
669
.pdf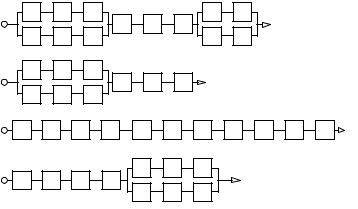
Рис. 3.12. Структурные схемы для расчета надежности рельсовых скреплений: а — для расчета надежности скрепления КБ:
1к — болты клеммные; 2к — клеммы; 3к — шайбы клеммные; 1п — прокладки резиновые под рельс (подрельсовые); 2п — подкладки; 3п — прокладки под подкладки (нашпальные); 1з — болты закладные; 2з — шайбы закладных болтов; б — для расчета надежности скреплений КН:
1з — болты закладные; 2з — клеммы; 3з — прижимные скобы; 1п — прокладки резиновые под рельс (подрельсовые); 2п — подкладки; 3п — прокладки под подкладками (нашпальные);
в — для расчета надежности скреплений ЖБР:
1з — болты закладные; 2з — боковые упоры; 3з — клеммы; 4з — подклеммники; 5з — прижимные скобы; 1в — прокладки резиновые под рельс;
г— для расчета надежности скреплений АРС:
1 — анкеры; 2 — изолирующие уголки; 3 — подрельсовые прокладки; 1з — монорегуляторы; 2з — клеммы; 3з — изоляторы
При составлении структурных схем исходным было положение, что система последовательно соединенных элементов работоспособна тогда и только тогда, когда работоспособны ее элементы. Вероятность безотказной работы системы из последовательно соединенных элементов определим по формуле (3.38).
При параллельном соединении отказ системы происходит тогда и только тогда, когда откажут все параллельные участки схемы. Вероятность безотказной работы участков схемы, состоящей из параллельных цепей, определим по формуле (3.39).
При составлении структурных схем для подкладочных скреплений КБ и КН учитывалось то, что подкладки объединяют работу прикрепителей (клеммных и закладных болтов). Отказ узла скреплений в экстремальных условиях эксплуатации произойдет тогда, когда откажут обе параллельные цепи элементов прикрепителей. У бесподкладочных скреплений ЖБР отказ узла скреплений наступит при отказе любого из его элементов.
Вероятность безотказной работы узлов рельсовых скреплений определяем по формулам:
– для узлов скреплений типа КБ
|
|
− |
1− |
3 |
|
2 |
− |
1− |
2 |
|
2 |
3 |
|
P = 1 |
P |
1 |
P |
|
P ; |
(3.40) |
|||||||
y |
|
|
|
∏ i |
|
|
|
|
∏ i |
|
|
∏ i |
|
|
|
|
|
i=1 |
|
|
|
|
i=1 |
|
|
i=1 |
|
– для узлов скреплений типа КН
|
|
− |
1− |
3 |
|
2 |
3 |
|
P = 1 |
P |
|
P ; |
(3.41) |
||||
y |
|
|
|
∏ i |
|
|
∏ i |
|
|
|
|
|
i=1 |
|
|
i=1 |
|
– для узлов скреплений типа ЖБР
|
|
|
|
11 |
|
|
|
|
|
|
|
Py |
= ∏Pi |
; |
|
|
(3.42) |
||
|
|
|
|
i=1 |
|
|
|
|
|
– для узлов скреплений типа АРС |
|
|
|
|
|
||||
|
|
− 1 |
− |
3 |
|
2 |
|
3 |
|
P = 1 |
P |
|
|
P . |
(3.43) |
||||
y |
|
|
|
∏ i |
|
|
|
∏ i |
|
|
|
|
|
i=1 |
|
|
|
i=1 |
|
Однако отказ узла скрепления еще не означает отказа всей системы связей рельса с основанием. Согласно нормативным документам, поперечная устойчивость рельсовых нитей и всей рельсошпальной решетки обеспечивается, если нет кустов из трех негодных шпал, а рельсовая нить не расшита более чем на трех шпалах подряд. Справедливость этих требований подтверждается результатами, проведенных в последнее время.
83
Для расчета надежности скреплений КБ, КН, ЖБР и АРС использованы статистические данные наших наблюдений, а также опубликованные данные [40, 52].
Частота отказов элементов скрепления приведена в табл. 3.8. Используя эти данные, определим значения Тср и σt (табл. 3.9).
Таблица 3.8
Частота отказов элементов скреплений, %
|
Наработанный тоннаж, млн т бр. |
|
|
|
Элементы скреплений |
|
|
|
||
Тип скрепления |
|
|
|
|
|
|
|
|
|
|
Клемма |
Подкладка |
Болт клеммный с шайбой |
Болт закладной с шайбой |
Анкер АРС |
Прокладка подрельсовая |
Прокладка нашпальная |
Прокладка подупорную скобу |
Уголок изолирующий |
||
|
|
|
|
|
|
|
|
|
|
|
|
100 |
0 |
0 |
0,7 |
0,6 |
– |
6 |
46 |
– |
– |
КБ |
500 |
0,2 |
6 |
1 |
1 |
– |
39 |
70 |
– |
– |
|
800 |
0,3 |
10 |
1,2 |
1,2 |
– |
100 |
100 |
– |
– |
|
100 |
0,2 |
0 |
– |
0,2 |
– |
3 |
0 |
– |
– |
КН |
500 |
0,5 |
9 |
– |
0,5 |
– |
8 |
6 |
– |
– |
|
800 |
1,5 |
14 |
– |
1,2 |
– |
18 |
10 |
– |
– |
|
100 |
0,2 |
0,5 |
– |
0,2 |
– |
0,2 |
0 |
– |
– |
КНУ |
500 |
0,5 |
5 |
– |
0,6 |
– |
0,5 |
0,5 |
– |
– |
|
800 |
1 |
9 |
– |
1,3 |
– |
1,5 |
1 |
– |
– |
|
100 |
0,3 |
– |
– |
0,5 |
– |
3,5 |
– |
5 |
– |
ЖБР |
500 |
2 |
– |
– |
2 |
– |
8 |
– |
15 |
– |
|
800 |
2,3 |
– |
– |
7 |
– |
18 |
– |
50 |
– |
|
100 |
0,5 |
– |
– |
– |
0 |
3,5 |
– |
– |
4 |
АРС |
500 |
1 |
– |
– |
– |
0 |
8 |
– |
– |
40 |
|
800 |
2 |
– |
– |
– |
1 |
18 |
– |
– |
100 |
Таблица 3.9
Параметры Тср и σt элементов скреплений, млн т бр.
Элемент |
|
|
|
|
Тип скреплений |
|
|
|
|
||
КБ-65 |
КН-65 |
КНУ-65 |
ЖБР-65 |
АРС-4 |
|||||||
скрепления |
|||||||||||
Тср |
σt |
Тср |
σt |
Тср |
σt |
Тср |
σt |
Тср |
σt |
||
|
|||||||||||
Клемма |
7141,5 |
2307,7 |
3680,9 |
1228,4 |
3723,2 |
1243,6 |
2210,4 |
773,1 |
3214,8 |
1172,4 |
|
Подкладка |
1011,8 |
250,2 |
932,9 |
228,5 |
1405,7 |
499,7 |
– |
– |
– |
– |
|
Болт клеммный с шайбой |
10348 |
4173,4 |
– |
– |
– |
– |
– |
– |
– |
– |
|
Болт закладной с шайбой |
7494,9 |
2945,6 |
3680,9 |
1228,4 |
3635,8 |
1233,1 |
1694,1 |
595,7 |
– |
– |
|
Анкер АРС |
– |
– |
– |
– |
– |
– |
– |
– |
1646,4 |
363,9 |
|
Прокладка подрельсовая |
435,6 |
89,2 |
1480 |
724,1 |
2222,1 |
649,4 |
1530,6 |
771,7 |
1530,6 |
771,7 |
|
Прокладка нашпальная |
450,5 |
94,5 |
1011,8 |
250,2 |
1849,9 |
478,2 |
– |
– |
– |
– |
|
Прокладка под скобу |
– |
– |
– |
– |
– |
– |
834 |
411 |
– |
– |
|
Уголок изолирующий |
– |
– |
– |
– |
– |
– |
– |
– |
489,4 |
117,1 |
Вероятность безотказной работы элементов скреплений приведена в табл. 3.10.
84
85
86
87
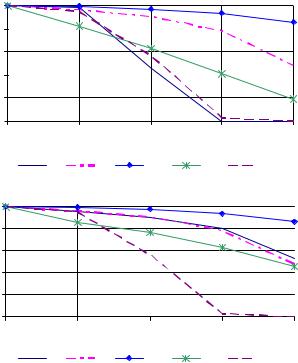
Вероятности безотказной работы узлов рельсовых скреплений, определенные в соответствии со структурными схемами (рис. 3.12) по формулам (3.40–3.43), приведены в табл. 3.10.
Из анализа данных табл. 3.10 следует, что наибольшей вероятностью безотказной работы обладают скрепления типа КНУ, а наименьшей — скрепления типа КБ и АРС.
Опыт эксплуатации скреплений КБ-65 на железобетонных шпалах показал, что после пропуска по участку с этими скреплениями 400–600 млн т бр. груза происходит отказ 20–30 % электроизолирующих деталей. Удельное сопротивление подрельсового основания снижается до 0,2–0,25 Ом·км, что ведет к отказу рельсовых цепей. Это подтверждается результатами расчетов, приведенными в табл. 3.11 и на рис. 3.13, а.
Таблица 3.11
Численные значения вероятности безотказной работы узлов скреплений
Тип скрепления |
|
Вероятности безотказной работы, при наработке тоннажа, млн т бр. |
||||||||||
|
по фактическим данным |
|
после повышения надежности |
|||||||||
|
|
об отказах элементов |
|
|
отдельных элементов |
|
||||||
0 |
|
200 |
400 |
600 |
|
800 |
0 |
200 |
400 |
600 |
800 |
|
|
|
|
|
|
|
|
|
|
|
|
|
|
КБ |
1 |
|
0,991 |
0,457 |
0,002 |
|
0 |
1 |
0,960 |
0,907 |
0,801 |
0,530 |
|
|
|
|
|
|
|
|
|
|
|
|
|
КН |
1 |
|
0,96 |
0,905 |
0,782 |
|
0,476 |
1 |
0,96 |
0,905 |
0,782 |
0,476 |
|
|
|
|
|
|
|
|
|
|
|
|
|
КНУ |
1 |
|
0,992 |
0,974 |
0,936 |
|
0,862 |
1 |
0,992 |
0,974 |
0,936 |
0,862 |
ЖБР |
1 |
|
0,825 |
0,631 |
0,408 |
|
0,191 |
1 |
0,860 |
0,762 |
0,627 |
0,460 |
АРС |
1 |
|
0,945 |
0,561 |
0,026 |
|
0 |
1 |
0,945 |
0,561 |
0,026 |
0 |
Анализ данных табл. 3.8–3.10 показывает, что наибольшую частоту отказов у скреплений КБ имеют подрельсовые и нашпальные прокладки. При повышении надежности этих элементов до уровня КН надежность узлов скреплений КБ можно существенно повысить при значительно большей наработке по сравнению с имеющейся в настоящее время (рис. 3.13, б).
Ускреплений типа КН высокую интенсивность отказов имеют металлические подкладки. При повышении надежности этих элементов эффективность работы скреплений типа КН будет еще выше.
Ускрепления ЖБР недостаточную надежность имеют подрельсовые прокладки и прокладки под упорную скобу. При доведении надежности этих элементов до уровня подрельсовых прокладок КН (рис. 3.13, б) уровень надежности этого скрепления в диапазоне наработки 200–600 млн т бр. груза будет все равно ниже, чем у скреплений КН и КНУ. Объясняется это худшей схемой надежности узлов этих скреплений. Подкладки КБ, КН и КНУ объединяют работу двух закладных болтов и цепи этих элементов являются дублирующими. Большую роль играет также качество изготовления элементов, особенно упругих клемм.
Низкая надежность скрепления АРС объясняется низкой надежностью изолирующих уголков с обеих сторон подошвы рельса. Происходит это из-за высокой горизонтальной жесткости скреплений и недостатками конструкции изоляции подошвы рельса от анкеров и упругих клемм.
а) |
|
|
|
|
|
|
1 |
|
|
|
|
Вероятность |
0,8 |
|
|
|
|
0,6 |
|
|
|
|
|
|
|
|
|
|
|
|
0,4 |
|
|
|
|
|
0,2 |
|
|
|
|
|
0 |
|
|
|
|
|
0 |
200 |
400 |
600 |
800 |
|
|
Пропущенный тоннаж, млн т бр. |
|
||
|
КБ |
КН |
КНУ |
ЖБР |
АРС |
б) |
|
|
|
|
|
|
1 |
|
|
|
|
Вероятность |
0,8 |
|
|
|
|
0,6 |
|
|
|
|
|
|
|
|
|
|
|
|
0,4 |
|
|
|
|
|
0,2 |
|
|
|
|
|
0 |
|
|
|
|
|
0 |
200 |
400 |
600 |
800 |
|
|
Пропущенный тоннаж, млн т бр. |
|
||
|
КБ |
КН |
КНУ |
ЖБР |
АРС |
88
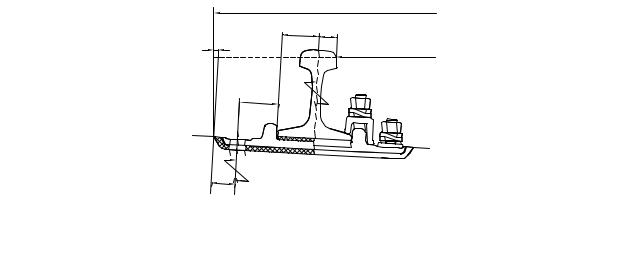
Рис. 3.13. Вероятность безотказной работы скреплений:
а— по фактическим данным об отказах элементов;
б— после повышения надежности отдельных элементов
3.8. Оценка точности сборки путевой решетки при различных конструкциях рельсовых скреплений
Параметры рельсовой колеи во многом определяются точностью сборки путевой решетки на производственных базах ПМС. В свою очередь, точность сборки зависит от разброса размеров деталей, из которых собирается рельсошпальная решетка.
Отклонения размеров элементов пути вызываются производственными причинами и в большинстве случаев проявляются случайно. Поэтому рассеивание действительных размеров деталей определяется законами теории вероятностей.
Наиболее совершенным методом оценки точности сборки путевой решетки является анализ размерных цепей, основанный на теории вероятностей и широко используемый в машиностроении [55, 56]. Размерная цепь — расположенные по замкнутому контуру размеры деталей, влияющие на точность одного из замыкающих размеров контура (ширина колеи). Это звено, формирующееся в последнюю очередь, называется замыкающим, а все остальные звенья, входящие в размерную цепь, — составляющими. Звенья размерной цепи делятся на размеры деталей и на размеры, связывающие поверхности или оси соседних деталей (зазоры).
Геометрическая характеристика рельсовых скреплений
Определение фактических размеров элементов железобетонных шпал и скреплений КБ-65, ЖБР-65, КН65 производилось на Горновском заводе спецжелезобетона и на производственных базах ОПМС-19, ПМС20. Всего было выполнено более 4000 измерений, данные которых затем были подвергнуты статистической обработке.
Определялись геометрические размеры элементов промежуточных рельсовых скреплений и железобетонных шпал, оказывающих наибольшее воздействие на работу рельсошпальной решетки (рис. 3.14): В1 — расстояние между наружными кромками углублений в шпале под подкладками; В2 = В11 — отклонения головки рельса от вертикали в расчетном уровне за счет подуклонки; В3 = В10 — расстояния от наружной кромки углубления в шпале под подкладкой до оси закладного болта; В4 = = В9 — расстояния от оси закладного болта до упорной грани ее реборды; В5 = В8 — расстояния от оси рельса
до упорной грани наружной реборды подкладки; В6 = В7 — размеры половины ширины головки рельса, замеренной на уровне измерения ширины колеи; La — размер между ребордами подкладки; La2 — размер между ребордами упорных планок ЖБР-65; LШ — расстояние между кромками углубления в шпале под подкладками; Lп — размер длины подкладки; М — подуклонка углубления в железобетонной шпале под подкладками;
В качестве параметров указанных размеров определялись: N — номинальный размер элемента; δ — допуск размера; em — середина поля рассеивания допуска размера.
Рис. 3.14. Схема размерной цепи рельсовой колеи
Размеры основных элементов железобетонной шпалы Ш-1 и скрепления КБ-65 представлены в табл. 3.12.
Таблица 3.12
Размеры элементов скрепления КБ-65
Параметры размерной цепи |
Нормативный размер, мм |
Фактический размер, мм |
|||||
N |
δ |
em |
N |
δ |
em |
||
|
|||||||
B1 |
2016 |
4 |
0 |
2016,5 |
4 |
0,5 |
|
В3 |
48 |
2 |
0 |
48,2 |
3 |
0,3 |
|
В4 |
79,5 |
2,5 |
–0,25 |
79 |
2,5 |
–0,25 |
|
В5 |
75,5 |
1 |
0,5 |
76 |
0,75 |
0,12 |
|
B6 |
35,9 |
0,5 |
0 |
35,9 |
0,5 |
0 |
|
La |
151 |
2 |
1 |
151,9 |
1,5 |
–0,15 |
|
LШ |
406 |
3 |
0,5 |
406,5 |
3 |
0 |
|
Lп |
370 |
4 |
0 |
369,4 |
3 |
0,1 |
89
М |
1/20 |
1/18÷1/20 |
|
1/20,03 |
1/18÷1/22,2 |
|
Размеры основных элементов железобетонной шпалы Ш-3 и скрепления ЖБР-65 представлены в табл. 3.13.
Таблица 3.13
Размеры элементов скрепления ЖБР-65
Параметры размерной цепи |
Нормативный размер, мм |
Фактический размер, мм |
|||||
N |
δ |
em |
N |
δ |
em |
||
|
|||||||
B1 |
1968 |
3 |
0 |
1968,7 |
3,5 |
–0,15 |
|
В3 |
64,5 |
2 |
0 |
65 |
2,5 |
–0,25 |
|
В4 |
39 |
2 |
0 |
38,4 |
1,5 |
0,15 |
|
В5 |
76 |
2,08 |
0 |
76,5 |
2,7 |
–0,13 |
|
B6 |
35,9 |
0,5 |
0 |
35,9 |
0,5 |
0 |
|
La2 |
230 |
2 |
0 |
229,8 |
3 |
0,2 |
|
М |
1/20,42 |
1/18÷1/20,2 |
|
1/20,42 |
1/18÷1/22,2 |
|
Размеры основных элементов железобетонной шпалы и скрепления КН-65 представлены в табл. 3.14.
Таблица 3.14
Размеры элементов скрепления КН-65
Параметры размерной цепи |
Нормативный размер, мм |
Фактический размер, мм |
|||||
N |
δ |
em |
N |
δ |
em |
||
|
|||||||
B1 |
2016 |
4 |
0 |
2016,4 |
3 |
0,1 |
|
В3 |
73 |
2 |
0 |
73,4 |
3 |
0,1 |
|
В4 |
54,5 |
2,5 |
–0,25 |
54,2 |
3 |
–0,2 |
|
В5 |
75,5 |
1 |
0,5 |
75,8 |
0,5 |
–0,05 |
|
B6 |
35,9 |
0,5 |
0 |
35,9 |
0,5 |
0 |
|
La |
151 |
2 |
1 |
151,6 |
1,3 |
0,05 |
|
LШ |
406 |
3 |
0,5 |
406,6 |
3 |
–0,1 |
|
Lп |
370 |
4 |
0 |
369,4 |
3 |
0,1 |
|
М |
1/20 |
1/18÷1/20 |
|
1/20,03 |
1/18÷1/22,3 |
|
Статистическая обработка полученных данных позволила сделать анализ точности изготовления элементов промежуточных рельсовых скреплений и железобетонных шпал. Исследование качества изготовления элементов скреплений КБ-65, КН-65, ЖБР-65 и шпал показало отклонение ряда размеров от нормативных требований. Основные отклонения от требований ГОСТов касаются размеров железобетонных шпал, в частности В1, В3, что оказывает влияние на получение требуемой нормы ширины колеи — 1520±2 мм при сборке на базах ПМС.
Методика оценки параметров рельсовой колеи
Параметры рельсовой колеи во многом определяются точностью сборки путевой решетки на производственных базах ПМС. В свою очередь, точность сборки зависит от разброса размеров деталей, из которых собирается рельсошпальная решетка.
Отклонения размеров элементов пути вызываются производственными причинами и в большинстве случаев проявляются случайно. Поэтому рассеивание действительных размеров деталей определяется законами теории вероятностей.
Наиболее совершенным методом оценки точности сборки путевой решетки является анализ размерных цепей, основанный на теории вероятностей и широко используемый в машиностроении [57].
Размерная цепь — расположенные по замкнутому контуру размеры деталей, непосредственно влияющие на точность одного из замыкающих размеров контура (ширина колеи). Это звено, формирующееся в последнюю очередь, называется замыкающим, а все остальные звенья, входящие в размерную цепь, — составляющие. Все звенья размерной цепи делятся на размеры деталей и на размеры, связывающие поверхности или оси соседних деталей (зазоры).
На величину допуска замыкающего звена оказывают влияние зазоры, в пределах которых сопряженные детали имеют возможность смещаться. Принимаем для сопряжения с зазором индекс z.
Смещение осей сопряженных поверхностей Lz
1
Lz = |
|
(La – Lb), |
(3.44) |
2 |
где La и Lb — случайные величины, например, расстояние между ребордами подкладки и ширина подошвы рельса.
Номинальный размер звена–зазора и координата середины поля допуска равны нулю. Величина смещения одной оси относительно другой в пределах зазора является случайной величиной. Погрешность звена– зазора состоит из двух составляющих: систематической и случайной.
Систематическая составляющая погрешности звена–зазора emz зависит от номинальных размеров охватывающей и охватываемой деталей, координат середин полей их допусков:
90
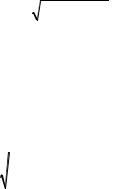
emz = |
1 |
|
[(Na– Nb) + (ema– emb) + (αа |
δa |
– αb |
δb |
)] — αz |
δz |
, (3.45) |
|
|
|
|||||||||
2 |
||||||||||
2 |
2 |
2 |
||||||||
|
|
|
|
|
где Na и Nb — номинальные размеры сопрягаемых деталей.
Случайная составляющая δz зависит от допусков охватывающего и охватываемого размеров деталей:
|
|
|
1 |
|
|
|
|
|
|
|
|
δ |
z |
= |
|
K |
2δ2 |
+ K |
2δ2 . |
(3.46) |
|||
|
|||||||||||
|
|
2KδZ |
|
|
a a |
|
b b |
|
|||
|
|
|
|
|
|
|
|
|
|
При определении допуска замыкающего звена цепи допуски линейных размеров и погрешности звеньев– зазоров суммируются отдельно. Для получения допуска замыкающего звена с некоторым запасом в качестве погрешности звена–зазора принимают максимальное значение радиального зазора:
1
Zmax = emz + 2 δz.
Допуск замыкающего звена размерной цепи, содержащей звенья–зазоры.
|
|
|
|
1 |
|
δ |
|
= |
|
|
|
|||
|
|
ø |
|
KΣ |
|
|
|
|
|
|
|
|
|
|
N − Nz |
Nz |
|
|
|
|
∑ Ki2δi2 |
+ ∑Kzi2 Zmax2 |
i |
|
, |
(3.47) |
|
|
|
|
|
|
i=1 |
i=1 |
|
|
|
|
|
|
|
|
где Кzi — приведенный коэффициент относительного рассеяния расположения деталей в поле зазора. Середина поля рассеивания допуска ширины колеи
еmш = emΣ = Ci(emi + 1/2αiδi) – 1/2αΣδΣ, |
(3.48) |
где Ci — передаточное отношение i-го звена размерной цепи; αΣ, αi — коэффициент асимметрии рассеивания замыкающего и i-го размера; δΣ, δi — допуск замыкающего и i-го звена цепи.
Для рельсошпальной решетки с железобетонными шпалами и промежуточными рельсовыми скреплениями типа КБ-65 размерная цепь может быть получена из схемы, приведенной на рис. 3.14.
Номинальный размер ширины колеи
i=10
Nø = NÂ1 − NÂ2 − NÂ11 − ∑Ci NÂi , (3.49)
i=3
где NB1 — расстояние между наружными кромками углублений в шпале под подкладками; NB2 = NB11 — отклонения головки рельса от вертикали в расчетном уровне за счет подуклонки; NB3 = NB10 — расстояния от наружной кромки углубления в шпале под подкладкой до оси закладного болта; NB4 = NB9 — расстояния от оси закладного болта до упорной грани ее реборды; NB5 = NB8 — расстояния от оси рельса до упорной грани наружной реборды подкладки; NB6 = NB8 — размеры половины ширины головки рельса, замеренной на уровне изме-
рения ширины колеи.
Размеры B4Z = B9Z , B5Z = B8Z — смещения осей сопрягаемых деталей, т.е. звенья-зазоры, которые могут
быть выбраны при сборке частично или полностью в любом направлении.
Учитывая, что разброс значений δш находится в полосе 6σш, можем определить вероятность получения установленной нормами ширины колеи, используя функцию Лапласа.
Φ |
(Ø |
|
< Ø < Ø |
|
) = Φ |
( |
Ø 2 − |
Ø |
) − Φ |
( |
Ø 1 |
− |
Ø |
) , (3.50) |
1 |
2 |
|
|
|
|
|
||||||||
0 |
|
|
0 |
|
σø |
0 |
|
σø |
|
|||||
|
|
|
|
|
|
|
|
|
|
где Ф0(Ш) — нормированная функция Лапласа.
Имеющееся у отдельных специалистов дороги мнение о значительном влиянии на увеличение ширины рельсовой колеи несоосности сопряжения осей отверстий под закладные болты шпалы и осей отверстий под закладные болты подкладки, расчетами и измерениями не подтверждается.
Основные размеры в большинстве случаев находятся в пределах норм, а нормативное сопряжение, даже с учетом неблагоприятных сочетаний допусков сопрягаемых элементов, в том числе и закладного болта, влияния на ширину колеи не оказывает (рис. 3.15).
а) |
б) |
91

Рис. 3.15. Нормативное сопряжение железобетонной шпалы
иметаллической подкладки скрепления КН-65:
а— при минимальном расстоянии между осями отверстий под закладные болты шпалы и максимальном расстоянии между осями отверстий под закладные болты подкладки; б — при максимальном расстоянии между осями отверстий под закладные болты шпалы и минимальном расстоянии между осями отверстий
под закладные болты подкладки
Некоторое влияние на соосность возможно в случае смещения осей рельса, металлической подкладки и подрельсовой площадки железобетонной шпалы относительно друг друга.
В расчетах принято, что при монтаже рельсошпальной решетки подошва рельса и металлическая подкладка располагаются симметрично относительно друг друга. Однако фактически при размещении рельса в пределах реборд подкладки не исключено его смещение от оси симметрии. Это смещение, определяющееся технологией сборки и подуклонкой шпал, может вызвать разброс ширины колеи.
Измерения, проводимые при скреплении КБ-65, не выявили существенного смещения осей. При скреплении ЖБР-65 фактическое смещение составило до 1 мм.
Расчетные параметры рельсовой колеи
Произведем расчет размерной цепи, характеризующей положение рельсовой нити в горизонтальной плоскости при монтаже путевой решетки с железобетонными шпалами, рельсами типа Р-65 и промежуточными скреплениями типа КБ-65, ЖБР-65 и КН-65.
Нормативные размеры основных звеньев, входящих в размерные цепи, приняты по нормативным документам [58–62].
Фактические размеры основных звеньев, входящих в размерные цепи, представлены соответственно в табл. 3.11–3.13.
Результаты расчетов сведены вместе и представлены в табл. 3.15.
Таблица 3.15
Основные характеристики ширины колеи
Тип |
|
Нормативные |
|
Фактические |
|
||||
скрепления |
Ш |
δш |
em ш |
% регулир. |
Ш |
δш |
em ш |
|
% регулир. |
КБ-65 |
1521,3 |
8,3 |
0,15 |
14,5 |
1521,4 |
11,2 |
0,3 |
|
31,4 |
ЖБР-65 |
1519,6 |
7,1 |
0 |
9,1 |
1519 |
10 |
–0,2 |
|
24,2 |
КН-65 |
1521,3 |
8,3 |
0,15 |
14,5 |
1520,9 |
10,5 |
–0,1 |
|
25,3 |
АРС |
1519,3 |
5,3 |
0,12 |
2,4 |
– |
– |
– |
|
– |
Определенные расчетами значения допусков ширины колеи, получаемой при сборке рельсошпальной решетки, показали:
При номинальных размерах рельсовых скреплений и шпал получаемый монтажный допуск ширины колеи равен для АРС — 5,3 мм; ЖБР-65 — 7,1 мм; КБ-65 и КН-65 — 8,3 мм. Вероятность получения ширины колеи с нормативным допуском ±2 составляет соответственно 97,6 %, 90,9 %, 85,5 %.
При фактических размерах скреплений и шпал наблюдается увеличение поля монтажного допуска: КБ65 — 11,2 мм; КН-65 — 10,5 мм; ЖБР-65 — 10 мм. Вероятность получения колеи в пределах монтажного допуска (4 мм) равна соответственно 68,6 %, 74,7 %, 75,8 %.
Для повышения качества работ по сборке рельсошпальной решетки на базах ПМС необходимо пересмотреть ряд существующих допусков на составляющие элементы, а также целесообразно установить увеличенные допуски ширины рельсовой колеи + 4 мм, –2 мм.
При переходе с существующего монтажного допуска 4 мм на предлагаемый допуск 6 мм погрешность получения нормативной ширины колеи при сборке РШР уменьшится в 2,6–3 раза (рис. 3.16).
92