
книги / Механика пластического деформирования трансверсально-изотропных композиционных сверхпроводниковых материалов
..pdfчительнее на первых проходах маршрута, так как по мере утонения проволоки шероховатость ее будет уменьшаться. Лучшему качеству поверхности будет соответствовать более высокая нагнетающая способность инструмента [9].
3.4. Реализация условий улучшенного (смешанного) режима трения при волочении
Эффективным путем решения проблемы снижения сил трения при волочении является реализация условий жидкостного трения за счет гидродинамического эффекта технологической смазки. Отличительной особенностью режима гидродинамической смазки является существование разделительного слоя смазки между поверхностями обрабатываемого изделия и инструмента. Смазочный слой при этом имеет толщину h0 , превышающую высоту микронеровностей по-
верхностей деформируемого тела и инструмента, обеспечивая разделение поверхностей и механически экранируя трущиеся поверхности от контакта,
h0 ≥ Rzз + Rzи , |
(3.12) |
где Rzз , Rzи – средняя высота микронеровностей заготовки и инструмента соответственно.
Учитывая, что для технологического инструмента Rzз >> Rzи ,
можно условие реализации гидродинамического трения (3.12) записать в следующем виде:
h0 ≥ Rzз . |
(3.13) |
Наряду с положительным влиянием режима жидкостного трения на технологические параметры процесса волочения следует отметить, что при гидродинамическом волочении качество поверхности изделий уступает по сравнению с волочением в граничном режиме трения, поскольку волочильный инструмент за счет механического экранирования контактных поверхностей не производит сглаживающего действия на микронеровности протягиваемого изделия. Данный момент зачастую является сдерживающим фактором при использо-
81
вании процесса гидродинамического волочения. Следует отметить также, что наличие излишнего слоя смазки на протягиваемой сверхпроводниковой заготовке может оказаться нежелательным при проведении промежуточных термообработок в случае многократного волочения сверхпроводниковой заготовки. В данном случае на поверхности заготовки могут сохраняться продукты сгорания смазки, снижающие качество поверхности изделий и затрудняющие последующее волочение. При этом может оказаться рациональной реализация улучшенного трения с пониженным коэффициентом трения по сравнению с коэффициентом граничного трения.
Известно также, что при гидродинамическом волочении в отдельных случаях возможно возникновение участков протягиваемых изделий с переменным значением диаметра, напоминающих по форме «бамбук». Данное явление сопровождается изменением усилия волочения и дополнительными динамическими нагрузками на протягиваемую заготовку, что является нежелательным для процесса волочения сверхпроводников.
В качестве параметра, определяющего коэффициент улучшенного трения, предлагается использовать толщину смазочного слоя в очаге деформации, полученную в результате решения гидродинамической задачи течения смазки в рабочем конусе инструмента. Коэффициент улучшенного трения предлагается определять следующей зависимостью:
f = f |
гр |
− ( f |
гр |
− f |
ж |
) |
h0 |
, |
(3.14) |
||
R |
з |
||||||||||
|
|
|
|
|
|
||||||
|
|
|
|
|
|
|
z |
|
|
||
|
|
|
|
|
|
|
|
|
|
||
где fгр – коэффициент граничного трения; |
fж |
– коэффициент тре- |
ния, соответствующий жидкостному режиму смазки.
В соответствии с формулой (3.14) при h0 = 0 реализуется режим граничного трения (f = fгр), при h0 = Rzз соответственно режим жидко-
стного трения (f = fж).
Толщина слоя смазки в зоне деформации может быть рассчитана с учетом закономерностей течения смазки в рабочем конусе инструмента (рис. 3.7).
82
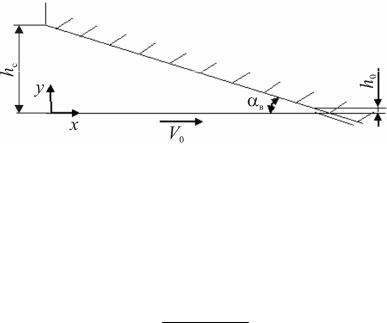
Рис. 3.7. Конический участок технологического инструмента
Разрешив дифференциальное уравнение (3.5) с учетом (3.1) и переменного значения толщины смазочного слоя
h(x) = hc − xtgαв ,
получим
3αµ0V0 |
|
h0 = tgαв (1− е− ασs ) . |
(3.15) |
При известных реологических характеристиках смазки ( α, µ0 ) и технологических параметрах (V0 , tgαв, σs ) рассчитывается значение h0 и по формуле (3.14) для известного значения средней высоты микронеровностей поверхности заготовки Rzз оценивается коэффи-
циент трения улучшенного (смешанного) режима смазки при волочении [29]. Найденное значение коэффициента трения улучшенного режима может быть использовано в расчетах энергосиловых режимов производства сверхпроводниковых изделий.
На основании анализа условий трения рекомендуется реализация при производстве сверхпроводниковых изделий условий гидродинамической смазки с использованием соответствующих конструкций сборного инструмента на больших размерах промежуточной заготовки (свыше 30 мм) и условий улучшенного (смешанного) трения на среднем и тонком волочении при использовании традиционного инструмента.
83
3.5. Определение оптимальной геометрии технологического инструмента при пластическом деформировании
Усилие пластической деформации в значительной степени зависит от профиля зоны деформации, материала, из которого изготовлен технологический инструмент, качества обработки поверхности рабочего канала инструмента.
Первые исследования, посвященные данному вопросу, были проведены Френсисом, Зибелем, в дальнейшем значительные исследования были продолжены И.Л. Перлиным [30], С.И. Губкиным [31], П.И. Мининым [32], А.Л. Тарнавским и многими другими.
При деформации в конических инструментах существует зона оптимальных углов, в пределах которой усилие волочения при прочих равных условиях имеет минимальное значение. При малых углах рабо-
чего конуса, когда |
форма волочильного |
инструмента |
приближена |
кформе цилиндра, |
происходит увеличение |
контактной |
поверхности |
и, следовательно, сил трения. С увеличением угла рабочего конуса контактная поверхность уменьшается, уменьшается сила трения ипадает общее давление металла на волоку. Однако с повышением угла αв воз-
растают неравномерность деформации, скорость деформации и ухудшаются условия смазки – все это ведет к повышению усилия волочения. Таким образом, в результате сложного взаимодействия перечисленных факторов образуетсяоптимальный уголилизона оптимальныхуглов.
Как и любой другой процесс пластической деформации металлов, процесс волочения характеризуется определенной энергоемкостью, снижение которой является актуальной проблемой.
Энергосиловые параметры при волочении определяются главным образом геометрией технологического инструмента, одной из основных характеристик при этом является угол наклона образующей волочильного инструмента к оси волочения [2]. Оптимизация угла αв позволяет
обеспечить минимальные значения напряжения волочения, что дает возможность снизить энергопотребление, уменьшить вероятность обрыва переднего конца заготовки, повысить единичные обжатия, обеспечитьдостаточную контактнуюповерхностьметаллас волокой.
84

Для определения напряжения волочения наибольшего внимания заслуживают те, которые выведены с учетом основных положений теории пластичности, к ним относятся:
– формула Закса:
σ |
вол |
= F {σ |
|
a + 1 |
[1− ( |
F1 |
)a ] + σ |
|
( |
F1 |
)a } , |
T a |
|
|
|
||||||||
|
1 |
|
F |
q |
|
F |
|||||
|
|
|
|
|
0 |
|
|
0 |
|
где a = fctgα ;
– формула Е. Зибеля:
σвол = F1σТС ln F0 (1+ ftgα + fctgα) ,
F1
где σТС – усредненное по зоне деформации сопротивление деформа-
ции протягиваемого материала;
– формула В.Н. Заруева:
|
|
σ |
вол |
= F |
{σ |
( |
a + 1 |
)[1− ( |
F1 |
)a ] + σ |
|
( |
F1 |
)a } , |
|
|
|
|
|
|
|
||||||||||
|
|
|
1 |
s |
|
a |
F |
q |
|
F |
|||||
|
|
|
|
|
|
|
|
|
|
0 |
|
|
0 |
|
|
где a = |
1 |
+ |
|
|
f |
|
− 1 [6]. |
|
|
|
|
|
|
||
|
|
|
|
|
|
|
|
|
|||||||
1− ftgα |
|
(1− ftgα) |
|
|
|
|
|
|
В настоящее время из существующих формул для определения напряжения волочения заготовок круглого сечения наиболее физически понятной и удобной для применения является упрощенная формула И.Л. Перлина [18]:
σ |
|
= ln |
F0 |
σ |
|
+ fctgα |
|
(σ |
|
− σ |
|
) |
+ σ |
|
, |
(3.16) |
|
F |
|
|
|
|
|
||||||||||
|
вол |
|
|
ТС |
|
П |
|
ТС |
|
q |
|
|
q |
|
|
|
|
|
1 |
|
|
|
|
|
|
|
|
|
|
|
|
|
где σТС – усредненное по зоне деформации сопротивление деформации протягиваемого материала; f – коэффициент внешнего трения между обрабатываемым металлом и волочильным инструментом; σq – противонатяжение при волочении; αП – приведенный угол инструмента, учитывающийналичие калибрирующего пояска (tg αП = 0,65 tg αв ).
85
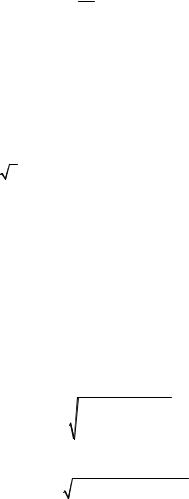
Упрощенная формула (3.16) широко используется в инженерной практике. Однако недостатком формулы (3.16) является то, что она не позволяет определять оптимальный угол конусности рабочей волоки. В теории деформации через конические инструменты (волочение, прессование) известно наличие оптимальных углов конусности технологического инструмента, обеспечивающих минимальные значения силовых параметров деформации.
В то же время множитель ln F0 = λ в формуле (3.16) является
F1
аналогом степени деформации при волочении [18], не учитывающим дополнительные сдвиговые деформации в коническом технологическом инструменте. С учетом дополнительных сдвиговых деформаций на входе в конический инструмент и выходе из него (2.25) предлагается модифицированная формула для определения напряжения волочения (3.16) в следующем виде:
σ |
|
= (ln λ + |
|
4 |
tgα |
) σ |
|
+ fctgα |
|
(σ |
|
− σ |
|
) |
+ σ |
|
. (3.17) |
вол |
|
|
ТС |
П |
ТС |
q |
q |
||||||||||
|
3 |
3 |
в |
|
|
|
|
|
|
|
|||||||
|
|
|
|
|
|
|
|
|
|
|
|
|
|
|
В отличие от формулы (3.16) формула (3.17) позволяет определять оптимальные углы конусности волочильного инструмента αв из
условия минимума напряжения волочения. Условие минимума напряжения волочения записывается в виде
∂σвол |
= 0. |
(3.18) |
|
||
∂tgαв |
|
Продифференцировав выражение (3.17) согласно (3.18) с учетом того, что tgαn = 0,65 tgαв , после преобразований и упрощений получим уравнение для определения оптимального значения tgαв :
tgαвопт = 1,414 ln λ f (1− |
σq |
) |
(3.19) |
|
|||
|
σТС |
|
и соответственно
опт |
|
|
(3.20) |
αв |
= arctg 1,414 |
ln λ f (1− σq / σТС ) . |
86

Наличие принудительного противонатяжения при волочении сверхпроводниковой заготовки нежелательно, поскольку противонатяжение приводит к увеличению напряжения волочения и повышению опасности разрушения сверхпроводящих волокон. Следует отметить, что при отсутствии противонатяжения ( σq = 0 ), что харак-
терно для большинства случаев, оптимальный угол не зависит от величины сопротивления деформации, определяется лишь коэффициентами вытяжки и внешнего трения в зоне деформации:
αвопт = arctg[1,414 ln λ f ] . |
(3.21) |
Коэффициент трения для сверхпроводниковой заготовки определяется как коэффициент трения пары медь–материал инструмента. Для волочения в граничном режиме трения величины коэффициента трения для меди меняются от 0,08 (отожженная медь – стальной инструмент) до 0,05 (упрочненная медь – технический алмаз в качестве инструмента) [18].
На рис. 3.8 представлены расчетные значения оптимальных углов конусности волочильного инструмента в зависимости от вытяжки для различных коэффициентов трения для волочения в условиях граничной смазки. Расчетные значения αоптв для f = 0,01 (кривая 4)
относятся к условиям гидродинамической смазки.
На рис. 3.8 видно, что с увеличением коэффициента вытяжки значения оптимальных углов возрастают, уменьшение коэффициента трения за счет улучшения условий смазки приводит к снижению оптимальных углов [33].
Геометрия волочильного инструмента, как правило, стандартизирована [34], поэтому для стандартных углов конусности могут быть определены оптимальные значения коэффициентов вытяжки, обеспечивающие минимальные значения напряжения волочения. Разрешив соотношение (3.21) относительно λ , получим оптимальную вытяжку
λопт = exp(0,5 |
tg2αв |
) . |
(3.22) |
|
f
87
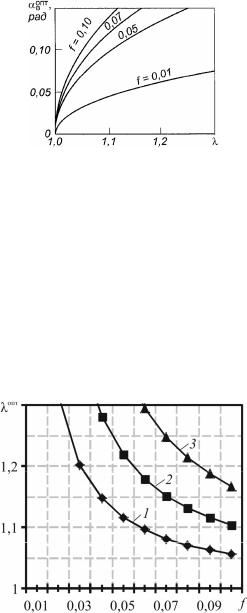
Рис. 3.8. Оптимальные углы конусности волочильного инструмента:
1 – f = 0,1; 2 – 0,07; 3 – 0,05; 4 – 0,01
Для коэффициента трения f = 0,05 расчеты по формуле (3.22) дают значения оптимальных коэффициентов вытяжки. Для αв = 6° получаем
λопт = 1,12; для αв = 8° – λопт = 1,21; дляαв = 10° – λопт = 1,36. С уве-
личением коэффициента трениярасчетные значения λопт уменьшаются.
На рис. 3.9 приведены расчетные значения оптимальных коэффициентов вытяжки, полученные по формуле (3.22), в зависимости от коэффициента трения для различных значений угла конусности технологического инструмента. На рис. 3.9 видно, что с увеличением αв оптимальные значения вытяжек возрастают, увеличение коэффи-
циента внешнего трения приводит к снижению λопт .
Рис. 3.9. Зависимость оптимальных коэффициентом вытяжки от коэффициента трения дляразличныхугловнаклонаобразующейконусаволоки: 1 – αв = 6º; 2 – 8º; 3 – 10º
88
Результаты расчета, приведенные на рис. 3.9, позволяют выбирать оптимальные значения вытяжки при известных значениях коэффициента трения и геометрии волочильного инструмента.
Список литературы к главе 3
1.Афонин В.К. Металлы и сплавы: справочник. – М.: Метал-
лургия, 2003. – 532 с.
2.Тимошенко С.П., Гудьер Дж. Теория упругости. – М.: Наука,
1975. – 576 с.
3.Колмогоров Г.Л., Ковалев А.Е., Бажин А.А. О роли контактного трения при обработке металлов давлением // Известия вузов. Черная металлургия. – 2002. – №9. – С. 64–65.
4.Волочение в режиме гидродинамического трения – технология XXI века / Г.Л. Колмогоров, В.Н. Трофимов, Т.С. Малинина, А.Е. Ковалев // Метизное производство в XXI веке: межвуз. сб. науч. тр. – Магнитогорск: Изд-во МГТУ, 2001. – С. 60–67.
5.Трение и износ / В.М. Корбут, В.И. Пикаева, Е.И. Кочеткова,
Г.М. Бартенев // Металлургия, 1982. – №5. – Т.3. – С. 784–788.
6.Корбут В.М., Пикаева В.И., Бартенев Г.М. Трение и износ //
Металлургия. – 1980. – №5. – Т. 1. – С. 869–877.
7.Денко В.П., Жилкин В.З. Основы теории и технологии волочения проволоки из титановых сплавов. – Минск: Наука и техника,
1970. – С. 204.
8.Боуден Ф., Тейбор Д. Трение и смазка твердых тел: пер.
сангл. – М.: Машиностроение, 1968. – 543 с.
9.Колмогоров Г.Л. Гидродинамическая смазка при обработке металлов давлением. – М.: Металлургия, 1986. – 168 с.
10.Крагельский И.В., Добычин М.Н., Комбалов В.С. Основы расчетов на трение и износ. – М.: Машиностроение, 1977. – 525 с.
11.Перлин И.Л., Шапиро В.Я., Школьников Е.Л. // Известия вузов. Цветная металлургия. – 1963. – №5. – С. 130–137.
12.Шапиро В.Я. Физико-химические закономерности действия смазок при обработке металлов давлением. – М.: Изд-во АН СССР,
1963. – С. 51–54.
89
13.Шапиро В.Я., Школьников Е.Л. Физико-химические закономерности действия смазок при обработке металлов давлением. – М.:
Изд-во АН СССР, 1963. – С. 55–61.
14.А.с. 152229 (СССР). Мосеев В.Ф., Коростелин А.А. Опубл.
вБ.И. – 1962. – №24. – 15 с.
15.Мосеев В.Ф., Коростелин А.А. // Сталь. – 1962. – №3. –
С. 280–281.
16. Christopherson D.G. // Journal of the Institute of Petroleum. – 1954. – Vol.40. – №370. – Р. 295–298.
17. Колмогоров Г.Л. Гидродинамическая подача смазки в процессах обработки металлов давлением // Механика деформирования и разрушения: сб. науч. тр. – Екатеринбург: Изд-во УрО РАН, 2001. –
С. 159–163.
18.Перлин И.Л., Ерманок М.З. Теория волочения. – М.: Метал-
лургия, 1971. – 447 с.
19.А.с. 165416 (СССР). Ерманок Ю.Н., Зубов Б.Г., Орлов С.И. [и др.]. Опубл. в Б.И. – 1964. – №19. – 7 с.
20.Недовизий И.Н., Петрухин С.И. // Сталь. – 1963. – №12. –
С. 1128–1130.
21.Недовизий И.Н., Петрухин С.И., Петров А.П. // Метизное производство. – 1972. – №1. – С. 26–33.
22.Недовизий И.Н., Петрухин С.И., Петров А.П. // Метизное производство. – 1972. – №1. – С. 33–39.
23.Tarrersall G.H. // The Journal of Mechanical Enineer Science. – 1961. – Vol. 3. – №4. – Р. 360–362.
24.Tarrersall G.H. // The Wire Industry. – 1962. – №346. – Р. 975, 978–980, 982, 992.
25.Christopherson D.G. and Naylor H. // The Wire Industry. – 1955. – Vol.22. – №260. – Р. 775–777.
26.Christopherson D.G. and Naylor H. // Scientific Lubrication. –
1956. – №3. – Р. 23–27.
27. Уилсон, Валовит. // Проблемы трения и смазки. – 1971. – №1. –
С. 71–76.
28. Колмогоров В.Л., Орлов С.И., Селищев К.П. Волочение в режиме жидкостного трения. – М.: Металлургия, 1967. – 155 с.
90