
книги / Производство метанола
..pdfпроизводства или используют для других целей.' Количество проду
вочных газов зависит |
от |
содержания СИ4, |
N2 |
в исходном |
газе, |
|
а также от принятого в цикле отношения И2:СО |
(см. табл. 28—29 |
|||||
стр. 61). |
Например, |
при |
содержании в |
исходном газе |
0,3— |
|
0,7 объемн. |
% СН4, 2—3 объемн. % N2 и отношении Н2: СО= 6-^8 |
выводят около 400—600 м3 газа на 1 тметанола-сырца (с учетом газов, выделяющихся через сальниковые уплотнения).
Наличие в описанной схеме выносного теплообменника и элект роподогревателя приводит к большой протяженности коммуника ций, высокому гидравлическому сопротивлению системы и потерям
Рис. 25. Схема агрегата синтеза с совмещенной насадкой колонны:
1.И -2 — фильтры; 3 — колонна; 4 — холодилышк^конденсатор; 5 — сепараторы: 6 — компрес сор; 7 — сборник.
тепла в окружающую среду. Перепад давления на таких агрегатах малой мощности составляет обычно 20—25 ат, а при высоких объ емных скоростях газа даже несколько больше. Установка электро подогревателя в центральной трубе катализаторной коробки упро щает схему и снижает сопротивление агрегата, однако выносной подогреватель более надежен и прост в обслуживании. При исклю чении обдува корпуса колонны холодным газом кольцевое прост ранство между насадкой и корпусом заполняют термоизоляцион ным материалом. Это уменьшает сопротивление системы, но и сни жает степень использования объема поковок высокого давления и не обеспечивает необходимого снижения температуры стенок кор пуса колонны. Определенные трудности встречаются также при сборке и разработке несовмещенных насадок, которые обычно про водятся при снятии корпусов высокого давления с фундаментов.
Агрегаты синтеза с совмещенной насадкой колонны (рис. 25) отличаются «существенными преимуществами перед описанными. Сжатый до 320 ат исходный газ проходит масляный фильтр 1 и угольный фильтр 2, после чего смешивается с циркуляционным газом (иногда смешение проводят перед вторым сепаратором). Смешанный газ, пройдя кольцевой зазор между катализаторной коробкой и корпусом колонны 3, поступает в межтру.бное. простран-
6-1245 |
'81 |
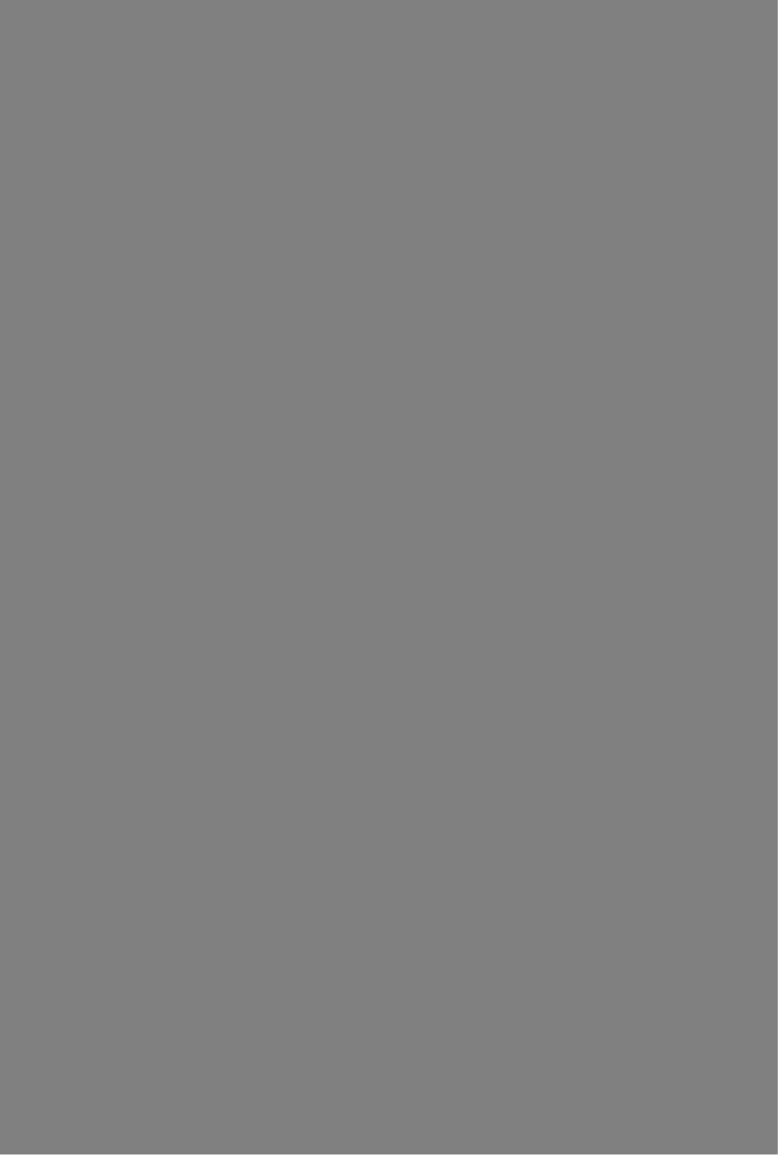
лизаторе за счет охлаждения ©оды ©ысокого давления получают пар. Прореагировавший газ из колонны с температурой около 130°С выводят в водяные холодильники.
В схеме фирмы Krupp в нижней части колонны синтеза имеется, как в колоннах с совмещенной насадкой теплообменник для подо грева смешанного газа до температуры начала реакции. В верхней части расположена катализаторная коробка полочного типа в цент ре которой установлен пусковой электроподогреватель. Отличие от описанных выше схем состоит в том, что при выходе из зоны ката лиза не весь конвертированный газ проходит через теплообменник. Часть его (приблизительно 20—25%) с температурой 370—380 °С выводится из колонны и используется для получения пара в кот лах-утилизаторах. Оба потока газа соединяются в водяном холо дильнике-конденсаторе. Диаметр колонны 1100 мм и высота 18 мм, синтез проводят при 390—410 ат,
С точки зрения экономической целесообразности вариант фир мы Montecatini предпочтительнее: регулируя количество циркули рующей воды в цикле высокого давления, можно проводить синтез в строго оптимальных температурных условиях. Это дает возмож ность одновременно с получением пара уменьшить образо«вание по бочных продуктов, увеличить выход метанола, улучшить условия эксплуатации катализатора, т. е. увеличить срок его службы. В аг регатах фирмы Krupp возможности регулирования температуры по высоте катализаторной зоны посторонним теплоносителем не имеется.
Нужно отметить, что в крупных агрегатах синтеза «метанола тем пературу в слое катализатора обычно не регулируют посторонним теплоносителем, избегая, видимо, усложнения конструкции агрега та. В этом случае можно использовать большое количество низко потенциального тепла путем установки теплообменников (котлов) между газовым теплообменником колонны и конденсатором. При
мером |
такого |
решения |
является |
технологическая схема фирмы |
BASF (ФРГ), которая приведена на рис. 26. Синтез проводят при |
||||
250-^320 ат и |
360—380 °С на катализаторе фирмы. Схема имеет |
|||
один |
агрегат |
синтеза |
метанола |
мощностью 700 т/сутки |
(~240 тыс. т(год). В качестве сырья используется легкий бензин каталитического крекинга, который испаряется в аппарате 1 (испа ритель). Предварительно в него вводится водород для гидрирова ния соединений серы на кобальт-молибденовом катализаторе в ап парате 2. Сероводород удаляется в адсорбере 3 путем адсорбции на окиси цинка при температуре около 350 °С. Затем в конверторе 4 смесь подвергается «паровой каталитической конверсии при темпе ратуре ~450°С , при этом «получается газ с содержанием около 62 объемн. % СН4. Этот газ подвергается вторичной паровой кон версии на другом катализаторе при 850—870 °С. В трубчатой печи 5 получают газ, пригодный для производства метанола без регулиро вания его состава. Реакционное пространство трубчатой печи 5 обогр.евают за счет сжигания (продувочных и танковых газов и от-
6* |
83 |
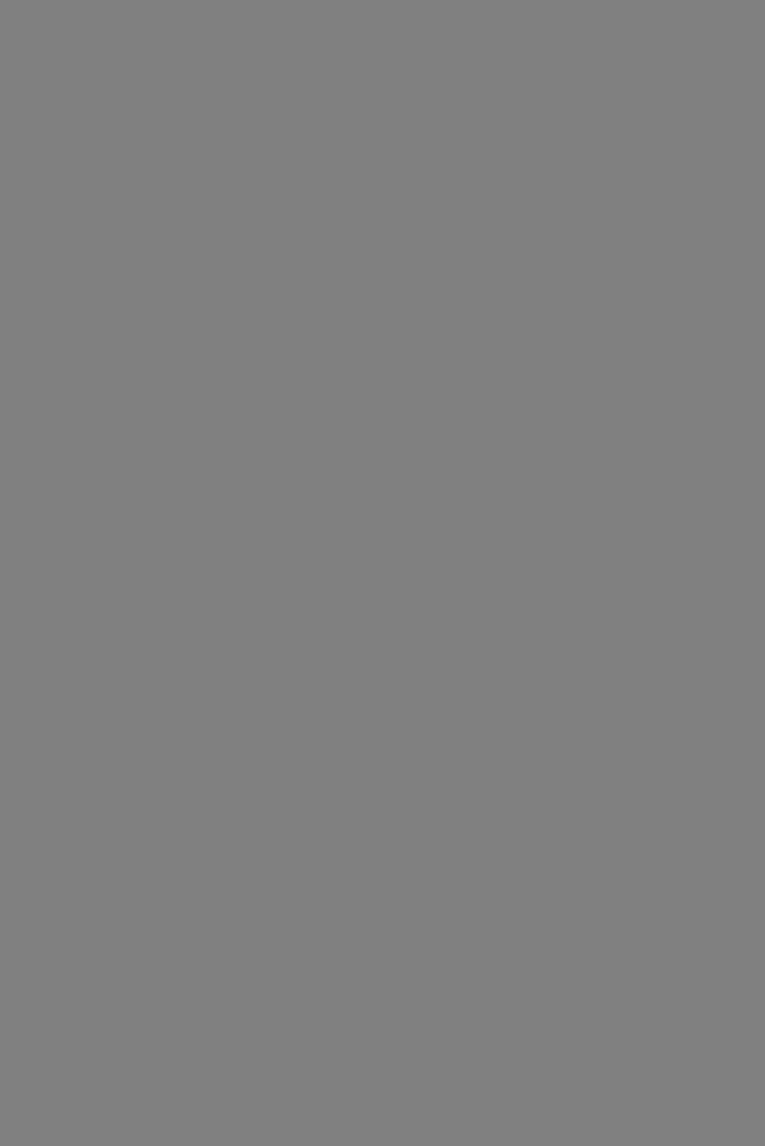
ны используют пар, получаемый непосредственно на установке (45—60 ат}
Как указывалось ранее, процесс производства метанола при низком давлении включает практически те же стадии, что и произ водства его при высоком давлении. Однако имеются и некоторые особенности. На рис. 27 приведена принципиальная схема произ водства метанола при 50—60., ат из природного газа с агрегатом мощностью около 300 тыс. т/год. Синтез проводят на низкотемпера турных медьсодержащих катализаторах, весьма чувствительных к каталитическим ядам, поэтому первой стадией процесса является очистка природного газа от соединений серы. Содержание соедине ний серы в технологическом газе должно быть не более 0,25 мг/м3, т. е. природный газ должен содержать их 1 мг/м3 (с учетом увели чения объема газа при конверсии).
Природный газ проходит сепаратор 1для отделения жидких угле водородов, ежи.мается турбокомпрессором2 до 28—30ат и подогре вается в подогревателе 3 за счет сжигания в межтрубном простран стве природного газа. Последующую очистку проводят в две ста дии. В аппарате 4 при 380—400 СС осуществляется каталитическое гидрирование органических соединений серы до сероводорода (во дород или подходящий по условиям процесса водородсодержащий газ вводят перед подогревателем 3). В адсорбере 5 при темпера туре ~ 360 °С сероводород поглощается адсорбентом на основе оки си цинка (объем катализатора и поглотителя должен обеспечивать срок службы, определенный для катализатора синтеза метанола, или быть больше его). В избранных технологических условиях до стигается высокая степень очистки. Очищенный газ подают на кон версию в трубчатую печь 6\ в газ предварительно вводят необходи мое количество водяного пара и двуокиси углерода. Температура паро-газовой смеси повышается в подогревателе трубчатой печи за счет тепла дымовых газов до 530—550 °С; подогретый газ направ ляется непосредственно на катализатор в реакционные трубы. Про цесс паро-углекислотной конверсии проходит при давлении до 20 ат. Тепло, необходимое для конверсии, получается в результате сжига ния отходов производства .или природного газа в специальных го релках. Тепло дымовых газов, имеющих температуру выше 1000 °С. используют’ для подогрева паро-газовой смеси, получения пара вы сокого давления в котле-утилизаторе, подогрева воды, питающей котлы, и топливной смеси перед подачей ее в горелки трубчатой печи 6. Охлажденные до 200—230 °С дымовые газы выбрасываются в атмосферу или частично направляются на выделение двуокиси углерода.
Конвертированный газ после трубчатой печи поступает в ко тел-утилизатор 7 и охлаждается до 280—290 °С. Затем тепло газа используется в теплообменнике 8 для подогрева питательной воды, направляемой в котел-утилизатор. Газ с температурой около 100 °С проходит воздушные холодильники-конденсаторы 9, в которых при охлаждении до 35—40 °С из него выделяются пары воды, и далее
85
| Дымобыб
газы
A;TК
ь—
73
J 18
„ ^ ____
I D
г - п
1L 15
/ 1
( ТМетанол -) сырец
Рис. 27. Схема производства метанола при 40—60 ат:
I, |
Ю и /« — сепараторы; 2, И и /2 — компрессоры; |
« — подогреватель; |
4 — аппарат |
для |
гидрирования |
||
соединений серы; 5 — адсорбер; |
б — трубчатая |
печь; |
7 — котел-утилизатор; 8, 13 и /4 — теплообменники; |
||||
9, |
17 — холодильники-конденсаторы; |
15 — подогреватель; |
16 — колонна; |
/« — сборник. |
|
|
сепаратор 10. Охлажденный конвертированный газ при давлении ~17 ат сжимается компрессором 11 до 55 ат и смешивается с цир куляционным газом после компрессора 12 (оба компрессора рабо тают с приводом от паровых турбин, использующих перегретый пар, полученный непосредственно на агрегате). Смешанный газ в теплообменниках 13 и 14 подогревается до 219—230 °С и поступает в колонну синтеза 16 (в период пуска агрегата газ проходит через подогреватель 15).
Параметры технологического режима следующие: давление ~50 ат; температура на входе 215—230 °С и на «выходе ~280°С; объемная скорость газа в начале процесса ~ 12 000 ч~\ в конце — 8500—9000 ч~1 (объемная скорость может оставаться постоянной ~ 10 000 н~1 при условии сохранения «в течение пробега одинакового содержания инертных компонентов в циркуляционном газе). Тем пературу в колонне регулируют с помощью холодных байпасов. Со держание двуокиси углерода в газах синтеза относительно высокое (8—12 объемы. %), так как отсутствует очистка от двуокиси углеррда. Концентрация окиси углерода (~ 1 2 —16 объемн. %) зависит от ряда факторов, в том числе от содержания инертных компонен тов в цикле. В этих условиях Нг:СО=5—7 а 2,5.
Тепло выходящего газа используют в теплообменниках 13 и 14 для подогрева поступающего в колонну смешанного газа. Возмож на установка между теплообменниками котла-утилизатора для по лучения пара относительно низких давлений. Далее газовая смесь охлаждается в холодильниках-конденсаторах 17, сконденсировав шийся метанол-сырец отделяется в сепараторе 18 и поступает в сборник 19. Циркуляционные газы возвращаются в компрессор 12, продувочные и танковые передают на сжигание в трубчатую печь.
Другие схемы производства метанола при низком давлении предусматривают наличие двух колонн синтеза в одной технологи ческой нитке, что обусловлено размерами колонны. Технологические условия процесса аналогичны описанным выше. Схемы производст ва метанола при низком давлении имеют хорошие технико-экономи ческие показатели, более просты в аппаратурном оформлении и по этому получают все большее признание.
Несколько отличаются от описанных технологические схемы на основе отходов производства ацетилена (синтез-газ). Этот газ со держит водород и окись углерода в соотношении, близком к двум,, однако присутствуют до 5,5 объемн. % СН4, 2—3 объемн. % N2,
ацетилен и его производные, этилен и соединения азота. Это за трудняет использование газа без предварительной подготовки. Имеется несколько способов переработки синтез-газа в метанол. Обычно его подвергают паро-кислородной, паро-углекислотной или высокотемпературной конверсии. Одновременно с окислением мета на конвертируется и большинство присутствующих в газе органиче ских примесей. Существуют схемы, в которых компоненты газовой смеси разделяются на у-становках глубокого холода или метан вы деляется промывкой жидким азотом. После конверсии газ очищает
37
ся'от С 02 и в результате имеет состав, необходимый • для синтеза метанола. Поэтому схема полученияметанола аналогична описан ным выше.
Представляют интерес технологическая схема7 переработки син тез-газа фирмы ICI й разработанный в СССР так называемый бес* конверсионный способ8. По схеме фирмы ICI из газов, полученных неполным окислением углеводородов, удаляют двуокись углерода промывкой аммиачной водой, затем ацетилен — обработкой жидким аммиаком при —70 °С, и наконец, этилен — абсорбцией нафтолом
Рис. 28. Схема бесконверсионной переработки синтез-газа производства ацетиле на при 320 ат:
/ и 7 — компрессоры; 2 и 6 — абсорберы; 3 — колонна; 4 — холодильник-конденсатор; 5 — се паратор; 8 — рекуперационная' машина; 9 и 10 — десорберы; // — сборник.
при —20 9С и 30 ат. Метан же выделяют из циркуляционных газов промывкой метанолом-сырцом при 30—40 °С и давлении синтеза. Таким образом, синтез метанола проводят в присутствии большого количества метана и азота, и технологическая схема, кроме обыч ных аппаратов, включает абсорберы для .их поглощения.
По бесконверсионной схеме8 (рис. 28) синтез-газ при давлении пиролиза метана до ацетилена поступает в отделение компрессии и дожимается компрессором 1 до давления синтеза метанола. Да лее газ поступает в абсорбер 2 для отмывки двуокиси углерода, ацетилена, этилена и других соединений метанолом-ректификатом. Одновременно в метаноле-ректификате растворяется некоторое ко личество водорода, окиси углерода и метана. Очищенный газ сме шивается с циркуляционным газом и поступает в колонну 3. Син тез проводят в обычных колоннах при содержании инертных компо нентов в газе до 30 объемн. %. Газ при выходе из колонны охлаж-
88
дается в .холодильнике-конденсаторе 4 до 30—35 °С и, пройдя сепа ратор 5, поступает в абсорбер 6, где из него метанолом-ректифика том частично отмываются инертные компоненты, главным образом метан. Далее газ поступает в турбоциркуляционный компрессор?, дожимается до давления, синтеза и, смешиваясь с исходным газом, вновь подается на синтез. Продувочные газы выводят после абсор бера 6. Метанол-сырец из сепаратора 5 дросселируется в сборник 11 и передается в отделение ректификации.
Метанол-ректификат с поглощенными газами из абсорберов 2 и 6 подают в рекуперационную машин/- 8, чтобы использовать энер гию отработанного метанола для сжатия регенерированного. Далее он поступает в промежуточный десорбер 9, где при снижении дав ления до 5— 10 ат выделяется основное количество абсорбирован ных газов. Окончательное выделение последних происходит в десорбере 10 при 1—2 ат. После десорбции регенерированный метанол сжимается до 280—320 ат и возвращается на орошение абсорберов 2 и 6. Газы после регенерации вместе с продувочными и танковыми газами могут быть использованы, например, в производстве аммиа ка или как топливо.
. На 1 г метанола-ректификата расходуется 3280 л3 синтез-газа и 27 кг рецир кулирующего ректификата. Количество десорбированных, продувочных и танковых газов, которые могут быть использованы в смежных производствах, составляет 709 M Z( T . Выделение метана по стадиям синтеза складывается следующим обра зом: при очистке исходного газа от ацетилена и этилена отмывается 23,2%; при конденсации метанола-сырца растворяется 8,8%; при отмывке метанолом цирку ляционного газа — 34,2%; выводится вместе с продувочными газами — 33,8%.
Описанная схема проста в исполнении, укомплектовывается .-ти повым оборудованием, в ней. полностью исключается-потребность в кислороде, катализаторе конверсии метана, моноэтаноламине, .аь кращается расход энергии и уменьшается необходимое число обслу: живающего персонала. По сравнению с конверсионным методом удельные капиталовложения снижаются на 12,5%, а себестоимость метанола — на 10,5% (аналогичное снижение затрат будет наблю даться при сравнении с любой технологической схемой при одина ковой мощности).
/ Метанол выделяют из.газов синтеза путем их охлаждения в хо лодильниках-конденсаторах. В интервале температур 20—40 °С дав ление насыщенных паров над чистым метанолом составляет 88,7— 243,5 мм рт. ст. Это позволяет на установках, работающих при дав лении выше 250 ат, охлаждать газ только до 30—40 °С оборотной водой или воздухом. В циркуляционных газах после отделения ме танола-сырца в сепараторах высокого давления содержится не бо лее 0,1 объеми. % метанола. Таким образом, степень выделения последнего составляет более 98%. При производстве метанола при 40—60 ат в циркуляционном газе в указанных условиях может со держаться до 0,6—0,7 объемн. % паров метанола, т. е. ~20% от образовавшегося в колонне. В этом случае для повышения степени выделения метанола имеет смысл проводить конденсацию при 20—
89
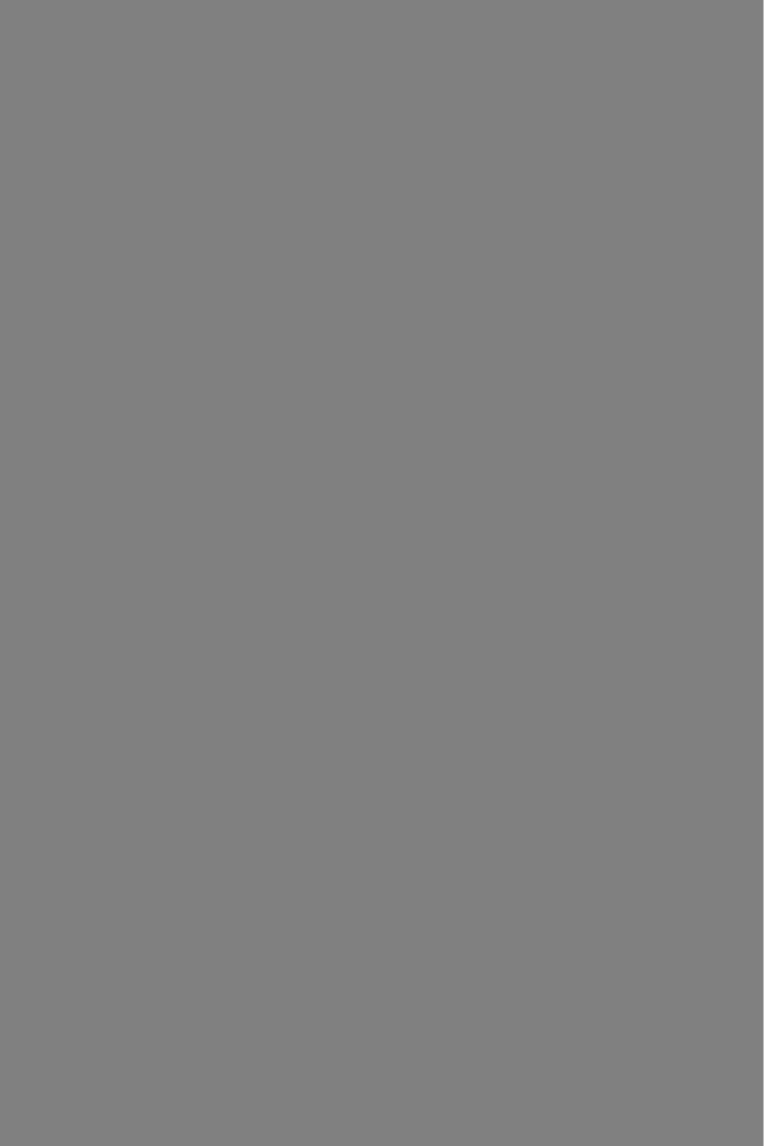