
книги / Материаловедение и технологии современных и перспективных материалов.-1
.pdfдавления. Для лучшего заполнения форм порошком, устранения «арочного эффекта», а также с целью получения ППМ с равномерной пористостью форму при засыпке подвергают вибрации (вручную или на вибровстряхивателе). Основное требование к материалу формы– отсутствие взаимодействия с материалом порошка при температуре спекания. Для порошков цветных металлов применяют стальные или графитовые формы, а для черных металлов – керамические. Предотвращению припекания частиц порошка к стенкам формы способствуют их покрытие подходящей суспензией, например глинозема с водой, и последующая сушка. Теоретически габариты заготовок, сформованных свободной засыпкой порошка в формы, не ограничены – они определены размерами пространства печей спекания.
Шликерным литьем изготовляют пористые детали сложной формы. Спекание пористых материалов, изготовленных из металлов, сплавов или металлоподобных соединений, осуществляется в вакууме или в защитной атмосфере водорода, диссоциированного аммиака, конвер-
тированного природного газа, эндогаза без расплавления.
Получение волокновых материалов. Технология включает в себя следующие стадии:
1)изготовление волокна;
2)формование волокон – прокатка, прессование, войлокование (жидкостное, воздушное, вибрационное, в магнитном или электрическом поле) или плетение;
3)спекание.
Изготовление волокна. Волокна могут быть получены волочением проволоки, однако для многих малопластичных сплавов и керамики этот вариант неприемлем.
Одной из распространенных технологий получения волокон (как металлических, так и керамических) является экстракция из расплава с помощью вращающегося охлаждаемого диска-кристаллизатора. Расплавление металлического стержня производят с помощью электроннолучевой пушки (ЭЛП) или индукционного нагрева. Минимальный диаметр получаемых таким способом волокон и лент составляет 30 мкм, а длина может быть неограниченной.
Форма поперечного сечения волокна зависит от адгезионного взаимодействия материалов волокна и диска, угла заточки диска, скорости вращения диска, скорости охлаждения и других параметров. Спека-
21
ние волокновых материалов проводят по тем же режимам, что и для соответствующих порошков.
Технология копирования матрицы. Матрицей для получения по-
ристых проницаемых материалов обычно служит пористый пенополиуретан (ППУ). Технология включает в себя следующие стадии:
1)подготовка порошка;
2)подготовка связующего;
3)приготовление шликера;
4)подготовка матрицы (включая придание электропроводности);
5)нанесение порошка (пропитка шликером или гальваностегия);
6)сушка заготовки;
7)удаление матрицы путем выжигания ППУ;
8)спекание заготовки.
Структура проницаемого ячеистого материала (ВПЯМ) состоит из ячеек, имеющих размеры, соответствующие размерам ППУ
Катализаторы на носителях ячеистой структуры
Основные виды пористых проницаемых материалов:
1)ячеистые (преимущество – более интенсивный тепло- и массообмен);
2)сотовые (преимущества: меньше гидравлические потери при высоких скоростях потока; выше стойкость к динамическим нагрузкам).
Если нет конструктивных ограничений по площади фильтрации, ячеистые носители однозначно предпочтительнее.
Приготовление ячеистого катализатора включает в себя сле-
дующие стадии:
1)изготовление блочного носителя (проницаемый ячеистый металл или керамика) дублированием структуры ППУ с предварительной пропиткой ППУ керамической суспензией или электрохимическое дублирование ППУ и последующая термодиффузионная обработка;
2)нанесение вторичного носителя – γ -Al2O3;
3)нанесение каталитически активного компонента – Pd ( пропитка
солью паладия → сушка → прокаливание в среде дисаммиака).
Свойства пористых проницаемых материалов
Свойства пористых проницаемых материалов (ППМ) разделяют на три большие группы: структурные, функциональные, каркасные.
22
Структурные свойства ППМ: пористость и ее распределение, размер пор и их распределение, форма пор и степень их извилистости,
удельная поверхность пор.
Функциональные свойства пористых проницаемых материалов – тонкость очистки, капиллярный потенциал.
К каркасным свойствам относятся плотность и ее распределение, характеристики межчастичных контактов.
Применение пористых материалов
Применение пористых проницаемых материалов. Основное на-
значение – фильтры. В настоящее время в связи с развитием техники высоких температур большое внимание уделяют применению ППМ для охлаждения «выпотеванием» (так называемых «потеющих» материалов): к нагретой поверхности «потеющих» деталей через поры в материале поступает охлаждающая жидкость или газ и, испаряясь, понижает температуру поверхности. Изделия из пористых материалов могут обеспечивать равномерный подвод газа или жидкости, например, в устройствах, создающих кипящий слой, осуществляющих пневмотранспортирование сыпучих тел, их охлаждение или сушку, смешивание и т.п. Порошковые пористые материалы используют в качестве эффективной преграды распространению пламени, которое гаснет, проходя через узкие капилляры. Пористые электроды находят широкое применение в различных электрохимических процессах.
Применение пористых непроницаемых материалов. Металличе-
ские пены из алюминия, магния, стали, титана или цинка выдерживают высокое давление, приглушают звук, ослабляют вибрации, хорошо изолируют, а потому успешно применяются для защиты от ударов в автомобилестроении. Они легко поддаются сверлению, распиливанию и фрезерованию. Применяются как биологически совместимый протез костной ткани в медицине.
Прочность алюминиевых пористых панелей обусловливает возможность их использования в новых моделях облегченных автомобилей, а также для изготовления корпусных шумозаглушающих деталей, электромагнитных экранов в виде настенных и потолочных плит, защищающих от проникновения электромагнитных волн частотой от 0,1 до 1000 МГц или вредных излучений, а также корпусов электронных приборов; тепловых экранов. Пористые панели можно использовать как
23

легкий строительный материал в качестве несгораемой альтернативы дереву и пластмассам (могут поставляться в виде плит с максимальными размерами 625 × 625 мм, толщиной от 8 до 25 мм); как гасители удара для автомобильного и рельсового транспорта; как шумогасители, работающие в тяжелых условиях (высокая температура, влажность, пыль, вибрация), в стерильных или пожароопасных помещениях (самолетах, отелях, универмагах, промышленных зданиях).
Цинковая «пена» может найти применение в качестве держателя активного материала в свинцово-кислотных аккумуляторах, что делает возможным создание сверхлегких электродов. «Пена» на основе серебра или золота вполне может использоваться в ювелирной промышленности.
Разработка процессов получения «пены» таких металлов, как сталь
ититан, может расширить сферу применения пористых металлов, включая отрасли производства, где требуются высокая теплостойкость
ипрочность. В силу хорошей совместимости таких металлов с биотканями они могут найти применение в изготовлении протезов (в частности, титановая «пена»).
2.2. СВЕРХТВЕРДЫЕ МАТЕРИАЛЫ
Сверхтвердые материалы – моно- и поликристаллические вещества, микротвердость которых больше микротвердости корунда. Из природных сверхтвердых материалов (СТМ) существует только алмаз, все остальные – синтетические материалы (табл. 2.1).
Твердость и ее связь с другими характеристиками могут быть выражены суммой действующих в месте контакта сил:
H = M |
|
E0ac |
+ M |
|
E0ac2 |
|
b |
+ M |
|
E0ac |
+ M |
|
E0ac |
, |
|
|
2 d 3 |
|
|
|
|||||||||
|
1 d 2 d |
|
d0 |
3 d 2 L |
4 d 2 |
где М1, М2, М3, М4 – коэффициенты пропорциональности; G – модуль сдвига; b – вектор Бюргерса – параметр, характеризующий дефектность структуры, расстояние, на которое смещена дислокация; d – межатомное расстояние; d0 – расстояние между атомами в соседних плоскостях сдвига; L – критическая длина трещины; Е0 – энергия межатомных связей; ac – уровень ковалентности.
24
Таблица 2.1
Синтетические сверхтвердые материалы с твердостью выше, чем у корунда
№ п/п |
Вещество |
HV, кг/мм2 |
1 |
Алмаз |
10 000 |
2 |
Кубический нитрид бора BN |
9250 |
3 |
Карбид бора B4С |
4900 |
4 |
Карбид кремния SiC |
3500 |
5 |
Корунд Al2O3 |
2000 |
Таким образом, твердость вещества может быть аналитически выражена через энергию межатомных связей, уровень ковалентности, межатомное расстояние, характеристики сопротивления деформированию (b) и разрушению (L). Из уравнения следует, что межатомные расстояния в сверхтвердых материалах должны быть малыми, ковалентные связи – жесткими и направленными, число связей больше 3, упаковка должна быть наиболее плотной.
Приатмосферном давленииграфит– это устойчивая фаза, поэтому:
Hгр < Hал, |
|
|
∆ Нгр → ал (Т) = Hал – Hгр > 0, |
|
|
∆ Gгр → ал = Gал – Gгр = – T (Sгр – Sал) + р (Vгр – |
Vал). |
(*) |
Поскольку р (Vгр – Vал) > 0, следовательно, ∆ Gгр → |
ал < 0 при р < 0 |
(должно происходить сжатие).
Из (*) следует, что при большом давлении фазовый переход может переходить только в фазу с меньшим удельным объемом. Таким образом, общей тенденцией фазовых превращений в твердых телах является увеличение физической плотности за счет структурных изменений.
Например, вычисленные по уравнению Лейпунского p = 0,55 + 2,64 · 10–3 · Т
значения температуры составили 4000 К, а давления – 12 ГПа. Механизм атомной перестройки графита в алмаз обусловлен изме-
нением конфигурации sp2 (графит) → sp3 (алмаз).
Под действием изменения давления происходит сжатие графита по оси С и сдвижка углеродных слоев, что приводит к образованию ромбоэдрической модификации графита с уменьшенным расстоянием между угле-
25
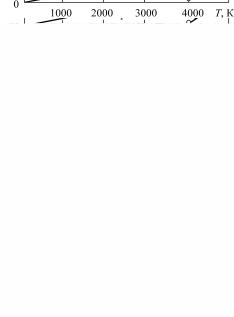
родными слоями. Такой сдвиг с энергетической точки зрения протекает легко под действием градиентов давления и температуры, так как силы связи между слоями графита в 6 раз слабее, чем в слое. Затем вэтой промежуточной форме плоские углеродные слои гофрируются иполучается структура алмаза.
Это превращение имеет признаки мартенситного перехода. Влияние давления на фазовые превращения зависит от положения
элемента в Периодической системе элементов Менделеева.
Вряду при увеличении главного квантового числа n у легких элементов в условиях высоких давлений формируется структура, характерная для более тяжелых элементов при начальных условиях. Давление перехода из одного структурного типа в другой уменьшается с ростом атомного номера элемента.
Вгруппе с высоким атомным числом структуры верхних элементов при воздействии давления изменяются на тип более тяжелый.
Современная фазовая диаграмма углеродных фаз представлена на рис. 2.4.
Рис. 2.4. Обобщенная фазовая диаграмма системы «графит – плотные формы углерода»: 1 – область каталитического превращения графит– алмаз; 2 – область прямого превращения графит– алмаз или графит– лонсдейлит; 3 – линия плавления метастабильного графита; 4 – гипотетическая область превращения в металлическую форму углерода; 5 – область ударной закалки графита с превращением в алмаз и в лонсдейлит
26
Синтез алмаза при высоком статическом давлении и высокой температуре. Первые успешные опыты по синтезу алмаза были проведены 15 февраля 1953 г. в Шведской электрической компании ASEA (Швеция) и 16 декабря 1954 г. в «Дженерал электрик» (США).
В настоящее время используются следующие способы синтеза алмазов: получение алмаза при высоких статических давлениях и высоких температурах, в том числе каталитический синтез; ударным сжатием; горячим изостатическим прессованием (ГИП); из газовой фазы при низких давлениях; лазерный синтез; плазменное осаждение; детонационное напыление и др.
Алмазные пленки. Правильнее называть алмазные пленки углеродными, так как улеродные пленки имеют структуру только ближнего порядка, соответствующую алмазной. Структура такой пленки – трехмерное изотропное образование атомов углерода, сгруппированных в алмазоиграфитоподобные фрагменты структуры.
Свойства пленок:
– плотность – 2,4–4,0 г/см3;
–прозрачность, твердость, световой показатель преломления,
–химическая стойкость, как у природного алмаза;
–высокая теплопроводность (выше, чем у Cu и Ag);
–термическая стабильность на воздухе (до 600 °C).
Применение пленок:
–износоустойчивый инструмент – подшипники;
–оптические системы – линзы, очки;
–средства связи – излучающие элементы громкоговорителей, воспроизводящие звук с предельной частотой;
–элементы микросхем компьютеров; в качестве полупроводника алмазная пленка может заменить Si или Ge; пленки позволяют уменьшить размеры схемы и увеличить скорость работы.
Способы получения пленок
Паровое осаждение:
PVD – физическое паровое осаждение, CVD – химическое паровое осаждение,
PACVD – химическое осаждение при участии паровой плазмы, MOCVD – металлоорганическоепаровоеосаждениеизпаровойфазы, PECVD – плазмохимическое осаждение.
Сущность паровых способов заключается в отрыве атомов водорода от молекул метана (CH4) или других углеводородов и в образова-
27
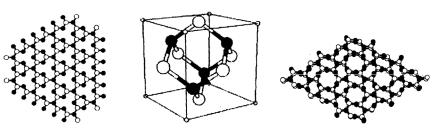
нии связей C–C при осаждении на поверхности. Контроль параметров процесса обеспечивает образование алмаза, а не графита. Основным компонентом является углеводород. Водород в этих процессах предотвращает образование двойных связей между атомами углерода. В результате углерод соединяется одинарными связями, необходимыми для образования алмазных кристаллов.
Нитрид углерода. В 1989 г. Liu и Cohen рассчитали возможность существования нитрида углерода (C3N4), который имеет в структуре одинарные, двойные, тройные ковалентные связи и существует в трех модификациях (рис. 2.5).
а |
б |
в |
Рис. 2.5. Кристаллические решетки ромбоэдрического (а), кубического (б) и гексагонального (в) нитрида углерода
В структуре гексагонального нитрида углерода (β -C3N4) находятся азот в sp2-гибридизации, самая высокая энергия связей, наиболее устойчивая структура; решетка в виде трехмерных решеток с 6, 8, 12 замкнутыми кольцами с чередующимися атомами углерода и азота; каждый атом углерода находится в искаженной тетраэдрической координации из атомов азота; каждый атом азота имеет трехкратную координацию из атомов углерода, расположенных с атомами азота в одной плоскости. Свойства: минимальная сжимаемость, модуль упругости примерно равен модулю упругости для алмаза.
Методы получения β -C3N4: ионно-лучевое осаждение; импульсная лазерная абляция; ионное и вакуумное осаждение; магнетронное осаждение; плазменное разложение CH4, N2. Исходные вещества: графит, аморфный углерод, C60 и криогенный азот.
Наличие sp2-гибридизации с короткими связями дает основание предположить возможность синтеза нанотрубок состава BxCyNz, которые будут служить новыми формами тонких покрытий или армирующих систем. Уже получены нанотрубки BN, BC2N, BC3.
28
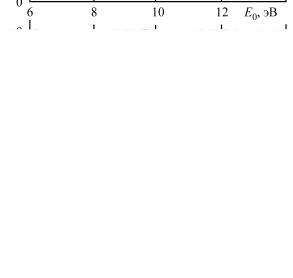
Нитрид бора. Среди СТМ нитрид бора обладает наиболее высокой твердостью, зависящей от энергии межатомных связей (рис. 2.6).
Рис. 2.6. Зависимость микротвердости от энергии межатомной связи для СТМ
Нитрид бора существует в нескольких модификациях: гексагональная структура, решетка вюрцита и обладающая алмазоподобной структурой решетка сфалерита (BN, BP, AlP, SiC).
Способы получения нитрида бора сходны со способами получения синтетического алмаза.
Алмазныйиабразивныйинструмент. Инструментделитсянадвавида:
1.Режущий элемент из СТМ (один или несколько), закрепленный
воправке, – буровые коронки, карандаши, резцы. Режущий элемент прикрепляется методом пайки, накатки, чеканки, опрессовки илизавальцовки.
2.Композиционный – режущий, шлифовальный, содержащий множество алмазных зерен, распределенных в матрице. Структура композиционного инструмента сложнее и содержит несколько фаз, выполняющих определенные функции, изготавливается методами порошковой металлургии, гальванохимии, электроконтактного спекания частиц СТМ.
Рассмотрим преимущества и недостатки наиболее распространенных видов алмазного инструмента (АИ), изготовленного с использованием гальванического нанесения алмазного покрытия, методом порош-
29

|
ковой металлургии и спекания алмазных |
|||
|
частиц. |
|
|
|
|
К достоинствам гальванического алмаз- |
|||
|
ного инструмента(рис. 2.7) следуетотнести: |
|||
|
1) возможность |
достаточно |
плотно |
|
|
уложить зерна на поверхности заготовки и, |
|||
|
как следствие, получение высоких режу- |
|||
|
щих свойств; |
|
|
|
|
2) возможность |
изготавливать |
доста- |
|
Рис. 2.7. Конструкция |
точно мелкие формы инструмента для су- |
|||
пертонкой работы, что практически невоз- |
||||
гальванического АИ |
||||
можно при других способах; |
|
|||
|
|
|||
3) возможность изготавливать самый широкий спектр форм ин- |
||||
струмента; |
|
|
|
|
4) относительную простоту изготовления |
и низкое содержание |
в нем алмазных зерен, что позволяет изготавливать инструмент с наименьшими затратами, следовательно, продавать его по цене значительно ниже, чем другие виды алмазного инструмента.
К слабым сторонам этого вида инструмента можно отнести:
–снижение режущих свойств по мере изнашивания единственного слоя алмаза, его постепенное затупление;
–« облысение» тех участков кромок рабочей части инструмента, которые эксплуатируются больше других;
–относительную недолговечность инструмента, так как после снашивания одного слоя он практически приходит в негодность.
Рис. 2.8. Конструкция инструмента, изготовленного методом порошковой металлургии
Основные достоинства спеченного ал-
мазного инструмента (рис. 2.8):
1)высокая износостойкость, долговечность, обеспечиваемая наличием множества слоевалмаза по всему объему инструмента;
2)стабильность режущих свойств, обеспечиваемая постоянным обновлением глубинных слоев алмаза, которые обнажаются по мере изнашивания верхних слоев.
3)прирабатываемостьи«мягкая» работа. К слабым сторонам следует отнести:
– невозможность изготовления очень
мелких форм из-за механического крепле-
30