
669
.pdfВбесстыковом пути на возникновение и развитие поперечных усталостных трещин в головке наиболее существенно влияет температура. В мороз одновременно со снижением живучести (трещиностойкости) возникают продольные растягивающие температурные силы, которые в рельсовых плетях прямо пропорциональны отрицательному температурному перепаду и. как известно, могут достигать 1200–1600 кН (в рельсах типа Р65 — 20 кН/ºС (рис. 2.10).
Всопоставимых эксплуатационных условиях, но при разном климате удельные отказы рельсовых плетей (шт./млн т бр.) могут быть на 30–40 % выше при более длительном периоде (в 1,6 раза) действия существенно больших (в 1,5 раза) продольных растягивающих сил в рельсах. Рассмотрели два варианта работы рельсовой плети: при температурах –20 и –60 °С и продольных силах 800 и 1600 кН. Расчет показал, что снижение при прочих равных условиях и напряжении в рельсах 160–180 МПа, характерном для средних условий нагружения пути, критическая площадь дефекта 21 снижается на 6–9 % при температуре –20 ºС и на 10–13 % при –60 °С.
Таким образом, во-первых, в некоторой степени можно учитывать влияние различных факторов на критическую площадь трещин, т.е. контролировать работу поврежденных рельсов. Во-вторых, по параметрам конструкционной прочности, прежде всего по трещиностойкости, современные рельсы имеют определенный запас, что позволяет поднять вопрос о продолжении эксплуатации рельсов с дефектами.
Протяженность бесстыкового пути увеличивается. Однако, как было уже отмечено, в рельсовых плетях действуют значительные продольные усилия, вызываемые изменением температуры. При ее повышении по сравнению с температурой закрепления возникают продольные силы сжатия, которые могут привести к выбросу пути, а при понижении температуры — растягивающие силы, которые могут вызвать излом рельсов. Более трудоемки ремонтные работы, например, изъятие из плетей участков с дефектом 21 и т.п.
Именно поэтому актуально усиление накладками сечения рельса с поперечными усталостными трещинами. Эта мера позволяет уменьшить изгибные растягивающие напряжения в головке до 30 %, замедлить развитие трещин, увеличить их критический размер до 60-80 % площади головки рельсов и в 1,5–2,0 раза повысить разрушающую нагрузку при статическом нагружении. Безопасность движения при работе рельсовых плетей с дефектом 21, взятом в накладки, также обеспечивается благодаря исключению поперечного смешения концов плетей в случае сквозного излома рельсов. Существенно снижается время «окна» для восстановления рельсовых плетей.
«Каталог дефектов рельсов НТД/ЦП-2-93» [31] допускает установку на поврежденное место в рельсах типа Р65 и Р75 шестидырных накладок в том случае, когда дефект 21 не выходит на поверхность, а границы его — за середину головки, примем как на звеньевом, так и на бесстыковом пути. «Технические указания по устройству, укладке, содержанию и ремонту беестыкового пути» [32] определяют три этапа восстановления плетей: краткосрочное, временное, окончательное. Однако в этом документе не определен «статус» усиления дефектного сечения накладками. Как и в НТД/ЦП-2-93, такой технологический прием восстановления целостности рельсовой плети допускается на тех же условиях. В то же время усиление дефектного сечения накладками (сверление четырех болтовых отверстий, монтаж) можно и нужно рассматривать как хорошую альтернативу временному восстановлению, которое более трудоемко (вырезка части рельса с дефектом, подготовка рубки длиной 8–11 м, сверление 12-болтовых отверстий, монтаж) и к тому же создаст сразу два болтовых стыка. Нетрудно подсчитать эффективность, если принять во внимание, что ежегодно в бесстыковом пути появляется несколько тысяч дефектных сечений.
Следует обобщить имеющийся у железных дорогах опыт использования накладок с целью дальнейшей корректировки условий, определяющих возможность эксплуатации рельсовой плети (выход трещины на поверхность или за середину головки рельса). Нужно изучить напряженное состояние дефектного сечения, усиленного накладками, при различной величине поперечной усталостной трещины. Кроме того, поскольку окончательное восстановление плети ввариванием заранее подготовленного рельса жестко связано с температурой закрепления плети, необходимо рассмотреть возможность восстановления в наиболее удобное время, в том числе при плановом ремонте летом и т.д., даже в случае выхода усталостных трещин на поверхность или за середину головки рельса (дефектное сечение в накладках). При этом снятие фасок и упрочнение болтовых отверстий, а также использование высокопрочных болтов следует считать обязательными атрибутами усиления накладками дефектных сечений.
Полезно рассмотреть еще два предложения. Первое — временное восстановление созданием пропила в дефектном сечении (разрядка напряжений) с усилением его накладками. Ширину и глубину пропила следует уточнить. Второе — окончательное восстановление вырезкой макротемплета (дефектное сечение) шириной 24–50 мм
споследующей сваркой образовавшегося зазора алюмнно-термитным способом. Преимущества этого способа: быстрота, исключение «подбора» ввариваемых рельсов (кстати, а как его подбирать по качеству металла?), но главное — дальнейшая эксплуатация плети без всяких ограничений [26].
Несомненно, в дальнейшем аналогичные меры можно принимать при других дефектах.
2.5.Рельсы для скоростных магистралей
Вусловиях возросшей жесткости взаимодействия колеса с рельсом большое влияние на уровень динамических сил, естественно, стали оказывать неровности на поверхности катания рельсов и колес.
Развитие неровностей зависит не только от грузонапряженности и пропущенного тоннажа, но и от первоначальной их величины на новых рельсах. Подсчитано, что если бы высота неровностей на новых рельсах
53
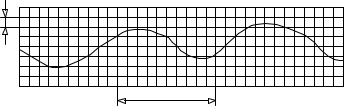
не превышала 0,3 мм, долговечность таких рельсов повысилась бы на 150–200 млн т пропущенного тоннажа, или на 20–25 %.
Поэтому специалисты-железнодорожники ставят улучшение параметров рельсов, связанных с геометрическими размерами, на первое место.
Для скоростного и, тем более, высокоскоростного движения (ВСМ) нужны рельсы лучшего геометрического качества, чем объемнозакаленные текущего производства. Это качество определяется как общей их искривленностью, так и периодическими неровностями на поверхности головки по всей длине, Достичь требуемого результата при существующей на меткомбинатах объемной закалке сложно, хотя такая возможность в настоящее время рассматривается. Для увеличения прочности «сырых» рельсов можно использовать низколегированную сталь [32].
Неровности на поверхности головки в основном измеряют трехточечной скользящей локацией продольного профиля. Существуют два варианта такой локации. Во-первых, «линеечный», являющийся отправным для лазерной системы, когда скрепленный ряд лазеров расположен над рельсом, крайние лазеры образуют так называемую «плавающую» линейку, и точки соприкосновения внутренних лучей лазеров, в крайнем случае одного, измеряют относительно этой линейки. Во-вторых, «тележечный», где в качестве концевых локаторов используют несущие ролики.
Во ВНИИЖТе создано устройство с базой 1,5 м записывающее продольный профиль на диаграммную ленту («тележечный» вариант). Это однониточная тележка, посередине которой находится измерительный ролик, катящийся вдоль контролируемого профиля и реагирующий на его неровности. Небольшая масса и автономное питание позволяют применять такое устройство в лабораторных условиях, при производстве рельсов на всех технологических операциях, в РСН и непосредственно на пути. При его помощи оценили прямолинейность продольного профиля головки рельсов, предназначенных для скоростного движения Фрагмент профилеграммы приведен на рис. 2.11. Как видно, величина периодических неровностей установлена с высокой точностью (допускаемая погрешность 50 мкм).
0,2 мм |
Рис. 2.11. Фрагмент профилеграммы продольного профиля рельса |
Амплитуды местных периодических неровностей на поверхности головки этих рельсов в основном не превышали 0,4 мм (91 %), однако имелись неровности, причем почти на каждом проверенном рельсе, с амплитудами 0,5–0,7 мм, т.е. в 1997 г. получить рельсы необходимой прямолинейности не удалось [33].
В соответствии с ТУ 0921-194оп-01124323-2005 «Рельсы железнодорожные типа Р65 для высокоскоростного движения» в 2005 г. НКМК прокатал рельсы из углеродистой стали с последующей объемной закалкой (исполнение ВС1). В РСП-1 у 10 из них также оценили прямолинейность. Дополнительно проверили пять рельсов СС (для скоростного совмещенного движения) и пять стандартных категории Т1, изготовленных НТМК. Получены следующие результаты. На поверхности катания всех объемнозакаленных рельсов (шифры ВС1, СС и Т1) имеются периодические неровности с четко выраженным синусоидальным характером. Амплитуды этих неровностей на рельсах ВС1 составляют в основном 0,3–0,4 мм/1,5 м (на одном рельсе
— 0,6 мм/1,5 м), на рельсах СС — 0,3–0,4 мм/1,5 м и на рельсах Т1 — 0,4–0,5 мм/1,5 м (на одном — до 0,7 мм/1,5 м) [32].
Таким образом, по прямолинейности объемнозакаленные стандартные рельсы Т1, изготовленные НТМК не подходят для высокоскоростных магистралей. В то же время из общего количества рельсов можно подбирать отдельные партии, в том числе шифров ВС1 и СС, для использования на участках скоростного и высокоскоростного движения. Также следует отметить, что прямолинейность оценена без учета концов рельсов.
На рельсопрокатных меткомбинатах можно выполнять селективный контроль прямолинейности всех рельсов.
2.6. Прогнозирование отказов и срока службы рельсов. Параметрическая надежность рельсов
Надежность рельсов можно характеризовать изменением выходного параметра — накоплением их отказов.
Изменение выходного параметра может происходить до определенного предельного значения, выше которого могут быть нарушения безопасности движения поездов или недопустимое снижение эффективности работы (выдача предупреждений о снижении скоростей движения поездов).
В общем случае при изменении выходного параметра η(t) во времени должно выполняться условие
η(t) ≤ ηпр , |
(2.1) |
54
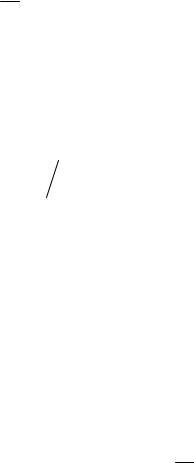
где ηпр — предельное значение параметра по критерию безопасности или эффективности функционирования системы.
Модели процессов изменения выходных параметров целесообразно выбирать среди случайных процессов, которые имеют определенную функциональную зависимость от времени (наработанного тоннажа), и их случайный характер обусловливается случайными параметрами, не зависящими от времени. Процессы такого вида принято называть полуслучайными.
В связи с этим зависимость выходного параметра от времени приближенно может быть выражена следующим образом [34]
η(t) = αTβ . |
(2.2) |
Проведенные исследования изменения параметров пути позволяют считать β детерминированной величиной.
Случайная величина α зависит от конструкции пути и условий ее работы. Зависимость для определения наработки до отказа запишем в виде
1
= ηпр β . (2.3)
T α
При этом случайным аргументом является α, т.е. Т = ϕ(α).
Выражение для плотности вероятности распределения наработки до отказа может быть получено из известного соотношения
|
dα |
|
|
|
|
||
f (t) = f [α(t)] |
|
, |
|
(2.4) |
|||
dt |
|
||||||
|
|
|
|
|
|
|
|
где α(t) — функция, обратная (2.3). |
|
|
|
|
|
|
|
Вероятность безотказной работы определяется по формуле |
|
||||||
|
η |
|
|
|
|
|
|
P(t) ≈ F0 |
пр |
− mα |
|
Sα . |
(2.5) |
||
β |
|
||||||
T |
|
|
|
|
|
|
Параметры mα, Sα и β определяются на основе обработки статистических данных, собранных с конкретного участка пути.
S |
α |
= α T(β1−β) . |
(2.6) |
|
1 |
|
Имея параметры mα и Sα по выражению (2.5) можно определить вероятность безотказной работы при любой наработке Т. Можно также определить гамма-процентный ресурс согласно выражения
P(T ) = |
γ |
. |
(2.7) |
γ |
100 |
|
После преобразований найдем гамма-процентный ресурс
|
|
|
|
|
1 |
|
|
||
|
|
|
η |
|
|
|
|
|
|
|
|
|
|
β |
|
||||
T = |
|
пр |
|
|
. |
(2.8) |
|||
|
+ λ α T |
|
|
||||||
γ |
m |
(β1 |
−β) |
|
|||||
|
|
α |
γ 1 |
|
|
|
|
Эта наработка, при которой только на 100-γ процентах километров отказы превысят ηпр.
Из обработки данных по выходу рельсов известно, что Vα = Sα = 0,45 . mα
Тогда получим
|
|
|
|
|
1 |
|
|
||
|
|
|
η |
|
|
|
|
|
|
|
|
|
|
β |
|
||||
T = |
|
пр |
|
|
. |
(2.9) |
|||
|
(1+ 0,45λ |
|
|
||||||
γ |
m |
γ |
) |
|
|||||
|
|
α |
|
|
|
|
Гамма-процентный ресурс Тγ можно определить после обработки данных о выходе рельсов и получения эмпирических коэффициентов α и β.
Предельное значение накопленного (суммарного) выхода рельсов согласно [31] нормируется в зависимости от класса пути (табл. 2.8).
Таблица 2.8
Параметры для определения гамма-процентного ресурса рельсов
Расчетные параметры |
|
Класс пути |
|
||
1 |
2 |
3 |
4 |
||
|
55
Предельный суммарный выход рельсов ηпр, шт./км |
4 |
6 |
6 |
8 |
Вероятность безотказной работы Р |
0,95 |
0,925 |
0,925 |
0,9 |
Квантиль нормального распределения λγ |
1,645 |
1,44 |
1,44 |
1,282 |
Согласно (2.9) и данным табл. 2.11 гамма-процентный ресурс рельсов для участков 2 и 3 классов определяется по формуле
|
η |
|
1 |
|
β |
|
|||
Tγ = |
пр |
|
. |
(2.10) |
|
||||
|
1,66mα |
|
|
Прогнозирование отказов рельсов по эмпирическим зависимостям
Накопленный (суммарный) выход рельсов при наработке тоннажа Т в млн т бр. определяется зависимостью
η = K |
P |
K |
αTβ . |
(2.11) |
|
R |
|
|
Коэффициенты учета влияния осевых нагрузок и радиуса кривых на выход рельсов можно представить в виде
|
|
|
= |
|
Pср γ |
|
|
|
|
Rст δ |
|
|
||
|
K |
|
|
ос |
|
; |
K |
|
= |
0 |
, |
(2.12) |
|
|
|
|
|
Pст |
|
R |
|
||||||||
|
|
P |
|
|
|
R |
|
|
|
|
||||
|
|
|
|
|
ос |
|
|
|
|
ср |
|
|
||
где Pср |
— средняя осевая нагрузка подвижного состава на рассматриваемом участке; Pст |
— стандартная |
||||||||||||
ос |
|
|
|
|
|
|
|
|
|
|
|
|
ос |
|
нагрузка, при которой определены параметры функции (2.10) ( Pосст = 160 кН); γ — эмпирический параметр; R0ст — стандартный радиус, при котором определены параметры функции (2.11), обычно принимают R0ст = 1000 м, так как в таких кривых выход рельсов мало отличается от прямых; Rср — средневзвешенный радиус
кривых на рассматриваемом участке; δ — эмпирический показатель степени.
Данные о выходе рельсов, полученные из рельсовых книг, группировались в зависимости от радиуса кривых и осевых нагрузок подвижного состава. Полученные значения выхода рельсов наносились на графики в виде точек в зависимости от пропущенного тоннажа. Затем по этим данным методом наименьших квадратов определялась аналитическая зависимость.
Средний срок службы рельсов можно определить из зависимости (2.11) приняв, что η = ηпр, тогда
|
|
η |
|
1 |
|
|
|
β |
|
||||
Tср |
= |
пр |
|
. |
(2.13) |
|
|
||||||
|
|
αKP KR |
|
|
|
Полученные на основе графиков, приведенных на рис. 2.12 и 2.13, эмпирические параметры для прогнозирования выхода и срока службы рельсов приведены в табл. 2.9.
Таблица 2.9
Эмпирические параметры для прогнозирования отказов и срока службы рельсов
Конструкция пути |
|
Эмпирические параметры |
|
||
α |
β |
γ |
|
δ |
|
|
|
||||
Звеньевая |
4,4.10-4 |
1,5 |
1,6 |
|
1,8 |
Бесстыковая |
3,2.10-4 |
1,5 |
1,6 |
|
1,7 |
Для примера определим средний срок службы и γ-процентный ресурс рельсов Р65 для участка второго класса при Рос = 140 кН (табл. 2.10). Тогда для звеньевой конструкции пути получим:
|
|
R |
1,2 |
|
|
|
R |
1,2 |
||
Tср = 700 |
|
cр |
|
и Tγ = 550 |
|
|
cр |
. |
||
1000 |
|
|
|
|||||||
|
|
|
|
1000 |
|
|||||
Для бесстыкового пути: |
|
|
|
|
|
|
|
|||
|
|
R |
1,13 |
|
|
|
R |
1,13 |
||
Tср = 1100 |
|
cр |
|
и Tγ = 875 |
|
cр |
. |
|||
1000 |
1000 |
|||||||||
|
|
|
|
|
|
Результаты расчета сведем в табл. 2.10.
56
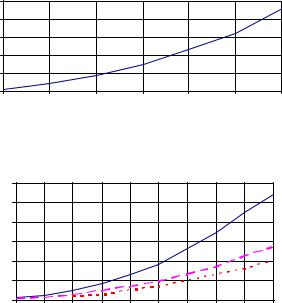
шт. |
5 |
|
|
|
|
|
|
4 |
|
|
|
|
|
|
|
рельсов, |
|
|
|
|
|
|
|
3 |
|
η = 0,00044T |
1,5 |
|
|
|
|
2 |
|
|
|
|
|||
|
|
|
|
|
|
||
Выход |
1 |
|
|
|
|
|
|
0 |
|
|
|
|
|
|
|
|
|
|
|
|
|
|
|
|
100 |
200 |
300 |
400 |
500 |
600 |
700 |
|
|
|
Пропущенный тоннаж, млн. т |
|
|
Рис. 2.12. Выход рельсов в зависимости от пропущенного тоннажа, |
||||||||||
|
|
R = 600–1000 м, Р65, Рос = 160 кН |
|
|
|
|||||
|
6 |
|
|
|
|
|
|
|
|
|
шт. |
5 |
|
|
|
|
|
|
|
|
|
|
|
|
|
|
|
|
|
|
|
|
рельсов, |
4 |
|
|
|
P |
= 180 кН |
|
|
|
|
3 |
|
|
|
|
|
|
||||
|
|
|
|
|
P |
= 155 кН |
|
|||
|
|
|
|
|
|
|
||||
Выход |
2 |
|
|
|
|
|
|
|||
|
|
|
|
|
|
|
|
|
||
1 |
|
|
|
|
|
P = 119 кН |
|
|||
|
0 |
|
|
|
|
|
|
|||
|
|
|
|
|
|
|
|
|
|
|
|
100 |
200 |
300 |
400 |
500 |
600 |
700 |
800 |
900 |
1000 |
|
|
|
Пропущенный тоннаж, млн. т |
|
|
|
Рис 2.13. Сводный график выхода рельсов в зависимости от пропущенного тоннажа, Р65, на прямых участках с различными осевыми нагрузками
Периодичность замены рельсов по боковому износу в кривых. Для определения основных факторов, оказывающих наибольшее влияние на интенсивность бокового износа рельсов, и выявления характера этого влияния на нескольких участках, были выполнены наблюдения за боковым износом рельсов и изменением параметров рельсовой колеи.
Таблица 2.10
Срок службы рельсов, млн т бр.
Конструкция |
|
|
Радиус кривой, м |
|
||
Срок службы рельсов |
|
|
|
1000 и |
||
пути |
400 |
600 |
800 |
|||
|
более |
|||||
|
|
|
|
|
||
Звеньевая |
Тср |
231 |
378 |
535 |
700 |
|
Тγ |
181 |
297 |
421 |
550 |
||
|
||||||
Бесстыковая |
Тср |
368 |
616 |
858 |
1100 |
|
Тγ |
293 |
490 |
682 |
875 |
||
|
Опытные участки находились на Западно-Сибирской железной дороге, где лежали термоупрочненные рельсы Р65 длиной 25 м, деревянные шпалы в количестве 2000 шт./км, щебеночный балласт, преобладали кривые радиусом 400–800 м с уклонами продольного профиля 6–9 ‰, грузонапряженность участка 75 млн т бр, средняя скорость движения 60 км/ч.
Измерения проводились на протяжении трех звеньев каждой кривой, в сечениях десятой, двадцатой и тридцатой шпал. В этих точках определялись возвышение наружного рельса с помощью шаблона ЦУЦ, боковой и вертикальный износ наружного и вертикальный износ внутреннего рельсов универсальным штангенциркулем «Путеец» (износ измерялся на 6-ти звеньях — в 18-ти точках) и углы наклона подошв наружного и внутреннего рельсов уровневым прибором.
Анализ результатов наблюдений на опытных кривых, а также результатов других исследований, позволил получить зависимость интенсивности бокового износа рельсов от основных факторов. Так, если за основу взять кривые радиусом R = 100 м. При средней осевой нагрузке подвижного состава Р = 170 кН/ось, твердости рельсов 350НВ, при уклонах продольного профиля i = 9 % в отсутствие смазки рельсов, то зависимость величины бокового износа рельсов от пропущенного тоннажа Т примет вид [35]
hб = 0,07T. |
(2.14) |
Иные условия эксплуатации должны учитываться специальными коэффициентами.
Основным фактором, влияющим на интенсивность износа рельсов, является радиус кривой. Анализ имеющихся данных, позволил получить зависимость интенсивности бокового износа от радиуса кривых
KR = (400/R)2. |
(2.15) |
Важным фактором, влияющим на интенсивность износа рельсов, являются осевые нагрузки подвижного состава.
57

Аппроксимация имеющихся данных позволила получить выражение для коэффициента, учитывающего влияние осевых нагрузок на интенсивность бокового износа рельсов
КР = (P/170)0,55. |
(2.16) |
Третьим существенным фактором, влияющим на интенсивность износа рельсов, является их твердость. Согласно ГОСТ Р 51685–2000 термоупрочненные рельсы должны иметь твердость в пределах 321–401 НВ. Аппроксимация полученных данных позволила найти выражение для коэффициента, учитывающего интенсивность износа от твердости рельсов в единицах по Бринеллю «НВ»
КHB = (350/НВ)3,5. |
(2.17) |
По мере увеличения уклонов затяжных подъемов и спусков тяговые и тормозные нагрузки на локомотивы увеличиваются, увеличивается относительное искажение их колес, а, следовательно, интенсивность износа рельсов. Аппроксимация имеющихся данных позволила получить выражение для коэффициента, учитывающего влияние крутизны уклона продольного профиля на интенсивность бокового износа рельсов
Кi = (i/9)0,3. |
(2.18) |
Величина коэффициента Кс, учитывающего снижение интенсивности бокового износа рельсов при применении смазки, находится в пределах от 0,5 до 0,9. Значение Кс = 0,5 можно получить при установке напольных лубрикаторов в начале каждой кривой и непрерывном их функционировании, чего добиться весьма сложно, или 2–3-кратном проходе электровозов рельсосма-зывателей с расходом смазки типа РП в количестве 500–700 г/км. Обычно Кс = 0,8–0,9.
Таким образом, интенсивность бокового износа рельсов зависит от следующих основных факторов
hб = 0,01KRKHBКРКiКсТ. |
(2.19) |
Управляемыми факторами здесь являются твердость и смазка рельсов. В соответствии с зависимостью (2.19) увеличение радиуса кривой от 300 до 600 м приводит к снижению интенсивности бокового износа рельсов в 4 раза. Снижение осевых нагрузок от 170 кН до 90 кН приводит к снижению интенсивности износа на 30 %. Увеличение твердости рельсов с 350 до 400 НВ снижает интенсивность износа на 37 %.
Увеличение уклонов затяжных подъемов и спусков в 2 раза приводит к возрастанию интенсивности износа на 23 %. Смазка рельсов имеющимися средствами снижает интенсивность износа на 10–20 %.
Сроки службы рельсов в кривых по износу. Тоннаж, который можно пропустить по кривой до достижения предельного износа рельсов наружной нити кривой можно определять по зависимости
T = |
hб |
|
0,07KR KHB KP Ki Kс . |
(2.20) |
При hб = 15 мм; KR = (400/R)2; КHB = (350/НВ)3,5; КР = (Р/170)0,55 и Кi = = (i/9)0,3 из (2.20) получим
Т = 214,3(R/400)2(HB/350)3,5(170/P)0,55(9/i)(1/Kc). |
(2.21) |
Определим тоннаж, который можно пропустить по кривым до смены наружной нити, при Р = 170 кН и Р = 90 кН.
Значение остальных коэффициентов примем равными единице, в этом случае при Р = 170 кН
T = 214,3(R/400)2 = 1,34·10–3R2. |
(2.22) |
При Р = 90 кН |
|
T = 304,3(R/400)2 = l,9 · 10–3R2. |
(2.23) |
Тоннаж, который можно пропустить по кривым до смены наружной нити, приведен в табл. 2.11. При этом расчет выполнен при отсутствии лубрикации Кс = 1 и при наличии Кс = 0,5.
Таблица 2.11
|
|
Тоннаж который можно пропустить по кривой, до предельного |
|||||||||
|
|
|
|
|
износа рельсов наружной нити |
|
|
||||
|
|
|
|
|
|
|
|
|
|
|
|
Осевая нагрузка, кН |
|
|
|
Радиус кривой, м |
|
|
|
|
|||
|
|
|
|
|
|
|
|
|
|
|
|
250 |
300 |
350 |
400 |
|
450 |
500 |
550 |
600 |
650 |
|
|
|
|
|
|||||||||
|
|
|
|
|
|
|
|
|
|
|
|
|
|
При отсутствии лубрикации |
|
|
|
|
|
||||
|
|
|
|
|
|
|
|
|
|
|
|
170 |
83,7 |
120,5 |
164,1 |
214,3 |
|
271,2 |
334,8 |
406,2 |
482,2 |
565,9 |
|
|
|
|
|
|
|
|
|
|
|
|
|
90 |
118,9 |
171,1 |
230,0 |
304,3 |
|
385,2 |
475,4 |
576,8 |
684,7 |
803,6 |
|
|
|
|
|
|
|
|
|
|
|
|
|
|
|
При наличии лубрикации |
|
|
|
|
|
||||
|
|
|
|
|
|
|
|
|
|
|
|
170 |
167,4 |
241,0 |
328,2 |
428,6 |
|
542,4 |
669,6 |
812,4 |
964,4 |
131,8 |
|
|
|
|
|
|
|
|
|
|
|
|
|
90 |
237,8 |
342,2 |
460,6 |
608,6 |
|
770,4 |
950,8 |
1153,6 |
1369,4 |
607,2 |
|
|
|
|
|
|
|
|
|
|
|
|
|
В соответствии с Положением о системе ведения путевого хозяйства на железных дорогах Российской Федерации, утвержденном министром путей сообщения 27.04.2001 г., в кривых участках пути в период
58
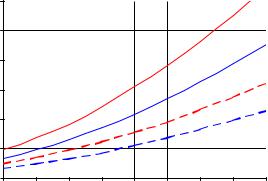
между усиленными капитальными ремонтами пути предусматривается дополнительная сплошная смена рельсов с периодичностью, приведенной в табл. 2.12.
Таблица 2.12
|
Периодичность дополнительных сплошных замен рельсов |
||
|
|
в кривых участках пути |
|
|
|
|
|
|
Количество дополнительных сплошных смен рельсов в кривых |
|
|
Группа пути |
в зависимости от радиуса кривой при наличии лубрикации рельсов |
|
|
|
351–650 м |
350 м и менее |
|
|
|
|
|
Б, В |
1 раз |
2 раза |
|
|
|
|
|
Г, Д |
— |
1 раз |
|
|
|
|
|
Используя данные табл. 2.12 подсчитаем количество дополнительных смен рельсов в кривых при нормативном тоннаже для звеньевого пути на деревянных шпалах Тн = 600 млн т бр.
п = Тн/Т – 1. |
(2.14) |
Результаты расчета приведены в табл. 2.13.
|
1500 |
|
|
|
|
|
|
|
|
|
|
|
|
|
|
P = 90 кН |
|
|
|
т |
1250 |
|
|
|
|
|
|
|
|
|
|
|
|
|
|
|
P = 170 кН |
|
|
млн. |
|
|
|
|
|
|
|
|
|
1000 |
|
|
|
|
|
|
|
|
|
тоннаж, |
750 |
|
|
|
|
|
|
P = 90 кН |
|
|
|
|
|
|
|
|
|
||
|
|
|
|
|
|
|
|
|
|
Наработанный |
500 |
|
|
|
|
|
|
|
|
|
|
|
|
|
|
|
P = 170 кН |
||
250 |
|
|
|
|
|
|
|
|
|
|
|
|
|
|
|
|
|
|
|
|
0 |
|
|
|
|
|
|
|
|
|
250 |
300 |
350 |
400 |
450 |
500 |
550 |
600 |
650 |
|
|
|
|
Радиус кривой, м |
|
|
|
– — – — без лубрикации; ––––––––– с лубрикацией.
Рис. 2.14. Периодичность замены рельсов по износу в наружных нитях кривых
59

Таблица 2.13
|
|
Количество дополнительных замен рельсов по износу в кривых |
|||||||||
|
|
|
|
в межремонтный период (Тн = 600 млн т бр.) |
|||||||
|
|
|
|
|
|
|
|
|
|
|
|
Осевая нагрузка, кН |
|
|
|
|
Радиус кривой, м |
|
|
|
|
||
|
|
|
|
|
|
|
|
|
|
|
|
|
250 |
300 |
350 |
|
400 |
450 |
500 |
550 |
600 |
650 |
|
|
|
при отсутствии лубрикации |
|
|
|
|
|
||||
|
|
|
|
|
|
|
|
|
|
|
|
170 |
6 |
4 |
3 |
|
2 |
1 |
1 |
1 |
0 |
0 |
|
|
|
|
|
|
|
|
|
|
|
|
|
90 |
4 |
3 |
2 |
|
1 |
1 |
0 |
0 |
0 |
0 |
|
|
|
при наличии лубрикации |
|
|
|
|
|
||||
|
|
|
|
|
|
|
|
|
|
|
|
170 |
3 |
2 |
1 |
|
0 |
0 |
0 |
0 |
0 |
0 |
|
|
|
|
|
|
|
|
|
|
|
|
|
90 |
2 |
1 |
0 |
|
0 |
0 |
0 |
0 |
0 |
0 |
|
|
|
|
|
|
|
|
|
|
|
|
|
Анализ табл. 2.13 показывает преимущество приведенной здесь методики определения периодичности замен рельсов наружной рельсовой нити в кривых. Сравнительный анализ показывает, что в кривых радиусом менее 670 м срок службы рельсов определяется боковым износом, и в кривых большего радиуса — накопленным одиночным выходом.
Таким образом, анализ многочисленных экспериментальных данных показал, что к основным факторам, влияющим на интенсивность бокового износа рельсов относятся: радиус кривых, твердость рельсов, осевые нагрузки подвижного состава, уклоны продольного профиля на затяжных подъемах и спусках и смазка боковых граней рельсов.
Прогнозирование годового выхода рельсов на участке
Основной задачей ведения рельсовой хозяйства дороги является снижение количества отказов рельсов [36].
Для прогнозирования отказов рельсов по эмпирическим зависимостям используем степенную функцию (2.11).
Влияние кривизны пути и осевых нагрузок на выход рельсов учитывается коэффициентами КR и КP.
|
|
|
1000 |
δ |
|
= |
Rcр |
γ |
, R = |
∑Rili |
|
||
K |
R |
= |
|
|
, K |
P |
|
|
|
∑li |
, |
||
|
|
||||||||||||
|
|
Rcр |
|
|
|
160 |
ср |
|
|||||
|
|
|
|
|
|
|
|
|
|
|
где Ri и li — соответственно радиус и длина i-й кривой. На прямых участках условно принимается радиус R = 1000 м.
Выход рельсов на километре пути за год при грузонапряженности Г составит
Δη(Г) = α (T + Г)β −T |
β K |
R |
K |
P |
. |
|
(2.25) |
|||||||
|
|
|
|
|
|
|
|
|
||||||
После преобразований при β = 1,5 получим |
|
|
|
|
|
|
|
|||||||
|
0,5 |
|
|
à |
|
|
|
|
|
|
|
|||
Δη(Ã) = 1,5αT |
|
à 1+ 0, 25 |
|
|
|
KR KP . |
|
(2.26) |
||||||
|
Ò |
|
|
|||||||||||
|
|
|
|
|
|
|
|
|
|
|
||||
Суммарный выход рельсов за год на участке L = Σli при α = 4.10-4 (звеньевой путь) составит |
||||||||||||||
|
|
|
|
|
à |
|
|
|
|
|
||||
∑Δηi = 6 10−4Tñð0,5 Ã 1+ 0, 25 |
KR KP |
, |
(2.27) |
|||||||||||
|
||||||||||||||
|
|
|
|
Ò |
|
|
|
|
|
|
|
|||
|
|
|
|
ñð |
|
|
|
|
|
|
∑T l K |
|
где Тср = |
j j Rj |
— средневзвешенный тоннаж на участке L, состоящем из локальных участков длиной lj |
∑lj KRj |
с наработанным тоннажем Тj и коэффициентом приведенной кривизны пути КRj.
На рис. 2.15 приведен суммарный выход рельсов за год на участке длиной L = 100 км при КRj = 1 и КP = 1. Увеличение средневзвешенного возраста пути (наработанного тоннажа) приводит к существенному росту отказов рельсов, особенно при высокой грузонапряженности.
Существенное влияние на годовой выход рельсов оказывают приведенный радиус кривизны пути и средние осевые нагрузки подвижного состава (рис. 2.16). Особенно велико влияние этих факторов при приведенной кривизне пути менее 600 м.
60
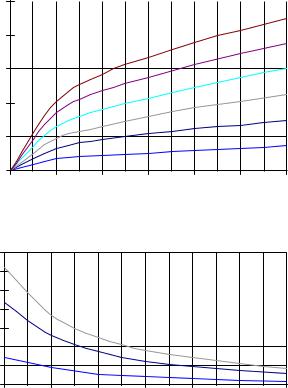
|
100 |
|
|
|
|
|
|
шт. |
|
|
|
|
|
Г = 60 млн |
|
80 |
|
|
|
|
ткм/км в год |
|
|
|
|
|
|
Г = 50 млн |
|
||
за год, |
|
|
|
|
|
|
|
|
|
|
|
|
ткм/км в год |
|
|
60 |
|
|
|
|
Г = 40 млн |
|
|
рельсов |
|
|
|
|
|
ткм/км в год |
|
40 |
|
|
|
|
Г = 30 млн. |
|
|
|
|
|
|
ткм/км в год |
|
||
|
|
|
|
|
Г = 20 млн |
|
|
Выход |
20 |
|
|
|
|
ткм/км в год |
|
|
|
|
|
Г = 10 млн |
|
||
|
|
|
|
|
|
||
|
|
|
|
|
ткм/км в год |
|
|
|
|
|
|
|
|
|
|
|
0 |
|
|
|
|
|
|
|
0 |
100 |
200 |
300 |
400 |
500 |
600 |
|
|
Наработанный тоннаж, млн т бр. |
|
|
Рис. 2.15. Суммарный выход рельсов за год на 100 км пути |
|
||||||
|
14 |
Р ср = 200 кН |
|
|
|
|
|
|
|
12 |
|
|
|
|
|
||
КR |
|
|
|
|
|
|
|
|
10 |
|
|
|
|
|
|
|
|
Коэффициент |
Р ср = 160 кН |
|
|
|
|
|
||
8 |
|
|
|
|
|
|||
|
|
|
|
|
|
|
||
6 |
|
|
|
|
|
|
|
|
4 |
Р ср = 80 кН |
|
|
|
|
|
|
|
2 |
|
|
|
|
|
|
|
|
|
0 |
|
|
|
|
|
|
|
|
|
300 |
400 |
500 |
600 |
700 |
800 |
900 |
|
|
|
Приведенный радиус кривизны, м |
|
Рис. 2.16. Влияние приведенной кривизны пути на одиночный выход рельсов
2.7. Совершенствование системы ведения рельсового хозяйства
Перспективы развития отрасли и рост грузонапряженности таковы, что в настоящее время важнейшей проблемой становится предоставление «окон» для ремонта пути. Одно из направлений ее решения — увеличение межремонтных сроков.
Как известно, главным критерием назначения усиленного капитального ремонта (УК) служит одиночный выход рельсов из строя (в сумме за срок службы — в среднем на участке ремонта). Этот показатель для линий первого класса составляет 4 шт./км и более, для линий второго класса — 6 шт./км и более. Такой подход в определенной мере был оправдан в 70–80-е годы прошлого столетия, когда основной причиной одиночного изъятия рельсов из пути являлись дефекты контактно-усталостного характера (11.1-2; 21.1-2; 30В; 30Г). Их доля на грузонапряженных участках составляла 60 % и более в общем числе изъятых рельсов. В 1995– 2005 гг. она стала менее 30 %. При этом нужно иметь в виду, что фактическая доля еще меньше, так как перебраковка рельсов (т.е. отсутствие дефекта в рельсах, изъятых по показаниям средств дефектоскоп-ного контроля) по дефекту 21.1-2 в настоящее время составляет 20 % и более. В то же время существенно возрос их выход из строя по дефекту 17 — отслоение и выкрашивание металла в стыке при отсутствии наплавки — более 20 тыс. в год или 20 % от общего числа изъятых. На долю дефекта 14 — термомеханические повреждения поверхности катания вследствие буксования колес подвижного состава приходится до 10 %, на дефекты в сварных стыках — более 5 % (а при учете протяженности бесстыкового пути — более 12 % дефектов рельсов такого пути). По-прежнему велик выход по дефекту 44 — боковой износ более нормативных значений — около 15 % общего числа изъятых рельсов; однако при этом не учитывается сплошная смена рельсов из-за данного дефекта, их перекладка с переменой рабочего канта из кривых в прямые участки пути и т.д.
Более 12 % рельсов изымается по дефектам 10, 20, 30 заводского происхождения.
Приведенный анализ позволяет сформулировать следующие два основных направления повышения эффективности ведения рельсового хозяйства [28].
1. Пересмотр дифференцированных норм одиночного изъятия рельсов, являющихся критериями назначения усиленного капитального ремонта пути.
На взгляд авторов [28] при определении предельного одиночного выхода необходимо учитывать только дефекты контактно-усталостного происхождения, образование которых носит не случайный характер, а следует определенным закономерностям.
61
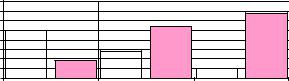
2. Совершенствование системы ведения рельсового хозяйства с целью предотвращения других дефектов или существенного отдаления момента их зарождения и замедления развития. Так, причины возникновения дефекта 17 заключаются как в технологии производства, так и в содержании пути. Сократить количество рельсов, пораженных этим дефектом, можно за счет увеличения протяженности бесстыкового пути. Для снижения потерь из-за появления дефекта 14 нужно предъявлять рекламации тем хозяйствам транспорта, по вине которых путейцы несут неоправданные потери. Рельсы с дефектом 17 надо наплавлять на начальном этапе его развития. Технологию ВНИИЖТ отработал, она внедрена на ряде дорог.
Для недопущения дефектов сварки следует усовершенствовать ее технологию, учитывая при этом изменение химического состава рельсовой стали и способы ее выплавки. Существенно ухудшает качество сварных стыков такой фактор, как концевая искривленность рельсов. Важно ужесточить входной их контроль в РСП.
Дефекты контактно-усталостного происхождения не появятся в головке, если съем металла по рабочей грани в результате бокового износа и профильного шлифования будет соответствовать значениям γбопт, которые зависят
от радиуса кривых (табл. 2.14). Интенсивность бокового износа рельсов можно оптимизировать, сочетая профильное шлифование с дозированной мубрикацией (при этом γбфакт = γбопт) за период с 1998 г. по 2003 г. во
ВНИИЖТе исследовали влияние износа и шлифования рельсов на их изъятие по дефектам контактноусталостного характера. Оказалось, что при γбопт указанных дефектов практически не бывает.
Таблица 2.14
Оптимальный съем металла в результате бокового износа и профильного шлифования рельсов в кривых различного радиуса
R, м |
γбопт, мм/млн т бр. |
< 350 |
> 0,05 |
351–500 |
> 0,04 |
501–650 |
> 0,03 |
Поскольку максимальный боковой износ не должен превышать 15 мм (по ТУ рельсы с боковым износом более 15 мм перекладывать нельзя), при износе 5 мм/100 млн т бр. срок службы рельсов в кривых радиусом менее 400 м должен составлять 300 млн т, но в настоящее время он в 2–4 раза меньше.
Для достижения межремонтного тоннажа в 1 млрд т и более в прямых, а также 500 млн т в кривых радиусом менее 400 м необходимо, чтобы контактно-усталостные дефекты в кривых R < 400 м не зарождались при износе 0,025–0,030 мм/млн т груза. Эту задачу можно решить, во-первых, повысив чистоту рельсовой стали, во-вторых, улучшив состояние пути, в том числе за счет геометрических параметров элементов верхнего строения и качества сборки рельсошпальной решетки, что позволит уменьшить напряжения в головке рельсов от воздействия подвижного состава.
Однако только лишь избавляясь от контактно-усталостных дефектов, проблему не решить, необходима технико-экономическая оценка сочетания этих дефектов и бокового износа. В качестве примера на рис. 2.17 приведены данные о сочетании дефектов 21 и 44 в кривых различного радиуса в зависимости от интенсивности износа рельсов. Имея такие зависимости, можно своевременно принять меры по замедлению износа, в том числе лубрикацией, или ускорить его, например, шлифовкой, и определить, окупаются ли соответствующие затраты снижением выхода рельсов из строя.
С целью продления срока службы рельсов, уменьшения расходов на содержание пути ВНИИЖТ разрабатывает Положение о системе ведения рельсового хозяйства на железных дорогах ОАО «РЖД», структура которого представлена на рис. 2.18 но определяет принципы, технические параметры и нормативы по заказу и приобретению рельсов на металлургических комбинатах, их содержанию, а также ремонту в пути и в условиях РСП.
) |
80 |
|
|
|
|
70 |
|
|
54 |
|
|
|
50 |
|
|
||
|
60 |
|
68 |
||
% |
|
|
|||
50 |
|
|
|
||
|
|
|
|
||
Доля, |
40 |
|
|
28 |
|
30 |
|
18 |
10 |
|
|
20 |
|
|
|
||
|
10 |
|
|
|
|
|
0 |
|
|
|
|
|
|
0,01 |
|
0,03 |
0,05 |
|
|
|
Интенсивность износа, мм/млн т бр. |
|
62