
книги / Экономика отрасли машиностроение
..pdfАнализ конкурентоспособности начинается с оценки нормативных параметров. Если хотя бы один из них не соответствует уровню, который предписан действующими нормами и стандартами, то дальнейшая оценка конкурентоспособности продукции нецелесообразна, независимо от результата сравнения по другим параметрам. В то же время, превышение норм и стандартов и законодательства не может рассматриваться как преимущество продукции, поскольку, с точки зрения потребителя, оно часто является бесполезным и потребительской стоимости не увеличивает.
Исключения могут составить случаи, когда покупатель заинтересован в некотором превышении действующих норм и стандартов в расчете на ужесточение их в будущем. Производится подсчет групповых показателей, которые в количественной форме выражают различие между анализируемой продукцией и потребностью по данной группе параметров и позволяют судить о степени удовлетворения потребности по этой группе. Рассчитывается интегральный показатель, который используется для оценки конкурентоспособности анализируемой продукции по всем рассматриваемым группам параметров в целом. Результаты оценки конкурентоспособности используются для выработки вывода о ней, а также — для выбора путей оптимального повышения конкурентоспособности продукции для решения рыночных задач.
Однако, факт высокой конкурентоспособности самого изделия является лишь необходимым условием реализации этого изделия на рынке в заданных объемах. Следует также учитывать формы и методы технического обслуживания, наличие рекламы, торгово-политические отношения между странами и т. д.
В результате оценки конкурентоспособности продукции могут быть приняты следующие решения:
•изменение состава, структуры применяемых материалов (сырья, полуфабрикатов), комплектующих изделий или конструкции продукции;
•изменение порядка проектирования продукции;
•изменение технологии изготовления продукции, методов испытаний, системы контроля качества изготовления, хранения, упаковки, транспортировки, монтажа;
201
•изменение цен на продукцию, цен на услуги, по обслуживанию и ремонту, цен на запасные части;
•изменение порядка реализации продукции на рынке;
•изменение структуры и размера инвестиций в разработку, производство и сбыт продукции;
•изменение структуры и объемов кооперационных поставок при производстве продукции и цен на комплектующие изделия и состава выбранных поставщиков;
•изменение системы стимулирования поставщиков;
•изменение структуры импорта и видов импортируемой продукции.
Принципы и методы оценки конкурентоспособности могут быть использованы для обоснования принимаемых решений при:
– комплексном изучении рынка и выборе направлений коммерческой деятельности предприятия;
– разработке мероприятий по повышению конкурентоспособности продукции;
– оценке перспектив продажи конкретных изделий и формировании структуры продаж;
– разработке предложений по развитию производственного потенциала предприятия;
– контроле качества продукции;
– установлении цен на продукцию;
– отборе продукции при покупке через тендеры и торги;
– аттестации продукции;
– подготовке технических заданий по созданию новых образцов продукции;
– решении вопроса о включении в экспортную программу и снятии продукции с экспорта, либо ее модернизации;
– подготовке информации для рекламы продукции.
Лекция 13
УПРАВЛЕНИЕ КАЧЕСТВОМ. ПОНЯТИЕ И СИСТЕМА
ПОКАЗАТЕЛЕЙ КАЧЕСТВА
Понятие «качество продукции» — экономическая категория и как объект экономической науки тесно связана с категорией
потребительной стоимости |
и проявлением последней лишь |
в процессе использования |
этой стоимости (продукции). |
К. Маркс писал: «Полезность вещи делает ее потребительной стоимостью. Но эта полезность не висит в воздухе. Обусловленная свойствами товарного тела, она не существует вне этого последнего. Поэтому товарное тело … само есть потребительная стоимость или благо».
Потребительная стоимость характеризуется двояко: с одной стороны, как вещь или материальный предмет; а с другой — как вещь, которая способна соответственно своим свойствам удовлетворить определенные человеческие потребности.
К. Маркс: «Продукт, потребительские свойства которого выше потребительских свойств других продуктов одинакового назначения, признается продуктом более высокого качества». Здесь существенны не сами свойства продукта, а, именно, потребительские свойства продукта, в какой мере и в какой степени они способны удовлетворять конкретную потребность общества. Потребителя не интересует природа предмета потребления как таковая, для него важно, чтобы данная потребительная стоимость обладала нужными ему свойствами. Оценка потребительной стоимости по степени удовлетворения конкретной потребности определяет ее качество.
До настоящего времени среди специалистов нет единства в определении понятия «качество продукции». Наиболее точное определение понятия «качество продукции» дано в ГОСТ. Согласно этому стандарту, качество продукции — это совокуп-
203

ность свойств продукции, обусловливающих ее пригодность удовлетворять определенные потребности в соответствии с ее назначением1.
Под свойством продукции понимается объективная особенность последней, проявляющаяся при ее производстве, эксплуатации или потреблении. Различают производственные (совокупность свойств, создаваемых в процессе производства) и потребительские (определяющие совокупность показателей, которая относится к числу наиболее важных и значимых для потребителя) свойства продукции.
Количественная характеристика свойств продукции называется показателем качества продукции. По количеству характеризуемых свойств и характеристик различают показатели качества:
1.Единичные — отражают одно свойство продукции (например, скорость, потребляемая мощность и др.).
2.Комплексные — характеризуют совокупность нескольких свойств продукции (например, надежность, воспроизведение телевизором типовой испытательной таблицы и др.).
3.Определяющие — оценочные показатели, по которым принимаются решения о качестве.
4.Интегральные — выражаются через соответствующую сумму экономических или технических показателей (например, суммарный полезный эффект от эксплуатации продукции, суммарные затраты на создание и эксплуатацию изделия).
Для продукции машиностроения может быть установлена следующая номенклатура показателей качества (рис. 13.1).
Приведенная на рисунке система показателей качества продукции является основной для количественной оценки и определения уровня качества конкретного вида продукции. При этом уровень качества изделия может оцениваться в зависимости от поставленной цели дифференцированно, либо по единичным, комплексным или интегральным показателям качества, либо по производственной или потребительской группе.
Уровень качества — это относительная характеристика ка- чества, основанная на сравнении значений показателей качества
1ГОСТ 15467–79. Управление качеством продукции. Термины и определе-
íèÿ.
204
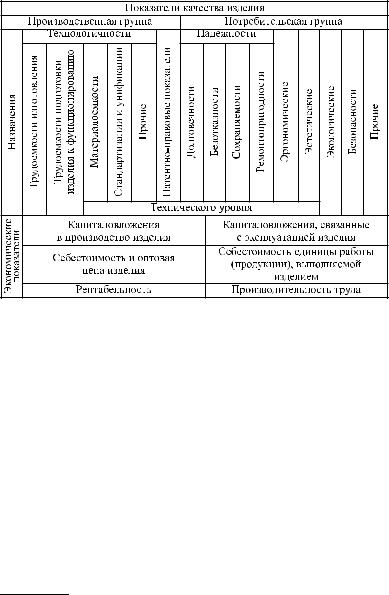
Рис. 13.1. Система показателей качества продукции |
оцениваемой продукции с соответствующими показателями продукции, принятой за базу для сравнения1.
Наряду с уровнем качества определяется технический уровень продукции. Оценка последнего обычно проводится при разработке новых или аттестации серийно выпускаемых изделий по номенклатуре технических показателей, представленных на рис. 13.1.
Эволюция подходов к управлению качеством
Поскольку качество является важнейшим фактором повышения уровня жизни, экономической, социальной и экологиче- ской безопасности и как комплексное понятие характеризует эффективность всех сторон деятельности (разработка стратегии, организация производства, маркетинг и др.), изучению данной
1Новицкий Н. И., Пашуто В. Л. Организация, планирование и управление производством: учеб.-метод. пособие.— М.: Финансы и статистика, 2006.— С. 234.
205
проблемы экономисты уделяют особое внимание. В данном разделе рассмотрим историю управления качеством от истоков возникновения до настоящего времени.
Эволюцию подходов к управлению качеством продукции на отечественных предприятиях можно проследить, начиная со времени Ивана Грозного, когда по его указанию впервые были введены стандартные калибры-кружала для измерения диаметров пушечных ядер, а при постройке сторожевого городка Свияжска — строительные элементы, заранее изготовленные по стандартным размерам в г. Угличе. Однако этот период характерен только для отдельных стандартизированных решений. Нача- ло более широкому внедрению стандартизации в производство с целью повышения качества продукции было положено Петром 1, во времена правления которого начинается отсчет русской промышленной стандартизации.
В первом собрании законов Российской империи эпохи Петра I имеется ряд указов, свидетельствующих о том, что в это время в России внедрялись элементы стандартизации и взаимозамещаемости с целью повышения качества продукции, выпускаемой на отечественных предприятиях. В контексте рассматриваемого вопроса об отечественном опыте государственного управления каче- ством продукции несомненный интерес представляет Указ Петра I о качестве от 11 января 1723 года. Из текста Указа ясны не только требования Государя к качеству продукции, но и к системе контроля качества, государственного надзора за ним и меры ответственности и наказания за выпуск недоброкачественной продукции.
Стремясь к расширению внешней торговли, Петр I не только ввел технические условия, учитывающие высокие требования иностранных рынков к качеству товаров, но и организовал в Петербурге и Архангельске правительственные бракеражные комиссии, которым вменялось в обязанность следить за качеством экспортируемого Россией сырья (льна, древесины) и других видов продукции.
Развитие промышленности и транспорта в России привело к расширению работ по стандартизации. В 1860 году был установлен единый размер железнодорожной колеи (1524 мм) и утверждены габаритные нормы приближения строений и подвиж-
206
ного состава. В 1889 году приняты первые технические условия на проектирование и сооружение железнодорожных путей, а в 1898 году — единые технические требования к поставке основных материалов и изделий для нужд железнодорожного транспорта. В 1899 году был выпущен единый сортамент профилей прокатной стали.
Внедрение российских национальных стандартов и единых требований к качеству продукции в дореволюционной России затруднялось из-за большого числа иностранных концессий, владельцы которых применяли, как правило, свои стандарты. Такое положение привело, в частности, к распространению в России трех систем мер (аршинной, дюймовой, метрической), затруднявших производство продукции и контроля ее качества.
Одним из первых после Октябрьской революции был принят декрет «О введении международной метрической системы мер и весов» (14 сентября 1918 года), имевший важное значение для развития стандартизации и повышения качества.
В 1926 году был утвержден первый общесоюзный стандарт ГОСТ 1 «Пшеница. Селекционные сорта зерна. Номенклатура». В том же году были приняты стандарты на новый сортамент стального проката, что позволило сократить число типоразмеров профилей в 6 раз, а также стандарты на метрическую и дюймовую резьбу, на допуски и посадки, благодаря чему было налажено серийное и массовое производство стандартных общемашиностроительных деталей. Эти стандарты послужили основой для овладения методами передовых зарубежных фирм по контролю качества продукции на основе системы допусков и посадок. Таким образом, одной из первых форм управления качеством продукции стала проверка изделий методом сортировки и разбраковки на годные и негодные, т. е. соответствующие и несоответствующие стандарту.
К началу 1975 года в СССР действовало уже более 20 тыс. стандартов, охватывающих важнейшие виды промышленной и сельскохозяйственной продукции, более 15 тыс. отраслевых стандартов и свыше 100 тыс. технических условий.
Для планомерного повышения качества выпускаемой продукции были введены аттестация промышленной продукции по высшей, первой и второй категориям качества и присвоение Государственного знака качества.
207
Однако множество разработанных стандартов и аттестация промышленной продукции на категории качества не привели к желаемому результату, так как проводились без системного подхода и лишь на одной стадии «жизненного цикла» изделия — на стадии производства. Практика показывает, что только системный подход к управлению качеством позволяет добиваться положительных результатов.
Проследим эволюцию воплощения системного подхода к организации работ по улучшению качества продукции в отече- ственной практике последних лет.
Â1955 году на предприятиях г. Саратова были разработаны
èвнедрены организационно-технические мероприятия по обеспечению бездефектного изготовления продукции и сдачи ее в от-
дел технического контроля (ОТК) с первого предъявления. В своей совокупности они образовали саратовскую систему управления качеством продукции (систему БИП).
Â1957–1958 годах на предприятиях г. Горького (теперь Нижний Новгород) появилась система КАНАРСПИ (качество, надежность, ресурс с первого изделия). В этой системе был сделан упор на повышение надежности изделий, в эксплуатации за счет укрепления технической подготовки производства, на долю которой приходилось 60–85 % дефектов, обнаруживаемых при эксплуатации. Создавались опытные образцы узлов, деталей, систем и изделия в целом, и проводились их испытания, выявлялись причины, вызывающие отказы изделия при эксплуатации, разрабатывались мероприятия по их устранению.
Внедрение системы КАНАРСПИ на ряде предприятий Горьковской области позволило: сократить сроки доводки новых изделий до заданного уровня качества в 2–3 раза; повысить надежность выпускаемых изделий в 1,5–2 раза; увеличить ресурс
â2 раза; снизить трудоемкость и цикл монтажно-сборочных работ в 1,3–2 раза.
Â1963–1964 годах на Ярославском моторном заводе была разработана и внедрена система НОРМ (научная организация труда по увеличению моторесурса). Цель системы — увеличе-
ние надежности и долговечности выпускаемых двигателей. В ней был учтен опыт предшествовавших систем БИП
208

èКАНАРСПИ, и введен новый важный элемент — управление связями между потребителями изделий и проектировщиками. В основу системы НОРМ был положен принцип последовательности и систематического контроля за уровнем моторесурса
èпериодическим его увеличением на базе повышения надежности и долговечности деталей и узлов, лимитирующих моторесурс. Основным показателем являлся ресурс двигателя до первого капитального ремонта, выраженный в моточасах. Рост этого показателя в системе планировался.
Â1975 году на предприятиях Львовской области появились комплексные системы управления качеством продукции (КС УКП). Целью этой системы было создание продукции, соответствующей лучшим мировым аналогам и достижениям науки
èтехники.
Âнастоящее время в различных информационных источниках содержатся многообразные определения термина «управление», то есть управление — это достаточно распространенное, но не стандартизированное в общем смысле понятие.
Так, например, В. В. Окрепилов определяет управление двояко: как процесс целеполагания, и как деятельность по достижению поставленной цели. Однако, по мнению автора, данная трактовка управления несколько узка.
Значительное внимание раскрытию содержания управления уделено в трудах З. М. Короткова. Выявляя потребность в управлении, он отмечает, что «вся жизнь человека — это бесконечная цепочка его деятельности, которая разнообразна и многообразна»1. Управление, по определению ученого,— это вид деятельности человека, возникший, выделившийся и обособившийся в процессе развития совместного труда, его разделения и кооперации, это объективная потребность всякой деятельности человека2.
Предложенный подход позволяет выделить основные составляющие процесса управления, включающие:
1. процесс превращения цели в согласованную деятельность;
1Коротков Э. М. Концепция менеджмента.
2Коротков Э. М. Концепция менеджмента.
209

2.функционирование системы управления;
3.взаимодействие звеньев;
4.разработку управленческих решений;
5.деятельность менеджера во времени и пространстве;
6.последовательность действий, составляющих управление (воздействие);
7.процесс формирования воздействия;
8.решение проблем развития предприятия.
Возвращаясь к истории, следует отметить, что приблизительно до конца 1980-х годов речь шла в основном о термине «управление качеством продукции». Еще в 1979 году А. В. Гли- чев, М. И. Круглов, И. Д. Крыжановский, О. Г. Лосицкий определили управление качеством продукции как «постоянный, планомерный, целеустремленный процесс воздействия на всех уровнях на факторы и условия, обеспечивающий создание продукции оптимального качества и полноценное ее использование». Это же определение приводит Т. В. Корнеева. Экономиче- ский словарь «Качество продукции» трактует данный термин следующим образом: «Управление качеством продукции — процесс руководства деятельностью коллективов предприятий и организаций по достижению и поддержанию динамичной сбалансированности свойств продукции с потребностью в этих свойствах в интересах ее наиболее полного удовлетворения».
В 1998 году А. В. Гличев пишет: «Управление качеством продукции — это подготовка и внесение в план по качеству, нормативную, техническую документацию значений показателей качества вновь осваиваемой или модернизируемой продукции или изменение показателей качества выпускаемой продукции, а также выполнение необходимых работ по достижению и поддержанию этих значений показателей»1.
К концу 1980-х годов стало ясно, что говорить лишь об управлении качеством продукции — значит иметь в виду десятую долю из всего многообразия объектов, об управлении каче- ством которых необходимо вести речь в современных условиях. В связи с этим понятие «управление качеством» было стандарти-
1Гличев А. В. Основы управления качеством продукции.— 1998.— С. 99.
210