПОНЕНТНЫХ СЛОЕВ
Адгезионную прочность МП, осажденных МР, ЭДИ, ЭДИ+МР, оценивают вдавливанием различных инденторов. Большинство слоев или МП на их основе хорошо сопротивляются нормальным нагрузкам, что обусловлено высокой аксиальной текстурой и сжимающими напряжениями. Скалывания или отслаивания слоев и МП в целом в большинстве случаев не наблюдается. Метод прямого отрыва МП от подложки также не дает количественных результатов, так как их адгезионная прочность
сподложкой выше прочности сцепления клеевого соединения на основе смол. Для оптимизации процесса осаждения слоев МП с высокой адгезионной прочностью используются различные методы ее оценки. Сравнительная характеристика адгезии МП к подложке и адгезии слоев МП, нанесенных при разных режимах осаждения, осуществляется по трем признакам: отслаивание не наблюдается, имеются отдельные участки отслаивания, полное отслаивание.
Методика оценки адгезионной прочности пленки в соответствии со стандартом VDI-3198, Германия. Адгезия определяется по совместной локальной пластической деформации слоя (или МП) и подложки путем внедрения индентора твердомера Роквелла (алмазный конус) при нагрузке на индентор 1471 Н в образец-свидетель со слоем или МП и последующей визуальной оценкой результата индентации по шестибалльной шкале (балл HF-1 соответствует наивысшей адгезионной прочности).
Метод скрабирования – метод поперечных насечек (метод решетки)
сиспользованием адгезиметра ELCOMETER 107. После нанесения насечек
поверхность слоя или МП очищается мягкой кистью для удаления чешуек. Наклеивается, а затем снимается подходящая липкая лента в соответствии с требованиями применяемого стандарта, после чего адгезионная прочность слоя (или МП) оценивается по табл. 2.1.
20