
Поведение конструкций из композитных материалов
..pdfные материалы, показана на рис. 13. Сведения о материалах, имеющих наиболее широкое применение при изготовлении волокон,*а также о ма териалах, используемых в качестве матриц, приведены ниже:
А1* Оэ - оксид алюми ния А1 - алюминий
В - бор* ВЫ - нитрид бора
Армирующие элементы
Be - бериллий
GI - стекло* (7г —графит*
Kv - арамид * (кевлар)
SiC - карбид кремния
Si3 Ы4 - нитрид кремния Ti - титан
W - вольфрам
Имеют преимущественное применение в качестве высокопрочных армирующих элементов
Материалы матриц (термостойкие, термопластичные, металлические)
Ацетатные |
Графит |
Эфир |
Полиимид* |
Полиакрилат |
Никель |
Полиэтилен |
Полиуретан |
Алюминий* |
Нейлон |
Фенолформальде |
Фенил |
Эпоксидная |
Полиоксибензоат |
гид* |
Титан |
Полипропилен |
Применяют для высокопрочных композитов
Следует отметить, что здесь не используется существующее на практи ке разделение на композиты с металлической и неметаллической мат рицей.
Влитературе наиболее полно описаны борные, стеклянные, углеродные
иорганические волокна, использующиеся в качестве армирующих эле ментов.
Армирующие и матричные материалы объединяются в композитные системы по следующей схеме:
Матрица |
Армирующие элементы |
Композитная структура |
|
(металлы, полимеры, |
(усы, |
волокна, прово |
(слоистые, волокнистые |
керамика) |
лока) |
|
намотанные изделия) |
Как уже отмечалось, комбинация волокон и матрицы может осущест вляться в разных структурных форма* в соответствии со способом изго товления материала. Далее мы расскажем о технологических процессах, применяющихся при производстве композитных материалов. Специаль ные виды структур могут быть синтезированы в ходе процесса изготов ления композита с учетом требований ^проектирования и функциональ ного назначения конструкции. Типичные армирующие элементы могут быть выполнены в виде усов, волокон или проволоки. Основным па раметром, характеризующим армирующие элементы, является их диа метр или средний диаметр пучков волокон. Данные, приведенные ниже,
Усы |
Волокна |
Проволока |
Пруток |
Стержень |
<0,01 |
0,01-1,0 |
1,0-1,0 |
10-50 |
> 50 |
1.4. TlEXHOЛОГИЧЕСКИЕ ПРОЦЕССЫ ИЗГОТОВЛЕНИЯ КОМПОЗИТОВ
Как отмечалось, образование некоторой композитной системы из во локна и матрицы происходит в ходе технологического процесса. Сведения о некоторых технологических процессах, относящихся к производству композитов с неметаллической и металлической матрицами, приведены в табл. 1.1. Следует отметить, что предпочтительность того или иного процесса определяется его производительностью, конструктивными осо бенностями изделия и экономическими показателями. Применение ука занных процессов не ограничивается высокопрочными материалами, ар мированными непрерывными волокнами. В связи с этим данные табл. 1.1 могут быть использованы как общая иллюстрация процесса изго товления композитных материалов.
Т а б л и ц а |
1.1 Технологические процессы изготовления |
||
|
композитов |
|
|
Технологический процесс |
Композиты с |
Композиты с |
Коротковолокнис- |
|
немсталлической |
металлической |
тые композиты |
|
матрицей |
матрицей |
|
Укладка вручную |
+ |
|
+ |
Формование вакуумным |
|
|
+ |
мешком или в автоклаве |
+ |
|
|
Прессование (литейная |
+ |
+ |
+ |
технология) |
|||
Намотка |
+ |
+ |
|
Прессование и прокатка |
|
+ |
|
Плазменное напыление |
|
+ |
+ |
Порошковая металлургия |
|
+ |
+ |
Пропитка жидкой фазой |
+ |
+ |
+ |
Экструдирование |
|
+ |
|
Направленная кристалли |
|
+ |
|
зация |
|
|
|
Ротационное формование |
|
+ |
+ |
Полгрузия |
|
+ |
|
Инжекторное литье |
|
+ |
+ |
Центробежное литье |
|
+ |
+ |
Изготовление листовых |
|
|
|
композитов |
|
+ |
+ |
Вакуумное всасывание |
|
|
Заметим, что технология изготовления композитов в основном опреде ляется матрицей. Например, при изготовлении композитов с полимерной матрицей применяют литье под давлением, экструдирование и некоторые другие специальные методы. Выбор метода формирования определяется целым рядом требований, главным из которых является экономичность. Для композитов с металлической матрицей основными методами форми рования служат литье, прокатка и экструдирование. И, наконец, для соз дания композитов с короткими, дискретными волокнами применяют непрерывное литье, ротационную разливку, инжекторное и центробежное литье.
Методы порошковой металлургии. Согласно этой технологии в качест ве армирующих элементов используют усы и короткие волокна. Уложен ные в определенном порядке или расположенные хаотично, исходные армирующие элементы смешиваются с соответствующей порошковой матрицей. После этого материал помещают в форму и подвергают горяче му или холодному прессованию (рис. 1.4) . В ходе процесса прессования может одновременно идти синтез материала.
Недостатком описываемой технологии является опасность повреж дения волокон, в особенности, если размеры частиц превышают средний диаметр волокон. Кроме того, следует иметь в виду и неизбежную в дан ном процессе пористость изделия. Типичными композитными системами, получаемыми по данной технологии, являются: алюминий — нержавею
щая сталь; алюминий - титановый сплав |
— молибден; алюминий — |
вольфрам. |
|
Прессование и прокатка. Согласно этому |
технологическому процессу |
слои матрицы с уложенными на них в определенном порядке волокна ми нагреваются до высокой температуры, а затем прессуются или прока тываются вместе для образования композитной системы (рис. 15). При этом необходимо проводить предварительную очистку поверхностей во локон и листов матрицы. Недостатком процесса является возможность реакционного взаимодействия между материалами волокон и матрицы, что может иметь место при длительной выдержке под давлением входе прессования. Указанная технология находит применение для следующих композиций: нержавеющая сталь - алюминий, вольфрам — алюминий.
Пропитка жидкой фазой. Этот вид производства композитных мате-
Зп
Рис. 1.4. Метод порошковой металлургии: 1 - верхняя плита; 2 - нагреватель; 3 — плунжер; 4 - образец; 5 - нижняя плита; 6 термопара
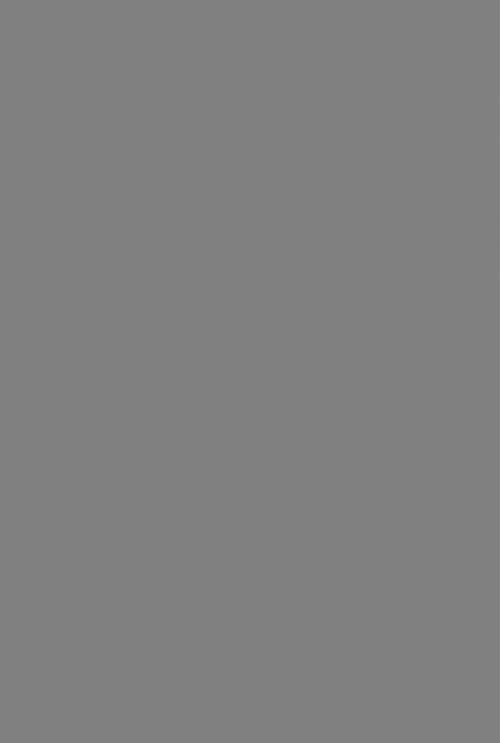
/ г j J 4 5
г |
6 |
|
7 |
||
|
||
1 |
|
Рис. 1.7. Совместное экструдирование:
1 - фильера; 2 - направляющие; 3 - покрытие; 4 - подложка; 5 - направление экструзии; 6 - плунжер; 7 - сердцевина; 8 - стенка камеры экструдирования
Рис. 1.8. Плазменное напыление:
1 — водяное охлаждение; 2 — смотровое окно; 3 - суспензия-распылитель; 4 —ис точник плазмы; 5 - термопара; 6 - выпускной клапан; 7 - оправка с композитом; 8 - резиновый кожух; 9 - источник энергии
Совместное экструдирование. Согласно этому методу материалы, подлежащие соединению, пропускают через специальную фильеру под высоким давлением (рис. 1.7). Таким образом, армирующая фаза и матричный материал подвергается совместному экструдированию.
В связи с необходимостью создания высокого давления данный процесс используется для материалов с мягкой матрицей. Основное преимущество процесса перед другими заключается в том, что при этомщостигается эф фективное соединение между матрицей и волокнами. Кроме того, наблю дается увеличение прочности композита, поскольку затвердевание матри цы происходит во время экструдирования. Таким образом получают композитные системы на основе хромоникелевых сплавов армирован ных волокнами сапфира.
Нанесение покрытий и напыление. Технология нанесения покрытий представлена двумя методами — плазменного напыления и электро осаждения. При плазменном напылении (рис. 1.8) слой волокон нама тывается на вращающуюся оправку. Материал матрицы при этом из исходного порошкообразного состояния осаждается на волокна плаз менным способом. Затем наматывается второй и последующие слои пока не будет достигнуто их заданное количество. После этого композит сни мается с оправки и может далее подвергаться горячему прессованию с целью снижения пористости.
При электроосаждении (рис. 1.9) в качестве катода используется электропроводящая оправка, а расходуемым анодом служит материал матрицы, размещенной в электролитической ванне. Слой из непрерыв ных волокон наматывается на оправку, затем на него осаждается слой материала матрицы. Количество осажденного материала зависит от скорости осаждения и площади поверхности волокна, намотанного на оправку. Примерами композитных систем, изготавливаемых технологией
Рис. 1.9. Электроосаждение:
1 - однонаправленный композит; 2 - оправка-катод; 3 - металлический анод; 4 - источник питания; 5 —бобина с волокнами; 6 - направляющая волокна; 7 - электролитическая ванна
Рис. 1.10. Направленная кристаллизация:
1 - нагревательное устройство; 2 - тигель; 3 - заряд; 4 —термопара; 5 - охлаж даемый блок; 6 - защитный экран; 7 - вода; 8 - инертный газ
нанесения покрытий, могут служить: сталь —алюминий, бор —алюминий, бор —титан.
Направленная кристаллизация. В этом процессе (рис. 1.10) в образце из сплава эвтектической концентрации при определенной скорости ох лаждения имеет место рост однонаправленных цилиндрических кристал лических образований. Основное преимущество способа заключается в том, что образование армирующей фазы, (в механически и химически совместимых композитных системах) не является искусственным про цессом. Примерами могут служить системы материалов: медь —алюми ний (СиА12) , алюминий —никель (Al3Ni) .
Ручная выкладка. В лабораторных условиях изготовление образцов из композитов с полимерной матрицей обычно осуществляется с помощью ручной выкладки. В промышленных условиях используется машинная выкладка, которая позволяет снизить вероятность образования пустот, и уменьшить себестоимость изделия. Для изделий из волокнис тых композитов обычно используют ленты препрега, которые распола гают в соответствии с предварительно определенными требованиями. Та ким образом, в ходе процесса производства заданная ориентация и после довательность укладки осуществляется в соответствии с исходными тре бованиями. Выкладка изделия проводится в специальном помещении. При этом используется оснастка, обеспечивающая формование по задан ной фазовой поверхности. Процесс изготовления заключается в выклад ке в соответствующем порядке необходимого числа слоев композита, а также разделительных и пористых слоев, обеспечивающих отделение готового изделия от поверхности оснастки и абсорбцию избыточной
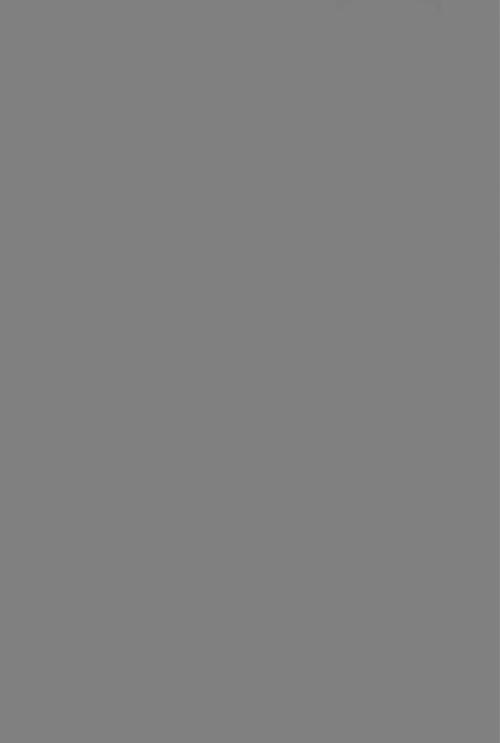
ными армирующими элементами, при этом достигается эффективное использование прочности волокон. Подаваемые непрерывно в виде от дельных нитей или ровинга волокна поступают в ванну со смолой и нама тываются на оправку соответствующего профиля. Может быть использо вана также предварительная пропитка. Специально переоборудованные токарные станки позволяют укладывать непрерывные стеклянные волок на по определенной схеме с обеспечением максимальной прочности в заданном направлении. После завершения намотки материал отверждает ся при комнатной или повышенной температуре. Типичными изделиями, изготавливаемыми по описанной технологии, являются химические резервуары и сосуды давления.
Вакуумное и автоклавное формование. Согласно этому методу па кеты, подготовленные ручной или машинной выкладкой, уплотняются с помощью вакуумного мешка или в автоклаве. Чаще всего такой обра ботке подвергаются пакеты, набранные из препрега. Предварительные операции включают выкладку препрегов, подготовку резделительных и впитывающих слоев, а также операции вакуумирования. Вакуумный мешок, соответствующий контуру формуемой детали, покрывает пакет, включающий композитные, разделительные и пористые слои. Вакуум ный патрубок присоединяется к мешку, место его соединения с осно ванием герметизируется. Система откачивается до создания неполного вакуума с целью контроля плотности прилегания мешка к поверхности детали. Окончательное формование и отверждение идут при полном вакууме в соответствии с предписанным режимом нагрева и охлаждения. Схематически процесс вакуумного формования показан на рис. 1.13.
Для формования эластичным мешком с помощью давления мешок помещается внутри предварительно сформированной стеклопластико вой детали, а вся эта система —в холодную пресс-форму. После тщатель ной пропитки в мешке создается давление 0,25 - 03 МПа, пресс-форма нагревается и деталь отверждается. После отверждения давление сбрасы вается и мешок удаляется обычно через отверстие на конце детали. Ме тод находит применение для изготовления резервуаров, используемых для смягчения воды, водоразборных систем, фильтрующих емкостей и хра нилищ, баллонов огнетушителей.
При открытом формовании вакуумным мешком выложенный слой пропитанных стекловолокон покрывается удаляемой оболочкой-мешком. Соединения герметизируются и осуществляется вакуумирование. При этом под воздействием атмосферного давления исчезают пустоты, выво дятся остаточные газы и лишняя смола. Применение метода ограничено изделиями небольшого объема, в частности, деталями электронных уст ройств.
В отличие от вакуумного формования отверждение в автоклаве проис ходит при высоких давлениях, что дает возможность получать более плот ные материалы. В этом процессе используется как давление и температу-
/ г з
г
Рис. 1.13. Метод вакуумного мешкай автоклавного формования:
1 - |
впитывающий слой; 2 - плита, создающая давление; 3 - |
вакуумный мешок; |
4 - |
ограничитель; 5 - герметик; 6 - инструментальная плита; |
7 - деталь; 8 - раз |
делительные слои |
|
|
Рис. 1.14. Метод прессования: |
|
|
1 - |
образец; 2 - разъемная матрица |
|
ра, |
так и вакуумирование. Последнее обеспечивает |
удаление воздуха |
и излишков смолы. При отверждении в автоклаве температура и дав ление воздействуют одновременно в течение всего цикла, а вакуум используется только на некоторой части цикла. В автоклаве можно по лучать изделия заданной толщины с минимальной пористостью. Парамет ры процесса зависят от применяемого оборудования. Так, давление при вулканизации может изменяться в пределах 0,18—0,56 МПа, а темпера тура вулканизации достигает 177 °С .
Прессование в металлических пресс-формах. Для производства неболь ших изделий разнообразной формы и размеров массовыми партиями часто используется прессование. Этот процесс ведется при высоких дав лениях (до 35 МПа) и высокой температуре (до 540 °С) и может приме няться для изготовления деталей различной конфигурации. Кроме того, в зависимости от особенностей обрабатываемого материала, процесс можно вести в атмосфере газа или в вакууме. Закрытое прессование успешно применяется для изделий, армированных как длинными, так и короткими волокнами. Таким способом могут быть изготовлены стандартные образцы для испытаний и качественного контроля. Преиму щественно эта технология используется для изготовления массовых
Рис. 1.15. Ротационное формование
Рис. 1.16. Метод непрерывной пултрузии
партий изделий коммерческого назначения, когда требуются детали опре деленных форм и размеров. Схема процесса формовки на прессе листо вой заготовки показана на рис. 1.14.
Ротационное формование. Согласно этому методу термопластичные порошки с добавленными к ним короткими волокнами помещают в подогреваемую форму (рис. 1.15). Форма имеет возможность вращения в одной или двух плоскостях, во время которого происходит перемеши вание и связывание материала. После отвердевания и охлаждения изде лие извлекается из формы. Процесс может применяться для изготовле ния контейнеров и других изделий типа оболочек.
Пултрузия. Процесс основан на протягивании пропитанных смолой жгутов волокон через систему формующих фильер (рис. 1.16). Отверж дение осуществляется в термопечах, обеспечивающих необходимый тем пературный цикл. Таким способом могут быть изготовлены такие эле менты, как трубы и двутавровые балки.
Инжекторная формовка. Этот процесс применяется для изготовления композитов с термопластичной и термореактивной матрицей. Для компо зитов с термопластичной матрицей используют обычно две системы пода чи матричного материала, обеспечивающие введение ее в виде шариков и размягчение с инжекторной камере. Подогретый материал матрицы, наполненной короткими волокнами, вводится в холодную формовочную камеру, где подвергается нагреву и давлению, обычно в течение одной минуты (рис. 1.17). Диапазон давлений может изменяться от 0,7 МПа до 10,5 МПа, в то время как температура отверждения —от 135 до 163 °С. Процесс используется для сложных формовочных составов и применя ется при изготовлении клапанов, деталей тяжелонагруженных подшип ников и небольших зубчатых колес.
Центробежное литье. Процесс может применяться для изготовления трубчатых элементов и изделий типа контейнеров. При центробежном литье изделия типа тел вращения образуются во внутренней полости вращающейся, подогреваемой формы (рис. 1.18) .Материал представляет собой смесь коротких волокон и смолы. Действие центробежных сил таково, что благодаря им материал постепенно перемещается к стенкам формы. Одновременно протекает процесс отверждения, который может быть ускорен подачей горячего воздуха во внутреннюю полость оправки.
Рис. 1.17. Метод инжекционного формования
Рис. 1.18. Метод центробежного литья