
книги / Производство метанола
..pdfмого состава можно руководствоваться соответствующими условия ми равновесия для данного процесса. Примерный состав газовой смеси после 'Конверсии природного газа различными способами приведен в табл. 31 (температурный режим конверсий — обычный для промышленных условий).
Т а б л и ц а 31. Примерный состав газовой смеси после конверсии природного газа различными способами
|
|
|
Состав конвертированного газа, |
|
|
||||
|
|
Давле |
|
|
объемн. % |
|
|
|
|
Виды конверсии |
|
|
|
|
|
|
Но:СО |
|
|
|
ние, |
|
|
|
|
|
|
||
|
|
am |
Н2 |
СО |
СОо |
СН4 |
No-rAr |
|
|
|
|
|
|
|
|||||
Паро-кислородная |
|
1 |
66,8 |
24,3 |
7,5 |
0,5 |
0,9 |
2,75 |
1,87 |
Паро-углекислотная с при |
20 |
65,6 |
22,1) |
10,9 |
0,5 |
1.0 |
2,98 |
1,66 |
|
|
|
|
|
|
|
|
|
||
менением кислорода |
|
1 |
62,2 |
27,1 |
9,1 |
0,5 |
1.1 |
2,30 |
1,48 |
Паро-углекислотная |
в |
1 |
68,5 |
25,0 |
4,6 |
1.7 |
0,2 |
2,74 |
2,15 |
трубчатых печах |
|
||||||||
|
|
20 |
68,6 |
16,8 |
10,9 |
3,5 |
0,2 |
4,08 |
2,08 |
Высокотемпературная |
. . |
20 |
62,2 |
34,2 |
2,1 |
0.5 |
1.0 |
1,82 |
1,69 |
Процессы конверсии углеводородных газов также широко осве щены в литературе, и здесь не рассматриваются. Для производства метанола представляют интерес лишь некоторые данные по полу чению исходного газа методами паро-углекислотной конверсии в трубчатых печах и паро-углекислотной конверсии с применением кислорода. В обоих случаях равновесный состав газовой смеси определяется равновесием реакций окисления метана водяным паром и восстановлением двуокиси углерода водородом:
СН4 4- Н20 ZH2 СО 4- ЗН2
С02 + Н2 |
СО 4- н 20 |
При высоких температурах промышленной конверсии равновесие |
|
реакции окисления метана |
кислородом практически полностью |
сдвинуто в сторону образования СО и Нг, а равновесие реакции окисления метана двуокисью углерода учитывается приведенными выше реакциями.
Константы равновесия для конверсии метана кислородом в ди апазоне температур 427—1127°С вычисляют по уравнению
9840
\g Kp==— — 4 8,34 lgГ - 2 , 059- Ю- з? + 0, 178- 10-«Г2 — 11,96
для конверсии метана водяным паром по уравнению:
,2217,5
\gKp = —т~ 4- 0,297 lg Т 4- 0,3525. Ю"3Г 4 0,0508- 10-0Г — 3,26
В промышленных условиях на применяемых катализаторах па ро-углекислотная конверсия протекает практически до равновесия. Это позволяет оценить состав полученного газа по термодинамиче-
71
ским данным. Из табл. 32 .следует, что. степень превращения .метана (степень конверсии) при .постоянной температуре -снижается при по вышении давления. При температуре выше 1000 °С можно получить конвертированный газ с низким содержанием .метана даже .при 50 ат. Из приведенных данных видно также, что для рассчитанных отношений окислителей отношение f не всегда соответствует требуе мому для синтеза -метанола. Его значения определяются в первую очередь давлением и температурой процесса. Поэтому в промыш ленной практике соотношение реагирующих компонентов несколько
Та б л и ц а 32. Зависимость равновесного состава конвертированного газа при паро-углекислотной конверсии* (С02:СН4 — 0,2) от температуры и давления
(Данные М. А. Шполянского)
|
|
Степень превра |
Равновесный состав в пересчете |
|
|
|
|||||
Давле' |
Отноше |
щения, % |
|
на сухой газ, объеми. % |
|
|
|
||||
нце, |
ние |
|
|
|
|
|
|
|
Н2:СО |
|
i |
am |
Н20:СН4 |
СН4 |
со2 |
со. |
СО |
|
Н2 |
СН4 |
|
|
|
|
|
|
|
. |
л |
||||||
|
|
|
1 |
|
|
|
|
|
|
||
|
|
|
|
|
|
|
|
|
|
|
|
I |
2,0 |
|
Т е м п е р а.т у р а |
827 °С |
|
|
|
|
|||
99,63 |
106,5 |
6,30 |
21,81 |
|
71,82 |
0,08 |
3,29 |
|
2,33 |
||
!0 |
4,0. |
99,94 |
131,9 |
11,49 |
15,06 |
|
73,44 |
0,01 |
4,88 |
|
2,33 |
2,0 |
83,60 |
92,7 |
7,65 |
19,62 |
|
68,41 |
4,32 |
3,48 |
|
2,23 |
|
|
4,0 ' |
93,28 |
127,0 |
11,81 |
14,54 |
|
72,57 |
1,08 |
4,99 |
|
2,30 |
20 |
2,0 |
43,59 |
59,7 |
13,53 |
10,30 |
|
55,03 .. |
21,14 |
5,34 |
|
1,74 |
40 |
4,0 |
62,63 |
96,6 |
15,77 |
8,40 |
|
64,90 |
10,93 |
7,73 |
|
2., 03s |
2,0 |
53,99 |
65,8 |
10,68 |
14,55 |
|
59,09 |
15,68 |
4,06 |
|
1,92 |
|
50 |
4,0 |
73,46 |
— |
. 13,37 |
11,90 |
|
67,55 |
7,18 |
5,68 |
‘ |
2,14 |
2,0 |
49,42 |
60,8 |
11,21 |
13,61 |
|
57,08 |
18,09 |
4,19 |
1,85 |
||
|
4,0 • |
68,59 |
.97,3 |
13,73 |
11,26 |
|
66,14 |
8,86 |
5,87 |
|
2,10 |
1 |
2,0 |
99,96 |
Т е м п е р а т у р а |
927°С |
|
|
|
|
|||
102,1 |
5,24 |
23,20 |
|
71,56 |
Следы |
3,08 |
|
2,33 |
|||
10 |
4,0 |
99,99 |
124,4 |
10,03 |
16,96 |
|
73,01 |
Следы |
4,30 |
|
2,33 |
2,0 |
96,44 |
99,1 |
5,49 |
22,78 |
|
70,87 |
0,86 |
3,11 |
' 2,31 |
||
20 |
4,0 |
99,29 |
123,9 |
10,07 |
16,89 |
|
72,88 |
0,16 |
4,31 |
|
2,33 |
2,0 |
89,49 |
93,0 |
6,01 |
21,92 |
|
69,39 |
2,68 |
3,17 |
|
2,27 |
|
40 |
4,0 |
97,37 |
121,9. |
10,20 |
16,68 |
|
72,52 |
0,60 |
4,35 |
|
2,32 |
2,0 |
76,95 |
82,0 |
7,04 |
20,20 |
|
66,28 |
6,48 |
3,28 |
.2, 17 |
||
50 |
4,0 |
91,68 |
116,1 |
10,59 |
16,03. |
71,39 |
1,98 |
4,45 |
|
2,28 |
|
2,0 |
72,11 |
76,7 |
7,48 |
19,47 |
|
64,90 |
8,16 |
3,33 |
|
2,13 |
|
|
4,0 |
88,61 |
112,9 |
10,86 |
15,68 |
|
70,74 |
2,78 |
4,51 |
|
2,25 |
1 |
2,0 |
99,99 |
Т е м п е р а т у р а |
1027 °С |
|
|
|
|
|||
98,7 |
4,46 |
24,20 |
|
71,34 |
0,00 |
2,95 |
|
2,33 |
|||
|
4,0 |
|
|
||||||||
10 |
99,99 |
118,9 |
8,86 |
18,49 |
|
72,66 |
0,00 |
3,93 |
|
2,33- |
|
2,0 |
|
|
|||||||||
|
99,33 |
98,1 |
4,50 |
24,13 |
|
71,21 |
0,16 |
2,95 |
|
2,33 |
|
20 |
4,0 |
99,87 |
118,8 |
8,87 |
18,47 |
|
72,63 |
0,03 |
3,93 |
|
2,33 |
2,0 |
97,61 |
96,5 |
4,62 |
23,94 |
|
70.84 |
0,61 |
2,96 |
|
2,32 |
|
40 |
4,0 |
99,50 |
118,9 |
8,90 |
18,43 |
|
72,56 |
0,11 |
3,94 |
|
2,33 |
2,0 |
92,09 |
91,8 |
4,98 |
23,33 |
|
69,69 |
2,00 |
2,99 |
|
2,29 |
|
50 |
4,0 |
98,12 |
117,0 |
8,98 |
18,29 |
|
72,30 |
0,43 |
3,95 |
|
2,32 |
2,0 |
98,14 |
89,2 |
5,18 |
22,99 |
|
69,03 |
2,80 |
3,00 |
|
2,27 |
|
|
4,0 |
97,17 |
116,1 |
9,04 |
18,18 |
|
72,12 |
0,66 |
3,97 |
|
2,3? |
72
отличается от расчетного. Например, при 20 ат и температуре кон версии около 860—870 °С соотношение компонентов следующее:
СН4:Н20:С02 = 1:3,3:0,24
.При промышленном осуществлении процесса следует учитывать термодинамические факторы, т. е. что паро-углекислотная конвер сия— процесс эндотермический и требует подвода тепла.
При добавлении «кислорода реакция протекает с выделением .теп ла, что позволяет осуществить процесс конверсии автотермично. Степень паро-углекислотной конверсии метана с добавлением кис лорода в аналогичных сравнимых условиях несколько выше, чем при паро-углекислотной конверсии. Однако заметно увеличивается содержание окислов углерода в конвертированном газе, что в ко нечном итоге приводит к снижению значения /, а при температура* выше 900 °С и отношения Н2:СО до значений .ниже 2. Поэтому не обходимо регулирование состава газа перед подачей его на синтез метанола, например очисткой от двуокиси углерода, а в отдельных случаях —г изменение соотношения окислителей и технологического режима конверсии. Равновесный состав газовой смеси при конвер сии метана смесью водяного пара, кислорода и двуокиси углерода при разных режимах приведен в табл. 33.
|
Т абл и ц а 33. |
Зависимость равновесного состава газовой смеси |
|
|||||
при конверсии метана смесью водяного пара, кислородай двуокиси углерода |
||||||||
при !соотношении СН4:Н5,0:02:С02 = |
1:0,7:0, 6:0,3 от температуры и давления1 |
|||||||
|
Степень превращения, |
Равновесный состав в пересчете на’ сухой газ, |
|
|
||||
Давле |
|
% |
|
объемн. % |
сн4- |
Н2:СО |
f |
|
ние, |
|
|
|
|
|
|||
am |
СН4 |
СОо |
со2 |
со |
Но |
|
|
|
|
|
|
Тем пе р а т у р а |
827 °С |
|
|
|
|
1 . |
99,85 |
7,96 |
11,95 |
28,94 |
59,06 |
0,05 |
2,04 |
1,15 |
10 |
91,18 |
10,73 |
13,84 |
27,34 |
55,82 |
3,00 |
2,04 |
1,04 |
20 |
81,58 |
13,77 |
16,30 |
25,26 |
51,58 |
6,86 |
2,04 |
0,85 |
40 |
70,52 |
17,25 |
19,79 |
22,31 |
45,56 |
12,34 |
2,04 |
0,61 |
|
|
|
Т ем пе р а т у р а |
927 °С |
|
|
|
|
1 |
99,98 |
2,54 |
10,41 |
31,18 |
58,40 |
0,005 |
1,87 |
1,15 |
10 |
98,43 |
3,01 |
10,71 |
30,95 |
57,83 |
0,51 |
1,86 |
1,13 |
20 |
94,90 |
4,10 |
11,41 |
30,39 |
56,49 |
1,71 |
1,86 |
1,08 |
40 |
87,32 |
6,50 |
13,11 |
29,02 |
53,32 |
4,55 |
1,84 |
0,95 |
|
|
|
Темпе р а ту р а |
1027 °С |
|
|
|
|
10 |
99,73 |
-1 ,5 5 |
9,25 |
32,92 |
57,74 |
0,09 |
1,75 |
1,15 |
20 |
98,96 |
—1,32 |
9,38 |
32,82 |
57,46 |
0,34 |
1,75 |
1,14 |
40 |
96,41 |
—0,57 |
9,86 |
32,47 |
56,47 |
1,20 |
1.74 |
1,10 |
В последние годы получила развитие высокотемпературная кон версия углеводородных газов кислородом при 1300—1500 °С. Этот процесс представляет собой неполное -сжигание метана и его гомо
логов в атмосфере кислорода. Преимуществом высокотемператур ной конверсии является то, что отпадает необходимость в очистке поступающего на конверсию газа от соединений серы (некатали- •пический процесс) и возможность проведения его с высокой сте пенью превращения при высоких давлениях. Недостатком процесса является выделение свободного углерода по реакции:
СН4 -----►С -f- 2Нг — 19,9 ккал
Эта реакция может протекать и при каталитической конверсии, но количество выделяющегося углерода не так велико, Специаль ными исследованиями установлено, что образование свободного углерода можно уменьшить, проводя конверсию с избытком водя ного пара или двуокиси углерода. Это широко используют в про мышленной практике, регулируя соотношение окислителей.
Из всего изложенного следует, что непосредственно для синтеза метанола может быть использован только газ, получающийся па ро-углекислотной конверсией при атмосферном пли повышенном давлении, так как он имеет значение 2. При конверсии с исполь зованием кислорода (кроме высокотемпературной) отношение Н2: СО в конвертированном газе достаточное для проведения син теза, но недостаточно велико значение f. Для использования этого газа в производстве метанола приходится удалять избыточное коли чество двуокиси углерода;.При высокотемпературной конверсии не достаточны отношение Н2: СО и /, т. е. без дополнительного регули рования состава газ не может быть использован для синтеза мета нола.
Скорость взаимодействия метана и его гомологов с водяным паром и двуокисью углерода в гомогенных условиях при темпера турах ниже 900 °С незначительна, поэтому паро-,углекислотиую конверсию (с кислородом и без него) проводят на катализаторах. Наибольшее распространение получили никелевые катализаторы на различных носителях с содержанием от 4 до 20% Ni. В качест ве промоторов используют окислы алюминия, магния, хрома, тория и некоторых других металлов. В Советском Союзе для конверсии используют катализаторы ГИАП-3 и ГИАП-5, разработанные в Го сударственном институте азотной промышленности2»^
Промышленные схемы получения технологического газа и их аппаратурное оформление весьма разнообразны. Наибольшее рас пространение получил процесс паро-углекислотной конверсии при родного газа. Он осуществляется в трубчатых печах при атмосфер ном или повышенном давлении. Ввиду эндотермичности реакций для поддержания требуемой температуры контактирования необхо дим подвод тепла со стороны. Обычно он осуществляется сжигани ем в межтрубном пространстве любого горючего газа. Для этой цели могут быть попользованы все отходы производства метанола. Пар для конверсии получают непосредственно на установке за счет тепла обогревающего и конвертируемого .газов. Двуокись углерода подводится из смежных производств или выделяется из топочных газов моноэтаноламином и другими способами,
74
Наиболее современная технологическая схема паро-углекислот ной конверсии природного газа, как и любая схема каталитической конверсии, включает очистку .природного газа от соединений серы, утилизацию тепла конвертированных газов и конверсию (техноло гические режимы процесса и принципиальная схема рассмотрены ниже, стр. 85—87, рис. 27). Полученный газ не требуется очищать от двуокиси углерода, и он направляется непосредственно на ком примирование. Материальный баланс паро-углекислотной конверсии природного газа -при соотношении СН4: С02: Н20 = 1:0,216:1,48 приведен в табл. 34 (для обогрева трубного пространства печи дан ной конструкции расходуется 2220 м3/ч природного газа).
Т а б л и ц а 34. Материальный баланс паро-углекислотнои конверсии природного газа
|
|
Природный газ |
Двуокись |
|
Конвертированный газ |
|
||
Компоненты |
|
|
влажный |
в пересчете на «.сухой» |
||||
|
|
углерода |
||||||
газовой |
лх3 |
% |
и водяной |
|
|
|
|
|
смеси |
пар, |
Л{3 |
% |
д<3 |
% |
|||
|
|
|
|
Л|3 |
||||
с н < . |
913,8 |
91,38 |
—— |
84,0 |
1,80 |
84,0 |
2 , 1 0 |
|
^гНв . . . |
34,0 |
3,40 |
— |
— |
— |
— |
— |
|
С3 н8 |
. . |
16,2 |
1,62 |
— |
— |
— |
— |
— |
С4 Н1 0 |
|
2 , 0 |
0 , 2 0 |
— |
— |
— |
— |
— |
|
|
|
|
|
|
|||
с о 2 . |
15,0 |
1,50 |
208,0 |
192,0 |
4,13 |
192,0 |
4,80 |
|
с о |
|
— |
— |
— |
984,0 |
21,19 |
984,0 |
24,65 |
н 2 . |
2 , 0 |
0 , 2 0 |
— |
2720,0 |
58,47 |
2720,0 |
6 8 , 0 2 |
|
N2 + |
Аг . . |
17,0 |
1,70 |
— |
17,0 |
0,37 |
17,0 |
0,43 |
н2о . . . . |
— |
— |
1535,0 |
653,0 |
14,04 |
— |
— |
|
|
|
|
|
|
|
|
|
|
В с е г о . |
1 0 0 0 , 0 |
| 1 0 0 , 0 0 |
| 1743,0 | |
4650,0 |
| 1 0 0 , 0 0 |
| 3997,0 | |
1 0 0 , 0 0 |
Менее -прогрессивная, но применяемая еще в настоящее время технологическая схема паро-кислородной конверсии природного газа с дозированием двуокиси углерода приведена на рис. 22. При родный газ при давлении 1,8—2,2 ат подается в сатурационную башню 1. Здесь он .насыщается парами воды до объемного отноше ния пар:газ=0,16—0,70 путем контакта с конденсатом или химиче ски очищенной водой, предварительно подогретой в теплообменни ке 6. Затем паро-газовая смесь поступает в межтрубное пространст во .газового теплообменника 2 и подогревается за счет тепла кон вертированного газа до ~500°С . Перед теплообменником вводят дозированное количество двуокиси углерода и водяного пара. В смеситель 4 вводят подогретую паро-газовую смесь и кислород (отношение кислород: газ зависит от состава газовой смеси, для природного газа оно колеблется в пределах 0,6—1,0). Скорость вво да обоих потоков высокая, но парогазовую смесь подают с боль
75
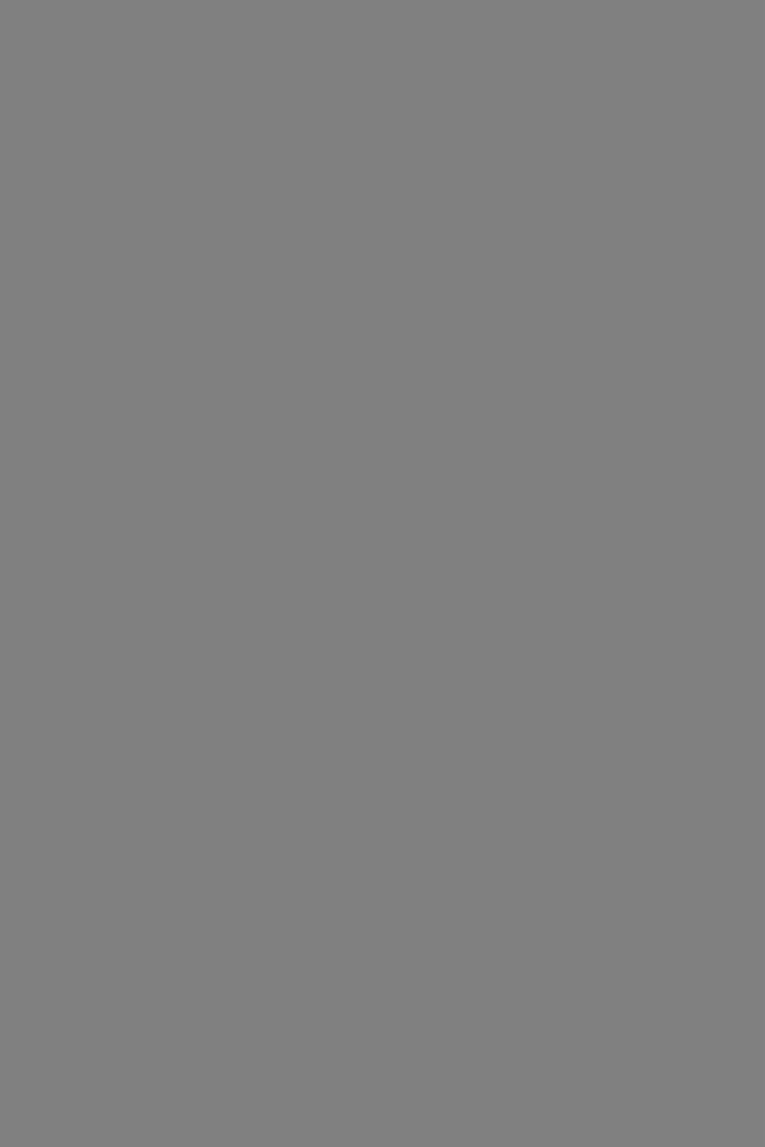
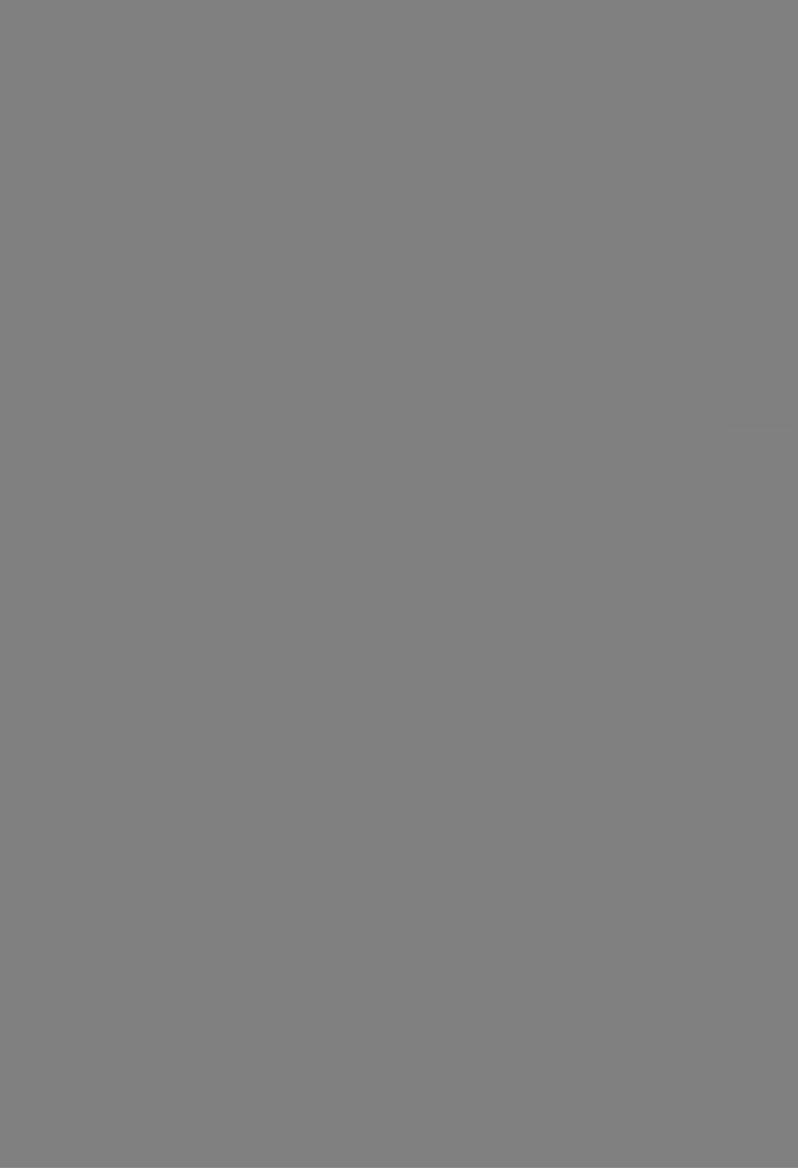

образовавшийся метанол, что достигается охлаждением газовой смеси, которая затем компримируется до давления синтеза и воз вращается в процесс.
В Советском Союзе при синтезе метанола на цинк-хромовом ка тализаторе (таблетки 5 x 5 мм и 9 x 9 мм) при 300 ат получили
распространение агрегаты с несовмещенной и совмещенной колон ной синтеза. Циркуляция газа осуществляется турбоциркуляционными машинами.
Принципиальная схема агрегата синтеза с выносным теплооб менником (или агрегата синтеза с несовмещенной насадкой колон ны) приведена на рис. 24. Из отделения компрессии газ при 320 ai
Рис. 24. Схема агрегата с несовмещенной колонной синтеза и вынос ным теплообменником:
1. 9 и 10 — сепараторы; 2 и 3 — фильтры; |
4 — компрессор; 5 — колонна; |
6 — теплообменник; 7 — электроподогреватель; |
8 — холодильник-конденсатор; |
11 — сборник. |
|
поступает в сепаратор-влагоотделитель 1, освобождается от влаги, сконденсировавшейся в результате сжатия газа, и направляется в угольный фильтр 2, где очищается от карбонилов железа.
Присутствие в газе карбонилов железа, в основном пентакарбонила железа Fe(CO)5, обусловлено карбонильной коррозией углеродистой стали, которая при высоком давлении наиболее интенсивно протекает при 150—200 °С. Вероятно, карбонильная коррозия инициируется наличием в газе соединении серы, главным образом сероводорода, который, взаимодействуя с поверхностью трубопроводов, разрушает окисную пленку металла. Обычно в газе присутствует незначительное количество карбонилов железа (до 3—4 мг/мг), однако, попадая вместе с газом на катализатор, они разлагаются при высоких температурах с выделением мел кодисперсного элементарного железа, которое является очень активным катали5затором реакции образования метана. Это может приводить не только к увеличе нию расхода сырья, но и к резкому возрастанию температуры в зоне катализа со всеми вытекающими отсюда последствиями. Карбонильную коррозию можно значительно снизить очисткой исходного газа от соединений серы, а также изго товлением горячих участков труб из хромистой стали, футеровкой их внутренней поверхности медыо пли нержавеющей сталью.
79
Для поглощения карбонилов железа используют активированные угли раз личных марок (АР-З, СГ-1 и др.). На некоторых марках угля происходит также частичная очистка газа от соединений серы.
Очищенный газ поступает в масляный фильтр 3 (необходимость этого аппарата обусловлена использованием поршневых машин), в который подается также циркуляционный газ из компрессора 4. Поток смешанного газа из масляного фильтра разделяется на две части. Одна из них (до 80—85%) направляется на обдув колонны синтеза 5 для снижения температуры корпуса и предотвращения водородной и карбонильной коррозии. За счет теплообмена с горя чими частями колонны температура газового потока повышается с 30—35 до 60—70 °С. Затем эта часть газа подогревается в тепло обменнике 6 горячими реакционными газами до 300—350 °С и по дается в колонну 5 (в описанной схеме используют колонны с раз личными насадками: полочного или так называемого шахтного ти па). Электроподогреватель 7 предназначен для подогрева газа в пе риод восстановления катализатора, при пуске системы или нару шении температурного режима в колонне синтеза.
Другая часть газа после фильтра 3 с температурой 30—35 °С поступает в колонну между слоями катализатора (так называемый холодный байпас). Это необходимо для поддержания температуры катализатора' ~ 3 6 0 —370°С, так как за счет тепла реакции обра зования метанола температура газа после прохождения каждой полки или слоя катализатора в шахтной насадке повышается. Тем пературный режим по высоте колонны приведен на стр. 99 (рис. 31). Подача газк по холодным байпасам зависит от активности катали затора и технологических параметров, определяющих скорость об разования метанола, а таюке от условий теплообмена; он колеблет ся в пределах 10—20% от общего расхода газа.
Пройдя колонну синтеза 5, реакционные газы с температурой 380—400 °С охлаждаются в теплообменнике 6 до 120— 140 °С и на правляются в холодильникжонденсатор 8. В этом аппарате при охлаждении газа до 30—40 °С происходит конденсация паров мета нола и воды, а также растворение в конденсате (метаноле-сырце) продуктов пббочных реакций и некоторого количества компонентов исходной газовой смеси. Газовая смесь и метанол-сырец разделя ются в сепараторе 10. Метанол-сырец передавливается в промежу точный сборник И (давление в нем 5—16 ат)\ откуда он направ ляется на ректификацию. Отделенный газ проходит через дополни тельный сепаратор 9 для выделения капель метанола, комприми руется циркуляционным компрессором до давления синтеза и воз вращается в аппарат 3 на смешение с исходным газом. Так как при циркуляции в системе накапливаются инертные компоненты (метан, азот, аргон)-, для поддержания заданного отношения Н2:СО часть рециркулирующего газа после сепаратора 9 выводят из системы (так называемый продувочный газ). Его объединяют с газами, вы деляющимися из метанола-сырца при снижении давления в сборни ке 11 (танковые газы), и направляют на переработку в смежные
во