
669
.pdf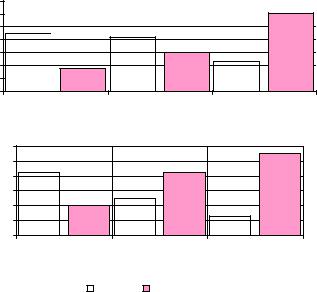
) |
|
70 |
|
|
|
|
|
60 |
|
|
|
|
|
|
|
45 |
|
|
|
|
|
|
50 |
|
42 |
61 |
|
|
% |
|
|
|||
|
40 |
|
|
|
||
|
|
|
30 |
|
||
|
Доля, |
|
|
|
||
|
30 |
|
18 |
23 |
|
|
|
20 |
|
|
|
||
|
|
|
|
|
||
|
|
|
|
|
|
|
|
|
10 |
|
|
|
|
|
|
0 |
|
|
|
|
|
|
|
0,01 |
|
0,02 |
0,035 |
|
|
|
|
Интенсивность износа, мм/млн т бр. |
|
) |
|
60 |
|
|
|
|
|
50 |
42 |
|
42 |
|
|
|
|
|
55 |
|||
|
|
40 |
|
|
|
|
|
% |
|
|
|
|
|
|
30 |
|
25 |
|
|
|
|
Доля, |
20 |
|
|
||
|
|
|
|
|||
|
20 |
|
13 |
|
||
|
|
|
|
|||
|
|
|
|
|
|
|
|
|
10 |
|
|
|
|
|
|
0 |
|
|
|
|
|
|
|
0,01 |
|
0,02 |
0,03 |
|
|
|
Интенсивность износа, мм/млн. т бр. |
|
||
|
|
|
|
21 дефект |
44 дефект |
|
|
|
|
|
Рис. 2.17. Сочетание дефектов 21 и 44 в зависимости от интенсивности |
||
|
|
|
бокового износа в кривых различного радиуса (по данным за 1992–2003 гг.): |
а— R < 350 м; б — 350 м < R < 500 м; в — 500 м < R < 650 м
Вструктуре «Положения» наиболее актуальными являются вопросы классификации, дефектов рельсов. Пересматривать НТД начали давно, но к сожалению, из-за ряда объективных и субъективных причин введение задерживается.
А между тем с развитием этой тематики неразрывно связан следующий большой пласт исследований: «Рельсовая дефектоскопия, основные требования к средствам дефектоскопного контроля». Необходимо четко определить критерии опасности дефектов применительно к условиям эксплуатации. Отсутствие таких критериев приводит часто как к перебраковке, так и к пропуску поврежденных рельсов, вызывает излишние затраты на содержание штата дефектоскопистов.
63
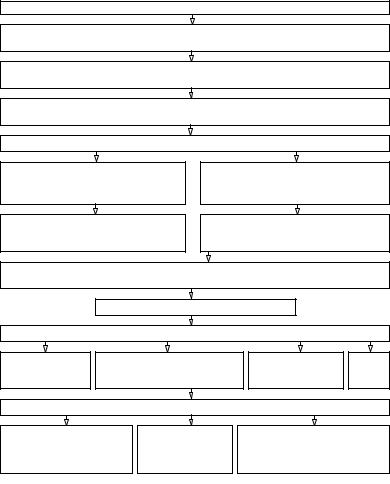
Рис. 2.18. Структура положения о системе ведения рельсового хозяйства
Основные изменения, внесенные в действующую классификацию дефектов рельсов, сводятся к следующим [37]:
–все изломы выделены в одну группу;
–для основных дефектов введено разделение на образовавшиеся «до» и «после» гарантии;
–введен дефект «контроленепригодные рельсы»;
–рельсы с продольными трещинами отнесены не к остродефектным, а к дефектным;
–приведены конкретные критические размеры для ряда дефектов;
–предусмотрен обязательный долом всех остродефектных рельсов, снятых по показаниям дефектоско-
пов;
–расширена установка накладок (и в случае обнаружения трещин в подошве);
–введен раздел с нормативами для рельсов на участках скоростного движения;
–изменены нормы по скоростям пропуска поездов после обнаружения дефектных рельсов.
Пришла пора разработки нового стандарта на рельсы для Российских железных дорог, который вобрал бы в себя лучшие достижения ГОСТ Р 51685–2000 [38] и всех технических условий, разработанных начиная с 2000 г. на рельсы категорий НК (НЭ), СС, И и ВС, а также был бы гармонизирован с Евронормами EN 13674-1:2003, стандартом канадских железных дорог (CN 12-16с), стандартом США (AREMA, версия 2003 г.). Перечислим технические требования к рельсам 10 категорий, которые должны войти в новый стандарт:
–временное сопротивление в зависимости от наличия и вида термического упрочнения должно быть более 700-900 Н/мм2. Наиболее высоким временным сопротивлением должны обладать рельсы категории И;
–относительное удлинение в зависимости от наличия и вида термического упрочнения должно быть более 9–12 %;
–ударная вязкость в зависимости от наличия и вида термического упрочнения должны быть более 15–25 Дж/см2;
–остаточные напряжения, контролируемые по величине раскрытия паза, должны быть менее 1,5–2 мм;
–высота падения груза при копровых испытаниях при температуре –60 °С должна быть более 5 м;
–прямолинейность рельсов в зависимости от их категории должна соответствовать классу «А» или «В» по EN 13674-1:2003;
–класс точности профиля рельсов в зависимости от их категории должен соответствовать классу «X» или «Y» по ЕN 13674-1:2003;
64
–твердость на поверхности катания и на глубине 10 мм в рельсах категории В должна составлять 363401 НВ, а в рельсах категории И — 375-401 НВ;
–твердость на глубине 20 мм должна составлять 341-388 НВ;
–колебания твердости по длине рельсов не должны превышать 30 НВ;
–структура во всех категориях рельсов должна быть однотипной (перлитной), мартенсит и бейнит не допускаются. Вопрос о предельных размерах зерна и перлитных колоний остается пока открытым и требует проведения дополнительных исследований.
По аналогии с лучшими мировыми стандартами в новый стандарт нужно включить квалификационные испытания, которые будут периодически производиться при стабильной технологии производства, а также сопровождать все важные изменения в технологии производства рельсов. В процессе их проведения должны проверяться важные параметры механики разрушения рельсов, определяемые при натурных испытаниях и при испытании специальных образцов:
–критическая величина коэффициента интенсивности напряжений в зависимости от категории рельсов Кк > 28–35 МПа/м;
–скорость распространения усталостной трещины при К = 10 МПа/м ≤ ≤ 77 м/109 циклов, при К = 13,5 МПа/м
≤55 м/109 циклов;
–долговечность при циклическом растяжении-сжатии с постоянной деформацией 0,00135 N более 5×10 млн циклов;
–условный предел выносливости натурных образцов полнопрофильных рельсов при натурных испыта-
ниях, σ0,1 не менее 350–410 МПа в зависимости от категории рельсов.
Очень важно включение в качестве обязательного требования в новый стандарт прохождения всеми рельсами трех видов неразрушающего контроля на отсутствие внутренних и поверхностных дефектов и прямолинейности. При проведении последнего нужно решить вопрос о предпочтительном применении лазерного контроля, принятого на большинстве заводов мира, или использовании устройства «Элекон», применяемого на отечественных рельсопрокатных заводах.
Для решения практических вопросов выбора конкретных фирм-поставщиков и приборов для неразрушающего контроля можно использовать предложение об обмене небольшим количеством рельсов для взаимной проверки с использованием существующего оборудования, например на одном из европейских и российских рельсопрокатных заводов. Полученные данные о доле забракованных по внутренним, наружным дефектам и прямолинейности можно использовать для обоснования выбора лучшего оборудования для неразрушающего контроля.
Без коренной реконструкции рельсового производства на обоих отечественных рельсопрокатных заводах нельзя будет существенно повысить качество и ресурс российских рельсов. Краткий список оборудования, без замены которого невозможно выполнение современных и тем более перспективных требований ОАО «РЖД» к рельсам, включает в себя:
–универсальные прокатные станы;
–оборудование для первичного и вторичного гидросбива окалины;
–оборудование для дифференцированной закалки с прокатного или отдельного нагрева;
–гидравлические прессы для правки с лазерным измерением прямолинейности;
–оборудование для сплошного контроля внутренних и поверхностных дефектов;
–оборудование для компьютеризации всех операций.
Наиболее сложной задачей является создание оборудования для нового метода дифференцированной термической обработки рельсов. Для создания нового метода упрочнения рельсов необходимо:
–получить прямые рельсы с низкими остаточными напряжениями;
–увеличить прокаливаемость головки;
–увеличить управляемость процессом закалки;
–получить возможность термически обрабатывать рельсы из низколегированной стали;
–исключить масло из технологического процесса упрочнения рельсов.
Главный недостаток практического действия системы сертификации на федеральном железнодорожном транспорте России в настоящее время заключается в том, что главные сертификационные испытания, на основании которых и выдаются сертификаты, проводятся на лучших объектах, чем те, которые в массовом порядке попадают на сеть железных дорог. Бороться с этим можно только одним способом: отбирать рельсы для повторной сертификации только на предприятиях ОАО «РЖД» из массовой поставки, а не на заводах-производителях. К сожалению, работники Регистра сертификации по-прежнему продолжают выдавать доверенности на отбор рельсов инспекторам ОАО «РЖД» для полигонных испытаний на заводах-изготовителях.
Основной путь к повышению качества рельсов и оптимизации их цены лежит в преодолении монополизма в производстве рельсов. Существующее положение монопольного производителя рельсов в России
ООО «ЕвразХолдинг», которому принадлежат ОАО «НКМК» и ОАО «НТМК», нельзя признать нормальным. Поэтому ОАО «РЖД» заинтересовано в выходе на отечественный рельсовый рынок продукции ОАО «Мечел», ОАО «Северсталь», которое приобрело итальянский рельсопрокатный завод «Луккини», и японского завода «НиппонСтил», рельсы которого хорошо зарекомендовали себя на Российских железных дорогах в 1990-х гг.
65
Всоответствии с ГОСТ Р 51685–2000 рельсы подразделяют по типам, категориям качества, наличию болтовых отверстий, способу выплавки стали, длине. Кроме того, в новый стандарт введены рельсы типа Р65К с измененным профилем для наружных нитей кривых. Для регионов с холодным и очень холодным климатом предназначены рельсы низкотемпературной надежности (НЭ из электростали и НК из кислород- но-конвертерной стали). Особенно актуальной становиться проблема применения таких рельсов в связи с расширением сферы укладки бесстыкового пути в Сибири и на Дальнем Востоке, где морозы достигают –55 °С, а годовая амплитуда температуры –112 °С [37].
Вэтих условиях особую тревогу вызывает тот факт, что оборудование РСП не позволяет в полной мере внедрить передовую технологию сварки рельсов новых категорий, например, низкотемпературной надежности из электростали и т.д. А ведь дефекты сварки и ранее служили одной из основных причин одиночного изъятия и излома рельсов в пути. Поэтому совершенствование технологий сварки становится одним из приоритетных направлений работы. С учетом расширения сферы укладки бесстыкового пути предусмотрена также поставка рельсов из стали повышенной чистоты с регламентированным содержанием кислорода.
Внедряются рельсы для скоростного совмещенного движения (СС из электростали по ТУ 0921-076- 01124328–2003 и СС из кислородно-конвертерной стали по ТУ 0921 144-01124328–2002) с улучшенными геометрическими параметрами по сравнению с рельсами категории Т1 по ГОСТ Р 51685–2000. При этом рассматривается целесообразность изготовления рельсов длиной 50 м с последующей их сваркой в плети, а также рельсов для высокоскоростного движения.
Конечно, нельзя сказать, что в настоящее время решены все проблемы обеспечения российских железных дорог рельсами, отвечающими возрастающим требованиям повышения эффективности перевозок, которые обусловлены, в том числе, включением наших магистралей в систему транспортных международных коридоров, проходящих по территории России и являющихся основным сухопутным транспортным мостом между Западом
иВостоком, Севером и Югом. В стратегической программе развития отечественных дорог, для которых характерно смешанное движение грузовых и пассажирских поездов, поставлена задача увеличить пропущенный тоннаж между ремонтами верхнего строения пути до 1,0–1,5 млрд т бр., повысить нагрузки грузовых вагонов до 10,5–11,0 т/м, массу грузовых поездов довести до 6000–10000 т, а маршрутную скорость пассажирских поездов поднять до 70–90 км/ч, что предполагает скорость на отдельных перегонах до 160 км/ч.
Способность изготавливать рельсы для таких условий эксплуатации Новокузнецкий и Нижнетагильский металлургические комбинаты обретут после завершения модернизации оборудования в рельсобалочных цехах, внедрения дифференцированного термического упрочнения рельсов, современных средств контроля готовой продукции. Но уже сейчас железные дороги получают отечественные рельсы, обладающие большей надежностью и ресурсом. В 2003 г. по заказам МПС таких рельсов было отгружено около 40 % всего объема поставок, в том числе 190 тыс. т рельсов низкотемпературной надежности и 40 тыс. т рельсов для скоростного совмещенного движения [28].
С целью конкретизации требований к рельсам повышенной эксплуатационной стойкости длиной 50 м для наиболее ответственных направлений сети дорог составлены соответствующие технические условия.
Для конкретных участков рельсы выбирают на основе технико-экономического обоснования в соответствии с методикой ВНИИЖТа. Очень важно правильно организовать работу с рельсами, поступающими в ПМС, РСП и на дистанции пути. Прежде всего нужен входной контроль. Важно также разгруппировать их в зависимости от условий эксплуатации.
Врамках работы «Совершенствование системы ведения рельсового хозяйства» подготовлен и утвержден ряд нормативных документов по шлифованию рельсов, ТУ по репрофилированию рельсов и т.д. Тем не менее нужно еще решить, как использовать рельсы при капитальном ремонте пути, в частности, сохранять и репрофилировать плети, как выпускать, перевозить и сваривать в условиях РСП рельсы длиной 50–100 м, как рационально разместить и реконструировать для этого рельсосварочные предприятия.
Анализируя выгоду от увеличения межремонтного срока до 1 млрд т бр. и более, надо рассчитать баланс рельсов с учетом их потребности для линий третьего, четвертого классов при втором и третьем сроках службы. Актуальна проблема нехватки репрофилированных рельсов для капитального ремонта пути, поэтому нужно вернуться к определению сфер применения старогодных рельсов с учетом их фактического состояния. Следует сформулировать правила списания рельсов, исчерпавших свой ресурс.
«Красная нить» Положения о системе ведения рельсового хозяйства — четкий порядок учета и контроля состояния рельсов на протяжении всего их жизненного цикла. Его предстоит разработать.
3.НАДЕЖНОСТЬ РЕЛЬСОВЫХ СКРЕПЛЕНИЙ
3.1. Новые конструкции промежуточных рельсовых скреплений
В настоящее время одной из актуальнейших задач стоящих перед железными дорогами России является необходимость разработки ресурсосберегающих технологий ведения путевого хозяйства. Одним из способов решения этой задачи является расширение полигона бесстыкового пути на железобетонном подрельсовом основании. Применение таких конструкций с упругими скреплениями и рельсовыми плетями длиной до перегона обеспечит долговременную стабильность пути и увеличение межремонтного тоннажа до 1 млрд т бр. груза.
66
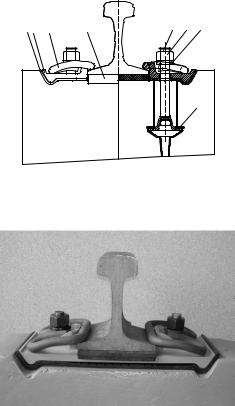
Протяженность бесстыкового пути на 01.01.2008 г. составила 66,7 тыс. км, что соответствует 53,9 % от длины главных путей. Ежегодные темпы прироста бесстыкового пути в среднем достигают 3,2–3,3 тыс. км и к 2010 г. длина бесстыкового пути должна быть 75,3 тыс. км или 61 % от всего протяжения главных путей.
На участках бесстыкового пути применяют серийные рельсовые скрепления трех типов: раздельное подкладочное КБ-65 — 89 % протяженности, бесподкладочное ЖБР-65 — 8 %, безболтовое бесподкладочное — 3 %.
Самым распространенным остается скрепление КБ-65 с жесткими клеммами. Опыт почти 50-летней эксплуатации показал, что оно обладает большим запасам прочности, обеспечено средствами механизации по сборки и содержанию рельсошпальной решетки. К положительным качествам этой конструкции следует отнести двухслойную амортизацию (подрельсовая и нашпальная прокладки) обеспечивающую оптимальную вертикальную и боковую жесткость пути.
Недостатки скрепления КБ хорошо известны: многодетальность, высокая металлоемкость, большой разброс ширины колеи, малый срок службы резиновых прокладок, плохая работа в кривых. Кроме того, требуют постоянного обслуживания резьбовые соединения (около 15 тыс./км), при несоблюдении сроков которого нарушается температурный режим бесстыкового пути.
Скрепление КБ-65, прообразом которого послужило немецкое скрепление «К», выполнило свою функцию и устарело минимум на 20 лет.
Первые серьезные попытки внедрить упругое скрепление на железобетонных шпалах предприняли в 70-х годах прошлого столетия, когда разработали и уложили в путь скрепления типа ЖБ, ЖБР (аналоги французского скрепления RN), клеммы «Краб» в скреплении КБ. По совокупности характеристик все они не удовлетворяли условиям эксплуатации.
Второй этап — начало 90-х годов, когда попробовали наладить производство клеммы ОП-105 — аналога Skl-12 — сначала в Магнитогорске, а затем в Брянске. Попытка обойти патент Vossloh по конфигурации клеммы и незнание ноу-хау изготовления не позволили до настоящего времени создать надежную конструкцию. Нельзя назвать полностью удачным опыт выпуска этой клеммы, также без участия патентовладельца, в Белоруссии. В тот период уложили опытную партию шпал со скреплением типа АРС на ЮгоВосточной дороге.
Третий этап — 1998 г. — начало освоения ЖБР-65 с переходом на массовое внедрение в 2001 г. (рис. 3.1 и 3.2).
1 2 |
3 |
4 |
5 |
6 |
7 |
|
|
|
|
|
8 |
Рис. 3.1. Скрепление ЖБР-65:
1 — упругая прокладка; 2 — упорная скоба; 3 — упругая прутковая клемма; 4 — упругая подрельсовая прокладка; 5 — болт закладной; 6 — гайка; 7 — скоба;
8 — изолирующий пустотообразователь
Рис. 3.2. Скрепление ЖБР-65 П
Cкрепление ЖБР-65 — бесподкладочное с упругими прутковыми клеммами. В отличие от известных зарубежных аналогов (Skl-8, Skl-14) конструкция скрепления ЖБР-65 приспособлена к отечественным условиям производства, эксплуатации и текущего содержания.
67
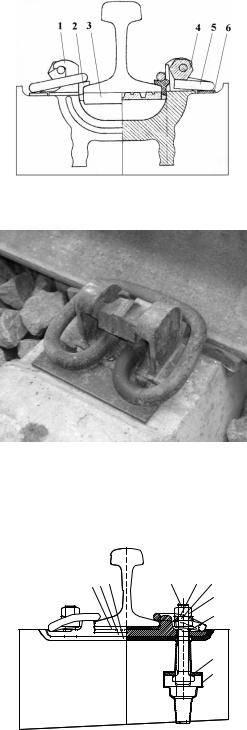
Модернизацией скрепления ЖБР-65 являются шурупно-дюбельный вариант ЖБР-65 ШД и подкладочный вариант ЖБР-65П (рис. 3.2).
Скрепление АРС-4 (рис. 3.3 и 3.4) — анкерное бесподкладочное с упругими клеммами, прижимаемыми к подошве рельса эксцентриковыми монорегуляторами.
Рис. 3.3. Скрепление АРС-4:
1 — анкер; 2 — изолирующий уголок; 3 — подрельсовая прокладка; 4 — монорегулятор; 5 — клемма; 6 — шайба изолятора.
Рис. 3.4. Скрепление АРС (общий вид)
Скрепление КН-65 (рис. 3.5 и 3.6) подкладочное, имеющее упругие пружинные клеммы, предназначено для укладки в прямых и кривых участках бесстыкового пути и на участках с высокими осевыми нагрузками от подвижного состава. Технологично и экономично в изготовлении (используются детали типового скрепления КБ-65, при этом ликвидированы 2 трудоемких паза в реборде, 2 клеммных болта и их пружинные шайбы и гайки) [39].
Рис. 3.5. Скрепление КН-65:
1 — упругая подрельсовая прокладка; 2 — металлическая подкладка; 3 — нашпальная прокладка; 4 — закладной болт; 5 — упругая прутковая клемма;
6 — скоба; 7 — гайка; 8 — шайба седловидная; 9 — изолирующий пустотообразователь; 10 — заглушка резиновая
68
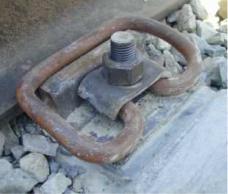
Рис. 3.6. Скрепление КН-65 (общий вид)
69
Таблица 3.1
Характеристика конструкций промежуточных скреплений
|
|
|
Тип скрепления |
|
|||
|
Показатели |
КБ-65 |
ЖБР-65 |
АРС-4 |
КН-65 |
КН-65 |
|
|
|
ШД |
|||||
|
|
|
|
|
|
||
1. |
Количество резьбовых соедине- |
4 |
2 |
— |
2 |
2 |
|
ний, шт. |
|||||||
|
|
|
|
|
|||
2. |
Общее количество деталей в ком- |
23 |
17 |
10 |
17 |
11 |
|
плекте скрепления, шт. |
|||||||
|
|
|
|
|
|||
3. |
Количество металлических дета- |
19 |
12 |
5 |
11 |
7 |
|
лей, шт. |
|||||||
|
|
|
|
|
|||
4. |
Масса узла скрепления, кг |
13 |
8,5 |
8,4 |
12,3 |
12 |
|
5. |
Масса металлических деталей, кг |
12,1 |
7,7 |
7,4 |
11,2 |
10,8 |
|
6. |
Регулировка по высоте, мм |
12 |
10 |
20 |
10 |
10 |
Вразработке и внедрении этого скрепления приняли участие работники СГУПСа профессор Карпущенко Н.И., доценты Антонов Н.И., Величко Д.В. и специалисты Горновского завода спецжелезобетона Отмахов В.А. и Михин А.Я.
В2003 г. поведены Усталостные испытания скреплений КН-65 на стенде «АпАТэК» испытательного центра ЦАГИ в г. Жуковском. Результаты испытаний обоих узлов скреплений под нагрузкой 12 т в условиях, моделирующих взаимодействие бесстыковой рельсовой нити с грузовым составом в крутой кривой радиусом 350 м при наработке 5,5 млн циклов, оказались весьма положительными. Все детали после окончания испытаний оказались целыми. Ослабление затяжки болтов оказалось незначительным.
С 2002 г. скрепление проходит полигонные испытания на Экспериментальном кольце ВНИИЖТа, к осени 2008 г. на участке со скреплением КН-65 пропущено 1300 млн т бр. Скрепления до настоящего времени находятся в хорошем состоянии, ширина колеи находится в пределах допусков, прижатие рельсов к шпалам стабильно, угон пути отсутствует, рельсовые цепи работают безотказно.
К 2007 г. на Западно-Сибирской железной дороге было уложено 126 км пути со скреплением КН-65, в том числе на среднесибирском и транссибирском направлениях.
Скрепление уменьшает динамические силы взаимодействия пути и подвижного состава, за счет этого экономия затрат на выправку пути в плане и профиле. Обеспечивает снижение периодичности подтягивания болтов не менее чем в 2 раза.
Экономическая эффективность его применения в типовой конструкции бесстыкового пути за межремонтный цикл соответственно не менее 400 тыс. р./км на грузонапряженных участках.
На опытных участках, уложенных на Западно-Сибирской дороге со скреплением КН-65, получены данные (наблюдения проводились совместно с путеобследовательской станцией ПС-1), свидетельствующие о хорошем состоянии пути. Ширина колеи находится в пределах допуска, прижатие рельсов к шпалам стабильное, угона пути нет, рельсовые цепи работают безотказно.
В2006 г. комиссия ЦП ОАО «РЖД» признала скрепление КН-65 выдержавшим приемочные испытания. Конструкторской документации присвоена литера «А».
В2007 г. проведено комиссионное обследование участков пути со скреплением КН на ЗСЖД. Комиссия ЦП ОАО «РЖД» на основании анализа материалов эксплуатационных, полигонных испытаний и личного изучения работы скрепления сделала вывод, что это скрепление является надежной, стабильной в эксплуатации и весьма технологичной при производстве путевых работ конструкцией. Западно-Сибирской железной дороге поручено подготовить предложения для ЦП ОАО «РЖД» по освоению массового производства этого скрепления для укладки в различных эксплуатационных условиях.
Дальнейшая модернизация скреплений КН-65 заключается в совершенствовании формы металлической подкладки, а также в коренном совершенствовании скрепления — разработки перспективного скрепления КНУ-65, шурупно-дюбельных вариантов КН-65 ШД (рис. 3.7) и КНУ-65 ШД.
Скрепление КНУ-65 является усовершенствованным вариантом скрепления КН-65, в конструкции также частично используются детали типового скрепления КБ-65, однако основным элементом является оригинальная металлическая подкладка. Реборды подкладки КНУ имеет меньшую толщину и большую высоту (40 мм) по сравнению с подкладкой КБ (32 мм), увеличение высоты реборды дает возможность регулировать положение рельсов по высоте до 18–20 мм, что весьма существенно для сибирских условий. Углубление в железобетонной шпале под подкладку КНУ-65 составляет 32 мм (у подкладки КБ-65 — 25 мм), что соответственно, позволяет увеличить высоту краев подкладки, что существенно уменьшает напряжения по краям нашпальной прокладки и повышает их долговечность.
При таких изменениях расстояние между закладными болтами 240 мм, что увеличивает давление от клемм на подошву рельса и позволит подтягивать гайки болтов моторными гайковертами.
70
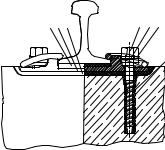
1 |
2 3 |
4 |
5 |
6 |
7
Рис. 3.7. Скрепление КН-65 ШД:
1 — подрельсовая прокладка; 2 — подкладка металлическая; 3 — нашпальная прокладка; 4 — шуруп путевой; 5 — пружинная прутковая клемма;
6 — скоба прижимная; 7 — дюбель
3.2. Сравнительные полигонные испытания скреплений
На Экспериментальном кольце ВНИИЖТ (ст. Щербинка) продолжаются сравнительные полигонные испытания опытных участков звеньевого пути с рельсовыми скреплениями АРС-4, КБ-65, ЖБР-65, КН-65, ЖБР-65П, КНУ-65, где осуществляется движение опытного состава весом около 10 тыс. т с осевыми нагрузками до 300 кН при установленной скорости движения 70 км/ч. Опытный участок пути имеет следующие основные характеристики: рельсы типа Р65 длиной 25 м; железобетонные шпалы с эпюрой 2000 шт./км; щебеночный балласт; круговая кривая R = 400 м; уклон i = 1,4 ‰; участок разбит на опытные микроучастки протяженностью по 50 м: АРС-4, КБ-65, ЖБР-65, КН-65; а также опытные микроучастки КНУ-65 — 25 м, ЖБР-65П — 12,5 м.
К2006 г. тоннажа по участкам АРС-4, КБ-65, ЖБР-65, КНУ-65 составила 786,0 млн т бр., КН-65 — 554,3 млн т бр., ЖБР-65П — 486,2 млн т бр. [40].
Основные показатели, полученные после пропуска по опытным участкам тоннажа 800 млн т бр., приведены в табл. 3.2 и 3.3.
Кконцу 2007 г. наработка тоннажа составила порядка 1,2 млрд т бр. — нашпальные прокладки скрепления КНУ целые.
Анализ данных табл. 3.2 и 3.3 показывает, что в крутой кривой ширина рельсовой колеи меньше расстраивается на участках с подкладочными скреплениями. Наиболее стабильной она оставалась на участке КНУ-65, КН-65 и ЖБР-65П [48].
71
Таблица 3.2
Основные показатели работы скреплений
|
|
Участки с наработкой |
Участки с наработкой тоннажа 500 млн т бр. |
|||||
Наименование показателей |
тоннажа 800 млн т бр. |
|||||||
|
|
|||||||
|
|
АРС |
КБ |
ЖБР |
КНУ |
КН |
ЖБР-П |
|
Длина участка, м |
50 |
50 |
50 |
50 |
25 |
12,5 |
||
Средняя ширина ко- |
0 млн т |
1524,2 |
1525,6 |
1521,6 |
1521,0 |
1523,9 |
1524,2 |
|
500 млн т |
1538,5 |
1538,6 |
1532,5 |
1529,9 |
1529,0 |
1529,5 |
||
леи, мм |
||||||||
800 млн т |
1532,9 |
1534,1 |
1532,8 |
1528,1 |
— |
— |
||
|
||||||||
Среднеквадратическое |
0 млн т |
0,98 |
0,66 |
1,80 |
1,72 |
1,11 |
1,25 |
|
500 млн т |
2,23 |
2,41 |
4,65 |
2,69 |
3,21 |
0,76 |
||
отклонение |
||||||||
800 млн т |
2,34 |
2,06 |
2,82 |
2,86 |
— |
— |
||
|
||||||||
Средняя подуклонка |
наружная |
1/29,6 |
1/23,8 |
1/25,9 |
1/21,3 |
1/21,2 |
1/27,8 |
|
рельсовых нитей |
внутренняя |
1/29,0 |
1/27,5 |
1/22,7 |
1/26,6 |
1/22,2 |
1/22,0 |
Таблица 3.3
Отказы элементов пути за период сравнительных полигонных испытаний рельсовых скреплений, имеющих наработку тоннажа 800 млн т бр.
Наименование |
Тоннаж, |
|
|
|
|
|
Отказы элементов |
|
|
|
||||
млн т |
АРС (50 м) |
|
КБ (50 м) |
|
ЖБР (50 м) |
|
КНУ (25 м) |
|||||||
элементов |
|
|
|
|||||||||||
бр. |
шт. |
|
% |
|
шт. |
% |
|
шт. |
% |
|
шт. |
|
% |
|
|
|
|
|
|
|
|||||||||
|
100 |
4 |
|
1 |
|
0 |
0 |
|
1 |
1 |
|
0 |
|
0 |
Клеммы |
500 |
4 |
|
1 |
|
1 |
1 |
|
4 |
1 |
|
1 |
|
1 |
|
800 |
7 |
|
2 |
|
1 |
1 |
|
5 |
2 |
|
1 |
|
1 |
Подрельсовые про- |
100 |
7 |
|
4 |
|
11 |
6 |
|
13 |
7 |
|
|
|
|
500 |
82 |
|
41 |
|
251 |
126 |
|
243 |
122 |
|
не осматривались |
|||
кладки |
|
|
|
|
||||||||||
800 |
106 |
|
53 |
|
274 |
137 |
|
339 |
170 |
|
|
|
|
|
|
|
|
|
|
|
|
|
|||||||
|
100 |
0 |
|
0 |
|
|
|
|
|
|
|
|
|
|
Анкеры |
500 |
0 |
|
0 |
|
|
|
нет |
|
|
|
нет |
||
|
800 |
1 |
|
1 |
|
|
|
|
|
|
|
|
|
|
Изолирующие уголки |
100 |
200 |
|
100 |
|
|
|
|
|
|
|
|
|
|
500 |
941 |
|
471 |
|
|
|
нет |
|
|
|
нет |
|||
АРС (наружные) |
|
|
|
|
|
|
|
|||||||
800 |
1110 |
|
555 |
|
|
|
|
|
|
|
|
|
|
|
|
|
|
|
|
|
|
|
|
|
|
|
|||
Нашпальные проклад- |
100 |
|
|
|
|
91 |
46 |
|
|
|
|
0 |
|
0 |
500 |
нет |
|
|
621 |
311 |
|
нет |
|
0 |
|
0 |
|||
ки |
|
|
|
|
|
|||||||||
800 |
|
|
|
|
753 |
377 |
|
|
|
|
0 |
|
0 |
|
|
|
|
|
|
|
|
|
|
|
|||||
Упругие прокладки |
100 |
|
|
|
|
|
|
|
169 |
85 |
|
|
|
|
500 |
|
|
нет |
|
|
|
259 |
130 |
|
|
нет |
|||
ЖБР (наружные) |
|
|
|
|
|
|
|
|||||||
800 |
|
|
|
|
|
|
|
298 |
149 |
|
|
|
|
|
|
|
|
|
|
|
|
|
|
|
|
|
|||
Металлические под- |
100 |
|
|
|
|
0 |
0 |
|
|
|
|
3 |
|
4 |
500 |
нет |
|
|
12 |
6 |
|
нет |
|
5 |
|
6 |
|||
кладки |
|
|
|
|
|
|||||||||
800 |
|
|
|
|
20 |
10 |
|
|
|
|
7 |
|
9 |
|
|
|
|
|
|
|
|
|
|
|
|||||
|
100 |
1 |
|
1 |
|
6 |
6 |
|
32 |
32 |
|
1 |
|
2 |
Железобетонные шпалы |
500 |
2 |
|
2 |
|
9 |
9 |
|
36 |
36 |
|
1 |
|
2 |
|
800 |
4 |
|
4 |
|
11 |
11 |
|
45 |
45 |
|
1 |
|
2 |
Подуклонка рельсовых нитей также стабильнее на участках с подкладочными скреплениями, в первую очередь, со скреплением КН-65. Более интенсивное изменение подуклонки в бесподкладочных скреплениях связано с их меньшей жесткостью и интенсивным износом подрельсовых прокладок.
На всех сравниваемых участках пути происходили отказы элементов в узлах скреплений. Очень большое количество отказов произошло на участке АРС-4 — 1223 (в основном — изолирующие уголки), КБ-65 — 1048 (нашпальные прокладки), ЖБР-65 — 647 (упругие и подрельсовые прокладки).
Значительно меньше отказов произошло на участках подкладочных скреплений, в том числе КНУ-65 — 8 шт. (участок протяженностью 25 м и не осматривались подрельсовые прокладки), ЖБР-65П (12,5 м) — 12 шт., КН-65 (50 м) — 95 шт. При этом участки КН-65 и ЖБР-65П имеют наработку тоннажа примерно 500 млн т бр.
Следует отметить, что состояние элементов скреплений существенно зависит от применяемых подрельсовых и нашпальных прокладок. Лучше всех отработали резинокордовые и армированные полимерными волокнами прокладки производства ООО «Союзспецмаш» (г. Барнаул). Например, за весь период испытаний 800 млн т бр. в скреплении КНУ-65 не зафиксировано ни одного отказа нашпальной прокладки данного производителя.
Анализ сравнительных полигонных испытаний рельсовых скреплений с упругими клеммами показал хорошую надежность подкладочных вариантов — скреплений КН-65 и КНУ-65.
3.3. Деформационные и жесткостные показатели прокладок
Решающая роль в формировании жесткости пути на железобетонных шпалах принадлежит прокладкамамортизаторам. Одновременно они являются лимитирующим элементом в промежуточных скреплениях, от служебных свойств которого в значительной степени зависит надежность пути, а также затраты на его содержание и ремонт. В настоящее время для изготовления таких прокладок используют резиновые смеси, подобранные с учетом особенностей работы пути [41, 42].
72