
книги / Материаловедение и технологии современных и перспективных материалов.-1
.pdf8.Назовите закономерности фазовых превращений при высоких давлениях.
9.Опишите методы получения синтетических алмазов и СТМ.
10.Охарактеризуйте структуру и свойства нитрида бора.
11.Опишите структуру, свойства, получение и применение углеродных пленок и пленок из нитрида углерода.
12.Какими особенными свойствами обладают стали с метастабильным аустенитом?
13.Назовите условия формирования метастабильного аустенита и механизм превращения аустенита в мартенсит деформации.
14.Какие технологии получения литых метастабильных аустенитных сталей существуют?
15.Какие факторы обусловливают формирование метастабильного аустенита в технологии получения МАС из порошков?
16.В чем заключается механизм эффекта памяти формы?
17.Опишите технологии получения и применение сплавов на основе интерметаллидов.
18.Дайте определение функционально-градиентных материалов (ФГМ) и классификацию ФГМ.
19.Какие методы применяются для получения объемных ФГМ
сплавно меняющейся концентрацией компонентов?
20.Как получают объемные слоистые материалы и покрытия с переменным химическим и/или фазовым составом на основе легированных сталей?
21.Опишите структуры и технологии получения слоистых ФГМ.
22.Назовите области применения ФГМ.
23.Охарактеризуйте виды жидких кристаллов и их применение.
24.Назовите свойства твердых электролитов, дайте классификацию твердых электролитов и определите механизмы проводимости.
25.Назовите методы получения твердых электролитов и их применение.
26.Дайте характеристику основного свойства диэлектриков, определите понятия «поляризация», «запрещенная зона».
27.Назовите механизмы поляризации диэлектриков.
28.Опишите структуру и свойства пьезоэлектриков и сегнетоэлектриков.
29.Назовите области применения активных диэлектриков.
30.Назовите области применения магнитных наноматериалов.
91
31.Чем отличаются свойства наноструктурных проводников от традиционных, в чем причина их отличия?
32.Назовите виды и области применения материалов для фотоники.
33.Что называют высокотемпературными проводниками?
34.Перечислите методы изготовления ВТСП.
СПИСОК РЕКОМЕНДУЕМОЙ ЛИТЕРАТУРЫ К РАЗДЕЛУ I
1.Елисеев А.А. Лукашин А.В. Функциональные наноматериалы / под ред. Ю.Д. Третьякова. – М.: Физматлит, 2010. – 456 с.
2.Рыжонков Д.И., Лёвина В.В., Дзидзигури Э.Л. Наноматериалы: учеб. пособие. – М.: БИНОМ: Лаборатория знаний, 2008. – 365 с.
3.Суздалев И.П. Нанотехнология: физикохимия нанокластеров, наноструктур и наноматериалов. – М.: КомКнига, 2006. – 589 с.
4.Сорокин В.С., Антипов Б.Л., Лазарева Н.П. Материалы и элементы электронной техники: учеб. для вузов: в 2 т. – Т. 1: Проводники, полупроводники, диэлектрики. – М.: Академия, 2006. – 448 с.
5.Сорокин В.С., Антипов Б.Л., Лазарева Н.П. Материалы и элементы электронной техники: учеб. для вузов: в 2 т. – Т. 2: Активные диэлектрики, магнитные материалы, элементы электронной техники. –
М.: Академия, 2006. – 384 с.
6.Кульметьева В.Б., Порозова С.Е. Керамические материалы: получение, свойства, применение: учеб. пособие. – Пермь: Изд-во Перм.
гос. техн. ун-та, 2009. – 237 с.
7.Сплавы с эффектом памяти формы / К. Ооцука, К. Симидзу, Ю. Судзуки[идр.]; подред. Х. Фунакубо. – М.: Металлургия, 1990. – 224 с.
8.Суперсплавы: Жаропрочные материалы для аэрокосмических
ипромышленных энергоустановок: в 2 кн. / под ред. Ч.Т. Симса, Н.С. Стоффа, У.К. Хагеля. – М.: Металлургия, 1995. – Кн. 1. – 384 с.;
Кн. 2. – 384 с.
9.Гусев А.И. Нанокристаллические материалы: методы получения
исвойства. – Екатеринбург: Изд-во УрО РАН, 1998. – 186 с.
10.Оглезнева С.А. Материаловедение и иехнологии современных
иперспективных материалов: учебное пособие. – Пермь: Изд-во Перм. нац. исслед. политехн. ун-та, 2012. – 307 с.
92

Раздел II
СОВРЕМЕННЫЕ ТЕХНОЛОГИИ ОБРАБОТКИ МАТЕРИАЛОВ
ЛЕКЦИЯ 4. ЛАЗЕРНАЯ ОБРАБОТКА МАТЕРИАЛОВ
4.1. ТИПЫ ЛАЗЕРОВ
Слово «лазер» представляет собой акроним английской фразы
«Light Amplification by Stimulated Emission of Radiation», переводимой как усиление света в результате вынужденного (индуцированного) излучения.
Лазер или оптический квантовый генератор – устройство, преобразующее энергию накачки (световую, электрическую, тепловую, химическую и др.) в энергию когерентного, монохроматического, поляризованного и узконаправленного потока излучения.
Впервые генераторы электромагнитного излучения, использующие механизм вынужденного перехода, были созданы в 1954 г. советскими физиками А.М. Прохоровым и Н.Г. Басовым, а также американским физиком Ч. Таунсом на частоте 24 ГГц. Активной средой служил аммиак.
Принцип работы лазера Басова с тремя энергетическими уровнями можно представить следующим образом. Под действием энергии накачки (например, светового потока) атомы с основного уровня Е0 поднимаются на верхний, неустойчивый уровень Е2. Оттуда они быстро опускаются на уровень Е1, отдавая часть своей энергии на нагрев вещества. С этого уровня атом возвращается в основное состояние Е0, излучая квант частоты n = (Е1 – Е0)/h, где h – постоянная Планка. Вернуться он может либо самопроизвольно, либо под воздействием пролетающего кванта той же частоты n. В этом случае говорят об индуцированном когерентном излучении.
В 1964 г. Басов удостоен Нобелевской премии по физике за фундаментальную работу в области квантовой электроники.
Принцип работы лазера заключался в следующем (рис. 4.1). Пучок молекул в источнике проходит через высокочастотное электромагнитное поле, где часть их переходит в возбужденное состояние. Далее пучок
93
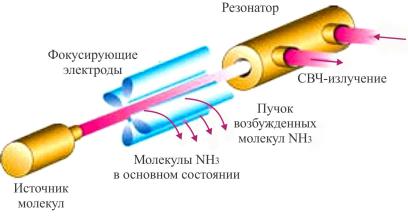
Рис. 4.1. Схема лазера Басова
из смеси молекул поступает в фокусирующее устройство – систему из четырех электродов, создающих четырехполярное электрическое поле. В нем на молекулы в возбужденном состоянии действуют силы, направленные к центру системы, а на молекулы в основном состоянии – силы, направленные наружу. В результате в сфокусированном пучке остаются только возбужденные молекулы, которые попадают в резонатор. В резонаторе возникают незатухающие колебания радиочастоты, которые выходят через волновод.
В настоящее время существует большое количество видов лазеров, использующих в качестве рабочей среды все агрегатные состояния вещества. Габариты лазеров разнятся от микроскопических для ряда полупроводниковых лазеров до размеров футбольного поля для некоторых лазеров на неодимовом стекле.
Твердотельный лазер работает на искусственно выращенных кристаллах рубина, алюмо-иттриевого граната и на стекле с примесью редкого элемента неодима (рис. 4.2). Стеклянный или кристаллический стержень вместе с импульсной лампой накачки окружен отражателем и помещен внутрь резонатора между парой зеркал. Энергия световой вспышки превращается влазерный импульс.
Газовый лазер – лазер с газообразной активной средой (рис. 4.3). Трубка с активным газом помещается в оптический резонатор, состоящий в простейшем случае из двух параллельных зеркал. Одно из них является полупрозрачным.
94
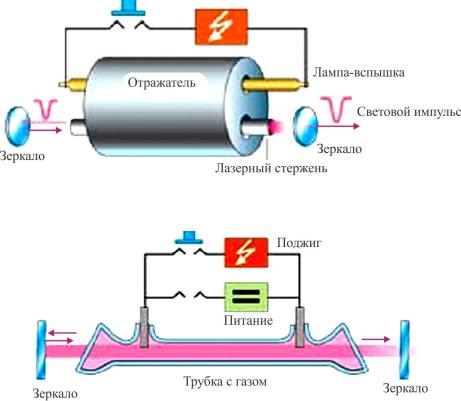
Рис. 4.2. Схема работы твердотельного лазера
Рис. 4.3. Схема работы газового лазера
Испущенная в каком-либо месте трубки световая волна при распространении её через газ усиливается за счёт актов вынужденного испускания, порождающих лавину фотонов. Дойдя до полупрозрачного зеркала, волна частично проходит через него. Эта часть световой энергии излучается газовым лазером вовне. Другая же часть отражается от зеркала и даёт начало новой лавине фотонов. Все фотоны идентичны по частоте, фазе и направлению распространения. Благодаря этому излучение лазера может обладать чрезвычайно большими монохроматичностью, мощностью и резкой направленностью.
Существующие газовые лазеры работают в очень широком диапазоне длин волн – от ультрафиолетового излучения до далёкого инфракрасного излучения – как в импульсном, так и в непрерывном режиме.
Активная среда CО2-лазера – смесь углекислого газа CO2, гелия He и азота N2. Возбуждение смеси выполняется разными видами электрического разряда в газах. Длина волны излучения CО2-лазера – 10 мкм.
95
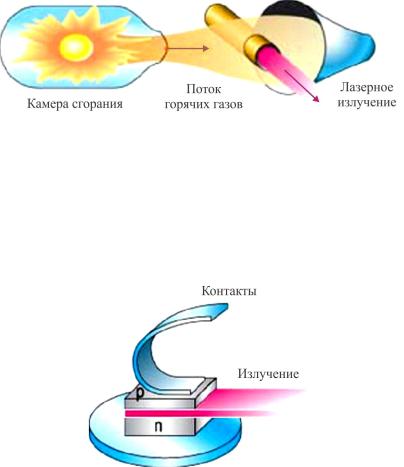
Из-за наименьшей расходимости луча CО2-лазеры являются самыми универсальными, так как позволяют располагать источник излучения вдали от зоны обработки без снижения качества лазерного луча. Особенно это влияет при обработке неровных материалов. Эти лазеры используются в основном для резки и гравировки.
Газодинамический лазер – разновидность лазера газового, напоминающий реактивный двигатель (рис. 4.4). Сгорающее в нем топливо создает поток горячих газов, ионы и молекулы которых возбуждены нагревом до тысячи градусов с лишним. Поток проходит через сопло и резонатор, где охлаждается и отдает энергию в виде непрерывного излучения мощностью до сотен киловатт.
Рис. 4.4. Схема работы газового лазера
Полупроводниковый лазер излучает за счет квантовых p-n-перехо- дов между зоной проводимости p и валентной зоной n (рис. 4.5). Излучающая область лазера исключительно мала, порядка 10–11 см (длина около 1 мм, толщина порядка 2 мкм), но энергия излучения достигает 10 Вт. Наиболее распространенным материалом для этих лазеров служит арсенид галлия GaAs.
Рис. 4.5. Схема работы полупроводникового лазера
96
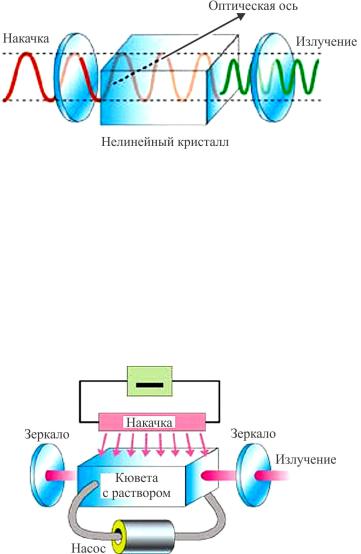
Параметрический лазер работает за счет преобразования мощной световой волны одной частоты, проходящей через нелинейный кристалл, в излучение меньших частот (рис. 4.6). Кристалл помещен между зеркалами, играющими роль резонатора. Меняя расстояние между зеркалами, можно при постоянной длине волны накачки менять частоту лазерного излучения в широких пределах.
Рис. 4.6. Схема работы параметрического лазера
Жидкостные лазеры работают на растворах органических красителей и на неорганических жидкостях, налитых в кювету (рис. 4.7). Они способны перестраивать длину волны излучения в широких пределах и могут работать как в непрерывном, так и в импульсном режиме. Накачка производится либо мощными лампами, либо лазерным излучением. Нагревающаяся в процессе работы жидкость прокачивается через холодильник. Лазеры на неорганических жидкостях по своим параметрам сходны с твердотельными лазерами.
Рис. 4.7. Схема работы параметрического лазера
97
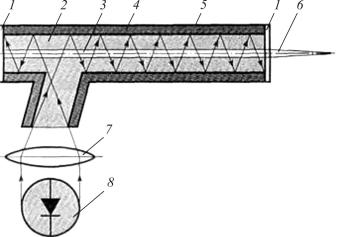
В волоконном лазере в качестве рабочего тела используется кварцевое волокно, легированное ионами редкоземельных металлов, например иттербия (рис. 4.8). Длина волны излучения – 1,06–1,09 мкм. Мощность от милливатт до 20 кВт. Чаще всего применяются для обработки металлов и большинства пластмасс.
Стержневым элементом волоконного лазера является внутреннее кварцевое оптическое волокно, которое легировано активными элементами, а именно Yb3+-ионами. Центральная часть, окружающая внутреннюю сердцевину, выполнена из кварцевого волокна, выполняющего роль волновода для сгенерированного лазерного излучения. Внутренние стенки волновода покрыты светоотражающей поверхностью, играющей важную роль, поскольку удерживает движущийся поток квантов света внутри волновода.
Их основными преимуществами являются высокое оптическое качество излучения, небольшие габариты и возможность встраивания в волоконные линии. Главная особенность этого лазера в том, что излучение здесь рождается в тонком, диаметром всего в 6–8 мкм, волокне (сердцевине – например, активная среда иттербий), которое фактически находится внутри кварцевого волокна диаметром 400–600 мкм.
Рис. 4.8. Схема работы волоконного лазера: 1 – торцевое зеркало; 2 – оптическое кварцевое волокно; 3 – активированное световедущее волокно; 4 – светоотражающее покрытие; 5 – защитная оболочка; 6 – лазерный луч; 7 – фокусирующая линза; 8 – светодиоды
98
Излучение лазерных диодов накачки вводится в кварцевое волокно и распространяется вдоль всего сложного составного волокна, имеющего длину несколько десятков метров.
4.2. ЛАЗЕРНАЯ ОБРАБОТКА МАТЕРИАЛОВ
Уникальные свойства лазеров – монохроматичность (строгая одноцветность), высокая когерентность (согласованность колебаний), острая направленность светового излучения. Лазеры находят широкое применение в современных физических, химических и биологических исследованиях, имеющих фундаментальный характер. При обсуждении практических применений лазеров обычно выделяют два направления. Первое направление связывают с применениями, в которых лазерное излучение (как правило, достаточно высокой мощности) используется для целенаправленного воздействия на вещество. Сюда относят лазерную обработку материалов (например, сварку, термообработку, резку, пробивание отверстий), лазерное разделение изотопов, применение лазеров в медицине и т.д. Второе направление связывают с так называемым информативным применением лазеров – для передачи и обработки информации, для осуществления контроля и измерений.
Лазерная обработка металлов. Возможность получать с помощью лазеров световые пучки высокой мощности до 1012–10 16 Вт/см2 при фокусировке излучения в пятно диаметром до 10–100 мкм делает лазер мощным средством обработки оптически непрозрачных материалов, не доступных для обработки обычными методами (газовая и дуговая сварка). Это позволяет осуществлять новые технологические операции, например, просверливание очень узких каналов в тугоплавких материалах, различные операции при изготовлении пленочных микросхем, а также увеличи-
вать скорость обработки деталей. При пробивании отверстий в ал-
мазных кругах применение лазера сокращает время обработки одного круга с 2–3 дней до 2 минут. Наиболее широко применяется лазер в микроэлектронике, где предпочтительна сварка соединений, а не пайка. Основные преимущества: отсутствие механического контакта, возможность обработки труднодоступных деталей, возможность создания узких каналов, направленных под углом к обрабатываемой поверхности.
Способ лазерной наплавки состоит в создании на поверхности изделий плакирующего слоя из порошкового материала с помощью лазерного луча. Высокая энергия и сконцентрированный луч современных
99
лазеров позволяют создавать прочные высокоплотные покрытия с большой скоростью и малыми потерями. Малая зона термического влияния приводит к высокой скорости охлаждения наплавляемого материала – тысячи градусов в секунду. Такая скорость охлаждения приводит к формированию мелкозернистой микроструктуры, хорошо противостоящей коррозионным и эрозионным процессам. Эта технология позволяет не только исключить недостаток, но и позволяет сохранить геометрические размеры подвариваемой детали в пределах поля допуска (вплоть до десятков микрон). При этом твердость в зоне наплавки остается на уровне твердости основного материала, последующая же механическая обработка восстановленного участка сводится к минимуму. Также существенным представляется то, что время, требующееся на устранение дефекта с помощью лазерной наплавки, минимально – от нескольких секунд до нескольких десятков минут, что напрямую связано с характером и геометрическими размерами изъяна.
Технология лазерной наплавки заключается в том, что к месту дефекта одновременно подводятся присадочная проволока или порошок и луч лазера. Присадочный материал, расплавляясь, заполняет место дефекта. Для того чтобы предотвратить окисление места дефекта, подварка проводится в инертных газах, таких как, например, аргон. Преимущества лазерной подварки в том, что после нее требуется минимальная механическая обработка (особенно если сравнивать с традиционными методами подварки штучными электродами). Кроме того, лазерный луч обладает высокой точностью наведения, что позволяет предельно точно навести его на место дефекта; положительным фактором выступает и локальность его действия, что позволяет исправлять строго конкретные участки детали, в том числе и точечные дефекты. Минимальное термическое воздействие обеспечивается кратковременностью протекающего процесса (несколько мс).
С помощью технологии лазерной наплавки можно выполнять такие работы, как восстановление кромок рабочих поверхностей прессформ и штамповой оснастки при случайном их занижении при механической обработке; ремонт поверхностных трещин глубиной до 3 мм; ремонт образующихся подрезов после наплавки штучными электродами; подварка задиров, сколов, забоин, раковин, пор; восстановление изношенных поверхностей штампов и пресс-форм; сварка калибров, мерительных скоб сложных конфигураций, прошедших предварительную цементацию, восстановление площадок заниженных рабочих поверхностей и прочее.
100