
книги / Эксплуатация, техническое обслуживание и ремонт горных машин калийных рудников
..pdfили нецелесообразно. Объект может перейти в предельное состояние, оставаясь работоспособным, если, например, его дальнейшее применение по назначению станет недопустимым по требованиям безопасности, экономичностииэффективности.
Ремонт – комплекс операций по восстановлению исправности или работоспособности изделий и восстановлению ресурсов изделий или их составных частей. В ремонт могут входить диагностика технического состояния, разборка, дефектация деталей, контроль технического состояния изделия, восстановление деталей, сборка и т.д.
Ресурс – суммарная наработка объекта от начала его эксплуатации или ее возобновления после ремонта до перехода в предельное состояние.
Дефект – каждое отдельное несоответствие продукции установленным требованиям.
Повреждение – событие, заключающееся в нарушении исправного состояния объекта при сохранении работоспособного состояния.
Отказ – событие, заключающееся в нарушении работоспособного состояния объекта.
Надежность – свойство объекта сохранять во времени в установленных пределах значения всех параметров, характеризующих способность выполнять требуемые функции в заданных режимах и условиях применения, технического обслуживания, хранения и транспортирования.
Надежность является комплексным свойством, которое в зависимости от назначения объекта и условий его применения может включать безотказность, долговечность, ремонтопригодность и сохраняемостьилиопределенныесочетанияэтихсвойств.
Понятие надежности включает следующие свойства технического объекта:
1. Безотказность – свойство объекта непрерывно сохранять работоспособное состояние в течение некоторого времени или наработки.
11
Безотказность в той или иной степени свойственна объекту в любом из возможных режимов его существования. В основном безотказность рассматривается применительно к его использованию по назначению, но во многих случаях необходима оценка безотказности при хранении и транспортировании объекта.
2.Долговечность – свойство объекта сохранять работоспособное состояние до наступления предельного состояния при установленной системе технического обслуживания и ремонта.
3.Ремонтопригодность – свойство объекта, заключающееся в приспособленности к поддержанию и восстановлению работоспособногосостоянияпутемтехническогообслуживанияиремонта.
4.Сохраняемость – свойство объекта сохранять в заданных пределах значения параметров, характеризующих способности объекта выполнять требуемые функции, в течение и после хранения и (или) транспортирования.
Наработка – продолжительностьилиобъемработыобъекта. Наработка может быть как непрерывной величиной (про-
должительность работы в часах, километраж пробега и т.п.), так
ицелочисленной величиной (число рабочих циклов, запусков и т.п.). Наработку объекта, работающего непрерывно, можно измерять в единицах календарного времени. Если объект работает с перерывами, то различают непрерывную и суммарную наработку. В этом случае наработку также можно измерять в единицах времени. Для многих объектов физическое изнашивание связано не только с календарной продолжительностью эксплуатации, но и с объемом работы объекта, и поэтому зависит от интенсивности применения объекта по назначению. Для таких объектов наработку обычно выражают через объем произведенной работы или число рабочих циклов.
Наработка до отказа – наработка объекта от начала эксплуатации до возникновения первого отказа.
Наработка между отказами – наработка объекта от окон-
чания восстановления его работоспособного состояния после отказа до возникновения следующего отказа.
12
Время восстановления – продолжительность восстановления работоспособного состояния объекта.
Срок службы – календарная продолжительность эксплуатации от начала эксплуатации объекта или ее возобновления после ремонта до перехода в предельное состояние.
Срок сохраняемости – календарная продолжительность хранения и (или) транспортирования объекта, в течение которой сохраняются в заданных пределах значения параметров, характеризующих способность объекта выполнять заданные функции. По истечении срока сохраняемости объект должен соответствовать требованиям безотказности, долговечности и ремонтопригодности, установленным нормативно-технической документацией на объект.
Остаточный ресурс – суммарная наработка объекта от момента контроля его технического состояния до перехода в предельное состояние (аналогично вводятся понятия остаточной наработки до отказа, остаточного срока службы и остаточного срока хранения).
Назначенный ресурс – суммарная наработка, при достижении которой эксплуатация объекта должна быть прекращена независимо от его технического состояния.
Назначенный срок службы – календарная продолжительность эксплуатации, при достижении которой эксплуатация объекта должна быть прекращена независимо от его технического состояния.
Цель установления назначенного срока службы и назначенного ресурса – обеспечить принудительное заблаговременное прекращение применения объекта по назначению, исходя из требований безопасности или технико-экономических соображений. Для объектов, подлежащих длительному хранению, может быть установлен назначенный срок хранения, по истечении которого дальнейшее хранение недопустимо, например, из требований безопасности.
13
1.2. Условия эксплуатации горных машин подземных разработок
Под горными машинами понимается весь парк машин, предназначенных для механизации процессов разрушения, погрузки и транспортирования горной породы, процессов возведения крепи, поддержания кровли и управления горным давлением и других технологических операций или процессов добычи полезного ископаемого, а также поддержания жизнедеятельности горнодобывающего предприятия [2].
Горные машины калийных рудников разделяются по своим функциональным признакам на следующие типы.
1.Выемочные машины, предназначенные для отделения полезного ископаемого и породы от массива и погрузки (в отдельных случаях компоновки машины в комбайны) горной массы на транспортные средства.
2.Оборудование для поддержания и крепления пород кровли, предназначенное для управления состоянием вмещающих пород, защиты рабочего пространства от продуктов обрушения и увеличения устойчивости горной кровли.
3.Погрузочные и транспортные машины. Первые осу-
ществляют погрузку отбитой горной массы на транспортные средства, а вторые – перемещение полезного ископаемого от очистного забоя до обогатительной фабрики или отвала.
4.Бурильные машины, предназначенные для производства (бурения) шпуров (цилиндрические полости диаметром до 75 мм
идлиной до 5 м включительно) и скважин (диаметр и длина соответственно более 75 мм или 5 м) различного назначения.
5.Вспомогательное оборудование разных видов для вы-
полнения вспомогательных операций, поддержания работы людей и техники в производственных условиях (дробильные и закладочные машины, отбойные молотки и др.).
Выполнение любых вышеперечисленных функций в подземных горных выработках обусловливают тяжелые условия эксплуа-
14
тации. К горным машинам, кроме общих требований к надежности и технологичности, предъявляются специальные требования. Из-за непостоянства и стесненности рабочего места при подземных работах горные машины должны быть достаточно мощными, но иметь минимальные габариты, что достигается, например, применением современных гидравлических приводов. Узлы и детали горных машин обрабатываются, а их изнашиваемые части дополнительно упрочняются от абразивного и химического воздействия горных пород и агрессивной окружающей среды.
Важным требованием к конструкции горных машин является простота их конструкции. Тяжелые условия труда усложняют обслуживание оборудования рабочими, а запыленность и агрессивность окружающей среды не позволяет проводить все виды ремонтных или обслуживающих операций на рабочем месте. Усложнение машин приводит к необходимости применения специальных средств и ремонтных баз для обслуживания, что снижает коэффициентготовностиоборудованияи, какследствие, производительность.
Дополнительные требования прочности к горным машинам предъявляются с целью обеспечения надежности работы оборудования при больших статических и динамических нагрузках, появление которых в условиях работы в подземных выработках сложно предсказать. Простейший пример – выброс газа при разработке выработки комбайновым комплексом. Газ, вырвавшийся из горного массива под давлением, бьет выемочную машину и может не только сместить ее, но и повредить.
Расходование заложенного в конструкцию горных машин ресурса в процессе эксплуатации связано с накоплением износа в узлах и деталях. Разрушение деталей горного оборудования происходит при их взаимодействии с твердыми (забой, порода, другое оборудование), жидкими (смазка с абразивом, химически активные и не активные воды и рассолы) и газообразными средами (химически активные газы, высокие и низкие температуры окружающей среды). Встречающийся в процессе эксплуатации машин износ можно разделить на две основные группы: моральный из-
15
нос, связанный с устарелостью конструкции, и физический. Физический износ подразделяют на естественный (нормальный) и преждевременный (аварийный).
Нормальный износ связан с номинальными условиями эксплуатации, заранее определен, и на него рассчитана конструкция машины. Аварийный износ почти всегда связан с дефектами в конструировании, изготовлении или уходе за машиной, имеет случайный характер и может быть учтен только за счет коэффициентов запаса.
Наиболее характерные причины, вызывающие аварийный износ, следующие:
–нарушение нормального режима работы (например, сверхнормативные нагрузки):
–нештатный режим смазки – отсутствие смазки или несоответствующий ее состав;
–несвоевременная замена изношенных деталей и узлов;
–усталостные явления в материале деталей;
–воздействие низких и высоких температур;
–старение материалов и др.
При эксплуатации машин могут возникнуть три вида разрушений деталей и узлов: вязкое, хрупкое и усталостное.
Вязкое разрушение наступает при напряжениях, превышающих предел текучести материала. Ему предшествует более или менее заметная пластическая деформация. Повысить сопротивляемость разрушению при этом можно ограничением перегрузки деталей (предохранительные устройства), повышением жесткости деталей, использованием материалов деталей с повышенными пределами прочности.
Хрупкое разрушение наступает без заметных следов пластической деформации и обычно вызывается перегрузкой при ударном приложении нагрузки. Сопротивляемость этому разрушению можно повысить снижением жесткости элементов машин, на которые непосредственно воздействуют ударные нагрузки (амортизирующие свойства).
16
Усталостное разрушение связано с усталостными трещинами, которые развиваются под действием переменных (часто циклических) напряжений, величина которых может не превышать предела текучести материала. Усугубляет износ при этом наличие концентраторов напряжений и знакопеременный характер изменения нагрузки. Основными средствами повышения усталостной прочности, кроме ранее перечисленных, являются: упрочнение деталей поверхностным пластическим деформированием; применением термиче- скойихимико-термическойобработкидеталейидр.
Постепенное изменение, как правило, уменьшение размеров, формы, массы или ухудшение состояния поверхности деталей горных машин, связано с их изнашиванием. Различают при этом механический, абразивный, гидроабразивный, химический и электрохимический износ.
Механическое изнашивание происходит в процессе эксплуатации машин и механизмов при естественном изменении количественных и качественных характеристик элементов этих машин и механизмов. Это связано с различными видами изнашивания. В целом характер изнашивания во времени выглядит следующим образом (рис. 1.1). Напервом этапе(зонаI) имеетместоускоренныйпроцесс, связанный с приработкой и активным истиранием микронеровностей трущихся деталей. Удельное давление велико, вероятность образования жидкостного и полужидкостного трения незначительна. Процесс стабилизируется в течение относительно небольшого промежутка времени, называемого периодом приработки. Зона II характеризуется постоянной интенсивностью износа, при котором отношение износа ко времени постоянно (tgα = const) и имеет название «период нормального изнашивания». Этот период во много раз больше первого. Зона III – зона аварийного изнашивания – характеризуется интенсивным износом. Период работы (срок службы) долженбытьограничен периодомзоны II.
Персоналу, проводящему техническое обслуживание и ремонт оборудования, важно знать срок его службы и время проведения соответствующего ремонта, замены деталей узлов и агрегатов машин.
17
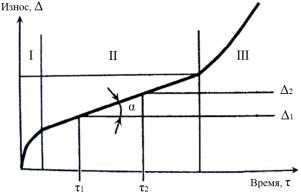
Рис. 1.1. Характер изнашивания деталей во времени
На современном этапе развития науки и техники допустимую величину износа можно определить аналитически для жидкостного трения при номинальном режиме смазки или на основе статистических данных для других видов трения. Жидкостное трение существует в том случае, когда трущиеся поверхности разделены сплошным слоем смазочного материала, внутри которого действуют законы гидродинамики. Коэффициент жидкостного трения колеблется в пределах 0,003…0,01 и соответствует коэффициенту трения в подшипниках качения.
Пренебрегая периодом приработки, срок службы T можно определить по формуле
T = |
/ tgα; |
|
||||
tgα = |
δΔ |
= |
τ |
2 |
− 1 |
, |
|
δτ |
|
2 |
− τ |
|
|
|
|
|
|
1 |
|
где ( 2 – 1) – величина износа между периодами времени τ1 и τ2, который может быть определен в процессе проведения соседних технических осмотров или ремонтов машины, после частичной или полной ее разборки.
Таким образом, зная допустимый износ и интенсивность изнашивания, можноразумнопланироватьсрокипроведенияремонтов.
18

Обеспечение качественной смазки важно для нормальной работы машин и механизмов, так как определяет характер и величину износа трущихся деталей.
Зазор в сопряжении вал – втулка, который обеспечивает оптимальные параметры жидкостного трения сопрягаемых деталей, определяется по формуле
Sн = 0,46d |
μn |
, |
|
cq |
|
где d – диаметр сопряжения; n – число оборотов вала; μ – кинематический коэффициент вязкости смазки; с – коэффициент, учитывающийконечнуюдлинуцапфы; q – удельноедавлениемеждуузлами.
Граничное трение происходит тогда, когда трущиеся поверхности разделены таким тонким слоем смазки, при котором она теряет несущую способность. При этом основную роль играет маслянистость, то есть способность смазки образовывать на поверхности адсорбированную пленку.
Промежуточное положение между жидкостным и граничным трением занимает полужидкостное трение.
Полусухое трение возникает тогда, когда адсорбированная пленка разрушена. В условиях полужидкостного, граничного и полусухого трения допустимый зазор
Sб = (2...3)Sн.
Сухое трение характерно отсутствием смазки. Коэффициент трения при этом колеблется в пределах 0,1…0,3.
Абразивный и гидроабразивный износ свойственен для машин, работающих в условиях сухого трения (транспортирующие машины); перекачивающих жидкости, содержащие абразивные частицы (насосы); осуществляющих разрушение горных пород (буровой инструмент).
Химическому и электрохимическому износу подвергают-
ся детали, работающие в агрессивных средах, при высоких тем-
19
пературах или в средах, проводящих электрический ток. Разрушение металлов при этом называется коррозией.
Основные методы повышения сопротивляемости износу следующие:
–соблюдение правильного режима смазки;
–покрытие рабочих поверхностей деталей защитным слоем (хромирование, никелирование и т.д.);
–упрочнение деталей поверхностным пластическим деформированием (дробеструйная обработка, обкатка роликами и др.).
В качестве защиты от коррозии используют окраску (лаки, краски), применяют легирование деталей (хром, никель, медь), покрытие специальными мастиками (битум, бакелит), создание защитной окисной пленки (оксидирование, анодирование), кор- розионно-стойкого металлического слоя (цинкование, лужение, гальванические методы, металлизация) и применение коррозион- но-стойких неметаллических материалов.
В сложных условиях эксплуатации тяжело сохранить техническую готовность машинного парка горного предприятия. Для поддержания их работоспособного состояния требуются значительные материальные и трудовые затраты, которые соизмеримы,
аиногда даже превышают затраты на изготовление машины. Поэтому горные предприятия при эксплуатации оборудования стараются предупреждать отказы машин в процессе использования, осуществляя заранее выбранную систему эффективной эксплуатации, технического обслуживания и ремонта.
1.3. Подготовка горных машин к ремонту
Основными операциями, выполняемыми при ремонте, являются: приемка машин в ремонт; их наружная очистка и мойка; разборка машин на агрегаты, сборочные единицы, детали; мойка деталей; контроль и дефектоскопия деталей; изготовление или ремонт (восстановление) деталей; ремонт металлоконструкций, гидравлического, электрического оборудования; комплектовка сборочных единиц и агрегатов; общая сборка; регулировка и наладка; испытание вхо-
20