
книги / Усталость металлов
..pdfОбразцы и их изготовление
Как форма, так и окончательная обработка образцов имеют большое влияние на сопротивление усталости и поэтому на кон струкцию и изготовление усталостных образцов необходимо об ращать больше внимания, чем при обычных механических ис
пытаниях. Чтобы |
исключить разрушение, происходящее |
в |
за- |
||||||
|
крепленных концах образца, |
го |
|||||||
146 |
ловки должны иметь большее се |
||||||||
чение, и важно сделать большой |
|||||||||
|
|||||||||
i _ r ^ |
переходный радиус между голов |
||||||||
|
кой |
и |
рабочим сечением, чтобы |
||||||
V |
снизить |
концентрацию |
напряже |
||||||
ния. Некоторые типичные образцы |
|||||||||
|
|||||||||
|
показаны |
на |
рис. 20. |
Веллеров- |
|||||
|
ский |
образец (рис. 20, а) |
может |
||||||
|
быть использован при одноили |
||||||||
|
двухточечном нагружении. Обра |
||||||||
|
зец для |
машины Хея |
с |
осевым |
|||||
|
нагружением |
(рис. 20,6) |
исполь |
||||||
|
зуется |
в |
диапазоне |
диаметров |
|||||
|
опасного сечения от 3,8 до 5 мм. |
||||||||
|
Длина части образца постоянного |
||||||||
|
сечения |
|
не |
превышает 6,35 |
мм |
||||
|
для |
предотвращения разрушения |
|||||||
|
или выпучивания при нагружении |
||||||||
|
сжимающими силами. |
|
|
|
Рис. 20. Типичные о бр азц ы д л я ус тал остн ы х испытаний:
а — образец для усталостной маши ны с консольно вращающимся образ цом; б — образец для усталостной ма
шины с осевым нагружением; в — ли стовой образец для усталостной маши
ны на растяжение-сжатие
Из опыта работы установлено, что при осевом нагружении дли на части образца постоянного се чения не должна быть более 1,5 минимальных диаметров.
Листовой образец (рис. 20, в) используется для испытаний при пульсирующем растягивающем нагружении.
Установлено, что ширина за жимаемых частей плоских образцов должна быть в 3 раза боль ше ширины испытуемого сечения, чтобы не произошло разруше ния в головках образца.
Следует отметить большие переходные радиусы на всех трех образцах.
Чтобы определить влияние концентрации напряжения на пре дел усталости, испытания можно проводить на надрезанных об разцах. Однако форма и величина надрезов не стандартизова ны и, по-видимому, каждый исследователь применяет образцы
42
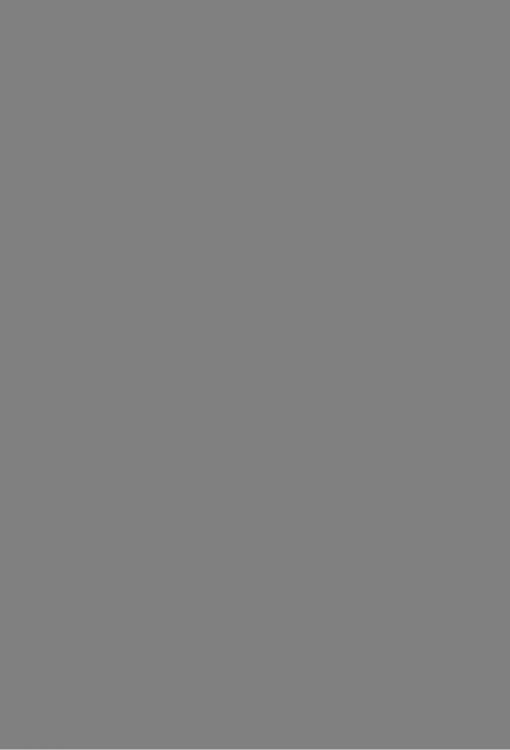
Тарировка машин
Согласованные стандарты точности или методы тарировки для усталостных иопытательных машин отсутствуют, и в этом отношении методы испытаний на усталость отстают по сравне нию с методами статических испытаний. Это положение неудов летворительно особенно потому, что динамические измерения напряжения более сложны, чем статические.
Наиболее трудной задачей является тарировка машин для осевого нагружения.
Определение напряжения по измерению действующей силы обычно является неточным, так как на нее могут влиять явление резонанса и инерция движущихся частей. Наиболее часто при меняется метод тарировки с помощью динамометра. Можно ис пользовать другие методы, например измерение усилий на опо рах кривошипа механического привода машины или электричес кого напряжения в электромагнитной машине. Динамометр дол жен быть спроектирован так, чтобы его деформации были уп ругими при действии максимальных нагрузок. Он может пред ставлять собой сплошной или трубчатый стержень, либо иметь форму кольца; к стержню присоединяется измеритель переме щения, обеспечивающий измерение при работе машины. Воз можно, что большую точность обеспечивает применение датчи ков сопротивления {74}, [75]. Используется обычно мостовая схе ма, когда в одном из плечей моста размещаются датчики сопротивления, в другом — декадное сопротивление; два одина ковых постоянных сопротивления составляют остальные два плеча. Применяя катодно-лучевой осциллограф, можно получить форму цикла динамической деформации во время испытания. Разница отсчетов по декадным сопротивлениям при сбаланси рованном мосте пропорциональна изменению сопротивления проволочных датчиков. Динамическую нагрузку можно вычис лить, используя результаты предварительной статической тари ровки.
Метод динамической калибровки, применяемый в Нацио нальной технической лаборатории, основывается на ранее опи санном методе Биллинга [76].
Преимущество использования датчиков состоит в том, что сигнал тензодатчика не зависит от частоты и можно достичь точности измерения ±1% максимальной амплитуды нагрузки. Недостатком этого метода является необходимость применения специальной аппаратуры, включающей стабилизатор питания и усилитель высокого качества. По этой причине предпочитают механическую или механико-оптическую калибровку с помощью динамометра. Точность в 1 % может быть достигнута для коль цевого динамометра, приспособленного для динамической тари ровки [77].
44
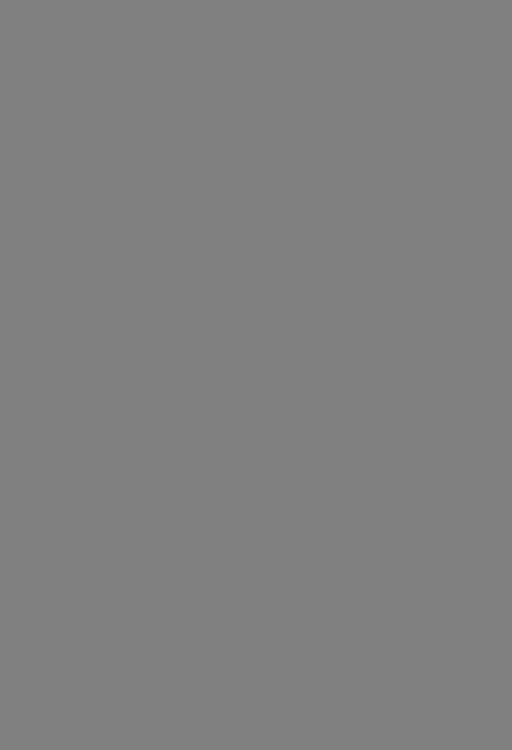
Поэтому рассмотрение рассеяния результатов испытаний ак туально в том случае, когда расчет ведется на ограниченную долговечность и напряжения превышают предел усталости.
Этот метод расчета применяется для самолетных конструк ций и в определенной степени для деталей двигателя; было до казано, что применение статистической техники при этих обстоя
тельствах полезно.
Имеется ряд статей, описывающих, как должна применяться статистика для интерпретации результатов испытаний [80, 81,
674, 675].
Главная цель испытания на усталость заключается в том, чтобы получить данные, которые можно использовать для рас чета на прочность в условиях эксплуатации. Наиболее простыми являются испытания на лабораторных образцах, но по данным таких испытаний не всегда можно оценить поведение детали в рабочих условиях, в связи с чем необходимо проведение испы таний на деталях или конструкциях. Однако испытания конструк ций являются дорогостоящими, так что объем этих испытаний обычно несколько ограничен. Вопрос заключается в том, чтобы оценить поведение большого числа деталей в рабочих условиях по небольшим выборкам результатов испытаний. Применение статистических методов обработки результатов испытаний дает такие возможности. Дальнейшее применение статистики в уста лостных испытаниях заключается в том, чтобы определить с не которой заданной степенью достоверности, значительно ли отли чаются результаты испытаний двух серий. Этот вопрос может воз никнуть, когда оценивается влияние горячей обработки или про цесса изготовления на усталостную долговечность.
Причины разброса. Некоторый разброс результатов устало стных испытаний должен возникать из-за различия условий их проведения, поэтому метод испытания следует тщательно кон тролировать, когда делаются статистические исследования. Это особенно важно, потому что трудно установить, от каких причин возник разброс: от различия в условиях проведения испытаний или от металлургических факторов. Воспроизводимые условия наиболее легко получаются при испытаниях на изгиб с вращени ем и этот метод испытания часто применяется для статистических экспериментов. Был сделан ряд попыток для определения раз броса из-за экспериментальных ошибок в этом виде испытания. Рейсом и Мел [82] установили, что разброс, вызванный отклоне ниями в действующем изгибающем моменте и в измерении диа метра образца, был мал по сравнению с разбросом, который они наблюдали для легированной стали SAE 4340; кроме того,
не было найдено соответствия между долговечностью и эксцен трицитетом образца в захвате.
При исследовании стали с 0,24% С Клейтон и др. [83] наш ли, что на разброс заметно влияли различия в изготовлении об-
46
разцов. При высоком качестве изготовления образцов, рассея ние результатов было более значительным, если испытания про водились на 12 машинах, по сравнению с испытаниями на од ной машине.
Более прямой метод определения различия между влиянием ошибки эксперимента и металлургических факторов был исполь зован Мак-Клинтоком (84, 85], который рассматривал разброс долговечности в связи с расположением мест разрушения на об разцах. Напряжения в образцах не меняются вдоль их длины, так что различие в положении мест разрушения может быть от несено за счет различий в свойствах материала.
Мак-Клинток нашел также, что рассеяние долговечности бы ло больше, чем это могло быть объяснено различием в свойствах материала, поэтому необходимо улучшить качество изготовле ния образцов.
Из результатов этих экспериментов видно, что рассеяние в величинах сопротивления усталости не является следствием только различия в способе испытания, но также связано с неод нородностью металла, хотя влияние на рассеяние того или ино го металлургического фактора не установлено. Для сталей мож но ожидать, что на рассеяние в основном влияет содержание включений, но данные до некоторой степени противоречивы.
Разброс может также возникать из-за отклонений в размере зерна, составе сплава или условий горячей обработки. Инесон и др. [86], например, нашли отклонение в 5% в пределе устало сти между верхней частью и основанием стального слитка с вре менным сопротивлением 94—101 кГ/мм2, что они отнесли к мест ным отклонениям в составе и горячей обработке.
Другой источник разброса, который может быть более важ ным на практике, состоит в том, что разброс от партии к партии может быть больше, чем от одного образца к другому в одной партии. Отклонения в процессе производства приводят к тому, что предел усталости сплава данной марки может изменяться очень широко. Г. Форрест [87], например, приводит следующие величины разброса пределов усталости при изгибе с вращением, полученные при испытаниях нормально изготовленного штам пованного алюминиевого сплава. Для преобладающих сечений диаметром до 50 мм для сплава НЕ15 WP (DTD364) предел усталости при 108 циклах изменялся от 14 до 18,8 кГ/мм2, а для сплавов ДТД683 и 363 — от ±15 до ±20,4 кГ/мм2. Опублико ванных сравнимых данных для сталей или железных сплавов нет, но подобные отклонения имеют место и для этих мате риалов.
Анализ данных испытаний на усталость. Данные, которые должны анализироваться для статистической обработки, обыч но состоят из долговечностей для выборки образцов, испытанных при постоянной амплитуде напряжения. Распределение долго
вечностей может быть представлено графически с помощью ги стограммы. Эта диаграмма, показывающая повторяемость значе ний, располагающихся внутри последовательных интервалов дол говечности, представлена на рис. 22 для 57 результатов [79]. При большом количестве образцов гистограмма может быть замене на кривой плотности распределения. Для статистического анали за должна быть выбрана форма этой кривой, надежность анали за будет зависеть от точности, с которой выбранная кривая соот ветствует действительному распределению.
Установлено, что частотное распределение усталостных дол' говечностей N обычно не соответствует нормальному распреде-
Рис. 22. |
Г и стогр ам м а, п о к азы в аю щ ая |
распределен ие |
|
усталостн ой долговечности 57 |
о б р азц о в |
и з алю м и н и ево |
|
го с п л ава |
75S -T 6, и спы танн ы х |
при 21 к Г /м м 2 (п — число |
|
|
р азр уш ен н ы х |
о б р азц о в) |
|
лению, но может быть получено довольно точное приближение, если данные N представлены в логарифмических координатах. Такое представление известно как логарифмически нормальное распределение, и в большинстве статистических анализов данных испытаний на усталость выполнялось на этой основе.
Нормальное распределение определяется уравнением
|
* |
s / 2 n |
М |
2s2 |
(6 ) |
|
J |
||||
где |
*« |
|
частота |
нахождения значений |
|
J ydx— относительная |
|||||
|
*1 |
|
|
|
|
|
между Х\ и xz\ |
|
|
|
s — стандартное отклонение;
Хр — арифметическое среднее всех значений. Зависимость между у и х симметрична относительно средне
го значения Хр и асимптотически приближается к оси абсцисс. Распределение _полностью определяется арифметическим
средним значением Хр и стандартным отклонением s, так что если эти значения известны для генеральной совокупности, то
48
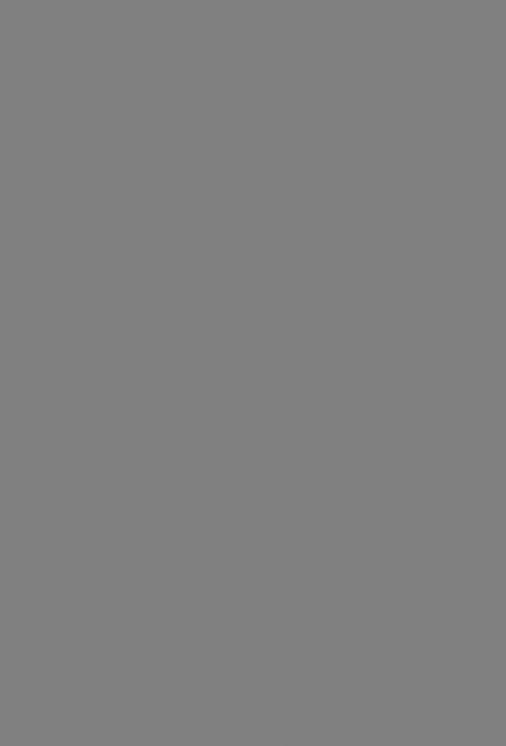
Т а б л и ц а 4
О б р а з е ц |
1 |
420000 |
2 |
3 |
4 |
5 |
6 |
Долговечность N |
. |
579000 |
640000 |
800000 |
900000 |
1200000 |
|
lg |
N |
5,623 |
5,763 |
5,806 |
5,903 |
5,954 |
6,079 |
Результаты приближаются к нормальному логарифмическому распределению. Среднее значение \g N = 5,855 и стандартное отклонение s = 0,159 [81]; «безопасная долговеч ность» в тыс. циклов.
|
7 = |
0,50 |
|
|
|
|
|
|
7 = |
0,95 |
|
|
|
|
|
|
Р в % |
|
|
|
|
|
|
90 |
95 |
99 |
99,9 |
90 |
95 |
99 |
99,9 |
90 |
95 |
99 |
99,9 |
436 |
378 |
288 |
211 |
288 |
231 |
152 |
9 3 ,7 |
238 |
184 |
112 |
6 3 ,7 |
логарифмическому нормальному распределению. Значения х и 5 вычисляются из уравнений (7) и (8) и безопасная долговечность
дается выражением (х — ks), где соответствующее значение k бе рется из табл. 3.
Табл. 4 иллюстрирует зависимость гарантированной долговеч ности от процента выживания р и степени требуемой достовер ности у. Для практического применения, особенно в авиации, для ряда деталей гарантированная долговечность должна осно вываться на процентах выживания, больших 90, следовательно, должна приниматься более низкая гарантированная долговеч ность, что подтверждается табл. 4. На основе шести результатов гарантированная долговечность с 95% достоверности для 90% выживания (или 10% разрушений) составляет 238 000; если при нимается только 1% разрушений, гарантированная долговечность снижается до 112 000, а для одного разрушения на 1000 — до 63 700, что составляет меньше 7ю средней долговечности всей вы борки. Значение гарантированной долговечности может несколь ко увеличиться при увеличении размера выборки, но это неэко номично для натурных деталей, и число испытаний в одних и тех же условиях обычно составляет 5—10. Одной из главных трудно стей оценки гарантированной долговечности для низкой вероят ности разрушения является надежность применения определен ного распределения. Чтобы определить долговечность, соответ ствующую одному разрушению из 1000, потребуется по меньшей мере 1000 испытаний, которые обычно неосуществимы.
Удобно представлять экспериментальные результаты нане сением вероятности разрушения в зависимости от lg N на лога рифмической вероятностной бумаге, для этой зависимости дан-
50
ные располагаются так, что логарифмически нормальное рас пределение представляется прямой линией. Результаты Синкле ра и Долана для плоских образцов из алюминиевого сплава 75S в логарифмических координатах показаны на рис. 23. Линии, проходящие через экспериментальные точки, представляют ло гарифмические нормальные кривые, имеющие среднее значение и стандартные отклонения, как вычисленные непосредственно из соответствующих экспериментальных данных. С первого взгляда кажется, что экспериментальные результаты довольно близки к логарифмическому нормальному распределению, но если ли-
Рис. 23. Д и а гр ам м а |
логариф м и чески -норм ального |
распределен ия д ол говеч |
|||
ности |
д л я |
о б р азц о в |
при |
разли чн ы х н ап ряж ен и ях |
[79]. р — отн оси тельн ая ч ас |
|
|
|
|
т о та разруш ен и й : |
|
1 — |
43,7 |
кГ/мм2\ 2 — 35 |
кГ/мм2; 3 — 31,5 кГ/мм2\ 4 — 28 кГ/мм2\ 5 — 24 5 кГ/мм2' |
||
|
|
|
|
6 — 21,0 кГ/мм2 |
|
нии эстраполируются |
к вероятности разрушения в 0,001 %, то вид |
||
но, что разрушение |
более вероятно при ±28 |
кГ/мм2, чем при |
|
±31 кГ/мм2 или ±35 |
кГ/мм2. Этот вопрос хорошо |
объясняется |
|
Коксом [89] применительно к результатам |
при |
±21 кГ/мм2 |
(рис. 23). Он показал, что эти результаты могут соответствовать кривой, представляющей равновероятность разрушения за каж дый цикл, так же как прямая линия представляет логарифмиче ское нормальное распределение. [Следует отметить, что наиболее низкая долговечность (около 433 000 циклов) располагается да леко от этой линии, что, по-видимому, относится к сериям ре зультатов при более высоком напряжении.] Однако эти серии результатов не являются типичными, в целом опыт показал, что экспериментальные зависимости, полученные на логарифмиче ской вероятностной диаграмме (рис. 23), обычно отклоняются постепенно от прямых линий, изгибаясь выпуклостью вверх при низких вероятностях разрушения.
Поэтому были сделаны попытки получить лучшее соответст вие кривых распределения с экспериментальными данными.
4 * |
51 |