
книги / Материаловедение и технологии современных и перспективных материалов.-1
.pdf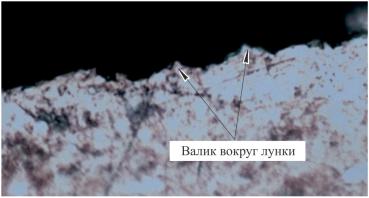
тура и свойства поверхностного слоя, образуются внутренние напряжения и другие физические явления.
Энергию импульса можно рассчитать по формуле
Wи = ∫0tи U I dtи,
где Wи – энергия импульса, Дж; I – сила тока, А; U – напряжение, подаваемое на электроды, В; tи – длительность импульсов (в зарубежной литературе обозначается ton), с.
Установлено, что в течение импульса металл с электрода-инстру- мента и электрода-детали удаляется в основном в жидком и газообразном состояниях. Как отмечалось ранее, рабочая жидкость окружающая канал разряда, испаряется, образуя газовую полость. В начальный момент скорость движения границ газовой полости достигает 200 м/с,
адавление в полости – сотен атмосфер. В результате обрабатываемый материал испытывает значительное механическое давление. После окончания импульса тока газовая полость по инерции продолжает расширяться, что наряду с конденсацией паров металла приводит к быстрому падению давления в ней, вплоть до давления ниже атмосферного. В момент, когда размеры газовой полости приближаются к набольшим,
адавление в ней к наименьшему, перегретый металл, который находится в образовавшейся лунке, вскипает и выбрасывается из нее. Реактивной струей паров металла оставшийся в лунке жидкий металл выдавливается из нее и, застывая, образует окаймляющийся валик (см. рис. 5.2 и 5.3).
Рис. 5.3. Лунка на поверхности ЭД при увеличении × 1000
111

В результате ЭЭО образуется поверхность, представляющая собой совокупность большого количества лунок. Основными характеристика-
ми лунок являются: радиус rл, глубина hл, их соотношение K = rл , hл
а также коэффициент перекрытия лунок β (отношение rл к расстоянию между соседними лунками L). В основном данные параметры и определяют основные показатели ЭЭ-процесса, такие как производительность, шероховатость обработанной поверхности и точность обработки.
Размеры лунок зависят от многих факторов, среди которых физи- ко-механические свойства обрабатываемого материала. Для оценки влияния этих свойств используется критерий фазового превращения Палатника. Данный критерий определяется как произведение основных физико-механических показателей:
П = сλρТП2,
где с – удельная теплоемкость материала; ρ – плотность материала; λ – коэффициент теплопроводности материала; Тп – температура плавления материала.
По данному критерию также можно судить об эрозионной стойкости того или иного материала. Чем выше значение критерия, тем выше эрозионная стойкость материала. Например, для стали У10
П = 4,79·1014 Дж·Вт/м4, для Х12Ф1 8,01·1014 Дж·Вт/м4.
5.2. ФАКТОРЫ, ВЛИЯЮЩИЕ НА КАЧЕСТВО ЭЭО
Как было изложено ранее, основным инструментом при расчете ЭЭО являются импульсы тока, образующиеся специальным генератором импульсов. Характеристики ГИ в основном и определяют технологические показатели ЭЭО. Основными парами периодических импульсов тока являются форма импульса, его длительность, частота следования и скважность. Импульсы характеризуются также крутизной переднего и заднего фронтов, максимальным и средним значением тока и напряжения, максимальной и средней мощностью и энергией.
На рис. 5.4 приведена идеальная прямоугольная форма импульса. Длительность включения импульса tи (ton – в зарубежных источниках) определяется временем его действия. При ЭЭО длительность импульса обычно лежит впределах от10–1…10–7 с. Дляконкретных условий
112
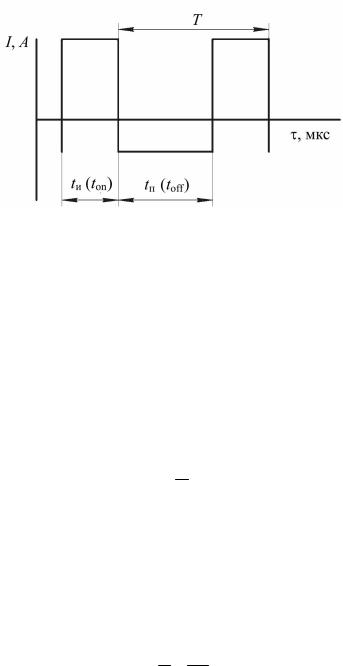
Рис. 5.4. Форма и параметры идеального импульса: tи (ton) – длительность включения импульса, мкс;
tп (toff) – длительность выключения (паузы) импульса, мкс; Т – период
обработки должна подбираться такая длительность импульса, чтобы соблюдались необходимые требования по производительности, точности и шероховатости поверхности.
Пауза tп – промежуток времени между двумя последовательно идущими импульсами. Период Т – промежуток времени, через который наблюдается повторение начала или окончания импульсов. Скважность q – отношение периода Т к длительности импульса tи:
q = T . tи
Различают скважность импульсов по ЭДС и по току. В первом случае скважность характеризуется при холостом ходе генератора, во втором – при нагрузке. Диапазон применяемых скважностей при электроэрозионной обработке находится в пределах от 1 до 30.
Частота импульсов f (измеряется количеством импульсов в секунду) определяется заданными длительностью и скважностью импульсов:
f = 1 = 1 .
T qtи
Амплитуда импульса – наибольшие значения, которых достигают изменяющиеся во времени величины тока или напряжения. Амплитуда импульсов тока изменяется при ЭЭО от единиц до тысяч ампер, а ам-
113
плитуда импульсного напряжения – от десятков до нескольких сотен вольт [10].
Энергия импульса – это работа (Дж), совершаемая единичным импульсом в МЭП. Как указывалось ранее,
Wи = ∫0tи U I dtи.
При технологических расчетах пользоваться этой величиной неудобно, и ее заменяют эквивалентной ей величиной средней мощности Рср или средним током Iср:
Pср = Uср Iср.
Производительность ЭЭО оценивается отношением объема или массы удаленного материала ко времени обработки, но в случае прово- лочно-вырезной ЭЭО под производительностью понимают отношение площади боковой поверхности паза ко времени обработки.
На производительность ЭЭО (Q) существенное влияние оказывают площадь обрабатываемой поверхности и состояние РЖ.
Для достижения высокой производительности необходимо правильно выбрать сочетание площади обрабатываемой поверхности и подводимой мощности.
ЛЕКЦИЯ 6. ТЕХНОЛОГИЯ ФИНИШНОЙ АБРАЗИВНОЙ ОБРАБОТКИ МАТЕРИАЛОВ
6.1.СУЩНОСТЬ АБРАЗИВНОЙ ОБРАБОТКИ ОБЛАСТИ
ЕЕПРИМЕНЕНИЯ
Одним из важнейших условий создания новых, более совершенных конструкций машин и приборов является повышение точности и качества обработки поверхностей деталей. Соблюдение жестких допусков на размер и форму деталей, уменьшение шероховатости рабочих поверхностей и удаление дефектного слоя металла – все это способствует увеличению износостойкости и срока службы деталей, повышению усталостной прочности и антикоррозионной стойкости, а также сохранению требуемых посадок в сопряжениях.
114
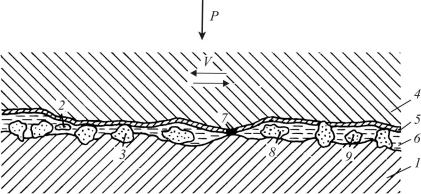
Из всех видов финишных операций доводке в наибольшей степени присущи черты искусства. Качество прецизионных деталей во многом зависит от умения, опыта, мастерства, а иногда и интуиции доводчика.
Наиболее распространенным в производстве процессом окончательной обработки поверхностей является процесс доводки «свободным» абразивным зерном. Особенность этого процесса состоит в том, что абразивные зерна (а точнее, смесь зерен с компонентами пасты или смазывающе-охлаждающей жидкости) под воздействием притира осуществляют съем металла. Притир не только сообщает зернам необходимые движения и усилия, но и обеспечивает требуемую точность обработки поверхности.
Процесс съема материала (формирование обработанной поверхности) при притирке осуществляется в результате действия абразивных зерен, химически активных элементов и рабочей поверхности притира на обрабатываемую поверхность рис. 6.1.
Рис. 6.1. Схема доводки: 1 – притир; 2 – стружка; 3 – шаржированное абразивное звено; 4 – обрабатываемая деталь; 5 – размягченный под химическим воздействием слой материала; 6 – жидкая фаза с химически активной добавкой; 7 – размягченный под воздействием трения слой материала; 8 – перекатывающееся абразивное зерно; 9 – осколок абразивного зерна
При доводке пластичных материалов, т.е. большинства металлов, съем осуществляется абразивными зернами, закрепленными на притире и царапающими обрабатываемую поверхность. При доводке хрупких материалов, наоборот, эффективно работают незакрепленные, свободные зерна, перекатывающиеся по поверхности детали и выкалывающие частицы материала.
115
В процессе доводки вследствие того, что притир имеет значительную твердость, распределение усилий между отдельными абразивными зернами происходит крайне неравномерно. Величина усилия, воспринимаемого каждым зерном, зависит от выступания его вершины над некоторым средним уровнем и может изменяться от предельного (разрушающего зерно) значения до нуля. Это обстоятельство является причиной интенсивного дробления абразивных зерен при доводке, но, с другой стороны, благодаря ему обеспечивается высокая точность геометрической формы обрабатываемой поверхности. Например, при плоскойдоводке случайное появление выпуклости или вогнутости на обрабатываемой поверхности немедленно вызывает такое перераспределение усилий, при котором съем металла увеличивается в зоне выпуклости и уменьшается в зоне вогнутости. При этом малейшая неплоскостность обрабатываемой поверхности вызывает значительные изменения сил резания в местах отклонений, т.е. процесс доводки твердым притиром обладает высокой чувствительностью к изменению геометрической формы поверхности.
Эта характерная особенность процесса доводки четко выявляет определяющую роль в формообразовании поверхности двух следующих факторов: точности геометрической формы рабочей поверхности притира
иоднородности зернового состава абразивного порошка, что принципиально отличает доводку от других видов абразивной обработки (например, отполирования), где названные факторы не имеют решающего значения.
Кчислу общих признаков, характеризующих процесс абразивной доводки, относятся:
1) одновременное воздействие на поверхность детали большого числа режущих зерен, протекающее при относительно низких скоростях
идавлениях;
2)движение режущих зерен по сложным траекториям;
3)незначительная роль тепловых явлений и отсутствие связанных
сними структурных изменений в поверхностном слое металла (как при шлифовании, точении, фрезровании).
На основании имеющихся результатов исследований и производственного опыта можно считать, что процесс доводки состоит из механических и химических явлений.
Механические явления сводятся к микрорезанию металла абразивными зернами с отделением мельчайших стружек либо к трению с изнашиванием обрабатываемой поверхности вследствие многократных пластических деформаций. Соотношение между процессами резания
116
итрения определяется свойствами обрабатываемого материала, геометрией и физико-механическими свойствами абразивных зерен, рабочим давлением и скоростью резания при доводке. Доводка резанием более производительна, но дает шероховатую поверхность, доводка же трением с изнашиванием, наоборот, менее производительна, но зато дает более чистую поверхность.
Химические явления при доводке заключаются в чрезвычайно быстром (сотые доли секунды, порядка 0,05) образовании окисных пленок
иадсорбционных слоев (8–15 нм), которые затем удаляются движущимися абразивными зернами. При этом существенная роль принадлежит жидким компонентам, входящим в состав пасты или суспензии, их составу и химической активности. Жидкие компоненты в процессе доводки выполняют следующие функции:
1)подводят абразивные зерна в рабочую зону, равномерно распределяют их по поверхности притира и создают зазор между притиром и деталью, необходимый дляразмещения идвижения абразивных зерен;
2)образуют поверхностные пленки и проникают в микротрещины обрабатываемого материала, что способствует его более интенсивному разрушению, т. е. повышают производительность доводки; Создают так называемое адсорбционное пластифицирование поверхностного слоя вследствие эффекта Ребиндера. Механизм этого эффекта заключается в облегчении выхода дислокаций (линейный дефект кристаллической структуры твёрдых тел) на поверхность тела при его деформировании, что обусловлено снижением поверхностной энергии твердого тела за счет действия содержащихся в пасте поверхносто-активных веществ. В результате снижается прочность металла, облегчается его пластическое течение и улучшается качество обработанной поверхности;
3)создают смазывающий слой, предохраняющий металлические поверхности детали и притира от непосредственного контакта, приводящего к их схватыванию и повреждению;
4)удаляют отходы процесса – частицы металла и абразива; (постоянной подаче суспензий);
5)охлаждают в процессе работы деталь и притир.
Образующийся на поверхности детали тончайший граничный слой смазки снижает режущее действие абразивных зерен и способствует получению менее шероховатой поверхности.
Таким образом, правильный выбор состава и дозировки жидких составляющих пасты или суспензии во многом способствует более производительному и качественному выполнению доводочных операций.
117
Абразивная доводка используется для получения высокой точности (допуски на размеры и отклонения от плоскости, плоскопараллельности
ицилиндричности составляют от 2–3 до 0,5–0,05 мкм) и малой шероховатости (Ra = 0,16…0,005 мкм) поверхности деталей.
Особенно целесообразно применение доводки при обработке тонких
илегкодеформируемых деталей, а также в случаях, когда необходимо сохранить специальные свойства исходного материала, изменяющиеся при значительных тепловых и силовых воздействиях, или удалить дефектный слой металла, образовавшийся при предшествующей обработке, в частности после шлифования. Наконец, методом взаимной доводки (притирки) прирабатываются друг к другу трущиеся и контактирующиеся поверхности деталей, работающих в паре, что обеспечивает высокую плотность прилегания иувеличение (до95 %) фактической поверхности контакта.
Доводка абразивом является высокопроизводительным процессом, так как в большинстве случаев в одном приспособлении производится одновременная обработка партии деталей от 3–4 до нескольких десятков штук.
Операции доводки широко применяются в различных отраслях промышленности при обработке калибров и эталонов, режущего и мерительного инструмента, поршневых пальцев и колец, деталей топливной аппаратуры, шаров, роликов и колец подшипников, шестерен, точных винтов, деталей арматуры, направляющих, столиков и наконечников оптико-механических приборов.
6.2. ФАКТОРЫ, ВЛИЯЮЩИЕ НА КАЧЕСТВО АБРАЗИВНОЙ ОБРАБОТКИ
Доводка плоскостей применяется для получения высокой точности геометрической формы и малой шероховатости поверхности детали. Достижение требуемой точности во многом зависит от правильного выбора абразивного материала (его твердости).
Важнейшими характеристиками твердых составляющих абразивных материалов являются: зернистость, гранулометрический состав, прочность, твердость, хрупкость, абразивная способность, химическая стойкость.
Такие материалы, как электрокорунд (нормальный, белый и монокорунд), электрокорунды с присадками хрома, титана, карбид бора, карбид кремния, природные и искусственные алмазы, кубический нитрид бора обладают высокой режущей способностью благодаря своей твер-
118
дости. Они применяются для обработки твердых сплавов, закаленных сталей, стекла, керамики.
В ряде случаев, в особенности при доводке мягких материалов (сырой стали, меди, свинца, латуни) лучшие результаты по производительности достигаются при использовании менее твердых абразивных материалов: окиси хрома, крокуса, каолина.
Притиры. Конструкция и размеры притиров зависят от формы и размеров обрабатываемой поверхности, а также оснащенности производства. Материал притира выбирают в зависимости от материала и механических свойств обрабатываемой детали, а также требуемой шероховатости поверхности обрабатываемой детали. В качестве материала для изготовления притиров применяют чугун, сталь, латунь, медь, оптическое стекло, текстолит, резину, кожу, древесину. Материал притира выбирают в соответствии со следующими общими требованиями:
1)притир должен быть по возможности мягче материала детали;
2)чем больше снимаемый припуск и выше зернистость абразива при притирке, тем выше должна быть твердость притира;
3)притир должен иметь удовлетворительную износостойкость;
4)абразивные зерна должны хорошо шаржироваться в поверхность притира;
5)притир должен обладать хорошими фрикционными свойствами. Чугунные притиры обеспечивают высокую производительность,
необходимые геометрические параметры поверхности, но более шероховатую поверхность, чем притиры из более мягкого материала. Их применяют при обработке деталей из наиболее твердых материалов и при использовании паст крупной зернистости. Стальные притиры применяют вместо чугунных в тех случаях, когда прочность чугуна оказывается недостаточной. Стальные притиры по сравнению с чугунными менее производительны, но имеют большую стойкость, в результате чего при работе с ними повышается точность обработки. Медные притиры, иногда со стальными сердечниками для повышения прочности, предпочтительно применять при притирке деталей пастами средней зернистости и относительно высоких требованиях к шероховатости поверхности. Фибровые притиры хорошо сохраняют форму при притирке пастами средней и мелкой зернистости, позволяют получать поверхность с малой шероховатостью. Кожаные, фетровые и войлочные притиры применяют только при работе пастами тонкой зернистости для полирования деталей до зеркального блеска.
119
Лучшие результаты при притирке стальных деталей достигаются при использовании притиров из серого перлитного чугуна без твердых включений и пористости с твердостью НВ 160–180.
Точность притираемых поверхностей зависит от точности рабочих поверхностей притиров, величина отклонения которых вследствие неравномерного износа при работе часто выходит за допустимые пределы. Для восстановления исходной точности геометрической формы рабочих поверхностей притиров, а также для обеспечения необходимой точности новых притиров их правят.
Правка притиров. Точность притираемых поверхностей зависит от точности рабочих поверхностей притиров, величина отклонения которых вследствие неравномерного износа при работе часто выходит за допустимые пределы. Для восстановления исходной точности геометрической формы рабочих поверхностей притиров, а также для обеспечения необходимой точности новых притиров их правят. Правку плоских притиров производят несколькими методами:
1.Предварительную правку на двухдисковых станках осуществляют резцом, закрепленным на оправке, установленной на кронштейне при правке верхнего притира или в центральном отверстии верхнего притира при правке нижнего. После правки резцом проводят взаимную притирку притиров с подачей абразивной суспензии. Основным недостатком этого способа является малый срок службы притиров при частой правке.
2.Правку осуществляют с помощью шлифовальной головки, установленной на консоли, смонтированной на притирочном станке. При этом методе торцовое биение и неплоскостность рабочей поверхности притира достигают 3–6 мкм. Основные недостатки этого метода – местный нагрев притира и появление дополнительных остаточных напряжений, приводящих к короблению притира.
3.Правку с помощью правильных колец в зависимости от типа притирочного станка осуществляют по двум схемам: а) непрерывная правка
впроцессе обработки– на однодисковых станках с правильными кольцами; б) периодическая правка через определенные интервалы времени на планетарных двухдисковых станках с правильными кольцами-шестернями, которые помещают между притирами вместо кассет-сепараторов. Недостаток правки с помощьюправильных колец – ускоренный износ притиров.
4.Метод «трех плит». Для осуществления этого метода правки необходимо иметь в одном комплекте три притира (плиты), которые притирают последовательно. Цикл правки приводится в табл. 6.1.
120