
730
.pdfПриведенныевтабл. 2результаты светопропусканияразличныхмароккерамикисвидетельствуютовыраженнойизбирательнойспособностикпоглощениювзависимостиотспектраизлучения. Так,дляалюмо- оксиднойкерамикимаркиА-995,структуракоторойпрактическиполно- стьюсложенаиз кристалловкорунда,измененияпоказателяпоглощения света взависимости от спектральной характеристикиизлучателя могут составлять от450м–1 до180 м–1.
|
|
|
|
|
|
|
Таблица 2 |
|
Результаты светопропускания алюмооксидной керамики |
||||||
|
|
|
|
различных марок |
|
|
|
|
|
|
|
|
|
|
|
Свето- |
|
|
|
Спектр излучателя – лампа накаливания |
|||
про- |
|
Марка керамики |
сплошной |
светофильтр |
светофильтр |
светофильтр |
|
|
( = 400 |
СЗС-7 |
ЖЗС-9 |
ОС-11 |
|||
пускание |
|
|
|||||
|
|
780 нм) |
( 560 нм) |
( = 500 580нм) |
( 560нм) |
||
|
|
|
|
||||
-1 |
|
|
А-995 |
194 |
395 |
449 |
180 |
м |
|
|
(h = 7,0 мм) |
||||
поглощенияПоказатель, |
|
|
|
|
|
|
|
|
Алюмооксидная |
ВК95-1 |
335 |
598 |
839 |
470 |
|
|
(h = 2,6 мм) |
||||||
|
|
|
|||||
|
|
|
|
|
|
|
|
|
|
|
|
|
|
|
|
|
|
|
22XC |
961 |
2513 |
3362 |
1398 |
|
|
|
(h = 1,4 мм) |
||||
|
|
|
|
|
|
|
|
|
|
|
|
|
|
|
|
У алюмооксидной керамики ВК95-1 показатель поглощения колеблется от335 до840, аукерамики22ХС сдобавлением Cr2O3 и MnO – от 960до3360.Важнымявляетсятотфакт,чтодлявсехисследуемыхкерамических образцов в диапазоне излучения = 500 570 нм (светофильтр ЖЗС-9)наблюдаетсямаксимумпоглощения.
Влияниеструктурыифазовогосостава(см. табл. 2)керамикипроявляется особенно четко при сравнении результатов светопропускания различныхмарокалюмооксиднойкерамикиА-995иВК95-1. Структура керамикимарокА-995иВК95-1отличаетсятем, чтоструктуракерамики А-995 является однофазной ( – Al2O3), а в керамике ВК95-1 наряду с корундом присутствует магний – алюмосиликатная стеклофаза в количестведо7 %. ПоэтомуповышенноесветопропусканиекерамикиА-995 обусловлено ее однофазным кристаллическим строением с небольшим содержанием пор. Меньшая светопропускная способность керамики ВК95-1 связана с ее мелкозернистым строением корунда, наличием стеклофазы и большей пористостью.
Большоезначениепоказателяпоглощенияалюмооксиднойкерамики 22ХСобусловленовлияниемкрасящихсядобавок(Cr2O3,MnO),вводимыхвсостав материала.
51

Заключение
Таким образом, установленныеструктурныеособенности алюмооксидной керамики ВК95-1 от температуры обжига образцов согласуется срезультатами ихсветопропускания, чтопозволяет рассматриватьсветопропусканиекаккомплекснуюхарактеристикуприисследованиипроцессовспеканиякерамическихматериаловиконтролякачестваготовых изделий. Достоинствами светопропусканияявляются высокаячувствительность к происходящим структурным изменениям материала, безопасностьиспользованияивозможностьсозданияизмерительныхсредств неразрушающего контроля качества различных светорассеивающих материаловиизделий.
Литература
1.Рубашов М.А., Бердов Г.И., Гаврилов В.Н. и др. Термостойкие диэлектрики
иих спаи с металлами в новой технике. М.: Атомиздат, 1980. 246 с.
2.Лиенко В.А., Бердов Г.И. и др. Улучшение структуры и свойств алюмооксид-
ной керамики // Стекло и керамика. 1989. № 7. С. 19–20.
3.Дегтярева Э.В. Микроструктура прозрачной поликристаллической корундовой керамики и ее взаимодействие с просвечиваемостью / Неорганические материалы. 1967. Т. III. № 12.
4.Бердов Г.И., Плетнев П.М. и др. Неразрушающий оптический контроль качества керамических изделий // Электронная техника. Сер. «Технология, организация производства и оборудования», 1979. Вып. 2. С. 1–6.
5.Бердов Г.И., Плетнев П.М. и др. Неразрушающий контроль качества керамических изделий оптическим методом // Стекло и керамика. М.: Стройиздат, 1988. Вып. 8. С. 17–18.
6.Зисман Г.А., Тодес О.М. Курс общей физики. 6-е изд. М.: Наука, 1980. Т. 3
496 с.
1.6.ВАКУУМНО-ПЛОТНАЯ ФОРСТЕРИТОВАЯ КЕРАМИКА СО СТРОНЦИЙ-АЛЮМОСИЛИКАТНОЙ СТЕКЛОФАЗОЙ*
Исследованы свойствавакуумно-плотнойфорстеритовой керамики, всоставкоторойвводилиуглекислыйстронций, чтообеспечивалополучениестеклофазы стронцийалюмосиликатногосостава. Показаны преимущества такой керамики перед материалами, имеющими барийалюмосиликатную стеклофазу: более низкая (на 30–50° С) температура и расширенныйинтервалспекания, высокаяпрочностьинадежностьспаев с титаном.
Свойства вакуумноплотной форстеритовой керамики, широко применяемой в электронной технике для спаев с титаном, в значительной
* Бердов Г.И., Плетнев П.М., Усов П.Г., Верещагин В.И., Шильцина А.Д. Вакуум- но-плотная форстеритовая керамика со стронцийалюмосиликатной стеклофазой // «Электронная техника». Сер. «Материалы». 1974. Вып. 3. С. 73–79.
52
степени зависят от состава его стеклофазы. В отечественных [1–3] и зарубежных [4–6] составах вакуумноплотной форстеритовой керамики стеклофаза имеет преимущественно барийалюмосиликатный состав. Стеклофаза такого состава обеспечивает хорошее сочетание свойств материала.Приэтомважнуюрольвформированиисвойствстеклофазы играет окись бария. Обычно используемые соотношения окислов BaO:Al2O3:SiO2 обеспечиваютполучениевакуумноплотныхизделийпри приемлемыхтемпературахобжига.
Возрастающиетребованияквакуумноплотнымкерамическим материалам, в частности к форстеритовой керамике, определяют необходимостьразработкиновыхсоставовсулучшеннымисвойствами.Однимиз путей совершенствованияфорстеритовой керамикиявляется использование новых составов стеклофазы. Среди окислов щелочноземельных элементов, которыемогутположительновлиятьнасвойствакерамическогоматериала,необходимовыделитьокисьстронция,влияниекоторой насвойствастеколбылоизученоглавнымобразомвпоследниегоды[7]. При этом было установлено, что окись стронция способствует улучшениюрядаважныхсвойствстекол:уменьшаеткристаллизационнуюспособностьивязкость, удлиняеттемпературныйинтервалполитогообжига, снижает его конечную температуру и т.д.
Представляет интерес исследование вакуумноплотной форстеритовой керамики состронцийсодержащей стеклофазой, использованиекоторой может обеспечить улучшение свойств материала.
Исследованные составы керамики
Соотношения окислов SrO : Аl2O3: SiO2 в составе стеклофазы были взятывполекристаллизациисиликатастронция(вобластинизкотемпературных изотерм) в соответствии с диаграммой состояния тройной системыSrO–Al2O3–SiO2 —составыV, VII,VIII,IX(см. рисунок).
При составлении шихты керамики в качестве основных исходных материаловиспользовалиобогащенныйталькАлгуйскогоместорождения[9]иокисьмагния«осажденную»марки«Ч»или«ЧДА».Вкачестве стеклообразующих компонентов применяли бентонит Огланлинского месторождения и карбонат стронция.
Количествокомпонентовустанавливалиизрасчетаполучениявгото- вомматериале88–93 %кристаллическойфазы(Mg2SiO4)и12–7%стек- лофазы(табл. 1).
При условии, что в исследуемых керамических материалах должна присутствовать лишь одна кристаллическая фаза (форстерит), количество которой определяется по полному связыванию введенной окиси магния,былирассчитанысоставыстеклофазыэкспериментальныхматериалови их основныесвойства(табл. 2, 3).
53
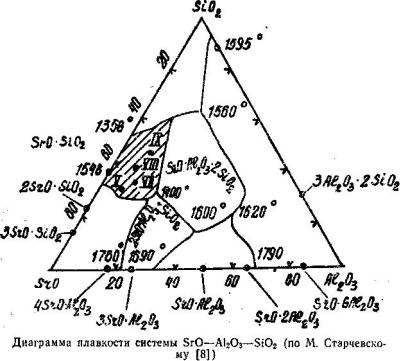
Расчет,выполненныйпометодикеА.А.Аппена[10],показывает, что КТРстекла,равный(100–127)·10-7,1/°С,имеетпрактическиполноесогла- сованиесКТРфорстерита, чтоявляетсянеобходимымусловием получения ненапряженной структуры керамики. С увеличением содержания SrO в алюмосиликатном стекле при соответствующем уменьшении содержанияSiO2происходитвозрастаниеКТР,КМС,значениядругихпараметров остаются практически неизменными.
Изделия и образцы из экспериментальных составов керамики были изготовленыпоспековойтехнологиисвыполнениемследующихосновныхопераций:
—мокрый помол шихты доостатка на сите063 не более0,5 %;
—гранулированиеизмельченнойгомогонезированнойшихтыпосле обезвоживания(влажность15–20 %);
—обжиг гранул по режиму: скорость нагрева 150–200 °С/ч до температурыобжига1300–1320 °С;
—измельчениеспеченныхгранул(спека)сдобавкойповерхностно-
активного вещества — олеиновой кислоты (0,4 вес. %) до суммарной поверхности5000–5500см2/г;
54
—приготовлениелитейногошликера(свведением 12,5%парафина)
иоформление изделий методом горячего литья под давлением;
—предварительный обжиг изделий на воздухе в течение 16–18 ч с максимальнойтемпературой 900–1000°С взасыпкеиз глинозема;
—окончательныйобжигизделийвокислительнойсредепорежиму: скоростьнагрева150–200°С/ч,температураобжига1250–1350°С.
Таблица 1
Состав шихты и расчетное содержание окислов в экспериментальных составах керамики
|
|
|
|
Шифр состава |
|
|
Компонент шихты |
1*ЛФA-1 |
ЛФА-V |
ЛФА-VII |
ЛФА-VIII |
ЛФА-1Х |
|
|
|
|
|
|
|
|
|
|
|
Состав шихты, мас. % |
|
||
|
|
|
|
|
|
|
Тальк алгуйский |
56,0 |
|
57,0 |
58,3 |
56,6 |
55,1 |
(обогащенный) |
|
|
|
|
|
|
Окись магния «осажденная» |
30,6 |
|
31,6 |
32,3 |
30,9 |
30,1 |
марки «ЧДА» или «Ч», МРТУ |
|
|||||
6–09–3391–67 |
|
|
|
|
|
|
Бентонит огланлинский, 1 |
6,2 |
|
4,1 |
4,2 |
5,2 |
7,2 |
сорт, ГОСТ 7032–54 |
|
|
|
|
|
|
ВаСОз, марка «Ч», ГОСТ |
7,2 |
|
– |
– |
– |
– |
4158–65 |
|
|||||
|
|
|
|
|
|
|
SrC03, марка «ЧДА», МРТУ |
– |
|
7,3 |
5,2 |
7,3 |
7,6 |
6-09–4061–67 |
|
|||||
|
|
|
|
|
|
|
Расчетное содержание окислов, мас. % |
|
|||||
|
|
|
|
|
|
|
SiO2 |
42,0 |
|
41,6 |
42,0 |
42,2 |
42,7 |
MgO |
50,7 |
|
52,0 |
53,2 |
51,2 |
50,1 |
|
|
|
|
|
|
|
А12O3 |
1,0 |
|
0,6 |
0,7 |
0,9 |
1,2 |
ВаО |
5,8 |
|
— |
— |
— |
— |
|
|
|
|
|
|
|
SrO |
— |
|
5,4 |
3,8 |
5,3 |
5,6 |
|
|
|
|
|
|
|
Другие окислы |
0,5 |
|
0,4 |
0,3 |
0,4 |
0,4 |
(CaO, Fe2O3, K2O, Na2O, ТiO2) |
|
|||||
|
|
|
|
|
|
* Состав 1 керамики марки ЛФА-1 приведен для сравнения [9].
55
Таблица 2
Соотношение фаз и расчетный состав стеклофазы экспериментальных составов керамики
|
Шифр состава |
|
|
Содержание фаз, % |
|
|
Содержание окислов, мас. % |
|
|||||||
|
|
|
|
|
|
|
|
|
|
|
|
|
другие |
|
|
|
керамики |
|
кристаллофаза |
|
стеклофаза |
|
SiO2 |
Al2O3 |
ВаО |
|
SrO |
|
|||
|
|
|
|
|
окислы |
|
|||||||||
|
|
|
|
|
|
|
|
|
|
|
|
|
|
|
|
|
|
|
|
|
|
|
|
|
|
|
|
|
|||
|
ЛФА-1 |
|
88 |
|
12 |
35,5 |
8,8 |
51,3 |
|
– |
4,4 |
|
|||
|
|
|
|
|
|
|
|
|
|
|
|
|
|
||
|
ЛФА-V |
|
90 |
|
10 |
27,8 |
6,7 |
|
– |
|
60,0 |
5,5 |
|
||
|
|
|
|
|
|
|
|
|
|
|
|
|
|
||
|
ЛФА-VII |
|
93 |
|
7 |
28,4 |
10,4 |
|
– |
|
56,7 |
4,5 |
|
||
|
|
|
|
|
|
|
|
|
|
|
|
|
|
||
|
ЛФА-VIII |
|
90 |
|
10 |
36,6 |
8,6 |
|
– |
|
51,0 |
3,8 |
|
||
|
|
|
|
|
|
|
|
|
|
|
|
|
|
||
|
ЛФА-IХ |
|
88 |
|
12 |
42,0 |
9,7 |
|
– |
|
45,1 |
3,2 |
|
||
|
|
|
|
|
|
|
|
|
|
|
|
|
|
|
|
|
|
|
|
|
|
|
|
|
|
|
|
|
|
Таблица 3 |
|
|
Расчетные свойства стронцийалюмосиликатной стеклофазы |
||||||||||||||
|
|
|
|
исследованных составов |
керамики |
|
|
|
|||||||
|
|
|
|
|
|
|
|
|
|
|
|
|
|
|
|
|
Свойства стеклофазы |
|
|
Состав керамики, мас. % |
|
|
|
||||||||
|
ЛФА-1 |
ЛФА-V |
|
ЛФА-VII |
|
ЛФА-VIII |
ЛФА-IХ |
||||||||
|
|
|
|
|
|
||||||||||
|
|
|
|
|
|
|
|
|
|
|
|
|
|
|
|
|
КТРx107, 1/°С |
|
102,0 |
|
126,0 |
|
121,0 |
|
114,0 |
109,0 |
|
||||
|
(20–400°С) |
|
|
|
|
|
|||||||||
|
|
|
|
|
|
|
|
|
|
|
|
|
|
||
|
Модуль упругости |
|
8,6 |
|
10,1 |
|
10,2 |
|
10,1 |
10,3 |
|
||||
|
E·10-3, кг/мм2 |
|
|
|
|
|
|||||||||
|
Поверхностное |
|
|
|
|
|
|
|
|
|
|
|
|
|
|
|
натяжение при |
|
405,0 |
|
492,0 |
|
495,0 |
|
495,0 |
496,0 |
|
||||
|
1300 °С, дин/см |
|
|
|
|
|
|
|
|
|
|
|
|
|
|
|
Коэффициент |
|
|
|
|
|
|
|
|
|
|
|
|
|
|
|
молекулярного |
|
1,9 |
|
2,1 |
|
1,8 |
|
1,4 |
|
1,1 |
|
|||
|
соотношения |
|
|
|
|
|
|
|
|
|
|
|
|
|
Свойствакерамическихматериаловсостронцийалюмосиликатной стеклофазой
Интенсивное спекание керамических материалов со стронцийалюмосиликатной стеклофазой происходит в интервале температур 1050–1300 °С. Объемная масса, усадка керамики состронцийсодержащей стеклофазой достигают максимальных значений при температуре 1275–1300°С,втовремякаккерамикисбарийсодержащейстеклофазой— при1325–1350°С.
Интервалспекшегосясостоянияизделийизфорстеритовойкерамики со стронцийсодержащей стеклофазой шире, чем укерамики с барийсодержащейстеклофазой, исоставляетот 30до60°С.
Петрографический анализ, выполненный в иммерсии и аншлифах, показал, что структуракерамики составов V иVIII однородна, встреча- ютсязернанеправильнойформы,реже—таблитчатые. Максимальный
56
размер зерен 16 4 мкм. Количество их в керамике не превышает 3 %. Средний размерзерен 6–7 мкм, ихпоказатели преломления: Nд=1,670, Np= 1,635. Стеклофаза равномернораспределена ибольшей частью обволакивает тонкой пленкой зерна форстерита. Содержание стекла со- ставляет15–20%,егопоказательпреломленияNcp =l,540 ± 0,01.
ДлясоставовVII, IXхарактернаболеекрупнаякристаллизацияфор- стерита(размерзерен7–10мкм)инеоднородностьструктуры,чтобыло обусловлено слишком высокой температурой обжига массы на спек (1320 °С). Следуетотметить, чтобольшинствосоставовимеловысокую плотность, содержание пор не более 3–5%.
Анализ рентгенограмм показывает, что структура исследованных составов керамики представлена в основном форстеритом. Однако в ряде случаев обнаружена дополнительная линия с межплоскостным расстоянием d = 3,27. Очевидно, она относится к силикатам стронция.
Сравнивалисвойстваисследуемыхсоставовкерамикиифорстерито- войкерамикисоставаЛФА-1сбарийсодержащейстеклофазой[9](табл. 4).
Плотностькерамикиисследованныхсоставовдостаточновысока(3,05– 3,07 г/см3). Исключением был состав VII, у которого недостаточное количестворасплавазатруднилоспекание. Прочностьпри статическом изгибе плотноспеченных образцов высокая, при этом для составов V и VIIIеезначениевыше,чемукерамикисбарийсодержащейстеклофазой.
КТР керамики и титана хорошо согласуются. Значения КТР исследованных составов различаются несущественно. Форстеритовая керамика со стронцийалюмосиликатной стеклофазой обладает высокими диэлектрическимисвойствами.Изменениетангенсаугладиэлектрическихпотерьидиэлектрическойпроницаемостисповышением температуры аналогично изменению этих свойств керамики с барийалюмосиликатнойстеклофазой.
Важным достоинством форстеритовой керамики со стронцийсодержащей стеклофазой является хорошеекачествоспаев ститаном.
Прочность при статическом изгибе образцов-трубочек из керамики составов V, VIII, спаянных через титановую шайбу с помощью медно- никелевогоприпоя,составляла1000–1300кг/см2,чтона20–30%превы- шаетпрочностьобразцовспаевститаномкерамикисбарийсодержащей стеклофазой.
Изоляторы из керамики со стронцийсодержащей стеклофазой [11] были опробованы в производстве титанокерамических ламп, при этом отмеченоснижениебракапонатеканиюпосравнениюслампами, имеющими изоляторы из керамики с барийсодержащей стеклофазой.
Опытныетитанокерамическиелампысохранилигерметичностьоболочки послевоздействия 2000 термоциклов сизменением температуры
57

от20до600°Ссохлаждениемнавоздухе;выдержалииспытаниявкамере влаги(температура40±2°С,влажность96–98 %)втечение5000ч.
Таблица 4
Свойства форстеритовой керамики со стронцийалюмосиликатной стеклофазой
Свойства |
|
Шифр состава керамики |
|
|||
ЛфА-I |
ЛфА-V |
ЛфА-VII |
ЛфА-VIII |
ЛфА-IХ |
||
|
||||||
|
|
|
|
|
|
|
Температура спекания, °С |
1340 |
1310 |
1350 |
1300 |
1280 |
|
|
|
|
|
|
|
|
Интервал спекшегося |
30–40 |
30–50 |
– |
40–60 |
40–50 |
|
состояния, °С |
||||||
|
|
|
|
|
||
Объемная масса, г/см3 |
3,08 |
3,07 |
3,0 |
3,07 |
3,05 |
|
Водопоглощение, % |
0 |
0 |
0,02 |
0 |
0 |
|
Прочность керамики при |
1650 |
1740 |
1300 |
1800 |
1680 |
|
статическом изгибе, кг/см2 |
||||||
|
|
|
|
|
|
|
Прочность при изгибе |
750–900 |
1000–1300 |
800–950 |
1000–1200 |
800–950 |
|
спая керамики с титаном, |
||||||
кг/см2 |
|
|
|
|
|
|
КТР·106 (1/°С) в |
|
|
|
|
|
|
интервале температур, °С: |
8,3 |
8,3 |
8,0 |
8,0 |
8,1 |
|
20–200 |
|
|
|
|
|
|
|
|
|
|
|
|
|
20–500 |
9,5 |
9,4 |
9,2 |
9,0 |
9,2 |
|
20–900 |
10,5 |
10,6 |
10,2 |
10,6 |
10,4 |
|
tg 104 на частоте 1 Мгц, |
2 |
2 |
2 |
2 |
3 |
|
при температуре, °С: 20 |
||||||
|
|
|
|
|
|
|
300 |
10 |
12 |
– |
10 |
– |
|
500 |
100 |
80 |
– |
110 |
70 |
|
на частоте 1 МГц при |
6,7 |
6,7 |
6,4 |
7,0 |
6,4 |
|
температуре, °С: 20 |
||||||
|
|
|
|
|
||
300 |
6,8 |
6,9 |
6,7 |
7,1 |
6,8 |
|
|
|
|
|
|
|
|
500 |
7,2 |
7,2 |
– |
7,2 |
7,0 |
|
|
|
|
|
|
|
|
v (Ом·см) при |
4·1013 |
5 ·1013 |
– |
5 ·1013 |
5 ·1013 |
|
температуре, °С: 300 |
||||||
500 |
4 ·1012 |
2 · 1012 |
– |
3 · 1012 |
5 ·1012 |
Выводы
Вакуумно-плотная форстеритовая керамика со стронцийалюмосиликатной стеклофазой обладает рядом преимуществ по сравнению с керамикой, имеющей барийалюмосиликатную стеклофазу:
—температура ее спекания ниже на 30–50 °С;
—шире интервал спекшегося состояния изделий;
—выше прочность спаев с титаном.
58

Форстеритовая керамика со стронцийалюмосиликатной стеклофазой обеспечивает высокую надежность в спаях с титаном и может быть рекомендована для использования в вакуумноплотных оболочках приборов(составыV, VIII).
Литература
1.Бердов Г.И., Грисюк М.Г., Коган X.Б., Мадриченко Г.Ф. Электроника, 1959.
№4. С. 27.
2.Казанцева И.Е., Кириллова Г.К., Полякова Н.Л. «Электроника», 1959. № 4. С. 21.
3.Корпачев М.Г., Таборский В.И., Богинская Н.П. «Электронная техника». Сер. «ПУЛ», 1966. Вып. 3, 4. С. 102.
4.Navias L. «J. Amer. Ceram. Soc», 1954, v. 37, N 8, p. 330.
5.Sigiura Masatosi and oth. «Repts. Govt. Industr. Res. Inst. Nagoya», 1959. 8.
№12. p. 863.
6.Atsusi Takasi, Saito Hirouki «Fuji. Electr. J.», 1966, 39, № 3. P. 217.
7.Штейберг Ю.Т. Стронциевые глазури. М.: Л.: Госстройиздат, 1967.
8.Топоров Н.А., Барзаковский В.П. и др. Диаграммы состояния силикатных систем: Справочник. Вып. 3. «Тройные системы». Л.: Наука, 1972. С. 191.
9.Бердов Г.И., Плетнев П.М., Верещагин В.И., Усов П.Г. «Электронная техника», сер. «Материалы», 1971. Вып. 4. С. 76.
10.Аппен А.А. Химия стекла. Л.: «Химия», 1970.
11.Усов П.Г, Бердов Г.И., Плетнев П.М., Верещагин В.И., Шильцина А.Д. Вакуумно-плотный форстеритовый материал. Авт. свид. СССР № 323392, заявл. 10/ 1II–70, опубл. 11/XII–71. Бюллетень «Открытия, изобретения, промышленные образцы, товарные знаки». 1972. № 1.
1.7.ТАЛЬК-АЛГУЙСКОЕ МЕСТОРОЖДЕНИЕ —
ВЫСОКОКАЧЕСТВЕННОЕСЫРЬЕ ДЛЯ ПРОИЗВОДСТВА
КЕРАМИЧЕСКИХ МАТЕРИАЛОВ*
Рассмотрены особенности высококачественного талька Алгуйского месторождения, отличающегося от Онотского повышенной чистотой. Исследован ряд составов вакуумноплотной стеатитовой и форстеритовой керамики на основе алгуйского талька. Показано, что при использовании этого талька могут быть получены высокие свойства керамических материалов.
Основным сырьем для производства стеатитовых и форстеритовых керамических материалов служит природный минерал – тальк. Среди вновьоткрытыхместорожденийвысокосортныхтальковыхпородбольшой интереспредставляетАлгуйское(Кемеровская обл.) [1].
Алгуйскийталькотличаетсямалымсодержаниемщелочей(до0,15 %) и окислов железа (до 0,08 %). В природном состоянии он представляет собой тонкодисперсное вещество серовато-белого цвета, содержащее
* Усов П.Г., Плетнев П.М., Верещагин В.И., Бердов Г.И., Собора Н.В. «Электронная техника». Сер. 5. Вып. 1(18). 1971. С. 80–84.
59

менее 10 % частиц размером 0,5 мм и более. Порода представлена в основном тальковым минералом крупночешуйчатого строения с примесями зерен кварца. Содержание кремнезема в тальковой породе колеблетсявпределах63,5 73,5%(табл.1).
Таблица 1
Химический состав исходных материалов, мас. %
Компонент |
SiO2 |
MgO |
Fe2O3 |
Al2O3 |
CaO |
B2O3 |
TiO2 |
K2O |
Na2O |
п. п. п |
|
|
|
|
|
|
|
|
|
|
|
|
|
Тальк алгуйский: |
63,5– |
22,2– |
|
0,1– |
0,1– |
|
|
|
|
4,0– |
|
природного состоя- |
0–0,08 |
— |
— |
— |
— |
||||||
73,5 |
31,6 |
0,9 |
0,36 |
4,56 |
|||||||
ния; |
|
|
|
|
|
|
|
|
|
|
|
обогащенный флота- |
|
|
|
|
|
|
|
|
|
|
|
цией (усредненная |
64,16 |
30,25 |
0,04 |
0,31 |
0,22 |
— |
— |
— |
— |
4,68 |
|
проба) |
|
|
|
|
|
|
|
|
|
|
|
Тальк онотский, |
62,02 |
31,64 |
0,45 |
0,45 |
0,42 |
— |
— |
— |
— |
4,78 |
|
сорт «Экстра» |
|||||||||||
|
|
|
|
|
|
|
|
|
|
||
Бентонит огланлин- |
|
|
|
|
|
|
|
|
|
|
|
ский, |
70,1 |
2,0 |
0,92 |
12,3 |
4,0 |
— |
0,24 |
0,48 |
2,6 |
7,3 |
|
1-й сорт |
|
|
|
|
|
|
|
|
|
|
|
Каолин еленинский, |
46,68 |
Следы |
0,88 |
37,72 |
0,28 |
— |
0,72 |
0,02 |
0,1 |
13,6 |
|
1-й сорт |
|
|
|
|
|
|
|
|
|
|
|
Борацитное стекло |
5,87 |
12,82 |
0,27 |
4,36 |
11,24 |
65,36 |
0,14 |
— |
— |
— |
|
|
|
|
|
|
|
|
|
|
|
|
Исследования показали, чтобольшинство пород талька Алгуйского месторождениятребуютобогащениясцельюудалениясвободногокремнезема. При этом наилучшие результаты достигаются при обогащении флотациейвследствиегидрофобностисамоготалька[2].Длянекоторых пробталькааналогичныйэффектпообогащениюдостигаетсяпросеиваниемчерез сито№045 или025.
Микроскопический анализ показывает, что алгуйский тальк представлен пластинчатымикристаллами размерами 3 100 мк. Показатели преломления Ng=1,580±0,002 и Np=1,538±0,002 соответствуют чистой разновидноститальковогоминерала. Показателипреломленияпримесныхзеренкварца:Ng = 1,533;Np =1,544.
Рентгеноструктурный анализ подтверждает результаты микроскопических исследований и выявляет предпочтительную ориентировку частицсплоскостью(001)погранибазопинакоида.Линии,соответству-
|
|
|
|
|
ющиеd=8,9A(002);4,65 A(004);3,09 A(006);2,33 A (008);1,86 A (010);
1,55 A (012) и 1,33 A (014), имеют более четкие максимумы и более значительную интенсивность, чем уонотского талька.
Максимум эндотермического эффекта процесса дегидратации алгуйского талька сдвинут на 20–30 °С в область высоких температур по сравнению с максимумом ДТА онотского талька.
60