
книги / Технология получения активных углей и их применение
..pdf6.4.Адсорбционные свойства активных углей
иметоды их определения
6.4.1.Методы определения динамической активности по бензолу и хлорэтилу
МетодыисхемыприборовприведенывГОСТ17218–71 и18261–72. Динамическая активность сорбентов характеризуется величиной, называемой временем защитного действия (ВЗД) слоя сорбента, – это промежуток времени от начала пропускания ГВС через слой сорбента до момента появления проскоковой концентрации вещества за слоем сорбента. При этом часть адсорбционной емкости в слое не ис-
пользуется.
Динамическая адсорбционная способность слоя сорбента характеризуется количеством вещества, поглощенного до момента «проскока» и отнесенного к массе загруженного в колонку сорбента (ад).
Отношение динамической адсорбционной способности слоя сорбента (ад) к его равновесной адсорбционной способности (ар) называется степенью использования адсорбционной емкости слоя α:
α = ад/ар. |
(6.21) |
Сущность метода определения ВЗД по бензолу или хлорэтилу заключается в измерении времени от момента пуска паровоздушной смеси через слой сухого активного угля до момента появления за слоем паров бензола или хлорэтила в количестве, фиксируемом индикатором.
На рис. 6.5 дана принципиальная схема типового динамического прибора, рассчитанного на одновременное испытание четырех проб; допускаются приборы с меньшим или большим числом динамических трубок. В качестве очистителя воздуха применяют любую коробку противогаза с фильтром.
За рубежом используются методы оценки адсорбционной активности по бутану и четыреххлористому углероду в соответствии
сASTM D 3467–04(2014), ASTM D 5742–95(2015).
ВРФ находятся в стадии разработки ГОСТы по определению активности активных углей по бутану и четыреххлористому углероду.
81
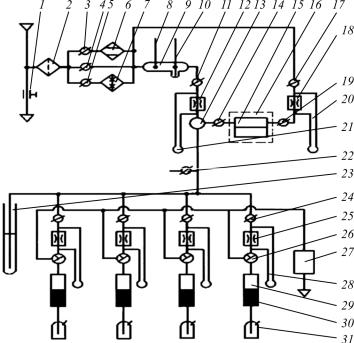
Рис. 6.5. Схема динамического прибора: 1 – зажим; 2 – очиститель воздуха; 3, 4, 5, 11, 14, 17, 19, 22, 24 – краны двухходовые; 6 – осушитель; 7 – увлажнитель; 8 – «сухой» термометр психрометра; 9 – аспирационная трубка психрометра; 10 – «влажный» термометр психрометра; 12 – диафрагма «воздушного» реометра; 13 – смеситель; 15 – испаритель; 16 – термостат; 18 – диафрагма «газового» реометра; 20, 21, 28 – дифманометры реометров; 23 – маностат; 25 – диафрагмы реометров в ветвях; 26 – краны трехходовые; 27 – поглотительный бачок; 29 – динамическиетрубки; 30 – испытываемыепробы; 31 – индикаторныесклянки
6.4.2. Определение суммарного объема пор по воде (ГОСТ 17219–71)
Этот метод основан на заполнении водой пор размером от 0,5 до 104 нм при кипячении навески активного угля в воде с последующим удалением ее избытка с поверхности зерен угля путем отсасывания в вакууме при определенных условиях.
Определение суммарного объема пор по воде проводят на приборе, представленном на рис. 6.6.
82
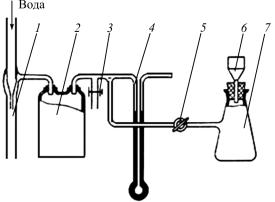
Рис. 6.6. Схема прибора для определения объема пор по воде: 1 – водоструйный насос;
2– колба двугорлая; 3 – зажим; 4 – манометр; 5 – соединительный кран; 6 – воронка;
7 – колба для отсасывания
Навеску угля высыпают через воронку в коническую колбу, заливают 100 см3 воды и отмечают ее уровень. Содержимое колбы кипятят в течение (15 ± 1) мин, после чего добавляют холодную дистиллированную воду до первоначального объема и наружную поверхность колбы охлаждают водой из-под крана до комнатной температуры. Через воронку с бумажным фильтром при разрежении (60 ± 5) мм рт. ст. фильтруют содержимое колбы, количественно перенося уголь на воронку. После полного удаления жидкости в течение 3 мин при разрежении (60 ± 5) мм рт. ст. продолжают отсасывание пробы угля, затем пробу ссыпают в бюкс, взвешивают с закрытой крышкой.
Суммарный объем пор (V , см3/г) вычисляют по формуле
V m1 m , |
(6.22) |
|
m |
|
где m – масса сухого угля, г; m1 – масса влажного угля, г; ρ – плотность воды, см3.
83

6.4.3. Определение адсорбционной активности активных углей по метиленовому голубому (ГОСТ 4453–74)
Приготовление исходного раствора метиленового голубого (МГ) с
концентрацией 1500 мг/дм3: 1,5 г МГ растворяют в воде в мерной колбе
V = 1 дм3.
Приготовление калибровочных растворов из исходного раствора
(С = 1,5 г/дм3):
1)10 см3 исходного раствора разбавляют водой до 100 см3, получают раствор с концентрацией С1 = 150 мг/дм3;
2)из раствора С1 отбирают 50 см3 и доводят до 100 см3, получают раствор с С2 = 75 мг/дм3;
3)из полученного раствора отбирают 50 см3 и доводят до 100 см3, получают раствор с С3 = 37,5 мг/дм3 и т.д.
Аналогичным образом получают калибровочные растворы с концентрациями 18,75 и 4,68 мг/дм3:
|
150,00 |
|
|
|
|
|
C, мг/дм3 |
75,00 |
37,50 |
18,75 |
9,38 |
4,68 |
|
D |
0,88 |
0,45 |
0,22 |
0,11 |
0,05 |
0,03 |
На основании полученных данных строят калибровочный график. Для определения адсорбционной активности образцов по МГ навеску АУ массой 0,1 г помещают в исходный раствор с концентрацией С0 = 1500 мг/дм3 объемом V = 25 см3. Встряхивают 30 мин, затем отфильтровывают, из полученных фильтратов отбирают 5 см3 и разбавляют водой в мерных колбах на 50 см3. Оптическую плотность раство-
ров определяют фотоэлектроколориметрическим методом.
Определение катионообменной активности по щелочи. Около
0,5 г угля взвешивают (результат взвешивания записывают с точностью до четвертого десятичного знака), помещают в коническую колбу вместимостью 250 см3, добавляют 50 см3 0,1 н. раствора гидроксида натрия, закрывают пробкой и вручную каждую минуту взбалтывают в течение 60 мин. Затем раствору дают отстояться и из колбы пипеткой осторожно, чтобы не попали частички угля, отбирают 10 см3 раствора, помещают в коническую колбу и титруют 0,1 н. раствором соляной ки-
84
слоты в присутствии индикатора фенолфталеина до исчезновения окраски. Одновременно проводят холостой опыт, для этого 10 см3 0,1 н. раствора едкого натра помещают в коническую колбу и титруют 0,1 н. раствором соляной кислоты в присутствии индикатора фенолфталеина до исчезновения окраски.
Сорбционную емкость угля по щелочи (А2, ммоль-экв/г) вычисляют по формуле
A2 |
|
(V1 |
V2 ) 100 |
, |
(6.23) |
|
m (1 W ) |
||||||
|
|
|
|
где V1 – объем 0,1 н. раствора соляной кислоты, израсходованный на титрование 10 см3 раствора едкого натра, см3; V2 – объем 0,1 н. раствора соляной кислоты, израсходованный на титрование 10 см3 раствора едкого натра после обработки углем, см3; 100 – поправочный коэффициент; W – влажность угля, %; m – масса навески угля, г.
За результат анализа принимают среднее арифметическое результатов двух параллельных определений, абсолютное расхождение между которыми не превышает допускаемое расхождение, равное 3 %.
Контрольные вопросы
1.В какие группы можно объединить методы анализа активных
углей?
2.Перечислите физико-механические методы анализа активных
углей.
3.В чем заключается сущность методов определения истинной
икажущейся плотностей активных углей? Как, зная ρист и ρкаж, определить общую пористость сорбента и его суммарный объем пор?
4.Что характеризует коэффициент объемной усадки гранул? Как его рассчитать?
5.Перечислитеметодыанализахимическихсвойствактивныхуглей.
6.Перечислите методы определения сорбционных свойств активных углей.
85

7. ТЕХНОЛОГИЧЕСКИЕ ОСНОВЫ ПРОЦЕССОВ ПОЛУЧЕНИЯ АКТИВНЫХ УГЛЕЙ
7.1. Основные технологические стадии получения активных углей и их влияние на качество готового продукта
В настоящее время активный уголь получают практически из всех видов углеродсодержащего сырья. Классификация активных углей по агрегатному состоянию с учетом их технологических переделов и вида исходного углеродсодержащего сырья представлена в табл. 7.1 [1].
Таблица 7 . 1
Классификация активных углей по типу углеродсодержащего сырья и агрегатного состояния
Тип сырья |
Порошко- |
Гранулированные |
Дробленые |
|
|
образные |
(экструдированные) |
из исходного |
через |
|
|
|
сырья |
передел |
Каменный уголь |
+ |
+ |
+ |
+ |
Бурый уголь |
+ |
– |
+ |
– |
Древесина |
+ |
+ |
+ |
– |
Торф |
+ |
+ |
– |
+ |
Лигнин гидролизный |
+ |
+ |
– |
+ |
Нефтекокс |
+ |
+ |
– |
+ |
Полимерные материалы |
+ |
+ |
+ |
– |
Косточка фруктовая, |
+ |
+ |
+ |
- |
скорлупа кокоса |
|
|
|
|
На рис. 7.1 приведена классическая принципиальная схема переработки углеродсодержащего сырья в активный уголь. Аппаратурное оформление приведенной схемы получения активного угля может быть самое разнообразное с высоким уровнем автоматизации всего процесса.
Основные технологические операции, используемое сырье и технологическое оборудование для производства различных типов активных углей достаточно близки. В связи с этим в технологических процессах полученияразличныхактивныхуглейиспользуетсяподобноеоборудование.
86

Рис. 7.1. Принципиальная схема переработки углеродсодержащих материалов в активный уголь
Как известно, на качество активных углей влияют характеристики сырья и заданные параметры технологического процесса. Основные характеристики сырья, используемого в технологии получения активных углей, приведены в табл. 7.2.
Таблица 7 . 2
Основные характеристики сырья, рекомендуемого для получения активных углей
Показатель |
Значение |
ГОСТ |
Зольность, %, не более |
6 |
ГОСТ 11055–78, |
|
|
ГОСТ 11022–95 |
Содержание влаги, %, не более |
10 |
ГОСТ 11014–2001, |
|
|
ГОСТ 27314–91 |
Содержание общей серы, %, не более |
0,5 |
ГОСТ 8606–93 |
Выход летучих веществ, % |
14–23 |
ГОСТ6382–2001 |
Размер кусков каменного угля, мм |
13–300 |
ГОСТ 2093–82 |
Технологические схемы получения активных углей различных типов отличаются, в основном, наличием или отсутствием стадий, связанных с получением сорбентов различной формы: порошков, дробленых частиц неправильной формы, гранул. Каждый технологический процесс характеризуется определенными значениями параметров, которые оказывают существенное влияние на качество получаемого готового продукта. Наиболее сложной является технология получения гранулированных активных углей (ГАУ), так как включает стадии подготовки связующего, получение угольно-смоляной композиции (пасты), формование гранул. В качестве примера рассмотрим факторы влияния основных стадий технологических операций и их параметров получения гранулированного активного угля.
87
В.М. Мухин и др. [27] рассматривают влияние различных факторов технологического процесса получения активных углей (АУ) на их качество на основании анализа многочисленных экспериментальных данных по влиянию технологических параметров конкретной стадии на прочность, насыпную плотность, параметры пористой структуры, адсорбционную динамическую активность, выход готового продукта и количество образующихся отходов. Для расчетов авторы использовали формулу
D |
Пmax Пmin |
100 %, |
(7.1) |
i Пср
где Di – доля вклада конкретного параметра стадии в формирование свойств АУ по конкретному показателю качества, %; Пmax, Пmin, Пср – максимальное, минимальное и среднее значение показателя.
Определение доли вклада всех параметров конкретной стадии в формировании каждого конкретного показателя качества активного угля D рассчитывали по формуле
D |
Di |
, |
(7.2) |
|
n |
||||
|
|
|
где n – количество параметров на стадии.
Суммарную долю вклада стадии D вычисляли по формуле
D |
D |
, |
(7.3) |
|
n |
||||
|
|
|
где n – количество анализируемых показателей качества активного угля. В табл. 7.3 приведены расчеты D для вклада технологических ста-
дий процесса получения ГАУ в формирование его свойств. Возможность получения широкого ассортимента активных углей
парогазовой активации различного назначения может быть обеспечена гибким изменением технологии без переоборудования действующего производства. Для этого необходимо определить факторы, оказывающие наибольшее влияние на качество получаемого активного угля и долю вклада каждого из них, что подробно анализируется в работе [27] на примере технологии получения ГАУ.
88
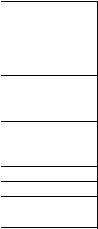
Таблица 7 . 3
Доля вклада технологических стадий процесса в формирование свойств газового гранулированного активного угля
Стадия |
Оборудование |
Доля вклада |
технологического |
|
в формирование |
процесса |
|
свойств АУ, % |
Дробление, размол гранул |
Система бункеров, дозаторов, транс- |
25–30 |
|
портеров |
0–1 |
Дробление сырья |
Зубчатые и валковые дробилки |
|
Размол сырья |
Шаровые мельницы |
2–5 |
Получение смеси смол |
Система емкостей, насосов, мерников |
15–20 |
Приготовление угольно- |
Объемные дозаторы смолы и пыли, |
5–10 |
смоляной пасты |
смесители |
5–10 |
Грануляция пасты |
Шнековые прессы |
|
Карбонизация гранул |
Барабанные печи карбонизации |
20–25 |
Активация гранул |
Многоканальные печи активации |
10–15 |
Рассев гранул |
Виброгрохоты |
3–5 |
Дробление, размол гранул |
ВальцевыестанкитипаЗРШ, мельницы |
2–4 |
Прежде всего следует выделить основные стадии процесса, необходимые операции на каждой стадии и границы варьирования технологическим параметром операции (табл. 7.4).
Таблица 7 . 4
Пределы измерений параметров технологических операций в производстве активных углей типа АГ
Стадия |
Операция |
Параметры операции |
Границы |
|
|
|
варьирования |
Подготовка углерод- |
Шихтование сырья |
Количество подшихто- |
0–100 % |
содержащего сырья |
|
вочного материала |
|
Подготовка связую- |
Получение смеси |
Количество компонен- |
То же |
щего |
смол |
тов смеси |
|
Приготовление |
|
Доля связующего |
25–35 % |
угольно-смоляной |
Смешение |
в пасте |
|
пасты |
|
Температурасвязующего |
40–80 °С |
Грануляция угольно- |
Формование гранул |
Размер гранул |
1–5 мм |
Производительность |
|
||
смоляной пасты |
|
пресса |
1–5 т/ч |
|
|
||
Карбонизация гранул |
Термообработка |
Температура |
450–750 °С |
Скорость подъема |
|
||
|
|
температуры |
10–40 °С/мин |
89
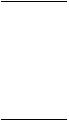
Окончание табл. 7 . 4
Стадия |
Операция |
Параметры операции |
Границы |
|
|
|
варьирования |
|
|
Температура |
850–1000 °С |
Активация гранул |
Термообработка |
Производительность |
0,1–6,0 т/сут |
Время термообработки |
24–72 ч |
||
|
|
Расход активирующих |
|
|
|
агентов |
2–15 кг/кг |
Рассев |
Рассев |
Размер гранул |
0,5–5 мм |
Дробление |
Дробление |
Размер зерен |
0,1–1,5 мм |
Размол |
Размол |
Остаток на сите № 01 |
1–10 % |
На первой стадии – подготовке углеродсодержащего сырья – показано влияние состава его угольной смеси на характеристики готового активного угля.
На примере получения ГАУ в работе [27] проведены расчеты и показано, что подшихтовка каменного угля полукоксом позволяет регулировать в достаточно больших пределах прочностные, структурные и адсорбционные свойства ГАУ (табл. 7.5).
Таблица 7 . 5 Характеристика активных углей в зависимости от состава сырья
Состав шихты, % |
Время акти- |
|
Характеристики активного угля* |
||||||||
Каменный |
Полукокс |
вации, мин |
, |
|
V , |
Пр, |
Vми, |
W0, |
Qпо |
||
уголь |
|
|
г/дм |
3 |
|
% |
3 |
/г |
3 |
/г |
бензолу, |
|
|
|
см3/г |
см |
см |
||||||
|
0 |
|
|
|
|
|
|
|
|
|
мин |
100 |
262 |
460 |
|
0,86 |
87 |
0,45 |
0,49 |
77 |
|||
75 |
25 |
230 |
450 |
|
0,86 |
86 |
0,34 |
0,33 |
70 |
||
50 |
50 |
208 |
460 |
|
0,88 |
83 |
0,32 |
0,33 |
68 |
||
25 |
75 |
184 |
450 |
|
0,85 |
79 |
0,30 |
0,32 |
64 |
||
0 |
100 |
166 |
450 |
|
0,86 |
78 |
0,28 |
0,28 |
52 |
*– насыпная плотность, г/дм3; V – суммарный объем пор по воде, см3/г;
Пр – прочность при истирании, %; Vми – объем микропор, см3/г; W0 – предельный объем сорбционного пространства, см3/г; Qпо бензолу – динамическая активность по бензолу, мин.
На стадии выбора связующего при получении ГАУ прежде всего следует учитывать, что прочностные свойства гранулы в основном определяются типом используемого связующего. Важнейшими показателями связующего являются выходы кокса и пека.
90