
книги / Производство метанола
..pdf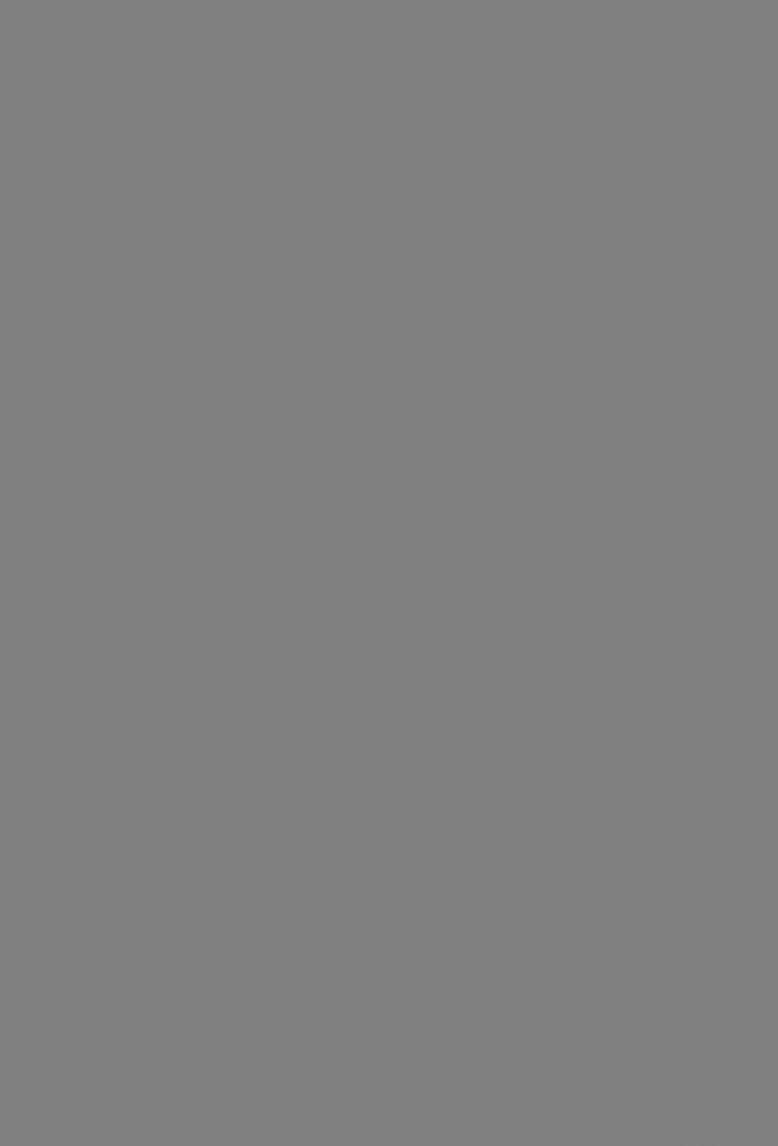
На вновь создаваемых крупных агрегатах применяется более про грессивное воздушное охлаждение циркуляционного газа.
На рис. 36 изображен горизонтальный трехконтурный аппарат воздушного охлаждения (поверхность теплообмена 20000 м2, вес 95 г, габариты 9X 8X 8 м). Поступающий на охлаждение циркуля ционный газ проходит внутри оребренных труб, смонтированных в секции. Снаружи трубы обдуваются воздухом, нагнетаемым вен тиляторами. Заданный температурный режим регулируется авто матически поворотом лопастей вентиляторов, жалюзей, впрыском воды для увлажнения воздуха. Аналогичные аппараты воздушного охлаждения применяются для конденсации паров метанола при ректификации.
Выносные теплообменники являются обычными теплообмеиными аппаратами трубчатого типа, в которых по трубам пропускает ся горячий газ из колонны, а в межтрубном пространстве — холод ный циркуляционный газ.
Пусковые электроподогреватели в настоящее время, особенно в крупных агрегатах, заменяют паровыми или огневыми подогрева телями, которые по конструкции близки к теплообменникам.
Сконденсировавшийся метанол в схемах синтеза при высоком давлении отделяют в сепараторах таких же конструкций, какие используют в производстве аммиака3. В системах, работающих при низком давлении, применяют сепараторы со специальными устрой ствами для улавливания брызг и лучшего отделения метано ла-сырца.
До последнего времени -в производстве метанола применяли поршневые компрессоры. Но эти машины обладают существенными недостатками: загрязнение газа маслом, из-за чего требуется после дующая его очистка перед -подачей на синтез, а также небольшая производительность и сложность обслуживания. Внедрение новых конструкций насадок колонн синтеза с низким сопротивлением по зволяет применить для циркуляционного газа центробежные комп рессоры, например марки ЦЦК-10. Этот компрессор состоит из цельнокованного герметического корпуса высокого давления, внут ри которого -размещен 12-ти ступенчатый центробежный компрессор и асинхронный трехфазный электродвигатель. Производительность при 40 °С и 290 ат составляет 360—400 мъ/ч, перепад давлений ~ 3 0 ат, скорость вращения вала 2970 оборотов в минуту. Электро двигатель обдувается специально подготовленным сухим газом.
Центробежные турбоциркуляционные компрессоры просты -в об служивании, исключают возможность загрязнения газа маслом. Они размещаются на открытой площадке непосредственно около колонн синтеза. Ввиду больших преимуществ этих машин все вновь строящиеся производства метанола, в том числе, безусловно, и си стемы, работающие при низком давлении, оборудуются турбоциркуляционными компрессорами, а на предприятиях средней мощно сти происходит замена ими поршневых машин. Общий вид турбоциркуляционного компрессора приведен на рис. 37.
102
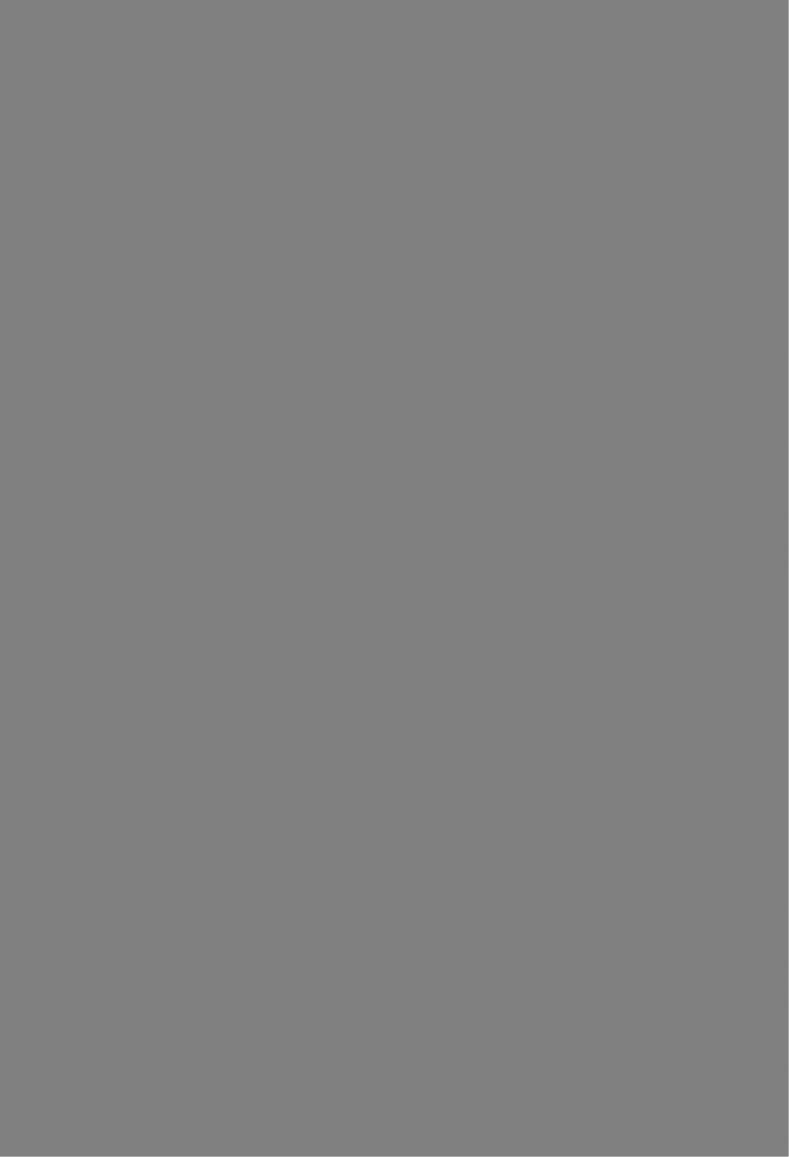
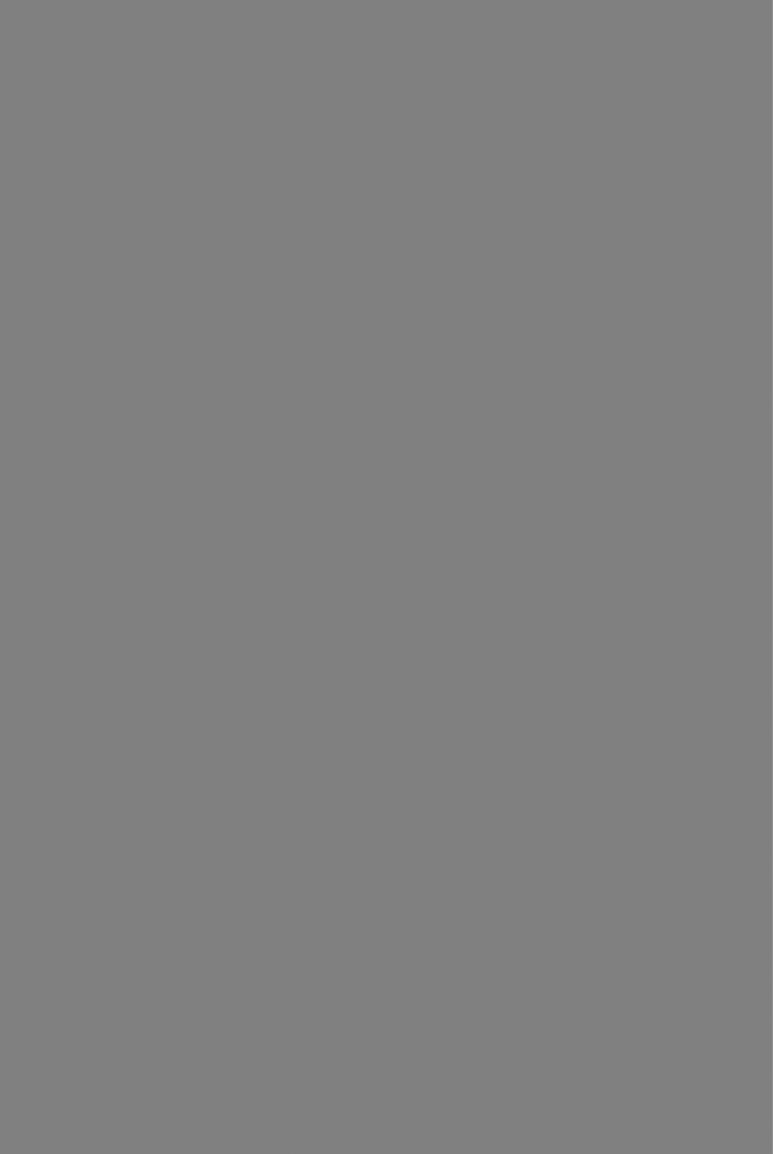
Как указывалось выше, реакционная зона обогревается сжига нием газа, который поступает в горелки при небольшом давлении (3,6—4,0 ат). Ори поступлении газа в горелку, за счет его давления инжектируется необходимое количество воздуха. Дымовые газы из топочной камеры печи с температурой до 1000°С направляются в котлы-утилизаторы для получения технологического пара высо кого давления (~ 4 0 ат, «о возможно и до 100 ат).
На создаваемых крупных агрегатах производства метанола кон версию осуществляют при давлении 16—25 ат. Конструктивное оформление трубчатой печи принципиально не отличается от описанной. Это крупный агрегат, оборудованный рядом теплообмен ных устройств, что позволяет в результате интенсивной утилизации тепла практически полностью обеспечить производство метанола ■необходимой ему энергией.
|
|
|
Л И Т Е Р А Т У Р А |
|
|
1. |
Л ей б у ш А. Г., Хим. пром., № 3, 213 (1960). |
|
|
||
2. |
Справочник азотчика. Т. 1. М., «Химия», 1967. |
|
|
||
3. |
Р у м я н ц е в |
О. В. Оборудование цехов синтеза высокого давления в азотной |
|||
4. |
промышленности. М„ «Химия», 1967. |
|
|
||
А т р о щ е н к о В. И., А л е к с е е в А. М. и др. Курс технологии связанного |
|||||
5. |
азота. 2-е изд. М., «Химия», 1969. |
|
связанного азота. Пер. с |
||
Б л а с я к Е., |
Л а й д н е р К. и др. Технология |
||||
6. |
польск. Полякова Н. Н. М., Госхимиздат, 1961. |
|
|
||
З о т о в а Н. И., Азотн. пром., № 5, 98 (1969). |
|
|
|||
7. Англ. пат. 836909 (1957). |
авт. свид. СССР 231702, 1968; |
||||
8. |
Б о н д а р е н к о П. П., З о т о в а Н. И. и др., |
||||
9. |
Изобр., пром. образцы. Товарн. знаки, № 36 (1968). |
К. П., Азотн. пром., № 4, |
|||
К а р а в а е в |
М. М., |
П о п о в И. Г., Пе т р и ще в |
|||
|
27 (1965). |
М. М., |
Лен дер А. А., По по в |
И. Г., Хим. пром. Украины, |
|
10. К а р а в а е в |
№1, 3 (1968).
И.Г а н з С. Н. Технологические процессы и оборудование производств синтез-га
за и связанного азота. Харьков, 1960.
Г Л А В А IV
РЕКТИФИКАЦИЯ МЕТАНОЛА-СЫРЦА
ТЕХНОЛОГИЧЕСКИЕ СХЕМЫ РЕКТИФИКАЦИИ МЕТАНОЛА-СЫРЦА
Метанол-сырец, «получаемый в агрегате «синтеза, содержит зна чительное количество органических примесей. Хотя их общее коли чество невелико (от 0,4 до 6,0% в пересчете на органическую часть), отделение их от метанола .представляет значительные труд ности. По физико-химичеоким «свойствам эти вещества отличаются друг от друга и от метанола. Температуры кипения всех органиче ских примесей лежат в интервале более 100 °С. Так, диметиловый эфир кипит при атмосферном давлении при —23,7 °С, а отдельные высшие спирты имеют температуру кипения выше 100 °С. При опре деленных концентрациях некоторые из присутствующих примесей могут образовывать с метанолом азеотропные омеси, причем воз можно образование «и тройных смесей вода — метанол — третий компонент1. Таким образом, проблема выделения чистого метанола очень сложна.
Процесс очистки метанола-сырца включает несколько стадий: ректификацию, которая является основным этапом очистки, адсорб цию и химическую очистку. Химическая очистка позволяет разру шить трудно отделяемые ректификацией примеси, адсорбция — извлечь некоторые примеси из метанола твердыми сорбентами.
Ректификация — сложный вид перегонки, основанный на противоточном взаимодействии пара и жидкости, позволяет достичь наи более полного разделения компонентов. Состав микропримесей,, присутствующих в метаноле-сырце, расшифрован «сравнительно не давно, да и то неполностью/ В связи с этим технологические пара метры процесса ректификации основаны на результатах экспери ментальных работ. Теоретическое обоснование получил лишь про цесс «разделения смеси метанол — «вода.
В практике разделения смесей близкокипящих веществ применя ют специальные виды перегонки: экстрактивную и азеотропную-. При экстрактивной перегонке «в смесь вводят дополнительный ком понент, который обладает значительно меньшей относительной ле тучестью, чем компоненты исходной смеси. Он отводится из колон ны с «кубовым остатком. При азеотропной перегонке вводимый ком понент образует легкокипящие азеотропные смеси с одним из ком понентов разделяемой смеси. Таким дополнительным компонентом: в процессе «ректификации метанола-сырца является вода, содержа
106
ние «которой колеблется от б до 20%. Низкокипящие примеси наи более эффективно удаляются при содержании 12— 15% еоды. Эффективности очистки -способствует также омыление эфиров, протекающее в кубе колонны под воздействием щелочи, вводимой в (метанол-сырец. В настоящее время ректификация метанола-сырца является непрерывным процессом. Установка состоит из 3 или 2-х колонн, на которых сначала удаляются низкокипящие компоненты смеси, затем высококипящие путем их вывода из определенной точ ки колонны и ее куба. Отбираемые фракции перерабатываются на отдельных колоннах с -выделением метанола и высших спиртов.
Для большинства производств ректификация метанола-сырца, полученного при 300 ат, «проводится в следующей последовательно сти:
1)-выделение диметилового эфира (обезэфиривание);
2)предварительная ректификация — выделение низкокипящих примесей;
3)химическая очистка;
4) основная ректификация— «выделение примесей, имеющих температуру кипения выше температуры кипения метанола.
Некоторые схемы предусматривают разделение боковых фрак ций колонны основной ректификации.
Технологическая схема процесса ректификации метанола-сырца изображена на рис. 39. Перед поступлением в колонну обезэфиривания 2 метанол-сырец обрабатывают 7—8%-ным раствором NaOH* для нейтрализации кислоты. Метанол-сырец подогревается в теплообменнике 5 за счет тепла кубового «остатка колонны 2 и па рового конденсата, выходящего из кипятильника 1, и вводится при мерно в «среднюю часть колонны о'безэфир.ивания 2. Здесь из него при 10— 12 ат и температуре «в кубе колонны 125—135 °С отгоняется диметиловый эфир (ДМЭ), часть растворенных газов и некоторых друпих примесей (азотистых соединений, карбонилов железа и д-р.). Отобранный из верхней части колонны эфир конденсируется в кон денсаторе 3 и поступает в сборник 4. Часть конденсата возвращает ся в виде флегмы на орошение колонны 2, а другая часть выводит ся потребителю или на сжигание. Несконденсировавшиеся пары из конденсатора и сборника проходят через циклон 6 и сжигаются или выбра-сы-ваются в атмосферу.
Из куба колонны 2 обезэфиренный метанол через систему тепло обменников 5 -направляется в колонну предварительной ректифика ции 7 (КПР). Перед подачей -в колонну для облегчения отделения примесей в него добавляют паровой конденсат (если содержание воды «в метаноле-сырце меньше 12—15%). Количество парового конденсата зависит от содержания примесей в метаноле-сырце.
Пары, выходящие из колонны 7, «конденсируются при 35—40 °С
вконденсаторе 3, и конденсат поступает -в сборник 4. Неоконденси-
*Если оборудование изготовлено из углеродистой стали; расход щелочи за висит от содержания органических кислот и обычно составляет 0,3—-0,6 кг на 1 г метанола-сырца.
107
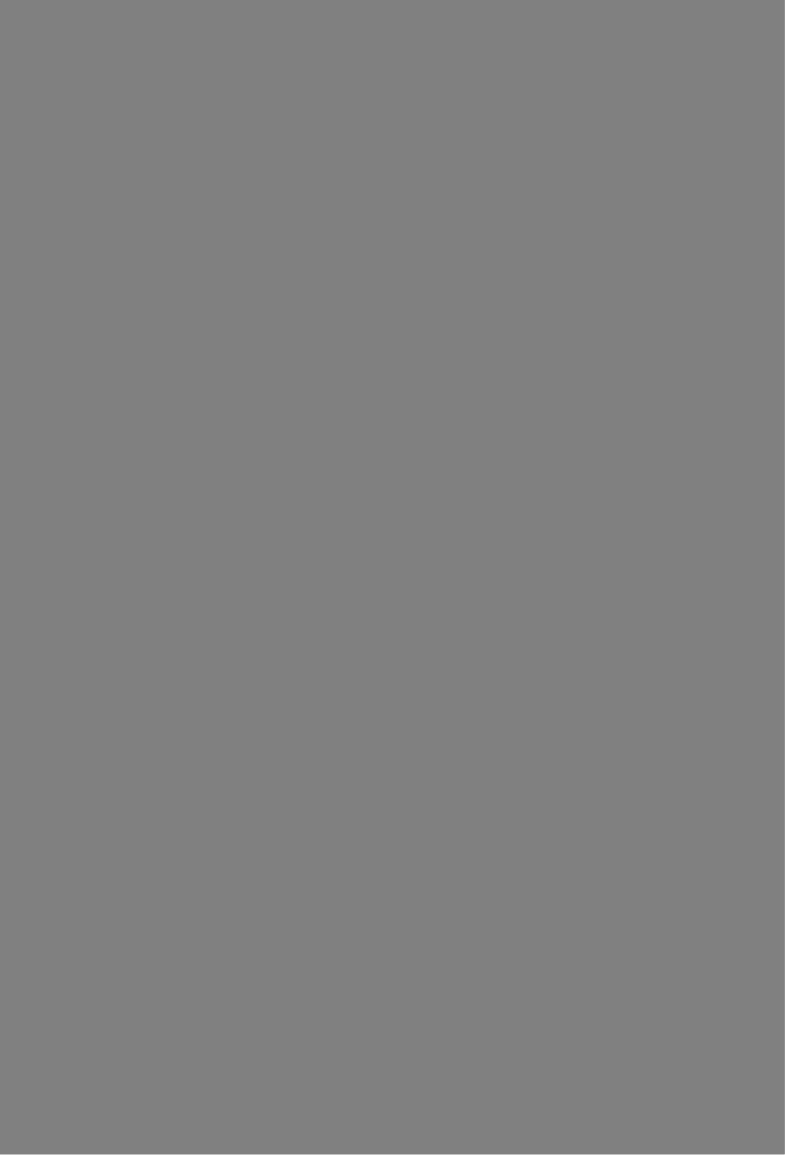
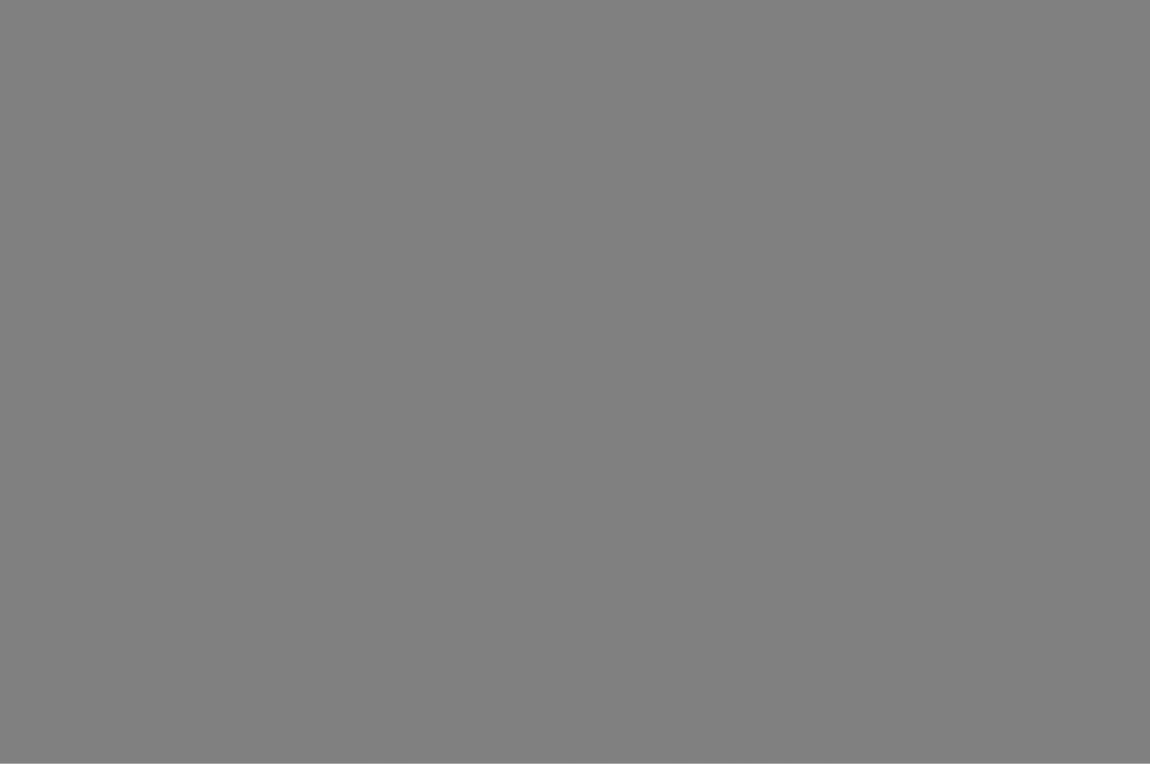