
книги / Переработка полимеров
..pdf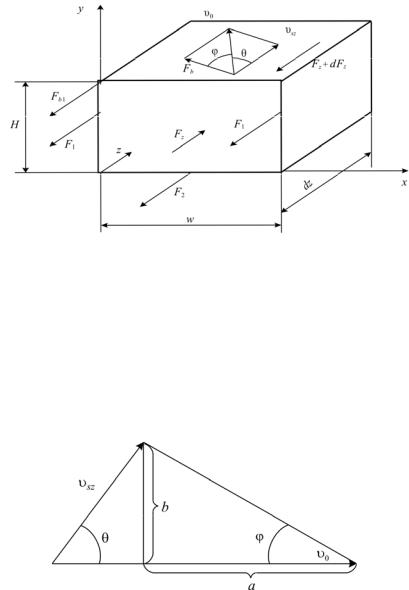
Рис. 9.2. Силы, действующие на пробку гранул: sz – скорость пробки; 0 –
обращенная скорость; – угол навивки; – угол транспортировки, определяет направление силы трения на движущейся поверхности; Fb – сила трения на цилиндрической поверхности корпуса; F1 – сила трения на боковых гранях; F2 – сила трения на дне канала; Fz – осевая сила, продвигающая полимер вперед по оси z; Fz+dz – сила, уравновешивающая отброшенную часть полимера (пробки гранул); Fb1 – локальная сила трения, действующая вдоль верхнего
ребра канала и обусловленная нормальной силой Fb sin
Рассмотрим баланс сил, действующих на элемент пробки гранул длиной dz (см. рис. 9.2). Но прежде определим угол из треугольника сил (рис. 9.3).
Рис. 9.3. Векторный треугольник a sz sin ; b 0 sz cos .
101
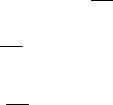
Тогда тангенс угла транспортировки
tg a |
|
sz sin |
. |
|
0 sz cos |
||||
b |
|
|
Таким образом, если заданы геометрия канала ( ), частота вращения шнека ( 0) и расход материала Q, который связан со скоростью пробки гранул через соотношение sz = Q/(Hw), то
угол транспортировки определен однозначно.
Спроектируем все действующие силы на пробку гранул на ось z.
Fz Fz dFz 2F1 F2 Fb cos Fb1 0 , (9.1)
где f1 – коэффициент трения на шнеке; f2 – коэффициент трения на верхней грани канала (на внутренней поверхности цилиндрического корпуса).
Рассмотрим силу трения на боковой поверхности канала. По закону Леонарда да Винчи
F1 f1 FN1 ,
где FN1 – нормальная сила.
FN1 HwFz k dz H ,
где величина HwFz представляет собой осевое давление.
При составлении баланса сил необходимо учесть тот факт, что давление HwFz , действующее вдоль оси канала, не полно-
стью передаётся на стенки канала, так как в разных направлениях свойства материала могут быть различны (в отличие от жидкой среды, где действует закон Паскаля). Отношение сил F1 Fz k; F1 k Fz . Иначе говоря, отношение радиального на-
пряжения к осевому равно постоянной величине k.
102
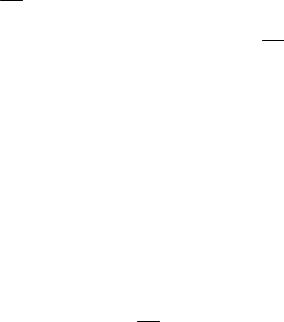
k учитывает неизотропность распределения давления в пробке гранул. По опытамнемецкогоученого Шнейдераk = 0,3 0,4.
Итак, HwFz k – давление, которое действует на боковую по-
верхность; dz H – площадь боковой поверхности; HwFz k Hdz –
нормальная сила, действующая на боковую поверхность канала, приложенная в центре боковой поверхности ( FN1 ).
F f |
Fz |
k Hdz . |
(9.2) |
|
|||
1 1 Hw |
|
|
Аналогичным образом могут быть получены остальные силы трения, действующие на выделенный элементарный участок твердого полимера в канале зоны загрузки.
F f |
Fz |
|
k wdz |
(9.3) |
|
|
|||||
2 |
1 Hw |
|
|
||
F f |
|
Fz |
k wdz |
(9.4) |
|
|
Hw |
||||
b |
2 |
|
|
Fb1 Fb sin f1 f2 HwFz k wdz sin f1 .
Подставим выражения (9.2)–(9.5) в (9.1).
Fz Fz dFz |
|
Fz |
k Hdz wdz wdzf2 sin( ) f1 |
||
|
Hw |
||||
|
|
|
|||
|
|
Fz |
|
kwdz f2 cos . |
|
Hw |
|||||
|
|
(9.5)
(9.6)
Преобразуем уравнение (9.6) и разделим все члены уравнения на Fz.
dF |
|
kH |
|
|
|
|
|
kw |
|
|
kw |
|
|
|
sin |
z dz 2 |
|
|
f1 |
|
|
|
f1 |
|
|
f2 |
f1 |
||||
Hw |
|
Hw |
Hw |
||||||||||||
Fz |
|
|
|
|
|
|
|
|
|
|
(9.7) |
||||
|
|
|
|
|
kw |
|
|
|
|
|
|
|
|||
|
|
|
|
|
|
|
|
|
|
|
|
||||
|
|
|
|
|
|
|
f2 cos |
, |
|
||||||
|
|
|
Hw |
|
|||||||||||
|
|
|
|
|
|
|
|
|
|
|
|
|
|||
|
|
|
|
|
|
|
|
|
|
|
|
|
|
|
103 |
dFz dPz .
Fz Pz
Проинтегрируем последнее выражение, обозначив величину, стоящую в квадратных скобках через А, и учитывая тот факт, что при z = 0 (в начале зоны загрузки) давление было равным атмосферному. Получим
Pz P0ezA ,
где P0 – атмосферное давление, МПа. Таким образом, изменение давления в зоне загрузки происходит по экспоненциальному закону. Очевидно, что соотношение осевых сил или давлений связано с величиной расхода через угол транспортировки (или скорости пробки). Это означает, что для заданного давления на входе фиксированное давление на выходе определяет расход, и, наоборот, заданный расход определяет величину давления на выходе, которое может создать данное устройство.
Поскольку задача теоретического описания и исследования процессов, протекающих в экструдере, заключается в определении полей скоростей, температур, напряжений, давлений и, как следствие, качества и толщины изоляции, режимы переработки, скорости движения проволоки, режимов охлаждения и так далее, то, в частности, в зоне загрузки задача исследования не ограничивается определением изменения давления по оси канала.
В результате трения полимера о движущийся корпус диссипируется энергия, кроме того, тепло подводится через корпус экструдера с помощью нагревательных элементов. Необходимо найти распределение температуры в поперечном сечении канала и по длине, что позволит определить длину зоны загрузки (ЗЗ).
Для определения длины ЗЗ и распределения температурного поля в пробке рассмотрим задачу о теплопереносе со следующими допущениями:
– канал ограничен двумя бесконечными параллельными пластинами (рассматриваем изменение температуры по высоте канала в серединном его сечении);
104
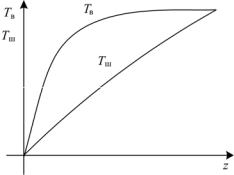
–процесс стационарный;
–диффузия тепла в направлении оси канала пренебрежимо
мала;
–внутренние источники тепла отсутствуют;
–теплофизические характеристики – константы.
Уравнение энергии в этой постановке примет вид
c |
|
T |
|
2T |
, |
(9.8) |
s s |
|
sz dz |
|
s y2 |
|
|
где sz – скорость пробки, сs – теплоемкость, ρs – плотность, λs –
теплопроводность твердого полимера. Граничные условия:
T |
|
z 0 T0 ; |
T |
|
y 0 Tш z ; |
T |
|
y H Tb z . |
(9.9) |
|
|
|
|||||||
|
|
|
|
Одинизвариантовграничныхусловийпредставленнарис. 9.4.
Рис. 9.4. Изменение температуры на шнеке и цилиндре
Если не известна функция распределения температуры по шнеку Tш(z), то рассматривают поверхность шнека как адиабатическую, то есть записывают следующее граничное условие:
T |
0 . |
(9.10) |
|
y |
|||
y 0 |
|
||
|
105 |
||
|
|
Длина зоны загрузки определяется сечением, на котором у цилиндрической поверхности корпуса температура материала достигает температуры плавления. Здесь закон сухого трения сменяется вязкостным. Появляется тонкая пленка расплава, возникает дополнительный источник тепла – диссипативный. Эта точка по длине канала соответствует началу новой функциональной зоны – зоны задержки плавления иконца зоны загрузки.
Зона загрузки рассчитывается с целью определения таких величин технологических параметров, которые бы позволили интенсифицировать процесс наложения пластмассовой изоляции с получением качественного изоляционного покрытия. Кроме того, необходимо стремиться к уменьшению длины зоны загрузки и шнека в целом. Обычно длина зоны загрузки составляет 5–6 витков шнека.
Существенное влияние на процесс теплообмена оказывают:
–величина расхода материала;
–частота вращения шнека;
–температура корпуса.
С одной стороны, хотелось бы стремиться к увеличению расхода материала, пропорционально чему возрастала бы производительность процесса. Однако увеличение расхода, с другой стороны, на столько же увеличивает скорость пробки в зоне загрузки. Последнее ведет к тому, что материал в ЗЗ не успевает прогреться и попадает в зону сжатия с уменьшающейся высотой канала, где возможна закупорка канала.
Казалось бы, достаточно увеличить мощность источников тепла, т.е. температуру корпуса, и процесс прогрева полимера будет ускорен. Но в этом случае, поскольку коэффициент теплопроводности полимеров очень мал (в 1000 раз меньше, чем у металлов), малое количество тепла может быть отведено от нагретой поверхности в глубь пробки. В этом случае возможны перегревы близлежащих слоев полимера при непрогреве в целом пробки гранул.
106
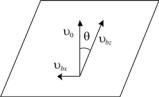
9.2. Зона задержки плавления
Зона задержки плавления характеризуется присутствием полимера в двух агрегатных состояниях: жидком и твердом. Зона задержки плавления (ЗЗП) заканчивается там, где толщина пленки расплава превысит величину зазора между гребнем шнека и корпусом в 3 4 раза, длина ее составляет 1,5-2 витка шнека. Далее начинается зона плавления. В отличие от зоны плавления процесс плавления в зоне задержки плавления происходит значительно менее интенсивно, поскольку мала доля жидкой фазы в этой зоне и, следовательно, не столь мощным является внутренний диссипативный источник тепла (с этим фактом – слабой интенсивностью процесса плавления – связано и название рассматриваемой зоны экструдера).
Течение и теплообмен ЗЗП моделируется тепломассопереносом между двумя бесконечными пластинами, одна из которых – развернутая на плоскость цилиндрическая поверхность корпуса, вторая – твердая поверхность полимерной пробки. Окружная скорость верхней подвижной пластины раскладывается на две составляющих по направлениюосей координат (рис. 9.5).
Рис. 9.5. Граничные условия по скорости на верхней пластине
Ненулевыми скоростями в данной постановке являются скорости z и x, изменяющиеся только по высоте канала, для которых запишутся следующие уравнения движения:
|
2 z |
ð , |
|||
|
y |
2 |
|
z |
|
|
|
|
|
||
|
2 x |
|
ð |
|
|
|
|
. |
|||
|
|
2 |
|
||
|
y |
|
x |
|
|
|
|
|
|
(9.11)
107
Расход в жидкой фазе в направлении оси x Qx равен нулю, так как в поперечном сечении канала реализуется только циркуляционное течение расплава, в продольном направлении расход Qz с учетом движения обеих фаз должен быть равным заданному расходу Qз.
Qx w H |
x dy 0 . |
(9.12) |
H h |
|
|
Qz wН z dy Qз . |
(9.13) |
|
0 |
|
|
Уравнения энергии для расплава и твердого материала будут иметь следующий вид:
c |
m |
|
m |
T |
|
m |
2T |
|
|
z |
|
x 2 |
(9.14) |
||||
z |
|
z |
|
y |
2 |
|
|
|
y |
|
|
y |
|
|
|||
|
|
|
|
|
|
|
|
|
|
|
|
|
|
||||
|
|
|
|
|
c |
|
T |
|
|
2T |
, |
|
|
|
(9.15) |
||
|
|
|
|
|
sz s |
s |
z |
|
|
s |
y2 |
|
|
|
|
|
где h – толщина пленки расплава.
Граничные условия для скоростей и температуры записываются исходя из условий прилипания к твердым стенкам для жидкой фазы.
T |
|
y 0 Tш; |
T |
|
y H h Tm ; |
T |
|
y H Tb ; |
T |
|
z 0 TЗЗ . (9.16) |
||||||||
|
|
|
|
||||||||||||||||
|
|
|
|
||||||||||||||||
|
|
z |
|
y h |
0 cos bz ; |
|
z |
|
y H h sz ; |
(9.17) |
|||||||||
|
|
|
|
|
|||||||||||||||
|
|
|
|
|
|||||||||||||||
|
|
x |
|
|
y H 0sin bx ; |
|
x |
|
|
0. |
|||||||||
|
|
|
|
|
|
y H h |
|
|
|||||||||||
|
|
|
|
|
|
|
|
Здесь Tm –температуры плавления материала, ТЗЗ – температура полимера в начале зоны задержки плавления (расчетная температура в конце зоны загрузки).
Сложность решения такой задачи заключается в том, что толщина жидкой фазы по мере продвижения материала вдоль по каналу увеличивается за счет плавления твердого материала, что не-
108
обходимо учитывать в итерационной процедуре расчета. Кроме того, необходимо учитывать зависимость вязкости и теплофизических характеристикоттемпературыианомалию вязкости.
Расчет в ЗЗП происходит до той длины, где толщина пленки расплава станет больше в 3–4 раза величины зазора над гребнем шнека. Результаты расчета представляются в виде зависимостей температуры, скоростей, давлений по глубине и высоте канала. Определяется длина ЗЗП. Анализируется влияние технологических, физических и геометрических факторов на процессы теп- ло-массообмена. Полученные поля скоростей, температур и давлений в конце зоны задержки плавления являются исходными для расчета следующей зоны – зоны плавления (ЗП).
9.3. Зона плавления
Зона плавления или зона фазового превращения определяется как та часть экструдера, в которой твёрдый полимер находится вместе с расплавом. Эта зона обычно не совпадает с сужающимся переходом шнека, хотя шнек необходимо проектировать так, чтобы плавление заканчивалось бы именно в конце зоны сжатия. Важной характеристикой экструдера является длина зоны плавления, которая составляет большую часть шнека. Длина зоны плавления является функцией не только геометрии шнека, но также условий переработки и физических свойств полимера. Несмотря на тот факт, что зона плавления обычно занимает большую часть экструдера и имеет главенствующее влияние на производительность экструдера и на качество экструдата, на сегодняшний день не существует полной модели, адекватно описывающей процессы в рассматриваемой зоне.
Механизм плавления в шнековом экструдере был впервые экспериментально исследован Маддоком и Стритом. Методика эксперимента заключается в следующем. Экструдер, работающий в установившемся режиме, резко останавливали, охлаждали цилиндр до температуры, при которой расплав затвердевал в канале червяка, а затем кратковременно нагревали цилиндр,
109
выталкивая червяк из цилиндра. Полученную полимерную ленту разрезали перпендикулярно гребню червяка. Для лучшей визуализации в полимер добавляли окрашенный полимер. Это давало возможность определить области непроплавленного и проплавленного полимера, а также линии циркуляции расплава.
В результате экспериментов установлено, что на большей части червяка экструдера существует твёрдая и жидкая фазы, кроме того, у толкающего гребня образуется область расплава (бассейн расплава). Бассейн расплава начинает образовываться с того момента, когда толщина плёнки расплава превысит величину зазора между гребнем и корпусом экструдера. Твёрдая пробка, имеющая форму непрерывной винтовой ленты изменяющейся ширины и высоты, медленно двигается по каналу, постепенно расплавляясь. Описанное поведение материала при плавлении является общим механизмом для аморфных полимеров и кристаллических и для разных типов пластифицирующих экструдеров.
Исходя из экспериментальных наблюдений механизм плавления в первых экструдерах был впервые математически описан Зиновием Тадмором.
Суть модели Тадмора заключается в следующем. Для ряда экструдеров было установлено, что форма твердой пробки на всем протяжении сохраняет прямоугольную форму (рис. 9.6), что позволило З. Тадмору сделать ряд упрощающих предположений:
–процесс стационарный, установившийся;
–свойства материала постоянные (жидкость ньютоновская);
–процесс плавления происходит только у цилиндрической поверхности корпуса;
–температура пробки гранул неизменяется по длине канала;
–течение расплава пленки – течение Куэтта.
–глубина канала мала (следовательно, можно развернуть винтовой канал на плоскость и обратить движение);
–пробка гранул однородна и непрерывна.
110