
книги / Управление производством и операциями
..pdfПроизводители должны помнить, что их цель не создание ценовых преимуществ или передовых технологий, цель – завоевание и удержание покупателей. И эта цель остается постоянной. Однако в мире жестокой конкуренции, где производственное превосходство и ценовые преимущества мимолетны, где предпочтения покупателей изменяются быстро и где технологии изменяются каждые два года, создание устойчивых конкурентных преимуществ кажется недосягаемым.
Ключ к конкурентным преимуществам лежит в решении проблем покупателей с использованием продуктов и услуг, которые могут меняться также быстро, как и сами проблемы. Производители должны фокусировать каждое подразделение организации прямо на покупателе, сосредоточивая свою деятельность вокруг деятельности покупателя.
4.6. Построение цепочки управления ценностью
Интегрированное управление бизнесом предполагает взаимосвязь управления спросом, продуктом и цепочкой ценностей. Продукт представляет собой основное средство удовлетворения потребителя. В задачу производителя входит определить потребность, создать продукт, удовлетворяющий этой потребности (см. рис. 4.3). Продукт – это ценность, обладание которой требует от потребителя определенных затрат (см. рис. 4.2).
Определение ценности продукта – первая задача построения цепочки управления ценностью.
Осуществление хозяйственной деятельности предполагает ее разделение на определенный набор функций: снабжение, производство, сбыт и т.д. В свою очередь, эти функции могут быть разделены на более мелкие, детализированные функции. Каждая из них реализуется определенным структурным подразделением предприятия или отдельным исполнителем.
Большая часть реальных рабочих процессов на предприятии включает множество функций, т.е. требует совместной работы нескольких подразделений. Однако в функционально ориентированных структурах управления обмен информацией, движение продукта между различными подразделениями часто сильно усложняется. Это приводит к большим накладным расходам и неоправданно длительным срокам выработки управленческих решений, что не может не сказаться на снижении общей ценности производимого продукта для потребителя и эффективности функционирования предприятия как единого целого.
Практика построения организационных структур управления производством на отечественных промышленных предприятиях показывает, что на них преобладает как раз функциональная структурная организация системы управления, что приводит
кпостроению так называемой «выталкивающей» системы изготовления продукции.
Вусловиях функциональной организации системы управления основной акцент сделан на «выталкивании» продукта на последующую стадию обработки. Построение единого информационного пространства (см. п. 4.5.2) не требуется, так
241

как каждая стадия обработки рассматривается как отдельный модуль со своими требованиями, слабо зависящими от предыдущей и последующей стадии.
Созданная как совокупность слабо связанных рабочих мест система управления позволяет улучшить качество выполнения отдельных функций, но не может дать существенного эффекта для общего повышения эффективности управления и нередко приводит к прямо противоположному результату.
Поэтому необходимо разработать механизм трансформации «выталкивающей» системы в «вытягивающую», в которой действующий механизм производственного процесса без ущерба для качества и функциональности должен быть преобразован в цепочку создания стоимости. Необходимо переосмыслить роль функциональных отделов и служб и всего предприятия, чтобы они не просто выполняли свои функции, а вносили свою лепту в создание ценности, и их работа соответствовала реальным потребностям. Необходимо пересмотреть взаимоотношения со всеми предприятиями, участвующими в жизненном цикле продукта (цепочке, потоке создания ценности) (см. рис. 4.15). Предприятиям (отделам, подразделениям) не следует работать порознь, разделяя поставку, производство и сбыт. Взаимоотношения необходимо рассматривать как единый поток создания ценности.
В основе построения клиентоориентированной системы управления производством лежат принципы бережливого производства, позволяющие сокращать процессы, снижающие или не добавляющие ценности конечному продукту. Выделяют до семи видов таких процессов, хотя никто не ограничивает фантазию по поводу умножения их номенклатуры:
1.Процессы, ведущие к перепроизводству.
2.Процессы ожидания.
3.Процессы лишней транспортировки.
4.Процессы излишней обработки.
5.Процессы, приводящие к избытку запасов.
6.Процессы, содержащие лишние движения.
7.Процессы, создающие дефекты.
Восьмая группа процессов связана с потерями, обусловленными игнорированием человеческого фактора. Последовательное или взрывное уменьшение таких процессов позволяет приблизить время и уровень издержек к минимуму, определяемому только временем передела.
Трансформация функционально-ориентированного («выталкивающего») производства в поточное1 («вытягивающее») должно начинаться с осмысления продуктов, процессов и потребностей. Осуществление процесса внедрения изменений будет подробно рассмотрено в гл. 5, сейчас мы опишем необходимые моменты преобразования производства.
Все начинается с наведения порядка и наглядной демонстрации неудобств, вызванных большими запасами. Для этого необходимо внедрить концепцию 5С (5S):
1 Поточное производство подразумевает «поток», цепочку создания ценности.
242
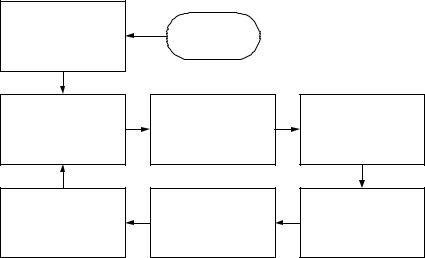
1)сэйри – организация (организация рабочего места – отделение вещей, которые необходимы для работы, от тех, которые не нужны, и поддержание их числа на минимально возможном уровне и в нужном месте). Сортируйте, избавьтесь от ненужного;
2)сэйтон – аккуратность (расположение предметов так, чтобы они наилучшим образом отвечали требованиям безопасности, качества и эффективности работы; упорядочение размещения предметов). Соблюдайте порядок: определите для каждой вещи свое место;
3)сэйсоо – чистота (поддержание рабочих зон всеми: от уборщицы до директора, в идеальной чистоте). Содержите рабочее место в чистоте;
4)сэйкэцу – стандартизация – постоянное поддержание и повторение установленных выше принципов «организации», «аккуратности» и «чистоты» как в отношении персонала, так и в отношении оборудования (стандартизация правил уборки, упорядочения и очистки). Стандартизируйте процедуры поддержания чистоты и порядка;
5)сицукэ – дисциплина – внедрение ответственности за то, что все должно делаться так, как это должно быть сделано, т.е. создание качественного рабочего места должно стать привычкой (дисциплина, соблюдение всеми работниками предприятия установленных правил поведения и норм общения). Совершенствуйте порядок, стимулируйте его поддержание чтобы каждый работающий смог понять
ипрочувствовать необходимость самоорганизации и исключения превышения некоторого разумного минимума.
Процесс совершенствования производства направлен на систематическое постоянное повышение потребительской удовлетворенности (рис. 4.18).
Определение |
Формирование |
|
|
ценности продукта |
|
||
рабочей группы |
|
||
для потребителя |
|
||
|
|
||
Анализ действующих |
Выявление процессов, |
Определение |
|
увеличивающих, |
необходимых реформ |
||
процессов создания |
не изменяющих, |
по изменению |
|
ценности |
уменьшающих |
производственных |
|
|
ценность |
процессов |
|
Анализ результатов |
|
|
|
внедрения |
Реализация |
Планирование |
|
(эффективность/ |
|||
намеченных планов |
проведения реформ |
||
удовлетворенность |
|||
|
|
||
потребителя) |
|
|
Рис. 4.18. Механизм совершенствования производственных процессов
243
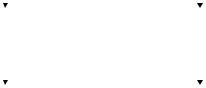
Команда проекта (рис. 4.19), сформированная из действующего персонала предприятия, должна быть наделена необходимыми полномочиями и ресурсами для осуществления проекта необходимых перемен.
|
|
Руководящая |
|
Координатор |
|||
|
|
группа |
|
|
проекта |
||
|
|
|
|
|
|
|
|
|
|
|
|
|
|
||
|
|
|
|
|
|
|
|
|
|
|
|
|
|
|
|
Руководитель |
|
|
Руководитель |
|
|||
группы |
|
|
|
группы |
|
||
процессов |
|
|
материалов |
|
|||
|
|
|
|
|
|
|
|
|
|
|
|
|
|
|
|
|
|
|
|
|
|
|
|
Группа |
|
|
|
Группа |
|
||
процессов |
|
|
материалов |
|
|||
|
|
|
|
|
|
|
|
Рис. 4.19. Структура управления проектом преобразования производства
Структура управления проектом по внедрению бережливого производства устанавливает внутреннее организационное построение для преобразования производством.
Руководящая группа контролирует деятельность по внедрению проекта. Группа формируется из руководящих сотрудников следующих подразделений:
−высшее руководство предприятия;
−проектирование;
−материально-техническое обеспечение производства;
−технологическое обеспечение производства;
−производство;
−контроль качества;
−кадры;
−информационное обеспечение.
Руководящая группа выполняет роль совета директоров по внедрению концепции бережливого производства и готовится к трансформации производства в масштабах всей компании. Поскольку группа помимо руководства проектом продолжает осуществлять свои функции, то работа руководящего комитета сводится к проведению совещаний, выработке решений по преобразованию производства, доведению их до персонала, ответственного за внедрение изменений.
Руководящая группа:
1) определяет приоритеты в реализации проекта, выбирает последовательность продуктов для вовлечения в цепочку ценности, разрабатывает план действий, осуществляет координацию реализации проекта с текущей деятельностью;
244
2)разрабатывает стратегию коммуникаций;
3)разрабатывает стратегию и программу обучения персонала;
4)направляет кадровые ресурсы предприятия в группы по внедрению;
5)обеспечивает финансирование проекта;
6)оценивает достигнутые цели и корректирует план действий.
Для обеспечения коммуникаций между руководящей группы и командами процессов и материалов выбирается координатор проекта, который занимается исключительно реализацией проекта. Координатор проекта должен: контролировать ход выполнения плана проекта, осуществлять коммуникации между руководящей группой и исполнительным персоналом, разрабатывать план вовлечения персонала компании, поставщиков, партнеров, потребителей в процесс управления цепочкой ценностей.
Поскольку бережливое производство моделирует производственные процессы, необходимо собрать и проанализировать значительный объем информации. Для улучшения решения поставленной задачи можно сформировать две рабочие группы: по внедрению производственных процессов (группа процессов) и по управлению материальными запасами (группа материалов). Руководитель каждой группы должен обеспечивать:
1)руководство группой и групповую работу;
2)доведение рабочих задач до членов команд с целью своевременного выполнения этапов и достижения целей;
3)руководство и контроль достижения целей этапов, распределение обязанностей, оценку и доступность ресурсов, выявление проблем реализации изменений;
4)мотивацию группы к выполнению поставленных задач;
5)документальное сопровождение инноваций.
В состав группы процессов входят представители проектирования, подготовки производства, производства, диспетчирования, контроля качества и планирования. Задачи группы процессов:
1. Определение производственных процессов:
− создание схем технологических процессов для всех исходных технологических линий, включенных в проект;
− определение параметров производственных процессов, выявление потерь. 2. Составление карты процессов:
− определение продукции, для которой используются общие производственные процессы;
− выявление повторной обработки, выявление потерь. 3. Составление карты последовательности событий:
−документирование последовательности рабочих задач;
−выявление времени для выполнения каждой задачи;
−определение и документирование критериев качества.
245
4. Проектирование линии оптимизации мощностей:
−определение требуемых ресурсов по типу и количеству;
−определение требуемого персонала;
−определение графика работы;
−разработка производственной линии;
−управление параметрами изменения производственных мощностей; 5. Обучение сотрудников:
−обучение сотрудников в условиях бережливого производства;
−обучение производству смешанной номенклатуры.
В состав команды материалов входят представители планового отдела, отдела снабжения, складирования, сбыта, маркетинга. Задачи группы материалов:
1. Определение продуктов, входящих в цепочки ценностей:
−определение продуктов из всего ассортимента для участия в проекте по внедрению цепочки ценностей;
−определение объема спроса на выбранные изделия.
2.Создание списка компонентов, входящих в выбранные изделия.
3.Разработка системы управления движения материалами:
−разработка системы – последовательность и частота поставки, размеры групп комплектующих, требования к упаковке, требования к расположению запасов, разработка системы учета;
−организация подачи материалов, управление информацией, наполнение стеллажей и транспортных машин;
−обучение персонала работе с вытягивающей системой при помощи управления информацией.
4. Определение последовательности выполнения заказов:
−разработка стандартного формата уведомления о последовательности заказов, подлежащих производству на линии;
−разработка информационной системы управления заказами.
Все продукты должны быть классифицированы по сходным группам. Для каждого производимого изделия должна быть составлена графическая схема технологического процесса, показывающая взаимодействие процессов производства (рис. 4.20). Если продукты имеют общую схему, то разрабатывается одна схема, которая впоследствии используется для окончательного проекта многономенклатурной линии.
Для каждого процесса, как указано на схеме технологического процесса, разрабатывается карта последовательности операций (табл. 4.5), иллюстрирующая подробные задачи, и требуемое время на выполнение каждой операции в ходе реализации процесса.
Карта последовательности операций представляет собой операционную карту технологического процесса, в которой каждая операция делится на три категории: наладка, необходимая работа и перемещение.
246
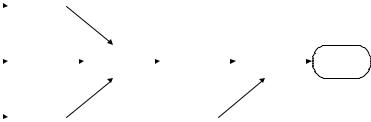
|
|
Процесс 9 |
|
|
Процесс 10 |
|
|
|
|
|
|
|
|
|
|
|
|
|
|
|
|
|
Готовый |
|||
|
|
|
|
|
|
|
|
|
|
|
|
|
|
|
|
|
|
|
|
|
|
|||||
|
|
|
|
|
|
|
|
|
|
|
|
|
|
|
|
|
|
|
|
|
|
|
|
|
||
|
|
|
|
|
|
|
|
|
|
|
|
|
|
|
|
|
|
|
|
|
|
|
|
|
||
|
|
Процесс 1 |
|
|
Процесс 2 |
|
|
Процесс 3 |
|
|
|
Процесс 4 |
|
|
|
Процесс 5 |
|
|
|
|||||||
|
|
|
|
|
|
|
|
|
|
|
|
|
|
|
продукт |
|||||||||||
|
|
|
|
|
|
|
|
|
|
|
|
|
|
|
|
|
|
|
|
|
|
|
|
|
||
|
|
|
|
|
|
|
|
|
|
|
|
|
|
|
|
|
|
|
|
|
|
|
|
|
|
|
|
|
|
|
|
|
|
|
|
|
|
|
|
|
|
|
|
|
|
|
|
|
|
|
|||
|
|
Процесс 6 |
|
|
Процесс 7 |
|
|
|
|
|
|
Процесс 8 |
|
|
|
|
|
|
|
|
|
|
|
|||
|
|
|
|
|
|
|
|
|
|
|
|
|
|
|
|
|
|
|
|
|
|
|||||
|
|
|
|
|
|
|
|
|
|
|
|
|
|
|
|
|
|
|||||||||
|
|
|
|
|
|
Рис. 4.20. Схема технологического процесса |
|
|
||||||||||||||||||
|
|
|
|
|
|
|
|
|
|
|
|
|
|
|
|
|
|
|
|
|
|
|
|
|
|
Таблица 4.5 |
|
|
|
|
|
|
Карта последовательности операций |
|
|
|
|
|
|
||||||||||||||
|
|
|
|
|
|
|
|
|
|
|
|
|
|
|
|
|
|
|
|
|
||||||
|
|
|
|
Продукт 1 |
|
|
|
|
|
|
|
|
|
|
|
|
Процесс 2 |
|
||||||||
№ |
|
Операция |
|
|
Ценность |
Наладка |
Работа |
|
Переме- |
Контроль |
||||||||||||||||
п/п |
|
|
|
|
щение |
|
качества |
|||||||||||||||||||
|
|
|
|
|
|
|
|
|
|
|
|
|
|
|
|
|
|
|
|
|
||||||
|
|
|
|
|
|
|
|
|
|
|
|
|
|
|
|
|
|
|
|
|
|
|
||||
10 |
Операция 10 |
|
|
Х |
|
|
|
|
|
|
|
|
|
|
|
|
|
|
|
|
|
|
||||
20 |
Операция 20 |
|
|
Х |
|
|
|
|
|
|
|
|
|
|
|
|
|
|
|
|
|
|
||||
30 |
Операция 30 |
|
|
|
|
|
|
|
|
|
|
|
|
|
|
|
|
|
|
|
|
|
|
|
||
40 |
Операция 40 |
|
|
|
|
|
|
|
|
|
|
|
|
|
|
|
|
|
|
|
|
|
|
|
||
… |
Операция … |
|
|
|
|
|
|
|
|
|
|
|
|
|
|
|
|
|
|
|
|
|
|
|
||
n |
Операция n |
|
|
Х |
|
|
|
|
|
|
|
|
|
|
|
|
|
|
|
|
|
|
Определение, является ли операция добавляющей ценность продукту, основывается на ответе на вопросы: Готов ли клиент оплачивать время выполнения операции при наличии выбора? Добавляет ли данная операция ценность путем изменения формы, размеров, функции или является необходимой для выполнения процесса? Каждая операция, не добавляющая ценность, помечается знаком «Х» и служит предметом для дальнейшего усовершенствования. Работы по наладке, перемещению и контролю качества рассматриваются как не добавляющие ценности и являются первыми кандидатурами на усовершенствование.
На основе схемы технологических процессов и карты последовательности операций составляется таблица процессов/продуктов (табл. 4.6) для определения групп продуктов с общими процессами и нормами времени.
Параллельно необходимо провести работу по делегированию полномочий и доведению стратегических целей от высшего уровня до рабочих, в соответствии с их квалификацией и способностями. Эта работа сочетается с выстраиванием цепочек внутренних потребителей и поставщиков, ориентированных на потребителей.
Цепочки внутренних потребителей и поставщиков необходимо превратить в последовательности процессов. Это даст возможность сформировать потоки создания
247
|
|
|
|
|
|
|
Таблица 4.6 |
|
|
Таблица процессов/продуктов |
|
|
|||
|
|
|
|
|
|
|
|
|
Процесс 1 |
|
Процесс 2 |
Процесс 3 |
|
Процесс … |
Процесс 10 |
Продукт 1 |
Х |
|
Х |
Х |
|
Х |
Х |
Продукт 2 |
Х |
|
Х |
Х |
|
|
|
Продукт 3 |
Х |
|
|
Х |
|
Х |
Х |
Продукт 1 |
|
|
Х |
|
|
Х |
Х |
Продукт n |
Х |
|
Х |
Х |
|
|
Х |
ценностей как для внутренних, так и для внешних потребителей. Эти потоки нужно распространить на внешних поставщиков, что позволит минимизировать дискретности и разовые объемы поставок с максимальным приближением их к реальным потребностям процессов. Фактически речь идет о подготовке к внедрению управления цепочками ценностей в рамках всего жизненного цикла изделий. Превращение сетей поставок в потоки означает также непрерывность движения перерабатываемых ресурсов в ритме, задаваемом потребителями по принципу «вытягивания». Таким образом, автоматически получается система «точно в срок». Все это приводит к созданию тотальной системы вовлечения работников в процессы создания ценностей в соответствии с целями предприятия.
Лучше всего начать путь преобразования предприятия с графической интерпретации потока создания ценности. Это поможет получить более полное представление о процессах предприятия. При визуализации текущего состояния предприятия будут представлены все действия (как добавляющие, так и не добавляющие ценность), необходимые для прохождения продукта от стадии проектирования до поставки заказчику.
Когда зафиксировано текущее состояние, становится ясно, где возникают потери и где их источник. Затем можно браться за интепретацию будущего, желаемого состояния предприятия, где уже будут отражены выровненные, более эффективные технологические потоки.
Следующие шаги по управлению цепочками ценностей осуществляются уже фактически с помощью и на основе инициатив по повышению качества и уменьшению издержек. Искусное направление этих инициатив в сторону поддержания непрерывного движения потока ценности с помощью инфраструктуры (оборудования и оптимально планируемых помещений) обеспечивает организацию управления производством.
Такая последовательность действий ведет к тому, что на предприятии начинает работать система тотального обеспечения качества и уменьшения издержек. Рабочие, инженеры и менеджеры, направляя свои усилия на устранение причин несоответствий и лишних и вредных издержек, в рамках периодических мероприятий по прорывным улучшениям способны совместными усилиями создать цепочку (поток) ценностей как высшую форму эффективного бизнеса.
248
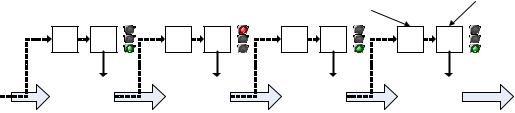
Особое значение имеет информационное обеспечение, которое поддерживает непрерывность цепочки (потока) ценности и ее эффективность. В системе обязательно наличие четкого управленческого учета, обеспечивающего пользователей только релевантной информацией, которая всегда достоверна, своевременна и объективна. Кроме того, информация должна быть представлена в форме, понятной ее потребителю, в виде, позволяющем очень быстро принять правильное решение.
Поэтому для работающих очень важно соблюдение принципа визуальной информированности о состоянии дел в ближайших точках цепочки. Информация должна отображаться в виде, доступном для наблюдения практически всем работающим в пределах данной актуальной части цепочки ценности.
Необходимо разработать систему сигналов, управляющих движением материалов (система «канбан»), которая позволит «вытягивать» материалы и комплектующие на основании потребностей последующих процессов. Выполнение работы должно производиться по принципу FIFO (First input – First Output, первый пришел – первый ушел).
Ключевым элементом информационной системы обеспечения является сигнал. По мере отпуска деталей (Д) в производство и истощения запаса на рабочем месте (опустошение контейнера, удаление детали из рабочей зоны и т.п.) система должна выдавать сигнал о потребности в определенной детали (рис. 4.21).
Точка
Точка потребления пополнения
Д |
Д |
Д |
Д |
Д |
Рабочее |
|
Рабочее |
|
Рабочее |
|
Рабочее |
место 1 |
|
место 2 |
|
место ... |
|
место n |
|
|
|
|
|
|
|
Поток создания ценности
Рис. 4.21. Управление материальными запасами
Когда запас деталей в точке их потребления исчерпан, система подает сигнал к пополнению запаса. Рядом с рабочим местом находится точка потребления материала (деталь, комплектующая) и точка пополнения, откуда деталь поступает в точку потребления. Поставщики материалов и комплектующих включаются в цепочку создания ценности и получают сигналы о потребности в поставке посредством Интернета в режиме реального времени. Основой для управления сигналами в цепочке создания ценности может быть ERP/MRP-система, обеспечивающая управление ресурсами предприятия и интегрированная с контрагентами (см. рис. 4.15), образуя единое информационное пространство.
249
В едином информационном пространстве обеспечивается видение всей цепочки ценности, позволяющее произвести комплексную оценку процессов и их взаимосвязь. В оперативном управлении производством все участники будут работать на основе визуализации, и для них важнее ситуационная информация о движении потоков, чем откорректированный централизованный план.
Согласно Д. Хоббсу [111], этапы внедрения бережливого производства – цепочки ценности:
1.Инициация и запуск проекта.
2.Оценка продуктов, процессов и материалов.
3.Завершение инициации проекта.
4.Планирование производственных мощностей.
5.Ввод в эксплуатацию.
6.Эксплуатация.
Этап 1. Инициация и запуск проекта
Цель: запустить проект по внедрению. Сформулировать стратегическое видение будущего. Определить состав групп и обучить участников. Составить план действий. Определить количественные критерии оценки внедрения бережливого производства. Выбрать продукты, с которых начинать построение цепочек ценностей. Определить объем производства на бережливой линии. Начать сбор информации для проектирования бережливой линии. Начать создание схем технологических процессов (см. рис. 4.20), карты последовательности операций (см. табл. 4.6). Определить комплектующие для включения в информационную систему пополнения запасов (см. рис. 4.21).
Этап 2. Оценка продуктов, процессов и материалов
Цель: продолжить сбор и документирование информации, начатых на этапе 1. Определить производительность на каждом процессе. Выявить группы продуктов с учетом общности процессов (см. табл. 4.6). Определить и задокументировать точки потребления и пополнения материалов и комплектующих. Установить цепочки «вытягивания» и время пополнения.
Этап 3. Завершение инициации проекта
Цель: завершить все действия по сбору информации. Окончательно определиться по продуктам, процессам, материалам, объемам выработки и времени работы бережливой линии. Завершить документирование всех задач карты последовательности операций, времени процессов и параметров производительности процессов. Окончательно отобрать компоненты для системы «вытягивания», произвести расчет всех ресурсов для планирования бережливой линии.
Этап 4. Планирование производственных мощностей
Цель: создать модель производственных мощностей на основании расчета ресурсов согласно схеме технологических процессов. Определить местонахождение устройств, информирующих о запуске предыдущих процессов, разработать план функционирования информационной системы вытягивания. Разработать план размещения производственных мощностей.
250