
669
.pdfгде Тф — фактический срок службы деревянных шпал за тот же год.
Для приближенного расчета фактического срока службы деревянных шпал на дистанциях пути предлагается упрощенный метод расчета.
Фактический срок службы деревянных шпал рекомендуется определять по формуле
T |
= |
Ø − (Í í − 0,5Ðâ ) |
, |
(4.8) |
|
||||
ô ñð |
Ø â |
|
|
|
|
|
|
где Тф ср — средний по дистанции пути срок службы деревянных шпал, год; Ш — общее число деревянных шпал, лежащих в пути (среднее за год), тыс. шт., за исключением новых шпал, уложенных при капитальном ремонте пути за последние 5 лет); Нн — количество негодных деревянных шпал, лежащих в пути на начало года, в тыс. шт.; Рв — выход деревянных шпал в год по их расчетному сроку службы; Шв — фактический выход деревянных шпал по негодности в течение года, тыс. шт.:
Шв = Нк – Нн + Шз, |
(4.9) |
где Нк — количество негодных деревянных шпал, лежащих в пути на конец года, тыс. шт.; Шз — число замененных негодных деревянных шпал в расчетном году, тыс. штук, определяемое количеством деревянных шпал (новых и старогодных), уложенных в порядке одиночной замены при текущем содержании или ремонтах пути, и количеством негодных деревянных шпал, указанных в актах формы ПУ-81, составленных по результатам рассортировки шпал в путевой рельсошпальной решетке, снятой при капитальном или среднем ремонтах пути.
Оценка и прогнозирование надежности деревянных шпал производится по формулам (4.1 и 4.2). Наибольшую угрозу для безопасности движения поездов представляет образование кустов из трех и бо-
лее негодных шпал. В соответствии с исследованиями [71] вероятность такой ситуации определяется по зависимости
Fк (ti) = [Fш (ti)]2,73. |
(4.10) |
4.5.Оценка надежности балластного слоя
4.5.1.Требования, предъявляемые к балластному слою
Повышение нагрузок и скоростей движения поездов на железных дорогах РФ предъявляет все более высокие требования к расчету и конструированию железнодорожного пути и, в частности, к обеспечению надежности балластной призмы и верхней части земляного полотна.
Интенсивный рост грузонапряженности, осевых нагрузок и скоростей движения поездов, появление в связи с этим новых конструкций верхнего строения пути, внедрение комплексной механизации, основанной на новом принципе уплотнения щебня (вибрационном обжатии), а также стремление к обеспечению наиболее полной стабилизации пути в период «окна» вызывают необходимость соблюдения требований к качеству путевого щебня.
Для того чтобы выполнить свою функцию, балластный слой должен [79]:
–передавать наиболее равномерно давление от рельсовых опор на возможно большую площадь земляного полотна;
–обладать возможно большей равноупругостью;
–обеспечивать наименьшую неравномерность остаточных осадок;
–оказывать максимально возможное сопротивление поперечному и продольному сдвигу шпал;
–позволять наиболее качественно и удобно выполнять выправочные работы;
–устраиваться из прочного материала, хорошо сопротивляющегося механическому износу и выветриванию, не пылящего при проходе поездов с высокими скоростями;
–обеспечивать по возможности более постоянный влажностный режим вокруг деревянных шпал. Наиболее пригодным материалом, могущим одновременно удовлетворить всем перечисленным требованиям,
является щебень, приготовленный из прочных каменных пород. Однако эффект усиления верхнего строения пути достигается только в том случае, если укладывается щебень хорошего качества. Низкое качество щебня не обеспечивает ожидаемого эффекта в повышении устойчивости пути, увеличении срока службы элементов верхнего строения пути и сокращении расхода средств на текущее содержание [79].
Максимальный размер отдельных зерен определялся размещением их под шпалой. При этом ширина нижней постели шпалы принималась 300 мм и считалось, что наиболее устойчивое положение шпалы будет в том случае, если она опирается в четырех точках. В таком случае размер отдельных зерен под шпалой не должен превышать 75 мм, и эта величина определяла верхний предел крупности щебня.
Нижний предел, т.е. минимальный размер отдельных зерен, также имел свое обоснование. Считалось, что для равномерной осадки и недопущения скалывания граней у крупных частиц пустоты между ними необходимо заполнить более мелким щебнем. Однако мелкий щебень не должен заполнять пустоты сплошной массой, поскольку в этом случае понизилась бы водопроницаемость балластного слоя. На основе опыта отечественных и зарубежных дорог установлено, что зерна щебня величиной 25 мм еще не заполнят сплошной массой промежутков между щебнем размером 75 мм.
В связи с этим нижний предел размера отдельных зерен был принят 25 мм.
113
Процесс накопления остаточных деформаций в балластном слое
В настоящее время, несмотря на многочисленные исследования, отсутствуют физически обоснованная общепризнанная методика априорного определения (предвидения) остаточных деформаций засоренного балласта с учетом образования выплесков, динамического (вибрационного) воздействия шпал на балласт под колесами подвижного состава и климатических сезонных его изменений. Многократные попытки решить эту задачу классическими методами теории упругости через использование монотонно изменяющегося (в процессе наработки тоннажа) модуля деформации не давали приемлемых результатов. Причина в том, что модуль деформации балластного слоя, в частности, и подшпального основания, в целом, величина стохастическая, чрезвычайно изменчивая как по протяжению пути, так и во времени (по сезонам года). Поэтому в детерминистической постановке эта задача решена быть не может. Для решения ее в стохастической постановке нет и в обозримой перспективе, видимо, не будет необходимого количества экспериментальных данных по фактическим значениям модуля деформации подшпального основания различного (реального) его состава и состояния. По нашему мнению, в современных условиях существует единственное возможное решение — это использование аппроксимирующих функций фактических экспериментальных и эксплуатационных данных по накоплению остаточных деформаций в зависимости от наработки тоннажа при интегральном учете напряжений и вибраций. Таких данных накоплено уже много [79–85].
Известно, что в пути балластный слой в процессе эксплуатации в зависимости от пропущенного тоннажа может находиться в одной из трех стадии состояния [72]:
–стадия 1 — синхронизации интенсивности развития остаточных деформаций после ремонтов пути, включающих очистку балласта, когда осадка и уплотнение после очистки происходят с наибольшей скоростью вследствие переупаковки частиц, которая (скорость) постепенно уменьшается с пропущенным тоннажем;
–стадия 2 — стабилизации интенсивности развития остаточных деформаций, когда осадка происходите постоянной скоростью вследствие истирания частиц при неизменном уплотнении. Этот процесс ограничивается возникновением локальных расстройств — выплесков;
–стадия 3 — критической интенсивности развития остаточных деформаций при значительной аккумуляции засорителей, воды, болезнях основной площадки земляного полотна, когда осадка сопровождается разуплотнением частиц щебня и происходит с постепенно увеличивающейся скоростью.
Продолжительность первой стадии после ремонта пути с очисткой балласта определяется величиной пропущенного тоннажа, при котором происходит переупаковка частиц в толще очищенного слоя балласта. Эта стадия начинается после приемки пути в эксплуатацию и зависит от толщины очищенного слоя балласта, степени его уплотнения перед вводом в эксплуатацию, прочности основания балластной призмы.
Продолжительность второй стадии стабилизации интенсивности развития остаточных деформаций при незначительном засорении балласта определяется величиной пропущенного тоннажа T, при котором засорение и увлажнение перового пространства в щебне достигают значений, предельно допустимых по условию возникновения выплесков у концов шпал.
Величина Т окончания второй стадии определена в документе «Нормы глубины и периодичности очистки щебня для скоростного совмещенного движения», утвержденном ЦП МПС в 1997 г. [86]. Максимально допускаемое засорение балласта устанавливается в два раза меньшим объема пустот между частицами щебня, т.е. 20 % от объема балласта. При этом среднесетевое предельно допустимое весовое содержание сухого засорителя одинакового со щебнем удельного веса не должно превышать 17 %.
Продолжительность третьей стадии критической интенсивности развития остаточных деформаций, когда интенсивная осадка пути сопровождается разуплотнением балласта и его повышенной пластичностью, определяется максимально допускаемым засорением балласта, равным 35 % от объема балласта. При этом предельно допустимое весовое содержание сухого засорителя одинакового со щебнем удельного веса не должно превышать 26 %. В этих условиях нормами ремонтов пути предусмотрена очистка щебня в соответствии с документами «Технические условия на работу по планово-предупредительной выправке пути» [77]
и«Нормы глубины и периодичности очистки щебня для скоростного совмещенного движения» [86].
4.5.2. Исследование упругих осадок шпал
Известно, что наиболее благоприятное взаимодействие пути и подвижного состава обеспечивается при максимальной равноупругости подрельсового основания. И наоборот, неравноупругость является основной причиной неравномерности остаточных осадок шпал, которая в свою очередь вызывает появление опасных расстройств пути в целом.
Исследования упругих и остаточных осадок шпал в эксплуатационных условиях были проведены П.П. Цукановым [88], на основе которых доказано, что между закономерностями изменения упругих и остаточных осадок шпал и процессом развития неисправностей пути по уровню имеются тесные корреляционные связи. Однако при этом не рассматривался вопрос о влиянии зернового состава щебня на неравномерность осадок шпал.
Изучение влияния зернового состава щебня на величину упругих и пластических (остаточных) деформаций щебеночного балласта проводилось в Австрии [89].
114
Исследования показали, что при щебне недостаточной прочности упругие деформации возрастают в два раза, а пластические (остаточные) деформации — в пять раз по сравнению со щебнем высокого качества.
При исследованиях [79] ставилась задача выявить в условиях действующего пути различие в упругости подрельсового основания и особенно ее неравномерности в зависимости от зернового состава щебня. Для этих целей были использованы хорошо обкатанные опытные участки, заложенные на экспериментальном кольце ВНИИЖТа: опыты проводились при щебне из гранита и песчаника при железобетонных шпалах. При этой влияние упругости шпал сводилось к минимуму.
Наиболее важным показателем является неравномерность упругих осадок, которая в конечном счете приводит к появлению неравномерных остаточных осадок и общему расстройству пути. Опыт показал, что, прослеживается тенденция возрастания неравномерности упругих осадок по мере увеличения крупности зерен щебня при любой его породе. В этом отношении целесообразно применять более мелкий щебень (до определенного предела).
Аналогичная тенденция прослеживается и в отношении величины упругих уклонов вдоль пути и их неравномерности.
При щебне фракции 25–50 мм как уклоны, так и их неравномерность в 1,18–1,93 раза меньше, чем при щебне 25–70 мм. Известно, к каким последствиям приводят динамические уклоны и как они отражаются на перерасходе локомотивами топлива и электроэнергии. Щебень фракции 15–40 мм обеспечивает достаточно хорошую равноупругость и равномерность упругих продольных уклонов, однако нецелесообразность его использования для балластного слоя вытекает из других показателей (недостаточная устойчивость при воздействии вибрационной нагрузки и др.).
В практических расчетах на эксплуатируемых участках пути используют эмпирические формулы, связывающие осадку y, мм, поверхности балласта и пропущенный тоннаж Т, млн т бр.
Накопление остаточных деформаций на всех трех стадиях интенсивности развития остаточных деформаций можно описать двучленной формулой вида [82]
y = |
T |
+ a Tâ . |
(4.11) |
|
|||
|
a1 + b1T |
2 |
|
|
|
|
где a1, b1, a2, в — эмпирические коэффициенты, характеризующие изменение прочностных характеристик в процессе многократного загружения, засорения и увлажнения балласта, которые определяются путем аппроксимации экспериментальной зависимости y(Т) на засоренных участках функцией (4.14).
Главный показатель накопления остаточных деформаций в балласте в процессе эксплуатации — величина динамических сил, передаваемых на балласт под поездами.
Учитывая прямую пропорциональную зависимость между удельными давлениями и интенсивностью накопления остаточных осадок, составим уравнения y1 = φ1(i) Для пути с деревянными и железобетонными шпалами. При этом исходным значением интенсивности накопления остаточных осадок будет ее величина при отсутствии неровностей на рельсах. По данным С.Н. Попова [90], она составляет 0,10–0,12 мм/млн т. Учитывая, что в данных опытах остаточные осадки измерялись по откосной нити, где они накапливаются быстрее, чем на междупутной, а также имея в виду результаты экспериментов, примем значение интенсивности накопления остаточных осадок пути при деревянных шпалах и отсутствии неровностей равным 0,14 мм/млн т. Удельные давления на балласт при железобетонных шпалах и отсутствии неровностей примерно на 35 % больше чем при деревянных. Соответствующее значение интенсивности будет 0,19 мм/млн т. Это совпадает с результатом экстраполяции до i = 0. Используя полученные значения, получим следующие зависимости:
при железобетонных шпалах
у = 0,0094i + 0,19; |
(4.12) |
при деревянных шпалах |
|
у = 0,0070i + 0,14. |
(4.13) |
Сравнивая интенсивности накопления остаточных осадок, полученные экспериментально без неровностей и по формулам (4.12, 4.13), можно убедиться в значительном влиянии вибраций в балласте на интенсивность накопления остаточных осадок пути при железобетонных и деревянных шпалах.
При наличии неровностей на поверхности катания рельсов указанные различия в жесткости и влияние их на работу элементов верхнего строения пути проявляются наиболее резко [91, 92]. Именно в этом случае следует ожидать наибольшей разницы в накоплении остаточных осадок пути с обоими видами шпал, так как неровности являются источником дополнительных динамических сил, а следовательно, и вибраций балласта.
Оценка состояния пути по записям путеизмерительных вагонов и тележек применяется как у нас, так и за рубежом.
Неравномерность осадки одной рельсовой нити по отношению к другой фиксируется на ленте, и все неисправности, выходящие за пределы допусков, штрафуются баллом по специально разработанной шкале. Следовательно, балльная оценка объективно показывает наличие неисправностей, превышающих установленные нормы [93].
В настоящее время оценка состояния пути по статистическим характеристикам реализована на путеизмерителе ЦНИИ-4 [87].
115
Планово-предупредительная выправка пути предназначена для восстановления равноупругости подшпального основания и уменьшения степени неравномерности отступлений по уровню и в плане, а также просадок пути [23].
Назначение планово-предупредительной выправки пути производится по результатам проверки путеизмерительным вагоном на участках с незначительным количеством негодных шпал и скреплений и чистым балластом, исходя из основных критериев, приведенных в табл. 4.7. При превышении показателей негодности и дефектности элементов ВСП значений, указанных в табл. 4.7, должны проводиться подъемочный или средний ремонт.
В процессе планово-предупредительной выправки пути выполняется:
–сплошная выправка пути с подбивкой шпал;
–рихтовка пути;
–частичная замена негодных шпал и элементов скреплений; регулировка стыковых зазоров;
–удаление регулировочных прокладок из-под подошвы рельсов и сплошное закрепление клеммных и закладных болтов при скреплении КБ;
–другие работы, входящие в перечень текущего содержания пути (если они требуются).
|
|
|
|
|
|
|
|
Таблица 4.7 |
|
|
|
Критерии выбора участков, подлежащих |
|
|
|
||
|
|
планово-предупредительной выправке пути |
|
|
|
|||
|
|
|
|
|
|
|
|
|
|
|
Основные критерии |
Дополнительные критерии, % |
|
||||
Класс пути |
Количество отступлении II сте- |
|
Загрязненность щебня, % |
Негодные деревян- |
Шпалы с вы- |
|
Негодные |
|
|
|
пени*, шт./км, более |
|
по массе |
ные шпалы |
плесками |
|
скрепления |
|
группа |
20 |
|
|
|
|
|
|
1 и |
Б, В |
|
|
|
|
|
|
|
|
|
менее 30 |
6 |
2 |
|
10 |
||
2 |
группа |
25 |
|
|
||||
|
|
|
|
|
|
|||
|
Г, Д |
|
|
|
|
|
|
|
|
|
|
|
|
|
|
|
|
|
3 |
30 |
|
менее 30 |
10 |
4 |
|
15 |
|
4 |
40 |
|
менее 30 |
15 |
5 |
|
20 |
|
5 |
|
|
по усмотрению начальника дистанции пути |
|
|
|
* По показаниям вагона-путеизмерителя в среднем за 3 месяца без учета отступлений по ширине колеи.
4.6.Продолжительность межремонтных периодов на участках
синтенсивным засорением балластного слоя
Как известно, необходимость очистки щебня, а следовательно, и ремонта пути по состоянию балластного слоя обусловливается его загрязнением, которое является причиной потери фильтрационной способности щебеночного слоя и общего расстройства пути.
Загрязнение щебня происходит в результате механического износа его зерен под воздействием подвижной нагрузки и шпалоподбивочных механизмов, а также попадания внешних засорителей.
Проведенными ранее исследованиями доказано, что износ щебня от воздействия проходящего по пути подвижного состава незначителен [90]. Это положение нашло подтверждение и при исследованиях [79]. Также доказано, что дробление щебня при работе современных шпалоподбивочных механизмов, основанных на вибрационном, вибрационно-ударном действии или вибрационном обжатии, также не приводит к такой степени загрязнения балластного слоя, чтобы его очистка потребовалась раньше, чем ремонт с целью обновления остальных элементов верхнего строения пути [79].
Наиболее значительно загрязняется балластный слой внешними засорителями, что и вызывает необходимость в преждевременной его очистке.
Это обстоятельство подтвердилось при разрезах балластной призмы. При щебне фракции 25–50 мм предельное загрязнение щебня обнаружено только в шпальных ящиках. Непосредственно под шпалой осталась зона незагрязненного щебня, нижний же слой до 5–10 см от подушки загрязнен незначительно. При щебне фракции 40– 70 мм во всех местах, где были сделаны разрезы, щебеночный слой был загрязнен по всему сечению балластной призмы, включая и подшпальную зону (причину попадания загрязнителя под подошву шпалы рассмотрим далее).
Показателем характера и степени загрязнения балластного слоя является также наличие выплесков. Проверка показала, что при щебне фракции 40–70 мм на многих участках имелись выплески на отдельных шпалах и группах шпал до 5 шт. подряд, чего не наблюдалось на участках со щебнем фракции 25–50 мм.
Путь по длине засоряется сыпучими грузами неодинаково. Проверка показала, что даже на перегонах, примыкающих к станциям формирования угольных маршрутов, на путь попадает большое количество угля лишь в тех местах, где поезда идут с неравномерной скоростью (рывками), с высокими скоростями или на тормозных участках, а на участках, где поезда идут более плавно и с небольшими скоростями, из вагонов высыпается угля меньше или он не высыпается совсем. Таким образом, даже на одном и том же километре часть пикетов оказывается сильно загрязненной, а остальные загрязнены незначительно. Следовательно, на величину загрязнения балластного слоя влияет не столько зерновой состав щебня, сколько план и профиль линии, а также плавность движения поездов.
Из сказанного следует, что загрязнение щебеночного слоя, потребность в его очистке и фактическая очистка на участках с интенсивным загрязнением внешними загрязнителями происходят независимо от зернового состава щебня.
116
Одной из главнейших задач балластного слоя является обеспечение необходимой устойчивости рельсошпальной решетки. Исследования показали, что щебень различного зернового состава по-разному выполняет эту функцию. Лучшим следует считать щебень такой фракции, при которой исправное состояние пути поддерживается при минимальных затратах труда, остаточные деформации накапливаются наиболее равномерно, без резких просадок и перекосов. Важно также, чтобы щебень был такой крупности, при которой можно выполнять точную выправку при подъемке пути на небольшую высоту.
Недостаточная устойчивость подшпального основания проявляется, во-первых, в наличии отрясенных шпал. Обследование показало, что меньшее количество отрясенных шпал имеется на участках, где путь уложен на щебень фракции 25–50 мм.
Наличие выплесков также характеризует недостаточную устойчивость пути. Известно, что если шпала будет плотно лежать даже на полностью загрязненном балласте, то выплеск не появится. Наличие выплеска свидетельствует о том, что у данных шпал имеется неустойчивая постель.
При подбивке таких участков после прохода небольшого количества, поездов путь снова дает осадку, появляются отрясенные шпалы, выплески, отступления по уровню, и следовательно, после короткого периода эксплуатации возникает необходимость в повторной выправке. При частых подбивках на участках с интенсивным загрязнением балластного слоя сыпучими грузами засоритель в значительном количестве попадает в подшпальную зону, загрязняя полностью все сечение щебеночной призмы, а это приводит к появлению выплесков со всеми вытекающими отсюда отрцательными последствиями.
Неравномерность (пилообразность) записи по уровню и величина амплитуды колебаний записи на лентах путеизмерителя отражают также наличие отрясенных шпал, выплесков и других неисправностей подшпального основания (при прочих равных условиях).
Поэтому балльная оценка — один из наиболее полных показателей состояния балластного слоя. Средний ремонт пути предназначен для сплошной очистки щебеночной балластной призмы, замены де-
фектных шпал и элементов скреплений в объемах, предусмотренных Техническими условиями [32]. Средний ремонт включает в себя сплошную очистку щебеночного балласта на глубину под шпалой не
менее 25 см с добавлением нового балласта или обновление загрязненного балласта других видов на глубину не менее 15 см под шпалой и сплошную выправку пути.
Критерии назначения работ по среднему ремонту приведены в табл. 4.8.
117
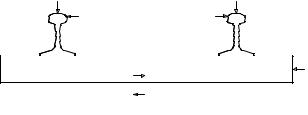
|
|
|
|
Таблица 4.8 |
|
Критерии выбора участков, подлежащихсреднему ремонту пути |
|
||
|
|
|
|
|
|
Основные критерии |
Дополнительные критерии |
||
Класс пути |
|
|
Количество негодных, %, более |
|
Загрязненность щебня, % по массе |
Количество шпал с выплесками, %, более |
деревянных шпал |
скреплений |
|
|
|
|
||
|
|
|
|
|
1 |
30 и более |
3 |
10 |
12 |
2 |
30 и более |
5 |
12 |
15 |
3 |
30 |
7 |
15 |
20 |
4 |
30 |
10 |
20 |
30 |
5 |
Не лимитируется. Средний ремонт назначается по усмотрению начальника дистанции пути по согласованию с начальником служ- |
|||
|
бы пути |
|
|
|
|
|
|
|
Примечание. Загрязненность щебня и количество выплесков оценивается в год, предшествующий назначению ремонта пути. При этом выплески, устраненные в течение года, также входят в эту сумму.
Состояние балластного слоя принято оценивать засоренностью щебня, протяженностью пути и выплесками загрязненного балласта у шпал или количеством отступлений по показателям вагона-путеизмерителя. Наиболее просто и наглядно оценивать состояние балласта по доле протяженности пути с выплесками [71]
F(t |
) = |
m(ti ) |
, |
(4.14) |
|
||||
i |
1000 |
|
|
|
|
|
|
где m(ti) — протяженность пути с выплесками в метрах в момент времени или наработки ti.
По результатам наблюдений строится упорядоченный ряд m(ti) по мере возрастания ti определяются частости F(ti) и квантили нормального распределения UPi, а по ним указанным ранее способом — Tср и σt, этого ряда наблюдений. По этим параметрам можно установить наработку для любой доли протяженности пути с выплесками. В Инструкции по текущему содержанию пути [74] доля протяженности пути с грязевыми выплесками варьируется от 5 до 30 %, при этом скорости движения поездов ограничиваются от 140 до 25 км/ч.
4.7. Оценка надежности поперечных связей шпал с балластом
Поперечная устойчивость пути определяется мощностью конструкции, его состоянием и характером силового воздействия подвижного состава на путь.
Для обеспечения поперечной устойчивости пути необходимо, чтобы силы сопротивления пути поперечному сдвигу были больше суммы боковых сил, передающихся от подвижного состава на рельсы. Вопросам боковой устойчивости пути под поездной нагрузкой посвящен ряд работ, в том числе [70, 72, 79, 95, 96].
Очевидно, что если ни одна шпала под действием поперечных сил не сдвигается в балласте, то устойчивость колеи против поперечного сдвига обеспечена. Это условие избыточное, так как поперечная устойчивость пути будет нарушена лишь при групповой сдвижке шпал. Расчет боковой устойчивости колеи с учетом сопротивления сдвигу группы шпал дан в работе [70]. В случае если одна из шпал, оказавшаяся в наиболее неблагоприятных условиях, начнет смещаться поперек пути, то в сопротивление перемещению окажутся вовлечены соседние шпалы. Поэтому достаточно, чтобы для отдельно взятой шпалы, выдерживались условия предельного равновесия.
Если сопротивление сдвигу поперек пути незагруженной подвижным составом шпалы обозначить через R0 (рис. 4.2), а коэффициент трения нижней постели шпалы по балласту — через fш, то условие предельного равновесия отдельно взятой шпалы примет вид [96]
Нш = 2fш Q + R0, |
(4.15) |
где Нш — полное горизонтальное усилие, воспринимаемое шпалой; Q — вертикальное давление рельса на шпалу.
Рис. 4.2. Схема сил действующих на шпалу
Если рассматривать путь как балку бесконечной длины, опирающуюся в вертикальном и горизонтальном направлениях на упругое основание, то
Нш = 2fш Q + R0. |
(4.16) |
Полная горизонтальная нагрузка на путь: |
|
Y1 = Yб ± Pf0, |
(4.17) |
здесь f0 — коэффициент трения скольжения колеса по рельсу. |
|
118

В кривых участках пути, где поворот экипажа происходит в направлении к внутреннему рельсу, сила трения, воспринимаемая этим рельсом, направлена внутрь кривой. В этом случае в формуле (4.17) перед Pf0 следует брать знак «минус», а коэффициент трения f0 — принимать равным осредненной величине 0,25. При движении в прямых участках пути между колесом и рельсом действуют силы псевдоскольжения (явление крипа), зависящие от относительного скольжения. Значение коэффициента трения при этом изменяется от 0 до 0,25. Направление силы трения, приложенной к рельсу, совпадает с направлением поперечного перемещения в колее, т.е. в случае набегания колеса на один рельс по другой рельсовой нити будут действовать силы трения в ту же сторону, что и боковая сила по первому рельсу. Поэтому в формуле (4.17) перед Pf0 для прямых участков следует принимать знак плюс.
Вертикальное давление рельса на шпалу аналогично (4.16) определится зависимостью
Q = 0,5kl/P, |
(4.18) |
где k — коэффициент относительной жесткости рельсового основания и рельса в вертикальной плоскости. Подставляя значения (4.16) и (4.18) в формулу (4.15), найдем для кривых участков пути
Y = 2Pf |
|
k |
+ |
2R0 |
+ Pf |
|
. |
(4.19) |
||
ø k |
|
|
|
|||||||
á |
ò |
|
lk |
ò |
|
0 |
|
|
||
|
|
|
z |
|
|
z |
|
|
|
|
При вписывании подвижного состава в кривые для направляющей оси можно записать, что рамная сила
Yð |
= Yá |
+ Pf0 . |
|
(4.20) |
|||
В соответствии с этим выражением (4.19) примет вид |
|
||||||
Y ≤ 2Pf |
|
k |
+ |
2R0 |
= R . |
(4.21) |
|
ø kò |
lkò |
||||||
ðä |
|
ø |
|
||||
|
|
z |
|
z |
|
|
Как выяснено в [96], наибольшему значению силы Yрд не соответствует наибольшее или наименьшее давление Р, поэтому рекомендуется брать среднее значение Р при наибольшем динамическом значении Yрд. По мере старения пути в нем накапливаются повреждения, в том числе в виде вертикальных и горизонтальных неровностей, вследствие чего Yрд будет расти. В то же время сопротивление шпал сдвигу вследствие загрязнения балласта, особенно при сильном его увлажнении, будет со временем снижаться. Наконец, в некоторый момент времени сила Yрд может превысить приведенное значение сопротивления шпалы сдвигу Rш и произойдет отказ.
При нормальном распределении сил Yрд и сопротивления шпалы сдвигу Rш отказ не произойдет, пока
Rø |
−Yðä = |
> 0 . |
(4.22) |
||
Среднее значение случайной величины |
|
в этом случае равно разности средних значений случайных ве- |
|||
личин Rш и Yрд, т.е. |
|
|
|
|
|
m = mR − mY ðä . |
(4.23) |
||||
|
ø |
|
|
|
|
Среднее квадратичное отклонение случайной величины |
|||||
|
|
|
|
|
|
σ |
= σ2 |
+ σ2 |
, |
(4.24) |
|
|
|
R |
Y |
|
|
|
ø |
ðä |
|
|
где σRø и σYðä — средние квадратичные отклонения случайных величин.
4.8. Сопротивления шпал поперечному сдвигу
Величина сопротивления поперечному сдвигу шпал имеет большое значение для поперечной устойчивости пути. Особое значение это приобретает при укладке бесстыкового пути. Поэтому понятно, что определение сопротивления поперечному сдвигу шпал интересовало многих исследователей.
Необходимым условием для успешного применения железобетонных шпал в бесстыковом пути является обеспечение их повышенного сопротивления сдвигу в балласте, особенно в поперечном по отношению к оси пути направлении.
На первом этапе применения железобетонных шпал как на отечественных железных дорогах, так и на большинстве зарубежных дорог для этой цели нижнюю поверхность шпалы делали не ровной и гладкой, а рифленой, устраивая на ней специальные углубления в бетоне или выступы той или иной формы. В результате специальных лабораторных исследований, проведенных ВНИИЖТом, были выбраны оптимальная форма, размеры и расположение углублений в бетоне. Наиболее эффективными оказались углубления квадратной формы размером 70×70×10 мм, расположенные в шахматном порядке в подрельсовых частях шпалы. Этот вид рифления был принят во всех отечественных стандартных шпалах и применялся до последнего времени.
Для выполнения таких углублений в бетоне на заводах при формовании шпал подошвой вверх применяли специальные массивные пригрузы, имеющие снизу выступы, рисунок которых соответствовал требуемому рисунку рифлений. После заполнения шпальной формы бетонной смесью на нее накладывали пригруз, всю форму подвергали интенсивной вибрации на виброплощадке и после уплотнения бетонной смеси на подошве шпалы оставались рифления заданного рисунка. При производстве шпал массивный пригруз, кро-
119

ме образования рифлений на шпалах, играл и другую важную роль — он облегчал укладку жестких бетонных смесей, необходимых для получения бетона шпал с высокой прочностью и долговечностью.
Получение бетона шпал, отвечающего заданным в стандартах и технических условиях требованиям по передаточной и нормативной прочности, а также по морозостойкости, достигалось применением жестких бетонных смесей с расходом высокомарочного цемента примерно 450 кг/м3 при малом количестве воды, равном 150–160 л на 1 м3 бетона.
Чтобы при укладке жесткой бетонной смеси не образовывались раковины внутри шпал и на их поверхностях, требовалось интенсивное вибрационное уплотнение смеси с применением пригруза. На типовых технологических линиях заводов железобетонных шпал были сделаны два поста формования шпал, оборудованных мощными виброплощадками: на первом осуществляли вибрацию без пригруза, на втором — с массивным гравитационным пригрузом.
Многолетний опыт применения типовых железобетонных шпал на дорогах страны показал их высокую прочность, долговечность, а также повышенную стабильность бесстыкового пути с этими шпалами. В то же время формование шпал с массивным пригрузом имеет и ряд недостатков, влияющих и на качество шпал, и на технологичность их изготовления. Например, при наложении пригруза на бетонную смесь в форме смещается вниз напряженная проволочная арматура. После снятия пригруза арматура стремится выпрямиться, в результате чего нарушается слой еще не затвердевшего бетона вокруг проволок. Это приводит к образованию вокруг проволок, видимых на торцах шпал, пустот, снижает сцепление арматуры с бетоном. Укладка бетонной смеси с пригрузом, кроме того, затрудняет выход воздуха из бетонной смеси, из-за чего внутри шпал иногда образуются воздушные поры-пустоты.
Впоследние годы появились и получили распространение различные химические добавки, улучшающие свойства бетонной смеси и бетона. Применение так называемых суперпластификаторов улучшает удобоукладываемость бетонной смеси с меньшим количеством воды. В результате существенно повышаются прочность и морозостойкость бетона при том же расходе цемента, так как меньше водоцементное отношение, или получается экономия цемента при заданных прочности и морозостойкости бетона.
Таким образом, отказ от применения пригруза при формовании шпал исключает возможность образования пустот в бетоне вокруг проволок арматуры, снижающих их сцепление с бетоном, а также пор и пустот внутри бетонной смеси, т.е. снижает брак при производстве шпал. Отказ от пригруза в сочетании с применением пластификаторов бетона, кроме повышения качества шпал, может дать заметный технико-экономический эффект на стадии производства шпал. К числу положительных факторов следует отнести:
– повышение производительности технологической линии и высвобождение рабочих площадей при исключении вторичного виброуплотнения и технологического оборудования — второй виброплощадки, тельферной установки, пригруза;
– уменьшение затрат труда путем устранения работ по обслуживанию и ремонту пригруза и очистке его подошвы от остатков бетонной смеси;
– снижение себестоимости изготовления шпал и в конечном счете соответствующее уменьшение их цены.
Вто же время отказ от применения пригруза при формовании шпал делает невозможным выполнение рифлений на их подошве, что в той или иной степени могло бы повлиять на сопротивление шпалы сдвигу по балласту. Это и было одной из причин того, что снова возник вопрос о влиянии углублений в подошве шпал, а также ее рифления на сопротивляемость железобетонных шпал сдвигу.
Сопоставление сопротивлений поперечному сдвигу шпал типовых и повышенной массы
ВНИИЖТом проводились исследования особенностей работы так называемых шпал повышенной массы ШСТ-1, предназначавшихся для линий с большой грузонапряженностью и повышенными осевыми нагрузками подвижного состава. При этом необходимо было оценить целесообразность устройства на постели шпал углублений той или иной формы.
Для проведения сравнительных испытаний железобетонных шпал различных конструкций на сдвиг по балласту в поперечном направлении во ВНИИЖТе был разработан и сооружен специальный стенд [94].
Эксперименты проводили в условиях, близких по состоянию балластной призмы к условиям на момент обкатки вновь уложенного пути, когда произведена выправка и подбивка пути, отсыпано плечо балластной призмы и засыпаны шпальные ящики. Анализ полученных материалов показал следующее. Сопротивление шпалы сдвигу по подошве зависит от массы шпалы и величины сдвига ее в балласте. Оно растет с убывающей интенсивностью до некоторого критического значения сдвига, после чего стабилизируется (рис. 4.3).
По результатам одиночных испытании на каждом этане вычисляли средние значения Y сопротивлений, средние квадратические отклонения σy, этой величины, после чего определяли вероятные границы зоны рас-
сеяния возможных значений Yi = Y ± 1,5σy.
Сравнение сопротивления шпал при одинаковых значениях сдвига (1 мм, 2 мм и т.д.) выявило линейную зависимость его от массы шпалы и вертикальной нагрузки на нее (рис. 4.3). В связи с этим на всех этапах испытаний сопротивление шпалы ШСТ-1 сдвигу в балласте, как правило, превышало аналогичные показа-
120
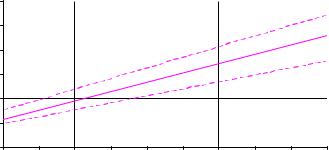
тели для шпалы ШС-1. Эта тенденция сохранялась как при очень малых сдвигах, начиная с 0,1 мм, так и при |
||||||||||
больших независимо от типа шпалы. |
|
|
|
|
|
|
|
|
||
|
6 |
|
|
|
|
|
|
|
|
|
|
5 |
|
|
|
|
|
|
|
|
|
|
4 |
|
|
|
|
|
|
|
|
|
, кН |
3 |
|
|
|
|
|
|
|
|
|
Y |
|
|
|
|
|
|
|
|
|
|
|
2 |
|
|
|
|
|
|
|
|
|
|
1 |
|
|
|
|
|
|
|
|
|
|
0 |
|
|
|
|
|
|
|
|
|
|
1 |
2 |
3 |
4 |
5 |
6 |
7 |
8 |
9 |
10 |
|
|
|
|
|
|
P , кН |
|
|
|
|
–––– средние значения; |
|
|
|
|
|
|
|
|
|
|
– — – границы зоны разброса экспериментальных значений. |
|
|
|
|
|
|
Рис. 4.3. Пример зависимости сопротивления сдвигу шпал ШСТ-1 и ШС-1
в балласте по подошве Y от вертикальной нагрузки Р, включая вес шпалы, при = 1 мм
Для определения сопротивления сдвигу шпалы в балласте по подошве была предложена эмпирическая формула
H = a + f P 0,25, |
(4.25) |
где H — сопротивление сдвигу по подошве шпалы, кН; Р — вертикальная нагрузка на шпалу, включая ее собственный вес, кН; — сдвиг шпалы относительно балласта, мм; a и f — эмпирические параметры.
При испытаниях шпал на щебеночном балласте было получено a = = 1,7 и f = 0,42, т.е. H = 1,7 + 0,42 P 0,25, (4.26)
Формула применима при значениях от 0,1 до 14 мм; погрешность — от 3 до 5 % в диапазоне значений = 1–4 мм и не более 10–15 % при крайних значениях размера сдвига.
Совместный анализ всех данных (табл. 4.9) позволил установить, за счет каких элементов формируется полное сопротивление шпалы сдвигу по балласту.
Полное сопротивление шпалы ШСТ-1 сдвигу в свеженасыпанном балласте при нормальном плече балластной призмы и полностью засыпанных ящиках превышает сопротивление шпалы ШС-1 в аналогичных условиях в среднем на 9–10 % во всем диапазоне сдвига шпалы относительно балласта: от 0,1 до 5–8 мм и более.
Анализ всех данных, приведенных в табл. 4.9 позволил установить, за счет каких элементов достигается увеличение на 10 % сопротивления сдвигу шпалы ШСТ-1 при полной, но не уплотненной балластной призме.
Таблица 4.10
Сопротивление шпал сдвигу
Тип шпалы |
|
Сопротивление сдвигу, % |
|||
полное |
по подошве |
по торцу |
по боковой поверхности |
||
|
|||||
ШС-1 |
100 |
41,3 |
13,5 |
45,3 |
|
ШСТ-1 |
110 |
49,9 |
17,9 |
42,2 |
|
Коэффициент изменения |
1,10 |
1,21 |
1,33 |
0,93 |
Из табл. 4.10 следует, что увеличение массы шпалы ШСТ-1 по сравнению с массой ШС-1 привело к повышению доли сопротивления сдвигу по подошве на 21 %, увеличение ширины и площади торца шпалы ШСТ-1 на 14 % повысило долю сопротивления сдвигу по торцу на 33 %, а отсутствие уширения шпалы ШСТ-1 к концам наоборот, уменьшило долю сопротивления сдвигу по боковым поверхностям шпал при засыпке шпальных ящиков на 7 %.
Из данных табл. 4.10 следует, что доля сопротивления сдвигу типовых шпал ШС-1 по подошве при щебеночном балласте составляет около 40 % полного сопротивления их боковому сдвигу. Такие же результаты были получены и при определении сдвига шпал в балласте на трехшпальном стенде ВНИИЖТа В.С. Лысюком [72]. При отсутствии нагрузки на шпалу и величине сдвига до 0,2 мм доля сопротивления сдвигу шпал по подошве составляла при щебеночном балласте 41 %, при асбестовом — 59 %.
Для того чтобы оценить значение рифления подошвы типовой шпалы в формировании ее полного сопротивления сдвигу в балласте, была проведена новая серия испытаний на стенде. Объект испытаний — типовые шпалы ШС-1y, изготовленные Вяземским заводом.
Исследования позволили установить факторы, влияющие на сопротивление сдвигу в балласте типовых железобетонных шпал, и пути его возможного повышения, оценить эти факторы количественно.
Установлено, что влияние специального рифления нижней поверхности подошвы на сопротивление шпалы сдвигу незначительно. Равноценное сопротивление сдвигу по балласту может быть получено у шпал
121
с шероховатой поверхностью, обеспечиваемой выступающими из бетона частицами крупного заполнителя. В связи с этим в настоящее время заводы железобетонных шпал перешли на изготовление шпал без пригруза и специального рифления подошвы.
Совместное воздействие на шпалу вертикальной нагрузки и сдвигающей силы приводит к возникновению напряжений в точках контакта балласта и шпалы и в самом балласте. Величины контактных напряжений распределяются по случайному закону, при этом даже при небольших значениях сил, действующих на шпалу, в отдельных точках они могут превышать предел прочности материала балласта. По мере увеличения вертикальной нагрузки число таких точек возрастает, в них развиваются пластические деформации. Этим и объясняется снижение интенсивности роста сопротивления сдвигу подошвы шпалы с увеличением вертикальной нагрузки.
Можно заметить, что увеличение сверх установленных пределов плеча балластной призмы оправдано лишь в случае применения щебеночного балласта. Для асбестового балласта оптимальная ширина плеча находится в пределах 20–30 см. В обоих случаях несомненно важным является своевременное пополнение шпальных ящиков [94].
Долевое участие сопротивлений сдвигу по подошве, торцу и боковой поверхности шпалы в формировании общего сопротивления сдвигу при различных значениях вертикальной силы, действующей на шпалу, отражено на рис. 4.4. Видно, что с увеличением вертикальной статической нагрузки доля сопротивления по торцу и боковой поверхности шпалы снижается от 33–65 % при Рв = 0, до 8–10 % при Рв = 10 кН.
Это позволяет сделать вывод, что мероприятия, направленные на повышение сопротивления по торцу и боковой поверхности шпал, могут быть рекомендованы лишь для обеспечения устойчивости пути при наличии температурных сил и не оказывают существенного влияния на сопротивляемость пути горизонтальным поперечным воздействиям подвижного состава.
Определение сопротивления поперечному сдвигу шпал производилось также на действующем пути. Участок, на котором производились опыты, был хорошо обкатан. В процессе исследования испытывае-
мая шпала расшивалась и сдвигалась гидравлическим домкратом, оборудованным манометром.
Сдвиг шпалы фиксировался индикатором с точностью до 0,01 мм. Расшитая шпала нагружалась куском рельса, вес которого соответствовал весу рельсов, приходящемуся на каждую шпалу.
122