
книги / Химия и технология полимерных материалов. Полимеры
.pdf8. СПОСОБЫ ПРОВЕДЕНИЯ ПОЛИМЕРНЫХ ПРОЦЕССОВ
До сих пор мы рассматривали химические аспекты полимеризации: классы мономеров, типы инициаторов и катализаторов, механизмы реакций и т.д. Для практического осуществления полимеризационных процессов не меньшее значение имеют и физические аспекты: агрегатное состояние мономера (газ или пар, жидкость, твердое вещество или раствор), необходимость применения растворителя или осадителя, непрерывный процесс или периодический, наконец, возможность проведения процесса
впромышленных условиях.
Взависимости от этих факторов используют различные способы полимеризации.
8.1.Цепная полимеризация
8.1.1.Полимеризация в массе (блочная полимеризация)
Вэтом способе используют только жидкие мономеры. Инициатор или катализатор, агент передачи цепи, если он нужен,
и другие обслуживающие процесс компоненты растворяют в жидком мономере. Таким образом, в этом способе вся система перед началом полимеризации представляет собой гомогенный раствор. Его нагревают или облучают подходящим источником для инициирования полимеризации и одновременно энергично перемешивают для облегчения тепло- и массообмена.
Недостатки способа. В процессе полимеризации быстро растет вязкость системы, что затрудняет перемешивание и приводит к образованию полимерных цепей с очень разной молекулярной массой. Как говорят, получается продукт с очень широким молекулярно-массовым распределением.
Возрастание вязкости системы уменьшает подвижность цепей. Падает вероятность столкновения макрорадикалов и обрыва цепей. В то же время из-за распада все новых молекул инициатора растет число активных центров и, следовательно, возрастает скорость про-
81
цесса (так называемый эффект автоускорения или гель-эффект). В результате постоянно возрастает количество тепла, выделяемого системой в единицу времени (цепная полимеризация – процесс экзотермичный). Выделяющееся тепло может привести к частичному разложениюполимераили даже ктепловому взрыву реактора.
Преимущества способа. Легко организовать производство: для проведения процесса нужен жидкий мономер, инициатор, нагреватель или источникУФ-излученияиподходящая емкость(реактор).
Полимер получается очень чистым: при протекании процесса до конца мономер и инициатор расходуются полностью, а кроме полимера, никаких других веществ не образуется.
Возможно получение сразу готовых изделий без их дополнительной обработки. В плоскодонном реакторе полимер получается в виде готового листа необходимого размера и толщины, а если раствор инициатора или катализатора в полимере залить в реактор определенной формы, то по окончании процесса полимеризации из реактора извлекаются готовые изделия достаточно сложной конфигурации(крышки, поддоны, коробки, детали конструкций ит.д.).
Блочную полимеризацию используют в процессе радикальной полимеризации метилметакрилата для получения прозрачных блоков и листов из оргстекла, готовых изделий несложной формы, а также гранул, которые перерабатывают плавлением. Этим же способом получают многие электроизоляционные материалы, например полистирол.
8.1.2.Полимеризация в растворе
Вэтом способе мономер и необходимые добавки (инициаторы, катализаторы, агенты передачи цепи) растворяют в инертном растворителе. Нерастворимые катализаторы суспендируют в растворе. Раствор нагревают или облучают для инициирования полимеризации и одновременно перемешивают.
Недостатки способа. Основной недостаток состоит в том, что, какой бы ни был выбран инертный растворитель, всегда существует вероятность передачи цепи на растворитель. Поэтому получить высокомолекулярныйпродуктэтимспособом довольнотрудно.
82
Полимер необходимо отделять от растворителя либо добавлением осадителя, либо испарением растворителя. В любом случае требуется дальнейшая весьма сложная процедура очистки полимера от осадителя и следов растворителя. Поэтому полимер редко бывает чистым.
Применение огнеопасных и токсичных растворителей требует принятия дополнительных мер пожарной безопасности и промышленной санитарии.
Преимущества способа. Если полимер будет использоваться в виде раствора в органическом растворителе, этот способ предпочтительнее всех других, поскольку позволяет сразу получить товарный продукт. Так получают лаки, клеи, адгезивы. Используют его и в том случае, когда полимер нерастворим в собственном мономере и выпадает в осадок в ходе блочной полимеризации.
Наличие растворителя препятствует быстрому нарастанию вязкости системы, поэтому обеспечение необходимого тепломассообмена не представляет проблемы.
В промышленности этот способ используют для радикальной полимеризации акрилонитрила и катионной полимеризации изобутилена. Полимеризацией в растворе обычно получают также блок-сополимеры.
8.1.3. Суспензионная полимеризация
Этим способом можно полимеризовать только водонерастворимые мономеры.
Мономер диспергируют в воде в виде мелких капелек, которые стабилизируют защитными коллоидами, поверхностно-активными веществами (ПАВ) и энергичным перемешиванием. Размер образующихся капелек можно регулировать соотношением мономера и воды, количеством и типом стабилизаторов и скоростью перемешивания. Для инициирования полимеризации используют растворимые в мономере инициаторы. Поскольку каждая капелька ведет себя независимо от других, ее можно рассматривать как микроблочныйреактор. Этодаетцелыйряд преимуществ.
Преимущества способа. Непрерывная водная фаза является отличным аккумулятором и переносчиком тепла, поэтому экзо-
83
термичность процесса не представляет проблем. К тому же вода намного экономичнее и безопаснее, чем любой органический растворитель при полимеризации в растворе.
Поскольку вся масса мономера разделена на микроблоки (капли), легко контролировать длину цепей и можно получить высокомолекулярный продукт с узким молекулярно-массовым распределением.
Полимеризация протекает почти всегда на 100 %, т.е. мономер расходуется полностью и не загрязняет полимер, который образуется с высоким выходом.
Полимер получается в виде гранул. Его легко отделить от воды фильтрованием, а остатки ПАВ и защитных коллоидов смываются с поверхности гранул чистой водой. Промытые и высушенные полимерные гранулы перерабатывают в изделия экструзией, литьем под давлением или растворяютдля получения лаковиклеев.
К недостаткам способа следует отнести большой объем сточных вод, требующих очистки, и низкую устойчивость полимерной суспензии с дальнейшим налипанием полимера на мешалку и стенки реактора. Поэтому в промышленности данный способ проводят по периодической схеме.
Суспензионную радикальную полимеризацию используют для получения гранул полистирола, которые перерабатываются в пенополистирол (пенопласт). Этим же способом получают поли- стирол-дивинилбензольные гранулы для изготовления ионообменных смол и гранулы поливинилацетата для переработки в поливиниловый спирт.
8.1.4. Эмульсионная полимеризация
Мономер, как и в предыдущем способе, диспергируют в воде, но не до отдельных капель, а до однородной эмульсии. Эмульсию стабилизируют эмульгаторами: ПАВ, защитными коллоидами, буферными растворами.
Поскольку ПАВ берутся в количествах, превышающих критическую концентрацию мицеллообразования, они находятся в системе в мицеллярной форме. Добавляемый в систему мономер
84
солюбилизируется в ядрах мицелл. Если мономер частично растворим в воде, то водный раствор эмульгатора содержит некоторое количество молекул мономера. Можно также допустить, что очень небольшая часть мономера находится в системе в виде мелких капелек, как при суспензионной полимеризации. Таким образом, эмульсия является сложной комплексной системой, в которой водный молекулярный раствор эмульгатора является дисперсионной средой, а дисперсную фазу образуют мицеллы ПАВ с солюбилизированным мономером и мелкие мономерные капли.
Как правило, в эмульсионной полимеризации используют водорастворимые инициаторы типа персульфатов или гидропероксидов. Поскольку инициатор водорастворим, а мономер нерастворим или очень мало растворим в воде, трудно представить, что молекулы инициатора попадут в капли мономера. Кроме того, количество мономерных капель в системе в сотни миллионов раз меньше, чем количество мицелл. Следовательно, полимеризация внутри этих капель маловероятна.
Напротив, полярная поверхность мицелл хорошо адсорбирует молекулы инициатора. Полимеризация легко инициируется на поверхности мицелл и распространяется далее в глубь ядер мицелл. По мере расходования мономера в мицеллу диффундируют новые мономерные молекулы из водного раствора и из отдельных мономерных капель до полного их исчерпания. Полимерная молекула продолжает свой рост, пока в мицеллу не попадет другой радикал и не оборвет цепь. Такое бывает нечасто, поэтому полимеризация идет обычно до полного исчерпания мономера. При этом получаются макромолекулы с очень большой молекулярной массой. Эти молекулы объединяются в более крупные агрегаты, на поверхности которых адсорбируются молекулы ПАВ из мицелл и из раствора. Такие агрегаты адсорбируют и молекулы мономера, набухая в нем и увеличивая свои размеры и рыхлость клубка. Это только облегчает проникновение в клубок новых молекул мономера, и полимеризация идет все дальше и дальше.
85
В результате образуются мелкие частички полимера, стабилизированные слоем эмульгатора и равномерно распределенные в водной фазе. Эту молочно-белую коллоидную систему называют латексом. По окончании реакции латекс готов к употреблению. Его используют иливкачествеадгезива, иликакводоэмульсионнуюкраску.
Полимер можно выделить из латекса путем коагуляции. Коагуляцию проводят электролитами, высушиванием или вымораживанием.
Описанная схема полностью выполнима, только если инициатор абсолютно нерастворим в мономере, а мономер совершенно нерастворим в воде. В действительности механизм эмульсионной полимеризации сложнее и меняется от системы к системе. В зависимости от растворимости мономера, инициатора иэмульгатора, от их соотношения и концентрации в системе процесс полимеризации может протекать и в растворенном в воде мономере, и на границе раздела вода – мономерная капля, ивнутри мономерных капель. Конечный результат тем не менее во всех случаях будет одинаков – образуется латекс, т.е. мелкодисперсные частицы полимера, стабилизированные слоеммолекул ПАВнаихповерхности.
Эмульсионная полимеризация – самый распространенный
впромышленности способ. По этому способу полимеризуют винилхлорид, бутадиен, хлоропрен, акрилаты и метакрилаты.
Преимущества способа. Легко регулировать теплоперенос
всистеме. Полимеризация идет в мицелле, в маленькой частице
сбольшой удельной поверхностью. Поэтому очень высока скорость реакции в ядре мицеллы.
Число растущих цепей в мицелле ограничено, не увеличивается и не уменьшается во времени, а мономер извне поступает регулярно и в неограниченном количестве. Поэтому в каждой
мицелле получается мало макромолекул, но очень больших и одинаковых по размерам. Образующийся латекс является готовым товарным продуктом.
Серьезным недостатком эмульсионной полимеризации является образование больших количеств загрязненных сточных вод и необходимость удаления из полимера эмульгаторов и стабилизаторов, которые значительно ухудшают свойства продукта.
86
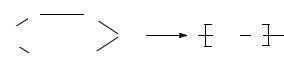
8.1.5. Твердофазная и газофазная полимеризация
Хотя основным видом полимеризации в промышленности являются жидкофазные процессы, иногда полимеризацию проводят в твердой или газовой фазе.
Если мономер представляет собой неплавкое и нерастворимое, термически нестойкое твердое вещество, он может быть заполимеризован только в твердой фазе. Примером твердофазной полимеризации может служить радиационное сшивание триоксана в полиформальдегид:
O |
CH2 |
|
|
|
|
|
|
|
|
|
|
n CH2 |
O |
hν |
CH2 |
O |
|
|
3 n |
OCH2
Врезультате полимеризации получается волокнообразный полимер с высокой механической прочностью и стойкостью к истиранию. В отличие от мономера, он устойчив при температуре до 80 оС и выдерживает кратковременный нагрев до 120 оС.
Твердофазная полимеризация представляет наибольшие трудности для роста цепи. Кроме того, чтобы исключить термическое разложение мономера (а иногда и полимера), реакцию обычно проводят при низких температурах, а следовательно, возможно только фотоили радиационное инициирование. Считалось, что скорость реакции в этих условиях крайне низкая.
Однако исследования последних лет показали, что в ряде случаев скорость реакции и качество получаемых полимеров при твердофазной полимеризации оказываются выше, чем при проведении процесса в жидкой фазе, например, радиационная полимеризация акрилонитрила, некоторых циклических мономеров и т.д. Особое значение имеет этот способ полимеризации для мономеров, являющихся твердыми веществами при комнатной температуре, например для акриламида. При фотополимеризации твердых диацетиленов получаются высококристалличные электропроводные полимеры:
87

R |
|
|
|
C |
|
|
|
|
|
C |
|
|
|
|
C |
|
|
|
|
|
C |
|
|
|
R |
|
|
|
|
|
|
|
|
|
|
|
|
|
|
|
|
|
|
R |
|
|
C |
|
C |
|
C |
|
|
|
|
|
|||||||
|
|
|
|
|
|
|
|
|
|
|
|
|
|
|
|
|
|
|
|
hν |
|
|
|
|
|
|
|
|
|
|
|
|
|
|
|
|
|
|
|
|
|
|
C |
|
R |
||||||||||||||||||
|
|
|
|
|
|
|
|
|
|
|
|
|
|
|
|
|
|
|
|
|
|
|
|
|
|
|
|
|
|
|
|
|
|
|
|
|
|
|
|
|
|
|
|||||||||||||||||||||
|
|
|
|
|
|
|
|
|
|
|
|
|
|
|
|
|
|
|
|
|
|
|
|
|
|
|
|
|
|
|
|
|
|
|
|
|
|
|
|
||||||||||||||||||||||||
R |
|
|
|
C |
|
|
|
|
C |
|
|
|
C |
|
|
|
|
C |
|
|
|
R |
|
|
|
|
|
|
R |
|
|
C |
|
|
C |
|
C |
|
|
|
|
|
|
|
|
|
|
|
|
|
|
|
|||||||||||
|
|
|
|
|
|
|
|
|
|
|
|
|
|
|
|
|
|
|
|
|
|
|
|
|
|
|
|
C |
|
|
R |
||||||||||||||||||||||||||||||||
|
|
|
|
|
|
|
|
|
|
|
|
|
|
|
|
|
|
|
|
|
|
|
|
|
|
|
|
|
|
|
|
||||||||||||||||||||||||||||||||
R |
|
C |
|
|
|
C |
|
C |
|
C |
|
R |
|
R |
|
C |
|
C |
|
C |
|
|
|
|
|
|
|
|
|
|
|
|
|
|
|
|
|
|
|
|
|
|
|||||||||||||||||||||
|
|
|
|
|
|
|
|
|
|
|
|
|
C |
|
|
R |
|
|
|
|
|
|
|
|
|
|
|
|
|
|
|
||||||||||||||||||||||||||||||||
|
|
|
|
|
|
|
|
|
|
|
|
|
|
|
|
|
|
|
|
|
|
|
|
|
|
|
|
|
|
|
|
|
|
|
|||||||||||||||||||||||||||||
... |
|
|
|
|
|
|
|
|
|
|
|
|
|
|
|
|
|
|
... |
|
|
|
|
|
|
|
|
|
|
|
|
|
|
|
|
|
|
|
|
|
|
|
|
|
|
|
|
|
|
|
Весьма перспективными представляются работы по получению методом твердофазной полимеризации полимеров с регулярной структурой.
Газофазную полимеризацию используют крайне редко из-за очень плохого отвода тепла. В настоящее время газофазной полимеризацией в промышленности в больших масштабах получают в основном полиэтилен. Газообразный этилен (температура кипения –103,8 оС) с трудом вступает в реакцию полимеризации из-за симметричного строения молекулы и отсутствия поляризации двойной связи. Поэтому полимеризация этилена проводится в довольно жестких условиях: температура порядка 200 оС и давление до 1500 атм (в некоторых случаях до 3000 атм) в присутствии инициаторов. Получаемый полимер называется полиэтиленом высокого давления (ПЭВД) или полиэтиленом низкой плотности (ПЭНП). Впервые этот процесс был осуществлен в 1936 г. Промышленное производство полиэтилена высокого давления началось в 1938 г. в Англии, несколько позже – в Германии, США и СССР. Технологический процесс производства полиэтилена методом высокого давления сложен тем, что требуется вести полимеризацию в аппаратуре, выдерживающей большие давления; возникает необходимость в неоднократной циркуляции этилена в реакционной системе из-за невысокой степени превращения и т.д. Однако до 1954 г. способ получения полиэтилена, основанный на применении таких высоких давлений, был единственным.
Положение изменилось после разработки технологии полимеризации этилена на катализаторах Циглера–Натта при гораздо более мягких условиях. В 1954 г. эта технология была в целом освоена и был получен патент. Несколько позже было начато промышленное производство. В настоящее время известно не-
88
сколько технологических схем полимеризации этилена на катализаторах Циглера–Натта при низком давлении. В качестве примера рассмотрим одну из них.
Хлорид титана и триэтилалюминий смешивают в среде пентана и распыляют смесь в колонне с насадкой. Пентан испаряется, а катализатор оседает на внутренней поверхности колонны
ина насадке в виде тонкой пудры.
Вколонну при температуре от комнатной до 70–80 оС под небольшим давлением (от атмосферного до 4–5 атм) подают газообразный этилен. Соприкасаясь с катализатором, этилен полимеризуется. Образующийся полимер собирают со дна колонны в виде легкого пушистого порошка.
Получаемый таким путем полиэтилен низкого давления (ПЭНД) является стереорегулярным кристаллическим полимером с молекулярной массой от 100 тысяч до миллиона. По эксплуатационным характеристикам он превосходит полиэтилен высокого давления (ПЭВД), но является более дорогим и несколько быстрее стареет.
Главным недостатком процесса является его огнеопасность и необходимость очистки полимера от твердого катализатора.
8.2.Способы проведения процессов поликонденсации
8.2.1. Поликонденсация в расплаве
Этот способ применяют, когда один из мономеров представляет собой твердое вещество и не разлагается при плавлении. Второй мономер (в случае гетерополиконденсации) растворяют в расплаве первого.
Температуры, при которых проводят поликонденсацию в расплаве, достаточно высоки, поэтому процесс проводят в инертной атмосфере азота или углекислого газа, чтобы предотвратить деструкцию получаемого полимера.
Часто реакцию проводят при пониженном давлении, что облегчает удаление выделяющегося низкомолекулярного продукта. Но даже в таких условиях на окончательном этапе реакции вяз-
89
кость системы сильно возрастает, что создает трудности для отвода низкомолекулярных продуктов.
Существует еще одно осложнение: полимер получается в виде расплава, и его надо удалять из реактора горячим и немедленно, иначе он застынет прямо в реакторе. Обычно горячий полимерный расплав сразу направляют на переработку методом экструзии или литья.
Достоинством метода является отсутствие необходимости удаления из полимера растворителя и регенерации последнего.
Поликонденсацией в расплаве в промышленности получают полигексаметиленадипамид (анид или найлон-6,6) из гексаметилендиамина и адипиновой кислоты и лавсан из диметилового эфира терефталевой кислоты и этиленгликоля. Выбор в этом процессе диметилового эфира терефталевой кислоты взамен самой кислоты связан с тем, что диметилтерефталат плавится при более низкой температуре (140 оС, а не 425 оС как кислота) и хорошо растворим в этиленгликоле в отличие от самой терефталевой кислоты.
8.2.2.Поликонденсация в растворе
Вэтом методе исходные мономеры перед проведением процесса растворяют в инертном растворителе, а сам процесс проводят при 20–50 оС.
Преимущества метода: более низкая по сравнению с поликонденсацией в расплаве температура реакции; облегченный тепло- и массообмен. Растворитель может служить улавливающим агентом для выделяющихся низкомолекулярных продуктов, что облегчает их удаление из реакционной массы.
Недостатки метода. Растворитель уменьшает вероятность роста цепи. Это снижает скорость реакции и молекулярную массу образующегося полимера.
Поликонденсацией в растворе получают большинство жидких полиэфирных смол на основе гликолей и непредельных дикарбоновых кислот. В качестве растворителя берут высококипя-
90