
книги / Усталость металлов
..pdfмеханически обработанных образцов при одной и той же шерохо ватости поверхности.
Грубое шлифование, однако, может снизить предел усталости [332], что можно считать результатом влияния остаточных рас тягивающих напряжений, наведенных в поверхности сильным местным нагревом.
Влияние специальных поверхностных обработок на сопротивление усталости
Поверхность металлов может обрабатываться различными способами. Во-первых, существует механическая обработка, включающая резание, шлифование и полирование, а также спе
* - t |
|
|
|
|
|
циальные |
виды обработки, |
на |
|||||
|
|
|
|
|
пример, обдувка дробью и об |
||||||||
кГ_ |
|
|
|
|
|
||||||||
мм1 |
|
|
|
|
|
катка |
поверхности |
роликами, |
|||||
77 |
|
|
|
|
|
благоприятно |
влияющие |
|
на |
||||
|
|
|
/ / |
|
|
сопротивление |
усталости. |
Во- |
|||||
55 |
|
|
|
|
|
вторых, |
существует |
термиче |
|||||
|
V |
|
|
|
ская обработка, например пла |
||||||||
|
|
|
|
|
менная или индукционная |
по |
|||||||
|
|
|
|
|
|
||||||||
33 |
|
|
|
|
|
верхностная закалка, и в-треть- |
|||||||
|
|
|
|
|
|
их, поверхностная химико-тер |
|||||||
1125 |
1 |
|
|
о 4*" |
мическая обработка, |
включаю |
|||||||
100 |
150 |
б$р кГ/мм1 |
щая цементацию, а также |
по |
|||||||||
50 |
|||||||||||||
|
|
|
|
|
|
крытия. Прежде чем подробно |
|||||||
Рис. 97. |
Влияние |
обезуглероживания |
изложить влияние поверхност |
||||||||||
на сопротивление |
усталости |
сталей |
ных обработок, рассмотрим со |
||||||||||
|
|
[326, 333]: |
|
|
противление |
усталости |
дета |
||||||
1 — |
полированные |
образцы; |
2 |
— образ |
лей, которым |
не дается |
ника |
||||||
|
|
цы после ковки |
|
|
кой дополнительной |
поверхно |
|||||||
стной обработки после формирования. |
Все металлы в этих слу |
||||||||||||
чаях показали |
пониженное сопротивление усталости |
из-за |
де |
фектов поверхности, но их влияние особенно существенно в ста лях, вследствие обезуглероживания поверхности, которое проис ходит в процессе горячей обработки или ковки в окисляющей ат мосфере.
Обезуглероживание. Заметное снижение сопротивления уста лости в результате обезуглероживания поверхности иллюстриру ется на рис. 97 [326, 333]. Испытывались образцы, не обработан ные после ковки, и полированные образцы, с которых был снят обезуглероженный слой. При низкой исходной прочности разли чие в пределах усталости небольшое, но влияние обезуглерожи вания возрастает с ростом предела прочности на растяжение. При свр = 94 кГ/мм2 предел усталости образцов после ковки составляет половину предела усталости полированных образцов,
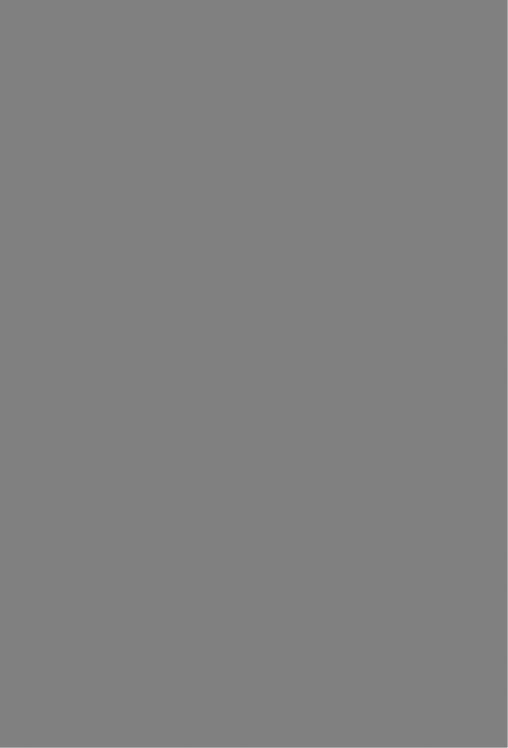
лости, а цементация с последующим хонингованием повышает прочность поверхности до такой степени, что усталостное раз рушение переносится под поверхностные слои.
Обдувка дробью. Основными результатами этой обработки является наклеп поверхностного слоя материала и наведение в нем остаточного сжимающего напряжения. Хотя поверхность, получаемая после обдувки дробью, много грубее, чем после ме ханической обработки, получающаяся при этом концентрация напряжений невелика, потому что глубина впадин составляет только небольшую часть их радиуса.
Обдувка дробью применяется почти исключительно для сталь ных деталей: влияние ее на сопротивление усталости описано в литературе [335—337]. Обдувка дробью мало влияла на предел усталости гладких полированных образцов. Лав [120] показал, что улучшение обычно составляет менее 20%, а в некоторых слу чаях образцы после обдувки дробью имели более низкий предел усталости, чем полированные. Значительное увеличение предела усталости можно получить при обдувке дробью кованых или тру- бо обработанных образцов. Данные об улучшении, которое мож но получить на окисленной и обезуглероженной поверхностях, приведены в табл. 36. Процесс наиболее широко используется для обработки пружин как спиральных, так и пластинчатых, так как пружины часто имеют обезуглероженную поверхность и дро беструйная обработка может увеличивать долговечность более эффективно и значительно более экономично, чем механическая обработка или шлифование. Этот метод используется также для обработки поверхностей, имеющих следы инструмента, царапины или другие источники концентрации напряжения и для шлифо ванных поверхностей, при наличии в поверхностном слое оста точных растягивающих напряжений. Лав [120] показал, что со противление усталости при дробеструйной обработке может увеличиваться на 5—100%.
Дробеструйная обработка повышает также сопротивление усталостной коррозии и коррозии трения (см. гл. VII).
Оптимальные условия дробеструйной обработки можно луч ше всего определять для каждого материала и детали проведе нием усталостных испытаний в рабочих условиях. Регулируемыми факторами являются тип и размер дроби, скорость, сообща емая ей, и длительность обдувки. Недостаток применения чугун- I ной дроби заключается в том, что она вследствие хрупкости рас калывается в процессе обработки, снижая ее качество. Стальная дробь из высокопрочной проволоки имеет большую долговеч ность, что обеспечивает постоянство режима обработки. Дробь диаметром 0,64—0,76 мм была признана удовлетворительной для обработки разнообразных по форме и величине деталей, но раз мер дроби, по-видимому, не является оптимальным (335, 336].
Дробь значительно меньших размеров оказалась эффектив-
164
ной для обработки деталей небольших сечений, таких как легкие пружины, и деталей с резкими изменениями сечения, хотя есть данные, что дробеструйная обработка эффективна, даже если дробь не проникает в вершину надреза [338]. Лессель и Бродрик
[339] |
показали, что для |
легированной стали оар = 91 и |
180,5 |
кГ/мм2 возникающее |
при обдувке максимальное остаточ |
ное напряжение не зависит от диаметра дроби при изменении его от 0,076 до 0,64 мм, а глубина остаточного сжатого слоя с увели чением размера дроби возрастает.
Джонис [336] установил, что при дробеструйной обработке давление сжатого воздуха обычно составляет 47—63 кГ/мм2, а
скорость дроби диаметром |
0,76 мм равна 55 м[сек\ |
при таком |
режиме сопротивление |
усталости сталей с |
овр = 135 |
-г- 157 кГ/мм2 повышалось. Чтобы получить хороший результат, обдувку дробью следует продолжать до тех пор, пока вся поверх ность детали не будет полностью обработана. Длительная обра ботка, а также слишком высокое давление могут дать перенаклеп, вызывающий поверхностные трещины и последующее пони жение предела усталости. Некоторый контроль интенсивности дробеструйной обработки можно осуществить, применяя пластин ки Олмена, представляющие собой тонкие стальные пластинки, наклепываемые дробью только с одной стороны; полученная в результате наклепа кривизна пластинки показывает величину остаточной напряженности [337, 340].
Олмен [341] показал, что максимальное сжимающее остаточ ное напряжение, вызываемое нормальной дробеструйной обра боткой, равняется приблизительно половине предела текучести материала, но оно может быть больше, если обрабатывается по верхность, на которую в это время действует растягивающее на пряжение; этот процесс известен как обдувка под напряжением. Сжимающее остаточное напряжение, равное пределу текучести От, можно получить при действии растягивающего напряжения, равного приблизительно от/2; Олмен считает это оптимальным условием. Максимальное увеличение предела усталости при этом может быть получено только тогда, когда на деталь при работе действует растягивающее напряжение; в противном случае ос таточное напряжение будет снижено последующей пластической деформацией. Влияние дробеструйной обработки под напряже нием на сопротивление усталости легких листовых рессор пока зано на рис. 98. В этих экспериментах некоторые образцы были обдуты под напряжением при сжатии, чтобы вызвать вредные растягивающие напряжения на поверхности. График результи рующего остаточного напряжения показан в правой части диа граммы; из результатов видно заметное влияние остаточных на пряжений на сопротивление усталости.
В некоторых случаях может быть необходимым или жела тельным применить дальнейшую поверхностную обработку после
165
обдувки дробью. Например, чтобы удалить очень острые высту пы на валу, возникшие в результате дробеструйной обработки, достаточно хонингования, которое незначительно снижает сопро тивление усталости (335]. Было показано, что предел усталости может быть увеличен на 20% полированием после обдувки дробью, причем оптимальная глубина полирования составляет около 0,13 мм [342]. Есть предположение, что повышение проч ности было получено в связи с тем, что максимум остаточного напряжения находился под поверхностью, но эта точка зрения не полностью разделяется и возможно, что этот эффект обуслов-
Рис. 98. Кривые для различных обдутых дробью листовых рессор в зависимости от степени наклепа [322]:
а — кривые усталости при изгибе в одной плоскости; б — рас пределение остаточных напряжений по толщине рессоры (х — расстояние от поверхности)
ливается также результатом полирования. Термообработка при температуре выше 250° С может снять остаточные напряжения и снизить сопротивление усталости.
Дробеструйную обработку можно также применять для улуч шения предела усталости деталей из цветных металлов и спла вов. Фаунд [343] исследовал влияние обдувки дробью на сопро тивление усталости литого магниевого сплава; он показал, что обычная обработка повреждала поверхность, но при свободном падении дроби с высоты 7,3 и 14,6 м предел усталости значитель но повышался. Влияние обдувки дробью также было исследова но для титановых [344] и алюминиевых сплавов [337].
Поверхностная обкатка. Обкатка поверхности металла может значительно улучшить его сопротивление усталости. Этот про цесс может быть более эффективным, чем обдувка дробью, пото му что при надлежащем давлении возможно достичь большей степени упрочнения и более высоких остаточных напряжений сжатия у поверхности. При поверхностной обкатке материал
166
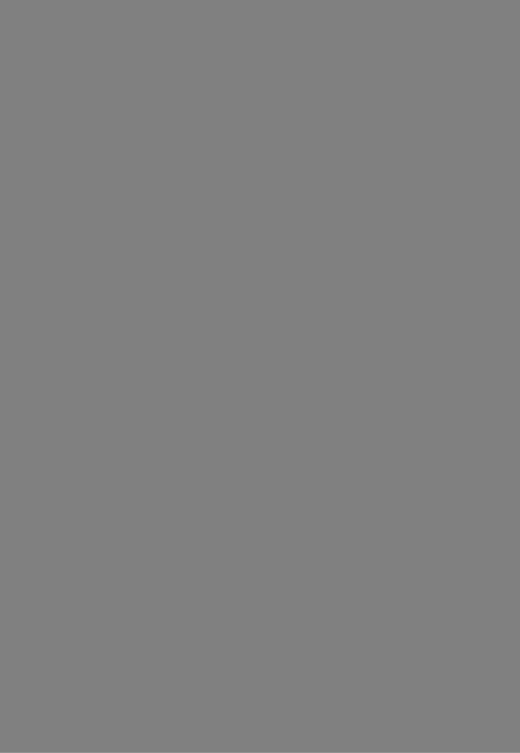
использован для улучшения сопротивления усталости воздушных винтов из магниевого сплава [347].
Предварительное деформирование. Благоприятное влияние растягивающего статического деформирования на предел уста лости стержня с надрезом было впервые показано Форрестом [321]. Он предварительно нагрузил образцы с надрезом из алюми ниевого сплава BS6L1 напряжением, составляющем 3/4 их проч ности на растяжение, и это удвоило предел усталости при 108 цик лах. Подобные эксперименты уже описывались Розенталем и Сайнисом [318] и Дагдейлем [319], показавшими, что повышение предела усталости зависит в первую очередь от остаточного на пряжения, так как большой эффект получался при высоких средних напряжениях и для материалов с высоким отношением От/сгвр. Предварительная деформация деталей и конструкций почти не используется в практике (исключая заневоливание пру жин), однако эта обработка является простым способом повы шения сопротивления усталости. Например, было показано, что предварительное нагружение собранного крыла самолета может заметно повысить его долговечность. Как и при поверхностной обкатке, оптимальную предварительную нагрузку для данной детали можно определить только экспериментально. Ограничен ные опубликованные данные показывают, что предварительное напряжение может составлять свыше 90% от предела прочности на растяжение, т. е. может быть значительно выше предела те кучести в областях концентраций напряжений [348]. Однако сле дует помнить, что остаточные сжимающие напряжения всегда уравновешиваются остаточными растягивающими напряжения ми в других местах, и следует соблюдать осторожность, чтобы
они не снизили предел усталости. |
из-за |
возникно |
|
П р а в к а . Холодная правка обычно вредна |
|||
вения |
растягивающих остаточных напряжений, |
которые наво |
|
дятся |
в областях, где материал перенапрягается |
при |
сжатии. |
Лав [120] приводит данные о снижении предела усталости при холодной правке на 20—50%, однако он также указывает, что предел усталости не снижается, если для операции правки ис пользуется наклеп молотком.
Упрочнение пламенной и индукционной закалкой. Для сталей пламенная или индукционная закалка часто используется для обеспечения сопротивления поверхностному износу. Остаточные напряжения растяжения на поверхности, наведенные при нагре ве, снимаются при увеличении объема детали, связанном с фазо выми превращениями [349]. Результирующее остаточное сжимаю щее напряжение на поверхности вместе с упрочнением поверх ностного слоя может значительно увеличить предел усталости, особенно для деталей, имеющих концентрацию напряжений (табл. 38). При закалке необходимо обеспечить, чтобы усталост ные разрушения не происходили на границе закаленных облас-
|
|
|
|
|
|
|
Изменение |
|
|
|
|
Условия |
|
предела |
|
|
|||
Сталь |
|
|
усталости |
|
|
||||
|
испытания |
|
вследствие |
|
|
||||
|
|
|
пламенной |
|
о |
||||
|
|
|
|
|
|
|
закалки |
|
|
|
|
|
|
|
|
|
в % |
*2 3 о >»■ |
(- |
|
|
|
|
|
|
|
CJ |
||
|
|
|
|
|
|
|
|
S к и п |
Гх |
|
|
|
|
|
Без надреза |
|
|
|
|
Углеродистая |
Изгиб с вращением |
40.0 |
+60 до +88 |
— |
[120] |
||||
|
Кручение |
|
|
22.0 |
+ 18 |
|
|||
|
|
|
|
|
|||||
Еп12 |
Изгиб |
с вращением |
33.0 |
— |
+ 19 |
| [350] |
|||
(0,35-0,45о/о С) |
То |
же |
|
|
|
40,8 |
+54 |
||
Еп16 (Мп, Мо) |
» |
» |
|
|
|
47.1 |
|
+40 |
|
Еп24 (1,5% Ni, Сг, |
|
|
|
|
|
|
|
|
|
Мо) |
|
|
|
|
|
|
|
|
|
|
|
|
|
|
С надрезеIMU |
|
|
|
|
SAE 1045 |
Изгиб с вращением |
|
+80 |
|
|
||||
(0,45о/о С) |
|
|
|
|
|
|
(обработан |
|
[120] |
|
Образец |
0 |
12,7 мм |
12,55 |
только бурт) |
|
|||
|
+ 190 |
|
|
||||||
|
с |
острым |
буртом |
|
(обработана |
|
|
||
|
|
|
|
|
|
|
вся деталь) |
• |
|
Никелемолибдено |
Изгиб |
с вращением |
24,5 |
+40 |
— |
[120] |
|||
вая |
Образец |
с |
умерен |
|
|
|
|
||
(2,5% Ni; 0,5% Мо) |
ным буртом |
|
|
|
|
||||
Хромоникелемолиб- |
Кручение |
60 мм |
16 |
+ 6 |
|
|
|||
деновая |
Образец |
0 |
|
[1201 |
|||||
|
Образец 0 |
60 мм с |
20,9 |
—19 |
— |
||||
|
|
||||||||
|
поперечным отвер |
|
|
|
|
||||
|
стием |
|
|
|
|
|
|
||
|
Оси с напрессованными колесами |
|
|
||||||
SAE 1045 |
Изгиб |
с вращением |
9,1 |
> + 2 4 6 |
— |
[120] |
|||
(0,45о/о с) |
Образец |
0 |
50,8 мм |
||||||
Углеродистая |
Образец 0 |
177,8 мм |
8,6 |
> + 8 3 |
— |
[120] |
|||
(0,52о/о С) |
Образец |
0 |
241,3лш |
7,7 |
+46 до +64 |
— |
|
тей, где вероятны очень высокие остаточные растягивающие на пряжения. Этим можно объяснить низкие' пределы усталости, иногда наблюдаемые для поверхностно закаленных деталей.
Повышение твердости поверхности стали путем цементации, азотирования и цианирования. Повышение твердости поверхнос ти используется главным образом для повышения сопротивления
169
износу поверхностей стальных деталей, а также для повышения сопротивления усталости, особенно при коррозии и коррозии тре ния. При цементации упрочнение получается в результате насы щения поверхности металла углеродом и последующей закалки. При азотировании металл нагревается в атмосфере аммиака и упрочнение достигается поглощением азота без закалки. При на греве в расплавленном цианиде как углерод, так и азот погло щаются, после чего для получения твердой поверхности обычно следует закалка [351].
Предел усталости повышается при любом из этих процессов как вследствие высокого предела усталости поверхностного твер дого слоя, так и вследствие сжимающего остаточного напряже ния, возникающего в этом слое при термохимических обработках. Комбинированного влияния этих факторов обычно достаточно, чтобы сопротивление усталости поверхностного слоя стало боль ше, чем сердцевины. Усталостные разрушения в деталях, под вергнутых термохимической обработке, начинаются в области, граничащей между слоем и сердцевиной. В этих условиях повы шение предела усталости, создаваемое поверхностной обработ кой, зависит от напряженного состояния и глубины слоя по от ношению к размеру детали. При осевом нагружении и при отсутствии концентрации напряжений, напряжение под поверх ностью приблизительно такое же, как на поверхности, и, следо вательно, упрочняющий слой меньше влияет на сопротивление усталости. IJpn изгибе или кручении небольших образцов наблю дается заметное повышение пределов усталости, но наиболее сильно повышается предел усталости образцов с надрезом, по тому что на прочность сердцевины концентрация напряжения у поверхности не влияет. (Это, конечно, не относится к тому слу чаю, когда концентрация напряжения, распространяющаяся глубже упрочненного поверхностного слоя, образуется после соз дания слоя.)
Некоторые типичные данные, показывающие влияние цемен тации и азотирования, представлены в табл. 39 и 40. По влия нию цианирования также есть некоторые данные в литературе: Ли [352] получил увеличение предела усталости до 97% для мяг кой стали; по данным Хенкинса предел усталости различных ста лей увеличивается на 5—74% при условии предварительного обезуглероживания [326, 333].
Обработка поверхностного слоя для каждого конкретного случая выбирается в зависимости от марки стали, глубины слоя, величины допускаемого коробления и температуры, при которой работает деталь. При цементации получается более толстый •слой, чем при азотировании; глубина науглероженного слоя со ставляет обычно 0,76—2,5 мм, а азотирование, например, при 485° С в течение 72 ч дает слой глубиной от 0,30—0,51 мм [351]. Есть данные, которые показывают, что предел усталости возрас-
170
Сталь
Временное соп ротивление на разрыв в кГ/мм*
|
|
Предел |
Изменение пре |
||
|
|
усталости |
дела |
усталости |
|
|
|
необработан |
образцов вслед |
||
Вид |
Детали |
ного образца |
ствие обработки |
||
в кг/мм* |
|
в % |
|||
нагру- |
образца |
|
|
|
|
женин |
|
глад |
с над |
глад |
с надре |
|
|
||||
|
|
кий |
резом |
кий |
зом |
Углеродистая |
|
47.1 |
|
|
|
25,9 |
22,0 |
+88 |
+82 |
||
(О,16о/0 |
с) |
|
|
94.2 |
|
|
|
|
|
|
|
Хромистая (1,0% Сг) |
|
|
|
40,8 |
19,9 |
+ 105 |
+95 |
||||
Хромомарганцевая |
|
|
Изгиб |
0 |
6,6 ММ, |
55.0 |
25.0 |
+75 |
+ 120 |
||
(1,4% Сг; |
1,0% Мп) |
|
|
|
|
|
|||||
Хромомарганцевомо |
105,0 с враще |
радиус |
44.0 |
20.0 |
+68 |
+ 120 |
|||||
либденовая (1,2% Сг; |
|
нием |
надреза |
|
|
|
|
||||
1,0% Мп; 0,25% Мо) |
|
|
0,5 м м |
|
|
|
|
||||
То же |
|
|
|
125,5 |
|
|
|
45,5 |
13,95 |
+72 |
+230 |
Никелехромомолибде |
|
|
|
59,7 |
16,0 |
+32 |
+219 |
||||
новая |
(2,0% |
Ni; |
|
|
|
|
|
|
|
|
|
2% Сг; 0,2% Мо) |
|
|
|
|
|
|
|
|
|||
2,0% Сг; |
2,0% |
Ni; |
125,5 |
Изгиб |
0 |
14 м м , |
61,2 |
49,5 |
+13* |
—38** |
|
0,25% |
Мо |
|
|
|
с враще |
с |
попе |
|
|
|
+2 9 *** |
|
|
|
|
|
нием |
речным |
|
|
|
|
|
|
|
|
|
|
Кручение |
отвер |
25 |
11,9 |
+ 2 6 * |
—17** |
|
|
|
|
|
|
|
|
стием |
|
|
|
+ 124*** |
Углеродистая сталь |
_ |
Изгиб |
0 |
7,95 м м |
32,7 |
__ |
+83 |
|
|||
Никелевая сталь |
|
97,5 |
с враще |
|
|
45,5 |
+85 |
|
|||
(3,5% |
N1) |
|
|
|
нием |
|
|
|
|
|
|
То же (5,0% Ni) |
|
113,0 |
|
|
|
53,5 |
— |
+62 |
— |
*Шлифовка после цементации.
**Отверстие просверлено после цементации. '** Отверстие просверлено перед цементацией.
тает с глубиной покрытия, но Фриш [196] относит это в основном за счет влияния размера небольшого образца — разрушение происходит между упрочненным слоем и сердцевиной, где напря жение заметно ниже максимального; если глубина покрытия со ставляет значительную часть радиуса образца. На больших дета лях от такого упрочнения был получен незначительный эффект, и по Фришу эффект различных обработок следует сравнивать по напряжению в месте разрушения. В соответствии с этим для хро момолибденовой стали Фриш установил, что тонкий азотирован
ный слой |
(1,0 мм, полученный за 10 ч при 485° С) |
дает |
почти |
такое же |
сопротивление усталости, как толстый |
слой |
(3,56— |
5,1 мм, полученный за 72 ч при 485° С), и для деталей была ре комендована первая обработка. При цементации наблюдается