
730
.pdf
кихпараметровсприменениемкритериальнойсистемыВ.И.Верещаги-
на[1].
Согласно предложенной методике воздействие микродобавки на модифицируемый оксид можно оценить по характерной зависимости расположениякатионовдобавоквдиаграмме, построеннойвкоординатах, гдеотносительная разница радиусов катионов соответствующего элемента добавки поотношению к катионумодифицируемогооксида; - разностьихэлектроотрицательностей.
Применительно к системе Mn—Zn— Fe наиболее эффективные модификаторыоказалисьрасположеннымивобластидиаграммысгра-
ницами |
r |
|
0,30 0,45 и |
|
|
|
160 кДж/моль. Можно предположить, |
|||
|
|
|
|
|||||||
|
|
|||||||||
|
|
|
|
r0 |
|
|
|
|
||
|
|
|
|
|
|
|
|
|||
чтопри |
|
|
|
r |
|
|
|
|
|
|
|
|
|
|
|
0,3 вполневероятнообразованиетвердыхрастворовмик- |
|||||
|
|
|
||||||||
|
|
|
|
|
||||||
|
|
|
|
r0 |
|
|
|
|
родобавки с модифицируемыми оксидами (область неограниченной
растворимости), а при |
|
r |
0,45 — образование микрофаз на повер- |
|
|
||
|
|
r0 |
хности микрокристаллов основной фазы; интервал, равный 0,30–0,45, определяет область ограниченной растворимости.
Местонахождениякатионадобавкинадиаграммевблизиединичной силы связи M–О в модифицируемом оксиде ( 160 кДж/моль) предопределяет ослаблениесвязейскислородом, чтовызывает ослабление связеймеждучастицами,микрокристалламииблоками(т.е.научастках, гденаблюдаетсялокализациядобавок).Этоприводит,всвоюочередь, к интенсификациипроцессауплотнениядисперсныхоксидовподдействием сил поверхностного натяжения по механизмузернограничного проскальзываниянаначальныхстадияхспекания.Назавершающихстадиях спекания в этом случае более интенсивнодолжен происходить процесс зернограничной диффузии. Частичное растворение добавок в решетке спекаемого оксида активировало процесс объемной диффузии.
Обработка пористых ферритовых изделий из-за гидрофильности минеральных составляющих текстуры прежде всего сопровождается хорошим смачиванием и прониканием раствора по объемутела за счет капиллярных сил. Приэтоммогутпротекатьпроцессытравлениявещества и ионообменное взаимодействие феррит–раствор.
Атомно-абсорбционныйанализ(спектрофотометрPERKIN-ELMER чувствительностью 0,001 мкг/мл) водных растворов солей до и после обработкивнихпористыхферритовыхобразцоввтечение30–50минпри комнатной температуре (табл. 1) показал незначительное растворение составляющихкомпонентовферритарастворамисолей;большейсклон-
141
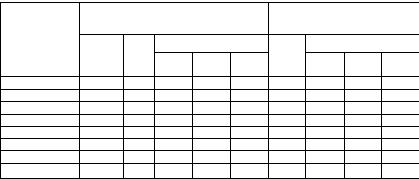
ностьюквытравливаниюобладаетмарганец,наименьшей—цинк.Уве- |
|||||||||
личение кислотности раствора повышает химическое взаимодействие |
|||||||||
его с ферритом, причем при использовании чистого раствора кислоты |
|||||||||
вытравливание компонентов происходит в несколько раз интенсивнее, |
|||||||||
чем при обработке раствором соли с близкими значениями рН. |
|
||||||||
|
|
|
|
|
|
|
|
Таблица 1 |
|
|
Раствор соли до обработки образцов |
Раствор соли после обработки |
|||||||
|
|
образцов |
|
||||||
|
|
|
|
|
|
|
|
||
Соль |
концен- |
|
содержание, мкг/мл |
|
содержание, мкг/мл |
||||
|
|
|
|||||||
|
трация, |
pH |
Fe |
Мn |
Zn |
pH |
Fe |
Мn |
Zn |
|
% |
|
|
||||||
VOSO4·3H2O* |
15 |
1,60 |
10,00 |
5,00 |
2,00 |
1,67 |
30,00 |
50,00 |
4,00 |
VOSO4·3H2O |
7,5 |
– |
5,00 |
5,00 |
2,00 |
– |
25,00 |
50,00 |
4,00 |
Zr(NO3)4·5H2O |
20 |
-0,10 |
20,00 |
5,00 |
2,00 |
0,20 |
150,00 |
100,00 |
10,00 |
Sm(NO3)4·6H2O |
20 |
5,45 |
0,30 |
5,00 |
2,00 |
5,45 |
0,30 |
20,00 |
2,00 |
Co(NO3)2·6H2O |
25 |
3,80 |
2,00 |
5,00 |
2,00 |
4,30 |
2,00 |
25,00 |
2,00 |
CuSO4·6H2O |
20 |
4,40 |
10,00 |
5,00 |
2,00 |
4,30 |
10,00 |
25,00 |
2,00 |
H2SO4 |
– |
1,60 |
0,01 |
0,01 |
0,10 |
1,90 |
0,30 |
13,00 |
2,00 |
HNO3 |
– |
-0,35 |
0,20 |
0,02 |
0,10 |
0,30 |
30,00 |
5,00 |
0,50 |
* Содержание ванадия как при однократной,, так и при многократной пропитке |
|||||||||
составило 60 мкг/мл (для определения содержания ванадия 15 %-ный раствор соли |
|||||||||
разбавлен в 500 |
раз). |
|
|
|
|
|
|
|
|
Фиксируемоевысокочувствительнойаппаратуройхимическоевзаимодействие междуферритом и раствором соли посвоему абсолютному значениюиприпринятыхусловияхобработкиявляетсянезначительным. Вытравливаниемарганца, наиболее подверженногоэтомупроцессу, не превышает0,0001%,чтозначительноменьшетребуемогодлясоблюдения стехиометрического состава феррита. При этом ионообменного взаимодействияферрита3000НМСсрастворомсолиVOSO4·3H2Oнеобнаружено.
На основе выполненного исследования выбрана технология модифицированияферритовыхизделий,предусматривающаяпредвари- тельнуютермообработкуобразцовпри600°Свтечение1,5–2ч, обработкупрокаленных пористых изделий в холодном растворесоли в течение 15–30мин, просушиваниепропитанныхизделийпринормальныхусловияхи последующееих спекание.
Аномальный ход кривых усадкиобразцов (рис. 2), модифицированных V2O5 и Bi2O3, по сравнению с другими модификаторами и контрольной партией, свидетельствует, что процессы деферритизации при спекании практически отсутствуют. Этому способствует образование легкоплавкихэвтектикмодификаторовV2O5 иBi2O3 вместесосновными
142
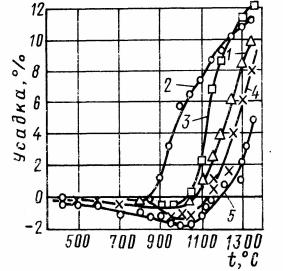
оксидамиферрита,преждевсегосFe2O3,чтопредотвращаетихфазовый распад.
Рис. 2. Спекание модифицированного феррита 3000 НМС (содержание добавок в молярных долях):
1— контрольный; 2 — 0,6 % V2O5; 3 — 0,1 % Bi2O3; 4 — 0,6 % ZrO2; 5 — 0,6 % Sm2O3
УвеличениесодержанияV2O5 от0,2до1,2%(молярнаядоля)усиливаетпроцессспекания(рис.3). Замедлениепроцессаспекания(см.рис. 2 и 4) модификатором Sm2O3, видимо, связано с большим значением ионного радиуса Sm3+ (0,113 нм по Гольдшмидту), что предопределяет расположение добавки по границам зерен и препятствует их росту.
Микродобавкипо-разномувлияют на формированиемикроструктуры и связанные с ней свойства феррита [2]. Микроструктура феррита с добавкойSm2Озравномерная,мелкокристаллическаясосредним разме- ромзерен7–10мкмивнутрикристаллическойпористостью0,5 %(рис. 5). Феррит, модифицированный ZrO2, при тех же условиях имеет крупнокристаллическую структуру со средним размером зерен 100 мкм и большойвнутризерновойпористостью(9%).Различноевлияниенаформирование микроструктуры добавок первой группы объясняется, вероятно, разными значениями ионных радиусов добавок Sm3+, Zr4+.
Характермикроструктурыобразцовсмодификаторамивторойгруппымаломеняетсяотвидадобавки. Болееоднороднаяпоразмерамзерен формируется структура у ферритов с добавками CuO, CaO и менее однородная - уферритов с модификаторами SnO2, In2O3 (см. рис. 5, в).
143
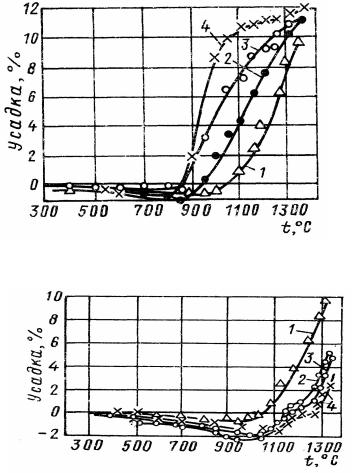
Рис. 3. Влияние добавки V205 (молярное содержание) на спекание
3000 НМС:
1 — контрольный; 2 — 0,2%; 3 — 0,6%; 4 — 1,0%
Рис. 4. Влияние добавки Sm2O3 (молярное содержание) на спекание феррита 3000 НМС:
1 — контрольный; 2 — 0,2 %; 3 — 0,6 %; 4 — 1,4%
МикроструктураобразцовсмодификаторомV2O5 крупнозернистая, однородная по размерам зерен (средний размер 40–50 мкм) с внутрикристаллической пористостью 1–3 % (см. рис. 5, г). Структура образцовсдобавкойBi2O3неоднороднаяпоразмерузерен,наблюдается вторичнаярекристаллизация.
Электромагнитные и физико-механические свойства модифицированныхферритовприведенывтабл.2.Наиболееблагоприятноевлияние намагнитныеипрочностныесвойстваобразцовоказываетдобавкаV2O5.
144

Рис. 5. Микроструктура модифицированного добавками (молярное содержание) феррита 3000 НМС:
а — контрольный; б — 0,6 % Sm2О3; в — 0,6 % CuO; г — 1,0 % V2O5
145
Таблица 2
|
|
Изменение свойств феррита по |
Микроструктура |
|||
|
Молярное |
отношению к контрольным |
||||
|
образцов |
|||||
|
содержание |
|
образцам, % |
|
||
|
|
|
|
|
||
Оксид |
добавки, |
магнитные |
магнитная |
прочность |
диаметр |
пористость, |
|
% |
потери |
проницае- |
|||
|
|
мость |
/ |
зерен, мкм |
% |
|
|
|
W/W |
||||
|
|
/ |
|
|
|
|
|
|
|
|
|
|
|
СаО |
0,72 |
+23 |
-19 |
+40* |
20 |
10 |
CuO |
0,40 |
-12 |
+4 |
+20* |
45 |
12 |
|
0,80 |
-7 |
-12 |
+18* |
28 |
11 |
CoO |
0,50 |
+73 |
-44 |
+45* |
31 |
5 |
In2O3 |
0,28 |
-4 |
+10 |
+30 |
80 |
8 |
|
1,02 |
-33 |
+37 |
+13 |
60 |
10 |
Sm2O3 |
0,30 |
+13 |
+5 |
– |
13 |
7 |
|
0,90 |
+41 |
-20 |
+70 |
7 |
10 |
ZrO2 |
0,20 |
+112 |
-44 |
+60* |
60 |
11 |
|
0,40 |
+102 |
-45 |
+60* |
100 |
10 |
Bi2O3 |
0,10 |
+13 |
-8 |
+78 |
35 |
8 |
V2O5 |
0,15 |
-18 |
+21 |
+40 |
40 |
6 |
|
0,40 |
+5 |
+10 |
+76 |
55 |
5 |
|
0,70 |
+18 |
-10 |
+80 |
70 |
6 |
* Образцы испытаны на сжатие, остальные — на изгиб.
Гибкость и надежность технологического процесса получения ферритовыхизделийметодоммодифицированияиз водныхрастворовсолей различныхэлементовиихкомпозицийпозволяетуправлятьпроцессами формированиямикроструктурыизделиинастадииспеканияипридавать им необходимыесвойства.
Литература
1.Верещагин В.И. Структурно-энергетические критерии модифицирования
микродобавками керамических материалов системы MgO–Al2O3–SiO2: Автореф. дис. ... д-ра техн. наук. ЛТИ, 1982. 36 с.
2.Горелик С.С., Бабич З.А., Летюк В.М. Формирование микроструктуры и
свойств ферритов в процессе рекристаллизации. М.: Металлургия, 1984. 110 с.
146

4.2.ФИЗИКО-ХИМИЧЕСКИЕ ОСНОВЫ МОДИФИЦИРУЮЩЕГО
ДЕЙСТВИЯ ДОБАВОК В Мn-Zn-ФЕРРИТАХ*
Взаимодействие вводимых добавок с основой керамического материала может сопровождаться различными процессами:
—образованиемизовалентныхилигетеровалентныхтвердыхрастворов с малодефектной или дефектной структурой возникающих фаз;
—изменением состава и свойств межзеренной прослойки между кристаллитами основной фазы;
—сегрегациейдобавокнаповерхностизеренкристаллическойфазы
собразованием новых соединений;
—образованием легкоплавкихмикрорасплавоввсистеме:основная фаза-добавка.
В зависимости от проявления того или иного вида взаимодействия добавкисосновойкерамикиопределяется эффектеедействиянареальную структуру и целевые свойства.
При разработке критериальной системы оценки предпочтительных добавок применительно к шпинельной керамики (система МnО-ZnО-
Fe2O3) нами были использованы соотношения кристаллохимических и энергетическихпоказателеймеждумодифицируемымимодифицирующим оксидами. При выяснении механизма действия добавок учитываласьвероятностьобразованиянеравновесныхдефектов(вакансий, дислокаций) в поликристаллах и на основе анализа диаграммы состояния исследуемой системыоценивалась возможностьвозникновениямикрорасплавов.
Теоретическийпрогнозпредпочтительныхдобавокбылосуществлен поихфизическим ихимическимпараметрам,приэтомбылаприменена графическая форма оценки добавок на диаграммах в координаторах: разность электроотрицательностей и относительная разница радиусов катионов[1]. Установлено,чтоточки,характеризующиекатионыэффективныхдобавок,располагаютсяпреимущественновзонедиаграммы,где разности электроотрицательностей приближаются к величине единичнойсилысвязи М–Овмодифицированном оксиде, апогоризонтальной координате — в области неограниченной растворимости (рис. 1). Результаты прогнозов имеют удовлетворительное совпадение с экспериментальнымиданными.
Выполненный анализ имеющихся диаграмм состояния систем, со-
держащихосновныекомпоненты(МnО,ZnО,Fe2O3)марганец-цинковых ферритов,ивыбранныхдобавокпоказывает,чтотольконемногиеизних, напримерV2O5,Li2O,Вi2O3,СаО,могутбытьпотенциальнымикомпонен-
*Плетнев П.М., Федоров В.Е. Пятая Всеросс. науч. конф. «Оксиды. Физ.-хим. Свойства», г. Екатеринбург, 2000. С. 531–533.
147
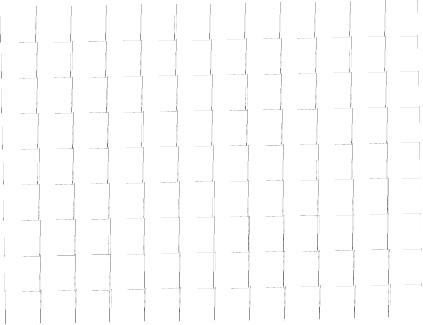
тамидляобразованиярасплавапритемпературахниже1300°С. Особый интересвызываетоксидванадия,длякоторогоэвтектическиетемперату- рывсистемах:V2O5-ZnО;V2O5-Fe2O3непревышают700°С.
Рис. 1. Диаграмма критериальной оценки по выбору добавок для оксидов: MnO, NiO, ZnO, FeO
Результатыпроведенногоанализалегливосновуэкспериментальных исследований.Учитываямалыеколичествавводимыхдобавок(от0,05до 1,0 мас. %) и требуемую высокую гомогенность их распределения по объемуматериала,привведениидобавокиспользовалсяметодобработки ферритизованной шихты или отформованных изделий водными растворами солей.
Превалирующими процессами взаимодействия ферритовой композициисхолоднымираствораминитратовисульфатов(поданнымхими- ческогоиатомно-адсорбционногоанализов) являютсякапиллярноенасыщениеифизическаяадсорбция;рольионногообменаприэтом незначительна.
Похарактерувлияниянапроцессеспеканияиформированиемикро- структурыМn-Zn-ферритов(напримеремарки3000НМС)модификато- ры можноразделить на три группы [2]:
—ухудшающиеспекание— ZrO2, Sm2O3, Nd2 O3;
—маловлияющиена спекание— СuО, СаО, In2O3, SnO2;
148
—активноинтенсифицирующиеспекание— V2O5, Вi2O3. Наиболее эффективно действуют на образование микроструктуры
ферритадобавкиSm2O3,Nd2O3, ZrO2 иV205.ДобавкаZrO2способствует образованию крупнокристаллической неравномерной структуры феррита, а оксидыредкоземельных элементов— Sm2O3 и Nd2O3— эффективно влияют на торможение рекристаллизационного роста зерен Мn- Zn-ферритами. Ихдействиесвязано с«блокировочным»эффектом сегрегированныхинертныхоксидов(ZrO2)илиобразующихсянаповерхности зерен феррита соединений с иной, чем ушпинели, структурой типа граната, перовскита(Sm2O3 Nd2O3).ДобавкиV2O5, Вi2О3 способствуют образованиюнизкотемпературногорасплава, засчетчегорезкоускоряется уплотнение материала по механизмумежграничного проскальзывания.
Наиболее однородной (с размером зерен 30–60 мм), малопористой (неболее5–7 %),счеткойогранкойкристалловхарактеризуетсямикроструктура феррита, легированного добавкой ванадия. В этом случае образующийся низкотемпературный расплав с добавкой V2O5обладает уникальным сочетанием физико-химических свойств (вязкостью, смачиванием, поверхностным натяжением и др.), что обеспечивает благоприятные условия для формирования малонапряженной структуры феррита. Сформировавшееся микроструктураи субструктура, включая ее доменный характер, в значительной мере определяет весь комплекс физико-механическихиэлектромагнитныхпараметровматериала.Ком- плексное применение добавок V2O5+СоO позволяет получить высокоплотный, прочный и термостабильный Мn-Zn-феррит.
Внедрение разработанных Мn-Zn-ферритов, модифицированных добавкамиV2O5+СоО, впроизводственавигационныхприборовобеспечило повышениеих техническогоуровня и в определенной мере позволило решить проблему по созданию прецизионных ферритов нового класса.
149

УДК 541.182 : 621.318.1
4.3.ЛАЗЕРНАЯ ГРАНУЛОМЕТРИЯ ПОРОШКОВ ПРИ
ПОЛУЧЕНИИ Mn-Zn-ФЕРРИТОВ*
Для определения гранулометрического состава шихты, используемой при получении изделий из Mn-Zn-ферритов использован метод дифракции лазерного излучения. Показано, что при увеличении содержания в ферритизованной шихте количества фракций с размером зерен менее 4 мкм увеличивается степень ферритизации шихты, возрастает намагниченность и температура спекания материала. Дополнительная термообработка шихты на воздухе при температуре 700–900 оС с последующим измельчением позволяет улучшить спекание и свойства изделий, однако термообработка при 1000–1100 оС приводит к получению порошка с преобладанием фракций более 4 мкм, спекание которого затруднено.
Изготовлениекерамическихизделий, втомчислеферритов, предусматривает получениешихты в видепорошка, формованиеизделий и их последующее спекание. Протекание твердофазных реакций, фазовых превращений, плотноеспеканиеизделийвомногом определяется свойствами исходных порошков, преждевсегоих дисперсностью. При этом важен не только средний размер частиц порошка (или его удельная поверхность), но и гранулометрический егосостав, распределениечастиц по фракциям.
Втехникеиспользуютразличныеметодыопределениядисперсности материалов[1–5]:ситовойанализ;микроскопическиеизмерения,вклю- чая оптическую и электронную микроскопию; определение газопроницаемостислояматериала;адсорбционныеметоды;импульсныеметоды (Коултера и др.). Большие возможности обеспечивает использование лазерныхметодов[4,5].
Вданной работе использован лазерный анализатор дисперсности типаPRO-7000фирмыSeishinEnterpriseCo.,LTD,Tokyo,которыйобес-
печиваетпроведениеизмеренийразмеровчастицвпределах1–192мкм по16интерваламзначений.Получаемыезначенияявляютсярезультатом не менее, чем 320 непрерывно повторяющихся измерений, производимых фотодетекторами в течение 30 с, что обеспечивает их высокую точность и воспроизводимость.
Объектом исследованияявляласьMn-Zn-ферритоваякерамикамар-
ки3000НМС[6],имеющаясостав,мас.%:71,3±0,3Fe2O3;19,8±0,3MnO; 7,6±0,2ZnO;0,9±0,1NiO.Ееначальнаямагнитнаяпроницаемостьсоставляет3000±500,температураКюри200 оС.Использованиеприполучении ферритизованнойшихтыэтогоматериаламетодомсовместногоосажде-
*Плетнев П.М., Новикова Н.И., Лиенко В.А., Бердов Г.И. Материаловедение. 2005. № 2. С. 11–15.
150