
- •С.П. Никитин
- •Никитин С.П.
- •ВВЕДЕНИЕ
- •1. РАЗРАБОТКА МАТЕМАТИЧЕСКОЙ МОДЕЛИ
- •1.1. Основы метода прямой аналогии
- •1.1.1. Сущность метода
- •1.1.2. Основные принципы метода прямой аналогии
- •1.1.3. Выделение в исходном объекте однородных физических подсистем
- •1.1.5. Установление связей между подсистемами
- •1.2.2. Проверка корректности
- •1.2.4. Линеаризация нелинейных уравнений
- •I.2.S. Построение линейной системы уравнений
- •2. МЕТОДЫ АНАЛИЗА ФИЗИЧЕСКОЙ СИСТЕМЫ ПО МАТЕМАТИЧЕСКОЙ МОДЕЛИ
- •2.1. Схема анализа физической системы по математической модели
- •2.3.6. Расчет частотных характеристик по передаточной функции системы
- •3. МАТЕМАТИЧЕСКИЕ МОДЕЛИ ТИПОВЫХ УЗЛОВ ФИЗИЧЕСКИХ СИСТЕМ
- •3.1. Моделирование рычажной системы
- •3.2. Моделирование взаимодействия твердых тел
- •3.2.1. Особенности моделирования динамики твердых тел
- •3.2.4. Моделирование взаимодействия двух твердых тел
- •4.1. Пример моделирования шпиндельного узла
- •4.5. Разработка математической модели плоскодоводочного станка «Растр»
- •4.6. Разработка математической модели тепловых процессов при резании
- •5. АНАЛИЗ ВЛИЯНИЯ ПРОЦЕССА РЕЗАНИЯ НА ДИНАМИКУ ТЕХНОЛОГИЧЕСКОЙ СИСТЕМЫ
- •5.1. Влияние параметров процесса резания на устойчивость системы с одной степенью свободы
- •5.2. Влияние параметров процесса резания на вынужденные колебания динамической системы с одной степенью свободы
- •ЗАКЛЮЧЕНИЕ
- •Список литературы
- •Оглавление
4. МАТЕМАТИЧЕСКИЕ МОДЕЛИ И ПРИМЕРЫ МОДЕЛИРОВАНИЯ ОСНОВНЫХ УЗЛОВ И ПРОЦЕССОВ ТЕХНОЛОГИЧЕСКОГО ОБОРУДОВАНИЯ
4.1. Пример моделирования шпиндельного узла
Шпиндельный узел во многих случаях определяет динамическое качест во некоторых станков [19, 20, 26]. К таким станкам относятся токарные, коор динатно-расточные, расточные, внутришлифовальные и т.д. При моделирова нии шпиндельный узел рассматривают как ступенчатую балку на упругих опо рах с вязким демпфированием. Балку разбивают на стержни постоянного сече ния, разграниченные изменением диаметра, опорами, сосредоточенной массой, внешней сосредоточенной нагрузкой и т.д., которые имеют распределенные по длине свойства жесткости. Смонтированные на шпинделе шкивы, зубчатые ко леса, патрон, маховики представляются в виде сосредоточенных масс, распо ложенных на границах стержней. Опоры шпинделя отражают как линейную жесткость по соответствующим координатам с вязким демпфированием.
Для исследования реакций шпинделя на внешние воздействия в рамках линейной модели используют принцип суперпозиции.
Применение метода прямой аналогии для исследования динамических характеристик рассмотрим на примере шпинделя, изображенного на рис. 4.1.
Рис. 4.1. Принципиальная схема шпиндельного узла
Шпиндель разбит на три участка, каждый из которых отражается невесо мым стержнем постоянного сечения. На концах шпинделя расположены сосре доточенные массивы: шкив ременной передачи (узел 1) и патрон (узел 4); со стороны процесса резания действует сила F.
Правая опора шпинделя учитывается в модели пружиной, имеющей ра диальную и угловую жесткости (Су, Сф), и элементами демпфирования (Ry, /?ф).
Левая опора отражена пружиной, имеющей радиальную жесткость (Су), и элементом демпфирования (Ry).
Эквивалентная схема данного шпиндельного узла изображена на рис. 4.2.
Рис. 4.2. Эквивалентная схема шпиндельного узла
Для расчета динамики шпиндельного узла с помощью программы PAN структура исходных данных представлена в табл. 4.1.
Таблица 4.1
Исходные данные системы шпиндельного узла
|
Ветвь |
|
Узел |
№ |
тип |
от |
до |
1 |
С |
1 |
0 |
2 |
PF |
1 |
0 |
3 |
PF |
1 |
0 |
4 |
L |
1 |
2 |
5 |
R |
1 |
2 |
6 |
PF |
2 |
0 |
7 |
PF |
2 |
0 |
8 |
L |
2 |
0 |
9 |
R |
2 |
0 |
10 |
PF |
2 |
0 |
11 |
PF |
2 |
0 |
12 |
L |
2 |
3 |
13 |
R |
2 |
3 |
14 |
PF |
3 |
0 |
15 |
PF |
3 |
0 |
16 |
L |
3 |
0 |
17 |
R |
3 |
0 |
18 |
PF |
3 |
0 |
19 |
PF |
3 |
0 |
20 |
L |
3 |
4 |
21 |
R |
3 |
4 |
22 |
PF |
4 |
0 |
23 |
PF |
4 |
0 |
24 |
С |
4 |
0 |
25 |
С |
5 |
0 |
26 |
PF |
5 |
0 |
27 |
PF |
5 |
0 |
28 |
PF |
5 |
0 |
вли |
|
с д х |
|
Значение |
|
|
E J,k |
||||
|
|
|
|
|
|
||||||
яния |
|
|
|
|
|
|
|
|
|
|
|
О II £ |
|
|
|
|
* = 6EJH2 |
||||||
5 |
|
|
|
|
|
||||||
6 |
|
|
|
|
|
А |
|
= 6EJ/F |
|||
L |
= 1 / С |
, = |
1 /(ПЕЛ?) |
|
|
|
|
|
|||
«г II £ |
|
|
|
|
к |
= 6 £ |
///3 |
||||
5 |
|
|
|
|
|
||||||
6 |
|
|
|
|
|
А |
|
= 6 |
£ |
/ / / 2 |
|
г |
и |
3 |
|
|
|
|
|
|
|
|
|
04 |
и |
|
|
|
|
Т ^ б Ё Ш |
|||||
6 |
|
|
|
|
|
||||||
7 |
|
|
|
|
|
~кТШ Л ? |
|||||
L |
= МСУ= 1 |
/ ( 1 |
2 |
£ |
/ / / J ) |
|
|
|
|
|
|
е* |
II |
|
|
|
|
|
|
|
|
|
|
6 |
|
|
|
|
|
|
II |
|
|
1 |
|
7. |
|
|
|
|
|
А |
= 6 |
£ |
/ / / * |
||
L = 1/С/ |
|
|
|
|
|
|
|
|
|
||
R = Л / |
|
|
|
|
|
|
|
|
|
|
|
7 |
|
|
|
|
|
|
|
II |
|
|
1 |
8 |
|
|
|
|
|
к |
= 6EJ/12 |
||||
L |
= \/Су= 1 |
/ ( 1 |
2 |
E |
/ / / J ) |
|
|
|
|
|
|
II & |
|
|
|
|
|
|
|
|
|
|
|
7 |
|
|
|
|
|
к |
= 6EJ/12 |
||||
8 |
|
|
|
|
|
А |
= 6EJ/12 |
||||
II и |
|
|
|
|
|
|
|
|
|
|
|
и |
|
|
|
|
|
|
|
|
|
|
|
и |
|
|
|
|
|
|
|
|
|
|
|
1 |
|
|
|
|
|
А |
= |
6 |
£ |
/ / / 2 |
|
2 |
|
|
|
|
|
А |
= |
6 |
£ |
/ / / 2 |
|
6 |
|
|
|
|
|
.А: |
= 6EJH |
знак
-1 -1
-1 -1
-1 -1
-1
|
Ветвь |
|
Узел |
|
№ |
тип |
от |
ДО |
вли |
|
|
|
|
яния |
29 |
L |
5 |
6 |
|
30 |
R |
5 |
6 |
|
31 |
PF |
6 |
0 |
1 |
32 |
PF |
6 |
0 |
2 |
33 |
PF |
6 |
0 |
5 |
34 |
Pf |
6 |
0 |
2 |
35 |
PF |
6 |
0 |
3 |
36 |
PF |
6 |
0 |
7 |
37 |
L |
6 |
7 |
|
38 |
R |
6 |
7 |
|
39 |
PF |
7 |
0 |
2 |
40 |
PF |
7 |
0 |
3 |
41 |
PF |
7 |
0 |
6 |
42 |
L |
7 |
0 |
|
43 |
R |
7 |
0 |
|
44 |
PF |
7 |
0 |
3 |
45 |
PF |
7 |
0 |
4 |
46 |
PF |
7 |
0 |
8 |
47 |
L |
7 |
8 |
|
48 |
R |
7 |
8 |
|
49 |
PF |
8 |
0 |
3 |
50 |
PF |
8 |
0 |
4 |
51 |
PF |
8 |
0 |
7 |
52 |
C |
|
|
|
53 |
J |
4 |
0 |
|
Значение
C,R,L
L = 1/(4EJ/l)
R = ЯФ
L = l/(4£///) li 04
II и >5
L = 1/(4EJ/[)
IIP4
C = J 4
E,J,k
*= 6£///2
*= 6£///2
it = 6£///
к= 6EJ/l2
к= 6E///2 it = 6£///
к= 6£///-
*= 6E///1
к= 6£///
*= 6£///3
it = 6£///
it = 6£///~ II vO к = 6£///
F
_| знак ,
-1
-1
-1
-1
-1
-1
Инерционность материала шпинделя при необходимости может быть уч тена путем присоединения к концам стержней сосредоточенных масс по из вестной методике [27].
4.2. Пример моделирования механического привода станка
Привод вместе с электродвигателем рассматривается как цепная система [8,9,26,27]. Он представляет собой крутильную, упругую механическую систему, состоящую из последовательно соединенных посредством упругих и демпфирующих элементов (пружин и сопротивлений) сосредоточенных масс (массивов). Значение податливости упругих элементов определяется деформациями закручивания и изгиба валов, контактными деформация!ии в соединениях валов с колесами, зубчатых передачах, ременных передачах и т.д. [27]. Сопротивления отражают демпфирование в этих же элементах кинематических цепей привода и обычно включаются в расчетную цепь параллельно с упругими элементами.
Использование метода прямой аналогии для моделирования динамики механического привода рассмотрим на примере главного привода станка 6Н13ПБ (рис. 4.3) [27]. При этом применяются приемы моделирования рычажной системы, изложенные выше.
Рис. 4.3. Кинематическая схема привода станка 6Н13ПБ
Метод прямой аналогии не требует приведения системы к тому или иному валу. Механизм приведения скоростей органически заложен в схему составления расчетной схемы. Для этого достаточно разделить весь привод на подсистемы, которые включали бы в себя элементы с одинаковыми скоростями. А при установлении связей между подсистемами учитывается передаточное отношение кинематических пар. Исходя из этого, в приводе станка 6Н13ПБ целесообразно выделить 7 подсистем, взаимодействие между которыми отражено в механической цепи привода (рис. 4.4) элементами к,.
£|СЭ*И.З |
^ IВ+Ш+Ш |
L\B*U1+M |
^КЗ-ИЗ />4в+ш+ш |
Рис. 4.4. Механическая цепь привода станка 6Н13ПБ при л = 60 об/мин
Такой подход дает дополнительное удобство, так как при анализе математической модели в результате расчетов получаются действительные координаты, скорости и усилия в элементах исходной системы.
Элементами механической цепи отражены податливости и сосредоточен ные массы. При необходимости к ним могут быть добавлены элементы сопроти вления. На рис. 4.4 обозначены:
Ljв, 1 ш, LM, LHз, Z,K.з - податливости кручения соответствующих валов, приведенные к крутильной податливости контактные деформации шлицевых (шпоночных) соединений, муфт, изгибные и контактные деформации зубчатых передач;
Jp, Л,, */Шп - моменты инерции ротора электродвигателя, полумуфт, шпинделя;
J:ij - моменты инерции зубчатых колес, шкивов и т.п.
По механической цепи привода на основе второй системы аналогий получаем эквивалентную схему (рис.4.5). Фиктивные источники в эквивалентной схеме реализуют трансформаторный тип связи и отражают взаимодействие между подсистемами, учитывая передаточные отношения соответствующих передач.
Демпфирование в зубчатых зацеплениях мало [27], и им можно пренебречь. Демпфирование в других элементах привода, прежде всего в стыках соединений и материалов валов, учитываем в эквивалентной схеме элементами сопротивлений, включенных параллельно пружинам, отображающим жесткость соответствующих элементов исходной схемы.
Рис. 4.5. Эквивалентная схема привода станка 6Н13ПБ при п = 60 об/мин
Структура исходных данных для исследований динамики привода с помощью программы PAN приведена в табл. 4.2.
|
|
|
Исходные данные системы привода станка 6Н13ПБ |
Таблица 4.2 |
|||
|
|
|
|
||||
|
|
Ветвь |
|
Узел |
|
Значение |
знак |
[ № |
тип |
от |
Д О вли |
C,R,L |
E,J.k |
||
|
|
|
|
яния |
|
|
|
|
|
L |
1 |
0 |
и |
|
|
к |
3 |
1 R |
1 |
0 |
R = 1/бя |
|
|
| |
С |
1 |
0 |
с = / , |
|
|
|
Г |
4 |
L |
1 |
2 |
L = £пми+ш |
|
|
|----- |
R |
1 |
2 |
R = l/^uMii+ui |
|
|
|
|
5 |
|
|
||||
и |
|
С |
2 |
0 |
С = * /M + Z 2 7 |
|
|
Ветвь
№тип
7JLF
8ELF
9С
10L
11R
12С
13JLF
14ELF
15С
16JLF
17ELF
18С
19L
20R
21С
22JLF
23ELF
24С
25L
26R
27С
28JLF
29ELF
30С
31L
32R
133 С
34JLF
35ELF
36С
37L
38R
39С
40J
|
|
|
|
|
Окончание табл. 4.2 |
|
|
Узел |
|
|
Значение |
|
|
от |
до |
вли |
|
C,RJL |
EJ,k |
знак |
|
|
яния |
|
|
|
|
2 |
0 |
3 |
L = £к.з+и.з |
-it = -27/53 |
|
|
3 |
0 |
2 |
L = £кз+из |
-it = -27/53 |
|
|
3 |
0 |
|
С = Jz53 |
|
|
|
3 |
4 |
|
L = ^2В+Ш+Ш |
|
|
|
3 |
4 |
|
R = 1/62В+Ш+Ш |
|
|
|
4 |
0 |
|
О 1 |
N4 |
|
|
4 |
0 |
5 |
L = £к.з+и.з |
-А = -16/39 |
|
|
5 |
0 |
4 |
L = £к.з+и.з |
-it = -16/39 |
|
|
5 |
0 |
|
С = «/z39 |
-Л—-18/47 |
|
|
5 |
0 |
6 |
L = £кз+из |
|
||
6 |
0 |
5 |
L = ^к.з+и.з |
-it = -18/47 |
|
|
6 |
0 |
|
С = «/z47 |
|
|
|
6 |
7 |
|
L = Т#4в+ш+ш |
|
|
|
6 |
7 |
|
R —1/64В+Ш+Ш |
|
|
|
7 |
0 |
|
II и |
о |
-it =-20/75 |
|
7 |
0 |
8 |
L - |
£кз+из |
|
|
8 |
0 |
7 |
L = £кз+из |
-it = -20/75 |
|
|
8 |
0 |
- |
II CJ |
о |
|
|
8 |
9 |
|
L = ^5В+Ш+Ш |
|
|
|
8 |
9 |
|
R = 1/^5В+Ш+Ш |
|
|
|
9 |
0 |
|
С = Jz42 |
-it = -42/30 |
|
|
9 |
0 |
10 |
L = £кз+из |
|
||
10 |
0 |
9 |
L = Ькз+из |
-it = -42/30 |
|
|
10 |
0 |
|
II и |
о |
|
|
10 |
11 |
|
L - |
^бв+ш+ш |
|
|
10 |
11 |
|
R = Rбв+ш+ш |
|
|
|
11 |
0 |
|
II и |
о |
|
|
11 |
0 |
12 |
L - LKз+из |
-it = -80/60 |
|
|
12 |
0 |
11 |
L = ^кз+из |
-it = -80/60 |
|
|
12 |
0 |
|
п II |
Г |
|
|
12 |
13 |
|
L = Т/7В+Ш |
|
|
|
12 |
13 |
|
R = /?7В+Ш |
|
i |
|
13 |
0 |
|
С = */шп |
J = M |
|
|
13 |
0 |
|
|
|
-1 |
4.3. Пример моделирования гидропривода станка
Гидравлический привод широко используется в металлорежущих станках для создания движений формообразования, автоматизации и обеспечения работы некоторых узлов станков (гидравлических опор, устройств гидроразгрузки направляющих и т.п.). Метод прямой аналогии является эффективным способом получения математической модели таких гидрофицированных узлов станка [32]. Использование метода прямой аналогии рассмотрим на примере моделирования гидросуппорта ГСП-41, схема которого приведена на рис. 4.6.
Рис. 4.6. Гидравлическая схема гидросуппорта ГСП - 41
Гидросуппорт представляет собой следящую систему с однокромочным золотниковым распределителем. Основными узлами являются: гидростанция Г48-1; 1 -напорный трубопровод, подающий рабочую жидкость от станции к гидроцилиндру; 2,5 - задняя и передняя полости гидроцилиндра; 4 - отверстие в поршне, соединяющее полости; 5 - неподвижный поршень гидроцилиндра; б - подвижная часть суппорта с корпусом гидроцилиндра; 7 - канал, соединяю щий переднюю полость с однокромочным золотником; 8 - корпус следящего золотника; 9 -плунжер следящего золотника; 10 -рычаг обратной связи; 11 -ко пир; 12 - сливной трубопровод.
Для разработки математической модели необходимо разбить гидросуп порт на три подсистемы: гидравлическую, механическую и гидравлическую, которые взаимодействуют друг с другом через полости гидроцилиндра. Меха ническая цепь гидросуппорта изображена на рис. 4.7.
Элементы механической цепи отражают физические явления, происхо дящие в гидромеханической системе. Работа гидростанции представлена источ ником постоянного давления Рн, то есть считается, что гидроклапаны идеальны, а пульсацией давления от работы насоса можно пренебречь. Элемент RTотра жает сопротивление напорного трубопровода течению жидкости, элементы Си Сз учитывают податливость жидкости в трубопроводах и самих трубопроводов. Элемент /?л учитывает сопротивление отверстия в поршне перетеканию жидко сти из одной полости в другую, оказывающее важнейшее влияние на работу гидросуппорта, а элемент N - нелинейный закон истечения жидкости через ко льцевую щель золотника. Элемент SUM| представляет собой сумматор, где складываются движения корпуса и плунжера золотника. Результат этого сложе ния определяет величину открытия кольцевой щели золотника. Элемент М от ражает инерционность механической части суппорта, элемент F - внешнюю си лу, в качестве которой выступает сила резания, элементы S\, S2 - площади поло стей гидроцилиндра, через которые осуществляется взаимодействие между под системами.
На основе механической цепи строится эквивалентная схема (рис. 4.8).
Для получения |
эквивалентной |
схемы |
подсистем |
|
гидравлических |
втор3* |
|||
использована первая система аналогий, а механической подсистеМь1 |
TJjna |
|||
система аналогий. Фиктивные источники JF отражают связь гиратОрн |
|
|||
между подсистемами. |
основе метода |
узловых |
„магическая |
|
Полученная на |
потенциалов матем*** |
|
модель отражает динамические процессы в гидросуппорте ГСП-41 и м быть использована для анализа его работы. Структура исходных данных, подготовленная для анализа динамики гидросуппорта с помощью программы
PAN, |
представлена в табл. 4.3. |
|
|
|
|||
|
|
|
|
|
|
|
Таблица 4.3 |
|
|
Исходные данные системы гидросуппорта ГСП - 41 |
|
||||
Ветвь |
|
Узел |
|
|
Значение |
|
|
№ |
тип |
от |
до |
вли |
C,R,L |
E,J,k |
знак |
|
|
|
|
яния |
|
|
|
1 |
ER |
1 |
0 |
|
Лт |
р» |
|
2 |
С |
1 |
0 |
|
с, |
S, |
|
3 |
JF |
1 |
0 |
2 |
|
|
|
4 |
JF |
2 |
0 |
1 |
м |
S, |
-1 |
5 |
С |
2 |
0 |
|
F |
|
|
6 |
J |
2 |
0 |
|
|
-1 |
|
"7 |
JF |
2 |
0 |
3 |
|
s 2 |
-1 |
8 |
JF |
3 |
0 |
2 |
с2 |
& |
|
9 |
С |
3 |
0 |
|
|
|
|
10 |
NOTR |
3 |
0 |
4 |
N |
|
|
11 |
R |
1 |
3 |
|
R:, |
|
|
12 |
SUM |
4 |
0 |
2 |
к = 1 |
0 |
|
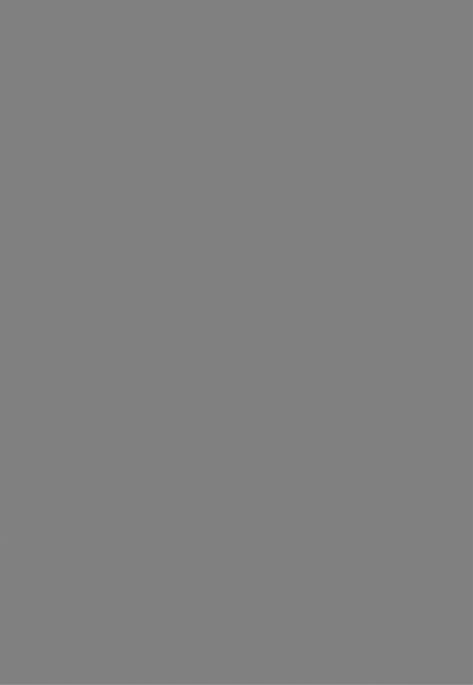
Рис. 4.10. Расчетная {а) и эквивалентная (5) схемы движения рабочего органа, отображающие демпфирование процесса трения
В расчетной схеме элемент Сх отражает жесткость связи, удерживающей стол в направлении оси х; Их- коэффициент сил сопротивления* по оси х, опре деляемый демпфированием в связи; Ит- коэффициент сопротивления по оси х, определяемый силами вязкого трения смазки; М - инерционность стола.
На основе второй системы аналогий получаем эквивалентную схему дви жения стола (рис. 4.10,6).
Используя метод узловых потенциалов, по эквивалентной схеме строим математическую модель, которая представляет собой дифференциальное урав
нение: |
|
М х+ (Их+ /?т )х+ Ctx = F. |
(4.1) |
Коэффициенты в уравнении описаны выше.
Наиболее часто, когда возникает задача исследования плавности движе ния рабочего органа станка, процесс трения отображается в модели как аперио дическое звено, имеющее передаточную функцию
fVAS) = *т |
(4.2) |
Г,5 + Г |
|
где кл - статическая характеристика контактного трения; Гт - постоянная времени процесса трения.
При моделировании методом прямой аналогии в этом случае процесс трения рассматривается как отдельная подсистема, взаимодействующая с меха нической подсистемой. Механическая цепь привода стола с учетом процесса трения, отраженного в виде апериодического звена, изображена на рис. 4.11.
Рис. 4.11. Механическая цепь привода рабочего органа с учетом процесса трения, отраженного в виде апериодического звена
Здесь элементом к отображено взаимодействие между механической под системой и процессом трения. Используя вторую систему аналогий, получаем эквивалентную схему привода исполнительного органа с учетом процесса тре ния как апериодического звена (рис. 4.12).
|
х |
|
т |
~ |
|
|
м - - F /k |
= 1 |
V |
1 |
PF |
Рис. 4.12. Эквивалентная схема привода рабочего органа с учетом процесса грсния. отраженного в виде апериодического звена
Взаимодействие между подсистемами в эквивалентной схеме учтено включением двух фиктивных источников: JF, PF, которые обеспечивают скоро стную связь:
PF =k F r,
(4.3)
JF = kT x.
Используя метод узловых потенциалов теории электротехники, получаем математическую модель, описывающую динамику привода рабочего органа с учетом процесса трения как апериодического звена:
|
М х+ hx х+ Схх - F + FT=0, |
(4.4) |
|
|
|
|
hTFT +Fr +kTx = 0, |
|
где М - |
масса стола; |
|
С, - |
жесткость связи рабочего органа по оси х\ |
|
Их- |
коэффициент демпфирования в связи по оси х; |
|
F - |
внешнее воздействие по оси х\ |
|
F, - |
сила трения; |
|
kt - |
статическая характеристика трения. |
|
В приводах рабочих органов прецизионных станков на точность обработ ки оказывает влияние как плавность движения, так и величина всплывания. По этому при перемещении рабочего органа необходимо исследовать влияние обо их этих параметров. В этом случае привод подач должен рассматриваться в пространстве двух координат. Расчетная схема привода в пространстве двух координат представлена на рис. 4.13.
Рис. 4.13. Расчетная схема привода рабочего органа в пространстве двух координат
При использовании метода прямой аналогии каждая из координат рас сматривается как отдельная подсистема. Вторая система аналогий отображения дает эквивалентную схему, показанную на рис. 4.14.
х |
у |
Рис. 4.14. Эквивалентная схема привода рабочего органа в пространстве двух координат
Фиктивные источники в эквивалентной схеме отражают взаимодействие между подсистемами, то есть перемещение рабочего органа по координатам л и у. Эта связь обусловлена процессами трения в направляющих. Выражения для фиктивных источников имеют следующий вид:
PF = кт- у,
(4.5)
JF = кд х.
Эти уравнения связи отражают условия смешанного трения.
При учете влияния жидкостного трения в эквивалентную схему необхо димо ввести дополнительный элемент. Сила жидкостного трения пропорцио нальна координате^ и скорости скольжения:
|
F = -* -К |
(4.6) |
где |
i t , - коэффициент пропорциональности, |
|
|
У0 - скорость скольжения. |
|
Если рассматривать У0 как постоянную величину, то структура эквива лентной схемы остается без изменений. Изменится только коэффициент в урав нении связи:
JF = (kJ+kxVa) y . |
(4.7) |
Для учета изменений скорости скольжения при перемещении рабочего органа по направляющим в эквивалентную схему необходимо ввести нелинейный элемент жесткости, который учитывает жидкостное сопротивление движе нию. Эквивалентная схема при таком подходе показана на рис. 4.15.
Рис. 4.15. Эквивалентная схема привода рабочего органа в пространстве двух координат с учетом жидкостного и смешанного трения
Полная математическая модель динамической системы привода подач в пространстве двух координат, полученная по приведенным выше эквивалент ным схемам, представляет собой систему двух обыкновенных дифференциаль ных уравнений:
М х+ Нхдг+ Схх + куу =О,
(4.8)
М у+ hy у+ Суу + kQх = О,
где М - масса рабочего органа; К к у - коэффициенты демпфирования в связи по оси х и стыке по оси у\
Сх>Су - жесткости связи по оси х и стыка по оси у;
kj. - коэффициент пропорциональности между перемещением по оси у и силой трения;
kQ - коэффициент пропорциональности между скоростями скольжения и усилием всплывания.
Исходные данные для программы PAN, соответствующие эквивалентной схеме (см. рис. 4.14), приведены в табл. 4.4.
В табл. 4.5 представлены исходные данные по эквивалентной схеме, изо браженной на рис 4.15, которая описывает динамику привода рабочего органа в пространстве двух координат.
Таблица 4.4 Исходные данные привода рабочего органа с учетом силы трения
|
Ветвь |
|
Узел |
|
Значение |
|
№ |
тип |
от |
до вли |
C,R,L |
E,J,k |
знак |
|
|
|
яния |
|
|
|
1 |
L |
1 |
0 |
L = 1/ С, |
2 |
R |
1 |
0 |
II 0* |
3 |
С |
1 |
0 |
с = м |
4 |
PF |
1 |
0 |
2 |
5 |
JF |
2 |
0 |
1 |
6 |
R |
2 |
0 |
R = l//jT=7V |
7 |
L |
2 |
0 |
L = 1 |
8 |
J |
1 |
0 |
|
k= \
и
Таблица 4.5 Исходные данные привода рабочего органа в пространстве двух координат
|
Ветвь |
|
Узел |
|
|
Значение |
|
№ |
тип |
от |
до |
вли |
C,R,L |
E,J,k |
знак |
|
|
|
|
яния |
|
|
|
i |
L |
1 |
0 |
|
L = 1 ICX |
|
|
2 |
R |
1 |
0 |
|
II * |
|
|
|
|
|
|
||||
3 |
С |
1 |
0 |
|
с = м |
|
|
4 |
PF |
1 |
0 |
2 |
|
к= \ |
|
5 |
JF |
2 |
0 |
1 |
|
и |
|
|
|
|
|||||
6 |
С |
2 |
0 |
|
с = м |
|
|
7 |
L |
2 |
0 |
|
ги |
|
|
8 |
R |
2 |
0 |
|
R = \!hy |
|
|
9 |
J |
1 |
0 |
|
|
1 |
|
Процесс резания оказывает определяющее влияние на динамические ха рактеристики и виброустойчивость динамической системы станка.
Так как всем рабочим процессам присущи общие черты [17], то для моде лирования процесса резания методом прямой аналогии используются приемы, аналогичные моделированию процесса трения.
Математические модели для процесса резания достаточно разработаны [13,17,19,21]. Вид и сложность модели определяется решаемой задачей. Для описания процесса резания используются: статическая модель, апериодическое звено, дифференцирующее звено, полная линейная математическая модель и т.д.
Динамические характеристики процесса резания и связь с другими звень ями динамической системы станка определяются геометрическими параметра ми срезаемого слоя (рис. 4.16).
Рис. 4.16. Геометрические параметры срезаемого слоя: a.h - толщина и ширина срезае мого слоя; I- глубина резания; <р - главный угол в плане; е - изменение толщины срезае
мого слоя
Если пренебречь инерционностью и демпфированием процесса резания, то модель будет представлять собой статическую характеристику вида
|
Р = кг гч |
(4.9) |
где кР- |
коэффициент силы резания, |
|
е - |
изменение толщины срезаемого слоя. |
|
Для токарной обработки с врезной подачей (рис. 4.17) [13] изменение толщины срезаемого сЛоя представляет собой относительное смещение инст румента и заготовки по координате у.
г = у.
Рис. 4.17. Принципиальная схема токарной обработки
сврезной подачей
Вэтом случае достаточно рассмотреть динамику системы в направлении оси у. Пусть система инструмента будет неподвижной, а система заготовки отображена упругой системой с одной степенью свободы. Тогда механическая цепь, отражающая динамические процессы в такой системе, будет иметь вид, показанный на рис.4.18.
Эквивалентная схема токарной обработки с врезной подачей, полученная по второй системе аналогий, показана на рис. 4.19.
У
I
Су hy M - j- кр
I
Рис. 4.19. Эквивалентная схема токарной обработки с врезной подачей при статиче ской характеристике резания
Математическая модель, построенная по данной эквивалентной схеме, представляет собой дифференциальное уравнение второй степени
М у + hy у + С уу + к Ру = F . |
(4.10) |
При учете явления демпфирования математическая модель процесса ре зания имеет более сложный вид и представляет собой дифференцирующее зве но
Р = кР -г + hp • в, |
(4.11) |
|
где htT- коэффициент вязкого трения процесса резания;
б - скорость изменения толщины срезаемого слоя.
В этом случае для токарной обработки с врезной подачей, когда е = v, ме ханическая цепь и эквивалентная схема несколько изменяются. Изменение за ключается в появлении дополнительного элемента, отражающего демпфирова ние процесса резания (рис. 4.20, 4.21).
С\ |
М |
|
У
Рис. 4.20. Расчетная схема токарной обработки с врезной подачей при учете жесткости и демпфирования процесса резания
Рис. 4.21. Эквивалентная схема токарной обработки с врезной подачей при учете жесткости и демпфи рования процесса резания
Математическая модель такой системы имеет следующий вид:
М у+ hy у+ Суу + кРу + hP у = 0. |
(4.12) |
Если возникает необходимость учесть инерционность процесса резания, запаздывание изменения силы резания при изменении толщины срезаемого слоя, то математическая модель значительно усложняется. Именно такая мо дель используется при исследовании виброустойчивости обработки. Пренебре жение демпфированием, то есть учет только жесткости и инерционности, при водит к математической модели процесса резания в виде апериодического звена
Р + Т р Р — к р Е у |
(4.13) |
где Т Р - постоянная времени стружкообразования;
Р - скорость изменения силы резания.
Такая математическая модель находит широкое применение при исследо вании проблемы виброустойчивости.
При отображении процесса резания в таком виде метод прямой аналогии требует выделения процесса резания в качестве подсистемы, которая взаимо действует с упругой системой. В этом случае механическая цепь токарной об работки с врезной подачей будет иметь вид, показанный на рис. 4.22.
Рис. 4.22. Механическая цепь токарной обработки с врезной подачей при учете резания как апериодического звена
Элемент к отражает взаимодействие между подсистемами. В эквивалент ной схеме (рис. 4.23) это взаимодействие учитывается включением фиктивных источников PF.
Су hy
Рис.4.23. Эквивалентная схема токарной обработки с врезной подачей при учете резания как апериодического звена
Уравнение связи при этом имеет следующий вид:
P F X= Р .
(4.14)
PF2 = - к г у .
Математическая модель, полученная по эквивалентной схеме, имеет вил:
М у+ //, v+ С\ у + Р = F.
(4.151
j r P+P = k,v.
где М —приведенная масса системы заготовки;
Ну - коэффициент демпфирования в упругой механической системе, Су - жесткость связи упругой механической системы, Р - сила резания,
ки - коэффициент силы резания.
Исходные данные системы токарной обработки с врезной подачей для программы PAN представлены в табл. 4.6.
Таблица 4.6 Исходные данные токарной обработки с врезной подачей
|
Ветвь |
|
Узел |
|
|
|
Значение |
|
№ |
тип |
от |
до |
вли |
|
C,R,L |
E,J,k |
знак |
|
|
|
|
яния |
L = 1 /Су |
|
|
|
1 |
L |
1 |
0 |
|
|
|
||
2 |
С |
1 |
0 |
|
пII |
|
|
|
3 |
R |
1 |
0 |
|
II * |
|
|
|
|
|
|
|
|
||||
4 |
PF |
1 |
0 |
2 |
|
|
* = 0,5 |
|
5 |
JF |
2 |
0 |
1 |
|
|
к -кр |
-1 |
6 |
R |
2 |
0 |
|
II С* |
£ |
|
|
7 |
L |
2 |
0 |
|
L = 1 |
|
|
|
8 |
J |
1 |
0 |
|
|
|
1 |
-1 |
Процесс резания является замыкающим звеном динамической системы и образует с упругой системой станка замкнутую систему. Кроме этого через процесс резания происходит взаимодействие между разными подсистемами станка: упругой несущей системой, упругой системой главного привода и упру гой системой привода подач. Это взаимодействие называют явлением коорди натной связи. При исследовании данных вопросов процесс резания должен рас сматриваться в виде полной линейной модели.
Р + Т р Р = к Рхх + hPx х + к Руу + hPy у + hP. z, |
(4.16) |
где крх, к,у - коэффициенты резания по осям х, у,
к/‘х, V - коэффициенты демпфирования по координатам х, у.
В данной модели учитывается жесткость и демпфирование по ортого нальным координатам х, у, которые определяют величину сечения срезаемого слоя материала а и Ь.
По координате z учитывается только демпфирование резания. В левой части уравнения отражена инерционность процесса резания.
Если отразить упругую несущую систему токарного станка в плоскости zOy, упругую систему главного привода и упругую систему привода подач в виде колебательных звеньев с одной степенью свободы, то получится механи ческая цепь токарной обработки, отражающая координатную связь через пол ную линейную модель процесса резания (рис. 4.24).
Рис. 4.24. Механическая цепь токарной обработки цри уч^е резания в виде
полной линейной модели
Элементами механической цепи отраженц основные физические явле ния, протекающие в динамической системе станка-
ПГД - система главного привода; П П - привод подач;
УНС - упругая несущая система; Сф, Ст, Су- приведенные жесткости соответствующих подсистем;
h9l hx, hy- приведенные коэффициенты демпфирования подсистем; J 9, Мх, Му- приведенные инерционные параметры системы;
ТР- постоянная времени стружкообразования; К кх, ку- элементы связи упругих подсистем с подсистемой резания.
На рис. 4.25 изображена эквивалентная схема динамической системы то карной обработки, построенная на основе механической цепи.
ПГД
Рис.4.25. Эквивалентная схема токарной обработки при учете резания в виде полной линейной модели
Фиктивные источники типа PF и JF обеспечивают связь межд\ хпругимп подсистемами ПГД, ПП, УНС и процесса резания. Уравнения связи определя ются выражениями:
PFP. = k:Py |
|
|
?¥Px=kxP, |
|
|
PF/>y = kyP, |
|
|
JF, = hpx x » |
(4.17) |
|
PF^ = kPxxf |
||
|
||
J¥y = hpy у , |
|
|
PFy = ^РуД'» |
|
|
JFZ=hP2z. |
|
Математическая модель динамической системы токарной обработки представляет собой систему четырех обыкновенных дифференциальных урав нений с четырьмя неизвестными:
Лр Ф +Лф Ф + С ф + * гР = 0,
Мх х+ hx х+ Схх + кхР = 0,
(4.18)
М у у+ Иу у+ Суу + куР = 0,
hPx х+ кРхх + у+ круу + hP: ф+— Р+ Р = О, Тр
где кРху кру - коэффициенты резания по соответствующим координатам; hPx, hpy, Л/>г - коэффициенты демпфирования резания по соответствующим
координатам;
кХ9 ку, L - коэффициенты, определяемые проекциями силы резания на соответствующие оси.
Некоторые авторы [17, 21] предлагают более сложные математические модели, которые учитывают собственную устойчивость процесса резания и его нелинейность.