
книги / Материаловедение и технологии современных и перспективных материалов.-1
.pdfТакже преимуществом этой технологии является возможность использования ее для процессов быстрого прототипирования (Rapid prototyping), т.е. создания деталей на основе ранее построенных их трехмерных CAD-моделей. Быстрое прототипирование может быть использовано для послойного создания деталей со свойствами, которые могут быть уникальными для данного типа деталей, такими как однородная структура, улучшенные механические свойства во всем объеме детали, создание сложной геометрии без применения традиционных методов лезвийной обработки. В связи с ее аддитивной природой (от англ. to add – добавлять, т.е. материал не удаляется с заготовки в виде стружки, а добавляется к ней в нужном количестве в виде порошка или проволоки) лазерная наплавка может быть применена для изготовления деталей, инструментов и оснастки, когда необходимо преодолеть ограничения существующих технологий обработки.
Врезультате можно привести ряд преимуществ данной технологии:
1)сокращение производственного времени;
2)контроль температурного воздействия лазера: в процессе наплавки также можно управлять подаваемой энергией для контроля ско-
рости кристаллизации и формирования желаемой микроструктуры
имеханических свойств;
3)ремонт инструмента: лазерная наплавка увеличивает срок службы инструмента и во многих случаях позволяет восстановить дорогостоящий инструмент, который в противном случае должен быть заменен;
4)производство функциональных биметаллических изделий: лазерная наплавка позволяет без труда наносить друг на друга различные по химическому составу и механическим свойствам материалы;
5)создание «умных структур»: лазерная наплавка дает возможность создания «умных структур», позволяя внедрять в детали такие объекты, как датчики и магниты, непосредственно в процессе изготовления самой детали.
Direct Metal Laser Sintering (DMLS) – « прямое металлическое ла-
зерное спекание» – аддитивная технология, разработанная компанией EOS из Мюнхена (Германия), которую иногда также называют технологией селективного лазерного спекания (SLS-технология) или селективного лазерного плавления (SLM). Этот процесс связан с использованием
3D CAD-модели, по которой будет создан файл *.STL (stereolitography)
иотправлен на программное обеспечение машины. Техник, работающий с этой 3D-моделью, правильно ориентирует деталь. После того как
101
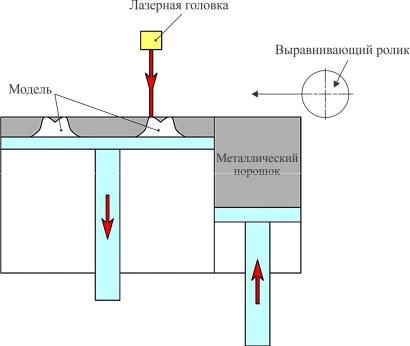
«построение файла» было завершено, программное обеспечение машины разбивает модель на слои, и машина начинает построение. Машина DMLS использует Yb-волоконно-оптические лазеры. В таких устройствах строительным материалом является металлический порошок (рис. 4.9). Порошок подается из питателя (контейнер) и с помощью специального ролика тонким слоем выравнивается по поверхности рабочей платформы. Луч лазера обводит контур первого слоя будущей модели и затем сканирует всю область внутри него. В результате термического воздействия излучения лазера частицы порошка оплавляются или расплавляются полностью, а после его отхода от рабочей области затвердевают, образуя сплавленную или спеченную структуру.
Рис. 4.9. DMLS-процесс
После завершения первого слоя платформа опускается на глубину следующего слоя и наносится очередной слой порошка. Второй и последующий слои создаются по такому же принципу с тем отличием, что новый слой наносится непосредственно на предыдущий.
Таким образом, слой за слоем, процесс продолжается до полного построения объекта. Модель при этом всегда находится в ванне из неспеченного порошка, которая является опорой для детали, что позволяет
102
исключить из процесса дополнительные построения в виде технических поддержек. В данном процессе материал проходит стадию расплавления (перехода в жидкое состояние) и затем отверждения.
Толщина слоя при таком процессе довольна мала и составляет, как правило, 20 мкм. Этот процесс позволяет строить детали с геометрией, которую сложно или невозвожно выполнить с помощью традиционных методов металлообработки.
DMLS-процесс имеет много преимуществ по сравнению с традиционными методами производства. Не требуется никаких специальных инструментов, и деталь может быть построена в течение нескольких часов. Диапазон используемых материалов достаточно широк – от мягких алюминиевых порошков, до твердых стальных. Эта технология используется при производстве деталей для различных отраслей промышленности, включая аэрокосмическую, стоматологическую, медицинскую и другие отрасли промышленности, которые имеют небольшие и среднего размера очень сложные детали. Технология очень эффективна в отношении времени производства. Технология используется для быстрого прототипирования, поскольку уменьшает время разработки новых продуктов, и для производства продукции как метод снижения расходов для упрощения сборки со сложной геометрией. Детали после изготовления должны быть обязательно подвергнуты финишной обработке (шлифование, полирование) для придания нужных размеров.
Laser Engineered Net Shaping (LENS) – «лазерное создание конеч-
ной формы» по получаемым прочностным характеристикам является наиболее совершенной технологией для послойного формирования деталей. Системы, построенные на таком принципе, не относятся к системам быстрого прототипирования в привычном понимании этого термина. Качество создаваемых деталей не всегда позволяет использовать эту технологию для визуализации конкретных деталей, но для производства функциональных деталей, технологической оснастки и при проведении ремонтных и восстановительных работ этой системе нет равных. В качестве материала построения применяются металлические порошки. Установки, работающие по принципу LENS, могут работать в двух режимах: режим построения по трехмерной CAD-модели (как в случае DMLS-технологии) и полуавтоматический режим. В первом случае процесс подготовки модели похож на DMLS. Полуавтоматический режим предназначен для целей ремонта и восстановления деталей. В качестве подложки в данном случае фигурирует сломанная или выполнен-
103
ная с отклонениями от требований деталь. Этот режим удобен, когда необходимо произвести локальное воздействие на ремонтируемую деталь (восстановить сколы, заплавить трещины или местные дефекты). Сфокусированный луч лазера производит оплавление поверхности подложки. Образуется ванна расплава (ее размеры достаточно малы). Одновременно струей инертного газа в ванну расплава вдувается металлический порошок. Данный метод позволяет использовать в качестве строительного материала практически любые металлические порошки, за исключением некоторых благородных металлов (у таких материалов коэффициент отражения близок к 1). При таком способе наплавки детали получают ультрамелкозернистую структуру и высокую твердость. Механические свойства этих деталей сравнимы, а в ряде случаев и превышают свойства деталей, полученных традиционными способами производства (штамповка, литье).
Оптические устройства. Лазерное излучение, обладающее достаточно высокой мощностью, может обратимо изменять физические характеристики вещества, что приводит к различным нелинейно-опти- ческим явлениям. Лазерная спектроскопия отличается исключительно высокой степенью точности (высоким разрешением). Лазеры позволяют также осуществлять избирательное возбуждение тех или иных состояний атомов и молекул, избирательный разрыв определенных химических связей. Лазеры позволили осуществить новый метод получения объемных и цветных изображений, названный голографией.
Лазеры широко применяются в медицине: офтальмологии, хирургии и онкологии. В хирургии сфокусированный световой луч непрерывного лазера (мощностью до 100 Вт) служит чрезвычайно острым и стерильным скальпелем.
Лазерная связь и локация. По сравнению с существующими средствами радиосвязи и радиолокации лазерные лучи обладают двумя основными преимуществами: узкой направленностью передачи и широкой полосой пропускания передаваемых частот. Сам лазер создает направленный луч (расходимостью ~10'), а прменение оптической системы позволяет сформировать еще более параллельный луч (расходимостью ~2–3''). Один лазерный луч позволяет передавать сигнал в полосе частот ~100 МГц. Это дает возможность одновременной передачи 200 телевизионных каналов.
Лазерная локация применяется также в геофизике для определения высоты облаков, исследования инверсионных и аэрозольных слоев в атмосфере, турбулентности и т.п.
104
Лазерные системы навигации и обеспечения безопасности полетов.
Лазерные гироскопы обладают достаточно высокой точностью, большим диапазоном измерения угловых скоростей, малым собственным дрейфом, невосприимчивостью к линейным перегрузкам. Лазеры успешно применяются как измерители скорости полета (воздушной и путевой), высотомеры. Лазерные курсоглиссадные системы обеспечивают безопасность полетов, связанную с увеличением точности систем посадки, снижением ограничений по метеоусловиям, обеспечением больших удобств работы экипажа при выполнении такого ответственного участка полета, как посадка. Вблизи взлетно-посадочного полотна установленные лазерные лучи создают геометрическую картину, позволяющую судить о правильности выдерживания траектории посадки.
ЛЕКЦИЯ 5. ЭЛЕКТРОЭРОЗИОННАЯ ОБРАБОТКА МАТЕРИАЛОВ (ЭЭО)
5.1.СУЩНОСТЬ ПРОЦЕССА ЭЭО, ПРЕИМУЩЕСТВА
ИОБЛАСТИ ПРИМЕНЕНИЯ ЭЭО
Современное машиностроение выдвигает очень жесткие требования к параметрам качества и надежности выпускаемой продукции. В условиях мирового экономического кризиса нужды потребителей в высококачественных товарах резко возросли. Возникшая конкурентная борьба заставляет российские предприятия создавать более новую высокотехнологичную продукцию, превосходящую по своим техническим характеристикам западные аналоги.
Одним из путей решения поставленных задач стало использование сверхтвердых материалов при производстве деталей машин и механизмов. Применение данных материалов позволяет повысить прочностные и эксплуатационные характеристики выпускаемых изделий, что в свою очередь позволяет создавать более функциональные механизмы, обладающие малыми габаритами при более высоких функциональных возможностях.
Несмотря на преимущества использования сверхтвердых материалов в машиностроении, их обработка на лезвийных металлообрабатывающих станках зачастую является невозможной.
105
Адекватным решением данной проблемы является применение электрофизических методов размерной обработки материалов. Одним из таких методов является электроэрозионная обработка (ЭЭО).
В настоящее время метод электроэрозионной обработки (ЭЭО) является одним из самых распространенных методов обработки высокотвердых материалов и положен в основу большинства технологических процессов как в серийном, так и в массовом производстве.
Основными преимуществами ЭЭО перед другими видами обработки являются:
–возможность обработки электропроводных материалов вне зависимости от их твердости;
–возможность сложного формообразования как методом копирования, так и методом вырезания профиля;
–высокая точность обработки сверхтвердых материалов (возмож-
ность обеспечения точности обработки в диапазоне ±0,001 мм при шероховатости поверхности Ra = 0,02 мкм);
–возможность обработки деталей любых размеров;
–легкая автоматизация процесса;
–отсутствие требования дорогой оснастки.
Согласно ГОСТ 25331-82 ЭЭО заключается в изменении формы, размеров, шероховатости и свойств поверхности заготовки под действием электрических разрядов в результате электрической эрозии.
Впервые явление эрозии металлов под действием электрического тока было описано английским ученым Д. Пристли в конце XVIII в. Пристли заметил, что при разрыве электрической цепи в месте разрыва возникает искра или более продолжительная по времени электрическая дуга. Причем возникновение электрического разряда приводило к сильному разрушению поверхностей контактов разрываемой цепи, которое сопровождалось интенсивным съемом металла. Данное открытие было названо электрической эрозией. Однако впервые идея использования явления электрической эрозии для размерной обработки была предложена советскими учеными Б.Р. Лазаренко и Н.И. Лазаренко. В годы Великой Отечественной войны супруги Лазаренко работали над проблемой устранения разрушения от электрической эрозии высоковольтных выключателей. Проведенные эксперименты показывали, что после размыкания электрической цепи в жидком диэлектрике жидкость мутнела уже после первых разрядов между контактами. Они установили, что вследствие электрической эрозии электродов в жидкости появляются мельчайшие металлические шарики, иными словами, происходит съем металла.
106
Оказалось, что если обеспечить прохождение электрических импульсов тока между двумя электродами, поместив их в среду определенной рабочей жидкости (РЖ) (при этом один из электродов представляет обрабатываемую заготовку (деталь), а другой – инструмент (ЭИ)), то сообщая инструменту поступательное движение (по мере разрушения заготовки вглубь), можно получить необходимую форму и размер обрабатываемой детали.
Таким образом, в 1943 г. был открыт абсолютно новый метод обработки токопроводящих материалов, названный ЭЭО. В настоящее время по технологическим признакам установлены следующие виды ЭЭО: прошивание (ЭЭПр), отрезка (ЭЭОт), вырезание (ЭЭВ), маркирование (ЭЭМ), объемное копирование (ЭЭОК), шлифование (ЭЭШ), доводка (ЭЭД) и электроэрозионное упрочнение (ЭЭУ).
При описании сущности процесса ЭЭО необходимо ввести следующие понятия:
–межэлектродный промежуток (МЭП) – это пространство меж-
ду электродом-деталью (ЭД) и электродом-инструментом (ЭИ) при электроэрозионной обработке;
–межэлектродный зазор (МЭЗ) – расстояние в рассматриваемом месте межэлектродного промежутка между поверхностями ЭИ и ЭД, перпендикулярными направлению подачи;
–рабочий импульс – импульсный разряд, производящий съем металла вследствие электрической эрозии.
Для осуществления процесса ЭЭО необходимо создать большую концентрацию энергии в зоне разряда. Для достижения этой цели используется генератор импульсов (ГИ). Импульсы тока, сформированные ГИ, подаются на электрод-деталь и электрод-инструмент. Процесс ЭЭО происходит в рабочей жидкости – диэлектрике, которая заполняет МЭП.
Поскольку при ЭЭ-обработке МЭП заполнен жидкой диэлектрической средой, для прохождения импульса тока необходимо, чтобы непроводящий слой РЖ превратился в проводник. Как известно, в любом веществе присутствует некоторое количество свободных носителей заряда (электроны и ионы), существование которых обусловлено рядом внешних факторов (ультрафиолетовое излучение и т.п.). При сближении двух металлических электродов, находящихся под напряжением, носители заряда из-за действия электрического поля начинают равноускоренно перемещаться, в результате чего происходит их соударение с молекулами вещества. После соударения заряженная частица передает
107

часть своей энергии молекуле вещества и теряет скорость. Энергия, которую электрон или ион может передать нейтральной молекуле, зависит от величины напряженности электрического поля:
E = Uδ ,
где E – напряженность электрического поля, U – напряжение между электродами, δ – МЭЗ.
Чем больше величина напряжения, тем больше энергии носитель заряда способен передать встречной молекуле.
При некотором значении напряженности на электродах достигается такое состояние, при котором электрон может передавать встречной нейтральной молекуле энергию, достаточную для ионизации, т.е. из молекулы атома жидкости будет выбит хотя бы еще один электрон, который, как и первый, произведет ионизацию. Когда напряженность электрического поля в некоторой зоне МЭЗ превысит критическое значение (т.е. там, где МЭЗ минимален), произойдет лавинообразное нарастание числа новых носителей зарядов, что приведет к перекрытию всего промежутка каналом, состоящим из свободных ионов и электронов и, следовательно, обладающим проводящими свойствами, иными словами, образуется стример.
Стример представляет собой плазменный канал, который расширяется в течение действия импульса.
В начальный момент времени плазма в канале пробоя не имеет ни радиуса, ни массы. Высокотемпературный канал пробоя излучает энергию, которая поглощается окружающим диэлектриком так же, как и металлическими электродами. Излучение плазмы испаряет и ионизирует тонкий слой окружающей жидкости, который идет на увеличение массы плазмы. Радиус канала плазмы увеличивается со временем из-за высокого внутреннего давления в канале и преобразования окружающего диэлектрика в плазму. На это преобразование уходит 70–74 % общей энергии. Процесс образования стримера зависит от множества факторов: от свойств РЖ, от степени загрязнения РЖ продуктами эрозии, от материала электродов и др.
После прохождения импульса тока напряжение между электродами отсутствует, происходит деионизация РЖ, т.е. нейтрализация заряженных частиц. Пространство между электродами подготавливается для нового прохождения очередного заряда. Вновь приложенное
108
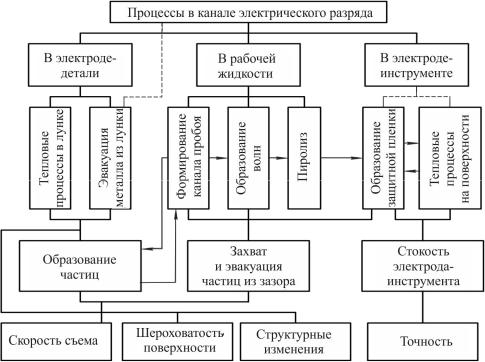
к электродам напряжение создает предпосылку к образованию следующего разряда электрического импульса, т.е. повторяется процесс образования стримера. Совокупность электрических разрядов, проходящих от ЭИ к ЭД с определенной частотой их следования, и реализует процесс ЭЭО. Процессы, протекающие в канале разряда, представлены на рис. 5.1.
Рис. 5.1. Взаимосвязь физико-химических процессов при ЭЭО
Количество тепловой энергии, которая выделяется на электродах неодинаково, так же, как и количество снимаемого материала с поверхностей ЭИ и ЭД. Данное неравновесие зависит от множества факторов: теплофизических свойств материалов ЭИ и ЭД, параметров рабочих импульсов, атакже полярности рабочих импульсов. При помощи варьирования этими факторами можно увеличивать илиуменьшатьэрозию электродов.
Эрозия ЭИ является нежелательным явлением в ходе ЭЭ-обработки. Это связано с тем, что искажение формы электрода-инструмента будет оказывать негативное влияние на точность ЭЭО и шероховатость обработаннойповерхности.
109
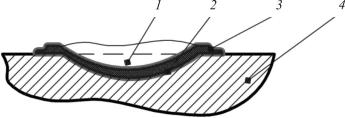
При электроэрозионной обработке стремятся создать условия, при которых износ ЭИ был бы незначителен. Одним из способов уменьшения величины износа ЭИ является применение униполярных импульсов.
Использование униполярных импульсов позволяет осуществлять процесс избирательной электрической эрозии одного из электродов. Если при этом оба электрода изготовлены из одного и того же материала, то при малой продолжительности импульсов преобладает эрозия электрода, имеющего положительную полярность (анода), а при импульсах большой длительности преобладает эрозия электрода, имеющего отрицательную полярность (катода). Разделение импульсов на импульсы малой и большой длительности является условным. Превышение эрозии одного электрода над другим принято называть в ЭЭО полярным эффектом.
Полярный эффект достигает наибольшего значения при использовании униполярных импульсов значительной длительности и небольшой энергии. Если обрабатываемая заготовка подключена к положительному полюсу ГИ, а ЭИ – к отрицательному, то такое включение электродов называется включением на прямую полярность. Если ЭИ подключен к положительному полюсу ГИ, а обрабатываемая заготовка – к отрицательному, то такое включение электродов называется включением на обратную полярность.
ЭЭО начинается с появления единичной лунки – следа на обрабатываемой поверхности, полученного в результате воздействия одного электрического разряда (рис. 5.2).
Рис. 5.2. Лунка, образовавшаяся на обрабатываемой поверхности под воздействием единичного разряда: 1 – выплавленный металл; 2 – белый слой; 3 – валик вокруг лунки; 4 – обрабатываемая деталь
Энергия импульса тока, распределяясь между анодом, катодом и столбом разряда, выделяется в течение весьма короткого времени (10–6 …10 –7 с) при высоких плотностях. В результате чего происходит удаление металла с обрабатываемой поверхности, изменяются струк-
110