
книги / Эксплуатация, техническое обслуживание и ремонт горных машин калийных рудников
..pdfДля того чтобы не смешивать детали различных групп годности, их маркируют краской: годные – белой; подлежащие ремонту – зеленой; негодные – красной.
Контроль деталей осуществляют работники отдела технического контроля. Детали, имеющие большую массу и габариты, контролируются на местах ремонта машин.
Контрольдеталейможнопроизводитьследующимиспособами.
1.Наружным осмотром (простукивание, ослушивание) устанавливают трещины, обломы, ослабление заклепок.
2.Промером универсальными (штангенциркулями, микрометрами и др.) и специальными (калибрами) инструментами – определяют овальность, конусность, допускаемые размеры.
3.Специальные методы дефектоскопии – ультразвуковой, маг- нитно-акустический, рентгеновский, люминесцентный, электромагнитный– определяютналичиемелкихтрещин, раковинидр.
4.Гидравлическими испытаниями на стендах проверяют герметичность блоков цилиндров, радиаторов, топливных баков и т.д.
5.Корпусные детали из стального литья бракуются (окончательно) при обнаружении сквозных трещин, изгибов, изломов, нарушающих прочность и влияющих на монтажные размеры.
6.Оси и валы при наличии трещин, изломов или остаточных деформаций списываются.
7.Зубчатые колеса не подлежат восстановлению, если имеются поломанные зубья, трещины, питинг на большом числе зубьев, отслоениянарабочейсторонезубьевцементированногослоя.
8.Шариковые и роликовые подшипники бракуются при наличии трещин на кольцах, бороздчатых выработок, сыпи, чешуйчатости и отслаивании на поверхности беговых дорожек колец, шариков или роликов, при отсутствии части шариков (роликов), при проявлении на поверхности металла цветов побежалости, а также при наличии рабочего зазора, превышающего допустимый. Узлы и детали электрооборудования бракуются, если не отвечают требованиям взрывобезопасности. Электродвигатели независимо
31
от состояния отправляются в электроцех, где проходят осмотр и определяют их пригодность.
9. Уплотнения из кожи, резины, прокладки из неметаллов повторно не используются. Болты, гайки, шпильки, бракуются при срыве (износе) более двух ниток резьбы, потере товарного вида. Деформированные шпонки всех видов бракуются и повторно не используются.
1.4. Хранение и транспортирование горных машин
Изнашивание горного оборудования происходит не только во времяработы, ноиприегохранении, атакжетранспортировке.
Хранение машин представляет комплекс организационных и технологических мероприятий, защищающих машины и их агрегаты, а также электротехническое оборудование от коррозии, деформации, солнечной радиации и других разрушающих воздействий.
Хранение горных машин и их сборочных единиц (деталей, узлов) производится в соответствии с руководством по эксплуатации в закрытом помещении или под навесом в условиях, исключающих воздействие атмосферных осадков, кислотных и других агрессивных сред, вызывающих коррозию. Правильность хранения периодически проверяют, при хранении на открытом воздухе – не реже одного раза в месяц, в закрытых помещениях – через два месяца и более.
Запасные части горных машин и оборудования должны храниться в закрытом неотапливаемом помещении на стеллажах или в таре и должны быть покрыты предохранительной смазкой.
Специальных условий хранения требуют следующие комплектующие:
– шины хранятся в закрытых складских помещениях в вертикальном положении на стеллажах или ровном полу при температуре от минус 30 до плюс 35 °С и относительной влажности
50…80 %;
32
–электродвигатели хранятся в закрытых проветриваемых помещениях при температуре не ниже плюс 5 °С и относительной влажности не более 80 %;
–рукава высокого давления гидросистемы хранятся в расправленном виде при температуре от 0 до +25 °С на расстоянии не менее 1 м от теплоизлучающих приборов. Не допускается хранить рукава под давлением, вблизи искусственных источников света, выделяющих ультрафиолетовые лучи.
Транспортирование горных машин и оборудования осуществляется с целью доставки на предприятие, первичный монтаж или перенос на новое рабочее место, перемещение на обслуживание и ремонт в специализированные цеха и т.д. Транспортирование машины осуществляется различными способами в зависимости от расстояния, местонахождения и технического состояния машины: автомобильным и железнодорожным транспортом, своим ходом, подъемными установками и буксировкой.
Транспортирование горных машин своим ходом допускается только на территории рудника (к месту работы). В особом порядке запрещается передвижение машины по дорогам общего пользования.
При буксировании особо важно соблюдать допустимую скорость движения. Например, для бункера-перегружателя она составляет всего 5 км/ч. Буксирование осуществляется только на жесткой сцепке. Следует не забывать снять доставляемую машину со стояночного тормоза.
Подъем и погрузка горных машин, их деталей и узлов с помощью подъемного механизма в расупакованном виде производится согласно схеме строповки, указанной в руководстве по эксплуатации. Перед такелажными работами следует проверить соответствие грузоподъемности крана и массы узлов машины.
Для удобства монтажа рекомендуется доставлять и размещать элементы машин согласно схеме их сборки, в обратной последовательности. При транспортировании должны быть приняты все меры, исключающие повреждение сборочных еди-
33
ниц и деталей: надежная фиксация, применение соответствующей упаковки, бережное перемещение. При этом необходимо, чтобы трубы гидросистемы, присоединительные штуцеры, а также открытые полости редукторов были заглушены, как во время транспортирования, так и при монтаже. Все обработанные и неокрашенные поверхности должны быть покрыты густой смазкой. Сборочные единицы необходимо доставлять и размещать в монтажной камере таким образом, чтобы избежать лишних разворотов при монтаже.
1.5. Оснащение ремонтно-механического цеха горнодобывающего предприятия
Технология современного горного производства требует применения большого числа машин и механизмов, выполняющих самые различные функции. Для поддержания оборудования в работоспособном состоянии необходима достаточно развитая цепь ремонтных баз, обеспечивающая систематическое техническое обслуживание, текущие и капитальные ремонты оборудования.
Ремонтные базы предприятий располагают в выработках или на поверхности рудника для обслуживания только оборудования данного предприятия. К ремонтным базам горных предприятий относятся: подземные участковые кладовые и мастерские; подземные общерудничные ремонтные мастерские; поверхностные общерудничные ремонтные мастерские; передвижные ремонтные мастерские.
При необходимости обслуживания группы предприятий организуются центральные электромеханические мастерские и рудоремонтные заводы.
Ремонтно-механические цеха организуются в соответствии с правилами безопасности и проектируются для ожидаемого количества техники в поступлении на ремонт, планируемого среднегодового объема работ по добыче, структуре существующей ремонтной базы и перспективе ее развития. Ремонтные цеха гото-
34

вятся для выполнения полного перечня операций обслуживания и ремонта горных машин. Для этого они оборудуются всем требуемым для этого слесарным инструментом и станками: сверлильными, токарными, фрезерными и т.д.
Расчет ремонтно-механического цеха рудника производится с учетом количества (N) и стоимости (Аобщ, руб) эксплуатируемого оборудования. Для выбора моечного оборудования должна быть известна масса машин Qм, кг.
Стоимость ремонта оборудования определяется по формуле
Aр = Aобщсba,
где с – коэффициент оплаты внеплановых работ, с = 1,4…1,7; b – коэффициент затрат на заработную плату производственных рабочих, b = 0,28…0,32; а – амортизационные отчисления, являющиеся переносом части стоимости основных фондов для возмещения износа оборудования, а = 0,09…0,11.
Исходя из стоимости ремонта эксплуатируемого оборудования, определяется штат рабочих и количество станков в цеху. Для этого рассчитывается имеющийся фонд рабочего времени:
Фрв = Aр ,
pkн
где р – стоимость одного часа работы слесаря 5-го разряда; kн – коэффициент начисления, для рудника kн = 6.
При данном фонде рабочего времени штат производственных рабочих должен содержать такое количество сотрудников, которое может выполнить данный объем работ:
Nпр = Фрв ,
αDр
где α – коэффициент выполнения нормы выработки, α = 1,15…1,20; Dр – годовой фонд рабочего времени одного рабочего
35

Dр = tkп (365 − В− П − О),
где t – продолжительность рабочей смены, ч; В – число выходных дней в году; П – число праздничных дней в году; О – число отпускных дней в году; kп – коэффициент потерь рабочего времени по болезни и другим уважительным причинам, kп = 0,97…0,98.
С учетом введения в штат персонала для проведения такелажных работ и инженерно-технических рабочих в объеме 18 %, общий штат рабочих составит:
Nобщ = 1,18Nпр.
Число требуемых производственных рабочих и общий штат рабочих округляется до большего целого значения.
Число моечных машин при этом
m |
= NQtм |
, |
|
м |
|
qDстkим |
|
|
|
|
где Q – масса промываемых деталей с одной машины,
Q = (0,25...0,40)Qм , кг; tм – время мойки машины, tм = 2…3 ч; q –
масса одновременно загружаемых деталей в ванну, q = 500…2000 кг; kим – коэффициент использования моечной машины или ванны (для моечной машины kим = 0,8…0,9; для ванны – kим = 0,5…0,8); Dст – годовойфондрабочеговремениремонтногооборудования
Dст = tkрnсм (365 − В− П),
где kр – коэффициент, учитывающий простои ремонтного оборудования, время на его обслуживание и ремонт, kр = 0,92…0,96; nсм – число смен в сутки.
Число металлорежущих станков при этом
mст = DβФkрв ,
ст ист
где β – коэффициент станочных работ, β = 0,2…0,35; kист – коэффициент использования станка, kист = 0,5…0,9.
36

Ориентировочное число постов для сварки
mсв = χDФрkвkсв , ст исв
где χ – коэффициент сварочно-наплавочных работ, χ = 0,05…0,1; kсв – коэффициент, учитывающий распределение между отдельными видами сварочных работ (для электродуговой сварки – kсв = 0,5…0,6; для ручной газовой сварки – kсв = 0,1…0,2; для механизированной наплавки – kсв = 0,1…0,3); kисв – коэффициент использования сварочного поста (для электросварочного и газосварочного постов – kисв = 0,8…0,9; для поста механической на-
плавки – kисв = 0,5…0,7).
Площадь слесарно-сборочного отделения определяется из расчета 30…40 м2/человек (станок) для разборочно-сборочного и моечного отделений; 20…30 м2/человек (станок) для сварочного и кузнечного отделения; 15…25 м2/человек (станок) для механического и электроремонтного отделений.
Под разметочную плиту отводят площадь не менее 6 м2. В электромеханическом отделении размещаются столы для сборкиразборки электрооборудования, верстаки, настольный сверлильный станок и стенд для испытания электродрели. При этом 20 % площади производственного цеха занимают административные, вспомогательныеискладскиепомещения(4, 10 и6 % соответственно).
Общая минимальная площадь ремонтной базы составляет
S = 1,2(30Nпр + 20mм + 20mсв + 15mст).
Минимальное расстояние между станками и стенами или колоннами зависит от габаритных размеров станка. Для движущихся частей габаритные размеры включают в себя размах как в одну, так и в другую стороны. При размещении станков должны быть выполнены следующие требования по минимальным расстояниям между станками (рис. 1.6).
1. Расстояние от стены до задней стенки станка должно быть не менее 500 мм.
37
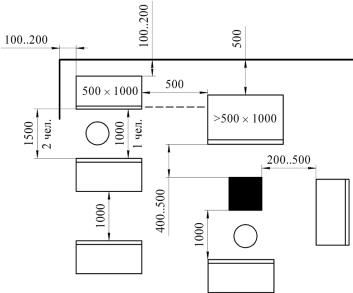
Рис. 1.6. Требования по расположению станков
времонтно-механическом цехе
2.Допускается установка станков вплотную к стене (100…200 мм) при небольших их габаритах (500×1000 мм) при условии, что позади станка нет движущихся частей и расстояние между станками не менее 500 мм. В случае если станок расположен вблизи колонны, крайне важно соблюдать следующие минимальные расстояния:
•между задней и боковой стороной и колонной – не менее
200…500 мм;
•между колоннойи передней стороной– не менее400…500 мм,
вслучае если есть рабочее место – не менее 1000 мм.
3. Расстояние между передней стороной станка и задней стороной смежного станка – не менее 1000 мм. Расстояние между передними сторонами станков, обслуживаемых двумя рабочими – не менее 1500 мм, одним рабочим – не менее 800…1000 мм. Поперечные расстояния между станками (не менее 500 мм) должны
38

быть ограждены для исключения прохода людей (можно установить шкафчики).
Для повышения коэффициента использования станка в основу организации рабочего места должен быть положен принцип отрыва рабочего от станка. Для этого крайне важно, чтобы наряд, чертеж, заготовки, инструмент доставлялись непосредственно к рабочему месту. Желательно, чтобы рабочий изготовлял однотипные детали. Работы по настройке станка должны проводиться в ремонтную смену. Необходимособлюдатьпорядокнарабочемместе.
Важной частью организации ремонтного цеха является расчет освещения. Необходимый уровень зрительной работоспособности достигается освещенностью, соответствующей визуальной задаче, снижением прямой слепости и отраженной блескости. Зрительный комфорт обеспечивают благоприятное распределение яркостей поверхностей в поле зрения и качество цветопередачи используемых ламп. На визуальное окружение оказывают влияние цвет излучения источников освещения, световые контрасты.
За основу расчета освещения принимается метод коэффициента использования светового потока. Требуемое количество ламп в помещение цеха определяется по формуле
N = EнSk ,
zFлUоу
где k – коэффициент запаса, учитывающий старение ламп и запыление светильников во время эксплуатации (выбирается по табл. 1.1); S – площадь помещения, м2; Fл – световой поток одной выбранной лампы, лм; Eн – нормированная освещенность, лк (значение требуемой освещенности проводимых работ в соответствии с СП 52.13330.2016 «Естественное и искусственное освещение» зависит от типа работ и должно учитывать такие параметры, как характеристику зрительной работы, разряд и возможный подразряд зрительной работы, контраст объекта с фоном и характеристику фона); z – число ламп в одном светильнике; Uоу – коэффициент использованиясветовогопотока(выбираетсяпотабл. 1.2).
39
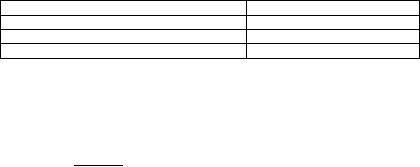
Таблица 1.1 Значения коэффициента запаса освещенности помещения
Запыленности помещения, мг/м3 |
Коэффициент запаса, k |
< 1 |
1,4…1,5 |
1…5 |
1,6…1,8 |
>5 |
1,8…2,0 |
Таблица 1.2
Значения коэффициента использования светового потока, Uоу
Светильники |
|
|
|
|
Потолочные |
|
|
|
|
|
|
Подвесные |
|
|
|
|||||||
р1, % |
|
50 |
70 |
|
|
50 |
|
30 |
|
70 |
|
|
|
|
50 |
30 |
||||||
р2, % |
|
|
|
30 |
50 |
|
30 |
10 |
|
50 |
|
|
30 |
50 |
|
30 |
10 |
|||||
р3, % |
30 |
|
10 |
|
30 |
|
10 |
30 |
|
10 |
10 |
30 |
|
10 |
|
30 |
|
10 |
30 |
|
10 |
10 |
i |
|
|
|
|
|
|
|
|
|
|
|
|
|
|
|
|
|
|
|
|
|
|
0,5 |
26 |
|
25 |
|
20 |
|
19 |
17 |
|
13 |
6 |
19 |
|
18 |
|
15 |
|
14 |
11 |
|
9 |
4 |
1 |
43 |
|
41 |
|
37 |
|
35 |
28 |
|
25 |
13 |
37 |
|
35 |
|
32 |
|
30 |
22 |
|
20 |
9 |
1,5 |
54 |
|
49 |
|
47 |
|
44 |
34 |
|
31 |
17 |
48 |
|
44 |
|
42 |
|
40 |
29 |
|
26 |
14 |
2 |
60 |
|
54 |
|
54 |
|
50 |
38 |
|
35 |
19 |
55 |
|
50 |
|
50 |
|
46 |
33 |
|
31 |
16 |
2,5 |
64 |
|
58 |
|
59 |
|
54 |
40 |
|
38 |
21 |
60 |
|
54 |
|
55 |
|
51 |
36 |
|
34 |
18 |
3 |
68 |
|
60 |
|
63 |
|
57 |
42 |
|
40 |
22 |
64 |
|
57 |
|
59 |
|
54 |
39 |
|
36 |
20 |
3,5 |
70 |
|
62 |
|
66 |
|
59 |
43 |
|
41 |
23 |
67 |
|
60 |
|
62 |
|
56 |
40 |
|
39 |
21 |
4 |
72 |
|
64 |
|
68 |
|
61 |
45 |
|
42 |
24 |
69 |
|
61 |
|
65 |
|
58 |
42 |
|
40 |
22 |
5 |
75 |
|
66 |
|
82 |
|
64 |
46 |
|
44 |
25 |
73 |
|
64 |
|
69 |
|
62 |
44 |
|
42 |
24 |
Величина коэффициента Uоу зависит от КПД светильника; формы его кривой силы света; ширины и длины помещения в плане, характеризуемых индексом помещения i; сочетания величин коэффициентов отражения потолка, стен и пола (р1, р2, р3 соответственно). При индексе помещения больше 5 в таблице принимается наибольшее его значение.
Индекс помещения может быть определен по формуле
i = |
AB |
, |
Hр ( A + B) |
где A – ширина помещения в плане, м; B – длина помещения в плане, м; Hр – высота освещения, м,
40