
648
.pdf
Расчётнаядинамическая грузоподъёмность
Cп |
2,8 |
60 220 6000 1 3 |
12,02 кН. |
|||
|
|
|
|
|||
10 |
6 |
|||||
|
|
|
|
|
|
Принят упорный подшипник особолёгкой серии 8110 со следующими характеристиками: d D H = 50 70 14; С = 29 кН,
С0 = 64 кН [7].
Вывод. Условие С > Ср выполнено для обоих типов подшипников. На обеих опорах приняты радиальные подшипники 210, на опоре 2 установлен упорный подшипник 8109.
Пример 14.7. Подобрать по статической грузоподъёмности
радиальные однорядные шарикоподшипники по схеме рис. 14.3. Исходные данные: радиальные нагрузки Fr1 = 4,2 кН; Fr2 =
= 3,6 кН, осевая нагрузка Fа = 2 кН, диаметр шейки d = 50 мм. Решение. Подшипник 2 принят плавающим, так как он вос-
принимает меньшую радиальную нагрузку. Расчёт проведен для более нагруженного фиксированного подшипника 1, восприни-
мающего полную осевую и бóльшую радиальную нагрузку. Статическая нагрузка при коэффициентах X0= 0,6 и Y0= 0,5 [7]:
Р0 = X0Fr1 + Y0Fa = 0,6·4,6 + 0,5·2 = 3,76 кН; Р0 = Fr1 = 4,6 кН.
Приняты подшипники 1000910 с параметрами d D В = = 50 72 12; С = 14,5 кН; С0 = 9,7 кH [5].
ЗАДАЧИ ДЛЯ САМОСТОЯТЕЛЬНОЙ РАБОТЫ
Часть экзаменационных задач не отражена в материале лабораторных работ. Им посвящён данный раздел. Для пояснения решений приведен минимально необходимый теоретический материал.
Шпоночные соединения
К ненапряжённым шпоночным соединениям относятся соединения призматическими и сегментными шпонками. Шпонка – специальная деталь, закладываемая в пазы вала и ступицы. При передаче крутящего момента Т на боковых гранях таких шпонок возникают напряжения смятия см, а в продольном сечении
141
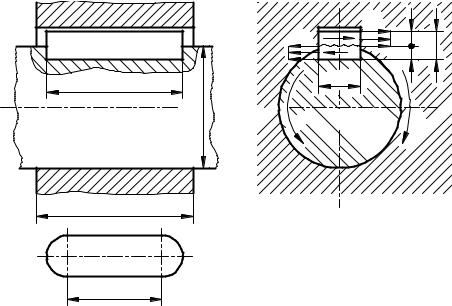
шпонки – напряжения среза (рис. 15.1). Стандартные призматические шпонки рассчитывают по напряжениям смятия.
l |
d
lст |
lр |
см |
см |
|
2 |
|
|
t |
h |
|
|
1 |
|
t |
||
b |
|
|
T T
Рис. 15.1. Соединение призматической шпонкой
Условие прочности на смятие
см |
|
2T |
см , |
(15.1) |
|
||||
|
|
dlp t2 |
|
где Т – крутящий момент, Н·мм; d – диаметр посадочного участка вала, мм; t2 – глубина паза ступицы детали вращения, мм; lp – расчётная длина шпонки со скругленными торцами, мм;
lр = l – b, |
(15.2) |
где l – полная длина шпонки; b – ширина шпонки.
Размеры сечений шпонок b h выбирают ГОСТ 23360 в зависимости от диаметра вала d из пособия [7] либо по табл. 1.2. Длину стандартной шпонки принимают l lст – 5 мм и округляют по ряду Ra20 ГОСТ 6636 (прил. И). Длину ступицы детали вращения принимают больше диаметра вала из условия центрирования по цилиндру по соотношению
lст = (1,2…1,5)d. |
(15.3) |
Допускаемое напряжение принимают [ см] = 100 МПа при переходных посадках (основное соединение – шпоночное) и [ см] = 150…200 МПа при посадках с натягом (основное соеди-
142
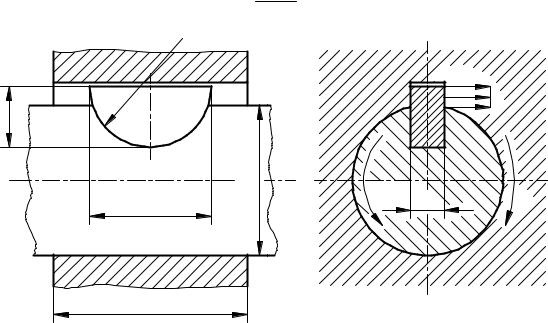
нение – прессовое). При переменной нагрузке их следует снижать на 20…25 %, при ударной нагрузке – на 40…50 %. При чугунной ступице напряжения уменьшают в два раза.
Пример 15.1. Подобрать и проверить на прочность шпо-
ночное соединение призматической шпонкой. Выполнить эскиз соединения и привести обозначение шпонки по ГОСТ 23360.
Исходные данные: диаметр вала d = 50 мм, крутящий момент на валу Т = 250 Н м, допускаемое напряжение [ см] = 100 МПа.
Решение.
Принята по диаметру вала шпонка с размерами сечения: ширина b = 14 мм, высота h = 9 мм, глубина паза втулки t2 = 3,8 мм
[7]. Длина ступицы lст = (1,2…1,5) 50 = 60…75 мм. Принята lст = = 70 мм [7]. Принята длина шпонки l = 63 мм [7]. Расчётная длина шпонки lp = 63 – 14 = 49 мм. Рабочее напряжение смятия
|
|
|
2T |
2 250 103 |
||
|
см |
|
|
|
|
53,3МПа < [100 МПа]. |
|
|
|||||
|
|
dlp t2 |
50 49 3,8 |
Вывод. Прочность достаточна. Принята шпонка 14 9 63
ГОСТ 23360–78.
Принцип работы сегментных шпонок (рис. 15.2) подобен принципу работы призматических шпонок. Расчёт на смятие выполняют по формуле
|
|
|
см |
|
2T |
|
|
|
|
d lt2 |
|
h |
d |
ш |
|
|
|
|
|
|
|
||
|
|
|
|
|
|
|
|
l |
|
d |
|
|
|
|
|
|
lст |
см . |
(15.4) |
|
|
см |
T |
b |
T |
Рис. 15.2. Соединение сегментной шпонкой
143
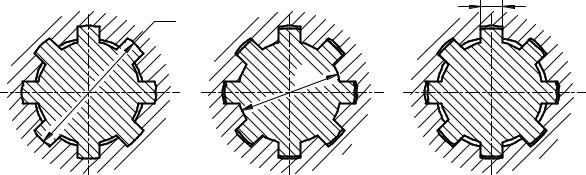
Пример 15.2. Подобрать и проверить на прочность шпо-
ночное соединение сегментной шпонкой. Выполнить эскиз соединения и привести обозначение шпонки по ГОСТ 24071.
Исходные данные: диаметр вала d = 30 мм, крутящий момент на валу Т = 200 Н м, допускаемое напряжение [ см] = 150 МПа.
Решение.
Принята по диаметру вала шпонка с размерами: ширина b = = 8 мм, высота h = 11 мм, глубина паза втулки t2 = 3,3 мм, диаметр шпонки dш = 28 мм [7]. Длина шпонки l = dш = 28 мм. Рабочие напряжения смятия
|
|
|
2T 2 200 103 |
|||
|
см |
|
|
|
|
144,3 Мпа < [150 МПа]. |
|
|
|||||
|
|
dlp t2 |
30 28 3,3 |
Вывод. Прочность достаточна. Принята шпонка 8 11 28
ГОСТ 24071–80.
Шлицевые соединения
Шлицевое соединение по конструкции является многошпоночным, где призматические шпонки выполнены заодно с валом (рис. 15.3). По форме профиля зубьев различают два основных вида соединений: прямобочные и эвольвентные. Центрирование осуществляют по внешнему D или внутреннему d диаметрам зубьев при обеспечении высокой соосности вала и ступицы, а также по боковым поверхностям зубьев b. Как и шпоночные, шлицевые соединения рассчитывают по напряжениям смятия.
b
a) |
D б) |
в) |
|
|
d |
Рис. 15.3. Соединение прямобочными шлицами
Условие прочности прямобочных шлицев
|
|
|
T |
[ |
|
], |
(15.5) |
|
см |
SFl |
см |
||||||
|
|
|
|
|
144
где l – рабочая длина зубьев; SF – удельный суммарный статический момент площади рабочих поверхностей в мм3/мм; принимается из прил. Т.
Пример 15.3. Подобрать и проверить прямобочное шлице-
вое соединение. Привести обозначение соединения по ГОСТ 1139 при центрировании по внутреннемудиаметруd.
Исходные данные: диаметр вала d = 60 мм, крутящий момент на валу Т = 600 Н м, допускаемое напряжение [ см] = 30 МПа.
Решение.
Длина ступицы l = (1,2…1,5) 60 = 72...90 мм. Принято l = = 80 мм (прил. И). Принято прямобочное шлицевое соединение 8 × 52 × 60 × 10 с числом шлицев z = 8, внутренним диаметром d = 52 мм, наружным диаметром D = 60 мм, шириной шлицев b = 12 мм и удельным суммарным статическим моментом площади рабочих поверхностей SF = 672 мм3/мм (прил. Т). Рабочее напряжение смятия
|
|
|
600 103 |
11,2МПа < [30 МПа]. |
|
см |
672 80 |
||||
|
|
|
Вывод. Прочность достаточна. Принято соединение d – 8 ×
×52H8 / e8 × 60 H10 / a11 × 10F10 / f8 ГОСТ 1139–80.
Эвольвентные шлицевые соединения (рис. 15.4) по сравнению
с прямобочными более технологичны, имеют более высокую точность и прочность, меньшую концентрацию напряжений. Условие прочности
|
|
|
2T |
[ |
|
], |
(15.6) |
|
см |
dm zhl |
см |
||||||
|
|
|
|
|
||||
где dm – средний диаметр; |
|
|
|
|
|
|||
dm mz(m – модуль, мм);` |
(15.7) |
|||||||
h – рабочая высота профиля зубьев; |
|
|
|
|
||||
|
|
|
h m; |
|
|
|
(15.8) |
– коэффициент, учитывающий неравномерное распределение нагрузки между зубьями и вдоль зубьев; = 0,7…0,8.
Допускаемые напряжения смятия назначают в зависимости от назначения машины и специфики эксплуатации. Значения
145
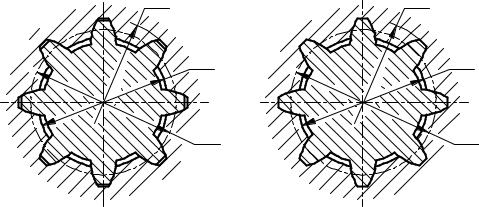
[ см ] для изделий общего машиностроения и подъёмнотранспортных устройств приведены в прил. У.
a) |
D |
б) |
D |
|
|
||
|
d |
|
d |
|
dср |
|
dср |
Рис. 15.4. Соединение эвольвентными шлицами
Пример 15.4. Подобрать и проверить эвольвентное шлицевое соединение. Привести обозначение соединения по ГОСТ6033–80 при центрировании по боковым сторонам зубьев b.
Исходные данные: наружный диаметр D = 70 мм, крутящий момент на валу Т = 600 Н м, допускаемое напряжение [ см] = = 20 МПа.
Решение.
Длина ступицы l = (1,2…1,5) 70 = 84...105 мм. Принято l = = 90 мм (прил. И). Принято эвольвентное шлицевое соединение с D = 70 мм, модулем m = 3 мм, числом зубьев z = 22 [7].
Средний диаметр dm = 3 22 = 66 мм, рабочая высота профиля h m 3 мм. Рабочее напряжение смятия
|
|
|
2 600 103 |
|
|
см |
|
|
4,1МПа < [20 МПа]. |
|
||||
|
|
66 22 3 90 0,75 |
Вывод. Прочность достаточна. Принято соединение 70 × 3 × × 9H / 9g ГОСТ 6033–80.
Коническая зубчатая передача
В коническом зацеплении перекатываются друг по другу на-
чальные конусы. Конические передачи бывают прямозубые, косозубые и с круговым зубом, с межосевым углом = 90°. Как и цилиндрические зубчатые передачи, их рассчитывают по контакт-
146

ным и изгибным напряжениям. Основным расчётным параметром является внешний делительный диаметр колеса de2, прини-
маемый стандартным аналогично межосевому расстоянию цилиндрической зубчатой передачи:
de2 165 3 |
u T2 KH |
, |
(15.9) |
|
|||
|
Н 2 Н |
|
где u – передаточное число; T2 – вращающий момент на валу колеса, Н·мм; KH – коэффициент нагрузки; принимать по табл. 10.1 и [7]; Н – коэффициент, учитывающий различную несущую способность конических и цилиндрических прямозубых колёс; для прямозубых конических колёс Н = F = 0,85; для колёс с круговыми зубьями определяют по табл. 15.1.
|
|
|
Таблица 15.1 |
|
Поправочные коэффициенты |
|
|
|
|
|
|
Коэффициент |
Стали I группы |
Стали II группы |
Стали III группы |
|
|
|
|
Н |
1,22 + 0,21u |
0,81 + 0,15u |
1,13 + 0,13u |
F |
0,94 + 0,08u |
0,65 + 0,11u |
0,85 + 0,043u |
При расчёте передачи назначают число зубьев шестерни z1 = = 18...32, число зубьев колеса рассчитывают по формуле
z zu.
2 1
Внешние делительные диаметры
de1 = mte z1; de2 = mte z2.
Внешнее конусное расстояние
R |
de2 |
1 |
1 |
. |
2 |
|
|||
e |
|
u2 |
Ширину венца определяют по формуле
b 0,285Re .
Угол при вершине делительного конуса шестерни
1 arctg z1 / z2 .
(15.10)
(15.11)
(15.12)
(15.13)
(15.14)
147
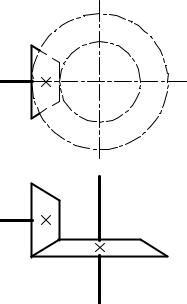
Угол при вершине делительного конуса колеса |
|
|||
2 90 1. |
(15.15) |
|||
Средний торцовый модуль |
|
|
|
|
mtm mte b sin 1 / z1. |
(15.16) |
|||
Среднее конусное расстояние |
|
|||
Rm Re 0,5b. |
(15.17) |
|||
Средние делительные диаметры |
|
|||
dm1 mtm z1; |
dm2 mtm z2. |
(15.18) |
||
Окружное усилие |
2T1 |
|
|
|
F |
. |
(15.19) |
||
|
||||
t |
dm1 |
|
Радиальное усилие на шестерне, равное осевому усилию на колесе:
Fr1= Fa2 = Ft tg · cos 1. |
(15.20) |
Осевое усилие на шестерне, равное радиальному усилию на колесе:
Fa1= Fr2 = Ft tg · sin 1. |
(15.21) |
Пример 15.5. Рассчитать и округлить по стандарту внешний делительный диаметр конического ко-
леса. Вычертить кинематическую схему передачи.
Исходные данные: мощность на валу шестерни Р1 = 14 кВт; частоты вращения валов n1 = 960 об/мин, n2 =
=420 об/мин; окружная скорость v =
=8 м/с; допускаемое контактное на-
пряжение [ Н] = 600 МПа; угол наклона = 35º.
Решение.
Кинематическая схема передачи
(рис. 15.5).
Рис. 15.5. Кинематическая схема конической передачи
148
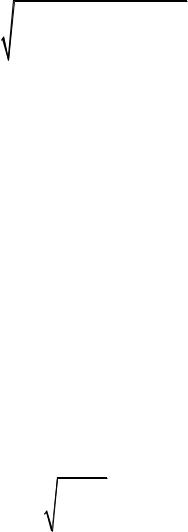
Передаточное число u = n1 / n2 = 960 / 420 = 2,29. Мощность на валу колеса Р2 = Р1η, где η – КПД зубчатой передачи; η = 0,96 (прил. М).
Р2 = 14 · 0,96 = 13,44 кВт.
Вращающий момент на валу колеса
Т2 = 9 550Р2 /n2 = 9 550·13,44 / 420= 306 Н·м = 306 Н·мм.
Принята 8-я степень точности колёс. Приняты коэффициенты: KH – концентрации нагрузки; для консольного расположения
колёс относительно опор KH = 1,3 [7]; KHv – динамической на-
грузки; при v = 5…10 м/с и 8-й степени точности KHv = 1,5 [7]. Коэффициент нагрузки KH = KHβ KHv = 1,3·1,5 = 1,95. Для сталей III
группы коэффициент Н = 0,81 + 0,15u = 0,81 + 0,15·2,29 = 1,15.
Внешний делительный диаметр колеса из расчёта на контактную выносливость
de2 |
|
2,29 306 |
103 1,95 |
мм. |
|
165 3 |
|
|
246 |
||
|
|
||||
|
6002 |
1,15 |
|
Ответ. Принято de2 = 250 мм по ГОСТ 2185 (табл. 10.2).
Пример 15.6. Рассчитать геометрические параметры ко-
нической прямозубой зубчатой передачи: средний модуль mtm, число зубьев колеса z2, ширину венца b, углы при вершинах конусов 1 и 2, диаметры делительные: средние – dm1 и dm2 и внешние – de1 и de2. Привести чертёж передачи.
Исходные данные: внешний окружной модуль mte = 5 мм, передаточное число u = 3; число зубьев шестерни z1 = 25.
Решение.
Чертёж передачи (рис. 15.6). Число зубьев колеса
z2 25 3 75.
Внешние делительные диаметры:
de1 = 5·25 = 125 мм; de2 = 5·75 = 375 мм.
Внешнее конусное расстояние
R |
375 |
1 |
1 |
197,64 мм. |
2 |
|
|||
e |
32 |
|
149
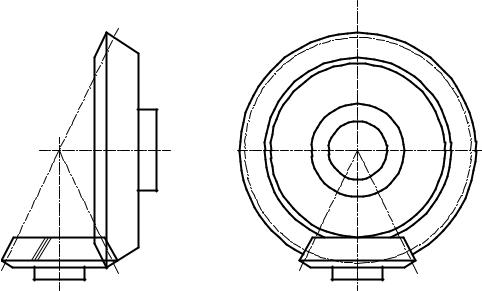
Рис. 15.6. Чертёж конической передачи
Ширина венца b 0,285 197,64 56,3 мм. Принято b = 56 мм по ГОСТ 6636 (прил. И). Угол при вершине делительного конуса шестерни
1 arctg 25/75 18,43 18 26.
Угол при вершине делительного конуса колеса
2 90 18,43 71,57 71 34 .
Средний торцовый модуль
mtm 3 56 sin18,43 / 25 2,29 мм.
Среднее конусное расстояние
Rm 197,64 0,5 56 169,64 мм.
Средние делительные диаметры:
dm1 2,29 25 57,25 мм; |
dm2 2,29 75 171,73 мм. |
Пример 15.7. Определить усилия в зацеплении конической зубчатой передачи. Показать усилия на эскизе зацепления. Угол зацепления w = 20 .
Исходные данные: мощность на валу шестерни Р1 = 13 кВт; частота вращения шестерни n1 = 350 об/мин, передаточное число u = 2,8; средний делительный диаметр шестерни dm1 = 85 мм; угол наклона = 0º.
150