
669
.pdf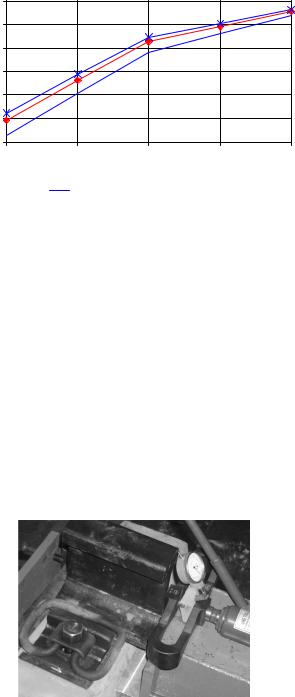
|
100 |
|
|
|
|
|
95 |
|
|
|
|
% |
90 |
|
|
|
|
Вероятность, |
|
|
|
|
|
85 |
|
|
|
|
|
80 |
|
|
|
|
|
|
|
|
|
|
|
|
75 |
|
|
|
|
|
70 |
|
|
|
|
|
4 |
5 |
6 |
7 |
8 |
|
|
|
Монтажный допуск, мм |
|
|
КБ-65 КН-65
ЖБР-65
Рис. 3.16. Вероятность получения ширины колеи
впределах монтажного допуска
3.9.Стабильность прижатия рельсов к шпалам
Одним из основных требований текущего содержания бесстыкового пути, является предотвращение продольного перемещения рельсовых плетей. Для недопущения продольного перемещения плетей под воздействием динамических и температурных нагрузок необходимо обеспечить погонное сопротивление — 25–30 кН/м.
Требуемое сопротивление смещению плетей бесстыкового пути создается при величине прижатия рельса к основанию не менее 20–25 кН.
Прижатие с таким усилием осуществляется установкой затяжки с крутящим моментом 150 Н·м и 120 Н·м для клеммных и закладных болтов соответственно.
В соответствии с ТУ-2000 [32], для обеспечения запаса усилия прижатия затяжку гаек необходимо производить с крутящим моментом 200 Н·м и 150 Н·м соответственно для клеммных и закладных болтов. Во избежания угона плетей средний крутящий момент затяжки клеммных болтов должен быть не менее 100 Н·м, закладных — 70 Н·м.
Испытания на продольный сдвиг
Для определения погонных сопротивлений продольному сдвигу рельсов проведены специальные эксперименты.
Лабораторные эксперименты выполнялись на специальном стенде (рис. 3.17).
Рис. 3.17. Стендовые испытания скрепления КН-65 ШД на продольный сдвиг
Таблица 3.16
Характеристика скреплений по силе сдвига рельса в узле скрепления
Тип |
|
|
Сила сдвига, кН |
|
|
|
|
при затяжке прикрепителей, моментом Н·м |
|
||||
скрепления |
|
|
||||
50 |
10,0 |
150 |
200 |
220 |
||
|
||||||
КБ-65 |
6,5 |
14,3 |
21,3 |
26,4 |
– |
|
КН-65 |
9,0 |
13,7 |
18,5 |
19,2 |
– |
|
КНУ-65 |
100 |
15,1 |
17,5 |
20,3 |
– |
|
КН-65 ШД |
9,0 |
13,6 |
17,7 |
19,4 |
19,7 |
Результаты экспериментов (табл. 3.16, рис. 3.18) показали, что при затяжке прикрепителей всех испытуемых скреплений моментом 150 Н·м погонное сопротивление продольному сдвигу рельса превышает 30 кН/м, что соответствует требованиям ТУ-2000 [32].
93
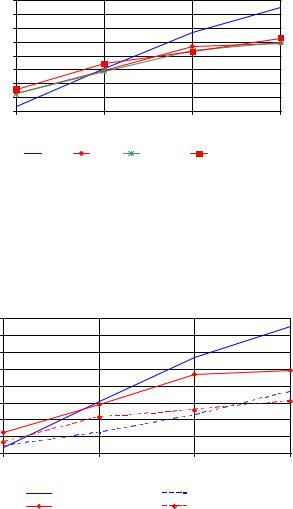
кН/м |
50 |
|
|
|
|
45 |
|
|
|
||
сопротивление, |
|
|
|
||
40 |
|
|
|
||
35 |
|
|
|
||
30 |
|
|
|
||
25 |
|
|
|
||
20 |
|
|
|
||
Погонное |
|
|
|
||
15 |
|
|
|
||
10 |
|
|
|
||
50 |
100 |
150 |
200 |
||
|
|||||
|
|
Момент затяжки прикрепителей, Н м |
|||
|
КБ-65 |
КН-65 |
КН-65 ШД |
КНУ-65 |
Рис. 3.18. Влияние момента затяжки болтов на погонное сопротивление
Испытания также показали, что уровень погонного сопротивления в значительной степени определяется качеством содержания и выполнения периодической смазки болтов. Так, для скрепления КБ-65 погонное сопротивление при смазанных болтах в среднем увеличивается в 1,5 раза, а для скрепления КН-65 — в 1,3 раза (рис. 3.19).
Расчетное погонное сопротивление продольному сдвигу рельса в узле скрепления КБ-65
r = 260Mк, |
(3.51) |
где Mк — крутящий момент, прикладываемый к гайкам клеммных болтов, Н·м.
50 |
|
|
|
кН/м |
|
|
|
45 |
|
|
|
40 |
|
|
|
35 |
|
|
|
30 |
|
|
|
сопротивление, 25 |
|
|
|
20 |
|
|
|
15 |
|
|
|
Погонное |
|
|
|
10 |
|
|
|
50 |
100 |
150 |
200 |
|
Момент затяжки болтов, Н м |
|
|
|
КБ-65 (болты смазаны) |
КБ-65 |
|
|
КН-65 (болты смазаны) |
КН-65 |
|
|
Рис. 3.19. Влияние условий эксплуатации скреплений |
|
|
|
на надежность бесстыкового пути |
|
Жесткость упругих элементов прикрепителей
В обеспечении оптимальной температурной работы рельсовых плетей и сохранении параметров рельсовой колеи определяющую роль играет стабильность монтажного натяжения прикрепителей скреплений.
Стабильность натяжения в свою очередь зависит от упругих деформаций клемм в рабочем диапазоне монтажного натяжения прикрепителей.
При статических испытаниях клемм в СГУПСе определялись деформации ветвей клеммы при приложении нагрузки по оси закладного болта; жесткость клемм по месту приложения нагрузки и остаточные деформации после снятия нагрузки [39].
Исследованиям подверглись: 10 клемм скрепления КН-65, изготовленных на Горновском заводе спецжелезобетона, по размерам и твердости соответствующих требованиям технической документации на их изготовление, диаметр прутка — 17 мм, сталь 60С2А; 10 клемм ОП-105 диаметром 13 мм для скрепления КБ-65 производства Магнитогорского калибровочного завода, сталь 60С2А.
Графики средних значений перемещений вышеперечисленных пружинных элементов представлены на рис. 3.20. Параметры жесткости упругих элементов скреплений в рабочих интервалах нагрузки приведены в табл. 3.17.
94
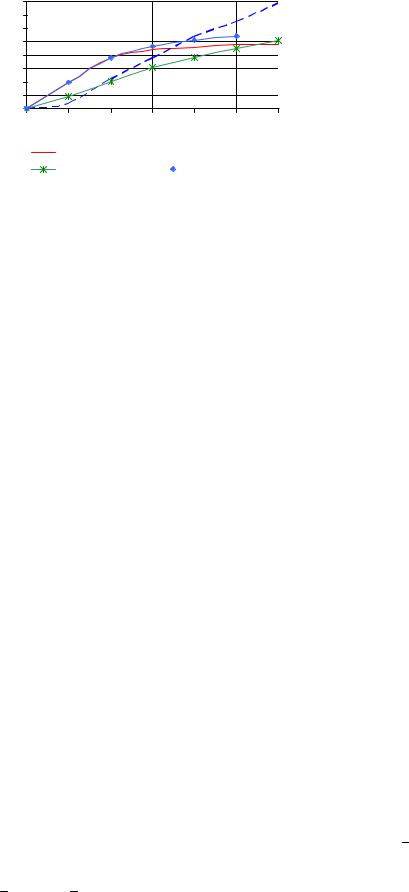
|
8 |
|
|
|
|
|
|
мм |
7 |
|
|
|
|
|
|
6 |
|
|
|
|
|
|
|
Перемещение, |
5 |
|
|
|
|
|
|
4 |
|
|
|
|
|
|
|
3 |
|
|
|
|
|
|
|
2 |
|
|
|
|
|
|
|
1 |
|
|
|
|
|
|
|
0 |
|
|
|
|
|
|
|
|
|
|
|
|
|
|
|
|
0 |
5 |
10 |
15 |
20 |
25 |
30 |
|
|
|
|
Нагрузка, кН |
|
|
|
Двухвитковая шайба |
|
|
|
|
ОП-105 |
|
|
|
|||||
ЖБР-3 |
|
|
|
|
|
КН-65 |
|
|
|
|
|
Рис. 3.20. Средние деформации пружинных элементов под нагрузкой, приложенной по оси болта
Анализ графиков рис. 3.20 показывает, что упругая деформация клемм и шайб по оси болтов под нагрузкой 25 кН для двухвитковых шайб КБ-65 и клемм ЖБР-3 составляет 4,7 мм, для клеммы КН-65 — 5,5 мм и для клеммы ОП-105 — 6,5 мм.
Это недостаточно для обеспечения стабильного натяжения прикрепителей.
Анализ данных табл. 3.17 показывает, что в рабочем диапазоне загружения упругих элементов скреплений наибольшей жесткостью обладает двухвитковые шайбы скрепления КБ-65, а наименьшей клеммы ОП105 этого же скрепления. Этим объясняется интенсивное ослабление натяжения клеммных болтов скрепления КБ-65 с типовой двухвитковой шайбой при полигонных испытаниях (табл. 3.18).
Таблица 3.17
Жесткость упругих элементов скреплений, кН/мм
Интервал |
|
|
|
|
Упругие элементы скреплений |
|
|
|
|
|
||||||
нагружения, |
|
двухвитковые |
|
клеммы |
|
клеммы |
|
клеммы |
|
|||||||
кН |
|
шайбы КБ-65 |
|
ОП-105, КБ-65 |
|
ЖБР-3 |
|
|
КН-65 |
|
||||||
0-25 |
|
5,2 |
|
|
|
3,8 |
5,6 |
|
|
|
4,6 |
|
||||
10-25 |
|
15,6 |
|
|
|
3,5 |
6,1 |
|
|
|
9,0 |
|
||||
|
|
|
|
|
|
|
|
|
|
|
|
|
|
|
|
Таблица 3.18 |
|
Изменение затяжки болтов различных типов скреплений |
|
|
|
||||||||||||
|
|
|
|
|
|
|
|
|
|
|
|
|
|
|
|
|
Параметры затяжки |
|
|
|
|
|
Тип скрепления |
|
|
|
|
|
|||||
|
|
|
|
|
|
|
ЖБР- |
|
|
|
|
|
|
|||
болтов |
|
АРС-4 |
|
КБ-65 |
|
ЖБР-65 |
|
|
КН-65 |
|
КНУ-65 |
|
||||
|
|
|
|
65П |
|
|
|
|||||||||
|
|
|
|
|
|
|
|
|
|
|
|
|
|
|
|
|
Начальный момент за- |
|
90-115 |
|
150 |
|
150 |
|
150 |
|
180 |
|
180 |
|
|||
тяжки болтов |
М0, Н·м |
|
|
|
|
|
|
|
||||||||
|
|
|
|
|
|
|
|
|
|
|
|
|
|
|||
Момент после наработки |
|
75-100 |
|
90 |
|
130 |
|
140 |
|
152,7 |
|
170 |
|
|||
тоннажа 100 млн т, Н·м |
|
|
|
|
|
|
|
|||||||||
|
|
|
|
|
|
|
|
|
|
|
|
|
|
|||
Снижение момента за- |
|
15 |
|
60 |
|
20 |
|
10 |
|
27,3 |
|
10 |
|
|||
тяжки болтов |
М, Н·м |
|
|
|
|
|
|
|
||||||||
|
|
|
|
|
|
|
|
|
|
|
|
|
|
|||
Интенсивность снижения |
|
|
|
|
|
|
|
|
|
|
|
|
|
|
||
момента затяжки болтов, |
|
0,15 |
|
0,60 |
|
0,20 |
|
0,10 |
|
0,27 |
|
0,10 |
|
|||
Н·м/млн т бр. |
|
|
|
|
|
|
|
|
|
|
|
|
|
|
|
|
3.10. Сравнение качества скреплений по интегральным критериям
Выбор интегральных параметров рельсовых скреплений на стадии проектирования или модернизации является сложной задачей. Имеющиеся ограничения на ряд параметров и наличие неоднозначных связей между ними и показателями динамических качеств приводят к процедуре отыскания некоторых компромиссных значений этих параметров. Определение оптимальных величин указанных параметров может быть выполнено с помощью различных методов. Следует, однако, иметь в виду, что при выборе оптимальных параметров рельсовых скреплений необходимо учитывать ряд параметрических и функциональных ограничений, определяющих границы изменения как оптимизируемых параметров, так и вспомогательных критериев оптимизации (табл. 3.19).
Оптимальные значения параметров сообщают некоторой целевой функции минимальное значение.
Если оптимизируемая система имеет несколько частных независимых критериев, то многокритериальную задачу часто сводят к однокритериальной путем введения обобщающего критерия. Используя принцип
справедливой абсолютной уступки [65], можно составить аддитивный критерий оптимальности F(x) в виде взвешенной суммы нормированных частных критериев
m |
|
F(x) = ∑λiUi (x) , |
(3.52) |
i=1
95

где Ui (x) — нормированный частный критерий данной системы; λi — весовой коэффициент i-го критерия; m
— число частных критериев.
96
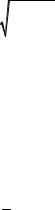
Таблица 3.19
Показатели надежности и эффективности рельсовых скреплений
Критерии эффективности |
Диапазон изменения кри- |
|
Тип скреплений |
|
|||
териев |
КБ |
ЖБР |
АРС |
КН |
КНУ |
||
|
|||||||
1. Надежность, доли |
|
|
|
|
|
||
1.1. Надежность узла скрепления |
|
|
|
|
|
|
|
|
0,8…1 |
0,69 |
0,55 |
0,1 |
0,65 |
0,9 |
|
1.2. Наименьшая надежность элементов |
|
|
|
|
|
|
|
|
0,8…1 |
0,8 |
0,85 |
0,1 |
0,85 |
0,99 |
|
1.3. Сохранность при сходе колес с рельсов |
|
|
|
|
|
|
|
|
0,6…0,9 |
0,9 |
0,7 |
0,5 |
0,8 |
0,8 |
|
2. Стабильность параметров |
|
|
|
|
|
||
2.1. Точность сборки рельсошпальной решетки, проценты |
|
|
|
|
|
|
|
|
0,9…1 |
0,855 |
0,909 |
0,972 |
0,86 |
0,90 |
|
2.2. Стабильность сохранения ширины колеи (уширение), |
|
|
|
|
|
|
|
мм/100 млн т бр. |
|
|
|
|
|
|
|
|
0…8 |
13 |
12 |
6 |
2 |
5 |
|
2.3. Стабильность натяжения прикрепителей (ослабление), |
|
|
|
|
|
|
|
Н·м/млн т бр. |
|
|
|
|
|
|
|
|
10…25 |
60 |
20 |
15 |
27 |
10 |
|
3. Пространственная жесткость, кН/мм |
|
|
|
|
|
||
3.1. Вертикальная |
40…80 |
40 |
37 |
37 |
56 |
60 |
|
3.2. Горизонтальная по головке рельса |
|
|
|
|
|
|
|
|
20…40 |
20 |
30 |
12 |
30 |
26 |
|
3.3. Горизонтальная по подошве рельса |
|
|
|
|
|
|
|
|
40…60 |
20 |
70 |
346 |
38 |
40 |
|
3.4. Жесткость клеммы (духвитковой шайбы) в диапазоне 10-25 |
|
|
|
|
|
|
|
кН |
|
|
|
|
|
|
|
|
4…9 |
15 |
6 |
6 |
9 |
8 |
|
4. Технологичность |
|
|
|
|
|
||
4.1. Технологичность при |
|
|
|
|
|
|
|
изготовлении, баллы |
1…5 |
3 |
3 |
2 |
4 |
4 |
|
4.2. Технологичность при сборке рельсошпальной решетки, |
|
|
|
|
|
|
|
баллы |
|
|
|
|
|
|
|
|
1…5 |
4 |
2 |
5 |
4 |
4 |
|
4.3. Технологичность при смене рельсов и разрядке напряжений, |
|
|
|
|
|
|
|
баллы |
|
|
|
|
|
|
|
|
1…5 |
4 |
2 |
3 |
5 |
5 |
|
4.4. Регулировка рельсов по высоте, мм |
|
|
|
|
|
|
|
|
1…5 |
4 |
3 |
5 |
4 |
5 |
|
5. Экономическая эффективность |
|
|
|
|
|
||
5.1. Экономическая эффективность за межремонтный период, |
|
|
|
|
|
|
|
баллы |
|
|
|
|
|
|
|
|
1…5 |
1 |
3 |
3 |
3 |
4 |
Различная значимость частных критериев учитывается с помощью весовых коэффициентов или коэффициентов
m
важности λi, причем ∑λi = 1 .
i=1
Обоснованное определение λi сталкивается с серьезными трудностями и обычно сводится к экспертной оценке λi [66, 67].
Дальнейшая оптимизация параметров рельсовых скреплений производится на основе отыскания паретовского (по имени В. Парето) множества решений и ранжирования его по критерию суммарных допустимых потерь [68, 69]
|
|
1 |
m |
|
|
Fj |
= |
∑Uɶi2 , |
(3.53) |
||
|
|||||
|
|
m i=1 |
|
где Uɶi — приведенные значения i-го частного критерия в j-й эффективной или паретовской точке;
U −U*
ɶ |
= |
|
i |
i |
|
|
Ui |
U |
** −U |
* |
, |
||
|
|
|
i |
|
i |
|
Ui* = minUi и Ui** = maxUi — минимально и максимально допустимые значения i-го частного критерия; для нормированных критериев Ui** = [Ui ] , здесь [Ui ] — допустимые по нормам значения соответствующего
частного критерия; m — количество частных критериев оптимизации.
При оптимизации параметров рельсовых скреплений задача сводится к выбору n таких значений xi (i = 1, 2,…, n) параметров, которые должны обеспечить минимум всех частных критериев оптимизации.
При этом целевая функция F(x) будет векторной
97
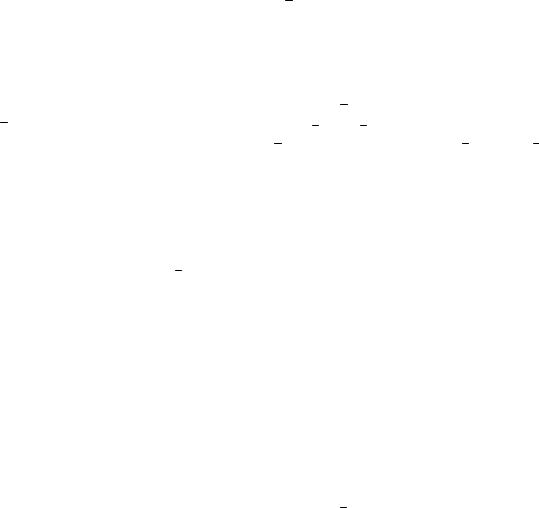
F( |
|
|
|
|
|
[Ui ( |
|
|
|
)], |
|
|
|
) = F |
|
),...,Um ( |
|
(3.54) |
|||||
x |
x |
x |
|||||||||
минимизация которой заключается в определении |
|
||||||||||
Ui ( |
|
) → min,i = 1,2,...,m , |
|
||||||||
x |
|
||||||||||
|
|
|
|
|
|
x D |
|
где D — множество допустимых значений переменной x = (x1...xn ) , определяемой в общем случае системой равенств и неравенств.
h |
|
( |
|
|
) = 0, j =1,...,l |
|
j |
x |
|||||
|
|
|
|
|
|
|
D: |
|
|
|
|
|
|
g j |
(x) ≥ 0, j = l +1,..., p. |
|||||
|
|
|
|
|
|
|
Решение многокритериальной задачи, вообще говоря, неоднозначно и лежит на так называемом переговорном множестве Парето [69]. Считается, что точка с координатами X / безусловно лучше, чем точка с координатами X , если при всех i = 1, 2, …, m выполняется условие Ui (x/ ) ≤ Ui (x) и хотя бы при одном значении i имеет
место строгое равенство. Если же не существует точки X / D , безусловно лучшей, чем X , то точка X называется эффективной или паретовской, а также нехудшей точкой. Нахождение множества Парето при значительном числе критериев представляет собой сложную задачу.
Для получения однозначного решения свертка частных критериев Ui (x) на полученном паретовском множестве производится с помощью критерия суммарных допустимых потерь в соответствии с (3.52) или (3.54).
Ранжируя точки в порядке возрастания Fj , на каждом этапе оптимизации выделим на паретовском множестве подмножество лучших (в смысле Fj → min) решений. После этого переходим к однокритериальной опти-
мизации по основным критериям U j (x) ( i = 1,…, mi), где mi — количество основных критериев c использова-
нием целевой функции (3.54) и зависимости (3.52).
Результаты многокритериальной оптимизации, где паретовские решения определены как частные критерии оптимизации по пяти параметрам для пяти рельсовых скреплений (табл. 3.20).
Таблица 3.20
Результаты оптимизации параметров рельсовых скреплений
|
Параметры |
Паретовские решения (частные критерии) для скреплений |
||||||
|
КБ |
ЖБР |
АРС |
КН |
КНУ |
|||
|
|
|
|
|||||
1. |
Надежность |
0,33 |
0,24 |
0 |
0,41 |
0,73 |
||
2. Стабильность |
0 |
0,20 |
0,63 |
0,50 |
0,62 |
|||
3. |
Пространственная жесткость |
0,50 |
0,58 |
0,30 |
0,68 |
0,67 |
||
4. |
Технологичность |
0,70 |
0,40 |
0,76 |
0,82 |
0,88 |
||
5. |
Экономическая эффективность |
|
|
|
|
|
||
|
|
|
|
0 |
0,50 |
0,50 |
0,50 |
0,75 |
|
Целевая функция F( |
|
) |
|
|
|
|
|
|
x |
0,31 |
0,38 |
0,43 |
0,58 |
0,73 |
Анализ частных критериев, входящих в целевую функцию F(x), показывает, что по стабильности сохра-
нения параметров рельсовой колеи лучшими оказались скрепления АРС и КНУ, а по показателям надежности лучшими оказались скрепления КНУ и КН.
Пространственная жесткость узла скрепления характеризуется многими неоднозначными показателями. Паретовские решения показали примерно одинаковые частные критерии для всех скреплений за исключением КБ. Для этого скрепления неприемлема высокая горизонтальная жесткость по подошве рельса. Это один из главных недостатков скрепления АРС.
По технологичности изготовления, монтажа, эксплуатации лучшими оказались скрепления КНУ и КН. Низкую экономическую эффективность имеют все скрепления за исключением КНУ. Связано это с низ-
кой надежностью элементов, требующих частых замен в процессе эксплуатации.
Анализ существующих промежуточных рельсовых скреплений с упругими клеммами показал основные тенденции в развитии этих элементов конструкции пути (рис. 3.21).
Наиболее перспективными скреплениями на сегодняшний день являются КН-65, КНУ-65 и АРС после доработки изоляции рельса от шпалы.
Одним из основных критериев при выборе упругого рельсового скрепления для применения в составе бесстыковой конструкции является надежность как отдельных элементов, так и всей конструкции в целом.
Критерию надежности в наибольшей степени отвечают скрепления подкладочного типа, в частности скрепление КН-65 и КНУ-65.
98
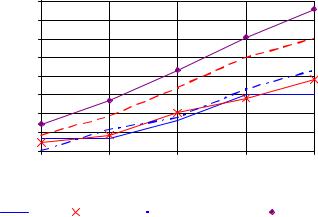
параметрам |
4 |
|
|
|
|
3,5 |
|
|
|
|
|
3 |
|
|
|
|
|
2,5 |
|
|
|
|
|
по |
|
|
|
|
|
|
|
|
|
|
|
критериев |
2 |
|
|
|
|
1,5 |
|
|
|
|
|
1 |
|
|
|
|
|
Сумма |
|
|
|
|
|
0,5 |
|
|
|
|
|
0 |
|
|
|
|
|
|
|
|
|
|
|
|
1 |
2 |
3 |
4 |
5 |
|
|
|
Параметры оптимизации |
|
|
|
|
|
для скреплений типа |
|
|
КБ-65 |
|
ЖБР-65 |
|
|
|
АРС-4 |
|
|
|
КН-65 |
|
КНУ-65 |
|
|
|
|
|
|
Рис. 3.21. Сравнение критериев оптимизации рельсовых скреплений
3.11.Перспективы совершенствования
ииспользования скреплений
Типовое скрепление КБ-65 ненадежно в кривых участках, что связано с недостаточной прочностью боковых упоров и как следствие значительными смещениями рельса и отказами при этом резиновых прокладок, закладных болтов и изолирующих втулок, а также с интенсивным снижением затяжки клеммных болтов [63].
Текущее содержание пути на участке КБ-65 заключается в исправлении ширины колеи по шаблону заменой дефектных нашпальных прокладок. Кроме того, периодически подтягиваются клеммные и закладные болты. Участок пути с этим скреплением самый сложный в эксплуатации.
Вместе с тем скрепление КБ-65 используется более 50 лет; обеспечивает стабильность подуклонки рельсов; допускает регулировку положения рельсовых нитей по высоте до 14 мм укладкой подрельсовых прокладок; допускает возможность восстанавливать путь в случае схода колеса с рельса.
Резервами увеличения надежности КБ-65 являются применение прокладок амортизаторов с повышенной износостойкостью из армированной резины или полимерных материалов и прутковых клемм вместо жестких клемм ПК с двухвитковыми шайбами.
ЖБР-65 с металлическими упорными скобами и упругими прокладками. В крутых кривых неустойчива ширина колеи. После наработки примерно 100 млн т бр. максимальная ее ширина на ЭК ВНИИЖТа в кривой радиусом 400 м составляла 1544 мм. Основная причина расстройства — износ наружных подклеммных упругих прокладок на обеих рельсовых нитях. Эти отказы приводят к тому, что повреждаются железобетонные шпалы из-за скола кромки бетона в местах контакта с металлическими упорными скобами (до 40 % в кривых малого радиуса) [40].
Кроме того, на Экспериментальном кольце отмечены массовые сползания клемм с подошвы рельсов во время наработки от 400 до 600 млн т груза. Последнее также связано с износом подклеммных прокладок. Помимо этого пришлось заменить 136 % подрельсовых прокладок ЦП-204.
При текущем содержании пути на участке с типовым скреплением ЖБР-65 довинчивают гайки закладных болтов, исправляют ширину колеи по шаблону, заменяя износившиеся упругие прокладки, сползшие клеммы возвращают в исходное положение.
ЖБР-65 с боковыми полимерными упорами. На кольце после наработки 188 млн т груза на участке с ЖБР-65 применили новое конструктивное решение — установили боковые полимерные упоры ЦП-369.006. Два упора весом по 260 г в узле надежно замещают четыре детали — две металлические скобы по 1440 г и две упругие прокладки по 100 г. Ширина колеи стала более устойчивой. В период пропуска от 190 до 500 млн т груза среднее уширение составило 5,8 мм, в то время как на звене с металлическими упорными скобами и упругими прокладками достигло 20 мм.
Надежность работы этой модификации скрепления ЖБР тоже зависит от усилия затяжки гаек болтов, также сползают клеммы с подошвы рельса при недостаточной затяжке болтов, также неудобно заменять инвентарные рельсы на бесстыковые плети.
ЖБР-65П. Скрепление испытывается на тех же старогодных шпалах, что и типовое бесподкладочное ЖБР-
65.До наработки 300 млн т бр. груза вышло из строя 2 % клемм. Отказов других элементов не было.
При неблагоприятном сочетании размеров из принятых полей допусков на геометрию подрельсовой
площадки шпалы и профиля подкладки возникают затруднения во время установки последней и ее неплотное прилегание к шпале (не собирается до 5 % узлов скреплений). Болтовой вариант скрепления отличается сложностью монтажа и замены элементов.
У скрепления АРС-4 самый слабый элемент — наружный изолирующий уголок. Изломы и износы этих уголков приводят к уширению рельсовой колеи до 1545 мм. За весь период испытаний на кольце ее регулировали семь раз, сплошь заменяя уголки: после наработки тоннажа 45–50 млн т бр.
99
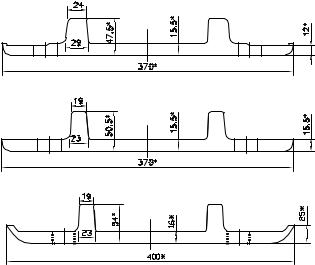
Основные трудности при текущем содержании пути на участке с АРС-4 заключаются в исправлении ширины рельсовой колеи по шаблону и установке сползших клемм в нормальное положение с обязательной заменой износившихся наружных изолирующих уголков новыми.
Скрепление практически не поддается ремонту после схода колеса с рельса.
Следует отметить, что при испытаниях в АпАТэК упругое кантование головки рельса составило 4,25 мм, что в несколько раз превышает аналогичный показатель у других видов скреплений. В узле скрепления прижимной виток наружной клеммы практически не отслеживает вертикального перемещения подошвы рельса, а неподвижно лежит на полке изолирующего уголка, опирающегося вертикальной стенкой на поверхность шпалы и прижатого к анкеру подошвой рельса, т.е. скрепление конструктивно недоработано.
С конца 2006 г. на кольце ВНИИЖТа испытывают скрепление АРС с усовершенствованными элементами, в том числе изолирующие уголки изготавливают из капролона с защитной полкой и выступом, стабилизирующим положение клеммы. Применены подрельсовые прокладки ЦП 204М-АРС из материала ТПК-5, облегченные на 9–18 % анкера (наиболее дорогостоящий элемент) [64].
Результаты обследования показали, что после наработки 113 млн т бр. скрепление с усовершенствованными элементами работало лучше. Так, уширение колеи оказалось практически вдвое меньше. Снизилось количество отказов клемм (в 4 раза) и изолирующих уголков снаружи колеи в 2,5 раз.
Однако очередная модернизация скрепления АРС не привела к существенному повышению его надежности (рис. 3.13, б). После наработки 200 млн т груза отказало 25 % изолирующих уголков их замена требует больших затрат ручного труда.
Подкладочное скрепление КН хорошо зарекомендовало себя при полигонных и эксплуатационных испытаниях на прямых участках пути. Поэтому решили проверить, как оно работает в кривой радиусом 400 м.
Скрепление обеспечивает устойчивость ширины рельсовой колеи в крутой кривой. За весь период испытаний среднее уширение составило 6,0 мм.
КНУ-65 — это улучшенный вариант скрепления КН-65 для кривых участков пути.
После наработки 600 млн т бр. груза среднее уширение колеи составило 5,8 мм. Это лучший показатель среди всех сравниваемых скреплений.
За период испытаний изломалась одна (1 %) клемма. Вышли из строя пять (5 %) пристыковых подкладок (один излом и четыре трещины) по краям отверстий вдоль реборд. Зафиксирован один отказ железобетонной шпалы. Все нашпальные резинокордовые прокладки, изготовленные ОАО «Союзспецмаш», работали очень хорошо.
Дальнейшая модернизация скреплений КН-65 заключается в совершенствовании формы металлической подкладки, а также в коренном совершенствовании скрепления — разработки перспективного скрепления КНУ-65, шурупно-дюбельных вариантов КН-65 ШД.
Модернизация подкладки КН включает (рис. 3.22):
–утоньшение толщины реборд подкладки с 24 мм до 19 мм (меньший размер реборд сложен для металлургического изготовление) по верхней площадке для удешевления конструкции за счет металлоемкости.
–увеличение высоты реборд подкладки с 32 мм до 35 мм для уменьшения трудозатрат и облегчения выправочных работ при текущем содержании.
–толщина подкладки оптимизируется — в зоне размещения прикрепителей толщина увеличивается с 12 мм до 15,5 мм, для удаления имевшейся ступеньки и соответственно исключении концентратора напряжений.
а)
б)
в)
Рис. 3.22. Подкладки скреплений:
а — КН-65; б — КН-65 (модернизированная); в — КНУ-65
100
Дальнейшая модернизация подкладки КН требует серьезного изменения прокатных валков, что по существу является переходом на новый прокат. Потребуется также некоторая переделка форм для изготовления шпал, так как подрельсовый лоток шпалы скрепления КНУ-65 шире на 40 мм и глубже на 10 мм.
Скрепление КНУ-65 предназначено для укладки в кривых радиусом менее 650 м.
Трехлетний опыт эксплуатации опытных образцов скреплений КН-65 ШД (с шурупно-дюбельным прикреплением) на станции Издревая Западно-Сибирской железной дороги дал положительные результаты: отказов элементов скреплений нет, рельсовая колея стабильна.
Таким образом, материалы исследований рельсовых скреплений для железобетонных шпал позволяют сделать следующие выводы:
1.Все эксплуатирующиеся в настоящее время конструкции рельсовых скреплений для железобетонных шпал требуют существенной доработки модернизации.
2.Для кривых участков пути радиусом менее 650 м и участков с высокой грузонапряженностью в российских условиях можно применять только подкладочные скрепления.
3.Для существенного повышения надежности и экономической эффективности бесстыкового пути на железобетонных шпалах в узлах скреплений нужно применять резиновые прокладки, армированные полимерными волокнами.
4.ОБЕСПЕЧЕНИЕ НАДЕЖНОСТИ ПОДРЕЛЬСОВОГО ОСНОВАНИЯ
4.1. Общие положения
Надежность железнодорожного пути во многом определяется надежностью подрельсового основания, от исправной работы который зависит бесперебойность и безопасность движения поездов. Ненадежность связей рельсов со шпалами приводит к нарушению ширины колеи и угону пути, а шпал с балластом — к накоплению остаточных продольных и поперечных смещений всей рельсошпальной решетки. Ликвидация последствий отказов горизонтальных связей требует выполнения сложных и трудоемких работ по регулировке ширины колеи, рихтовке пути и регулировке зазоров. Отказы связей часто происходят на участках с мощным верхним строением пути, имеющим небольшой наработанный тоннаж.
За последние годы выполнен ряд исследований, касающихся надежности железнодорожного пути [70–72]. Однако решены далеко еще не все вопросы обеспечения надежности связей рельсов с основанием. Решение задачи создания конструкций верхнего строения пути, имеющих необходимую надежность связей рельсов с основанием, требует нового методологического подхода. Такой подход может быть основан на теории надежности, теории взаимодействия пути и подвижного состава, теории взаимодействия элементов рельсошпальной решетки под поездной нагрузкой, учете экспериментальных данных и нормативных документов.
Использование физических закономерностей, описывающих старение конструкции пути и возрастание со временем силового воздействия на нее от подвижного состава, позволяет получить модели для оценки изменения безотказности связей рельсов с основанием и рассмотреть влияние основных факторов, определяющих уровень надежности пути.
Все существующие конструкции пути эксплуатируются в условиях накопления местных остаточных деформации и других повреждений практически во всех элементах: в верхней части головки рельсов, в прокладках между рельсами и шпалами, в шпалах под подкладками и в зонах их контактов со щебенками, в балластном слое и в верхней части земляного полотна. Кроме того, в процессе эксплуатации истираются (изнашиваются) контактные зоны элементов пути; ослабляются соединения рельсов со шпалами; снижается несущая способность шпал вследствие старения; образуются «выплески» и ослабление балластного слоя из-за его засорения; накапливаются расстройства пути в плане, профиле и по ширине колеи. Скорость развития всех указанных процессов нелинейно возрастает с увеличением наработки после капитального ремонта пути.
Железнодорожный путь как объект надежности имеет две характерные особенности: большую протяженность и необходимость восстановления работоспособного состояния после отказа на месте в условиях его функционирования. Путь — многоэлементный ремонтируемый и восстанавливаемый объект надежности. Он не резервирован по основному несущему элементу — рельсу — и имеет нагрузочное резервирование по элементам рельсового основания. Другими словами, отказ рельса является отказом пути в целом, а отказ какого-либо элемента рельсового основания, например шпалы, подкладки, прикрепителя, не является отказом пути, так как соседние элементы воспринимают нагрузку на себя и этим обеспечивают нагрузочное резервирование [72].
4.2. Методологические основы к оценке надежности шпал
Опыт показывает, что шпалы, эксплуатирующиеся примерно в равных условиях, при одинаковых объемах перевозок отказывают в различное время вследствие существующего разброса прочностных свойств древесины, качества обработки антисептиками, условий опирания шпал в балласте, наличия неровностей на поверхности катания рельсов, в том числе стыков. Следовательно, повреждение шпал — случайный процесс, а пропущенный тоннаж до отказа шпалы — случайная величина.
Применение модели нормального распределения обусловлено следующим: отказы шпал вызываются многими факторами, каждый из которых оказывает определенное воздействие на развитие дефектов; теоре-
101
тическое распределение должно иметь монотонно возрастающую функцию интенсивности отказов, так как известно, что с ростом наработки повышается интенсивность отказов шпал.
При обработке данных об отказах шпал необходимо учитывать, что на грузонапряженных участках продолжительность эксплуатации пути (в годах) сокращается, и можно получить данные о наработках до отказа только части шпал, т.е., как и в случае с рельсами, в нашем распоряжении есть цензурированные (ограниченные) справа выборки [71].
Исходная информация об отказах шпал собирается по ведомостям покилометрового учета замененных шпал и отчетам о наличии в пути негодных шпал. При проведении статистических экспериментов выполняется следующее условие: данные об отказах шпал собираются на участках, характеризующихся определенным набором основных признаков (грузонапряженность, нагрузки на ось, скорость движения поездов, тип верхнего строения, план и профиль пути).
Результаты статистической обработки данных об отказах шпал представляется в виде сгруппированного ряда, полученного по результатам статистического эксперимента, выполненного на одном из участков железной дороги.
При построении сгруппированного ряда весь диапазон наработки делится на интервалы. Для каждого интервала подсчитывалась частота отказов шпал r(ti) нарастающим итогом. По частоте определялось значение частости F(ti)
F(t |
) = |
r(ti ) |
, |
(4.1) |
|
||||
i |
|
Nø |
|
|
|
|
|
|
где Nш — средняя эпюра шпал.
Эмпирическая квантиль UPi находилась по частости F(ti) с использованием табулированных значении
функций F(ti) = Р.
Оценки параметров нормального распределения долговечности шпал Тср и σ определялись методом квантилей в сочетании с методом наименьших квадратов.
Прогнозирование отказов шпал производится так же, как и рельсов:
nш (tλ) = Nш F (ti), |
(4.2) |
здесь Nш — количество шпал на километре (эпюра).
4.3.Обеспечение надежности железобетонных шпал
4.3.1.Сферы применения и требования
кжелезобетонным шпалам
Существующие отечественные железобетонные шпалы достаточно надежны, чтобы обеспечивать надежность пути в целом в части, зависящей от шпал в период первой части срока своей службы, т.е. в период между смежными обновлениями (заменой) рельсошпальной решетки. По проектным данным существующие железобетонные шпалы рассчитаны на срок службы 50 лет. Сплошную смену рельсошпальной решетки на дорогах России производят в среднем через 20–25 лет.
При повторном использовании снятой рельсошпальной решетки и старогодных железобетонных шпал в отдельности возникает необходимость определения их остаточного ресурса. К сожалению, теоретически такое определение произвести невозможно, а экспериментальных данных пока недостаточно. В настоящее время практикуется использование на малодеятельных линиях и на станциях снятой старогодней рельсошпальной решетки после необходимой ее переборки и ремонта на базах ПМС. Кроме того, используются железобетонные шпалы для разрядки «кустовой» негодности деревянных шпал. Для указанных действий уже создана нормативная база Департаментом пути и сооружений ОАО «РЖД». Можно планировать только совершенствование указанной нормативной базы в части использования в локальных зонах изолированных неровностей на рельсах специальных виброзащитных железобетонных шпал.
Важнейшим резервом ресурсосбережения на дорогах России является расширение сфер применения железобетонных шпал. Железобетонные шпалы, в отличие от деревянных, не подвержены гниению. Они способны служить в малодеятельных путях с загрязненным и обводненным балластом многие десятки лет, тогда как деревянные шпалы в таких условиях сгнивают через 10–15 лет. Поэтому применение на малодеятельных линиях (в том числе на станционных путях) старогодных железобетонных шпал или новых облегченной конструкции с позиции сокращения эксплуатационных расходов чрезвычайно важно. Разработанная сейчас система использования железобетонных шпал (в том числе облегченных конструкций) для разрядки кустовой негодности деревянных шпал [73] должна повсеместно реализовываться на дорогах России. В ближайшем будущем эффект от такой реализации будет непрерывно возрастать.
Железобетонные шпалы предназначены для применения на железнодорожных путях всех классов, установленных Положением о системе ведения путевого хозяйства на железных дорогах Российской Федерации (далее — Положением) [74] в зависимости от грузонапряженности, скоростей движения поездов и плана пути.
В пути применяют как новые железобетонные шпалы первого и второго сорта, так и старогодные шпалы, повторно используемые после первого срока службы в пути [75].
На путях 1 и 2 классов следует применять новые железобетонные шпалы первого сорта.
102