
книги / Технология получения активных углей и их применение
..pdf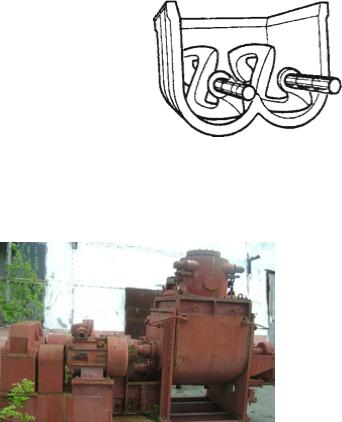
Для получения паст наиболее пригодны лопастные смесители. Чаще всего эти смесители имеют два вращающихся вала, на которых смонтированы различные лопасти. Корпус смесителей неподвижен и может иметь рубашку для нагрева или охлаждения продукта. Схема лопастного смесителя с Z-образными гладкими лопастными валами приведена на рис. 7.13.
Внешний вид смесителя ЗЛ–630–23К–01 представлен на рис. 7.14.
Рис. 7.14. Смеситель ЗЛ–630–23К–01
Техническая характеристика смесителя ЗЛ–630–23К–01: |
|
||
объем рабочий, м3............................................................................. |
|
|
0,63 |
площадь поверхности теплообмена, м2 .......................................... |
|
|
2,47 |
температура рабочая, °С................................................ |
от –20 до +160 |
||
частота вращения ротора быстроходного, с–1 (об/мин) |
..... 0,61 |
(36,6) |
|
частота вращения ротора тихоходного, с–1 (об/мин)......... |
0,405 |
(24,3) |
|
среда в камере смешения................................................. |
|
коррозионная |
|
среда в рубашке........................................... |
вода, водяной пар, рассол |
||
угол опрокидывания корыта, град............................................. |
|
110 ± 5 |
111
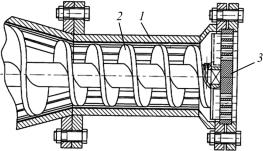
7.5.5. Оборудование для гранулирования
Необходимость гранулирования порошковых материалов обусловлена преимуществами гранул по сравнению с порошкообразной формой веществ. Гранулы обладают высокими сорбционными характеристиками, хорошей сыпучестью, не слеживаются при хранении, не пылят при транспортировке и расфасовке.
Для гранулирования могут применять разные методы: окатывание порошков в присутствии жидких связующих добавок, диспергирование суспензий в псевдоожиженном слое, прессование порошков, экструзия.
Гранулирование методом формования (экструзии) заключается в продавливании исходного материала через перфорированную решетку и последующей конвективной сушке гранул.
Формование и гранулирование служат для получения контактной массы в виде частиц определенной формы и размеров, обеспечивающих необходимые параметры проведения процесса (скорость, избирательность и др.) при допустимых энергетических затратах на преодоление гидравлическогосопротивленияслояматериалаивысокойегопрочности.
Грануляторы для формования цилиндрических гранул. В грануляторах этого типа формование проводят путем продавливания влажной пастообразной массы через отверстия формующей головки с последующим разрезанием жгутов на грануляционных устройствах. По принципу создания давления, необходимого для экструзии, различают шнековые (червячные) (рис. 7.15) ипоршневыевинтовыеилигидравлическиемашины.
Рис. 7.15. Схема шнекового гранулятора: 1 – корпус; 2 – шнек; 3 – решетка
112
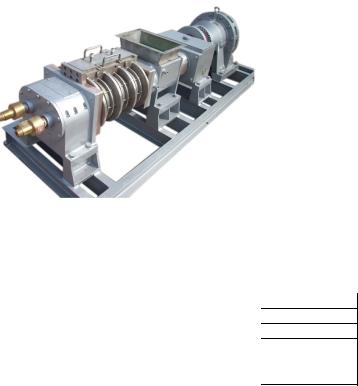
Грануляционные устройства, применяемые в производстве, и комплектующие экструзионные машины разделяются на ножевые, дисковые, струнные и барабанные. В ножевых устройствах резка жгутов осуществляется ножами, установленными на вращающемся роторе в радиальном направлении. Плоскость вращения перпендикулярна направлению движения жгутов. Длина гранул определяется скоростью экструзии, частотой вращения ротора и числом ножей, установленных на роторе. В струнных устройствах жгут разрезают струны, натянутые между двумя вращающимися дисками (кольцами). В дисковых гранулятоpax функции ножей выполняют вращающиеся с частотой 150–400 об/мин диски. На рис. 7.16 изображен шнековый гранулятор марки PRG. Данный гранулятор подходит для получения катализаторов, углеродных сорбентов, оксидов, сложных удобрений (табл. 7.7).
Рис. 7.16. Шнековый гранулятор PRG
|
|
Таблица 7 . 7 |
|
Технические характеристики грануляторов PRG |
|||
|
|
|
PRG-780 |
Показатель |
PRG-440 |
PRG-600 |
|
Производительность, кг/ч |
250–800 |
2000–5000 |
4000–10000 |
Диаметр частиц, мм |
2–15 |
2–30 |
2–35 |
Площадь отверстий, см2 |
759 |
1382 |
1724 |
Внешние размеры, мм |
1600×824×1297 |
2235×1768×1720 |
2450×1400×2125 |
Диаметрплоскойматрицы, мм |
440 |
600 |
780 |
113
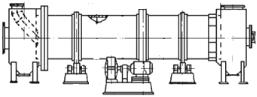
7.5.6. Оборудование для термообработки
Сушка гранул в процессе получения активного угля проводят в барабанной сушилке.
Барабанная сушилка. Барабанные сушилки предназначены для сушки в производстве строительных материалов, в металлургической, химической, угольной промышленностях. Они характеризуются быстрой сушкой, длительным сроком службы, низкой стоимостью, простотой в эксплуатации, удобным техническим обслуживанием и ремонтом. Оборудование состоит из вращающегося барабана, подъемной плиты для материала, системы передачи и пр. Схема барабанной сушилки приведена на рис. 7.17.
Рис. 7.17. Схема барабанной сушилки
Высушиваемый материал подается с верхнего конца вращающегося барабана, а теплоноситель – с нижнего конца. Когда барабан вращается, материал начинает двигаться в сторону нижней части вследствие своей силы тяжести. В процессе движения материал получает тепло от теплоносителя и тем самым сушится. Затем высушенный материал выгружается из разгрузочного отверстия. Как правило, теплоноситель представляет собой нагретый воздух или топочный газ.
На рис. 7.18 показан внешний вид сушилки типа Ф производства Китай, втабл. 7.8 приведенытехническиехарактеристикитакихсушилок.
Термическая обработка углеродсодержащего сырья включает два основных процесса: карбонизацию и активацию, которые могут осуществляться во вращающихся барабанных и шахтных печах.
Вращающаяся печь барабанного типа состоит из горизонтально расположенного цилиндрического кожуха (барабана), футерованного изнутри огнеупорным кирпичом, опорных устройств и привода, головок (топочной и газоотводящей) и холодильника (рис. 7.19).
114
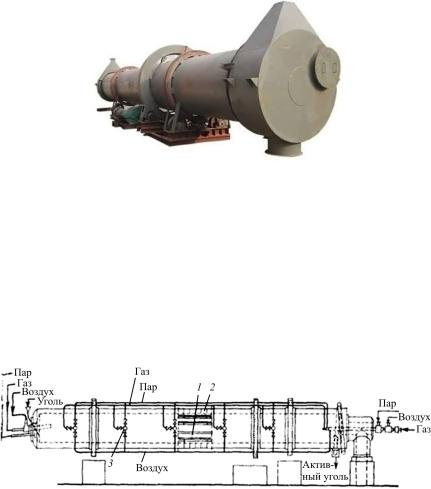
Рис. 7.18. Барабанная сушилка марки Ф
Таблица 7 . 8 Технические характеристики сушилок типа Ф
Показатель |
Ф 0.8×10 |
Ф 1.2×10 |
Ф 1.5×12 |
Ф 2.2×12 |
Производительность, т/ч |
0,8–2,5 |
1,8–5,0 |
3,5–9,0 |
6,0–15,0 |
Внутренний диаметр, мм |
800 |
1200 |
1500 |
2200 |
Длина, м |
10 |
10 |
12 |
12 |
Температура воздуха на входе, С |
|
180–350 |
|
|
Температура воздуха на выходе, С |
|
90–100 |
|
Рис. 7.19. Схема вращающейся печи: 1 – подъемные лопатки по длине печи; 2 – кладка печи; 3 – горелка
Кожух обычно глухой по всей длине, сварен из листового железа толщиной 10–30 мм. Изнутри кожух футерован шамотным, магнезитовым или высокоглиноземистым кирпичом. Снаружи кожуха закреплены опорные стальные бандажи и большая венцовая шестерня. Бандажи опираются на ролики. Печь вращается со скоростью 0,6–2 об/мин.
115
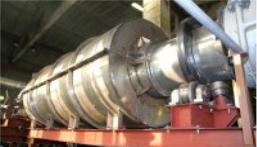
Печь парогазовой активации барабанного типа «КВАРК-500» для производства активного угля. Эта печь служит для активации карбонизированных продуктов углеродного состава: бурого и каменного угля, антрацита, торфа, дерева, растительных отходов (грецкого, кокосового и других орехов, косточек плодов фруктовых деревьев, шелухи риса). В результате получается активный уголь, применяемый для очистки, разделенияиизвлеченияразличныхвеществ, чтонеобходимовразныхсферах.
Всостав оборудования входят: линия автоматической подачи сырья
взону активации, печь активации барабанного типа, парогенератор, автоматическая выгрузка полученного продукта и его упаковка (рис. 7.20).
Функциональность печи активации барабанного типа не ограничивается активацией углеродсодержащего сырья. Также «КВАРК-500» может использоваться для карбонизации и пиролиза продуктов углеродного состава. В этом случае требуются определенные изменения конструкции оборудования.
Технико-экономические показатели печи активации «КВАРК-500»:
количество потребляемого сырья, т/сут |
.................................... 0,5–4,8 |
производительность, т/сут........................................................ |
0,25–2,7 |
фракция сырья, мм ............................................. |
зависит от вида сырья |
габаритные размеры, мм............................................. |
7800×2500×3800 |
Рис. 7.20. Печь «КВАРК»
Печи шахтного типа с внутренним обогревом широко используют для активирования кускового угля, который затем перерабатывается в дробленый или порошкообразный. Многоступенчатая печь шахтного типа с боковыми горелками изображена на рис. 7.21 [12].
116
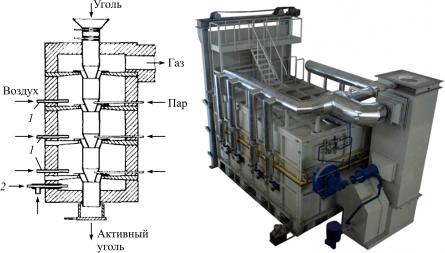
Рис. 7.21. Схема и внешний вид шахтной печи:
1 – каналы для подвода реакционных газов; 2 – огневой канал
Шахтные печи состоят из камер, расположенных вертикально одна над другой. Сверху загружается активируемый материал, снизу подается водяной пар. Для улучшения перемешивания и увеличения реакционной поверхности используют насадки и направляющие устройства. Часто несколько печей соединены в одну технологическую цепочку из соображений экономии энергии. В промежутках между отдельными ретортами производится сжигание активирующих газов, что делает процесс самоподдерживающимся.
Контрольные вопросы
1.Перечислите основные стадии процесса получения гранулированных активных углей.
2.Чем отличается процесс получения ГАУ и ДАУ?
3.В чем заключается сущность методов определения влияния различных факторов технологического процесса получения активных углей и доли вклада всех параметров конкретной стадии в формирование каждого показателя качества активного угля?
117
4.Каковы основные требования к качеству сырья для получения активных углей?
5.В чем состоит сущность процесса карбонизации? Каковы условия проведения процесса, от каких факторов они зависят?
6.Что такое активация в технологии получения активных углей? Механизм процесса парогазовой активации.
7.В чем заключается сущность процесса химической активации?
8.ОпишитемеханизмсмешаннойактивациисиспользованиемK2CO3.
9.Приведите условную технологическую схему получения ГАУ
иДАУ. Сравните их.
10.Перечислите оборудование дробления и размола, используемое при производстве активных углей.
11.Перечислите оборудование, которое используется для получения угольно-смоляной композиции и формования гранул.
12.Какие аппараты используются для карбонизации и активации?
8. РЕГЕНЕРАЦИЯ ОТРАБОТАННЫХ АКТИВНЫХ УГЛЕЙ
Широкое применение активных углей в различных процессах очистки твердых и жидких сред приводит к формированию и накоплению твердых отходов – отработанных активных углей. Эффективное применение углеродных сорбентов возможно только при условии их регенерации и многократном использовании [35].
Известен ряд основных методов регенерации сорбентов:
–химический метод,
–метод вытеснительной десорбции,
–экстракционный метод,
–термический метод,
–биологический метод и др. [36].
8.1. Химическая регенерация
Химическая регенерация – это обработка использованного сорбента жидкими или газообразными реагентами при температуре, как правило, не выше 100 С. В результате такой обработки сорбат либо де-
118
сорбируется без изменения химического состава, либо десорбируются продукты его взаимодействия с регенерирующим агентом.
Химическую регенерацию часто проводят непосредственно в адсорбционном аппарате. Самый простой метод химической регенерации АУ – нагревание отработанного сорбента в воде, что приводит к увеличению степени диссоциации и растворимости сорбата и, в итоге, к частичной его десорбции. Иногда достаточным бывает простое аэрирование отработанныхАУвводе, чтотакжеприводиткчастичнойихрегенерации.
Слабые органические электролиты достаточно просто десорбируются с угля при переводе их в диссоциированную форму путем изменения рН на 3–4 единицы. Диссоциированные ионы сорбата переходят в раствор в объеме пор, откуда затем вымываются регенерирующим раствором или водой [37].
Из всех методов химической регенерации углей наибольшее распространение в водоподготовке получила обработка АУ растворами гидроксида и карбоната натрия. Десорбция органического сорбата с АУ растворами кислот используется сравнительно редко. Чаще кислоты служат окислителями сорбата на угле. Окислителем органического сорбата может служить и перекись водорода. По окончании обработки АУ растворами неорганических веществ сорбент промывают теплой или холодной водой, а иногда для стабилизации рН растворами, содержащими противоположно заряженные ионы.
Таким образом, общим для любых способов химической регенерации отработанных углей является:
–приготовление, хранение и подача регенерирующих растворов;
–циркуляция этих растворов через слой адсорбента;
–сбор и очистка отработанных элюатов;
–ликвидация кубового остатка;
–отмывка паром или водой активного угля от остатков реагентов. Любой метод химической регенерации приводит к формированию
инакоплению отработанных растворов, которые в свою очередь также требуют очистки. Сточные воды иногда после физико-химической очистки и всегда после биохимической содержат загрязнения, которые после адсорбции на угле не десорбируются химическими методами, осмоляются, закрывая активное поровое пространство сорбента. В этом случае эффективна лишь термическая регенерация.
119
8.2. Методы вытеснительной десорбции
Вытеснительная десорбция осуществляется путем вытеснения из адсорбента поглощенного вещества (адсорбата) другим компонентом, являющимся вытеснителем (десорбентом), к которому предъявляются следующие требования:
–хорошая сорбируемость;
–способность активно вытеснять поглощенные компоненты из адсорбента;
–пожаро- и взрывобезопасность;
–экологическая безопасность (нетоксичность);
–низкая стоимость.
Вкачестве компонента-вытеснителя органических веществ из адсорбента могут применяться такие вещества, как аммиак, диоксид углерода, вода и т.д. При выборе десорбирующего агента необходимо учитывать, что адсорбент должен не только эффективно удалять адсорбат, но и сам эффективно удаляться в последующем [38].
8.3. Методы экстракционной регенерации
Для десорбции органического сорбата часто используют прием экстракции. С этой целью применяют низкокипящие легко перегоняющиеся с водяным паром органические растворители (спирты, ацетон, хлороформ, дихлорэтан, бензол, бутилацетат) с последующей отгонкой отработанного растворителя.
Для успешного проведения экстракционной регенерации необходимо, чтобы были выполнены следующие условия:
–растворимость сорбата в растворителе была выше, чем в воде;
–коэффициент распределения сорбата при экстракции его растворителем из воды был предельно большим;
–растворитель хорошо смачивал АУ; имел низкую температуру кипения и вязкость; был негорючим и невзрывоопасным; легко десорбировался с активного угля после регенерации и разгонялся для возврата его для следующего цикла обработки.
Предварительная щелочная промывка активного угля повышает эффект последующей экстракции растворителями за счет сдвига pH
ичастичного гидролиза сорбата. Экстракционная регенерация углей от
120