
669
.pdf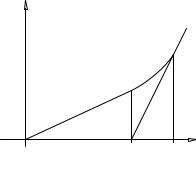
При вертикальном сжатии прокладок под движущимся колесом в зависимости от нагрузки и свойств эластомера резина может работать в двух режимах — упругой и высокоэластической деформации. В первом случае форма прокладки после разгрузки мгновенно восстанавливается, ее жесткость остается постоянной; соотношение сил и деформаций подчиняется закону Гука. Во втором случае из-за внутреннего трения скорость восстановления первоначальной формы прокладки существенно замедляется. Она начинает работать как демпфер. В результате по сравнению с упругим режимом ее жесткость существенно возрастает (рис. 3.8). Жесткость прокладки в упругом режиме принято называть статической, а при демпфировании — динамической.
Прокладка находится в упругом режиме, если ее относительная деформация, определяемая выражением ε = h/h, меньше 0,15, где h — вертикальная деформация прокладки; h — толщина прокладки при отсутствии нагрузки. Несущественный рост жесткости под движущейся нагрузкой наблюдается при ε < 0,2, поэтому практически можно принять, что статическая жесткость имеет место, если ε не более 0,2. Эта жесткость прокладки при сжатии и модуль ее упругости подсчитывается по формулам
Ж |
|
= |
ES0 |
; |
|
(3.1) |
||
ст |
h |
|||||||
|
|
|
|
|
|
|||
|
|
|
|
|
|
|
||
E = |
2G(1+ µ)KФ |
, |
(3.2) |
|||||
|
||||||||
|
|
|
0,25 |
|
|
|
где S0 — опорная площадь прокладки со стороны рифления; G — модуль сдвига; ‚ — коэффициент Пуассона, который для резины принимают 0,47–0,5; Кф — коэффициент формы прокладки.
В свою очередь модуль сдвига и коэффициент формы находят из соотношений
G = |
H 2 |
, |
(3.3) |
||||
|
|
||||||
|
|
380 |
|
|
|
||
K |
|
= |
S0 |
|
, |
(3.4) |
|
Ф |
Sб |
|
|||||
|
|
|
|
|
|
||
|
|
|
|
|
|
|
где Н — твердость резины в условных единицах по Шору; Sб — площадь свободной боковой поверхности прокладки, которая во время сжатия может подвергаться выпучиванию в горизонтальной плоскости.
Следует отметить, что наиболее достоверные характеристики статической и динамической жесткости прокладок различной конфигурации в зависимости от твердости резины можно получить только при испытаниях на стендах. В данном случае динамическая жесткость в диапазоне частот приложения нагрузок 5–30 Гц рассматривается как эквивалентная статистической, используемой в расчетах модели пути как балки на сплошном упругом основании.
Жесткость прокладки на сдвиг при отсутствии и наличии вертикального демфирования
Жсд = |
GS0 |
и |
Жсд = |
GS0 |
, |
(3.5) |
h − h |
(h − h )(1− ε) |
|||||
|
м |
|
|
м |
|
|
где hм — деформация прокладки после приложения монтажных усилий.
Боковая жесткость скрепления при отсутствии люфтов в противоположных боковых упорах равна Жб = Жуп + Жсд. При люфте со стороны внутреннего бокового упора Жуп = 0.
В связи с тем, что модуль сдвига G в 8–12 раз меньше модуля сжатия E, жесткость прокладок на сдвиг Жсд меньше жесткости на сжатие в таком же соотношении.
Рис. 3.8. Изменения жесткости прокладки |
Обычным сочетанием твердости выпускаемых сегодня прокладок к скреплению КБ являются: подрельсовой ЦП-143 — 60–65 ед. и нашпальной ЦП-328 — 75–80 ед. Для прокладок ЦП-204 твердость резины не должна быть ниже 75–80 ед.
При создании бесстыкового пути в первую очередь стремились обеспечить равножесткость конструкции. Использование железобетонных шпал вполне отвечает этой цели, поскольку у каждой из них практически одинаковые характеристики в отличие от деревянных шпал. Сегодня указанное преимущество сводится к
73

минимуму из-за бессистемного применения упругих прокладок, статическая жесткость которых в соответствии с действующими ТУ может различаться в 1,8 раза и не контролируется на дорогах.
В связи с этим на дорогах необходимо установить строжайшую приемку готовой продукции, обеспечить получателей и Центры диагностики твердомерами, обязать изготовителей в документах на каждую партию прокладок указывать их твердость — один из главных параметров, характеризующих срок службы резины.
На оптимальную жесткость скреплений существенное значение оказывают демфирующие свойства прокладок.
Коэффициент демпфирования (безразмерный коэффициент демпфирования) ξ — отношение между действительным и критическим демпфированием. Критическое демпфирование — это граничное демпфирование, при котором процесс перестает быть колебательным. Обычно принимается, что резина обладает вязко-упругими свойствами, т.е. демпфирование зависит от скорости деформации. Обычные прокладки имеют коэффициент демпфирования на уровне 5–10 % от критического [5].
Эксперименты, выполненные различными исследователями, показывают, что для большинства циклически нагружаемых материалов энергия, поглощаемая за цикл, не зависит от частоты в широком диапазоне частот. В этом случае используется понятие комплексного модуля упругости:
|
|
G* = G' + iG» = G (1 + itgδ) = G (1 + iγ), |
(3.6) |
||
где tgδ = |
G′′ |
— коэффициент потерь (тангенс угла потерь); i = |
|
— мнимая единица. |
|
−1 |
|||||
G′ |
|||||
|
|
|
|
Использование понятия комплексной жесткости в задачах вибрации конструкций представляется удобным потому, что для учета демпфирования необходимо в представленных выше уравнениях умножить параметры, определяющие жесткости, на (1 + iγ). Отметим, что для резонансных кривых с равной амплитудой при резонансе, коэффициент потерь равен удвоенному коэффициенту вязкости.
При определении коэффициентов безразмерного демпфирования используется выражение
ξ = |
tgδf0 |
, |
(3.7) |
|
|||
|
2 f |
|
где f0 — собственная частота прокладки; f — частота спектра колебаний подвижного состава, для которой производится расчет.
3.4. Способы улучшения виброзащитных свойств конструкций верхнего строения пути
Обзор конструкций верхнего строения пути, в различных странах, позволяет сделать вывод о том, что наиболее эффективные решения связаны с разъединением элементов конструкции пути и основания резинополимерными (эластомерными) виброизоляторами.
Следует отметить, что эффективность применения в конструкции пути различных упругих прокладокамортизаторов и т.п. не является абсолютной, т.е. существуют определенные частотные диапазоны, где возможно даже некоторое увеличение уровня вибрации.
Перечислим основные способы, позволяющие улучшить упругие и демпфирующие свойства конструкций верхнего строения пути:
–установка подрельсовых подкладок повышенной упругости;
–установка нашпальных прокладок повышенной упругости под рельсовыми подкладками;
–установка подшпальных прокладок;
–укладка подбалластных матов;
–возможна комбинация этих способов.
В настоящее время в европейских странах получили широкое распространение виброзащитные конструкции пути, в которых в качестве упругих элементов: подрельсовых прокладок, нашпальных накладок, подшпальных прокладок и подбалластных матов, выполненные из материала Sylomer (синтетическая вспененная резина). В Австрии и Германии проведена серия испытаний эффективности таких конструкций. В частности были проведены замеры колебаний в тоннелях вблизи концертного зала в Мюнхене [43]. На основании анализа результатов испытаний германскими и австрийскими исследователями для оценки эффективности виброзащиты для пути в тоннеле с подбалластным матом предложена упрощенная модель [44–46] с одной степенью свободы.
Для расчета ослабления L в уровня вибраций подбалластным матом предложена формула
|
|
|
|
|
|
|
|
|
|
Ss |
|
|
|
|
|
|
|
||
|
|
|
|
|
|
Le = 20lg |
1+ |
|
|
Sì |
|
|
|
|
|
, |
|
(3.8) |
|
|
|
|
|
|
|
|
f |
|
|
2 |
|
|
|||||||
|
|
|
|
|
|
|
|
1− |
|
|
0 |
|
|
|
|
||||
|
|
|
|
|
|
|
|
|
f |
|
|
||||||||
|
|
|
|
|
|
|
|
|
|
|
|
|
|
||||||
где |
s |
= s′′S |
w |
(1+ id |
м |
) — жесткость эквивалентной пружины; |
s" |
— динамическая жесткость подбалласт- |
|||||||||||
|
м |
м |
|
|
|
|
|
|
|
|
|
|
|
|
|
м |
|
ного мата; dм — тангенс угла потерь материала, из которого выполнен подбалластный мат; Sw — эффективная площадь, на которую распределяется давление балласта, определяемая из условия конического распре-
74
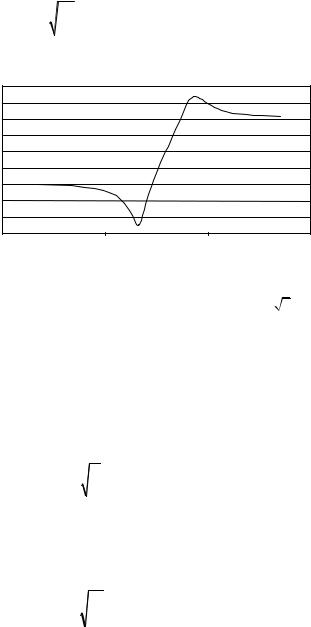
деления давления; i — мнимая единица; Ss — жесткость балластного слоя; f — частота вибраций; f0 — резонансная частота, которая для обычного пути с рельсошпальной решеткой при жесткости балластного слоя
— Ss и неподрессоренной массой M определяется по формуле
f0 = |
1 |
|
Ss |
. |
(3.9) |
2π |
|
||||
|
|
M |
|
Кривая эффективности конструкций пути, описываемых системой с одной степенью свободы, имеет вид, представленный на рис. 3.9, она хорошо согласуется с экспериментальными данными.
|
30 |
|
|
|
25 |
|
|
|
20 |
|
|
Дб |
15 |
|
|
|
|
|
|
Вибрация, |
10 |
|
|
5 |
|
|
|
0 |
|
|
|
|
|
|
|
|
-5 |
|
|
|
-10 |
|
|
|
-15 |
|
|
|
10 |
100 |
1000 |
|
|
Частота, Гц |
|
Рис. 3.9. Кривая эффективности виброзащитной конструкции верхнего строения пути
На низких частотах вплоть до частоты, определяемой выражением f ≤ 2 f0 , наблюдается отрицатель-
ный эффект, поэтому, чем ниже собственная частота конструкции, тем лучше ее эффективность с точки зрения виброзащиты. Анализ зарубежного и отечественного опыта позволяет дать следующие оценки реализуемых собственных частот для различных конструкций верхнего строения пути:
–конструкция пути с упругими подрельсовыми и нашпальными прокладками: f0 ≥ 35 Гц;
–конструкция пути с упругими подшпальными прокладками: f0 ≥ 25 Гц;
–конструкция пути с подбалластными матами: f0 ≥ 15 Гц;
–конструкция пути с дополнительной массой (плитой) на упругих опорах: f0 ≥ 6 Гц.
Собственная частота прокладки определяется по статическому перемещению под нагрузкой Рu прихо-
дящейся на одну прокладку. |
|
|
|
|
|
|
|
|
|
|
||
|
Pu |
|
|
|
1 |
|
|
|
|
|
|
|
= |
и f |
|
= |
|
|
g |
, |
(3.10) |
||||
Cz |
0 |
2π |
||||||||||
|
|
|
|
|
|
|||||||
|
|
|
|
|
|
|
где g — ускорение свободного падения.
В стандартах некоторых стран рекомендуется выбирать опоры таким образом, чтобы относительная деформация резиновых опор составила 0,015 при воздействии рабочей нагрузки. Тогда 1 = 0,015 h, где h — высота слоя резины в опоре.
Для рабочих нагрузок P1:
|
= |
Pi |
и f |
|
= |
1 |
|
|
g |
|
. |
|
i |
C |
z |
i |
2π |
|
|||||||
|
|
|
|
|
i |
|||||||
|
|
|
|
|
|
|
|
|
Для повышения эффективности бесстыкового пути с железобетонными шпалами и щебеночным балластом в гашении вибраций, возбуждаемых проходящим подвижным составом, вертикальная жесткость скреплений не должна превышать 100 МН/м.
Допускаемые максимальные деформации резины при сдвиге γ.
Допускаемые деформации резины при сдвиге — важная характеристика резиновых опор. Опоры, используемые в качестве виброизоляторов, должны выдерживать сдвиговые деформации от собственного веса конструкции и перемещения от динамических воздействий. Приемлемые постоянные деформации сдвига в соответствии со стандартом Bridge Engineer Standards [43] определяются формулой
γW = 0,2εt, |
(3.11) |
где εt — кратковременная деформация разрушения при простом растяжении. На основании анализа зарубежных рекомендаций и отечественных стандартов можно принять, что допускаемая деформация сдвига
tanγ = 0,7. |
(3.12) |
Следовательно, расчетная формула имеет вид
перемещение |
= tanγ = 0,7. |
|
|
||
толщина резины h |
||
|
75
Для прокладки толщиной 10 мм поперечное перемещение не должно превышать 7 мм. Экспериментальные исследования, выполненные во ВНИИЖТе, показали, что вибрации рельсов, шпал и
балласта возникают под проходящими поездами вследствие наличия стыков между рельсами, неровностей на колесах и рельсах. При увеличении скоростей и жесткости подрельсового основания вибрационное воздействие на путь увеличивается [47].
Вибрации играют значительную роль в накоплении остаточных осадок пути, особенно на участках с железобетонными шпалами.
Под воздействием вибрационной нагрузки наблюдается ослабление болтовых соединений. Выправка пути по уровню и подтягивание ослабевших болтов на пути с железобетонными шпалами занимают до 80 % рабочего времени путевых бригад. Отсюда следует, что уменьшение вибраций подрельсового основания путем виброизоляции важный резерв повышения эффективности использования железобетонных шпал.
Из всех элементов пути наиболее интенсивным вибрациям подвергается рельс. По мере удаления от точки соударения колеса с рельсом вибрации затухают. Ускорения шпалы в несколько раз меньше, чем ускорения рельса. Шпале передается некоторая доля ускорений рельса:
K |
|
= |
jш |
, |
(3.13) |
|
рш |
jр |
|||||
|
|
|
|
|||
|
|
|
|
|
где jр и jш — ускорения соответственно рельса и шпалы. По данным [47] Крш = 0,13–0,17.
Характерно, что, несмотря на существенное различие в величинах ускорений, в различных опытах значения Крш примерно одинаковы. Значит, этот коэффициент отражает некоторое свойство пути как механической системы при воздействии на него ударной нагрузки разной интенсивности, а именно, он показывает, насколько чувствительна шпала к вибрациям колеса при ударных нагрузках. Чем меньше коэффициент Крш, тем менее чувствительна шпала к вибрациям рельса.
Значительное уменьшение ускорений шпал по сравнению с ускорениями рельса объясняется рядом причин. Во-первых, погонная масса шпал в 4 раза больше массы рельса, а во-вторых, на соотношении величин ускорений рельса и шпалы сказывается амортизирующая роль скреплении. При ударе колеса о рельс в последнем возникают колебания, характеризуемые широким диапазоном частот. Высокочастотные колебания рельса не имеют достаточно энергии для того, чтобы вызвать подобные колебания шпал Отсутствие в сложных колебаниях шпалы высокочастотных составляющих влечет за собой уменьшение ускорений.
Ускорения рельсов, шпал и балласта в зоне стыка зависят от скорости подвижного состава. При изменении скорости от 25 до 70 км/ч ускорение шпалы увеличивается в 3 раза.
Железнодорожный путь под воздействием динамических сил не колеблется как одно целое. Рельс, шпалы, балласт и земляное полотно совершают вынужденные колебания под воздействием этих сил и свободные затухающие колебания под действием сил упругости и трения. Колебания разных элементов складываются, интерферируют, в результате чего возникает сложный колебательный процесс. Для практических целей важно знать, какие элементы пути более всего подвержены вибрации, от каких вибрации следует изолировать подрельсовое основание и какие из них являются небольшими и опасности не представляют. Ответы на эти вопросы дает спектральный анализ колебаний, с помощью которого можно обнаружить преобладающие вибрации в сложном процессе.
В работе [47] выполнен спектральный анализ на ЭВМ свободных колебаний рельса и шпалы, возбуждаемых взаимодействием колеса и рельса в стыке.
Полученные спектрограммы позволяют установить особенности вибраций рельса и шпалы. На спектрограмме колебаний рельса видны области, характеризуемые пиковыми значениями плотности спектра ускорении. Максимальные ускорения приходятся на частоты 230–400 и 700–1050 Гц.
Максимальная плотность спектра ускорений колебании шпалы при отсутствии подрельсовых прокладок в скреплении достигает наибольших значений в диапазоне частот 200–400 Гц. Затем на спектрограмме виден пик на частоте 700 Гц. При более высоких частотах пик не наблюдается, а гармониками с частотой более 800 Гц практически можно пренебречь.
Отсюда можно сделать вывод о том, что энергия колебаний рельса с частотой более 500 Гц не столь велика, чтобы вызывать такие же колебания шпалы.
Кроме того, на этих частотах, возможно, проявляется амортизирующая способность типовых резиновых прокладок. Таким образом, вибрации рельса имеют частоту до 2000–2100 Гц, а вибрации шпалы — 700–800 Гц.
Поскольку основной причиной вибрации пути являются неровности и стыки рельсовых нитей, то наиболее эффективными мероприятиями по борьбе с вибрациями будут те, которые направлены на создание пути без стыков и неровностей. К таким мероприятиям относятся внедрение бесстыкового пути и шлифовка рельсов.
Для оценки вибрационных свойств промежуточных скреплений используют коэффициент передачи К(ω), который является функцией частоты ω.
При малых частотах вибрации К(ω) имеет наибольшие значения, с увеличением частоты уменьшается. Убывание К(ω) указывает на то, что мощность колебаний падает, и они не передаются на основание рельса. Зависи-
76
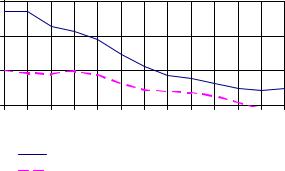
мость коэффициента передачи от частоты (рис. 3.10) при прокладках повышенной упругости имеет тот же вид, что и при типовых скреплениях: К(ω) убывает с ростом частоты, но величина его значительно уменьшается.
передачи |
0,6 |
|
|
|
|
|
|
|
|
|
|
|
|
0,4 |
|
|
|
|
|
|
|
|
|
|
|
|
|
Коэффициент |
0,2 |
|
|
|
|
|
|
|
|
|
|
|
|
0 |
|
|
|
|
|
|
|
|
|
|
|
|
|
|
200 |
250 |
300 |
350 |
400 |
450 |
500 |
550 |
600 |
650 |
700 |
750 |
800 |
|
|
|
|
|
|
Частота, Гц |
|
|
|
|
|
||
|
|
|
с типовыми прокладками |
|
|
|
|
|
с прокладками повышенной упругости
Рис. 3.10. Коэффициенты передачи ускорений от рельсу к шпале при скреплениях
Однако наибольшего эффекта для снижения вибрации, передающихся на балластный слой, можно добиться за счет укладки упругих прокладок под шпалы.
3.5. Расчетные нагрузки на рельсовую нить и узел скрепления
Вертикальная составляющая колесной нагрузки
Исходя из перспективных осевых статических нагрузок грузовых вагонов (270 кН/ось), средняя вертикальная (статическая) нагрузка от колеса на рельс принята равной Рср = 135 кН.
Максимальная вертикальная динамическая нагрузка Рдин в общем случае (при различных динамических неровностях на пути и колесах) определяется из средней (статической), умноженной на коэффициент динамики: Рдин = РсрКд. Анализ результатов многочисленных расчетов и экспериментальных исследований показал, что обычно коэффициент динамики находится в пределах Кд = 1,3–1,5. С учетом неровностей в зоне сварного стыка глубиной до 1,0 мм, состояния некоторых участков земляного полотна Севера, Сибири и Дальнего Востока, а также длительного зимнего периода, принимаем наибольшее из приведенных выше значений коэффициента динамики Кд = 1,5. Тогда расчетное значение максимальной вертикальной динамической нагрузки на рельс будет равно: Рдин = 135 · 1,5 = 200 кН.
Поперечная составляющая колесной нагрузки
По результатам измерений, полученных отделением Комплексных испытаний и взаимодействия пути и подвижного состава ВНИИЖТ в кривых участках пути различного радиуса на Экспериментальном кольце при осевой нагрузке 270 кН [48], а также с учетом поперечной составляющей температурных сил в кривых участках пути, принимаем следующие расчетные значения максимальных боковых динамических нагрузок набегающего колеса на рельсовую нить: Нб = 80 кН — для кривых участков пути с радиусами R > 600 м; Нб = 100 кН — для кривых с радиусами R = 600–350 м. Боковая сила величиной Нб = 100 кН установлена также приказом МПС 41Ц [49] от 12.11.2001 г. из условия прочности рельсовых скреплений.
Продольные силы
Для восприятия этих сил в зимний период эксплуатации при отрицательных температурах до минус 45– 50 °С рельсовые скрепления должны обеспечивать наибольшее в соответствии с ТУ-2000 [50] погонное сопротивление продольному перемещению плетей — 30 кН/м. В этом случае удерживающая способность узла скрепления в продольном направлении (расстояние между осями шпал L = 0,55 м) должна быть [Qx] = 30·0,55 = 16,5 кН. При принятом нормативном прижатии рельса к подкладке Q0 = 25 кН получаем удерживающую способность скрепления при продольном перемещении рельса на подрельсовой резиновой прокладке с учетом соответствующих коэффициентов трения но резине — f1 и по металлу — f2:
Qx = Q0 (f1 + f2) = 25(0,5 + 0,2) = 17,5 кН > [Qx].
Такие параметры скрепления обеспечивают также сопротивление угону рельсов от воздействия подвижного состава, в том числе тормозных сил [42].
Нагрузки на узел скрепления
Если на рельс как балку, лежащую на сплошном упругом основании, действует сосредоточенная сила Р от колеса, то давление Q на шпалу, расположенную под колесом, равно
Q = 0,5Pkl, |
(3.14) |
где k — коэффициент относительной жесткости рельсового основания и рельса; l — расстояние между осями соседних шпал.
77

k = 4 |
U |
, |
(3.15) |
|
|||
|
4EJ |
|
где U — модуль упругости подрельсового основания; Е — модуль упругости рельсовой стали, принимаемый обычно равным 2,1·105 МПа; J — момент инерции сечения рельса относительно горизонтальной оси, для рельса Р65 J = 3540·10-8 м4.
Жесткость подшпального основания в летнее время находится в пределах Ж0 = 100–300 МН/м. Вертикальная жесткость современных скреплений согласно [41] находится в пределах Жск = 37–112 МН/м.
Жесткость пути Жп найдем из зависимости
1 |
= |
1 |
+ |
1 |
. |
(3.16) |
|
|
|
||||
Жп |
|
Ж0 |
Жск |
|
При Ж0 = 300 МН/м, Жп = 33–82 МН/м. Модуль упругости подрельсового основания в этом случае составит U = 66–164 МПа и коэффициент относительной жесткости k = 1,216–1,527 м-1.
Используя эти значения k при Р = 200 кН и l = 0,5 м, согласно (3.14) получим Q = 60,8–76,4 кН.
Таким образом, при изменении жесткости подрельсового основания в 2,48 раза, нагрузка передаваемая от рельса на шпалу изменится всего на 26 % из-за высокой изгибной жесткости рельса EJ в вертикальной плоскости.
Горизонтальное поперечное давление рельса на шпалу
Боковое давление от рельса на шпалу Qг в кривой зависит от бокового давления экипажа на упорную нить Yб.
Qг = z0Uгl, |
(3.17) |
где z0 — упругий прогиб рельса в горизонтальной плоскости, измеряемый по центру кручения в расчетном сечении; Uг — модуль упругости подрельсового основания при поперечной горизонтальной нагрузке; l — расстояние между осями шпал.
Так как сила Yб, передается от колеса на рельс выше низа подошвы рельса, т.е. выше места передачи бокового давления шпале, упругий прогиб рельса z01 в горизонтальной плоскости, несколько уменьшенный за счет его кручения, составляет
z01 = z0 – φ0 h2, |
(3.18) |
где h2 — расстояние от низа подошвы рельса до центра кручения его; φ0 — угол закручивания в том же сечении.
Тогда
Qг = Uгт l (z0 – φ0h2), |
(3.19) |
где Uгт — модуль упругости подрельсового основания при изгибе рельса в горизонтальной плоскости при одновременном действии и вертикальных, и горизонтальных поперечных сил.
Аналогично (3.17) при рассмотрении работы рельса в горизонтальной плоскости как балки на сплошном упругом основании, найдем
Qã = 0,5Yá kãl . |
(3.20) |
Величина kг определяется по формуле
kг = 4 4Uг , (3.21)
EJг
где Jг — момент инерции сечения рельса относительно вертикальной оси (Р65 — 572 см4; Р50 — 377 см4). Более точно в отличие от формулы (3.20) величина Qг определяется исходя из того, что давление рельса
на шпалу передается на уровне низа подошвы рельсов, т.е. с учетом формулы (3.19) при этом [51]
Q = |
k l |
|
|
− |
Uãò hï ðh2 |
|
|
ã |
Y |
1 |
|
, |
(3.22) |
||
|
|
||||||
ã |
2 |
á |
|
kãβφ |
|
|
|
|
|
|
|
|
|
где hпр — приведенное плечо боковой силы.
hï ð = hï′ð − |
P b |
|
|
|
||
|
|
ã |
− rã |
, |
(3.23) |
|
|
2 |
|||||
|
Yá |
|
|
|
где hпр' — расстояние от центра изгиба рельса до места приложения боковой силы; bг — ширина головки рельса; rг — радиус верхней выкружки головки рельса; βφ — жесткость рельса при кручении, зависящая от формы рельса и жесткости элементов его сечения.
β |
= 2D |
φ |
h2 |
r |
r |
(r |
– r ), |
(3.24) |
φ |
|
Q |
|
1 2 |
1 |
2 |
|
78
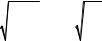
r = |
Cφ |
|
; r = |
Uφ |
, |
(3.25) |
D h2 |
|
|||||
1 |
2 |
C |
|
|||
|
φ |
Q |
|
φ |
|
где Сφ — полярная жесткость поперечного сечения рельса, не прикрепленного к основанию; Dφ — жесткость подошвы и головки рельса при горизонтальном изгибе; hQ — расстояние между центрами тяжести головки и подошвы рельса.
Значения Сφ, Dφ, hQ и r1 являются постоянными для каждого типа рельсов и для Р65 равны: hQ = 14,90 см; Сφ = 230·106 кг/см2; Dφ = 210·106 кг/см2; r1 = 0,0717; h1' = 11,26 см; h2 = 4,4 см.
|
|
U ò h h |
|
|
Выполнив вычисления, получим 1 |
− |
ã ï ð 2 |
|
≈ 0,9 . |
|
||||
|
|
kãβφ |
|
|
|
|
|
|
При учете кручения рельса боковое давление на шпалу снижается на 10 %.
3.6. Влияние жесткости рельсовых скреплений на работоспособность прокладок
Жесткость и зависящий от нее модуль упругости являются сквозными характеристиками деформативности пути в целом и отдельных его элементов. При железобетонных шпалах модуль зависит от комбинации двух параметров — жесткости прокладок и подшпального основания. Установим связь между жесткостью основания и модулем его деформации на основе результатов расчета, приведенных в табл. 3.4, 3.5.
Анализ полученных данных в первом приближении позволяет предложить разделять подшпальное основание на категории в зависимости от доли его деформации в общей деформации пути (табл. 3.4).
В результате, варьируя жесткостью скреплений, эпюрой шпал, площадью их опорной поверхности, можно выбрать оптимальную конструкцию пути на основе комплексной оценки затрат на его ремонт и содержание в зависимости от деформативности подшпального основания. При этом прежде всего следует исходить из минимизации совокупных затрат, связанных с долговечностью прокладок-амортизаторов, объемами выправки, сопротивлением движению поезда и, значит, расходами на тягу [41].
Таблица 3.4
Жесткостные характеристики подшпального основания
Подшпальное основание |
Доля в общей |
Жос, кН/мм |
Uос, МПа |
||
Категория |
Состояние |
деформации пути, % |
|||
|
|
||||
I |
прочное |
менее 10 |
более 300 |
более 600 |
|
II |
малодеформируемое |
11–20 |
160–300 |
300–600 |
|
III |
среднедеформируемое |
21–50 |
40–150 |
80–300 |
|
IV |
слабое |
более 50 |
менее 40 |
менее 80 |
Оптимальную жесткость скреплений определим в зависимости от величины сил, передаваемых от рельса на узел скреплений и демфирующих свойств прокладок скреплений.
Параметры вертикальной и горизонтальной жесткости различных типов скреплений примем по результатам лабораторных испытаний в НПП «АпАТэК» [52], полученные по единой методике (табл. 3.5).
По данной программе испытаны скрепления следующих типов:
КБ-65 — с жесткими клеммами ПК и типовыми прокладками из резиновых смесей РП; ЖБР-65 — с закладными болтами, шурупами и резиновыми прокладками ЦП-204 толщиной 14 мм, а
также с комбинированными прокладками из резины 46ПМ02 и полиамида ПА-6, а также с прокладками из полимера ТПК-4 ОАО «АРТИ»;
АРС-4 — бесподкладочное безболтовое анкерное скрепление с серийными прокладками ЦП-204; КН-65 и КНУ-65 — подкладочное нераздельное скрепление с упругими клеммами (разработчик СГУПС)
с нашпальными прокладками из резинокорда; ЖБР-65П — подкладочное нераздельное скрепление с упругими клеммами ЖБР-3 в болтовом и шуруп-
но-дюбельном исполнениях с нашпальными и подрельсовыми прокладками из полимера ТПК-5;
W-14 — бесподкладочное шурупно-дюбельное скрепление с клеммами Skl-14 фирмы Vossloh с полимерными прокладками.
Силы, передаваемые на узел скрепления в зависимости от жесткости пути, определены по вышеприведенной методике.
|
|
|
|
|
|
|
|
Таблица 3.5 |
|
|
Параметры жесткости и силы, передаваемые на узел скреплений |
|
|||||
|
|
|
|
|
|
|
|
|
|
|
Вертикальная жесткость |
|
|
Горизонтальная жесткость |
|
||
Тип скреп- |
жесткость узла |
|
коэффициент относи- |
давление на |
жесткость узла |
коэффициент относи- |
давление на |
|
ления |
скрепления, |
|
скрепления, |
|
||||
|
тельной жесткости, м-1 |
опору, кН |
|
тельной жесткости, м-1 |
опору, кН |
|||
|
МН/м |
|
|
|
МН/м |
|
|
|
КБ |
37 |
|
1,216 |
60,8 |
16 |
|
1,36 |
34 |
ЖБР |
37-112 |
|
1,216-1,525 |
60,8-76,2 |
72-277 |
|
2,36-3,31 |
59-83 |
ЖБР-П |
112 |
|
1,525 |
70,2 |
44 |
|
2,1 |
52,5 |
АРС |
37 |
|
1,216 |
60,8 |
346 |
|
3,5 |
87,5 |
КН |
56 |
|
1,330 |
66,5 |
38 |
|
2,0 |
50 |
79
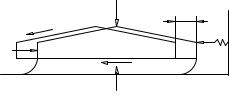
КНУ |
61 |
1,359 |
67,9 |
30 |
1,88 |
47 |
W-14 |
80 |
1,431 |
71,6 |
166 |
2,91 |
73 |
|
|
|
|
|
|
|
Анализ данных табл. 3.5 показывает, что вертикальная жесткость рельсовых скреплений оказывает небольшое значение на величину сил, передаваемых на шпалу.
Согласно данным табл. 3.5 при изменении жесткости скреплений от 37 до 112 МН/м, т.е. в 3 раза, нагрузка на шпалу изменяется всего на 25 %.
Горизонтальная жесткость узлов скреплений существенно зависит от их конструкции и варьируется для рассматриваемых скреплений от 16 до 346 МН/м. При этом горизонтальное давление на шпалу изменяется от 34 до 87,5 кН, т.е. увеличивается в 2,2 раза.
У скрепления ЖБР-65 горизонтальная жесткость по подошве рельса колеблется в пределах 72–277 МН/м. При этом горизонтальное давление на шпалу изменяется в пределах 59–83 кН, т.е. увеличивается в 1,4 раза.
Горизонтальная жесткость бесподкладочных скреплений ЖБР-65 существенно зависит от материала прокладки под упорной скобой. При применении полимерных прокладок боковое давление на шпалу возрастает на 40 %.
Наибольшую горизонтальную жесткость имеют анкерные скрепления АРС-4. При этом конструкция скреплений не позволяет регулировать величину горизонтальной жесткости этих скреплений.
Оптимальную горизонтальную жесткость имеют подкладочные скрепления КН-65 и ЖБР-65П.
Давление на боковой упор скреплений
Сопротивление поперечному смещению рельса обеспечивается за счет упругой деформации сдвига подрельсовой прокладки Qп у бесподкладочных скреплений или нашпальной прокладки у подкладочных скреплений, упругой деформации бокового упора клеммы Qб у бесподкладочных скреплений или загнутой части нашпальной прокладки у подкладочных скреплений, а также сил трения на контакте одной клеммы Fк с подошвой рельса. Другая (упорная) клемма следует за рельсом [42].
До момента проскальзывания подошвы рельса или подкладки по прокладке равновесие системы (рис. 3.11) имеет вид
Qz = Qп + Qб + Fк. |
(3.26) |
Вследствие малости силы трения Fк клеммы по подошве рельса (порядка 1,5–2 кН) без большой погрешности для практических расчетов ею часто пренебрегают.
При поперечном смещении рельса упругие деформации упора и резиновой прокладки на сдвиг равны и соответствуют перемещению подошвы рельса zп.
Qz = zп (жгпр + жб). |
(3.27) |
где жгпр и жб — соответственно жесткость прокладки на сдвиг и жесткость бокового упора.
Поперечная жесткость скрепления является суммой жесткости резиновой прокладки на сдвиг и жесткости деталей бокового упора.
Жесткость подрельсовых и нашпальных резиновых прокладок на сдвиг в определенной степени зависит от вертикальной нагрузки; при этом величина изменения поперечной жесткости определяется в основном относительным сжатием прокладок, в соответствии с формулой (3.5).
Рис. 3.11. Схема загружения узла скрепления
Относительная деформация при сдвиге для твердой резины (твердостью 75 единиц по Шору) — [εсд] = 0,25. Так как в реальных условиях это требование выполняется, то поперечная устойчивость узла скрепления определяется прочностью бокового упора.
В целях предотвращения преждевременного выхода резиновых прокладок из строя необходимо, чтобы напряжения на отогнутой части нашпальной прокладки или подклеммника не превышали
σñæ = |
Qá |
≤ [σñæ ], |
(3.28) |
|
|||
|
Sá |
|
где Sб — площадь отогнутой части прокладки или подклеммника.
С учетом зависимости (3.28) допустимое давление на боковой упор
Rб = [Qб] ≤ [σсж] Sб. |
(3.29) |
Как правило, удельное давление при сжатии резины не должно превышать для новых прокладок 10 МПа, а для армированных прокладок 20 МПа.
Действующую нагрузку на боковой упор можно определить:
80
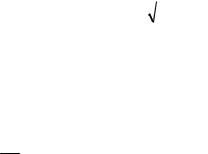
Qб = Qz – zп жгпр. |
(3.30) |
Имея величины боковых сил и характеристики поперечной упругости пути в зависимости от толщины нашпальных прокладок и величины углублений в шпалах под прокладками, по формуле (3.30) определим нагрузки на боковой упор в шпале.
При нормальном распределении сил Qб и несущей способности бокового упора в шпале Rб отказ не произойдет, пока
Rб – Qб = > 0. |
(3.31) |
Математическое ожидание и среднее квадратичное отклонение случайной величины в этом случае
m = mR |
− mQ |
; |
|
|
Á |
Á |
|
|
|
|
|
|
|
|
σ = σ2R |
+ σQ2 |
, |
(3.32) |
|
Á |
Á |
|
|
где σRÁ и σQÁ — средние квадратичные отклонения случайных величин Rб и Qб. Работоспособность поперечных связей рельсов со шпалами определяется зависимостью
m
где Ф σ
|
m |
|
|
|
Р = 0,5 + Ф |
, |
(3.33) |
||
σ |
||||
|
|
|
— нормированная функция Лапласа.
Удельное давление на боковой упор скреплений определим по формуле (3.28), используя данные табл. 3.5.
Таблица 3.6
Параметры давления на боковой упор скреплений
Тип |
Опорная площадь |
Давление на боко- |
Удельное давление на |
скрепления |
бокового упора, см2 |
вой упор, кН |
боковой упор, МПа |
КБ-65 |
21 |
32 |
15 |
|
|
|
|
КН-65 |
20 |
35 |
17 |
КНУ-65 |
33 |
33 |
10 |
|
|
|
|
ЖБР-65 |
25 |
53–76 |
21–30 |
|
|
|
|
ЖБР-65П |
35 |
47 |
14 |
АРС-4 |
11 |
80 |
73 |
Анализ данных табл. 3.6 показывает, что удельное давление на прокладки боковых упоров всех скреплений, за исключением КН и КНУ, превышает допускаемое значение. Особенно велики эти давления у скреплений ЖБР-65 с полимерными боковыми упорами и недопустимо велики у скреплений АРС-4.
Высокое удельное давление и недостаточная прочность прокладок бокового упора скреплений КБ-65 и ЖБР-65 (табл. 3.7) приводит к тому, что после наработки 100 млн т бр. (это годовой тоннаж грузонаряженных участков и двухгодовой среднегрузонапряженных участков) ширина колеи указанных скреплений попадает в зону четвертой степени неисправности и требует немедленного исправления, т.е. смены прокладок бокового упора. Износостойкость прокладок, армированных полимерными волокнами, обеспечивает большую стабильность ширины колеи у скреплений КН и КНУ.
Таблица 3.7
Изменение ширины колеи при различных типах скреплений
Параметры |
|
|
Тип скрепления |
|
|
||
|
|
|
|
|
|
||
|
|
|
|
|
|
||
рельсовой колеи |
АРС-4 |
КБ-65 |
ЖБР-65 |
ЖБР-65П |
КН-65 |
КНУ-65 |
|
|
|
|
|
|
|
|
|
Начальная ширина колеи |
1520,4 |
1525,6 |
1521,6 |
1524,2 |
1523,9 |
1522,0 |
|
S0, мм |
|||||||
|
|
|
|
|
|
||
Ширина колеи после |
|
|
|
|
|
|
|
наработки 100 млн т бр. |
1527,1 |
1538,8 |
1533,6 |
1528,2 |
1526,0 |
1527,0 |
|
S100, мм |
|
|
|
|
|
|
|
Среднеквадратическое |
|
|
|
|
|
|
|
отклонение ширины ко- |
1,64 |
1,98 |
4,53 |
– |
1,36 |
2,15 |
|
леи σS, мм |
|
|
|
|
|
|
|
Приращение ширины |
6,7 |
13,2 |
12,0 |
4,0 |
2,1 |
5,0 |
|
колеи S, мм |
|||||||
|
|
|
|
|
|
||
Интенсивность уширения |
0,06 |
0,13 |
0,12 |
0,04 |
0,02 |
0,05 |
|
колеи, мм/млн т бр. |
|||||||
|
|
|
|
|
|
81
3.7. Оценка надежности рельсовых скреплений
Показатели надежности это количественные характеристики одного или нескольких свойств, составляющих надежность объекта. Численные значения показателей могут быть выражены размерными или безразмерными величинами [53, 54].
Отказом в теории надежности называют событие, заключающееся в нарушении работоспособного состояния объекта. Принципиальной основой ведения путевого хозяйства является не ликвидация отказов, а их предупреждение, т.е. выполнение профилактических работ и установленные сроки. Исходя из этого основными показателями надежности элементов верхнего строения пути будут показатели надежности невосстанавливаемых объектов или объектов, работающих до первого отказа.
Для оценки надежности таких объектов используют вероятностные характеристики случайной величины наработки Т объекта от начала его эксплуатации до первого отказа. Под наработкой понимают продолжительность или объем работы объекта в часах, циклах или в других единицах. Для объектов верхнего строения пути чаще всего наработка выражается в млн т бр. пропущенного груза или в единицах времени работы.
Функцией надежности называют функцию, выражающую вероятность тою, что Т — случайная наработка до отказа — будет не менее заданной наработки (0; t), отсчитываемой от начала эксплуатации, т.е.
p(t) = P (T ≥ t). |
(3.34) |
Вероятность безотказной работы по статистическим данным об отказах оценивается выражением
|
(t) = |
N(ti ) |
, |
|
|
P |
(3.35) |
||||
|
|||||
|
|
N0 |
|
где N0 — число объектов в начале испытаний; N(ti) — число безотказно проработавших объектов к моменту наработки ti.
На практике иногда более удобной характеристикой является функция ненадежности q(t):
q(t) = 1 – p(t) = Р (Т < t). |
(3.36) |
Она характеризует вероятность отказа объекта на интервале (0; t). Функция ненадежности является функцией распределения случайной величины Т; эта функция в теории вероятностей обозначается F(t).
Вероятность отказа по статистическим данным
|
|
) = |
r(ti ) |
. |
|
|
F(t |
(3.37) |
|||||
|
||||||
|
i |
|
N0 |
|
||
|
|
|
|
где r(ti) — число отказавших объектов к моменту наработки ti.
Скрепление проектируют так, что обычно у него нет функционально «лишних» деталей. Отказ любой из них сильно снижает эффективность функционирования узла скрепления, вызывает интенсивный износ соседних деталей и повышает расходы на содержание пути. Поэтому, оценивая надежность скреплений различных типов в условиях нормальной эксплуатации, необходимо все элементы считать соединенными последовательно, а вероятность безотказной работы узла такой системы оценивать по формуле
n |
|
Pö (t) = ∏Pi (t) , |
(3.38) |
i=1
где Рi — вероятность безотказной работы i-го элемента.
Оценивая надежность скрепления в экстремальной ситуации, в которой конструкция может находиться ограниченное время, после чего переходит в аварийное состояние, отдельные цепи элементов можно считать параллельными. Безотказность работы элементов цепи
|
n |
|
2 |
|
Pö (t) = 1− 1 |
− ∏Pi |
(t) |
, |
(3.39) |
|
i=1 |
|
|
|
Частота отказов элементов рельсовых скреплений типов КБ-65, КН-65, ЖБР-65, АРС определяется на основании статистических данных об отказах элементов во время эксплуатации. После определения параметров Тср и σt и вероятности безотказной работы Pi (t) отдельных элементов скреплений переходят к определению вероятности безотказной работы узлов скреплений. Для этой цели составляются схемы анализа надежности скреплений КБ, ЖБР, АРС и КН (рис. 3.12).
82