
книги / Усталость металлов
..pdf
|
1а |
|
Предел |
Изменение |
|
||
|
О3 |
|
усталости |
предела уста- |
|
||
|
SET |
Вид |
необработан |
лости образ- |
|
||
|
о .* |
ных образцов |
цов вследствие |
X |
|||
Сталь |
с га |
|
в кГ/мм2 |
обработки в % |
|||
нагрузки |
X |
||||||
|
У Ь |
|
|
|
|
ГГ |
|
|
|
|
|
|
|
||
|
|
глад |
с над |
глад |
с над |
о |
|
|
га - |
|
н |
||||
|
|
|
ких |
резом |
ких |
резом |
S |
|
|
|
|
|
|
|
|
Хромомолибденованадие- |
141,5 |
Осевое |
62,8 |
16,5 |
—5 |
Р |
|
+ 142 |
|
||||||
вая |
97,4 |
Осевое |
35,9 |
|
|
|
|
Хромоалюминиевая |
— |
+ 2 |
|
|
|||
(1,7% Сг, 1,3% А1) |
|
Изгиб с вра- |
50,0 |
— |
+20 |
|
|
Хромомолибденовая |
106,5 |
щением |
60,0 |
19,65 |
+36 |
+300 |
^ [120J |
То же |
|
||||||
|
133,0 |
» |
74,6 |
27,8 |
+20 |
+ 189 |
|
Хромомолибденованадие |
141,0 |
» |
65,3 |
29,4 |
+24 |
+170 |
J |
вая |
|
|
|
|
|
|
|
Хромомолибденовая |
97,5 |
Плоский |
51,9 |
22,8 |
+23 |
+90 |
|
|
|
изгиб |
31,3 |
16,5 |
+20 |
+88 |
[196] |
|
|
Кручение |
|
||||
Хромомолибденованадие |
141,5 |
Плоский |
68,0 |
30,3 |
+ 1 0 |
+50 |
[311] |
вая |
|
изгиб |
39,7 |
22,4 |
+ 14 |
+60 |
|
|
|
Кручение |
|
||||
Хромоникелевая |
62 ,8 |
Изгиб с вра- |
23,6 |
__ |
+ 3 0 |
_ |
|
|
|
[120] |
|||||
(18,7% Сг, 9,3% Ni) |
|
щением |
43,0 |
7,85 |
+ 15 |
+750 |
|
Хромистая (12,3% Сг) |
91 ,0 |
|
|||||
|
|
большее коробление, чем при азотировании, так что обычно пос ле цементации требуется шлифование. Кроме того, в процессе закалки могут образоваться трещины.
Поверхностные покрытия стали. Покрытия из цветных метал лов наносятся электролитическим или другим способом и приме няются для повышения сопротивления износу, коррозии или усталостной коррозии, а также для восстановления изношенных деталей машин. Их влияние на сопротивление усталости рас сматривалось Хеймондом и Вильямсом [353]. Электропокрытие мягкими металлами, такими как кадмий, свинец, олово и цинк, мало влияет на сопротивление усталости, но покрытия тверды ми металлами (никелем или хромом) могут существенно снизить его. Некоторые типичные данные представлены в табл. 41—43. Понижение сопротивления усталости в результате хромирования зависит в некоторой степени от условий покрытия, однако дан ных для выбора оптимальных условий нет. На предел усталости обычно мало влияет толщина хромирования (табл. 43). Однако
Т а б л и ц а
Влияние хромового покрытия на сопротивление усталости стали
|
|
Покрытие |
нагруженияВид |
усталостиПредел обнепокрытых кГ/мм*вразцов усталоПредел покрытыхстиоб кГ/ммвразцов2 предеИзменение посусталостила покрытиялев % |
|
|
|
|
|
||
Сталь |
°вр |
|
|
|
|
в |
|
Толщина |
|
|
|
|
кГ/ммг |
Тип |
|
|
|
|
|
в мм |
|
|
|
|
|
|
|
|
41
Источник
Углеродистая (0;3% С) |
63 |
|
0,127 |
|
24.3 |
25.3 |
+ 2 |
[354] |
||||
SAE |
Х4130, нормализо |
|
|
0,0025— |
|
|
|
|
|
|||
ванная (0,3% С, 1% Сг) |
|
|
0,225 |
|
31.4 |
28.3 |
— 12 |
|
||||
SAE 4130, закаленная и |
|
|
0,0025— |
|
|
|
|
|
||||
отпущенная |
|
и |
|
— |
0,432 |
|
66,1 |
40,9 |
- 3 9 |
[355] |
||
SAE 6130, закаленная |
|
0,025— |
|
58,2 |
39.3 |
—32 |
|
|||||
отпущенная |
(0,3% |
С, |
|
|
0,225 |
|
|
|||||
1% Сг, 0,2% |
V) |
|
|
|
|
|
|
|
|
|
||
|
|
|
|
|
|
Стандарт |
0,025 |
|
|
42,5 |
—26 |
|
|
|
|
|
|
|
ное |
|
|
|
|||
SAE 4130 |
|
|
|
130,2 |
То же |
0,25 |
S |
57,2 |
44.7 |
—23 |
|
|
|
|
|
|
|
CR 110 |
) 0,025 |
ш |
52.8 |
—8 |
[353] |
||
|
|
|
|
|
|
(свойство |
К |
|
||||
|
|
|
|
|
|
/0,025 |
к |
|
|
|||
|
|
|
|
|
|
раствора) |
S |
|
51.8 |
—9 |
|
|
|
|
|
|
|
|
|
|
то |
|
|
|
|
|
|
|
|
|
|
|
|
сх |
|
|
|
|
|
|
|
|
|
|
|
|
m |
|
|
|
|
|
|
|
|
|
|
|
0,0025 |
о |
|
43,0 |
- 2 5 |
|
|
|
|
|
|
|
|
VO |
|
|
|||
|
|
|
|
|
|
|
0,0075 |
К |
|
42.4 |
—28 |
|
|
|
|
|
|
125,5 |
|
0,0127 |
(_ |
|
|
||
|
|
|
|
|
|
со |
59,0 |
42.4 |
—28 |
|
||
£п25 (2,3-2,8% Ni; 0,5— |
|
|
0,025 |
S |
37,7 |
—36 |
|
|||||
|
Стандарт |
0,150 |
|
|
33.9 |
—42 |
[353] |
|||||
0,8% Сг; 0,4-0,7% Мо) |
|
ное |
0,300 |
|
|
33.9 |
—42 |
|||||
|
|
|
|
|
94,5 |
|
0,025 |
|
43,7 |
32,4 |
—26 |
|
|
|
|
|
|
|
0,150 |
|
33,9 |
—22 |
|
||
|
|
|
|
|
|
|
0,30 |
|
|
33,2 |
—23 |
|
|
|
|
|
|
|
CR 110 |
0,0015 |
|
|
50.8 |
—33 |
|
SAE |
4140 |
|
|
— |
0,003 |
|
76,5 |
50.8 |
—33 |
|
||
|
|
(свойство |
|
[353] |
||||||||
|
|
|
|
|
|
раствора) |
0,0075 |
|
52,6 |
—31 |
||
|
|
|
|
|
|
|
0,25 |
|
|
51,5 |
—32 |
|
S11 |
(3% |
NiCr) |
|
|
99 |
— |
0,038 |
|
55,7 |
27.8 |
—50 |
|
S82 |
(4% |
NiCr), |
цементо |
111,5 |
|
0,25 |
VO |
68,2 |
27.8 |
—50 |
|
|
|
0,127 |
US |
30,2 |
—56 |
[310] |
|||||||
ванная |
|
|
|
|
|
|
со |
|
|
|
||
DTD 306 (3% СгМо), азо |
95,7 |
|
0,051 |
S |
72,6 |
60,5 |
—17 |
|
||||
тированная |
|
|
|
|
|
|
|
|
|
|
|
|
|
Покрытие |
|
Сталь |
°вр |
|
Тол |
Внутрен |
В |
|
нее |
||
|
кГ/мм2 |
Тип |
щина |
напряже |
|
|
|
в мм |
ние |
|
|
|
|
в кГ]мм2 |
Вид нагружения |
Предел устало сти до покрытия в кГ/мм2 |
Предел устало сти после покры тия в кГ/мм2 Изменение пре дела усталости после покрытия в % |
Источник |
Углеродис |
|
|
|
Высокое |
Изгиб 23,9 |
16,0 |
—33 |
|
тая: |
|
|
|
Низкое |
с вра |
|
22,3 |
—7 |
0,09% С |
— |
— |
|
|
|
|
|
|
|
|
ще |
|
|
|
|||
0,14% С |
|
|
0,0127 |
|
|
|
|
|
|
|
|
нием |
25,2 |
24,4 |
—3 |
||
|
|
|
|
|||||
|
|
|
0,0889 |
|
|
14,15 |
—44 |
|
|
|
|
|
|
|
|
||
Армко-желе- 31,4 |
|
0,102 |
|
|
20,7 |
22,6 |
+ 9 |
|
30 |
100,0 |
— |
0,038 |
— |
Изгиб |
|
34,2 |
—38 |
S11 (3% Ni, |
|
55,2 |
||||||
|
|
|
|
|||||
Сг) |
|
|
0,38 |
|
|
23,5 |
—57 |
|
SAE 4330 |
|
Мягкое |
0,0102 |
|
|
|
37.8 |
—32 |
|
(Watts) |
0,0102 |
|
|
|
37.8 |
—32 |
|
(Ni, Сг, Мо) |
— |
Твердое |
— |
— |
55,2 |
|||
|
|
|
0,076 |
|
|
|
30.9 |
—44 |
|
|
Мягкое |
0,025 |
|
|
|
30.9 |
—44 |
|
|
(Watts) |
|
|
|
|
|
|
|
|
|
0,025 |
29,0 |
— |
40,0 |
30,9 |
—20 |
|
|
Watts |
0,125 |
23,1 |
—40 |
|||
BS5005/401 |
68 |
|
0,125 |
|
|
|
29,4 |
—24 |
|
|
|
|
|
|
|
||
(3% Ni) |
|
|
0,025 |
|
|
|
43,3 |
+12 |
|
|
|
|
|
|
|||
|
|
Bright А. |
0,125 |
— |
— |
— |
28,9 |
—24 |
|
|
|
0,125 |
|
|
|
41,0 |
+ 7 |
|
|
|
0,025 |
18.85 |
|
|
46,4 |
—14 |
S65 |
|
|
0,125 |
18.85 |
|
|
29.8 |
—44 |
|
|
0,025 |
Небольшое |
|
|
36,1 |
—28 |
|
(3% Ni; |
114 |
Watts |
|
сжимаю |
— |
34 |
|
|
0,025 |
щее |
51.9 |
+ 3 |
|||||
1% Сг) |
|
|
Небольшое |
|
|
|||
|
|
|
|
сжимаю |
|
|
|
|
|
|
|
0,125 |
щее |
|
|
41,7 |
—21 |
|
|
|
—5,19 |
|
|
|||
|
|
Обдувка |
|
|
Изгиб |
|
13,35* |
—60* |
|
|
дробью |
|
|
|
28,8* |
—13* |
|
|
|
перед по |
|
|
с вра |
|
||
— |
— |
крытием |
— |
— |
ще |
33 |
38,5 |
- 1 7 ** |
|
|
Обдувка |
|
|
нием |
|
||
|
|
дробью |
|
|
|
|
|
после
покрытия
* Дробеструйная обработка перед покрытием. '* Дробеструйная обработка после покрытия.
[356)
[310)
[357)
[353)
[358)
Вильямс и Хеймонд (359] обнаружили заметное влияние толщи ны покрытия в зависимости от термообработки (рис. 99). При
Т а б л и ц а 43
Влияние цинкового покрытия на сопротивление усталости стали при изгибе с вращением [120]
Сталь
а вр |
Предел |
усталости |
|
в кГ/ммг |
до покрытия |
|
в кГ/мм* |
Изменение в % пре дела усталости вследствие
электрополирова ния |
гальваниза |
|
ции в рас |
|
плавленной |
|
соли |
л
ч
О)
н
са
и
с
еС
О)
4
о
и
5
0,2% С |
отпущенная |
31,4 |
19,0 |
+ 2 |
—4 |
|
0,45% С, |
55,5 |
25,3 |
_ |
—25 |
Шван- |
|
0,45% С, закаленная |
85,0 |
56,3 |
—42 |
|||
0,45% С . . . |
72,2 |
32,7 |
+ 5 |
— 14 |
гер |
|
0,72% С, |
отпущенная |
64,5 |
24,5 |
0 |
—13 |
и |
0,72% G, закаленная |
124 |
87,5 |
|
—40 |
Франс |
|
0,72% С |
|
118 |
66,0 |
+11 |
—42 |
|
0,5% С, |
нормализованная |
67,5 |
25,8 |
—2 |
—10 |
Соп- |
( 0 7 мм) |
вис |
|||||
0,5% С, |
после протягивания |
|
|
|
|
и |
( 0 7 мм) |
102 |
38,5 |
0 |
+ 1 |
Гаф |
|
Проволочная (0 2,54 мм) |
119—133 |
44—50,2 |
_ |
—21 до —28 |
Уотт |
|
|
|
153,5— |
45,5—51,75 |
— 15 до —20 |
||
|
|
176,0 |
|
|
|
|
никелевом покрытии предел усталости значительно понижается с увеличением толщины слоя (табл. 42). Было установлено, что снижение предела усталости в результате хромирования и никелирования непосредственно связано с растягивающими остаточными напряжениями в нанесенном слое. Барклай и Девис [356] и Олмен (358] показали, что предел усталости образцов, покры тых никелем, может повышаться, если остаточное растягивающее напряжение понизится при изменении процесса покрытия (табл. 42). Предел усталости деталей можно заметно изменить последующей термообработкой (рис. 99). Термообработка при 200—300° С снижает предел усталости, а при температуре выше 400° С — повышает. Было показано, что это связано с влиянием остаточных напряжений в слое; термообработка при 200—300° С увеличивает остаточное растягивающее напряжение, в то время как при температурах выше 440° С образуются сжимающие ос таточные напряжения. Подобные результаты были получены Лодженом (355] для хромомолибденовой стали SAEX4130. Тер мообработка после хромирования при температуре не меньше
400—450° С может рекомендоваться в том случае, когда допус кается размягчение нанесенного слоя и обработка не влияет на механические свойства стали [359]. В отличие от хрома низ котемпературное никелевое покрытие, примененное к средне- и
высокопрочной стали, мало влияет на предел усталости. |
|
|
||||||||||||
|
|
|
|
|
|
Предел |
усталости хромиро |
|||||||
кГ |
|
|
|
|
6-1 |
ванной |
|
или |
никелированной |
|||||
|
|
|
|
стали |
может |
увеличиваться |
||||||||
|
|
|
г |
% |
||||||||||
мм2 |
|
|
|
0 |
азотированием, |
дробеструйной |
||||||||
57 |
|
|
|
|
10 |
обработкой |
или поверхностной |
|||||||
*7 |
|
|
|
fp - |
обкаткой. Влияние дробеструй |
|||||||||
|
|
|
20 «о |
|||||||||||
|
|
|
ной обработки на никелирован |
|||||||||||
|
|
3 / |
|
f |
:э |
|||||||||
37 |
|
|
|
30 «о |
ные образцы |
исследовалось |
||||||||
|
|
|
|
съ |
Олменом (табл. 42). Обработ |
|||||||||
|
|
|
|
|
ка |
дробью |
перед |
покрытием |
||||||
27 |
|
|
|
|
50^ |
значительно увеличивает |
пре |
|||||||
|
|
|
|
|
60 |
дел усталости, но большее уве |
||||||||
17 |
|
5 / |
|
|
70 |
личение было получено при об |
||||||||
|
|
|
|
работке дробью после |
покры |
|||||||||
|
|
|
|
80 |
||||||||||
|
|
|
|
|
тия. Более |
поздние |
исследова |
|||||||
|
100 |
200 300 т |
500 t°c |
|
ния подтвердили, что обработ |
|||||||||
Рис. |
99. |
Влияние |
температуры t |
ка дробью |
высокопрочной ста |
|||||||||
ли |
после |
покрытия повышает |
||||||||||||
термообработки на |
предел устало |
ее |
предел |
усталости. |
Тонкое |
|||||||||
сти |
хромированных |
сталей |
при |
|||||||||||
разной |
толщине покрытия (сталь |
шлифование обдутой и необду- |
||||||||||||
|
Еп25, DPH400) |
[359]: |
|
той |
поверхностей, |
проводимое |
||||||||
/ — образец после механической обра |
либо до, либо после покрытия, |
|||||||||||||
ботки, без покрытия; 2 — электропо- |
||||||||||||||
лированный образец, |
без покрытия; |
не |
имеет |
значительного |
влия |
|||||||||
3 — |
0,025 мм Сг; 4 — 0,15 мм Сг; 5 — |
ния |
на |
сопротивление |
устало |
|||||||||
|
|
0,3 мм |
Сг |
|
|
|||||||||
|
|
|
|
|
|
сти |
[353]. |
установлено, |
что по |
|||||
|
|
|
|
|
|
Было |
нижение предела усталости в результате гальванизации можно частично объяснить влиянием водорода , проникающего в про цессе покрытия в сталь, однако влияние это невелико [360]. Пре делы усталости образцов, с которых были удалены никель или хром, равны или почти равны пределу усталости до гальваниза ции [120].
Сопротивление усталости сталей, покрытых никелем или хро мом, можно объяснить в общих чертах следующим образом. Когда основной металл менее прочен, чем покрытие, предел уста лости зависит почти полностью от свойств основного металла и покрытие влияет незначительно (см. результаты для сталей с 0,3% С в табл. 41 и для армко-железа в табл. 42). Для высоко прочных сталей предел усталости зависит преимущественно от прочности покрытия. Это очевидно из связи между пределом усталости и остаточным напряжением нанесенного слоя, а также из того, что для данной термической обработки предел усталости
хромированной стали почти не зависит от ее прочности [353]. Это поведение можно объяснить тем, что усталостная трещина обра зуется в нанесенном слое; концентрация напряжения в конце трещины может быть достаточной, чтобы обеспечить ее распро странение в слой металла под покрытием. С другой стороны, со противление основного металла распространению трещины мо жет иногда влиять на сопротивление усталости; например, азо тирование и наклеп перед нанесением покрытия повышают пре дел усталости.
В табл. 43 показано, что покрытие цинком, в отличие от нике лирования и хромирования обычно незначительно повышает пре дел усталости, в то же время горячее цинкование вредно.
Лав [120] по различным источникам сделал вывод, что покры тие свинцом, кадмием и распыленным алюминием мало влияет на сопротивление усталости; омеднение снижает предел усталос ти при изгибе на 12% и заметно снижает прочность при повтор ной нагрузке спиральных пружин. Другие опыты, однако, пока зали, что гальванизация кадмием может понизить предел уста лости очень прочных сталей [671]. Чтобы уменьшение сопротив ления усталости было минимальным, перед гальванизацией рекомендуется применять обработку, вызывающую остаточные сжимающие напряжения в поверхностных слоях. Для предотвра щения охрупчивания термообработку следует применять после гальванизации. Напыление металлом может заметно снизить сопротивление усталости (вероятно в результате грубой обработ ки, применяемой перед напылением). В последнее время, одна ко, было показано, что удовлетворительное сцепление можно по лучить при напылении тонкого слоя молибдена на поверхность, обдутую дробью, при этом предел усталости различных сталей снижается не более чем на 10% [361]. Фосфатизация повышает сопротивление коррозии трения, но значительно уменьшает пре дел усталости [120, 310].
Поверхностные покрытия цветных металлов и сплавов. Дан ных по влиянию поверхностных покрытий на предел усталости цветных сплавов значительно меньше, чем для стали. Влияние никелирования или хромирования на алюминиевый сплав не устойчиво; в некоторых случаях было найдено небольшое сни жение предела усталости [310], в то время как в других случаях предел усталости снижался значительно [353]. Покрытие чистым алюминием алюминиевых сплавов заметно понижает предел усталости лабораторных образцов (см. табл. 7), но мало влияет на предел усталости соединений деталей. Оксидные пленки обычно мало влияют на усталость алюминиевых сплавов [362], хотя предел усталости алюминиево-медного сплава снизился на 50% [363]. Значительное понижение предела усталости в резуль тате анодной обработки было обнаруженр также для магниевого сплава (см. табл. 51).
12 Заказ 893 |
" |
Г л а в а VII
КОРРОЗИОННАЯ УСТАЛОСТЬ И КОРРОЗИЯ ТРЕНИЯ
Коррозионная усталость
К оррозия поверхности металла может вызывать общее
увеличение шероховатости поверхности и образование каверн или трещин в отдельных точках, что может значительно умень шить сопротивление усталости, если на металл впоследствии действуют переменные напряжения. Значительно больше со противление усталости уменьшается в результате одновремен ного действия коррозии и переменных напряжений. Для характе ристики совместного влияния этих факторов используется поня тие коррозионной усталости.
Обзор по коррозионной усталости был составлен Гафом в 1932 г. [364], Гильбертом [365], Гоулдом [366] и Ивенсом [367]. Процесс образования трещин коррозионной усталости отличает ся от процесса образования трещин под действием статического напряжения в условиях коррозионной среды.
Коррозионное растрескивание под напряжением проявляется только в определенных металлах, в основном после неправиль ной термообработки [367], в то время как коррозионной усталости подвержено большинство металлов. Коррозионные усталостные разрушения отличаются от обычных усталостных разрушений.
Во-первых, поверхность излома часто изменяет окраску при коррозионном разрушении, хотя это не является характеристи кой существенной значимости. Степень наблюдаемой поверхно стной коррозии зависит от материала и коррозионной среды и обычно выше при разрушениях в рабочих условиях, чем в лабо раторных из-за относительной кратковременности большинства лабораторных испытаний. Поверхность обычных сталей незначи тельно ржавеет при испытании в пресной воде и больше в соле ной, но нержавеющие стали и азотированные стали часто не имели явных признаков ржавчины, даже если предел усталости значительно снижался при действии соленых брызг.
Другой отличительной чертой коррозионной усталости являет ся внешний вид усталостных трещин. Обычно возникает значитель но больше трещин, чем при обычном усталостном разрушении; это является следствием электрохимического поражения, интенсивость которого понижается по мере уменьшения трещины.
178
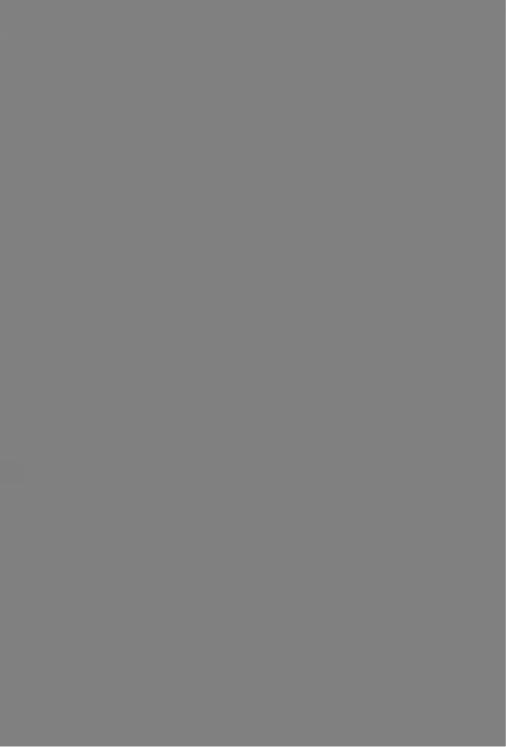
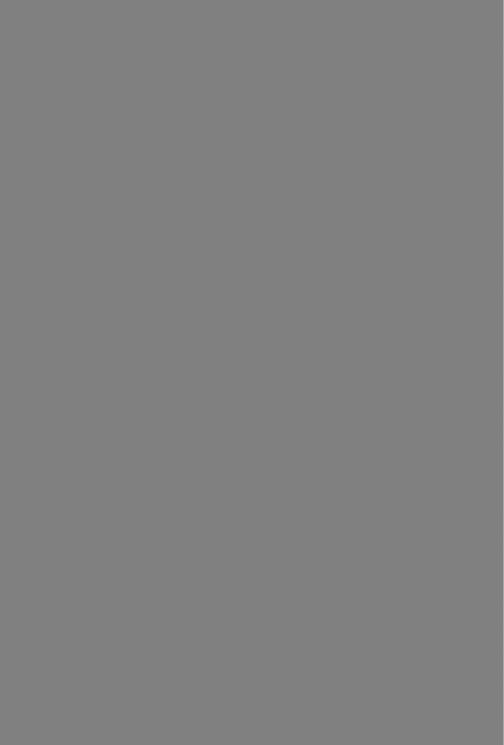
усталости, можно объяснить влиянием местного повышения на пряжения от коррозионных каверн.
Сравнения результатов усталостных испытаний, проводимых в коррозионной среде, с проводимыми на воздухе, показали, что вредное влияние коррозии увеличивается с продолжительностью
Рис. 103. Испытания на усталость (штриховые линии) и коррозионную усталость (сплошные линии) авиационных материалов [369]:
а |
— при изгибе; б — при растяжении-сжатии; |
1 — хромоникелевая сталь 17/1; |
|||
2 |
— углеродистая сталь |
(0,5% |
С); 3 — хромистая сталь (15% Сг); |
4 — хромо |
|
|
никелевая сталь 18/8; |
5 — |
дуралюмин; 5 |
— магниевый сплав |
(27а А1) |
испытания. Кривые ст — N, полученные при коррозионных испы таниях, имеют значительно меньшую тенденцию приобретать асимптотический характер даже в относительно слабой корро зионной жидкости, подобной пресной воде, и вряд ли какие-ни будь металлы имеют в этих условиях определенный предел уста лости. В сильно коррозионной среде непрерывное понижение кривой а — N может быть очень заметным. Это иллюстрируется рис. 103, где показаны результаты испытаний различных мате риалов при разбрызгивании соленой воды. В связи с этим необ ходимо проводить ограниченные пределы усталости для данной долговечности и не применять термина «коррозионный предел усталости». Установлено, что коррозионный предел усталости зависит от частоты циклического напряжения, и соответствую-
181