
книги / Эксплуатация, техническое обслуживание и ремонт горных машин калийных рудников
..pdfПо основным признакам шахтные самоходные вагоны принято классифицировать:
I.По грузоподъемности:
–легкие (до 5 т);
–средние (от 5 до 15 т);
–тяжелые (свыше 15 т).
II.По конструкции ходовой части: 1. По количеству и назначению осей:
–двухосные и многоосные;
–с одной или двумя ведущими осями;
–с одной или двумя управляемыми осями. 2. По типу подвески ходовой части:
–с жесткой подвеской;
–с балансирной подвеской.
III.По конструкции разгрузочной части:
–со стационарной погрузочной частью;
–с подъемной разгрузочной частью. IV. По принципу подвода энергии:
–независимого типа (дизельные, дизель-электрические и аккумуляторные);
–зависимого типа (троллейные, кабельные и троллейнокабельные);
–комбинированного типа (троллейно-аккумуляторные).
В настоящее время машиностроительными предприятиями выпускаются двухосные и трехосные вагоны грузоподъемностью 15–30 тонн. На калийных рудниках России и стран Таможенного союза наибольшее распространение получили вагоны 10ВС-15 и ВС-30 производства ООО «УГМК Рудгормаш» (г. Воронеж).
Вагон 10ВС-15 предназначен для транспортирования горной массы в шахтах, опасных по газу (метану) и угольной пыли; температуре окружающей среды ± 35 °С и относительной влажности до 98 %.
Технические характеристики самоходного вагона 10ВС-15 представлены в табл. 5.6.
131
|
|
|
Таблица 5.6 |
|
|
Технические характеристики самоходного |
|
|
|
|
вагона 10ВС-15 |
|
|
|
|
|
|
|
|
№ |
Наименование параметров |
Значение |
|
Единицы |
п/п |
|
измерения |
||
1 |
Грузоподъемность, не более |
15 |
|
т |
2 |
Масса для калийных рудников |
16,5 |
|
т |
3 |
Емкость кузова базовой модели |
8,6 |
|
м3 |
4 |
Максимальная скорость движения |
8 |
|
км/ч |
по горизонтальному пути без груза |
|
|||
|
Наибольшийуклонпути, преодолеваемый |
|
|
|
5 |
сгрузомнаучасткедлинойнеболее40 м, при |
15 |
|
град |
|
коэффициентесцепленияколесспочвой>0,6 |
|
|
|
6 |
Вместимость кабельного барабана |
200 |
|
м |
7 |
Минимальный радиус поворота |
8500 |
|
мм |
|
по наружному габариту, не более |
|
|
|
8 |
Дорожный просвет, не менее |
320 |
|
мм |
9 |
Установочная мощность |
127 |
|
кВт |
10 |
Характеристика тока |
Переменный, |
Гц |
|
50 |
|
|||
|
|
|
|
|
11 |
Напряжение |
660/1140 |
|
В |
|
Габаритные размеры: |
|
|
|
12 |
– длина |
8200 |
|
мм |
– ширина |
2500 |
|
||
|
– высота |
1750 |
|
|
13 |
Минимальная высота загрузки |
1125 |
|
мм |
Вагон шахтный самоходный (рис. 5.11) представляет собой бункер-кузов 1 со встроенным в его днище конвейером 2, кузов шарнирно установлен на шасси с пневмоколесным ходом 3.
Два телескопических гидроцилиндра обеспечивают изменение высоты подъема кузова в пределах 430…1445 мм. Кузов 1 состоит из правого 4, левого 5 и заднего 6 бортов, жестко связанных с рамой кузова.
Привод на колеса 3 осуществляется от двух ходовых двигателей 7, установленных на заднем подрамнике рамы кузова, каждый из которых приводит в движение два колеса: один – пару левого борта, второй – правого. Вращение на колесо
132
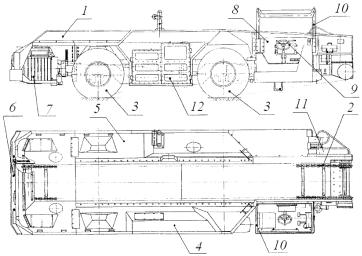
передается через цилиндрический редуктор, прифланцованный к двигателю, карданную передачу, коническую пару шестерен (угловой редуктор) и одноступенчатый планетарный редуктор, встроенный в колесо.
Рис. 5.11. Шахтный самоходный вагон 10ВС-15
Самоходное шасси вагона состоит из рамы хода, переднего и заднего мостов и подрамника, на котором справа установлена кабина 8 с рулевым управлением 9 и силовой рамой 10, а слева – привод конвейера и маслостанции 11. Задний мост крепится к раме жестко, передний – балансирно.
Питание вагона электроэнергией осуществляется от сети переменного тока напряжением 660 или 1140 В. Электрооборудование выполнено во взрывозащищенном исполнении с видом взрывозащиты «Взрывонепроницаемая оболочка» и «Искробезопасная цепь» и заключено в магнитную станцию 12.
Кинематическая схема шахтного самоходного вагона 10ВС-15 приведена на рис. 5.12.
133
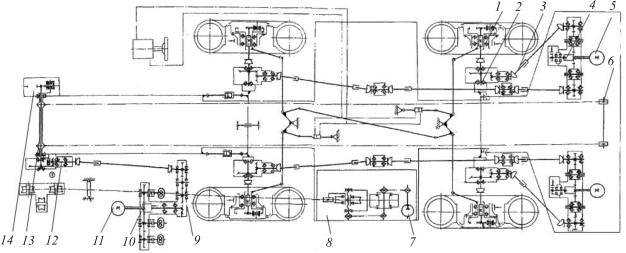
134
Рис. 5.12. Кинематическая схема вагона 10ВС-15: 1 – колесный планетарный редуктор; 2 – угловой редуктор; 3 – карданная передача; 4 – редуктор хода; 5 – электродвигатель хода; 6 – вал натяжной; 7 – мотор-насос; 8 – кабельный барабан; 9 –промежуточный редуктор; 10 – редуктор маслостанции; 11 – электродвигатель конвейера; 12 – конический редуктор; 13 – вал приводной; 14 – планетарный редуктор
Донный скребковый конвейер ШСВ предназначен для равномерного размещения руды в кузове и последующей ее выгрузке, состоит из приводного 13 и натяжного 6 валов и скребковой цепи. Привод конвейера и маслостанции является совмещенным и установлен на раме ходовой части, состоит из двухскоростного электродвигателя 11, редуктора 10, маслонасосов и промежуточного редуктора 6 с карданным валом.
Вагон оснащен двумя приводами хода, расположенными вдоль правого и левого бортов кузова. Каждый привод включает трехскоростной электродвигатель 5, прифланцованный к нему редуктор 4, карданную передачу 3 и стояночный тормоз.
Используемый тип привода обеспечивает равенство крутящих моментов, подводимых к ведущим колесам обоих бортов при движении по прямой, и определенное перераспределение крутящих моментов между бортами при движении по криволинейной траектории. Это перераспределение таково, что момент, подводимый к колесам внутреннего борта, всегда больше момента, подводимого к колесам наружного борта, причем неравенство усиливается при уменьшении радиуса поворота.
Ходовая часть представляет собой четырехколесный движитель со всеми приводными управляемыми колесами. Ходовая часть состоит из рамы, переднего и заднего мостов. Крепление заднего моста – жесткое. Балансирная подвеска переднего моста позволяет колесам моста при наезде на препятствие перемещаться вверх или вниз от среднего положения.
Вагон может работать в комплексе с комбайнами типа «Урал-10Р», «Урал-20Р», погрузочными машинами и бункерамиперегружателями с высотой погрузки от 1,2 м и более, разгружаться в рельсовые вагонетки, на конвейеры, в рудоспуски и другие приемные устройства высотой до 1,4 м. Длина доставки самоходным вагоном составляет до 400 м при условии установки запитывающего трансформатора посередине трассы.
Минимальное сечение выработки, в которой может эффективно эксплуатироваться вагон – 3×2,1 м; угол наклона трассы до 15° при длине уклона не более 40 м.
135
5.3.3. Техническое обслуживание и ремонт самоходных вагонов
Для ШСВ устанавливаются следующие виды технического обслуживания:
–ежесменное техническое обслуживание (ЕО);
–первое техническое обслуживание (ТО1) проводится через 18 часов работы (ремонтная смена);
–второе техническое обслуживание (ТО2) проводится через 300 часов работы.
1. При ежесменном техническом обслуживании произво-
дится внешний осмотр машины, в том числе проверяется: состояние крепежа, отсутствие подтекания масла в местах соединений, уплотнений узлов и деталей гидросистемы, редукторов. Узлы, детали должны быть надежно закреплены, подтекание масла в местах соединений и уплотнений узлов и деталей гидросистемы не допускается.
Требуется проверить работу ходового и стояночного тормоза, убедиться в отсутствии самопроизвольного движения вагона на уклоне. Тормозной путь вагона на максимальной скорости без груза при движении по ровному горизонтальному участку пути не должен превышать 2,5 м.
Перед началом работы проверяется действие звукового сигнала, наличие света передних и задних фар, состояние оболочек электрооборудования, питающего кабеля, исправность заземляющей жилы кабеля пункта подключения вагона, работу схемы цепей управления всеми электродвигателями. Запрещается эксплуатация при отсутствии звукового сигнала и неработающих фарах, нарушениях параметров взрывозащиты, а также повреждении оболочек кабеля и нечетком срабатывании переключателей.
2. Первое техническое обслуживание требует проверки уровня масла в редукторах и наличие смазки в узлах. Уровень масла в редукторах должен быть по уровню контрольной пробки.
136
Наличие консистентной смазки в узле проверяется путем шприцовки до появления смазки в зазорах. Проверяется отсутствие замасливания накладок тормозных колодок. Дальнейшее обслуживание направлено на то, чтобы привести параметры работы вагона в соответствие руководству по эксплуатации:
–давление в шинах должно быть 700 ± 25 кПа;
–максимальный ход штоков гидроцилиндров подъема кузова не должен превышать 45 мм;
–радиальный зазор между накладками колодок в их средней части и тормозным барабаном 0,3–0,5 мм.
Перед передачей в эксплуатацию проверяется: наличие свободного хода педалей управления тормоза и включения ходовых двигателей; отсутствие люфта шаровых пальцев в наконечниках продольных и поперечных тяг; натяжение втулочно-роликовых цепей привода кабельного барабана и кабелеукладчика – прогиб цепей не должен превышать 15–18 мм; состояние уплотнений вводимых кабелей; зазоры между фланцами крышек и корпусов магнитной станции и пульта управления; общее сопротивление изоляции электрооборудования; наличие давления в гидросистемах кабельного барабана, рулевого управления, рабочих тормозов; зарядку пневмогидроаккумулятора; уровень масла в маслобаке, при необходимости производится дозаправка.
3. При втором техническом обслуживании, включающем в себя все операции ТО1, также производят проверку осевой игры конических роликовых подшипников; затяжку болтовых соединений фланцев и креплений; положение скребков (при необходимости устраняется их перекос). В рамках ТО2 разбирается токосъемник и проверяется величина износа контактных колец, от-
сутствие грязи и стружки, масла на изоляционных кольцах. В случае необходимости проводится промывка. Отверстия контактных колец заполняются свежей смазкой. Осмотр электроаппаратуры производится с вскрытием выводных коробок двигателей, крышек магнитной станции и пульта управления.
137
Особое внимание уделяется гидросистеме. При обслуживании требуется разобрать фильтр и заменить фильтроэлемент. Слить масло из гидросистемы и маслобака, вскрыть смотровой люк, произвести очистку внутренней поверхности маслобака от ржавчины
игрязи, затем промыть керосином. В случае ненормальной работы какого-либо из гидроагрегатов (течь масла, отсутствие давления
ит.д.) произвести его демонтаж и ремонт или замену.
138
6. ОБОРУДОВАНИЕ ДЛЯ КРЕПЛЕНИЯ КРОВЛИ ВЫРАБОТОК
6.1. Технология крепления кровли выработок на калийных рудниках
Выработки калийных рудников достаточно устойчивые для эффективного применения анкерной крепи в качестве средств крепления кровли. Анкерная крепь – это пространственная система стержней (анкеров), закрепленных в соляном массиве, вмещающем горную выработку. Размещенные в специально пробуренных шпурах и закрепленные там различными способами анкеры скрепляют между собой отдельные слои и структурные блоки соляных пород, препятствуют свободному их деформированию и тем самым повышают устойчивость горного массива. Таким образом, анкерная крепь обеспечивает возможность использования несущей способности массива, снижения материалоемкости и стоимости применяемых в сочетании с ней крепей, а в отдельных случаях исключает надобность в дополнительном креплении.
Крепление выработок калийных рудников – сплошное. Осуществляется винтовыми (горно-капитальные выработки панельного и главного направления) или клинораспорными анкерами (блоковые, транспортные, выемочные, вентиляционные штреки, блоковые разрезные штреки, сбойки блоковых штреков) стандартной длины L = 1,5 м с параметрами, подобранными по горногеологическим характеристикам соответствующих пластов кровли выработок (рис. 6.1).
Креплению подлежат все сопряжения выработок. Места геологических нарушений, сопряжения выработок и районы нарушения паспортов проходки подлежат немедленному креплению после их образования. Отставание крепи от забоя при проходке подготовительных выработок не должно превышать 200 м по длине и по времени – не более одного месяца. При необходимости оставления тупиковых выработок вся выработка должна быть закреплена до
139
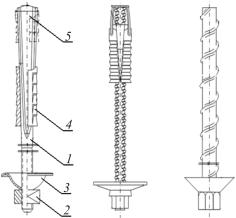
отгона комбайна из нее. Технология возведения, конструкция крепи, порядок установки описываются в технологических регламентах по охране и креплению горных выработок предприятия.
а |
б |
в |
Рис. 6.1. Конструкцияанкернойкрепи: а– анкерсразрезнымраспорным замкомКАС; б– клинораспорныйанкерКРА-16; в– винтовойанкер; 1 – стержень; 2 – гайка; 3 – опорнаяшайба; 4 – разрезнаямуфта; 5 – клин
Порядок установки анкерной крепи следующий:
1.Проводится визуальный осмотр предполагаемого места установки анкера.
2.Проверяется состояние кровли выработки методом простукивания «ширмой», ей же производится оборка заколов из безопасногоместа. Проводитсябурениешпуровдляустановкианкеров.
3.Проводится повторная проверка состояния кровли выработки с использованием «ширмы».
4.Устанавливается анкер:
–винтовой анкер при помощи бурильной машины ввинчивается в шпур;
–клинораспорный анкер КАС с помощью установочной трубы вводится в пробуренный шпур нажатием, затем ударами
140