
книги / Получение наночастиц и наноматериалов
..pdf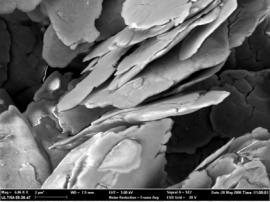
ратуры. Нанопорошки, полученные в среде жидкого азота, покрыты тонкой поверхностной оксидно-нитридной пленкой, вследствие чего они обладают повышенной стойкостью к спеканию и сохраняютразмер частиц при нагревании до 900–950 °С.
Рис. 1.7. Морфология частиц алюминия после измельчения в вибромельнице в течение 120 ч
Высокоэнергетическое измельчение и механосинтез могут обеспечить получение нанопорошков различного состава в широких масштабах, но чистота получаемых продуктов не всегда бывает высокой, так как в процессе измельчения практически всегда происходит загрязнение продукта материалом шаров и футеровки, а также кислородом. Кроме того, минимальный размер частиц также ограничен.
При осуществлении метода противоточного размола в псевдосжиженном слое измельчение частиц порошка происходит за счет столкновения друг с другом. При этом процессы взаимного столкновения частиц, разогнанных до высоких скоростей в струе газа, происходят в середине псевдосжиженного слоя, образованного этими частицами. Только очень незначительная доля частиц соприкасается со стенками камеры, в которой осуществляется процесс размола. Принципиальная схема процесса показана на рис. 1.8.
21
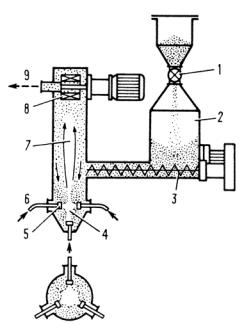
Рис.1.8. Схема установки для противоточного размола в псевдосжиженном слое: 1 – питающее устройство, 2 – бункер с исходными частицами вещества, 3 – система подачи частиц в камеру размола, 4 – псевдосжиженный слой, 5 – сопла подачи газа, 6 – трубопровод подачи газа высокого давления, 7 – камера для размола, 8 – сепаратор, 9 – выходной коллектор газа с мелкими частицами
В нижней части рабочей камеры имеется система сопел, из которых под высоким давлением выходит газ. Образующиеся газовые струи встречаются друг с другом в центре нижней части камеры, разрыхляют размалываемое вещество и образуют псевдосжиженный слой. В этом слое размалываемые частицы с большими скоростями перемещаются от краев к центру камеры. Из зоны размола поток частиц уносится струями газа в верхнюю часть установки, в которой имеется сепаратор для разделения частиц по размерам. Частицы, меньшие определенного размера, уносятся с потоком газа в систему фильтров, где отделяются от газового потока и попадают в накопительный бункер. Крупные частицы сепаратор направляет обратно в зону размола.
22
Порошки, получаемые этим методом, отвечают высоким требованиям по чистоте, обладают высокой однородностью и содержат частицы примерно одинакового размера. Интенсивный поток газа существенно уменьшает нагрев частиц при размоле. Это позволяет обрабатывать аморфные и нанокристаллические порошки. Основной недостаток – сложность и высокая стоимость технологического оборудования в случае получения порошков с наноразмерными частицами.
Метод механического измельчения имеет как положительные стороны, так и недостатки. К положительным сторонам относятся:
•сравнительная простота технологии;
•универсальность;
•возможность получения порошков сплавов, интерметаллидов и композитов.
Недостатки метода:
•трудность получения порошков с одинаковым размером частиц и заданной формы;
•невозможность изготовления особо чистых материалов;
•сложность регулирования свойств материала в процессе его получения.
Очень перспективной разновидностью метода механическо-
го измельчения является механическое легирование, или механо-
химический способ, основанный на том, что при измельчении смеси различных компонентов между ними ускоряется физическое взаимодействие. Кроме того, возможно протекание химических реакций, которые при контакте, не сопровождающемся измельчением, вообще не происходят при таких температурах. Такие реакции принято называть механохимическими.
Например, механохимический синтез нанопорошков карбидов TiC, ZrC, VC и NbC размолом смеси порошков металла
иуглерода в шаровой мельнице приводит к образованию карбидов через 4–12 часов размола, а размер карбидных частиц после 48 часов размола составлял (7 ± 1) нм. Порошки нитридов переходных металлов с размером частиц несколько нанометров син-
23
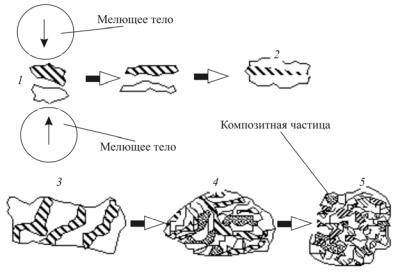
тезируют размолом металлических порошков в вибромельнице
ватмосфере N2. Нанокристаллические сплавы Fe–Ni и Fe–Al с размером зерен 5–15 нм получают размолом порошков металлов в шаровой вибромельнице в течение 300 часов. Вариантом механохимического синтеза, совмещенного с получением нанокомпозитной смеси, является 100-часовой размол смеси крупнозернистых (~75 мкм) порошков вольфрама, графита и кобальта
взаполненной аргоном высокоэнергетичной шаровой мельнице;
врезультате была получена нанокомпозитная смесь WC–Co из зерен кобальта и карбида вольфрама со средним размером час-
тиц 11–12 нм.
Протекание механохимических реакций зависит от дисперсности исходных компонентов, характера и режима измельчения. Воздействие деформирования на свойства вещества можно охарактеризовать как механическую активацию.
Механизм процесса механического легирования традиционно подразделяется на пять последовательных стадий (рис. 1.9).
Рис. 1.9. Поведение порошковых частиц на различных стадиях процесса механического легирования
24
1.Стадия, в течение которой происходит увеличение доли частиц как более грубых, так и доли более тонких по сравнению
сгранулометрическим составом начальной загрузки. Более грубые частицы представляют собой композитные новообразования из различных составляющих шихты, а более тонкие являются главным образом измельченными частицами более хрупких компонентов шихты.
2.Стадия сваривания, в течение которой более крупная фракция порошка продолжает увеличиваться, в то время как количество более мелкой фракции остается практически неизменным. При этом крупные вторичные частицы имеют многослойную композитную структуру со слоями, параллельными поверхности воздействующих мелющих тел или большей оси частицы. Объем этих элементарных слоев значительно меньше объема исходных частиц шихты и они, таким образом, представляют собой измельченные частицы исходных порошков, включающие различные составляющие шихты.
3.Стадия образования равноосных частиц, во время протекания которой резко уменьшается количество крупных пластинчатых частиц-конгломератов и идет образование более равноосных частиц. Наиболее мелкие фракции порошка располагаются теперь параллельными слоями, как и отдельные крупные фрагменты композиционных частиц, а фрагменты частиц элементарных порошков практически отсутствуют. Как крупные, так и мелкие частицы представляют собой конгломераты аналогичной структуры, в которых слои из частиц отдельных компонентов шихты соединены между собой в основном спомощью холодной сварки.
4.Стадия, где происходит произвольная ориентация участков сварки, при которой образуются округлые конгломераты из композиционных частиц, сваривающихся между собой без ка- кой-либо предпочтительной ориентации.
5.Стадия завершения механического легирования: формируется устойчивое распределение частиц по размеру и достигается максимальный уровень их твердости. Композиционная неоднородность сохраняется лишь на субзеренном уровне, т.е. 10–100 нм.
25
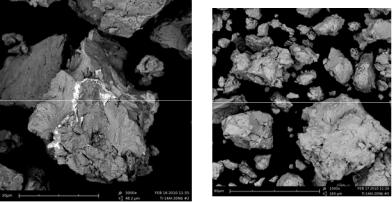
На рис. 1.10 представлены изображения частиц смеси Ti– 14Al–20Nb, полученной механическим легированием в аттриторе после различного времени смешивания.
а |
б |
Рис. 1.10. Структура частиц смеси Ti–14Al–20Nb, полученной механическим легированием в аттриторе после смешивания в течение: а – 25 мин; б – 50 мин
Механическое легирование применяют для получения широкого спектра многофазных порошковых сплавов, таких как дисперсно-упрочненные сплавы, а также композиции материалов с ограниченной растворимостью.
Следует особо отметить, что высокая твердость в результате наклепа и форма частиц механически легированных порошков часто не позволяют применять при производстве изделий традиционные методы прессования и спекания, таким образом, преимущества механического легирования реализуются в полной мере только в том случае, если следующее за механическим легированием компактирование, термомеханическая и термическая обработка тщательно оптимизированы путем контроля микроструктуры.
Ультразвуковое диспергирование. Наночастицы можно по-
лучить путем ультразвукового измельчения (с частотой колебаний выше 20 000 с–1) веществ, переведенных в состояние коллоидных растворов. Этот метод особенно эффективен для веществ
26
с низкой прочностью: смол, гипса, серы, графита. Этот метод известен как сонохимический синтез, в основе которого заложено явление кавитации микроскопических пузырьков. При кавитации в малом объеме развиваются аномально высокая температура (до 3000 К) и давление (до 50–100 МН/м2), а также огромные скорости нагрева и охлаждения (до 1010 К/с). В условиях кавитации пузырьки становятся как бы нанореакторами. С использованием экстремальных условий внутри кавитационных пузырьков получено много нанокристаллических (аморфных) металлов, сплавов и тугоплавких соединений (например, наночастицы Fe, Ni, Co и их сплавов из карбонилов, золота и меди, нанооксид циркония и др.).
Основная область применения сонохимического диспергирования связана с разрушением агломератов в порошках, полученных другими методами.
Для диспергирования металлов и сплавов можно использовать электроэрозию. В этом случае процесс распыления протекает внутри диэлектрической жидкости, продукты превращения которой покрывают поверхность образующихся наночастиц. В зависимости от условий проведения процесса, природы металла и среды диспергирования диаметр получаемых наночастиц лежит в интервале 2,5–20 нм, но отдельные частицы могут иметь размеры до 100 нм. Однако в этом случае наблюдается значительное взаимодействие образующихся наночастиц со средой диспергирования. Например, при использовании органических растворителей в качестве диэлектрической среды происходит науглероживание продукта, а при использовании расплавленной серы – образование сульфидов. С помощью метода электроэрозии были получены наночастицы со сложным составом для постоянных магнитов.
Распыление расплава
Данная группа методов основана на быстром распылении и охлаждении расплава исходного материала. Эта технология позволяет получить порошки размером не меньше 100 нм. Вме-
27
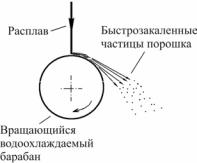
сте с тем получаемые порошки с размером частиц 0,5–10 мкм имеют нанокристаллическую (а в ряде случаев и аморфную) структуру и, следовательно, могут также быть отнесены к наноматериалам, а технология их получения – к нанотехнологиям. Процессы получения порошка можно вести в защитной атмосфере. В настоящее время для получения нанопорошков используются в основном три варианта этой технологии.
1. Контактное охлаждение при помощи водоохлаждаемого диска или барабана. Этот метод основан на подаче расплавленого материала на быстро вращающийся водоохлаждаемый диск или барабан, которые изготовлены из материалов с высокой теплопроводностью (рис. 1.11). Как
правило, в качестве такого мате- Рис. 1.11. Принципиальная схема рас-
риала используют медь. При пыления порошка из расплава при этом обеспечивается скорость помощи водоохлаждаемого барабана
охлаждениядо 108 К/с.
Поверхность барабана или диска выполняется шероховатой (зубчатой). Гладкая поверхность будет обеспечивать получение только фольги, полосы или проволоки толщиной порядка 10– 50 мкм с аморфной или нанокристаллической структурой. Получаемый порошок отличается хлопьевидной формой частиц. Такая форма частиц может быть причиной неоднородной структуры и анизотропии свойств у изделий, сформированных из подобных порошков. В связи с этим получаемые рассматриваемым методом порошки обычно дополнительно подвергают механическому измельчению. Это и является главным недостатком метода.
2. Ударное распыление расплава. При этом методе струя или капли расплава механически разбиваются на мелкие частицы при соударении с интенсивно охлаждаемыми быстро вращающимися металлическими лопатками. Обеспечивается скорость охлаждения до 107 К/с. Как и в предыдущем методе, частички
28
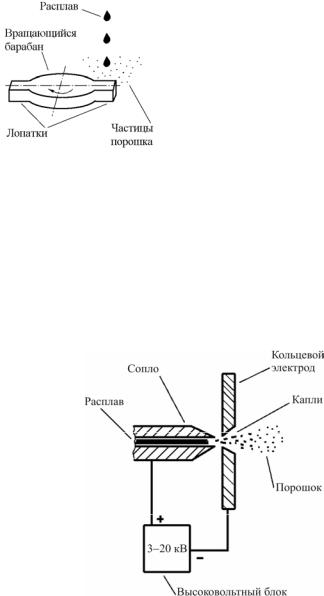
|
порошка имеют неправильную форму |
|
и для получения при последующем фор- |
|
мовании качественных изделий с одно- |
|
родной структурой необходимо допол- |
|
нительно подвергать порошок механи- |
|
ческому измельчению (рис. 1.12). |
|
3. Электрогидродинамическое рас- |
|
пыление расплава. В этом методе для |
|
распыления расплава используются |
Рис. 1.12. Принципиальная |
электростатические силы (рис. 1.13). |
схема процесса ударного |
Струя расплава подается в сопло с |
распыления расплава |
диаметром отверстия порядка 80 мкм, |
|
перед которым распо ложен кольцевой электрод. К нему прикладывается постоянное напряжение 3–20 кВ. В результате из сопла вылетают положительно заряженные мелкие капли расплава, образующие после охлаждения частицы порошка. Размер частиц в зависимости от материала и технологических параметров может составлять 100 нм–10 мкм. Недостатком этого метода является очень низкая производительность (2 г/ч с одного сопла).
Рис. 1.13. Принципиальная схема процесса электрогидродинамического распыления расплава
29
1.3.Методы получения наноразмерных частиц, основанные на химических процессах
Химическое осаждение из паровой фазы
Метод основан на синтезе наноматериалов в ходе химического взаимодействия, протекающего в атмосфере паров легколетучих соединений. Все многообразие газофазных химических реакций можно разделить на реакции разложения, протекающие
сучастием одного исходного химического соединения
А= В + С,
иреакции между двумя и более химическими соединениями
А + В = С + D.
Обязательным условием использования первого типа химических реакций является существование подходящего химического соединения, содержащего все элементы конечного продукта, что встречается нечасто. Поэтому второй тип газофазных реакций является более распространенным.
В качестве исходного сырья используются легколетучие вещества: галогениды (главным образом хлориды) металлов, оксихлориды металлов MOnClm, алкильные соединения M(R)n, алкоксидыM(OR)n и др. Размер получаемых частиц может регулироваться температурой и скоростью осаждения. По такой технологии получены нанопорошки, непосредственный синтез которых другими методами связан со значительными трудностями, а именно порошки кремния, бора, оксидов титана, циркония, алюминия, нитриды, карбиды и карбонитриды кремния и диборид титана с размером частиц от 20 и более нм.
Например, для синтеза TiB2 используется взаимодействие в газовой фазе паров натрия Na в среде аргона с газовой смесью хлоридов Ti и В. Натрий связывает анионы хлора, а бор взаимодействует с титаном с образованием порошка диборида титана.
Реакционный газ вводится в печь с внешним нагревом, при этом соединения в определенной зоне реакционной камеры термически разлагаются с образованием твердого осадка в виде на-
30