
книги / Эксплуатация, техническое обслуживание и ремонт горных машин калийных рудников
..pdfлостую и под нагрузкой; устранение недостатков, обнаруженных прииспытании, исдачамашинынаэксплуатацию.
Для ремонта машин каждого типа (выемочной, транспортной, подъемной и др.) разрабатывается типовой технологический процесс, позволяющий заранее провести необходимую конструкторскую, технологическую, материальную и организационную подготовку, обеспечивающую высокое качество в короткие сроки ремонта. Обязательные технологические операции ремонта для каждого наименования оборудования приведены в руководстве по эксплуатации машины.
1.3.1. Разборка машины
До начала разборки необходимо подготовить рабочее место:
–подготовить около машины площадку, достаточную для нормальной работы слесарей-ремонтников и правильной укладки снятых с машины деталей, а также для их кантовки;
–обеспечить наличие необходимых средств освещения на монтажной площадке, смонтировать отдельное распределительное устройство, средства радиоили телефонной связи;
–проверить наличие всех необходимых для работы исправных и испытанных стопоров, грузозахватных приспособлений;
–заготовить требуемое количество прокладок, распорок и козел для укладки снятых деталей.
Машины, поступающие в ремонт, должны быть чистыми. Наружную мойку машин производят струей воды из моечных установок. В высоконапорных передвижных моечных установках типа ОМ-5285, ОМ-5360, ОМ-5359 машины очищаются струями воды под высоким давлением (до 12 МПа) и температурой воды
на выходе из установки 30…85 °С. После очистки и внешнего осмотра приступают к разборке.
Технологический процесс разборки представляет собой часть производственного процесса, непосредственно связанного с последовательным разъединением машины на узлы, подузлы (сборочные единицы) и детали.
21
Разборка может осуществляться методами последовательного и комбинированного хода операций.
В первом случае время, затраченное на разборку, складывается из продолжительности выполняемых при этом операций:
T = ti ,
где ti – время, затрачиваемое на одну разборочную операцию. Во втором случае
T = kв ti ,
где kв – коэффициент, учитывающий одновременность выполнения операций, kв < 1.
Трудоемкость разборочно-сборочных работ составляет более половины трудоемкости ремонта машин. При этом около 60 % трудоемкости приходится на резьбовые, а около 20 % на прессовые соединения.
При разборке необходимо соблюдать следующие правила:
–разборку нужно вести инструментами или приспособлениями, применение которых исключает возможность порчи годных деталей;
–удары молотком следует наносить по деталям, используя проставки из дерева или мягкого металла, разбираемые детали надо снимать аккуратно, без перекосов и повреждений;
–к трудно снимающимся деталям нельзя прилагать большие усилия, следует выяснить причину заедания и устранить ее;
–разборка длинных валов должна производиться с применением нескольких опор;
–детали каждого разбираемого механизма необходимо укладывать в отдельные ящики, а не нагромождать одну на другую, особенно осторожно следует укладывать детали с хорошо отделанными поверхностями;
–ящики с деталями обязательно закрывать крышками;
–болты, шайбы и другие крепежные детали при полной разборке сборочной единицы укладывают в специальный ящик, при
22
частичной разборке целесообразно крепежные детали вставлять обратно в предназначенные для них отверстия;
– крупные детали укладывают на подставки возле ремонтируемой машины.
Следует отметить, что при выполнении монтажно-демонтаж- ных работ следует с особой тщательностью следить за соблюдением требований техники безопасности. Большинство несчастных случаев на ремонтном производстве происходит именно на этих этапах ремонтно-восстановительных работ.
1.3.2. Мойка деталей
После разборки машин детали очищают, промывают и обезжиривают. Качество очистки деталей влияет на их восстановление и дефектацию. Выбор способа отчистки зависит от материала, конфигурации и размеров детали, вида ее загрязнения. Детали могут быть загрязнены маслами и смазками, углеродистыми отложениями (нагар, лаковые отложения и осадки), продуктами коррозии и накипи, пыле- и маслогрязевыми отложениями.
Детали можно промыть различными способами. Самый простой – ручная мойка керосином (бензином, соляркой) в открытых ваннах или при помощи волосяных щеток и ветоши. Детали укладываются на деревянную или металлическую решетку, находящуюся на некоторой высоте от дна ванны. В моечном помещении обычно устанавливают две ванны: одна для предварительной промывки, другая – для чистой. Отработанный керосин сливается и заменяется свежим. Для мойки подшипников применяют керосин в смеси с маслом. Удаление нагара и накипи производится в солевых растворах следующего состава: едкий натр 60…65 %, азотнокислый натрий 30…35 %, хлористый натрий 5 %.
Недостатки такой мойки – большой расход моющей жидкости; малая производительность процесса; огнеопасность; воздействие на кожу мойщика и отравляющее воздействие паров керосина (бензина, солярки) на дыхательные органы работающего персонала даже при наличии хорошей вентиляции.
23
Широкое применение для очистки получила струйная мойка в моечных ваннах, а также погружение деталей в выварочные ванны с сильнодействующими моечными средствами и оборудованные устройствами для перемешивания жидкости. В ремонтном производстве для очистки деталей из черных металлов от горюче-смазочных материалов применяют 3…4%-ный водный раствор каустической содыNa2CO3, подогретойдотемпературы80…90 °С.
Для очистки деталей от сложных загрязнений применяют синтетические моющие средства МЛ-51, МЛ-52, МС-5, МС-8, содержащие в своем составе кальцинированную соду, триполифосфат натрия, металлосиликат натрия, жидкое стекло, смачиватель ДБ и др. Эти растворы малотоксичны и позволяют организовать работу моечных установок по замкнутому циклу с многократным использованием моющих растворов.
Лучшее качество очистки обеспечивает обмывка деталей в горячем растворе в специальных выварочных ваннах. Процесс очистки длится 6…20 ч. Детали перемещаются на конвейерах в специальных ящиках. Для мойки подшипников качения на конечных операциях применяют средства, не вызывающие коррозию металла (керосин). Удаление нагара и накипи производят в растворах солей на основе едкого натра (60…65 %), азотнокислого натра (30…35 %), хлористого натра (5 %).
Для мойки деталей механизированным способом применяют моечные машины циклического действия одно-, двух- и трехкамерного типа, а также конвейерного типа с непрерывным принципом действия. На рис. 1.2 представлена однокамерная моечная машина. В ней на грязевый слой, кроме физико-химического действия моющей жидкости, оказывает влияние удар струи из труб оросительного устройства.
Процесс очистки в машине протекает последовательно: сначала детали обмывают горячим содовым раствором (t = +75…+90 °С), а затем горячей водой (t = +80…+90 °С) под давлением 0,2 МПа. Время мойки зависит от конфигурации и размеров детали, но не превышает6 мин.
24
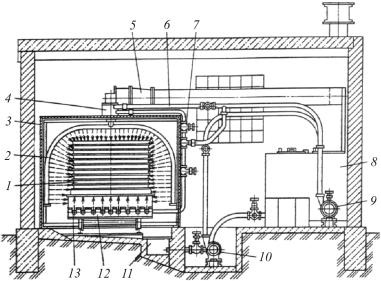
Рис. 1.2. Однокамерная моечная машина: 1 – очищаемые детали; 2 – трубы оросительного устройства; 3 – моечная камера; 4 – приводная головкаоросительныхтруб; 5 – вентиляционныетрубы; 6, 7 – трубопроводы; 8 – емкость для подогрева раствора; 9, 10 – насосы; 11 – приямок; 12 – тележка; 13 – трубы нижнего душа
При виброабразивной очистке деталей (рис. 1.3) контейнеру с мелкими деталями, помещенному в моечную жидкость с мелкозернистым абразивом, сообщают с помощью вибратора колебательное движение с частотой 25 Гц и амплитудой 2 мм. Сущность вибрационной обработки состоит в последовательном нанесении по поверхности обрабатываемых деталей большого числа микроударов гранулами абразива под действием направленных вибраций, сообщаемых рабочей камерой.
Вибрационная мойка ведется в закрытых машинах различными органическими растворителями и эмульсиями. При этом механическое воздействие на очищаемые поверхности деталей усилено вибрацией. Появляющиеся при этом турбулентные потоки жидкостей способствуют повышению качества очистки.
25
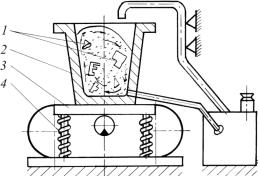
Рис. 1.3. Схема вибрационной обработки деталей: 1 – обрабатываемые детали; 2 – рабочая камера, заполненная шлифовальным материалом; 3 – основание; 4 – пружины вибропривода
Пневматический способ очистки деталей применяют для удаления ржавчины, нагара, старой краски и т.п. При этом поверхность детали обрабатывают металлическим песком под действием сжатого воздуха.
Для очистки и мойки деталей гидро- и пневмоаппаратуры, подшипников качения используют моечные установки с ультразвуковой очисткой. В качестве ультразвукового элемента применяют магнитострикционные преобразователи, соединенные с генераторами высокочастотных колебаний (частотой 19…20 МГц). Под действием колебаний в жидкости образуются области сжатия или разряжения, а при определенной интенсивности – кавитационные явления, связанные с образованием и захлопыванием воздушных пузырьков. Происходящие при этом микрогидравлические удары разрушают трудно отделяемые масляные загрязнения, превращая их в эмульсию, которая легко удаляется с поверхности. Промышленность выпускает несколько типов установок для ультразвуковой очистки деталей: УЗВ-16, УЗВ-17, УЗВ-18 и др. В них используются подогретые до t = + 60 °С щелочные растворы. Продолжительность очистки деталей 0,5…4 мин. После очистки детали промывают в горячей и холодной воде и покрывают смазкой.
26
1.3.3.Методы измерения, контроль
идефектоскопия деталей
Вследствие несовершенства технологии изготовления или в результате эксплуатации в тяжелых условиях в деталях машин появляются различные дефекты – нарушения сплошности или однородности материала, отклонения от заданного химического состава или структуры, а также от заданных размеров. Дефекты изменяют физические свойства материала (плотность, электропроводность, магнитные, упругие свойства и др.), которые могут быть измерены при дефектоскопии и соотнесены с допустимыми или предельными значениями. Дальнейший анализ состояния деталей в рамках дефектации производится с целью оценки возможности их ремонта или отбраковки.
Методы дефектоскопии принято делить на две группы: органолептические (визуальный и акустический контроль) и инструментальные (с использованием измерительного инструмента и специализированных приборов).
Визуальный осмотр – самый простой метод дефектоскопии, заключающийся во внешнем осмотре деталей. При осмотре отдельных деталей и узлов можно обнаружить различные поверхностные пороки (трещины); более детальное изучение поверхности осуществляется посредством оптических приборов.
Акустический метод применяется для проверки состояния частей работающей машины, недоступных для непосредственного осмотра и проверки. Осуществляется ослушиванием посредством, например, стетоскопа, при помощи которого выявляется стук, отличный от шума и звука, сопровождающих нормальную работу механизмов. С помощью различных шумомеров анализ шумов проводится как по гармоникам, так и по общему уровню шума. При этом в спектре шумов возможно выделение шумов отдельных узлов и соединений: детали с трещинами дают дребезжащий или приглушенный звук.
Ультразвуковой метод дефектоскопии основан на том, что высокочастотные звуковые волны (частота f = 0,5…10 МГц) в
27
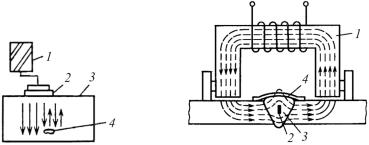
однородных твердых телах распространяются почти без затухания, а на границе «металл – воздух», «металл – жидкость» почти полностью отражаются (рис. 1.4). Этим способом можно обнаружить в металле, пластмассах и других материалах пустоты, трещины, пороки литья и дефекты на глубине от нескольких миллиметров до метра.
Электромагнитный метод – способ обнаружения дефектов в металлических деталях при прохождении электрического тока или магнитного потока по исследуемому изделию. Испытуемое металлическое изделие располагается между полюсами сильного электромагнита постоянного тока. По искривлению фиксируемого магнитного потока судят о наличии посторонних включений, повреждений, раковин, трещин и волосовин (рис. 1.5). Так как трещины почти не деформируют электромагнитное поле, если их направление совпадает с направлением магнитного потока, то изделие должно быть намагничено в двух взаимно-перпендикулярных направлениях.
Рис. 1.4. Схема обнаружения |
Рис. 1.5. Схема обнаружения |
|
дефекта в детали ультразвуковым |
дефекта в |
детали магнитным |
методом: 1 – ультразвуковой |
методом: 1 – намагничивающее |
|
генератор-приемник; 2 – пласти- |
устройство |
(электромагнит); |
на пьезоэлектрическая; 3 – деталь; |
2 – дефект; 3 – сварной шов; |
|
4 – дефект |
4 – магнитная лента |
Магнитно-акустический метод основан на слабом намаг-
ничивании изделия. При перемещении прибора-искателя возле
28
дефектного места в приемнике, выполненном в виде катушки колебательного контура, меняется наведенная электродвижущая сила (ЭДС). Внезапное изменение ЭДС обусловливает изменение тона звукового сигнала. Этот метод широко применяется для контроля сварных швов, вагонных осей, рельсов.
Магнитно-порошковая дефектоскопия слагается из трех ос-
новных операций: намагничивание изделий; покрытие намагниченных изделий магнитным индикатором и осмотр поверхностей; размагничивание изделий. Магнитное поле рассеяния возникает над дефектом вследствие того, что в намагниченной детали магнитные силовые линии, встречая на своем пути дефект, огибают его как препятствие с малой магнитной проницаемостью, в результате чего магнитное поле искажается, отдельные магнитные силовые линии вытесняются дефектом на поверхность, выходят из детали и входят в нее обратно. При этом по обе стороны от трещин, то есть по краям дефекта, возникают местные магнитные полюсы, создающие локальное магнитное поле рассеяния. Для обнаружения магнитного поля рассеяния на контролируемые участки детали наносят магнитный индикатор в виде сухого ферромагнитного порошка или магнитной суспензии. В качестве магнитного порошка обычно применяют крокус (Fe2O3), измельченный до 10 мкм и превращенный в ферромагнитную модификацию нагревом до 700 °С с последующим охлаждением. После дефектоскопии применяют следующие основные способы размагничивания: протягивание намагниченной детали через катушку, питаемую переменным током; пропускание через деталь переменного тока.
Рентгеновский метод – просвечивание рентгеновскими лучами на пленку или экран позволяет контролировать сварочные швы, литье из легких сплавов. Рентгеновские лучи поглощаются различными химическими элементами по-разному, в частности воздухом они задерживаются меньше, чем металлом. На пленке видна неоднородность материала детали и имеющиеся дефекты в виде пустот.
29
Гамма-дефектоскопия – метод выявления скрытых внутренних дефектов в материалах путем их просвечивания радиоактивными изотопами химических элементов. Применяют два метода гамма-дефектоскопии: фотографический и ионизационный. Первый более нагляден и позволяет получить объективную информацию о дефектах на пленке. Второй менее чувствителен, но имеет преимущества в скорости контроля. Чувствительность при просвечивании гамма-лучами от радиоактивных изотопов в 3…4 раза меньше, чем при просвечивании рентгеновскими лучами, но во много раз дешевле рентгеновского.
Люминесцентный метод – метод дефектоскопии на основе облучения ультрафиолетовыми лучами деталей в растворе минерального масла. Детали погружают на 3 мин в раствор трансформаторного или индустриального масла с керосином. Затем детали просушивают и посыпают порошком окиси магния, после чего осматривают под ультрафиолетовыми лучами. Дефектные места, благодаря раствору масла с керосином, который вытягивается магнезиевой пудрой на поверхность, ярко светятся. Им можно выявить трещины толщиной менее 5 мм.
Для оценки дальнейшего использования деталей и узлов машин производится их дефектация. Дефектацию выполняют в соответствии с возможными дефектами деталей и способами их определения, критериями выбраковки, размерами и техническими характеристиками деталей.
В процессе дефектации все детали разделяют на три группы.
1.Годные детали, размеры которых лежат в пределах допустимых величин. Их отправляют на сборку или склад готовой продукции.
2.Детали, подлежащие ремонту, износ и повреждение которых могут быть исправлены. Их отправляют на ремонт или склад деталей, ожидающих ремонта.
3.Детали забракованные. Восстановить их невозможно или экономически нецелесообразно. Их отправляют на склад утиля как лом.
30