
книги / Получение наночастиц и наноматериалов
..pdfСуществует два необходимых и достаточных условия получения нанопорошков конденсационными методами – большое пересыщение и присутствие в конденсируемом паре молекул нейтрального газа. Изменяя пересыщение системы (увеличивая или снижая давление пара), можно регулировать значение радиуса критического зародыша и добиваться нужного размера частиц получаемых порошков.
Установки, использующие принцип испарения-конденсации, различаются способом ввода испаряемого материала; способом подвода энергии для испарения; рабочей средой; организацией процесса конденсации; системой сбора полученного порошка.
Испарение металла может происходить из тигля, или же металл поступает в зону нагрева и испарения в виде проволоки, всыпаемого металлического порошка или в струе жидкости. Может использоваться также распыление металла пучком ионов аргона. Подвод энергии может осуществляться непосредственным нагревом, пропусканием электрического тока через проволоку, электродуговым разрядом в плазме, индукционным нагревом токами высокой и средней частоты, лазерным излучением, электронно-лучевым нагревом. Испарение и конденсация могут происходить в вакууме, в неподвижном инертном газе, в потоке газа, в том числе в струе плазмы.
Конденсация парогазовой смеси с температурой до 5000– 10000 K может происходить при ее поступлении в камеру (с большими сечением и объемом), заполненную холодным инертным газом; в этом случае охлаждение происходит за счет расширения газовой смеси и благодаря контакту с холодной инертной атмосферой. Существуют установки, в которых в камеру конденсации коаксиально поступают две струи − парогазовая смесь подается вдоль оси, а по ее периферии поступает кольцевая струя холодного инертного газа. В результате турбулентного смешения температура паров металла понижается, увеличивается пересыщение и происходит быстрая конденсация. Благоприятные условия конденсации металлических паров создаются при адиабатическом расширении
11
в сóпле Лаваля, когда в результате быстрого расширения создается высокий градиент температуры и конденсация пара происходит почти мгновенно.
Самостоятельной задачей является собирание полученного конденсацией нанопорошка, так как его частицы настолько малы, что находятся в постоянном броуновском движении и остаются взвешенными в движущемся газе, не осаждаясь под действием силы тяжести. Для сбора получаемых порошков используют специальные фильтры и центробежное осаждение; в некоторых случаях применяется улавливание жидкой пленкой.
Основными закономерностями образования наноразмерных частиц методом испарения и конденсации являются следующие:
1.Образование наночастиц происходит при охлаждении пара в зоне конденсации, которая тем больше, чем меньше давление газа. Внутренняя граница зоны конденсации находится вблизи испарителя, а ее внешняя граница по мере уменьшения давления газа может выйти за пределы реакционного сосуда.
Впроцессе конденсации существенную роль играют конвективные потоки газа.
2.При увеличении давления газа до нескольких сотен Па средний размер частиц сначала быстро увеличивается, а затем медленно приближается к предельному значению в области давлений более 2500 Па.
3.При одинаковом давлении газа переход от гелия к ксенону, т.е. от менее плотного инертного газа к более плотному, сопровождается ростом размера частиц в несколько раз.
В зависимости от условий испарения металла (давление газа, расположение и температура подложки) его конденсация может происходить как в объеме, так и на поверхности реакционной камеры. Для объемных конденсатов более характерны частицы сферической формы, тогда как частицы поверхностного конденсата имеют огранку. При одинаковых условиях испарения и конденсации металлы с более высокой температурой плавления образуют частицы меньшего размера. Газофазный
12
синтез позволяет получать частицы размером от 2 до нескольких сотен нанометров. Получаемые испарением и конденсацией наночастицы размером ≤ 20 нм имеют сферическую форму, а более крупные частицы могут быть огранены. Более мелкие частицы контролируемого размера получают с помощью разделения кластеров по массе во время пролета в масс-спектрометре.
Разновидностью метода испарения-конденсации является
левитационно-струйный метод. При данном методе испарение металла происходит с поверхности жидкой металлической капли в ламинарном потоке инертного газа. Капля бесконтактно удерживается в зоне нагрева неоднородным высокочастотным электромагнитным полем. Аэрозоль испаренного металла поступает в охлаждающее устройство, затем в фильтр, улавливающий частицы, которые собираются в контейнер. Схема установки для получения нанопорошков испарением в потоке инертного газа показана на рис. 1.3. Увеличение скорости газового потока уменьшает средний размер частиц и сужает распределение частиц по размеру. Данным методом были получены нанопорошки различных металлов и сплавов, размер частиц которых составляет от 5–10 до 100–200 нм.
В последние годы газофазный синтез наночастиц получил заметное развитие благодаря использованию разнообразных методов нагрева испаряемого вещества. Для получения нанокристаллических порошков применяются плазменный, лазерный и дуговой способы нагрева. Так, были получены наночастицы карбидов, оксидов и нитридов с помощью импульсного лазерного нагрева металлов в разреженной атмосфере метана (в случае карбидов), кислорода (в случае оксидов), азота или аммиака (в случае нитридов). Импульсное лазерное испарение металлов в атмосфере инертного газа (Не или Аr) и газа-реагента (O2, N2, NН3, СН4) позволяет получать смеси нанокристаллических оксидов различных металлов, окcидно-нитридные или карбиднонитридные смеси. Состав и размер наночастиц можно контролировать изменением давления и состава атмосферы (инертный газ и газ-реагент), мощностью лазерного импульса, температур-
13
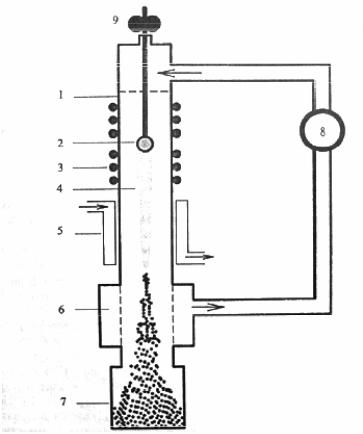
ного градиента между испаряемой мишенью и поверхностью, на которую происходит конденсация. Производительность установок зависит от скорости испарения.
Рис. 1.3. Схема получения высокодисперсных металлических порошков в левитационно-струйном генераторе: 1 – испаритель, 2 – капля, 3 – индуктор, 4 – аэрозоль, 5 – холодильник, 6 – фильтр, 7 – контейнер, 8 – насос, 9 – механизм подачи проволоки
В Научном центре порошкового материаловедения разработан метод получения наноразмерных порошков оксидной керамики лазерным испарением мишени. Процесс лазерного физического
14
газофазного осаждения состоит из двух этапов. Первый этап – это испарение мишеней под воздействием лазерного излучения и создание источника синтезируемого материала. Второй этап – синтез наночастиц порошка (размер частиц меньше 50 нм) из паровой фазы. Размер образующихся частиц зависит от общего давления в камере синтеза. Изменяя давление в широком диапазоне значений, можно влиять на размер частиц синтезируемого порошка и тем самым добиваться заданной дисперсности.
К достоинствам метода можно отнести высокую химическую чистоту конечного продукта; ультрадисперсный состав полученного порошка оксида и заданный размер частиц; сферическую форму частиц; узкое распределение частиц по размерам. Недостатки метода: низкая производительность (~ 1 г/ час); высокая энергоемкость (к.п.д. мощных технологических лазеров меньше 10 %).
При испарении мишени композиционного состава ZrO2– 5Y2O3–20Al2O3 (мас. %) образуются порошки с частицами слоистой структуры: ядро из стабилизированного диоксида циркония, а оболочка из аморфного оксида алюминия, средний размер которых составляет от 7 до 30 нм в зависимости от условий испарения. Установлено, что давление газа в реакторе при синтезе нанопорошка является одним из главных параметров, влияющих на фазовый и гранулометрический состав порошка. При понижении давления в реакторе увеличивается дисперсность порошка и изменяется соотношение тетрагональной и кубической фаз диоксида циркония (рис. 1.4).
На аэрокосмическом факультете Пермского государственного технического университета разработан метод получения ультрадисперсного оксида алюминия сжиганием аэровзвесей алюминиевых порошков. Многие металлы (алюминий, магний, цирконий, титан и др.) при горении в активных газах (кислороде, азоте, диоксиде углерода или их смесях) образуют конденсированные продукты сгорания (оксиды, нитриды, карбиды), обладающие высокой твердостью и тугоплавкостью. Если горение этих металлов происходит в виде газовзвеси металлических час-
15
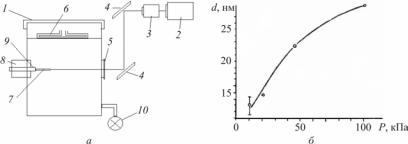
тиц, то продукты их сгорания получаются в газодисперсной форме. Изменяя условия горения (давление, температуру, состав газовой фазы, концентрацию дисперсной фазы, дисперсный и химический состав исходных порошков металлов), можно влиять на форму и структуру частиц продуктов сгорания, их размер, химический и фазовый состав. Обеспечив высокую химическую чистоту исходного порошкообразного металла и газообразного металла и газообразного окислителя, можно обеспечить высокую химическую чистоту конечного продукта. Таким образом, сжигая распыленные в активном газе порошкообразные металлы, в технологической установке можно синтезировать новые порошковые материалы с заданными свойствами. Процессы горения металлов являются сильно экзотермическими, протекают при высокой температуре и с большими скоростями. При этом для осуществления процессов не требуется дополнительная энергия.
Рис. 1.4. Схема установки по синтезу (а) и зависимость среднего размера частиц порошка от давления газа в реакторе (б): 1 – реактор; 2 – лазер; 3 – измеритель мощности; 4 – поворотные зеркала; 5 – входное окно реактора с пластинкой из KCl; 6 – медный диск для сбора порошка; 7 – мишень; 8 – держатель мишени; 9 – обойма; 10 – вакуумный насос
На рис. 1.5 приведена схема экспериментальной технологической установки, включающей систему подачи порошков металлов – 1, камеру воспламенения (форкамеру) – 2, камеру сгорания (синтеза) с соплом – 3, устройство отбора дисперсных оксидов из двухфазного высокотемпературного потока – 4.
16
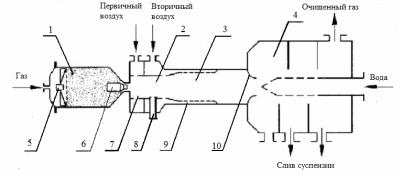
PNRPU
Рис. 1.5. Схема экспериментальной установки для получения дисперсного оксида алюминия
Конечным продуктом является γ – Al2O3 с размером частиц 0,03–0,3 мкм и удельной поверхностью 12,6 м2/г. Форма частиц сферическая. Химический состав порошка составляет оксид алюминия (Al2O3) – более 99 %. Основные примеси – оксиды железа, кремния и кальция.
Электрический взрыв проводников. Быстро развивающимся методом получения тонкодисперсных порошков является электрический взрыв проводника при прохождении по нему мощного импульса тока длительностью 10–5–10–7 с и плотностью 104– 106 А/мм2. Метод является одним из вариантов метода испаре- ния-конденсации.
В этом методе тонкие проволочки диаметром 0,1–1,0 мм помещают в камеру, где импульсно подают ток большой силы
(рис. 1.6).
Электровзрыв проводника представляет собой резкое изменение физического состояния металла в результате интенсивного выделения энергии в нем при пропускании импульсного тока большой плотности. Электровзрыв сопровождается генерацией ударных волн и создает возможность быстрого нагрева металлов со скоростью более 1·107 К·с–1 до высокихтемператур более 104 К.
На начальной стадии электровзрыва джоулев нагрев проводника сопровождается его линейным расширением с относительно небольшой скоростью 1–3 м/с. На стадии собственно
17
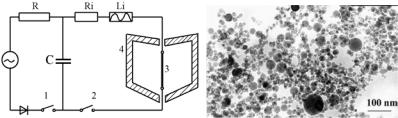
взрыва в результате прохождения импульса тока металл перегревается выше температуры плавления, расширение вещества взрываемого проводника происходит со скоростью до 5·103 м/с
иперегретый металл взрывообразно диспергируется. Давление
итемпература на фронте возникающей ударной волны достигают нескольких сотен МПа и ~104 К соответственно. В результате конденсации в потоке быстро расширяющегося пара образуются частицы очень малых размеров. Регулируя условия взрыва, можно получать порошки с размером частиц от 100 мкм до 50 нм. Средний размер частиц монотонно убывает с ростом плотности тока и сокращением длительности импульса. Форма наночастиц преимущественно сферическая.
а |
б |
Рис. 1.6. Схема получения порошка из проволоки взрывным испарением (а): 1 – зарядный контур, 2 – разрядный контур, 3 – взрывающаяся проволока, 4 – камера синертнымгазом; нанопорошокNiO, полученныйметодом электровзрыва(б)
Электровзрыв в инертной атмосфере позволяет получать порошки металлов и сплавов, а с помощью введения в реактор дополнительных реагентов (воздух, смесь кислорода и инертного газа и др.) можно получать тонкодисперсные порошки оксидов, нитридов, карбидов или их смесей.
Недостатками метода являются: значительный расход энергии и, как следствие, относительная дороговизна получаемых нанопорошков и трудность удаления частиц микронного диапазона размеров, которые возникают из капель расплава.
Лазерная абляция. В методе лазерной абляции материал испаряется под действием импульсного лазерного излучения и затем конденсируется в виде частиц. В последние годы все боль-
18
ший интерес вызывает лазерная абляция твердой мишени, погруженной в жидкость. В этом случае закономерности диспергирования материала существенно изменяются. Это вызвано тем, что наночастицы образуют коллоидный раствор, вследствие чего они могут вернуться в лазерный пучок и повторно подвергнуться облучению.
Вметаллических наночастицах, размеры которых меньше длины свободного пробега электронов объемного материала, возникают коллективные колебания электронного газа, характеризующиеся плазмонной частотой. В спектрах растворов таких частиц возникает соответствующая плазмонная полоса поглощения. Наночастицы интенсивно поглощают излучение на плазмонной частоте, плавятся и локально испаряют окружающую их жидкость. Неравномерное распределение давления паров жидкости вызывает повторное дробление капель расплава на еще более мелкие. В результате лазерное облучение коллоидного раствора приводит как
кизмельчению частиц, так и к изменению их распределения по размерам.
Лазерной абляцией в жидкостях получают частицы благо-
родных металлов (Ag, Au, Pd), их сплавов, Ti, Zn, Cu, Co, Ni,
оксиды TiОх, ZnО, CuО, TiС, полупроводников CdS, ZnSe и др. Этим же методом удается синтезировать частицы структуры ядро–оболочка.
Вкачестве жидких сред используются вода и разнообразные органические растворители: алифатические спирты, хлорированные углеводороды, диметилсульфоксид и др.
Диспергационные методы
Механическое измельчение (механосинтез). Механическое измельчение частиц материала (предварительно полученные порошки, гранулы, размолотые слитки) принадлежит к числу наиболее распространенных методов изготовления порошков. Основой механосинтеза является большое ударное и истирающее воздействие на диспергируемые твердые вещества.
19
При измельчении материалов механическое воздействие является импульсным, т.е. возникновение поля напряжений происходит не в течение всего времени пребывания частиц в реакторе, а только
вмомент соударения частиц и в короткое время после него. Механическое воздействие является также локальным, так как происходит не во всей массе твердого вещества, а там, где возникает поле напряжений. Благодаря импульсности и локальности в небольших областях диспергируемого материала в течение короткого времени сосредотачиваются большие нагрузки. Это приводит к возникновению в частицах дефектов, напряжений, полос сдвига, деформаций, трещин. В результате происходит измельчение вещества, ускоряется массоперенос и перемешивание компонентов, активируется химическое взаимодействие твердых реагентов. Благодаря механическому истиранию и механическому сплавлению может быть достигнута более высокая взаимная растворимость некоторых элементов в твердом состоянии, чем она возможна в равновесных условиях. Особенно легко получать порошки на основе хрупких материалов. Порошки пластичных, высокопрочных и аморфных материалов получитьтруднее.
При механическом измельчении с использованием мельниц уменьшение размеров частиц материала происходит в результате интенсивного раздавливания между рабочими органами мельницы. В зависимости от вида материала и требуемых свойств нанопорошка используются в основном планетарные, шаровые и вибрационные мельницы. Средний размер частиц получаемых порошков может составлять от 5 до 200 нм.
При виброизмельчении, например, сферического порошка алюминия в течение 120 ч в атмосфере аргона с добавлением
вкачестве поверхностного активного вещества стеариновой кислоты получены частицы пластинчатой формы толщиной 160–
180 нм и средним диаметром около 10 мкм с удельной поверхностью до 17,5 м2/г (рис. 1.7).
Особенно мелкие частицы получаются при помоле металлических порошков в среде жидкого азота или аргона (криопомол). Это связано с увеличением хрупкости металлов при понижении темпе-
20