
книги / Материаловедение и технологии современных и перспективных материалов.-1
.pdf
Таблица 2.4 Принципы легирования жаропрочных сплавов
Основа |
Легирующий элемент |
Действие |
|
|
Cr, Mo, W, Nb, Ta, Ti |
Карбидообразование и твердорастворное |
|
|
упрочнение |
||
|
|
||
Ni |
Al, Cr |
Оксидообразование – стойкость против |
|
|
окисления и коррозии |
||
|
|
||
|
Hf |
Образование устойчивых дисперсных карбидов |
|
|
Cr, Mo, W, Nb, Al, C, B, Zr |
Твердорастворное упрочнение |
|
Fe |
Cr |
Стойкость против окисления и коррозии |
|
Ti, Al |
Дисперсное упрочнение |
||
|
|||
|
V, Mg, Mn |
Горячая деформируемость |
Суперсплавы. Сплавы на основе элементов VIII группы, разработанные для эксплуатации при повышенной температуре под воздействием механических нагрузок в условиях, при которых от материала требуется термическая стабильность. Работают при температурах, близких к температуре плавления (реактивные двигатели, атомные реакторы, газовые турбины). Суперсплавы применяют для изготовления специальных газотурбин (тяговых агрегатов космических кораблей, насосов ракетных двигателей, авиационных реактивных двигателей) сресурсомработыболее 100 000 ч.
Суперсплавы были получены в США путем введения небольших добавок титана и алюминия к жаростойкому хромоникелевому сплаву, что позволило существенно увеличить сопротивление ползучести. Алюминий ититанобразуют всплавахосновнуюупрочняющуюγ′-фазу Ni3 (Al, Ti).
Известные суперсплавы США: на никелевой основе Astroloy, Inconel 718, Rene 41, железоникелевые сплавы Hayness 556, N 155, кобальтовый сплав L605, работающие при температуре 980 ° С. Разработаны российские суперсплавы: ХН55ВМКЮ, работающий при температуре 950 ° С длительное время, ХН55ВМТКЮ – притемпературе 850 ° С.
Структура суперсплавов:
1)матрица (аустенит),
2)включения, когерентные матрице (γ′-фаза),
3)карбиды (в кобальтовых сплавах),
4)зернограничная фаза (улучшает сопротивление разрыву),
5)бориды в виде редких частиц по границам зерен (затормаживают диффузию на границах зерен),
6)плотно упакованные фазы.
41
2.6. ФУНКЦИОНАЛЬНО-ГРАДИЕНТНЫЕ МАТЕРИАЛЫ
Функционально-градиентные материалы (ФГМ) – композиционные или однофазные материалы, функциональные свойства которых систематически изменяются по объему или по одному из размерных параметров частицы, пленки или объемного образца.
Структура материала определяет свойства материала. Как правило, высокие эксплуатационные свойства имеют материалы с упорядоченной определенным образом ориентированной структурой.
Виды градиентных материалов:
1.Объемные материалы и покрытия, однородные по химическому составу, но с изменяющейся макро- и микроструктурой.
2.Объемные материалы с плавно меняющейся концентрацией компонентов, т.е. с отсутствием резкой границы раздела между областями с различными свойствами.
3.Объемные слоистые материалы и покрытия с переменным химическим и/или фазовым составом.
Объемные материалы и покрытия, однородные по химическому составу, но с изменяющейся макро- и микроструктурой. Структурно-неод-
нородные материалы могут быть полученыприоблучении образцов низко-
исреднеуглеродистых сталей Ст. 20 и У7 альфа-частицами с энергией 50 МэВ и отжигами при температуре 1173 К в течение 1 ч. В образцах формируется высокодисперсная структура с размером зерна 20–30 мкм, тогда как в областях, загороженных при облучении проволочными фильтрами, аустенитные зерна вырастают приотжигедо 300 мкм.
Объемные материалы с плавно меняющейся концентрацией ком-
понентов. Для улучшения эксплуатационных характеристик материалов активной зоны на основе циркония может проводиться их ионноплазменная обработка ионами металлов. Преимуществом данной технологии является то, что почти любой материал может быть имплантирован ионами, и его поверхностные слои могут обогащаться контролируемым количеством других элементов.
Объемные слоистые материалы и покрытия с переменным химическим и/или фазовым составом на основе легированных сталей. Этот класс композитов характеризуется тем, что фазы или компоненты расположены послойно. На субмикроструктурированном уровне слоистые композиционные материалы (КМ) могут быть реализованы при осаждении из паровой фазы, а на микроструктурированном уровне – в слои-
42
стых эвтектических структурах, полученных направленной кристаллизацией. На макроскопическом уровне слоистые КМ могут быть реализованы в парах металл– металл, полимер– полимер, металл– полимер. Они представляют собой слои разнородных материалов толщиной от 1000 мкм с различной природой границы раздела. Однако независимо от природы взаимодействия компонентов на границе раздела связь между слоями должна быть достаточной для исключения необратимого перемещения одного слоя относительно другого при взаимодействии механической нагрузкиитемпературы.
Методы получения слоистых ФГМ:
–метод порошковой металлургии – прессование в пресс-формах, экструзия;
–литье – ленточное, шликерное, центробежное;
–селективный метод;
–самораспространяющийся высокотемпературный синтез;
–нанесение покрытий и пленок;
–сварка – диффузионная, взрывом;
–химические: совместная химическая инфильтрация, электрофоретическое осаждение;
–комбинированные методы, сочетающие, например, пакетную прокатку или литейное плакирование с последующей прокаткой; сварку взрывом трехслойной заготовки с последующей горячей прокаткой.
Применение и перспективы слоистых композитов
Слоистые композиционные материалы – это важнейший класс композитов, обладающих широким спектром и уникальным сочетанием таких ценных свойств, как высокая прочность, коррозионная стойкость, электро- и теплопроводность, жаропрочность, износостойкость и др. Сегодня эти материалы находят все большее применение в судо-, авто-, тракторостроении, приборостроении, металлургической, горнодобывающей, нефтяной и других отраслях машиностроения. Из поли- и биметаллов изготавливают листы, ленты, трубки, проволоки, трубы, фасонные профили, детали и другие конструкции. Их использование позволяет существенно сократить расход высоколегированных сталей, дефицитных и дорогостоящих цветных металлов (Ni, Cu, Cr, Mo и др.).
Новые композитные материалы изготовлены из эпоксидной смолы и армированы волокнами упрочняющего наполнителя – волокнами смеси, запоминающей форму, и оптическими волокнами. Оптические во-
43
локна передают информацию о пункте, где «интеллектуальный композит» был перегружен, или о месте, где произошло его разрушение. Если стекловолокно деформируется, то эта длина волн изменяется. Интеллектуальные композиты, которые сами исправляются, найдут применение везде, где ремонт важных элементов едва возможен и даже невозможен. Первая область применения – это космическая техника, а также судостроение и аэронавтика. Возможное применение этих интеллектуальных материалов в массовых товарах, таких как лыжи или роликовые коньки, напротив, ограничено стоимостью производства.
2.7. АМОРФНЫЕ ВЕЩЕСТВА И СТЕКЛОМАТЕРИАЛЫ
Аморфные вещества – вещества, в которых отсутствуют кристаллические области (структуры дальнего порядка), обладающие изотропными свойствами.
Стекло – аморфное твердое тело, в котором отсутствуют дальний порядок и периодичность в расположении атомов.
Классификация аморфных веществ По типу связи:
–ковалентные (оксиды, элементы, органические полимеры);
–ионные (галогениды, нитраты);
–с водородной связью (водные растворы солей);
–с молекулярной связью (органические жидкости);
–с металлической связью (сплавы).
По химическому составу:
1)элементы (S, Se, Te,…);
2)оксидные (SiO2, B2O3, P2O5,…);
3)халькогенидные (As–S, As–Se, P–Se);
4)галогенидные (BeF2, ZnCl2);
5)нитратные (KNO3–Ca(NO 3)2);
6)смешанные (оксофторидные, галогенхалькогенидные);
7)водные растворы (HCl, LiCl, KOH, H2O2);
8)металлические (Au–Si, Fe–B, Co–P).
Аморфные вещества можно рассматривать как микро- и нанокристаллические с высокой плотностью дефектов структуры.
Классификация по кристаллической структуре:
1) халькогениды (1D) – линейные полимерные цепи, дефекты структуры – разветвления цепей;
44
2)бораты (2D) – треугольные бороксоловые группы BO3, дефекты – полиэдры BO4;
3)силикаты (3D) – тетраэдры SiO4, дефекты – немостиковый ки-
слород.
Склонность к стеклообразованию определяется значениями температуры плавления и вязкости расплава из уравнения Фогеля– Фулчера– Таммана:
η = η0exp(A/(T – T 0)),
где A = const, η – вязкость расплава при температуре Т, η0 – вязкость расплава при температуре плавления в равновесных условиях, T0 – равновесная температура стеклования. Чем ниже температура плавления и выше вязкость расплава, тем больше склонность к стеклообразованию.
1. Оксидные стекла Классификация оксидов:
–стеклообразующие оксиды – SiO 2, GeO2, B2O3, P2O5, As2O3;
–условно стеклообразующие оксиды – TeO2, SeO 2, MoO3, WO3,
Bi2O3, Al2O3, Ga2O3, V2O5.
Образование оксидных стекол подчиняются полуэмпирическим правилам В. Захариансена и Г. Роусона.
Кристаллохимические правила В. Захариансена (гибкий каркас из связанных по вершинам полиэдров):
1)координационное число кислорода ≤ 2, при этом образуется трехмерная сетка без дальнего порядка;
2)координационные числа других атомов невелики, структура – полиэдры, не требующие «плотной упаковки»;
3)координационные полиэдры сочленяются вершинами, структура – « рыхлая» и подвижная трехмерная сетка;
4)трехмерная сетка полиэдров, структурные единицы ближнего порядка.
Энергетические правила Г. Роусона (прочность связи кислорода):
1)значение отношения энергии связи и температуры плавения (Есв/Тпл) должно быть велико, Есв ≥ 330 кДж/моль, эти условия в расплаве повышают вязкость, затрудняют перестройку расплава в кристалл;
2)низкоплавкие эвтектики склонны к стеклованию.
45
Метод синтеза стеклокерамики – кристаллизация стекла при воз-
никновении зародышей с плотностью их распределения 1012–10 15/см3:
1)гетерогенная кристаллизация: в коллоидный раствор Cu, Ag, Au, Pt добавляют частицы TiO2, P2O5, ZrO2, происходит ликвация, поверхностное натяжение понижается, появляется возможность эпитаксиального роста кристаллов;
2)гомогенная кристаллизация: отжиг ниже стеклования Tg. Структура стеклокерамики – поликристаллическая с размерами
кристаллов d = 0,1…1 мкм, полностью или частично закристализованная.
Свойства:
–высокая плотность (3…4)10 3 кг/см3, которая снижает склонность
кразвитию трещин;
–регулируемый коэффициент термического расширения (КТР)
(0…2)10 |
–5 ; |
– |
высокая температура деформации (1000…1200 ° С); |
–изоляционные свойства;
–регулируемая прозрачность;
–пористость 0 %.
Области применения:
–обкладка печей;
–сочленение металла и керамики;
–теплозащитная оболочка ракет;
–печатные платы;
–оптические волокна (оксид кремния);
–ксерокс (халькогениды).
2. Аморфные металлы
Аморфные металлы (металлические стёкла) – класс металличе-
ских твердых тел с аморфной структурой, характеризующейся отсутствием дальнего порядка и наличием ближнего порядка в расположении атомов. В отличие от металлов с кристаллической структурой аморфные металлы характеризуются фазовой однородностью, их атомная структура аналогична атомной структуре переохлаждённых расплавов.
Аморфные сплавы подразделяются на 2 основных типа: металлметаллоид и металл-металл.
При аморфизации методом закалки из жидкого состояния могут быть получены сплавы, содержащие следующие элементы:
46
– для типа металл-металлоид: B, C, Si, Al, P, Ti, V, Cr, Mn, Fe, Co,
Ni, Cu, Ge, As, Zr, Nb, Mo, Rh, Pd, Ag, Sn, Te, Hf, Ta, W, Ir, Pt, Au, Tl, La;
– для типа металл-металл: Be, Mg, Al, Ca, Ti, V, Fe, Co, Ni, Cu, Zn, Ga, Sr, Y, Zr, Nb, Rh, Pd, Ag, Sb, Hf, Ta, Re, Ir, Pt, Au, Pb, La, Ce, Pr, Nd,
Sm, Eu, Gd, Th, Dy, Ho, Er, Lu, Th, U.
Существуетмножествоспособовполученияметаллическихстёкол. 1) осаждение газообразного металла:
–вакуумное напыление,
–распыление,
–химические реакции в газовой фазе;
2)затвердевание жидкого металла:
– закалка из жидкого состояния;
3)нарушение кристаллической структуры твёрдого металла:
– облучение частицами,
– воздействие ударной волной,
– ионная имплантация;
4)электролитическое осаждение из растворов.
Закалка из жидкого состояния является основным способом получения металлических стёкол. Этот метод заключается в сверхбыстром охлаждении расплава, в результате которого он переходит в твёрдое состояние, избежав кристаллизации, – структура материала остаётся практически такой же, как в жидком состоянии. Он включает в себя несколько методов, которые позволяют получать аморфные металлы
вформах порошка, тонкой проволоки, тонкой ленты, пластинок. Также были разработаны сплавы с малой критической скоростью охлаждения, что позволило создавать объёмные металлические стёкла. Для получения пластинок и порошков массой до нескольких сотен миллиграмм капля расплава с большой скоростью выстреливается на охлаждаемую медную плиту, скорость охлаждения при этом достигает 109 °C/ с. Для получения тонких лент шириной от десятых долей до десятков миллиметров расплав выдавливается на быстро вращающуюся охлаждающую поверхность. Для получения проволок толщиной от единиц до сотен микрон применяются разные методы. В первом расплав протягивается
втрубке через охлаждающий водный раствор, скорость охлаждения при этом составляет 104–10 5 °C/ с. Во втором методе струя расплава попадает
вохлаждающую жидкость, которая находится на внутренней стороне вращающегося барабана, где удерживается за счёт центробежной силы.
47
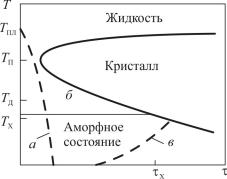
Использование специальных методов позволяет достигать скорости охлаждения более 105 К/с и получать металл в стеклообразном аморфном состоянии. На рис. 2.11 представлено схематическое изобра-
жение ТТТ-диаграммы (temperature–time–transformation), которая пока-
зывает характер фаз, образующихся в сплаве при различных скоростях охлаждения. При переохлаждении жидкой фазы ниже равновесной температуры плавления ТПЛ скорость кристаллизации достигает максимума при температуре ТП. Если жидкость закалить со скоростью выше критической до температуры стеклования ТД, то система будет «заморожена» и образуется аморфное состояние.
Рис. 2.11. Диаграмма процесса образования фаз в переохлажденном расплаве: а – критическая скорость охлаждения с получением аморфного состояния; б – изотермический отжиг аморфного состояния, приводящий к кристаллизации в период времени t К; в – медленный нагрев аморфного состояния, ведущий к кристаллизации
при температуре Тх
Критическая скорость охлаждения для разных аморфных сплавов составляет от 102 до 1010 К/с. Из диаграммы также следует, что если аморфный сплав впоследствии нагреть до температуры Т < ТП и выдерживать изотермически в течение времени tК; он начнет кристаллизоваться. Если же аморфный сплав медленно нагревать от комнатной температуры, то кристаллизация начинается при температуре ТХ, которая повышается по мере увеличения скорости нагрева. Условия перехода в кристаллическое состояние меняются в широких пределах для разных аморфных систем.
Следствием такой аморфной структуры являются необычные магнитные, механические, электрические свойства и коррозионная стойкость аморфных металлических сплавов. Наряду с высокой магнитной мягко-
48
стью (уровень электромагнитных потерь в аморфных сплавах с высокой магнитной индукцией существенно ниже, чем во всех известных кристаллических сплавах) эти материалы проявляют исключительно высокую твердость и прочность при растяжении, в ряде случаев имеют близкий к нулю коэффициент теплового расширения, а удельное электросопротивление в 3–4 раза выше для железа и его сплавов. Некоторые из аморфных сплавов характеризуются высокой коррозионной стойкостью.
Затвердевание с образованием аморфной структуры принципиально возможно для всех металлов и сплавов. Для практического применения обычно используют сплавы переходных металлов (Fe, Co, Mn, Cr, Ni и др.), в которые для образования аморфной структуры добавляют аморфообразующие элементы (В, С, Si, P, S). Такие аморфные сплавы обычно содержат около 80 % (ат.) одного или нескольких переходных металлов и 20 % неметаллов, добавляемых для образования и стабилизации аморфной структуры. Состав аморфных сплавов близок к формуле
M80Х20,
где М – один или несколько переходных металлов, а Х – один или несколько аморфизаторов. Известны аморфные сплавы, состав которых отвечает приведенным формулам: Fe70Cr10P15B5, Fe40Ni40S14В6, Fe80P13B7
идр. Аморфизаторы понижают температуру плавления и обеспечивают достаточно быстрое охлаждение расплава ниже его температуры стеклования так, чтобы в результате образовалась аморфная фаза. На термическую стабильность аморфных сплавов оказывают наибольшее влияние кремний
ибор, наибольшей прочностью обладают сплавы с бором и углеродом, акоррозионная стойкостьзависитотконцентрации хрома ифосфора.
Аморфные сплавы находятся в термодинамически неравновесном состоянии. В силу своей аморфной природы металлические стекла имеют свойства, присущие неметаллическим стеклам: при нагреве в них проходят структурная релаксация, «расстекловывание» и кристаллизация. Поэтому для стабильной работы изделий из аморфных сплавов необходимо, чтобы их температура не превышала некоторой заданной для каждого сплава рабочей температуры.
Свойства и применение аморфных сплавов
Аморфные металлы часто называют материалами будущего, что обусловлено уникальностью их свойств, не встречающихся у обычных кристаллических металлов (табл. 2.5).
49
Таблица 2.5 Свойства и области применения аморфных металлических материалов
Свойство |
Применение |
Составсплава |
Высокаяпрочность, высо- |
Проволока, армирующие мате- |
Fe75Si15B10 |
каявязкость |
риалы, пружины, режущий инст- |
|
Высокая коррозионная |
румент |
|
|
|
|
стойкость |
|
|
Высокая магнитная индук- |
Электродныематериалы, фильтры |
Fе45Сr25Мo10Р13С7 |
ция насыщения, низкие |
для работы врастворах кислот, |
|
потери |
морскойводе, сточныхводах |
|
Высокаямагнитная прони- |
Сердечники трансформаторов, |
Fe81B15C2 |
цаемость, низкая коэрци- |
преобразователи, дроссели |
|
тивная сила |
Магнитныеголовкииэкраны, маг- |
Fe5Co70Sl10B15 |
|
||
|
нетометры, сигнальныеустройства |
|
Постоянство модулейуп- |
Инварныеи элинварные материалы |
Fе83В17 |
ругостиитемпературного |
|
|
коэффициенталинейного |
|
|
расширения |
|
|
|
|
|
Уникальный характер металлических стекол проявляется в физи- ко-механических и химических свойствах. Отсутствие свойственной кристаллам периодичности в структуре оказывается причиной высокой прочности, магнитомягкого поведения, крайне низких акустических потерь и высокого электросопротивления. Процессы усталостного разрушения и намагничивания в металлических стеклах и кристаллических металлах во многом схожи. Химическая однородность обусловливает высокую коррозионную стойкость некоторых металлических стекол в кислых средах, а также растворах, содержащих ионы хлора. Почти неограниченная взаимная растворимость элементов в стеклообразном состоянии представляет большой интерес для изучения процессов электронного переноса при низких температурах.
Вследствие металлического характера связи многие свойства металлических стекол значительно отличаются от свойств неметаллических стекол. К ним относятся вязкий характер разрушения, высокие электро- и теплопроводность, оптические характеристики.
Плотность аморфных сплавов лишь на 1–2 % меньше плотности соответствующих кристаллических тел. Металлические стекла имеют
50